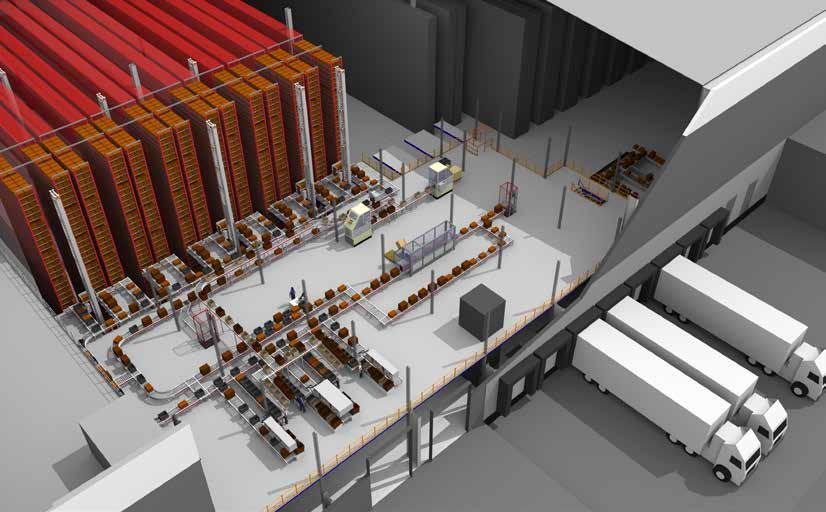
6 minute read
Swisslog
E-commerce fulfillment is a key competitive advantage and a pivot to success Swisslogs work on the site in East Midlands will commence in March 2021
Over the last few years, as e-commerce sales have increased and customer expectations have shifted, there has been a steady race to move fulfillment closer to the customer, affirms Alain Kaddoum, General Manager, Swisslog Middle East.
Today’s consumer has a four-pronged fulfillment mandate: fast, free, sustainable, and branded shipping. Globally, 64% of consumers want their orders shipped for free, while peak-level ecommerce and strict same-day shipping cutoff times have made it difficult to meet rising customer demands.
Something once as innovative and de rigueur as two-day delivery has led to next-day delivery, which is quickly becoming obsolete as consumers demand same-day delivery. In a recent survey, 67% of U.S. consumers expect the same-, next-, or two-day delivery, while 72% of global consumers want brands to use sustainable packaging.
With the cost to fulfill orders soaring, brands must turn fulfillment into a strategic asset. Fulfillment must be smarter, closer to the consumer, and automated.
Free shipping at a premium
Proprietary data from Shopify shows the number of brands offering free shipping has increased 5.3% since the pandemic began. To answer consumer demand while maintaining profitability, brands are setting free-shipping thresholds.
A full 65% of consumers check free-shipping thresholds before adding something to their cart. Interestingly, free shipping is just the tip of the iceberg: 39% of U.S. shoppers expect two-day shipping to be free, while the same-day shipping market in the U.S. is forecast to top US$ 9.6bn in 2022.
This trend has accelerated during the Covid-19 pandemic, especially as more consumers become comfortable with online ordering of perishable items and groceries. One of the significant changes in supply chain strategies we are seeing as a result of this is the rise of fulfillment centres that bring fulfillment closer to the consumer.
Warehouse / Distribution Centres
Typically, one of the dominant components in a company’s supply chain is the large warehouse or distribution centre that acts as a central hub from where products are shipped to retail outlets.
These are now being joined by a network of fulfillment centres that focus on localized, direct-to-customer service.
They are designed to primarily get online orders to the customer quickly. These facilities have become a powerful tool in conquering the last mile and helping maintain a pleasant, seamless customer experience.


Micro-fulfillment centres
One relatively new type of fulfillment centre that is gaining a lot attention is the micro-fulfillment centre. Micro-fulfillment centres are a simple and compact lastmile delivery solution that can be quickly deployed anywhere, especially where real estate space is limited or cost-prohibitive.
While they are generally smaller in size than regional or metro-fulfillment centres, they can be virtually any size, providing the needed flexibility to meet customer needs and fit nicely into a wide range of supply chain strategies.
Micro-fulfillment centres can be built as a standalone facility, or built inside or bolted onto an existing location to expand fulfillment capacity, especially within limited footprint. They are also well suited for automation technology, bringing it to the lowest supply chain level.
While they can be used in a number of market segments and industries, micro-fulfillment centres have gained the spotlight as a result of the accelerated demand in e-grocery fulfillment. Microfulfillment has shown to be an ideal solution for streamlining e-grocery fulfillment.
For instance, Swisslog is working with H-E-B to deploy multiple automated micro-fulfillment centres to support the supermarket chain’s curbside grocery pick-up at more than 40 stores in the San Antonio area. The new micro-fulfillment centres feature AutoStore empowered by Swisslog’s SynQ software, pick stations and integration.
Swisslog CarryPick
Integral component of supply chain
Micro-fulfillment centres are quickly becoming an essential part of the supply chain. They hold much promise for helping reduce delivery costs and shorten the last mile and the time to consumer.
They are also an ideal solution for fulfilling online orders for curbside pickup. With the right approach and automation technology, they can help you meet changing expectations and enhance customer experience.
Swisslog has a comprehensive portfolio of solutions to meet the needs of retail, e-commerce and e-grocery customers. From large distribution centres to smaller fulfillment centres, there is a wide range of technologies available to address the today’s challenges and demands.
Brands have little choice but to creatively re-imagine fulfillment. In the first half of 2020, ecommerce spurred a blistering 51% increase in large fulfillment centre demand. Around the world, businesses are prioritizing fulfillment to fight rising costs and meet consumer expectations.
Swisslog AutoStore

Alain Kaddoum is General Manager, Swisslog Middle East, a company which is shaping the future of logistics automation and transforming warehouses and distribution centres to achieve maximum efficiency, flexibility and agility.
The brand’s portfolio consists of different key technologies, such as conveyor systems, ASRS, AGVs, shuttle systems, monorails, robotics and warehouse management software.
RM Resources consolidates supply chain with Swisslog automation The Tornado solution will feed ergonomic goods to person stations

Swisslog selected to build a new automated distribution centre for education resources provider
RM Resources, the established provider of education resources for early years, primary schools and secondary schools, has selected Swisslog’s Tornado miniload cranes to power its new build warehouse in Hucknall, East Midlands in the UK.
RM Resources develops and supplies resources which help bring the curriculum to life in both UK and international markets via its two brands, TTS and Consortium.
Automated material flow
Partnership
Together with Swisslog and the storage density of its system, RM Resources will be able to consolidate its warehouse operations in the UK, which is currently spread across four different sites. As part of the KUKA Group, Swisslog covers the entire automation value chain with robotic and data-driven automated solutions for forward thinking businesses.
“This project merges four warehouse operations together, while simultaneously allowing sufficient space for RM Resources to expand in the future,” remarked Shane Faulkner, Head of Sales, Swisslog UK.
Transportation throughout the solution will be facilitated by Swisslog’s QuickMove conveyor. Goods will be conveyed to the Automated Storage & Retrieval System (ASRS), provided by a seven aisle Swisslog Tornado miniload solution. The ASRS will store cartons or totes double deep providing dense but rapidly accessible storage.
Single point fulfillment
The Tornado solution will feed ergonomic goods-to-person stations, each allowing up to six open orders to be picked at a time thereby facilitating an increased hit rate, improved order fulfilment time, and reduced throughput requirement in the system. With a single level pick-to layout, each goods-to-person station will benefit from one-touch fulfilment, enabling RM Resources to dramatically shorten lead times.
Swisslog SynQ software will provide all the necessary WCS functionality, while also integrating with RM Resources’ WMS & ERP systems. SynQ will deliver greater stock accuracy, as well as increased visibility of order progress. It will also provide RM Resources operators with the ability to pick from available new stock immediately as it enters the warehouse.
“We are delighted to be progressing with our plans to consolidate our warehouse portfolio, which will deliver a number of efficiencies across the business as we move to one automated site,” commented Monique Louis, Managing Director, RM Resources.
Swisslog’s work on the site in East Midlands will commence in March 2021 and is due to complete at the start of 2022, to allow RM Resources to work on the curriculum line before the following school year.