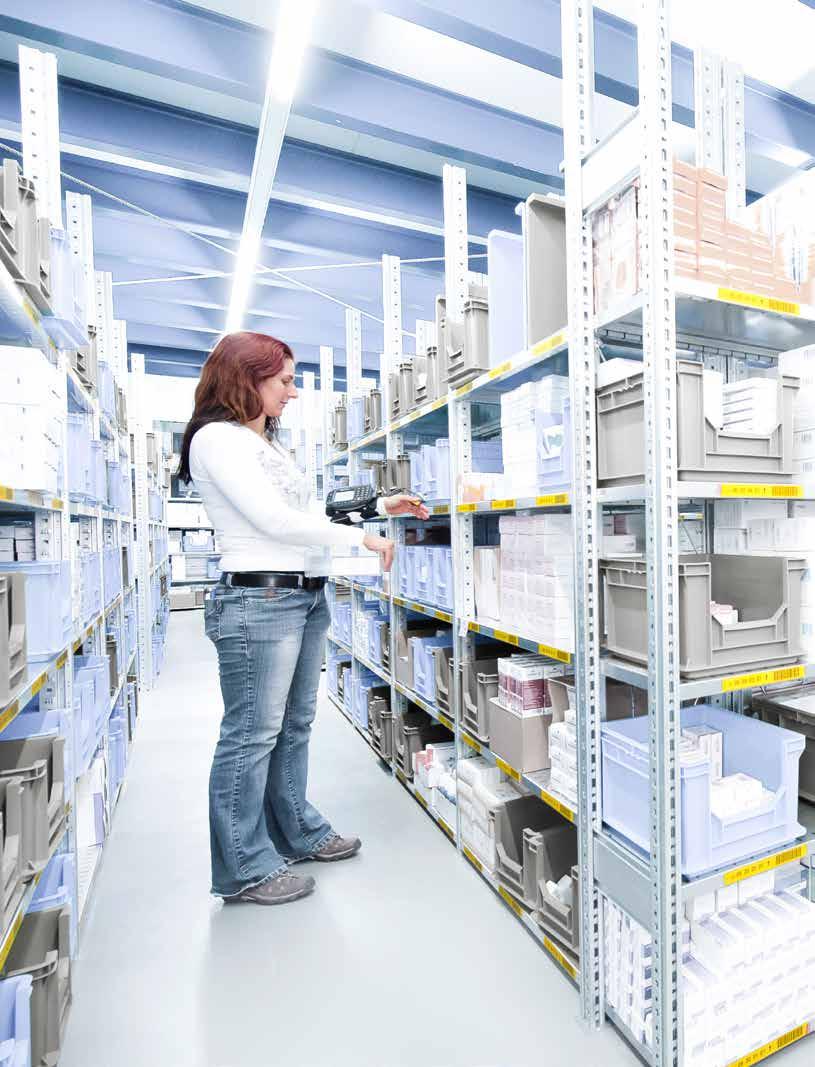
15 minute read
SSI Schaefer
A resurgent SSI SCHAEFER savours the sweet scent of success
The logistics titan emerges resilient post Covid, doubling down on ingenious technologies and cutting-edge automation
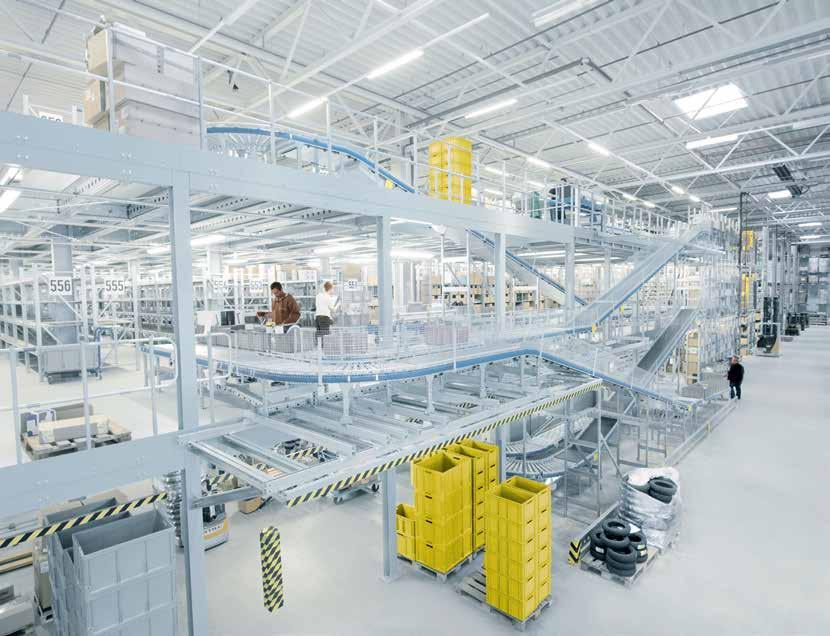
Following its lead in innovation and its total commitment to and involvement in intralogistics, SSI SCHAEFER stellar performance bears testimony to its leadership role and the confidence reposed by its growing clientele. Now the revitalized company has made major inroads in the pharmaceutical, perfumery and mass consumer products.
More than eight decades ago, the firm foundation was laid for the SSI SCHAEFER Group in its native Germany opening new vistas and reshaping the future of the logistics and supply chain industry.
SSI SCHAEFER’s pre-eminent products are omni present across the globe, providing efficient and competent solutions for all of the customers’ requirements. The company is one of the world’s largest full-range suppliers and component manufacturers. Its portfolio encompasses logistics systems, storage and conveyor systems, workstations, logistics software along with waste engineering, and recycling.
The SSI SCHAEFER Group is the world’s leading manufacturer of storage and logistics systems. The company maintains an excellent international position with five competence centers in Germany, Austria and Switzerland along with numerous production facilities and a total of more than 70 branches worldwide.
In an exclusive and expansive interview with Global Supply Chain, Carsten Spiegelberg Managing Director, Middle East & Africa, SSI SCHAEFER, held forth on wide-ranging issues related to the company, how the company was able to overcome and buck the trend during the pandemic; its forays in the pharma and fmcg sector in the region’ case study narratives and his vision and road-map for the future.
Global Supply Chain (GSC): Briefly, what are key takeaways / broad observations / general comment of the fallout of the Covid-19 pandemic from the SSI SCHAEFER corporate perspective? Carsten Spiegelberg (CS): The Corona pandemic has accelerated the boom in e-commerce, not only in the generic e-commerce and online retail but also the online ordering of healthcare products, OTC (over the counter) and prescriptions drug alike. This has a major impact on logistics (same day delivery) and leads to an increasing demand for automation solutions. Now, new challenges for warehousing and material handling are steadily emerging.
To be able to process e-commerce orders quickly and efficiently in tandem with stationary businesses, companies have been increasingly relying on distribution centres and omnichannel order fulfilment centres for years. Scalable, highly flexible systems with a customized degree of automation are in demand, turnkey from a single source and upgradeable and expandable at any time, including software and after sales services.
In this environment, SSI SCHAEFER stands by small, medium-sized, and large companies as an intralogistics partner with many years of experience and supports them with modular, scalable and sustainable solutions and services for specific e-commerce and omnichannel requirements.
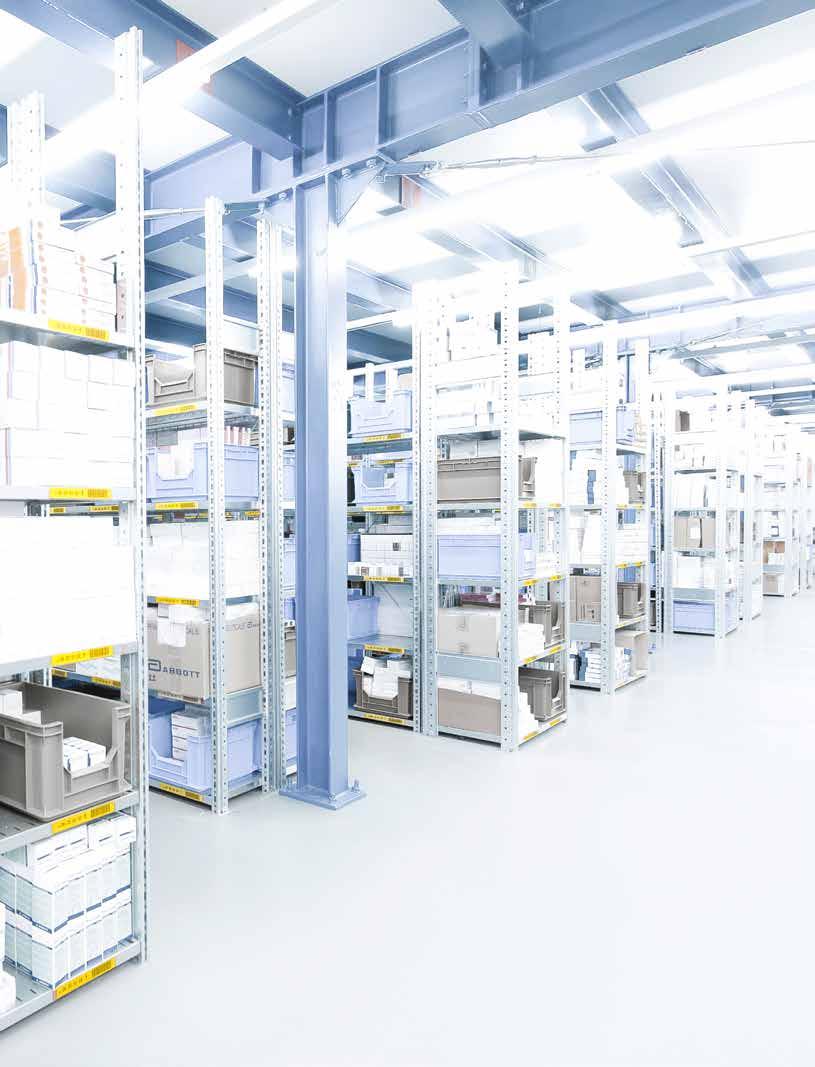
GSC: How is the onset of the pandemic impacting your regional and global operations? CS: We live in uncertain times of pandemic and wars, which from a macroeconomic perspective are leading to supply chain disruptions, increased raw material prices, or shortage of particular electronic parts and other factors, thus heavily influencing both production and implementation of automated intralogistics warehouse devices and installations.
Dealing with such crises seems to become the ‘new normal’ - that is, companies need to become more flexible to be able to react quickly to changing conditions.
With our broad scope of supply of manual, partially and fully automated systems, logistics software and customer services, we at SSI SCHAEFER cover a highly complex value chain of intralogistics. This includes, among other things, metal working and processing, plant engineering
with all electrics, electronics, machine control and software, and very many process steps in between.
As a result, we are broadly affected by the current supply situation, but we have the advantage that we can move comparatively flexibly in this market thanks to our decades of expertise and have so far largely been able to keep our delivery promises to the customer.
Fortunately, for many years we have relied on clear production planning systems and regular coordination between the units to keep and implement our promises to our customers.
Now we are seeing the value of these costly coordination programmes. If we hadn’t practiced this for years, we would have major problems meeting customer expectations and delivery schedules, as many other companies do today.
We need to ensure that we can manage our supply chains and carefully balance their benefits and risks. A ‘global at any cost’ procurement strategy is often not the most cost-effective solution. Especially in the current times, it is evident that a company is often more resistant to crises if its supply chains are not too wide-ranging.
Especially since the latest developments in freight costs put the calculations for sourcing from Asia in a different light. In some cases, we are also seeing customers bringing production back to Europe because, on the one hand, costing allows it and, on the other, sustainability is now more than just a marketing slogan.
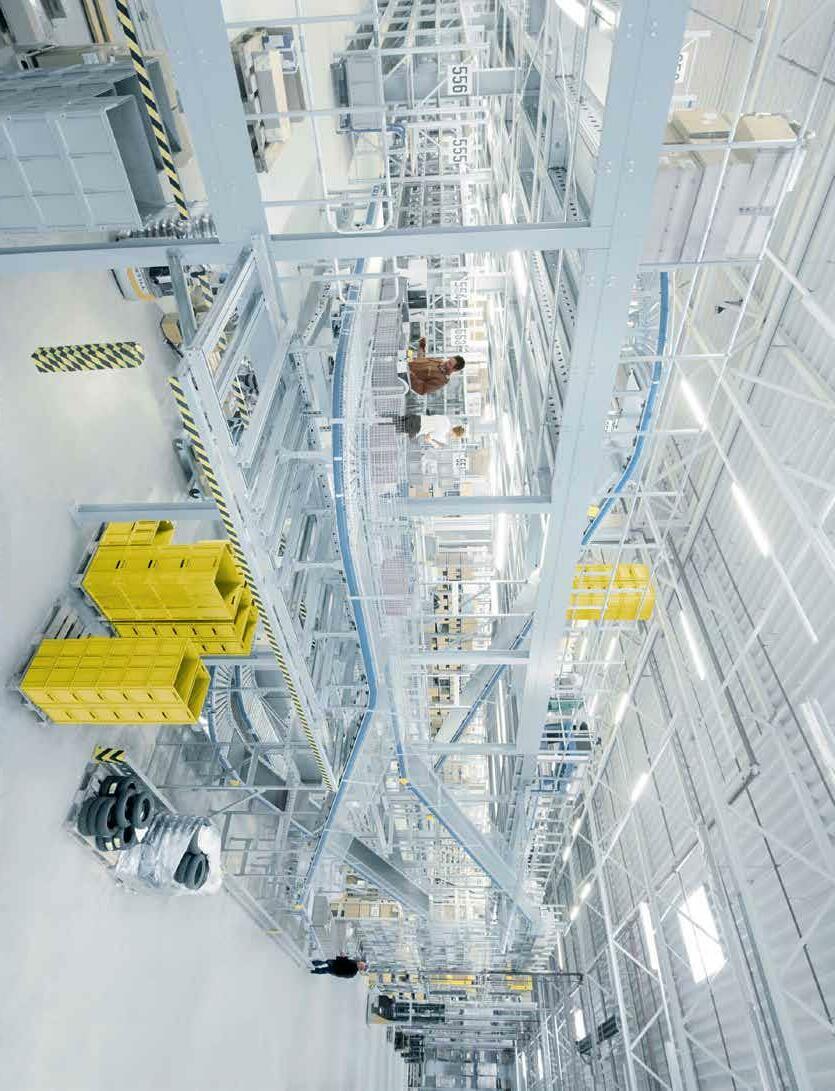
GSC: Tell us about the SSI SCHAEFER footprint in the Pharma sector? What broadly is your contribution? CS: Our approach to any client’s request is to think in terms of complete system solutions, we want to give way for growth, this is what I think is the main contribution SSI SCHAEFER has to offer to their clients’ success story.
The pharma and cosmetics sector has seen a stable growth trajectory even before the pandemic and I think the best word to describe the domain is “agility”. The retailers and manufacturers must constantly re-think their operations and strategies in order to meet the market requirements. This has a cascade effect on how we approach a client’s challenge.
In addition to fast order processing for same-day or next-day delivery and covering order peaks, zero error tolerance and complete item tracking have top priority in the healthcare sector to ensure essential client satisfaction. These requirements pose challenges for the intralogistics of manufacturers and distributors.
SSI SCHAEFER has a broad range of products and solutions covering the entire internal material flow and we are continuously expanding this range to adapt to changing markets and requirements. These products then form the foundation for system solutions specifically developed to meet individual requirements more effectively, efficiently, and sustainably. for a dry warehouse, adding 25.000 pallet positions to the site.
The facility serves as one of the largest healthcare storage hubs in the region and beyond, incorporating eight configurable cold chambers each capable of storing pharmaceutical products at temperatures from +25°C down to -26°C.
The hub houses Covid-19 vaccines used in the UAE’s vaccination programme and has also facilitated the storage and distribution of over 260 million vaccine doses to over 60 countries around the globe through the HOPE Consortium, an Abu Dhabi-led public private partnership which AD Ports Group is a founding member of. The facility can hold over 120 million vaccines at any time, positioning it as the core product storage and distribution center in the fight against the pandemic.
Founded in 1982 in the UAE, Al Khayyat Investments (AKI) is a family-owned conglomerate regarded as a pioneer in several industries in the Middle East, delivering profitable partnerships through specialized industry expertise.
AKI enjoys sustained growth across multiple sectors, including Distribution, Retail, Healthcare, Contracting, Fitness & Leisure, and Automotive. Being one of the fastest growing pharmaceuticals, medical, and consumer distributor in the region, AKI handles specialty products, prescription drugs, OTC, skincare products, and is a leading supplier of hi-tech medical equipment in the UAE, frequently being the first to introduce cutting-edge products to the market.
AKI implemented a versatile LS600 mezzanine system that provides both storage area and a working surface. It installed a 3-level mezzanine that provides high-density storage for various SKUs, while utilizing the available plot size and height of the warehouse.
The project’s target was to find a system that allows AKI to run a highly efficient operation and deliver on their business priorities, all while optimizing its facility space for maximum storage capacity. The ability to meet all these objectives were among the reasons why AKI worked with SSI SCHAEFER MEA on this project.
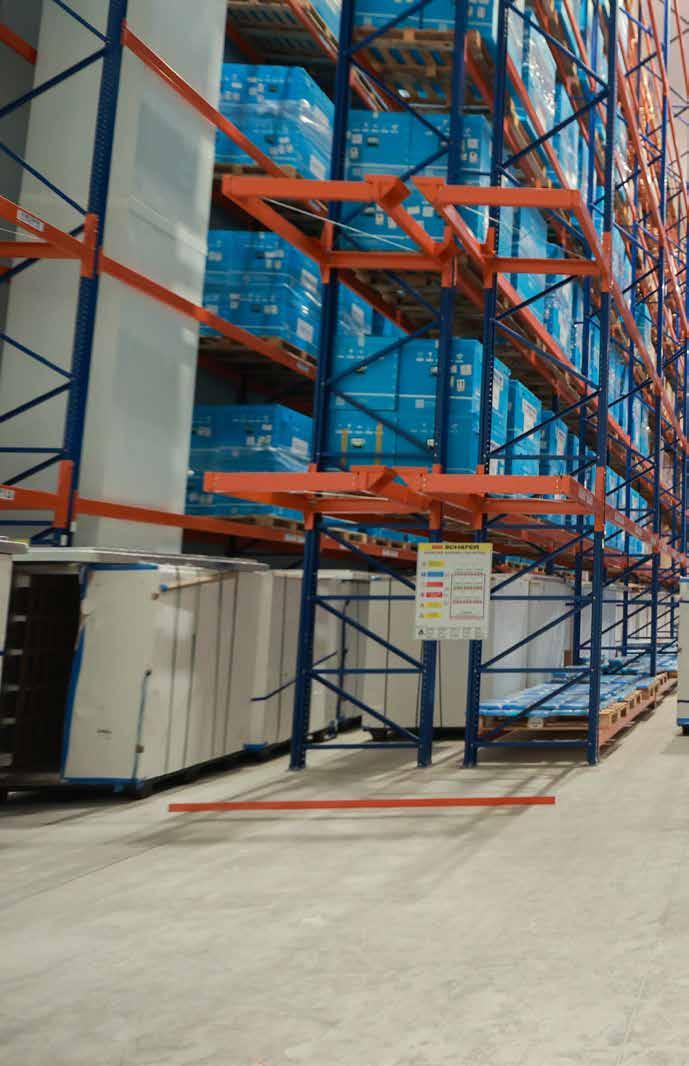
GSC: Enumerate (briefly) one or two possible case studies (as a case in point) to highlight your enhanced role for your foray in the pharma segment? CS: Our goal at SSI SCHAEFER is to assist our customers to improve their business performance, through intelligent processes. In 2020, when AD Ports Group’s Logistics Cluster was developing its cold and ultracold healthcare storage and distribution hub in KIZAD, SSI SCHAEFER supported their logistics demands through an in-house designed, state-of-the-art storage system. For the 19.000sqm hub, SSI SCHAEFER manufactured and delivered Interlock 600 VNA wire guided pallet racking system,
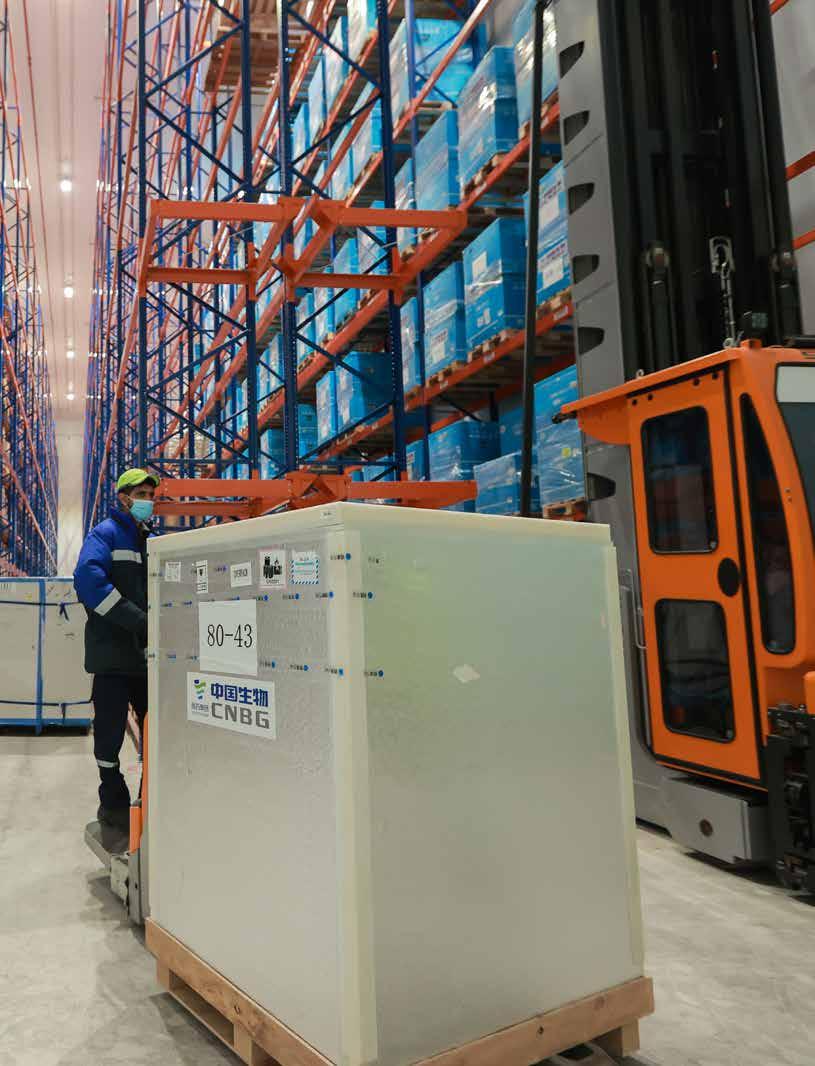
SSI SCHAEFER has extensive knowhow and innovative technologies for the pharmaceutical and cosmetic supply chain. This includes manual as well as semiautomated and fully automated solutions.
When the perfume and cosmetics wholesaler Perfume Unlimited LLC needed a system that would cater to their growing demands of the current market, as well as supporting future volumes, they approached SSI SCHAEFER for a tailor-made plan to provide an omni-channel solution for bulk and e-commerce order processing.
For the 17 years old Dubai-based company we implemented a zone routing conveyor system with pick by light technology, which serves a warehouse of about 8,000 sqm holding more than 15,000 SKUs. This is a total system solution consisting of heavy-duty pallet plus box picking solution connected to a mezzanine with a semi- automated piece picking system. GSC: Why is the pharma sector of interest to SSI SCHAEFER and what potential growth prospects do you foresee? CS: Fragile products, complete implementation and complex conditions place high demands on intralogistics operations for both manufactures and distributors within the Healthcare & Cosmetics industry.
Declining inventory levels mean an increase in frequent deliveries – even with small volumes. Quick delivery expectations as well as a significant increase in online business, further increase pressure within the logistics chain. The Healthcare industry expects maximum reliability, security, and extremely high picking performance at peak times.
With over 40 years of experience in pharma distribution, SSI SCHAEFER is well positioned to tackle the challenges that come with high customer requirements, order peaks caused by multiple orders per day, diversity in product shapes, need for differentiation between OTC and prescription goods and complete traceability for quality assurance and security, validation and certification of software solutions (GDP, GMP) and the integration of value-added services and batch picking and sorting for mail order pharmacies.
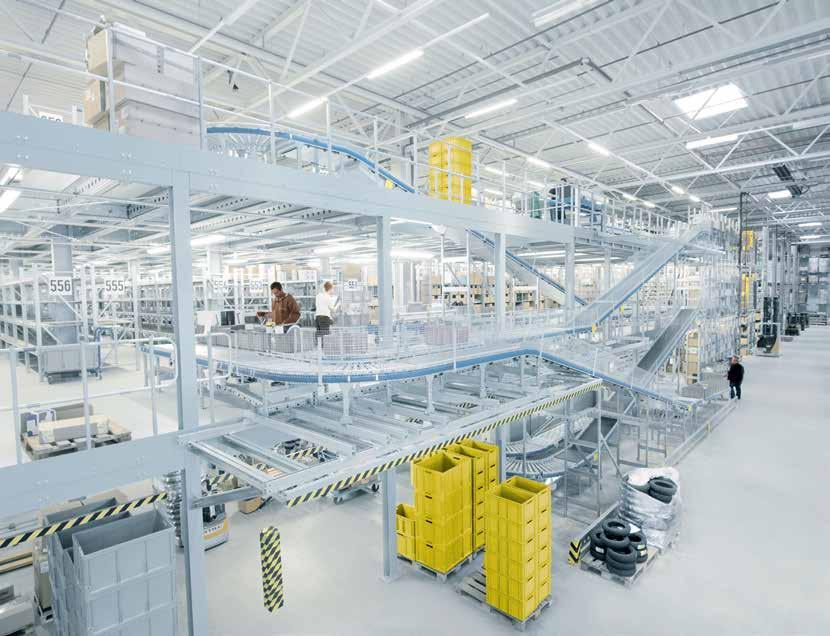
GSC: What are the critical points of a warehouse for pharmaceuticals and why are they vital? CS: Very short throughput times are required from order receipt to delivery, which means that fast and efficient order picking must be guaranteed. Systems should also be designed so that, in addition to normal picking operations, they can also cover enormous order peaks within a day.
Due to the legal requirements of local administrations and guidelines, processes must also be guaranteed that enable complete traceability in warehousing, order
Carsten Spiegelberg had been appointed the new Managing Director of SSI SCHAEFER Middle East & Africa earlier this year
Following a new office opening this year, the material handling system expert continues to build on its strategy of providing the most reliable and accessible warehouse logistics solutions to the market.
SSI SCHAEFER appointed a new Managing Director with a proven track record to drive the company’s growth and direction.
The new Managing Director, Carsten Spiegelberg will take up the role with immediate effect and will focus on further developing and expanding SSI SCHAEFER’s state-of-the-art warehouse logistics solutions and cutting-edge technology to meet the requirements of MEA’s market.
Carsten brings with him a wealth of international experience in warehouse Logistics Automation and Infrastructure, gained from over 20 years of managing the business in ASEAN region, Australia, and the Middle East. His insights include technology development, sales and marketing, business development, project, and asset management.
“I am very excited to join such a competent and capable team in Middle East & Africa, to play a key part in shaping and delivering our new strategic priorities for the years ahead. SSI SCHAEFER has been very successful in combining German Technology with the needs of the local market and has become a frontrunner in Intralogistics.” observed Carsten on his appointment.
Carsten Spiegelberg joined SSI SCHAEFER Singapore in March 2000 and has contributed to many successes in the Automation business in APAC and MEA. He started as a Regional Manager in the region and was the cornerstone in the setting up of the KLS factory in Malaysia and multiple Automation Teams in the area.
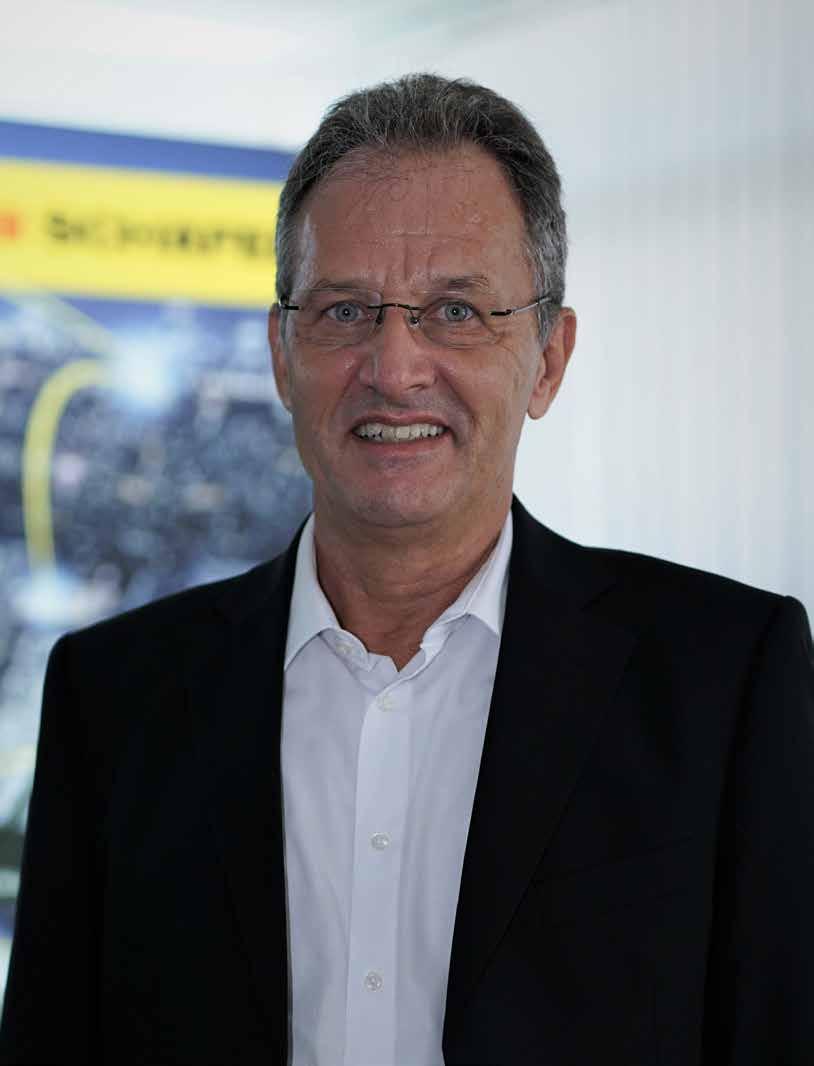
picking and delivery. Compliance with the legal requirements for tracking & tracing guarantees the necessary patient safety and can make up the decisive competitive advantage.
At SSI SCHAEFER, we are committed to the topic of safety and offer complete documentation of prescription drugs throughout the entire warehouse. This traceability ensures protection against counterfeiting and ensures the reliability of the supply chain. In addition, quality controls and compliance with certain processes are very important to ensure safety. For example, with separate storage areas for refrigerated items or toxic items.
GSC: Which solutions for tracing within such a warehouse are available from a technical point of view and are practicable for pharmaceuticals? CS: SSI SCHAEFER offers a comprehensive portfolio of manual to partially and fully automated solutions for capturing serial numbers, batch numbers and expiry dates. In addition to the manual scanning of products using RF picking (radio frequency picking), we offer our ergonomically optimized Advanced Pick Station, a goodsto-person workstation system for picking directly into order containers and boxes with an integrated product scan. The Advanced Pick Station offers high picking performance and can be connected to an automated warehouse.
With the A-Frame, products can be picked automatically and verified in connection with a directly connected Product Verifier. Each individual item is aligned and recorded from all six sides by highly sensitive cameras. Any reading errors are marked and affected containers are automatically ejected to a control station. The Product Verifier is many times faster than conventional, manual verification and enables seamless tracking and tracing of pharmaceutical items.
SSI SCHAEFER offers a fully automated robotic solution for picking, identification, documentation, and control with a modern piece picking application. The high-performance piece picking robots for automated individual piece picking can be seamlessly integrated into overall logistics systems.
They cover a wide variety of order structures and deliver consistent performance regardless of environmental conditions or ergonomic requirements. Integrated cameras record each individual product and at the same time ensure 100 percent verification.
Automated quality control of customer orders picked manually, partially or fully automatically is carried out with the Order Verifier. In a single step, the items are identified, counted, checked, verified, and documented - regardless of whether it is a cubic or cylindrical shaped item, a blister pack, tube, or bag. As an end-of-pipe solution, the Order Verifier can be easily integrated into existing warehouses.
In addition to tracking & tracing applications, we serve the entire range of manual, partially and fully automated products and systems to meet individual customer requirements with tailor-made solutions. GSC: How can the three pharmaceutically relevant temperature zones (-25°C, +2°C to +8°C and +15°C to +25°C) be integrated into this system and controlled? CS: In a classic distribution center for pharmaceuticals, temperatures are above zero. All our systems and solutions for fulfillment, order picking, handling and verification are designed and used for this. In addition, all our storage solutions required for cold room storage are designed and used to work in these particular environments.

GSC: Can customers integrate the SSI SCHAEFER software solutions for controlling the transport and conveyor systems into their own IT structure? CS: Our software solutions are the backbone of every reliable and flexible warehouse. The standard logistics software WAMAS®, which we developed ourselves, combines all the customer’s intralogistics components into one intelligent system and is a modular solution that can be seamlessly integrated into existing intralogistics. It is the link in the logistics chain from goods receipt to storage and order picking to delivery.
The WAMAS standard software includes a comprehensive range of functions, from warehouse management to the material flow system, and is also compatible with all SSI SCHAEFER components and interfaces to third-party providers. The software enables serial numbers and batches to be traced - which is particularly important for this industry, as well as checking the expiry date and continuity of the cold chain.
With WAMAS® Lighthouse, the customer monitors, controls and optimizes the productivity of the entire system. As a ‘central point of information’, the software solution bundles all the warehouse information and makes it available on the move and in real time in the form of easyto-understand analysis dashboards.
WAMAS Lighthouse is an open system that integrates the data from all existing IT and control systems in an intralogistics facility. Cutting-edge technologies and smart interface concepts enable every connection - from the automation level to the merchandise management system. It is the tool for data collection, integration and visualization and provides employees with the right information.