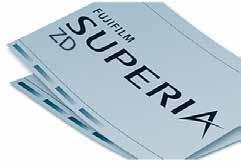
6 minute read
Process-less or process-free plates
Process-less or process-free plates – the quiet winners
With digital printing taking up most of the oxygen in news coverage in the graphic arts world, we tend to lose sight of other critical developments in our industry. One remarkable silent evolution has been the gain in importance of process-less plates in offset printing. Simply put, in a process-less plate production process, the plate goes straight from the image platesetter to the printing press, bypassing the plate processor. The plate coating is subsequently removed during the start-up of the press.
Advertisement
Although process-less or process-free plates have been commercially available since the beginning of the new millennium, it took until approximately 2014 that we saw the first uptick in the adoption rate of this technology. However, it’s only in the last couple of years that the technology has really gained traction. The three major players in this field – Fujifilm, Agfa and Kodak – have consistently invested major R&D dollars in the development of their respective processless plates. Recent introductions include Fujifilm with their Superia ZD line, Agfa with their Eclipse and Azura lines, and Kodak with their next-generation Sonora line. These R&D investments underscore the importance that these OEMs are paying to this technology. As we take a closer look at reasons why process-free plates are gaining popularity, we believe that there are four interrelated factors driving their adoption: technological improvements, cost benefits, environmental benefits and business trends. The coalescence of these four complementing factors is accelerating the adoption rate of these plates.
1. Technological Improvements
There’s no doubt that the initial releases of process-less plates encountered some challenges that jeopardized both quality and productivity, which slowed their adoption rate. Shortcomings in quality were reflected in elevated sensitivities to scuffing and scratching, fingerprints, and unintended light exposure. Residue build-up on the press required frequent cleaning, degrading print quality during a run which then triggered reprints. Shorter run lengths limited the types of jobs that could run using these plates. UV inks also caused major issues. The latest technological improvements exemplified by the most recent product releases by Fujifilm, Agfa and Kodak have drastically elevated both quality and productivity levels for both web and sheetfed presses. These technological improvements have now pushed the adoption rate of process-free plates past its lethargic early-adoption phase into the mainstream.
2. Cost benefits
Substituting conventional plates with process-less plates eliminates a critical step in the prepress workflow, shortening the time from platesetter to press, thus gaining productivity. The technology also eliminates the need for the plate processor itself – which in turn cuts out its related high usage costs of water and electricity. Removing the platesetter also eliminates its utilization and maintenance costs and creates the opportunity to redistribute labour elsewhere within the production process. Lastly, it also frees up costly floor space that can be repurposed. Combining all these cost benefits is another factor that drives the adoption rate. Although process-less plates might demand a slightly higher up-front price, the price differential is more than offset by cost savings and their overall production benefits.
3. Environmental advantages
Over the last several decades, the graphic arts industry has made major strides in responding to environmental challenges – and the introduction (and evolution) of process-free plates is yet another important step in that awareness cycle. The environmental benefits with process-free plates are self-evident. The elimination of a plate processor not only saves a production step in the pre-press workflow, but also sharply reduces the use of water and electricity while eliminating a multitude of chemicals. There’s no doubt that this technology drastically reduces an operation’s overall carbon footprint. And as mentioned before, the physical removal of the plate processor also saves real estate in the prepress department.
4. Business trends
Next to the factors already stated, there are underlying business trends in our industry that are making the case for process-less plates. As I mentioned earlier, most of the news cycles are focusing on digital printing while under-reporting advances made in conventional printing. Although conventional lithographic offset still produces the lion’s share of printed pages by far, the changing demands for shorter runs and faster
turnaround times have put tremendous pressure on offset press manufacturers to meet these demands. There’s no doubt that digital presses are changing our industry’s landscape by offering successful solutions for the increasing demand of personalization and versioning. And the continuously improving financial break-even point of digital presses for shorter runs compared to lithographic offset presses is putting pressure on conventional production processes. Offset manufacturers have reacted by launching faster presses, introducing highly automated makeready processes, and leveraging their integrated workflows. Process-less plates seem to be a logical extension and tool to partly compete with these changing digital challenges of faster turnarounds and shorter run lengths. The three major plate manufacturers continue to make their mark
Martin Boucher, National Director of Sales, Graphic Systems Division, Fujifilm Canada, has seen a substantial uptake in their process-less Superia ZD plate line. He insisted that clients are sensitive to the environmental impact of their production processes, and are looking for solutions without compromising on quality and costs. TC Transcontinental in Aurora recently adopted these processless plates. Paul Houde, Director ISM Manufacturing, specifically referred to their environmental and cost benefits. The removal of the plate processing equipment triggered a sharp reduction in power consumption and water usage while eliminating the use of chemicals. Transitioning to process-less plates also contributed to workflow productivity improvements and overall cost reductions.
Fujifilm Superia ZD Plate
Mitchell Press, based in Burnaby, British Columbia has been one of the early adopters of process-less plates when they switched to the Kodak Sonora line in 2014. Scott Gray, VP of Sales and Marketing, explained that the company prides itself to be at the forefront of incorporating sustainability as an integral part of their business practices – hence their decision on process-free plates. In a recent interview with UK-based Print Business, John O’Grady, President of the Print Systems Division at Kodak, said that the demand for process-free plates is on the rise. “There are several trends fueling the growing popularity of processfree plates, including the increasing interest in protecting the environment, constant pressure in the industry to cut costs, and the desire for more efficient workflows and faster prepress processes,” he pointed out.
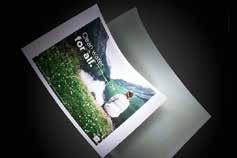
Kodak Sonora Plate
Sheetfed commercial printers here in Canada and around the globe are reporting the benefits of Agfa’s processfree printing plate, the Eclipse. It not only eliminates the need for a processor using chemicals, but distinguishes itself as a ‘drop-in’ that’s just as easy to use as a conventional plate. Iris Bogunovic, Product Manager of Plate & CTP Systems at Agfa, insists that this plate “eclipses” all other process-free plates because it combines superior and stable image contrast with easy handling and cleaner operations. She stated that several adopters have already confirmed this, reporting up to 40% faster start-up times, up to a 15% reduction in paper waste, and savings up to 25% on press cleaning. Process-free is here to stay
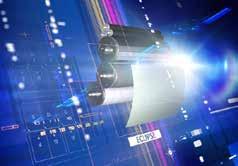
There’s no doubt that the graphic arts industry is going through some major changes. The digitization of communication tools is fundamentally changing the printing industry and is rewriting how we do business within the overall communications industry, which we are part of. The printing industry is reacting by continuously launching newer digital technologies, but also by introducing innovative new “conventional” products – of which process-free plate technology is one truly remarkable example. Although the evolution of process-free plates is not grabbing headlines, or is not the subject of major news cycles, it’s definitely a winning technology – albeit a quiet one!
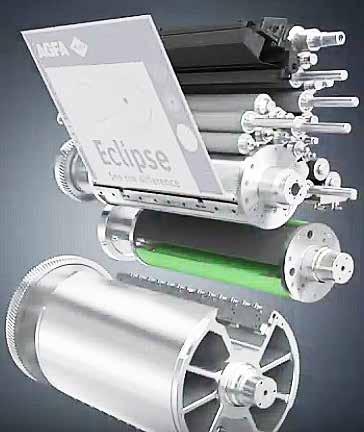
Alec Couckuyt is an experienced printing executive who held key roles at Canon Canada, Agfa Graphics (Belgium, Canada, Germany), Transcontinental Printing, Symcor, and U.S.-based EDS. He holds a Bachelor of Science Degree in Economics from the University of Antwerp in Belgium, and can be reached at alec@agcconsulting.ca