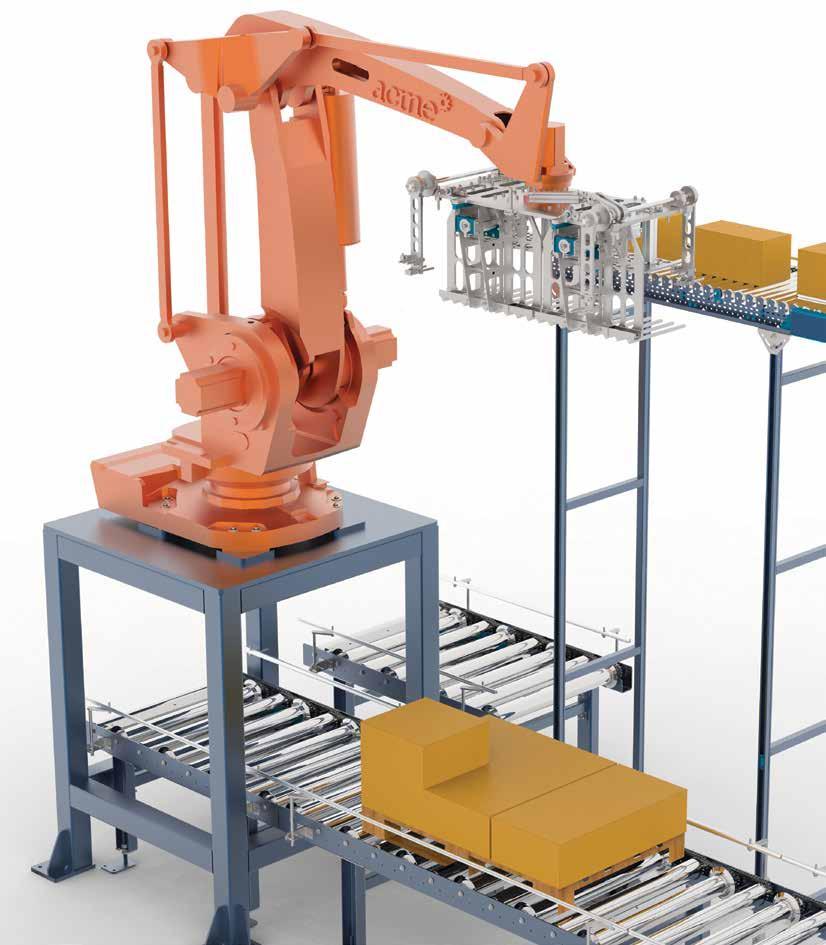
6 minute read
ACME
Improving efficiency through robotics
Investment in Robotics and Automation gaining ground globally and regionally


It’s no secret that the pandemic has accelerated the recognition, adoption and embrace of automation and digitalization across multiple sectors particularly manufacturing, retail and e-commerce. Acme Intralog, a leading regional provider of material handling & warehouse automation solutions, is reporting new breakthroughs and heightened business, bucking trends even in the face of the pandemic.
More and more companies around the globe enhance their manufacturing process and supply chain to improve their ability to react to disruptions and new safety and distancing regulations while remaining competitive.
Based on the 2021 MHI Annual Industry Report, 53% of global companies are increasing their investment in Robotics & Automation, which represents the category with the highest substantial investments planned.
Acme, a leading regional developer of material handling solutions, is observing a similar trend in the Middle East, yet at a slower pace.
Manual labor still has a stronger foothold in logistics and material handling here than in some regions of the world. We therefore see bigger companies embracing the trend for automation a lot faster than smaller ones.
Bigger companies, particularly manufacturers and retailers, often already have some automated solutions along their supply chain yet tend to face a bottleneck when it comes to their end of line.
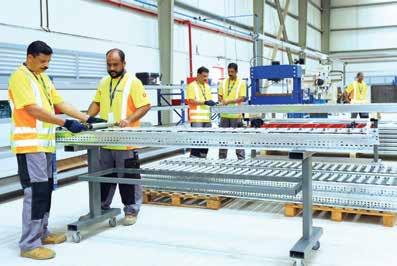
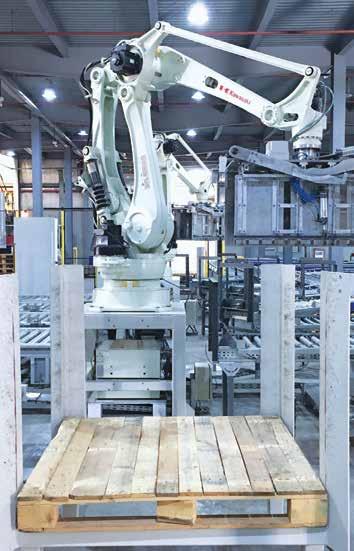
Robotic palletisation
This is where robotic palletisation can fill the gap and handle a significantly higher throughput faster, more accurately and safer at a lower cost than conventional palletisers or teams of employees working in multiple shifts.
A lot of smaller companies are not yet on board with automating their end of line as their throughputs are more manageable and probably also due to the perception that a substantial investment is required to automate manual processes, particularly when it comes to robotic solutions.
Yet robotic palletisation can provide even smaller companies with significant competitive advantages. The investment for a
About Acme
Acme Intralog Fzco is one of the leading material handling & warehouse automation solution providers in the Middle East, developing tailor-made approaches for complex needs.
Founded in 1975 with its headquarter in Dubai, Acme optimizes intralogistics for customers across multiple industries, including retail, e-commerce, FMCG, food & beverage, pharma.
Their offering ranges from solutions for factory automation, sortation systems, pallet and tote storage and retrieval solutions as well as industrial automation components. Besides having a full-fledged manufacturing facility located in Jebel Ali Free Zone, Acme has a dedicated service team that provides 24/7 life cycle service and maintenance support throughout the GCC.
As part of the industrial automation components vertical, Acme has established strong partnerships with leading global suppliers for years, bringing their technology to our region.
basic yet efficient robotic solution typically pays off within 3.8 years on average, for larger installations this period shortens. As a rule of thumb, if a robot replaces just 3 headcounts, the return on investment is already higher when implementing automation.
Robotic palletisation is not just about the robot itself, which a number of companies offer as is. It is the system around the robot, using the right gripper and connecting conveyors, that create real competitive advantages.
Customization
Being a system integrator, for Acme customization is key. None of their solutions are off-the shelf but each is tailored to the specific requirements and needs for each client, taking into account throughput, capacity, type of products and the expected return on investment.
The ultimate goal is to help regional businesses to truly optimize their supply chain by developing a solution through robotics, not just a robot alone.
Thanks to the vast opportunities for customization, robotic solutions can well integrate into already existing systems. And even after initial installation, there is flexibility. When a company changes their product line at any point in time, Acme’s systems can be adapted to product ranges with different weight / size or special features a lot easier than other solutions and at a minimal cost.
Acme’s team has recently installed 2 palletising robots for one of their clients, Lubrex, increasing their end of line productivity by 210%.
Lubrex facility
Being a leading manufacturer of high quality automotive, industrial and other lubricant solutions in the GCC and globally, Lubrex’ facility produces close to 200 types of products that come in 200 different shaped and sized packaging due to their individual specific handling requirements.
Until recently, these products had been palletised manually, allowing the handling of 30-35 pallets an hour best case at full capacity.
Lubrex decided to automate their end of line for two main reasons: to align the throughput of the palletisation with the much higher production capacity as well as to increase safety. Acme’s
solution which combines high speed roller conveyors and the use of robots with high quality grippers have increased the palletisation capacity to 80-90 pallets per hour.
They are also significantly increasing safety as the conveyors used are built with accumulation zones, which prevent boxes from touching each other and therewith avoid damage and leaks.
In-house tests

This solution, like all of Acme’s systems, was first designed, manufactured and tested in-house before being built-up in Lubrex’ facility. This way, the customer could review their new technology and verify it suiting all their needs without any disruption of the ongoing production – by providing just one pallet of their products for testing real scenarios.
With only two robots, Lubrex is now able to better fulfill their demand and justify their production capacity, while drastically reducing manual labor in heavy duty jobs.
And Acme is close by for any support if needed, offering different types of maintenance contracts depending on any customer’s preference. The most common choices are warm-up support, where Acme is on site for the first months after installing a system, regular preventive maintenance or having a permanent person on ground who is operating the system.
Innovative solutions
For other customers, Acme is currently designing and installing dedicated solutions as well. While requirements differ depending on industry and type of products being handled, robotic solutions can cater to all and solve challenges for any client. Just to name a few examples: High capacity: FMCG companies typically produce a vast quantity of products every day, operating 24/7. This requires approximately 2-3 shifts and a lot of people per day when palletising manually.
A robotic solution can match the production capacity better, at higher speed, while also enhancing safety standards.
Hygiene factors: while companies within the food & beverage industry often have similar needs as FMCG, safety and hygiene play a big role as well, maybe even more so since Covid.
Particularly when palletising liquids or fragile goods, robots are a lot more accurate, preventing damage and therewith avoid interrupting the process for cleaning after a leakage.
Size & weight challenges: some products across different industries are hard to palletize manually, for example 5 gallons water cans or heavy products that come in sacks like cement / rice. Robotic solutions improve the process tremendously; they only differ from other solutions in terms of the model of the robot, gripper and conveyors.
Special care products: when handling chemicals, lubricants as in Lubrex case or toxic products, the safety for employees & maintaining packaging fully sealed is key. The precision in picking and moving that robots offer allow for highest safety standards.
No matter the industry or products, palletisation can be a bottle-neck in our region. Robotic systems tailored to individual needs are the way forward that allow both big and smaller companies to optimise their end of line significantly in order to be more competitive and thrive.