
16 minute read
Offset press update
Offset press update: The domination continues
According to Smithers Pira, by 2022 digital print will be 19.1% in terms of value worldwide – but only 4.3% in terms of volume! The rest will be offset! So it’s no surprise that the world’s leading offset press manufacturers continue to raise the bar in terms of increased automation, improved print quality, reduced waste and a host of ultra-efficient, built-in processes. Here’s a brief update. Koenig & Bauer’s Rapida 106 X Sheetfed Offset Press
Advertisement
The oldest offset press manufacturer in the world, Koenig & Bauer, launched a second-generation, feature-rich, 8-colour, B1 sheetfed offset press for the commercial print and packaging markets one year ago this month. The all-new Rapida 106 X was previewed in depth at a live-streaming event from the OEM’s headquarters in Würzburg, Germany. It’s well worth watching again: www.youtube.com/ watch?v=XB2if3Uf9Ac. The fascinating video was the final part of the OEM’s daily series that reviewed new products and technologies that would have been released at drupa 2020. With a maximum speed of 20,000 sheets per hour (sph), the new-generation Rapida 106 X was shown as an 8-unit perfector press with coater for the commercial print market. Cutting-edge automation and productivity have always been the driving forces behind Koenig & Bauer presses. So it’s not surprising that just about every component and process of this sophisticated yet easyto-use press was built for maximum production efficiency. In fact, just about all Rapida 106 X upgrades were based on customer feedback that resulted in the improvement of existing features, or the addition of new efficiency-boosting functions. In the video, eight different 300-sheet projects utilizing three different substrates were completed in just 26 minutes! The new Rapida 106 X was developed from the ground up and is “the fastest packaging sheetfed press on the market, delivering time savings of 25 minutes by optimizing production schedules and job specifications,” the company added. A huge array of new features. The Rapida 106 line has been “the make-ready world champion” in medium-format since 2008. Some important new features include an MIS system that’s connected to the Koenig & Bauer Logotronic Press Management System, yielding even more make-ready efficiencies. Simultaneous roller-wash technology can accommodate UV and conventional inks, and can be changed over in less than two minutes due to the press’s upgraded ink ducts. Among many innovations, the new Rapida 106 X accepts unbent plates, eliminating a prepress step, and features a new cold-foil module that also reduces foil costs. The 106 X has a sleek new design with illuminated glass side panels. Operation is made easier via its new and larger touchscreen, a pressstatus display panel at delivery, and an easy-to-use app for mobile devices that shows current and next-in-line project information.
Summary of key Rapida 106 X benefits
• New sleek and highly functional press design • Maximum 20,000 sheets / hour output • Lower overall maintenance • Enhanced touchscreen panel with more functionality and better visual recognition of press production and procedures via new 24/7 LED lighting • Seamless, simultaneous one-minute plate changes – from CtP to storage unit to transport to press without the risk of scratching (i.e. no manual touching of plates) • Side-lay infeed system for stable processing of each sheet • Specially coated ink ducts for faster, maintenance-free ink changeovers • Simultaneous roller wash function can be deployed while producing other jobs • Supported roller adjustment for longer life and easier changing of rollers • Improved print blanket washing • Inline colour control for accurate colour management – a photo is taken of every sheet and compared to a master sheet or the original PDF. Any errors are reported • Optimized dryer configuration for faster drying of output • Automatic register control – two double-camera systems measure precise registration • DriveTronic SIS feeding system that further guarantees precise registration • A host of finishing capabilities including inline rotary die cutting, embossing, cold foil, gloss or matte effects and varnish for multiple coating applications • Optional optimized long-life automatic lubrication throughout the press Koenig & Bauer also offers a variety of options that allow its presses to be configured to meet specific customer needs. In fact, the OEM was traditionally – and still is – a custom press manufacturer that’s experienced great success in this highly demanding area. Finally, a number of flexible, affordable tech-support options are all aimed at reducing downtime.
For more information call Aleks Lajtman, Koenig & Bauer Regional Sales Manager for North America, at (647) 719-3069, or e-mail Aleks.Lajtman@koenig-bauer.com.
The Rapida 106 X Sheetfed Offset Press from Koenig & Bauer
Heidelberg Speedmaster XL 106 UX
It’s no surprise that Heidelberg remains the world’s largest press manufacturer with the most comprehensive portfolio of sheetfed offset machines. Its flagship, peak-performance press – the Speedmaster XL 106 – reflects the huge success of its Push to Stop technology for totally autonomous printing. However, other features such as Zero Defect Packaging have been added to enhance productivity even further while reducing workflow touch points. Using new features such as Inspection Control 2 in tandem with a Waste Sheet Ejector, now means that print errors can be removed from the good-sheet pile. Plus, start-up waste can be ejected and all sheets in the delivery will be of the highest quality. This is done automatically based on parameters set by the operator. A new feature called AutoPlate Coating now allows automatic loading of plates in the Coating Unit in tandem with the print units. This is especially effective in presses with multiple coating units – a growing requirement in packaging printing. As far as commercial print, the XL 106 is ideal for longer runs with frequent job changes, while maintaining exceptional print quality at speeds of 18,000 sph in straight printing or perfecting mode. Parallel make-ready processes also increase productivity in commercial, packaging and label printing. Overall, Heidelberg’s intelligent interaction of automation processes enables more cost-effective production of virtually any printed product. Other major benefits include: continuous AI-based process optimization; no additional make-ready time due to fully automated air settings when changing substrates; automatic plate changes with AutoPlate XL 3 in under one minute; a waste-ejection system that eliminates subsequent quality inspection issues; and Inpress Control, an inline colour control and registration system.
Push to Stop autonomous printing
Heidelberg’s breakthrough “Push to Stop” technology for fully autonomous printing from the last to the first good sheet also includes auto plate loading, inline colour management, automated measurement and register. With new Quality Assist software, jobs can be autonomously produced with no operator touch points. Make-ready times are cut in half, with the first measurable result in less than a minute while using less than 60 sheets.
As further proof of the popularity of Push to Stop technology, and in one of the biggest recent deals in Heidelberg’s history, leading European book and publishing printer Wilco (Amersfoort, The Netherlands) invested in no less than 11 Speedmaster XL 106 presses for a total of 61 latest-generation printing units, for a massive boost in productivity. This also included a Print Site Contract to supply consumables. Final installation of all 11 presses is expected to be completed this September. With over 500,000 works published each year, Europe’s book industry has performed exceptionally well despite the pandemic. This trend resulted in a much better investment climate for book printers. This landmark installation included various press configurations, as well as four models just for the Speedmaster XL 106 8P.
Heidelberg’s unique subscription program
The OEM’s unique subscription program, especially helpful given tight budgets due to the pandemic, supplies the press, consumables, service, advanced training and consulting, while focusing on maximum productivity over the five-year life of the subscription. Heidelberg still owns the press, and so it’s a way for the customer to increase capacity and improve productivity without making a substantial capital investment. The customer pays a cost per sheet, which drops with increasing volume. The program is designed for highervolume printers who produce 20–25 million impressions per year or more. Other subscription models have been created, and are known today as LifeCycle Solutions. They offer customers convenient, “scalable” subscription programs that may include ranges of consumables, services, training and equipment. Heidelberg can actually build a program suited to an individual customer’s specific production operation or business needs.
More info: Ray Fagan, Heidelberg Product Manager & Sales Support Specialist for Sheetfed, Digital & Postpress Packaging; (647) 271-2862; Ray.Fagan@heidelberg.com.
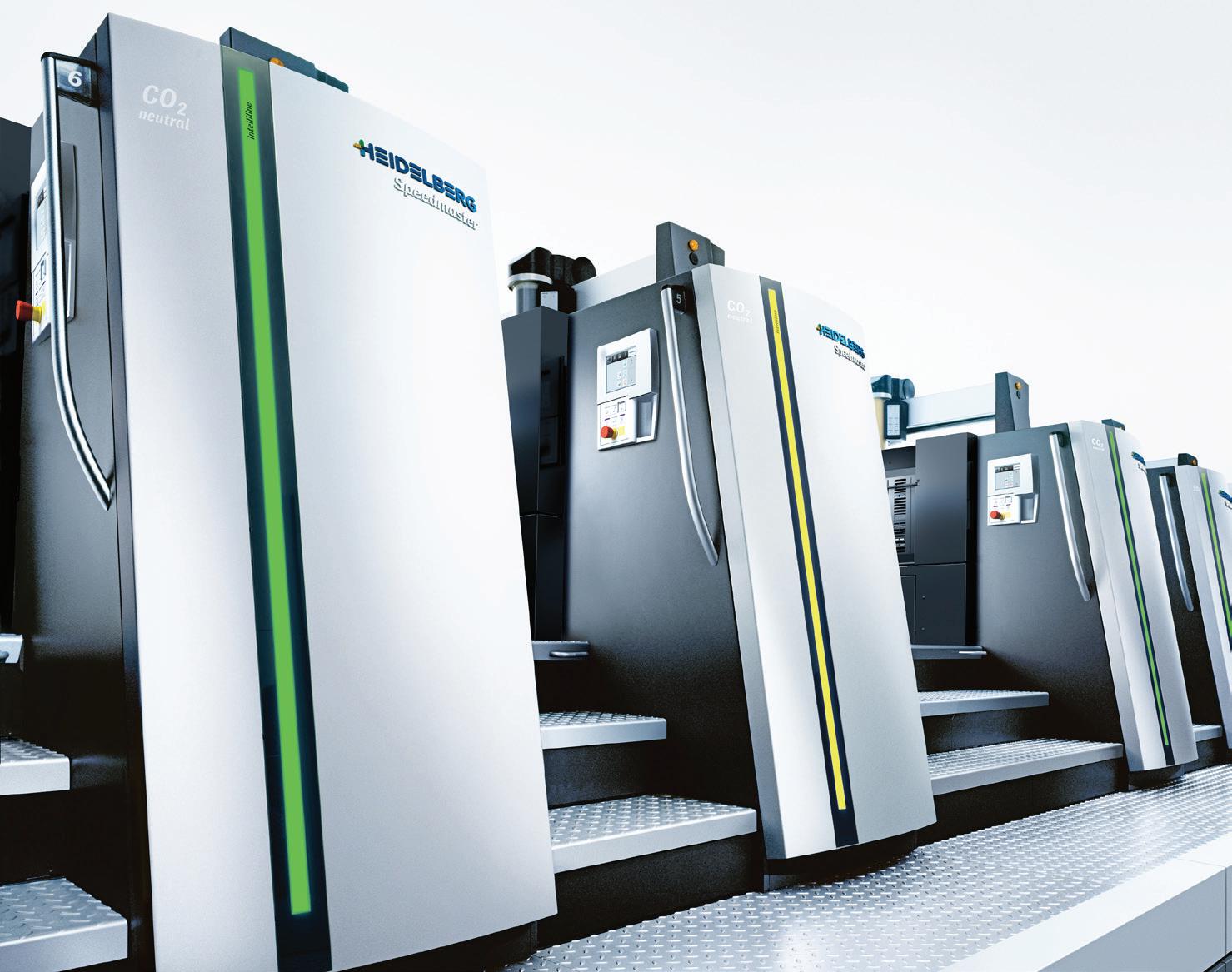
Heidelberg Speedmaster XL 106 UX (User Experience)
RM Machinery Canada’s RMGT 970 and 10 Series Offset Presses
Major cost-cutting features. “Printers know there are two ways of increasing profits: sell your printing for more or reduce manufacturing costs,” said 30-year industry veteran Steve Klaric, Canadian Sales Manager for RM Machinery. “As we emerge from the pandemic, the former option may not be feasible. So, if you’re looking to significantly reduce your initial equipment investment and ongoing manufacturing costs, while still being competitive in the 40-inch-format market, the RMGT 970 Series is ideal. For example, the 970 can reduce plate costs by 20%, power consumption by 34%, and installation space by 30%, based on our research. To date, more than 70 RMGT 9 Series presses have been installed across North America.”
RM Machinery Canada leads the way.
Led by CEO Rahul Kaushik, the Mississauga-based company specializes in some of the world’s best printing equipment and supplies – including RMGT LED-UV and Mitsubishi, sheetfed, web offset and newspaper presses, Standard Horizon finishing systems, Miyakoshi flexo presses, Böttcher print consumables and GEW LED-UV curing systems. “Our team has decades of expertise, training and specialized experience in selling, installing and servicing this equipment,” said Kaushik. “We’re totally focused on making our customers more productive and more profitable.” New 8-up+ sheet size of 25”x38”. Today’s RMGT 9 Series presses fill the gap between small, expensive-to-run digital devices and 40” offset presses that seldom run a full-sized sheet for applications such as direct mail, 16-page signatures and shortrun packaging. The new 8-up+ RMGT 970 can produce jobs such as 9”x12” booklets on the same size sheet that a 40” offset press would run. Printers asked for easier access to cover-weight stocks that many paper merchants inventoried in 25”x38” sheets – so RMGT addressed that market directly with the 970’s unique format size that yields significantly lower manufacturing costs. The series includes straight printing presses and convertible perfectors from 2 to 10 colours at speeds up to 16,200 and 15,000 sph respectively. Fully automatic plate changing features a bender-less plate clamp that eliminates the need to bend plates. LED-UV curing units at the perfecting and delivery stages dry prints instantly. Check this short video: https://www.youtube.com/ watch?v=9oaLI9EWRJI.
RMGT 10 Series. RMGT’s Flagship Straight Press is a high-throughput, maximum uptime, full-size press that consistently outputs high-quality commercial products and colour-rich short-run jobs. The RMGT 1020ST, 1050ST and 1130ST eliminate operational variables that can rob printers of profitable production time – such as excessive powder, oil stains, scratches, sheet misalignment, doubling, ghosting and watermarking. Automated plate changing, various preset systems and automatic cleaning greatly shorten make-ready times. Double-diameter impression and transfer cylinders transport paper with minimum flapping, providing stable paper transport even with heavy
The Return of Excellence
For years, Mitsubishi set the superior technology standard for Canadian printers. Today, RM Machinery returns that innovation to Canada, but with an even higher standard: Ryobi Mitsubishi Graphic Technology (RMGT).
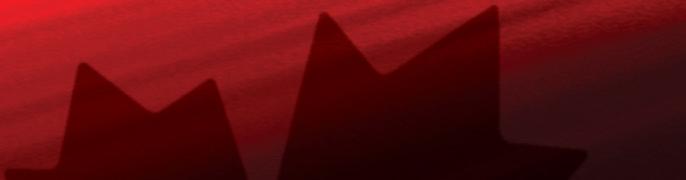
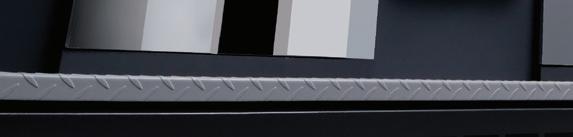
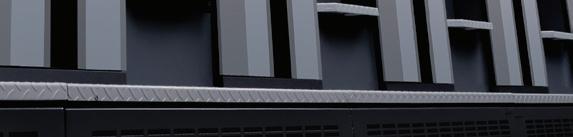
Serving the US market for nearly a decade, RM Machinery (RMM) proudly brings our expertise to Canada’s printing industry. We deliver the highest quality sheetfed o set, digital inkjet, and flexo printing presses by partnering with the finest manufacturers in the industry.
RMM is the premier distributor in Canada for Mitsubishi, RMGT, and Miyakoshi printing presses; Böttcher rollers, blankets, and chemistry; Standard Horizon finishing systems; GEW UV curing systems and TOYO inks.
RM Machinery Inc.
905-238-9797 • 1-855-RMGT-123 5250 Satellite Drive, Unit 9, Mississauga, ON L4W 5G5
We are stable, local, and o er the best-in-class technology. We maintain an ample supply of parts, and for as long as you own one of our supported presses, you are guaranteed ongoing service and support programs that are among the best in the industry.
Equipping North America to print.
www.rmmc.ca
RM MACHINERY, YOUR PREMIER PRINTING TECHNOLOGY DISTRIBUTOR FOR:
RMGT 970 Series Offset Press

stocks. Fully automated plate changing, a bender-less plate clamping system, a lubrication-free gripper shaft torsion bar, and oil-less bearings (on gripper shafts of impression and transfer cylinders), can save operators hundreds of hours a year. Plus, “Maintenance Mode” and “Cleaning Mode” functions result in faster adjustments and quicker press clean up. The optional LED-UV curing unit dramatically improves work efficiency, lowers power consumption and prevents warping of film and other heat-sensitive media.
More information: Steve Klaric (647) 4507599 or e-mail sklaric@rmgt.com. Or, call Rahul Kaushik at (905) 238-9797 or 732910-9300, e-mail rahul@rmgt.com, or visit https://www.rmmc.ca/.
Manroland Sheetfed
I’d be remiss if I didn’t mention two other offset giants. Manroland Sheetfed is a leading German manufacturer of sheetfed offset presses founded in 1871. Product lines range from small-format, up to the 1,850 mm (64 A4-page) Roland 900 XXL. Manroland’s strength has always been to put as much automation as possible into its presses to boost throughput via one-pass printing. Its trademark “highest efficiency, highest quality” approach is evident in the fact that the OEM was the first to initiate Direct Drive technology, simultaneous make-readies – and most of all, the first to pioneer inline colour control. That trend continues with its impressive Evolution series. In recent years, Manroland Sheetfed has added new features to improve performance, drive productivity and reduce operating costs. Aside from simultaneous plate loading, these include precision sheet-guiding technology, printing speeds up to 18,200 sph, an upgraded Inline Inspector and InlineColorPilot (which enhances quality control with a fully automatic system to ensure consistent colour), a sheet-numbering system that speeds up error detection, lowenergy UV drying technology, an Indexed Inline Foiler and much more.
The company continues to partner with its clients to drive more production efficiencies. Its Autoprint technology, coupled with the OEM’s exclusive TopAnalysis system, can monitor production daily, and report the findings over a 30-day period to evaluate press performance and OEE (Overall Equipment Effectiveness). In this way, clients get the support they need. Komori
The Japanese press manufacturer’s Flagship Lithrone G/GX press series (sold exclusively in Canada through Komcan of Georgetown, Ontario) can print reliably at up to 18,000 sph (even on heavy stocks) with all the key automation features one would expect, while offering exceptional ROI. As the flagship of the G series, the GLX40 provides short make-ready times, fast run speeds, excellent uptime, and a low cost of ownership. Particularly successful in Canada with numerous installations, commercial printing and packaging shops have benefitted from the G Series’ huge array of efficiencies. These include Asynchronous Automatic Plate Change technology that’s capable of changing all plates in less than 80 seconds. With fully automatic non-stop delivery, the GLX40 and GLX40P also ensure that users produce the most quality sheets in the least amount of time.
Options such as PQA-S full-sheet inspection and colour/register control, remove variables from of the hands of press operators, allowing them to focus on maximum productivity during the run. The Lithrone GLX40 Advance delivers both significantly improved print quality and enhanced agility during colour changeovers. Extraordinary productivity also comes from optional, automatic non-stop technology for long runs at high speeds, control systems, and new cleaning and washing systems. KHS-AI, Komori’s core system for meeting diverse printing needs, is combined with new features that provide powerful support for commercial and packaging printing in particular. Its energy-conserving and space-saving design, along with reduced heat emissions, also benefit the environment.
Tony Curcio Editor, Graphic Arts Magazine tony@graphicartsmag.com
Warren’s Waterless installs Horizon AFC-566-FG Folder from RM Machinery Canada
Earlier this year, Warren’s Waterless Printing (Toronto, ON), Canada’s first and only waterless printing company, installed a new Horizon AFC-566-FG Automated Folder from RM Machinery Canada (Mississauga, ON). RM specializes in selling, installing and servicing some of the world’s best printing equipment and supplies – including RMGT UV sheetfed offset presses, Mitsubishi sheetfed offset presses, web offset and newspaper presses, Standard Horizon finishing systems, Miyakoshi flexo presses, Böttcher print consumables and GEW LED-UV curing systems. The installation eventually cut folding production time by 50% by reducing bottlenecks in production. “Makeready times on our other folders needed attention,” recalled owner Glen Warren. “With the AFC-566-FG, prep time was significantly reduced and we’ve been able to minimize congestion among our print jobs.” Founded in 1972, the company transitioned to a full-service waterless printer in 1995. It also operates two 40” Mitsubishi offset presses that use VOC-free, soy-based inks. Waterless printing – in combination with ink recycling and specific methods of cleaning press blankets – has resulted in saving an estimated 200,000 litres of water per year! The new folder will be used for direct mail, newsletters, brochures, maps and more. Other in-house equipment includes digital presses for variable-data projects. The Horizon AFC-566-FG is an ideal finishing solution for both offset and digital output. It has six fold plates that allow for 17 different folding patterns, and can handle sheet sizes as large as 21.97” wide and 33.46” long. Up to 200 jobs can be programmed and the folder can reach speeds up to 42,000 sph.

Warren Waterless’ Horizon AFC-566-FG Automated Folder
Lacasse installs second Anapurna FB2540i LED from Agfa Graphics Canada
Lacasse Printing (Tecumseh, Ontario) recently purchased its second Agfa wide-format printer, an Anapurna FB2540i LED. The company has been serving the Ontario market since 1952, offering its clients a full range of visual communication services – including sign and display applications, marketing, vehicle graphics, digital and offset printing, custom flags, indoor/outdoor banners, canvas prints and fine art, and even imaged glass and ceiling tiles. Its slogan is “We Print Everything.” With the addition of its second Anapurna, the shop will continue to maintain the highest quality standards, as it continues to provide affordable on-demand printing and much faster turnaround times. Agfa’s Anapurna FB2540i LED is a 6-colour-plus-white high-speed, UV-curable flatbed inkjet printer that can output at speeds up to 96 m²/h. The UV-curable inkjet system on a moving gantry flatbed is ideal for both step-and-repeat work, and for printing multiple jobs on differently sized media. Borderless printing capabilities avoid an extra finishing step, saving users both time and money. Its multilayer-printing feature allows the Anapurna FB2540i LED to print several colours and white-ink layers in one run. The engine delivers high-quality prints on practically any rigid and sheet material. White ink and six colours, with 13-picolitre print heads, deliver vibrant prints that “will give you and your customers a competitive advantage,” said the OEM. A highdensity colour printing function makes prints even brighter and more intense. The printer is fitted with air-cooled 16 Watt/cm² UV LED lamps, which results in a number of unique advantages related to generating extra business – as well as cost savings and environmental friendliness, a wider scope of applications, higher productivity and substantially less power consumption.
Lacasse Printing’s second Anapurna FB2540i LED
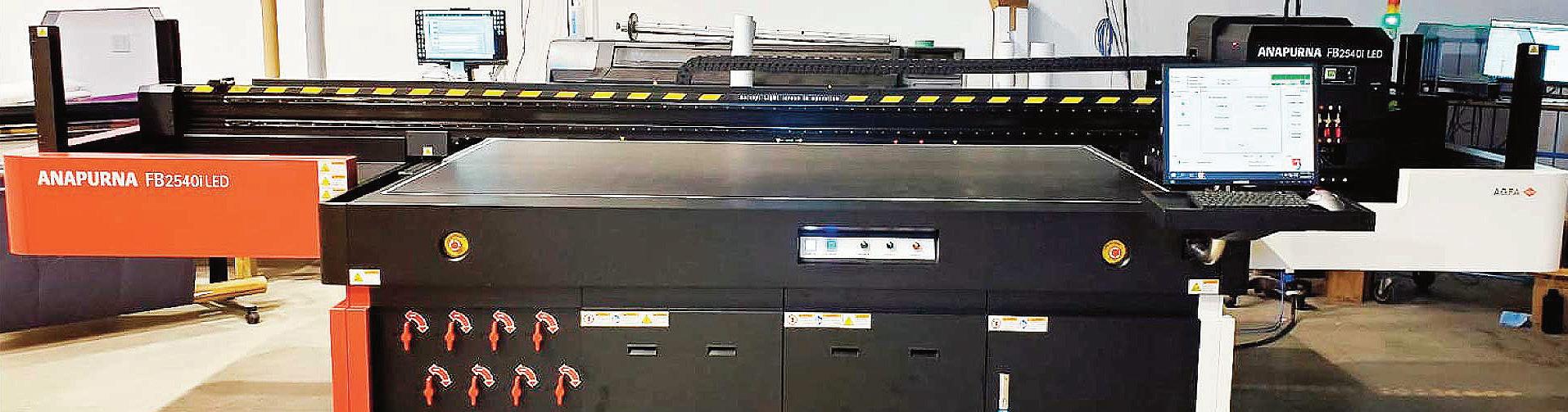