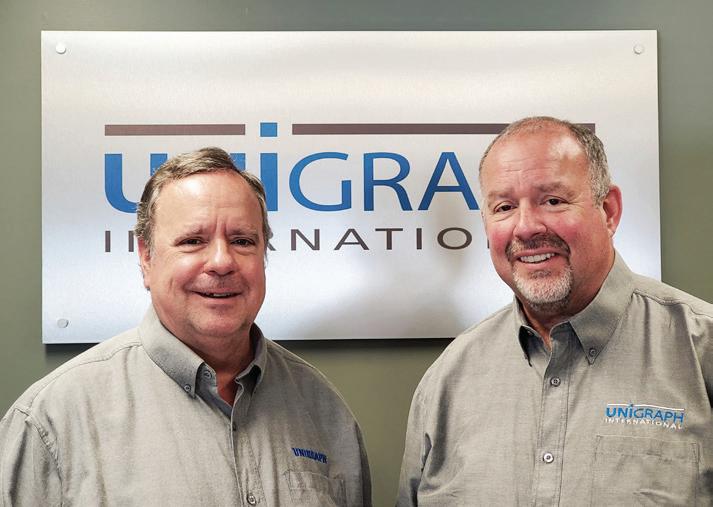
14 minute read
Print consumables update
Paper, ink, plates, blankets, pressroom chemicals – at the end of your printing day, it’s all about managing these traditional costs while maintaining on-press performance, print quality and overall productivity.
Yes, consumables do indeed “consume” – a great deal of your profits. It’s as if your primary press is bellowing every day: “feed me, feed me.” Let’s briefly review these necessities and examine how OEMs (original equipment manufacturers) are cutting the cost of consumables, improving their efficiency, and therefore adding more overall value to your operation. Pressroom chemicals Pressroom chemicals are essential to the efficient running of any offset press. These can include fountain solutions and additives, roller and blanket washes, silicones, roller deglazers, alcohol replacements, specialty products and more. A common problem, according to Canadian pressroom chemical leader Unigraph International of Delson, Quebec, is that regular press maintenance checks are often overlooked. These can affect ink/water balance, drying times, colour consistency and the ability to have repeatable, predictable on-press results. At the end of your production day, however, the bottom line should also involve another too often overlooked factor – the final cost per printed page.
Advertisement
Mike Thibault (left), VP of Technical Services at Unigraph International, with Unigraph President John Thibault.
“Specializing exclusively in pressroom chemistry for nearly 40 years, our message has been basically the same – never buy consumables, especially pressroom chemicals, based solely on a lower up-front price,” said Mike Thibault, Vice President of Technical Services at Unigraph. “You must have a guarantee of on-press performance. For example, in some cases, just changing to a better fountain solution or alcohol replacement can lower a printer’s ink bill by at least 5% at the end of the year, while also reducing paper waste.” Corporately, Unigraph has kept every employee on its payroll despite the pandemic. But it did have to make adjustments. “Myself and two other technical reps were spending two weeks a month supporting our customers in the U.S.,” Thibault said. “When that had to stop, we reverted to tech support over the phone and with Facetime. We reached out to our clients and dealers and held technical webinars via GoToMeeting. We also partnered with other suppliers such as plate and ink manufacturers, and conducted seminars together. Finally, we are extremely proud that the Thibault family has been serving the print community for almost 100 years. Our grandfather Wilbert Thibault was a stone polisher in the early 1920s. It’s a privilege to serve this great industry.” While COVID-19 adversely affected its sales in April, Unigraph rebounded quickly and is still making progress in Canada and the U.S. after expanding its production facility four years ago. “We secured our raw material supply chain with our suppliers,” said Unigraph President John Thibault. “This has enabled us to maintain full production, albeit with new health and safety protocols in place. Also, a high percentage of our customer base fell into the essential services category – such pharmaceutical, food packaging, medical and label beverages. This helped alleviate the slowdown in other markets that we serve. Overall, our continued success in the U.S. continues through our established dealer network who are doing a fantastic job.”
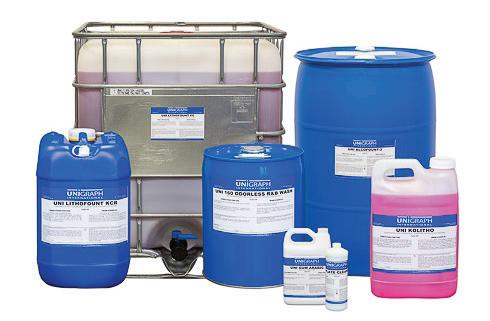
The company has even added to its line of fountain solutions by rolling out two new products to accommodate the growing variety of ink technologies. Uni Lithofount 2020 is a two-part fountain solution specifically formulated for UV/ HUV/LED inks as well as conventional inks. Uni Lithofount One is a one-step fountain solution introduced last year with tremendous success. The result was a much cleaner water system able to print huge solids while keeping reverse type exceptionally clean. Printing plates
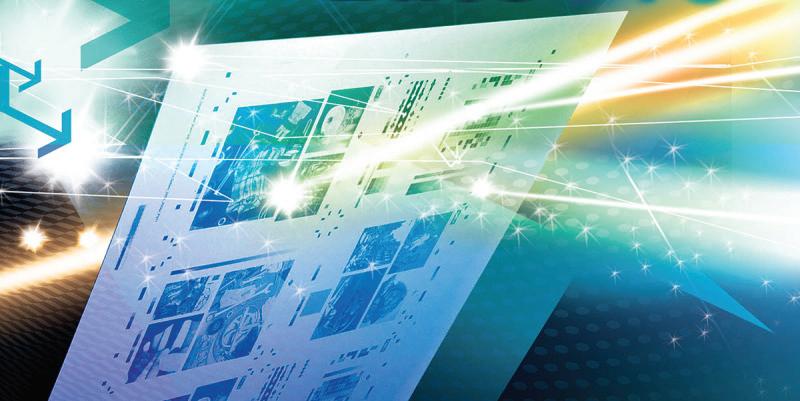
The three big players in this space are Agfa, Kodak and Fujifilm, who were forced to increase their prices 9% to 10% in 2018 due mainly to the escalating prices of raw materials (i.e. aluminum) and higher labour costs. However, the newest entry into this market in early April was Verico Technology’s Zahara Elite Waterless Plate for newspapers, sheetfed, narrow-web label, security printing and CD/DVD applications. The drop-in plate requires no exposure
adjustments, is 100% chemical-free, and uses only water for cleanout. Users simply expose, rinse and print. Not surprisingly, plates do represent a substantial cost. However, by simply placing more attention on proper plate cleaning, exercising caution when demounting, and meticulously identifying when a plate is becoming worn, savings can really add up. Realize too that each plate has different emulsion and plategraining characteristics that can affect ink/water balance, tone reproduction, dot gain, run life, handling, paper waste and overall print performance. So do your homework and find out the average processing time of a plate before you buy. Will you be able to run more jobs with it? Can last-minute changes and rush jobs be accommodated? Will it fit seamlessly into your prepress workflow? Your best bet is to discuss your needs with your supplier, then investigate other options. I’d be remiss if I didn’t mention one of the current technology leaders (and Green Leaf Award Winner) in the processfree plate arena. Kodak’s Sonora Plates go straight from the imager to the press with no processing step in between. This streamlines platemaking, reduces waste, improves productivity and saves money. In almost all cases, a printer’s current press set-ups, sequences, inks, fountain solutions and blankets can be used successfully. Sonora also works with integrated and non-integrated, conventional and continuous dampening systems, and with automatic start-up sequences.
Printing blankets
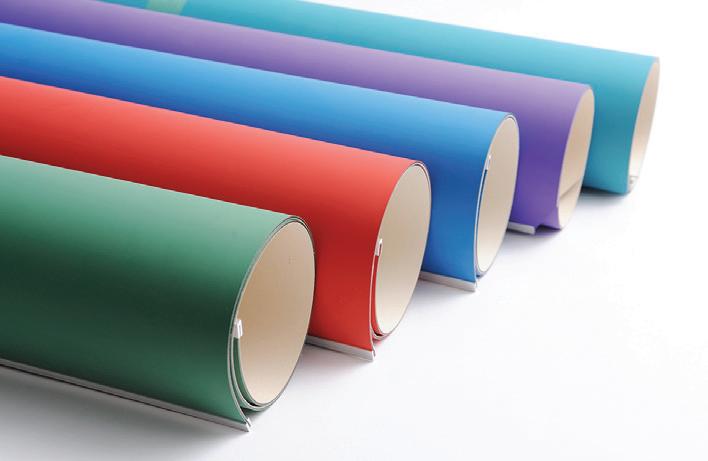
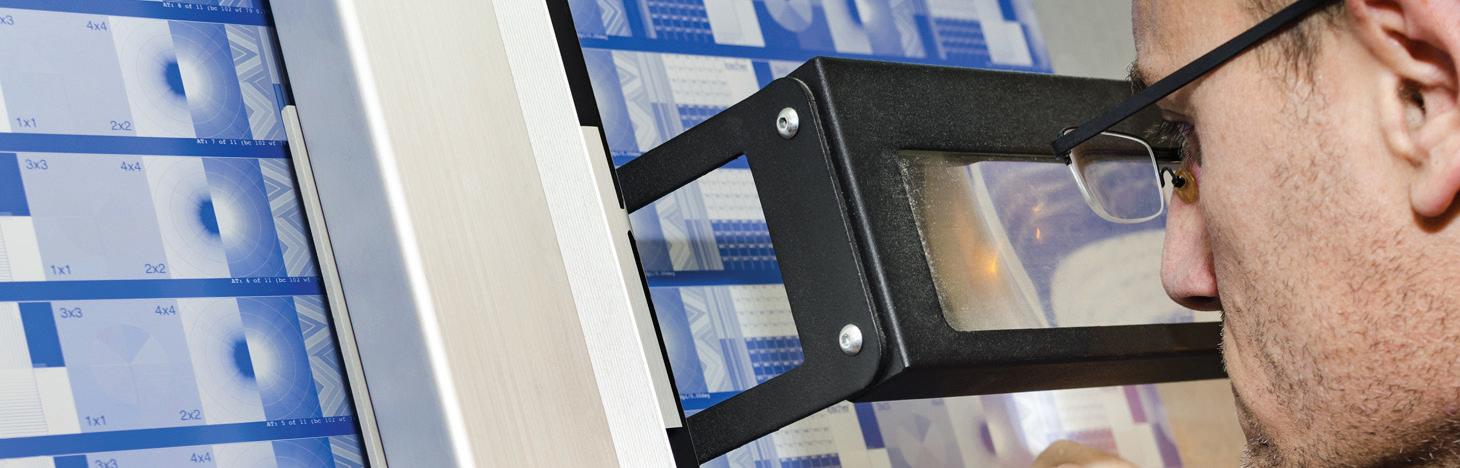
You already know that these items can make or break a print run. The most important advance in printing blankets in recent years has been the gradual rollout of Landa Nanographic printing presses. Their use of specially treated blankets utilizes breakthrough technology to ensure an optimal image – including the full image transfer to the paper, the prevention of any ink residues, and a smooth and stable blanket motion. Their design enables the transfer of NanoInk ink drops to the various substrates without leaving a trace on the blanket. This ensures that the full image is transferred without any distortions and, most importantly, that the blanket remains completely clean and ready to receive the next image. The estimated life of these blankets is about 500,000 sheets. I’d also like to call out Heidelberg’s MC05V rubber printing blanket for Heidelberg Speedmaster sheeted presses, that utilizes a solvent-free rubber laminating process. The MC05V uses closed-cell, ThermaSphere compressible layer and carcass technology that give the blanket longer life via improved shock absorption and faster recovery. Its ground and polished printing surface ensures exact gauge control, plus excellent ink transfer and sheet release. This results in exceptional print quality and dot gain control for smooth and even ink laydown, resulting in fuller solids and cleaner halftones. Finally, I should also mention Vancouver’s Enviro Image Solutions (EIS). Through its low-cost blanket-rejuvenation program, printers can reuse their blankets up to 12 times. That’s also great for our environment because a press that uses only 20 blankets a month is still putting over 1,000 lbs. of rubber waste annually into landfill. Substrates
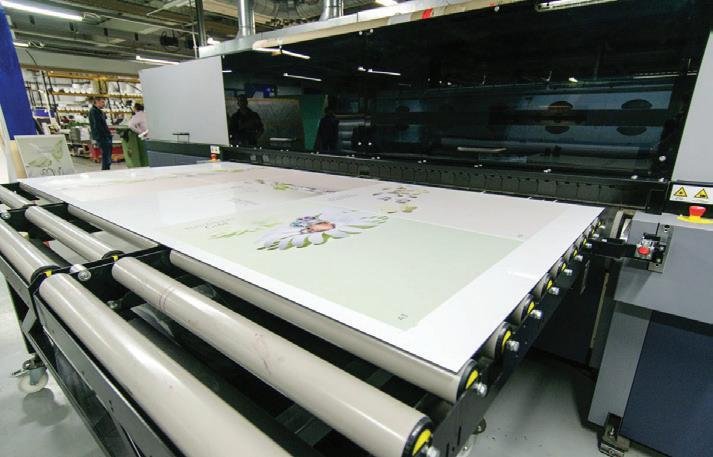
Today, graphic papers (particularly newsprint, coated and uncoated papers) are being squeezed out by digitization. In fact, 2015 saw worldwide demand for paper decline for the first time in our history – and that fall continues to this day. We’re also seeing machine conversions for packaging and specialty papers. Despite these trends, the paper and forest-products industry as a whole is now growing, albeit very slowly, while other products are filling the gap. For example, demand for packaging, tissues and paper for hygiene products is on the rise worldwide. Bottom line: the paper and forest-products industry is
not disappearing. But it is indeed changing and currently experiencing the most substantial transformation in decades. Unfortunately, this is having a negative impact on the profitability of many paper suppliers. Not surprisingly, commercial printers continue to look for guarantees when it comes to a substrate’s runability, printability, shade, smoothness – anything that might affect production, overall workflow and image quality. Ergo, many leading press manufacturers have gone to great lengths to certify or recommend certain substrates for maximum on-press performance. And there are literally thousands of choices out there, especially for inkjet. However, we’ve also seen an increase in the use of specialty and synthetic substrates. For printers who deal in small runs, these specialty substrates can differentiate you from your competitors. These papers are often lightweight with high opacity, and can play a unique role in packaging, printing and industrial printing. Generally speaking, synthetic papers combine the versatility of traditional paper with the durability of plastic, which makes them ideal for outdoor applications. They can be environmentally friendly, waterproof, more durable than traditional papers, flexible, foldable and can even hold colours well regardless of the printing process used. Inks and toner

For commercial printers, two emerging trends today are an increase in flexographic printing inks and the shift towards environment-friendly inks – such as water-based products that have less toxic effects compared to conventional printing inks. Also, as more sophisticated presses emerge, inks and toner options are becoming more specialized, especially for wide-format inkjet and textile printing. The most disruptive technology here is still Landa Nanography that utilizes tiny ink pigments that absorb much more light than traditional inks. These ultra-small Landa NanoInk pigments form a very thin layer of ink and allow digital printing at very high speeds on ordinary untreated paper stocks, and on just about any plastic packaging film or label stock. The final images are abrasion-resistant and scratch-resistant – and the overall ink savings are quite substantial. Also important in this space is software and technology that control the amount of ink used for any given print project. Agfa’s wide-format inkjet printers are a leader in this area, utilizing an extremely low ink laydown that can result in major cost savings without sacrificing print quality. Also key in reducing ink waste are devices such as ink dispensers, ink levellers, agitators, fountain liners and dosing equipment, which have proven their worth over the years. In the end, it’s all about cutting costs by reducing consumable and substrate waste while maintaining optimal print quality. As far as in-plants, the trend to high-yield toner cartridges and more cost-effective inkjet printers continues. In general, inkjet technology produces much less waste, consumes much less energy and produces up to 90% less carbon dioxide than laser printers. Plus, the overall inkjet market is still growing at a CAGR of 10.2% up to and including this year. printing industry that will also include consumables. With a visit from one of its specialists and an assessment of your printing and prepress processes, this program can save up to 30% on ink and paper, up to 50% on waste, and up to 90% on water. It accomplishes this though its hardware, software and consumables innovations. Here are some components of Agfa’s ECO³ program. Agfa’s software packages, PressTune and InkTune, add value by reducing costs, in prepress and pressroom environments, while improving print quality and productivity. PressTune ensures colour matching to specifications and colour consistency throughout a run. It allows printers to track, manage and improve press and operator performance, thus reducing makeready times by up to 40%. InkTune fine-tunes press settings to increase profitability. It can reduce ink consumption by up to 30%, improve colour stability, image quality and consistency, and lead to faster printing speeds and drying times. Agfa has also developed a Value Calculator that compares its products with competitive systems – including hardware, software and consumables. The technology takes into account water and energy consumption, developer or gum use, labour, maintenance, waste-disposal costs, amount of plate remakes, first sellable sheet, and so on. Agfa launched its SPIR@L technology in June of 2019. This new screening technology replaced traditional dots with alternative shapes to improve print
Major OEMs continue to add more value
Across our industry, major OEMs are going to unprecedented lengths to make sure that their consumables are compatible, effective on press, costefficient, and continue to add value to your business as they roll out new technology. Here are two leaders in this area. Agfa Graphics ECO³ program Economy, Ecology and Extra Convenience – or ECO³ in short. These are the key benefits that will characterize Agfa’s next-generation of innovations for the quality and reduce production costs. Due to the shape of the screen, image slur or smaller CtP imaging artifacts become invisible. The new screen avoids colour contamination in the blue range, yielding higher quality reproduction. Because of the nature of the dot shape, the ink layer is also reduced, which positively impacts drying time or energy consumption, while reducing total ink costs. Finally, SPIR@L requires no hardware additions to existing presses or workflow set-ups.
Soon after SPIR@L, in October of 2019, Agfa introduced its Eclipse processfree printing plate that eliminated the need for a processor using chemicals, thus reducing prepress costs. But it distinguished itself from other processfree plates because it was “just as easy to use as a conventional plate.” In addition, said Agfa, Eclipse was the only processfree plate to provide stable image contrast that allows for a quick visual inspection that lasts, even after one week. The new plate is up to five times more scratchresistant than competitive plates, which means worry-free loading, storing, transporting or mounting, resulting in greater productivity. Moving forward, Agfa will continue to roll out technology that includes its ECO³ benefits. Heidelberg’s Saphira Brand As we enter a dozen years of Saphira print consumables, the OEM reminds us that all Saphira products are optimized and tested specifically for use on Heidelberg presses. Heidelberg also offers bespoke packages customized for a printer’s specific needs from one single, trusted source. In short, Saphira consumables’ packages help maximize press performance to achieve consistent, repeatable print quality while cutting costs. Heidelberg has also reported that over 2,300 clients worldwide are already using its Heidelberg Online Shop.

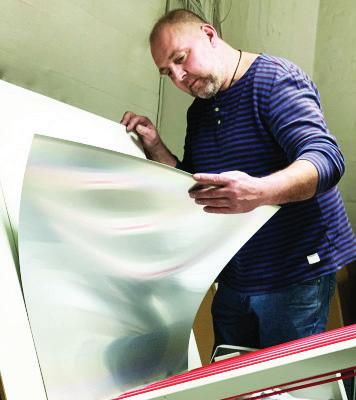
“With our eShop, we offer easy access to all products, which is unique in the industry,” said Hans Huyghe, Head of Lifecycle Segment Consumables at Heidelberg. “Our customers can also choose between different packages that include plates, inks, coatings, blankets, rollers, pressroom chemicals, etc. In fact, Heidelberg is now one of the largest suppliers worldwide of consumables to print shops.”
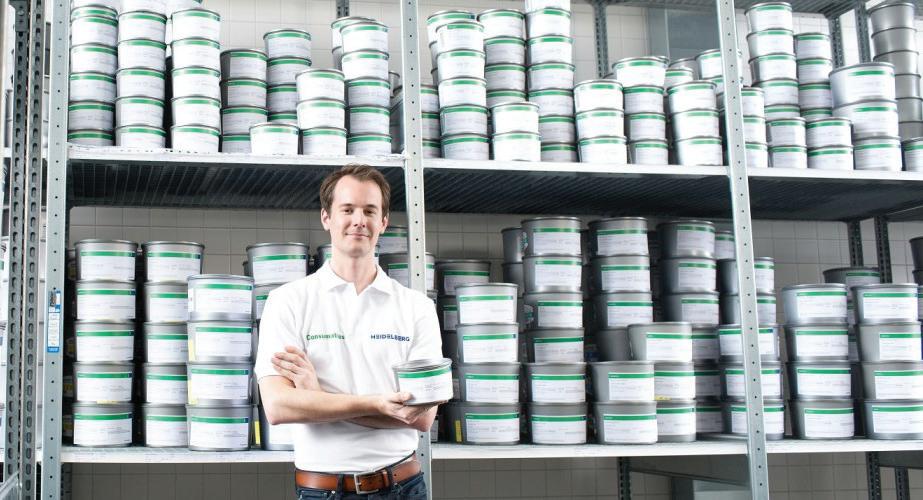
Hans Huyghe, Head of Lifecycle Segment Consumables at Heidelberg.
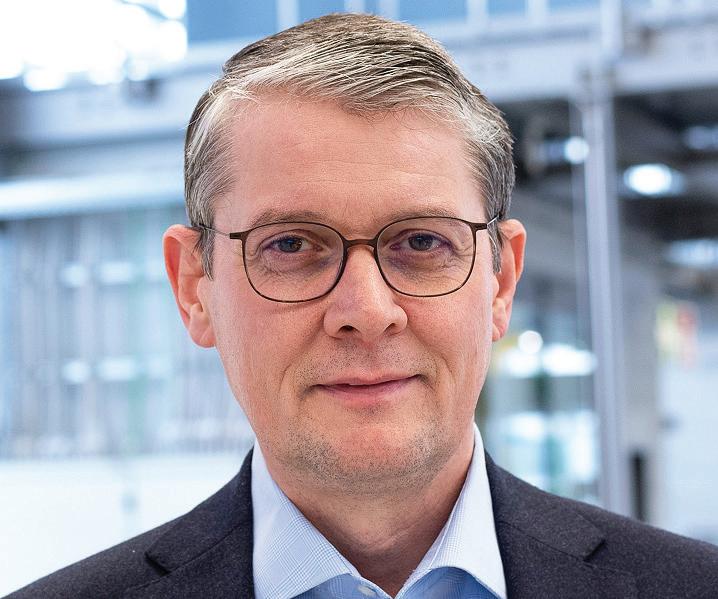
Huyghe pointed out more compelling reasons why printers should choose Heidelberg consumables. “First, all our products are tested on the latest generation of our high-speed presses under real-life conditions in each major region (Germany, the U.S. and China), and in combination with other print consumables. Second, Heidelberg doesn’t use just one supplier. For example, we have a different supplier for LED inks than we have for conventional inks in one country. This enables us to offer the best products for each application in each country. And third, by using our machine data, we’re able to track any malfunctions of consumables and/or machine settings. This inevitably results in improved print quality and productivity, repeatability and reduced waste sheets.” The OEM’s consumables are also tested and supported by Heidelberg application experts. “The expertise of our application specialists always ensures reliable results,” Huyghe added. “Our customers also benefit from Heidelberg's Vendor Managed Inventory (VMI) system. Basically, we assume control of the customer's stock so that he or she can concentrate more on selling print. For special applications, we offer a range of consumables specially developed to ensure optimum interaction with each other and with the presses.” Finally, last month Heidelberg introduced new print-site contract options (available as lifecycle agreements or subscriptions) to reduce costs and boost efficiency. They included a combination of services, software, performance consulting, training, equipment solutions – and consumables – in a single package with the aim of further improving overall performance. Plus, the Heidelberg subscription model under which customers no longer pay for the equipment they use, but for the number of sheets they produce, is now successfully established throughout the industry. And consumables are a key part of that growing model.
Tony Curcio Editor, Graphic Arts Magazine tony@graphicartsmag.com
FINALLY FOR THE TRADE VC70000 High Speed Inkjet Production Speed Up to 500 feet per minute
AIIM sets a new standard with Ricoh VC70000 in high speed production for quality and productivity on offset coated and uncoated papers.
Expanded media choices combined with a competitive cost for variable data printing increase the value of the application, while delivering an advantage your competitors cannot provide.
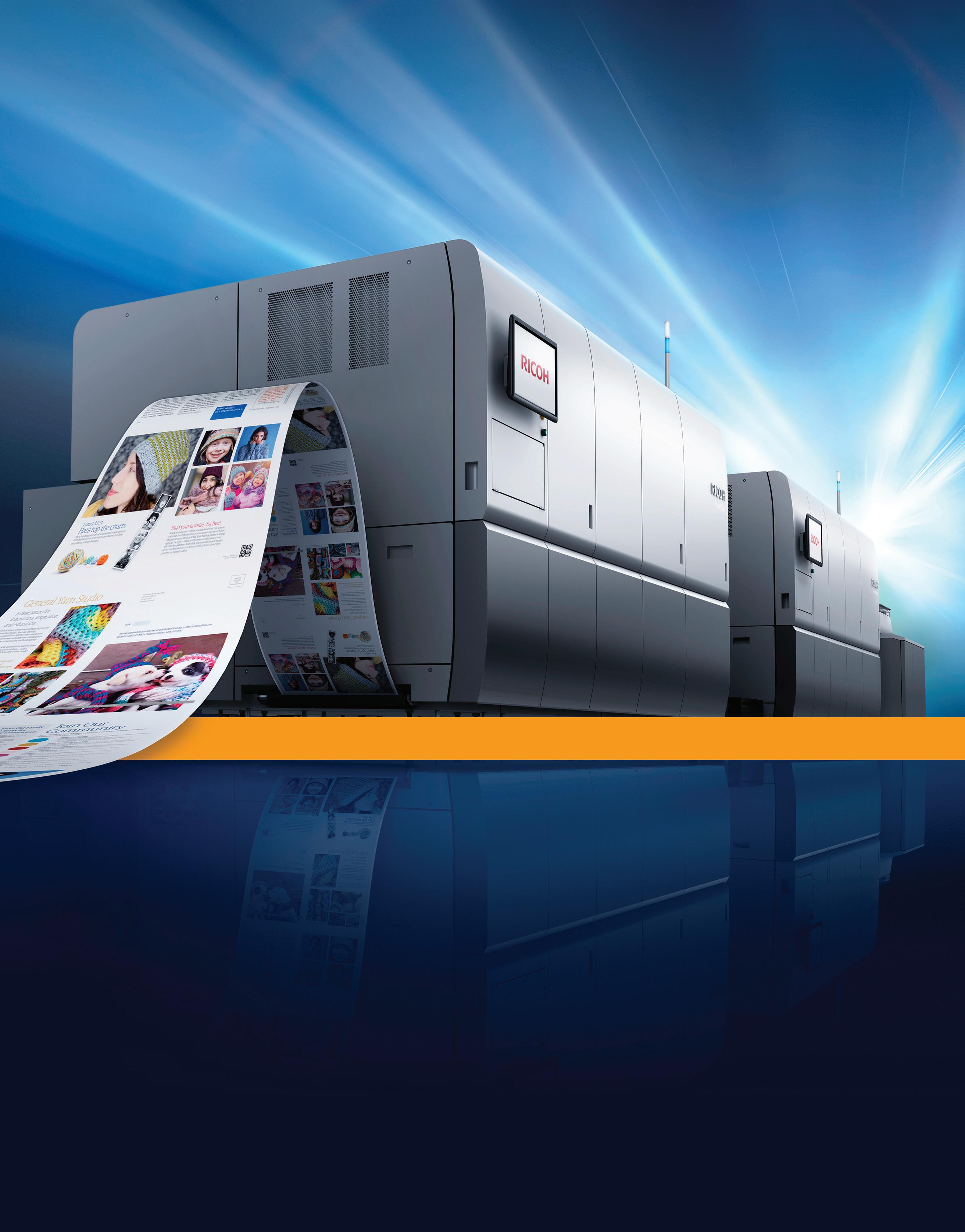
◼ Fully variable colour ◼ 1200 x 1200 DPI ◼ No Pre-treatment of paper ◼ Coated and uncoated paper ◼ 40 GSM to 250 GSM
MEDIA FLEXIBILITY
Commercial Print Critical Communication Application
Direct Mail Catalogues
Book Publications Flyers
Inquire on how all printed products can be integrated and amplified on Social Media Contact: inkjet@aiim.com Call: 416-798-7110 or 877-841-2177 | www.aiim.com
