
4 minute read
CAN GREEN HYDROGEN WORK FOR AFRICA?
HHydrogen is used mainly to make chemicals such as fertiliser and in oil refineries. Most hydrogen in the world today is made from natural gas or coal – methods associated with large carbon-dioxide emissions. Developed countries are therefore looking to “green hydrogen” instead – produced using renewable electricity such as solar and wind power.
Global hydrogen demand reached 94-million tons in 2021 and contained energy equal to about 2.5% of global final energy consumption. Only about 0.1% of current global hydrogen production is green, but big expansions are planned.
Advertisement
New applications for green hydrogen are also envisaged. Since the objective of using green hydrogen is really to reduce carbon dioxide, the applications to target first should be those that will yield the largest reductions in emissions.
Michael Liebreich’s classification is a useful indicator of the potential markets for green hydrogen. At the top of that classification in terms of efficiency are the following applications: fertiliser, hydrogenation, methanol, hydrocracking and desulphurisation. In the second tier are shipping (using e-fuel or ammonia), steel, off-road vehicles, chemical feedstock and long-term storage. By contrast, using green hydrogen for metro trains and buses would make no sense, in terms of Liebriech’s table.
But green hydrogen currently costs much more to make than less clean types of hydrogen. Using it to produce the 180-million tons per annum of ammonia required globally for fertiliser production would have a severe knock-on effect on food prices. So it is difficult to see how this transition is going to occur.
HOW IS GREEN HYDROGEN MADE?
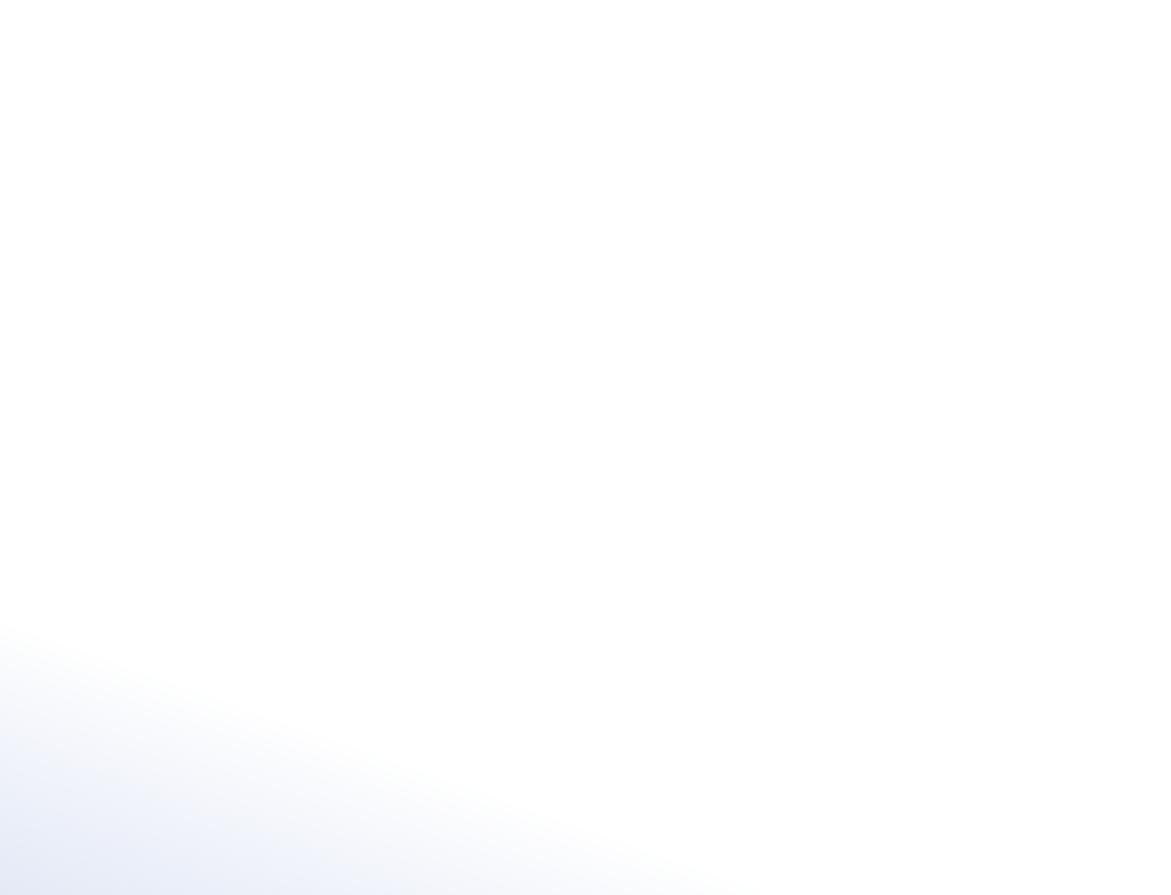
Green hydrogen is made from water. Using renewable (green) electricity, equipment called electrolysers separates the hydrogen from oxygen in water (H₂O). The process is called electrolysis.
Green hydrogen production emits no carbon dioxide, but the construction of renewable electricity infrastructure currently uses fossil fuels, which do emit carbon dioxide.
Hydrogen has traditionally been made from non-renewable energy sources like coal (black hydrogen) and natural gas (grey hydrogen). When these methods are combined with carbon capture and storage, the hydrogen produced is known as “blue hydrogen”.
WHAT CHALLENGES DOES GREEN HYDROGEN PRESENT?
Although the costs of renewable power generation have been coming down, the cost of electrolysis is still not commercially competitive.
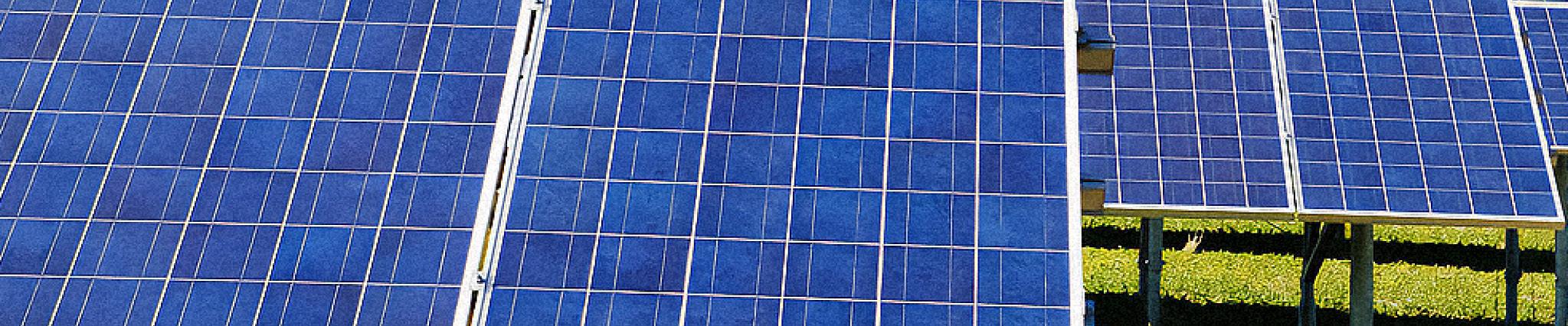

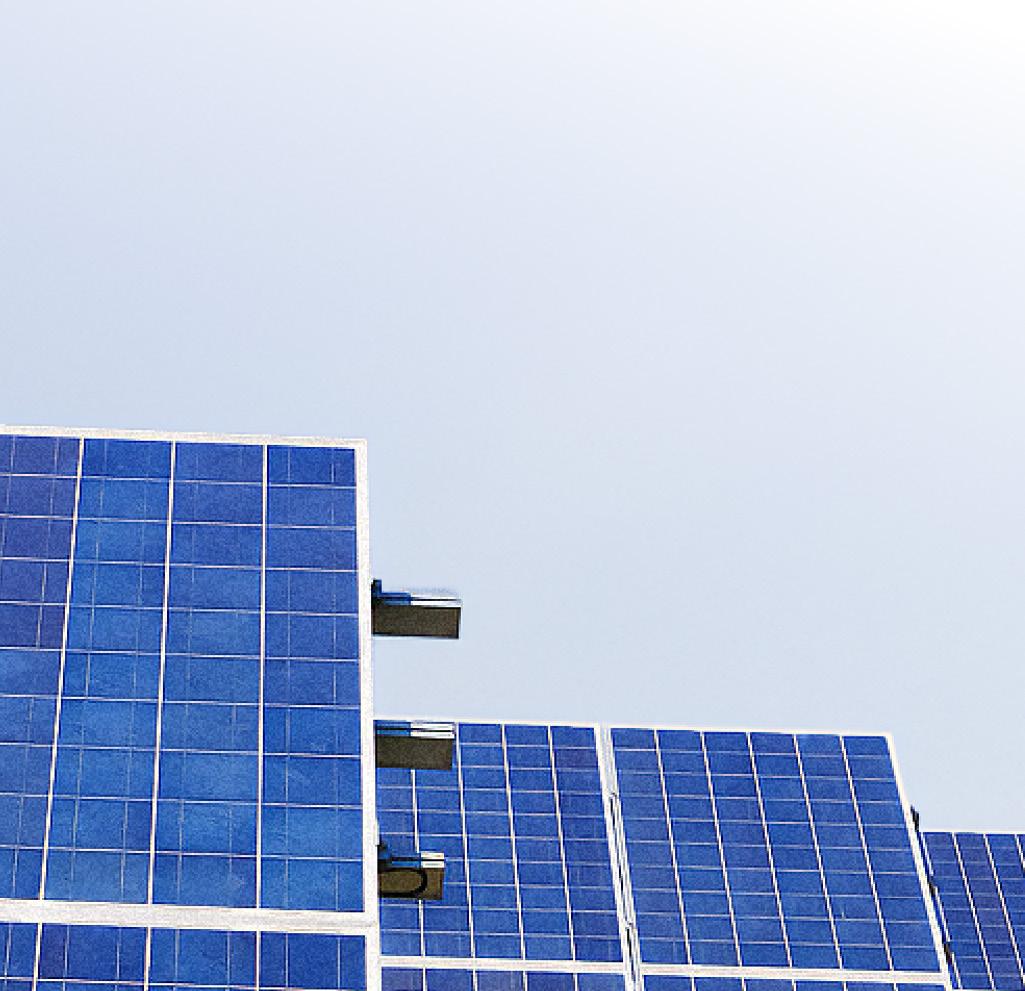

Today, green hydrogen has an estimated energy equivalent cost of between $250 and $400 per barrel of oil at the factory gate, according to the International Renewable Energy Agency (IRENA). Future cost reductions are forecast but these are uncertain. Current oil prices are around $100 a barrel – much less than it would cost to use green hydrogen instead of conventional petroleum products.
The costs of transporting hydrogen must be taken into account too.
Unfortunately, the physics of hydrogen is against low-cost hydrogen transport. It is much more challenging than oil-based liquid fuels, liquefied petroleum gas or liquefied natural gas. Ocean transport of hydrogen has to be at very low temperatures (-2530C). Petrol or diesel doesn’t need costly refrigeration: it is transported at ambient air temperature.
And hydrogen carries only 25% of the energy that a litre of petrol does, making it much more expensive to transport and store the same amount of energy.
Alternative ways to transport hydrogen have been investigated. Because ammonia (NH₃) is much easier and cheaper to transport than hydrogen, the IRENA has recommended “storing” hydrogen in ammonia for shipping. But that requires additional equipment to put the hydrogen into ammonia and strip it out at its destination. These processes add costs of about $2.50-$4.20/kg (equivalent to $123-$207 per barrel of oil), according to the agency.
Hydrogen is more difficult to handle than conventional fossil fuels. It is a colourless, odourless and tasteless gas, unlike conventional hydrocarbons. This makes leak detection more difficult and increases the risk of fire or explosion. Hydrogen fires are invisible to the human eye.
Historically, hydrogen has been controlled within factory perimeters and managed by trained people. The widespread introduction of hydrogen into society will require new measures and skills, including insurance, materials handling, firefighting and disaster management.
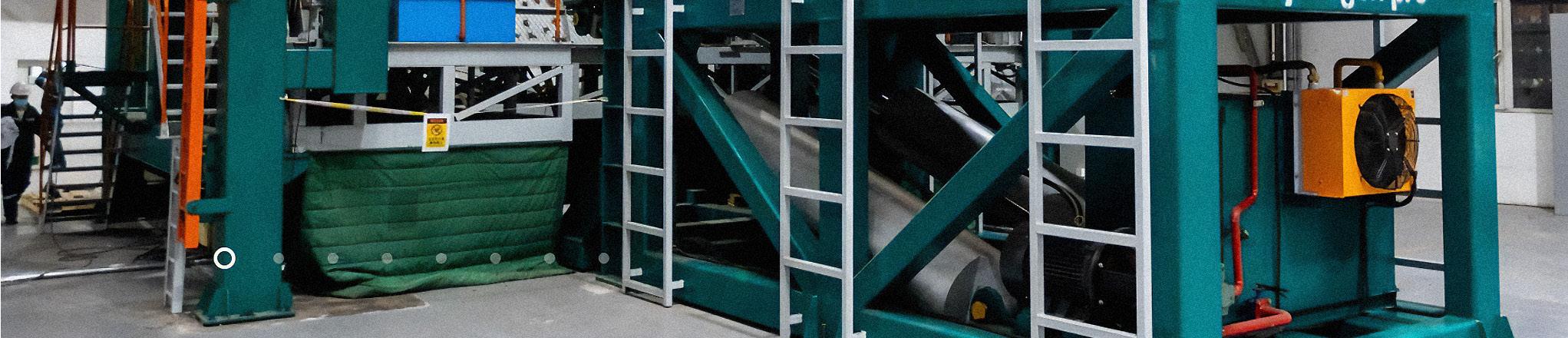
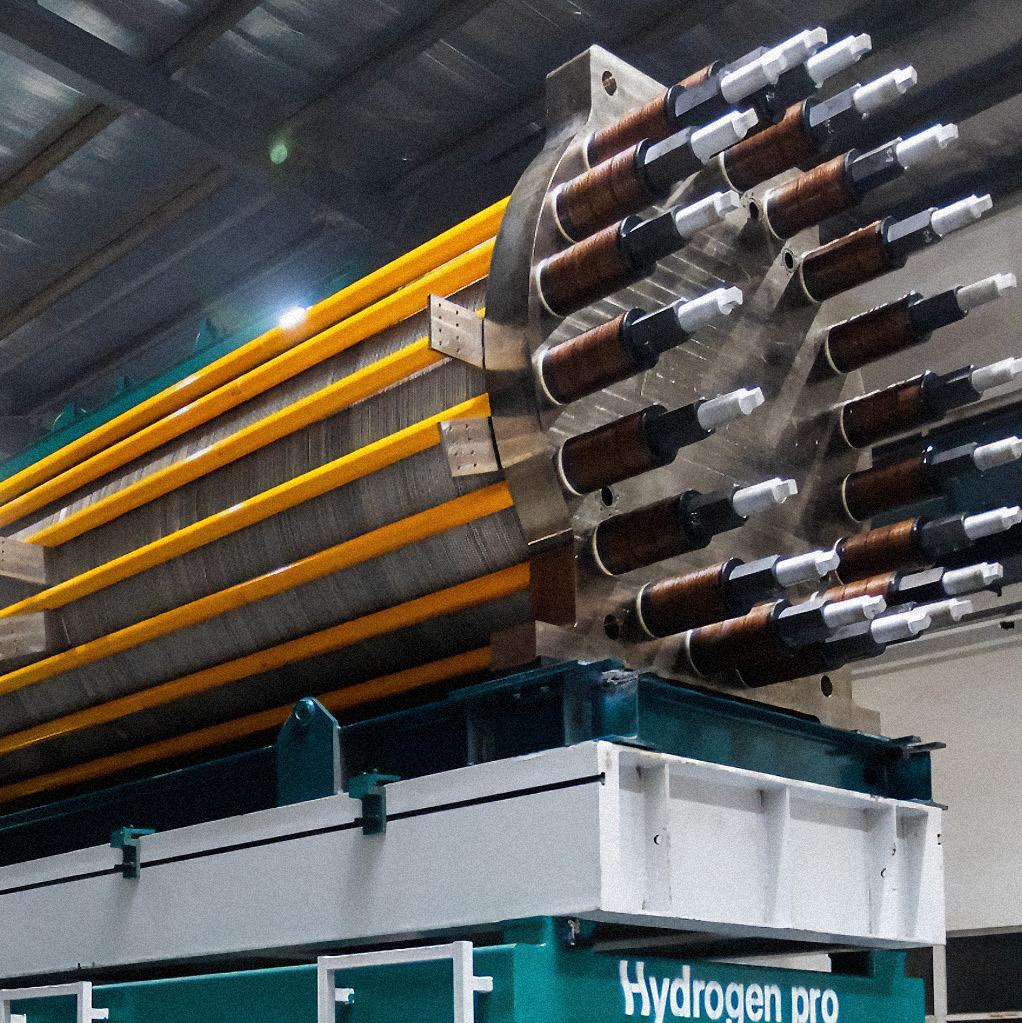
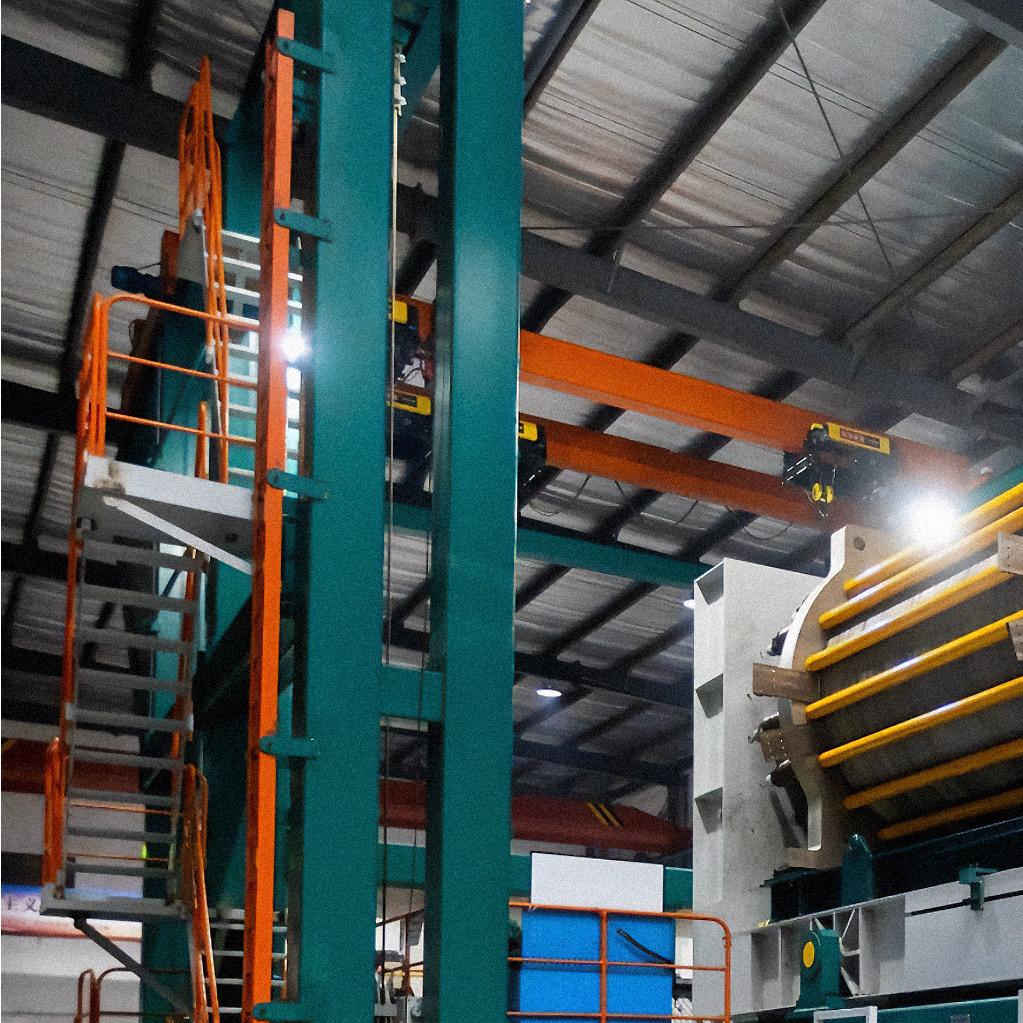
WHERE ARE THE FIRST HYDROGEN MEGAPROJECTS LIKELY TO BE BUILT?
Construction of the first gigawatt-scale green-hydrogen project in Saudi Arabia has already started. Many of the pioneering projects will be built in the southern hemisphere, mostly in developing countries. This is because they are less densely populated and have better renewable energy resources (solar and wind) for generating the necessary electricity.
Although this may sound positive for developing countries, there are big risks in developing hydrogen mega-projects. For one thing, the “iron law” of mega-projects states: Over budget, over time, under benefits, over and over again.
Project owners bear the project execution risk.
Risks also include exchange-rate risk, remote locations, pioneering technology and a lack of skills. Prospective host countries will have to balance these risks against the temptations of improved investment, employment and balance of payments. They would be wise to extract guarantees from their customer countries so as to avoid the injustice of the global south subsidising the global north as it transitions to cleaner energy.
South Africa now has a “Hydrogen Roadmap” after many years of government funding. There is talk by the energy company Sasol and vehicle manufacturer
Toyota of a “Hydrogen Valley”, a geographical corridor of concentrated hydrogen manufacture and application industries. And the South African government and Sasol are talking of establishing a new port on the west coast at Boegoebaai for the manufacture and export of green hydrogen. In Nelson Mandela Bay, Hive Hydrogen is planning a $4.6-billion green ammonia plant.
Namibia also has big plans for a $10-billion green-hydrogen project. The key to reducing green hydrogen costs in the future lies mainly in technological improvements and cost reductions related to mass manufacture and a scaleup in electrolysis. And to a lesser extent, incremental cost reductions in transport and handling.
About The Authors
Rod Crompton is a Visiting Adjunct Professor at the African Energy Leadership Centre, Wits Business School, University of the Witwatersrand, and is a non-executive director at Eskom and SANEA. Bruce Douglas Young is a Senior Lecturer at the Africa Energy Leadership Centre, University of the Witwatersrand.
The Conversation
The Conversation is funded by the National Research Foundation, eight universities, including the Cape Peninsula University of Technology, Rhodes University, Stellenbosch University and the Universities of Cape Town, Johannesburg, KwaZulu-Natal, Pretoria and South Africa. It is hosted by the Universities of the Witwatersrand and Western Cape, the African Population and Health Research Centre and the Nigerian Academy of Science. The Bill & Melinda Gates Foundation is a Strategic Partner.