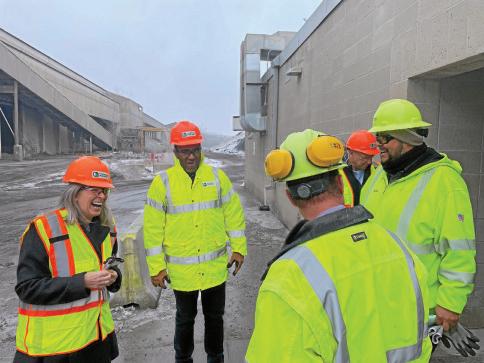
2 minute read
Mason City Cement goes green
from Progress 2023
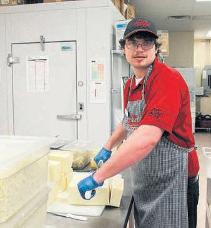

Advertisement
Grinding the burned product, known as “clinker,” together with some 5% gypsum to control the time of set of the cement.
MATTHEW REZAB
Globe Gazette
Mason City Cement, in collaboration with parent company Heidelberg Materials, is taking steps to reduce carbon dioxide emissions from its cement plant.
Plant Manager Patrick Karamaga said the company is committed to spending $4 million to $5 million in the next few years to get the company to using 50% alternative fuels by 2026.
David Perkins, vice president of government affairs and communications North America for Heidelberg, said the company is committed to generating 50% of its revenue from sustainable products by 2030. Perkins and other company officials said they plan to reduce carbon dioxide emissions by 50% by 2030.
“Obviously, we want to be proactive as a company and really try to lower our carbon footprint, really trying to lower our energy intensity while recognizing we have to be competitive,” Perkins said.
Germany-based Heidelberg Materials employs more than 50,000 worldwide and about 8,500 in North America at its various businesses, including about 120 in Mason City.
Reserves for creating cement in North Iowa are believed to be able to sustain production for another 75 to 100 years.
“That’s the thing about our industry is we’re really a longterm industry on the cement side for sure because of the investment that’s required to produce,” Perkins said.
Perkins said the process of making cement includes a step that turns the limestone into lime. That process — called calcination — produces CO2. Perkins said that’s about 65% of emissions from cement.
According to Encyclopedia
Britannica, There are four stages in the manufacture of portland cement:
Crushing and grinding the raw materials.
Blending the materials in the correct proportions.
Burning the prepared mix in a kiln.
As a whole, Heidelberg plans to earn 50% of its revenue from sustainable products by 2030. According to the company’s webpage:
It focuses on heavy building materials.
It is committed to generate 50% of revenue from sustainable products by 2030.
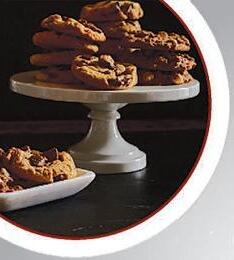
It is committed to reducing CO2 emissions by almost 50% by 2030.
“These are things we’re doing voluntarily, Perkins said. “We realize that the marketplace is starting to pull for this and we want to get out in front of this.”

Perkins said there are things that could be done 100% of the time that are not being done all the time now. He pointed out CO2 content can be reduced, but some materials are reusable. He said concrete is fully recyclable by crushing it, screening it and putting it back into production.
Perkins also said the company has been working with MIT and other institutions around the world to come up with solutions to become cleaner. He said they’ve learned 25% to 30% of the CO2 created when concrete is produced is reabsorbed into the product itself.
Perkins said cement, being produced on the North End since 1911, can sometimes be a misunderstood product.
“Cement is really what holds everything together,” he said. “Cement and concrete, you always here those two terms, and sometimes they’re used interchangeably. Cement is like flour to a cake, it holds everything together.”
As of now, Mason City Cement has no plans to capture the carbon it produces as has been proposed with ethanol plants across the Midwest. But officials aren’t saying it is completely off the table in the future.
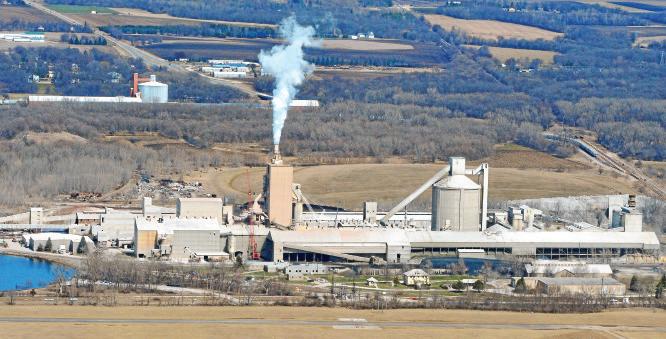