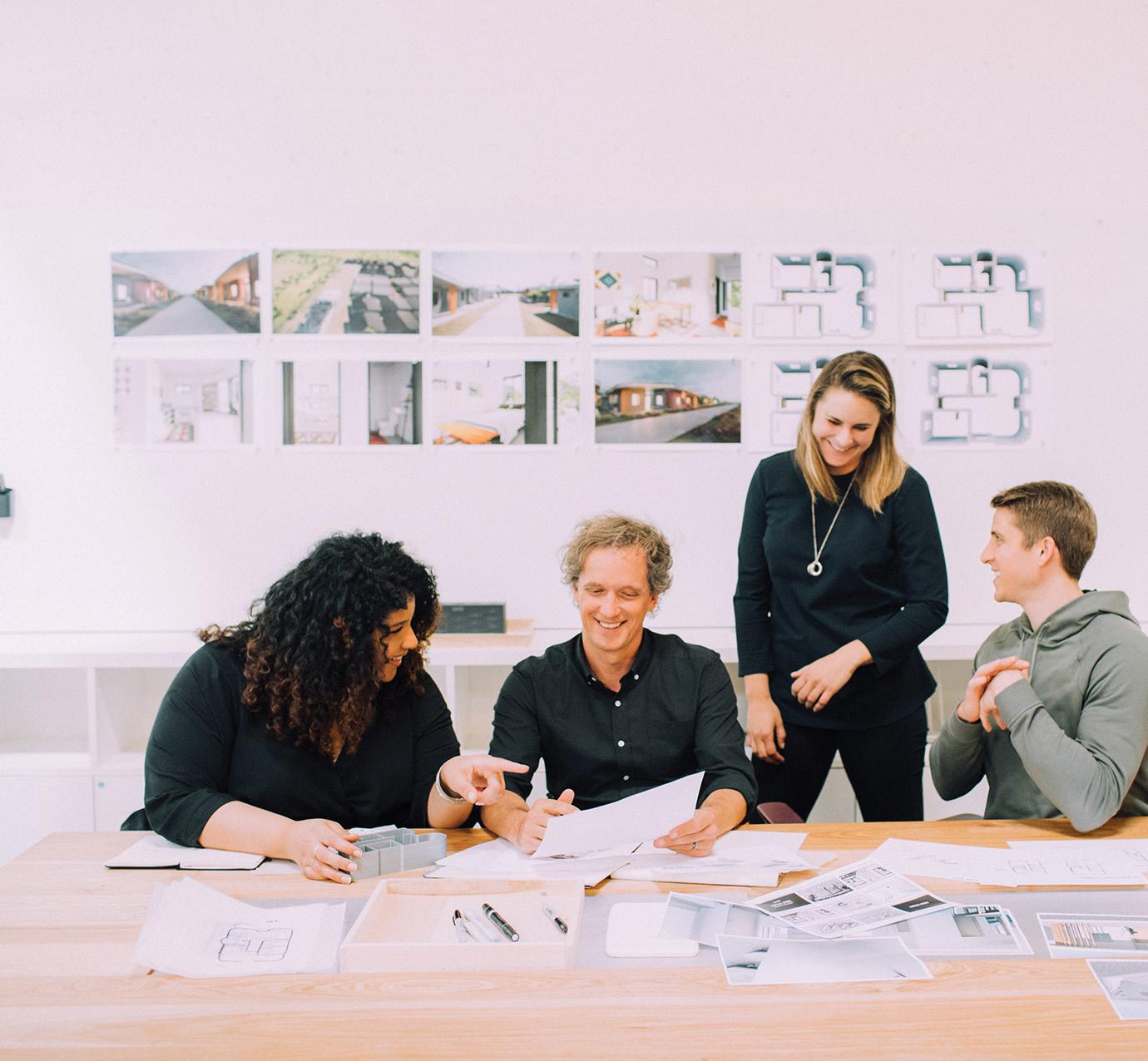
10 minute read
PRINT PROGRESS
The nonprofit New Story teams up with designer Yves Béhar to create the world’s first 3D-printed community in Latin America.
By RACHEL GALLAHER

THREE YEARS AFTER THE 2010 EARTHQUAKE IN HAITI, 24-year-old Brett Hagler traveled to the dual-nation Caribbean island of Hispaniola to help with humanitarian efforts. While working just outside Port-au-Prince, Hagler, who had previously founded a for-profit tech startup in San Francisco, was deeply struck by the children he saw living in flimsy tents and makeshift shelters without running water, electricity, or means to ensure their safety.
“When I went to Haiti, I had no desire to start an organization,” Hagler says. “But what I saw down there absolutely broke my heart.” Fast-forward to today, when he serves as the cofounder and CEO of the San Francisco–based housing charity New Story, an organization poised to begin erecting the first 3D-printed community in Latin America later this year.
After a week in Haiti, Hagler returned to the States with plans to get involved in a charitable organization that embraced emerging technology to challenge traditional nonprofit aid methods. A few months into searching for the right group, Hagler realized he hadn’t come across one that checked all the boxes. “I couldn’t find any organizations that were really prioritizing or willing to take calculated risks on innovation and new design concepts,” he says. So, like many entrepreneurs before him, Hagler decided to start his own group.
Hagler enlisted cofounders Alexandria Lafci and Matthew Marshall (the three met through a social entrepreneurship group in Atlanta), and launched New Story in 2014 with the goal of helping create a world where no human is without shelter. Five years later, the organization has not only built more than 2,200 houses in Mexico, Haiti, El Salvador, and Bolivia, but is helping to facilitate some of the most exciting advances in mass housing in the past 20 years.
In 2018, after a year of research and development, New Story and ICON, an Austin, Texas–based construction technology company dedicated to revolutionizing homebuilding, announced the successful printing of the country’s first permitted 3D-printed home. A year later, the two companies unveiled plans for the world’s first 3D-printed community, which is slated for completion in an undisclosed Latin American country next year. Swiss designer Yves Béhar, founder of the San Francisco–based Fuseproject industrial design and brand firm (and a member of New Story’s advisory board), worked closely with New Story, ICON, and the future residents of the community to design functional, aesthetically pleasing houses that will serve multiple generations and could act as stepping stones out of extreme poverty. “This partnership is an example of how design, technology, and social good can combine to present new solutions to global issues,” Béhar says. “This
FROM LEFT: Designer Yves Béhar reviews design plans at the Fuseproject office in San Francisco. Sketches and models of the houses at the Fuseproject office. A rendering showing a group of 3D-printed houses.
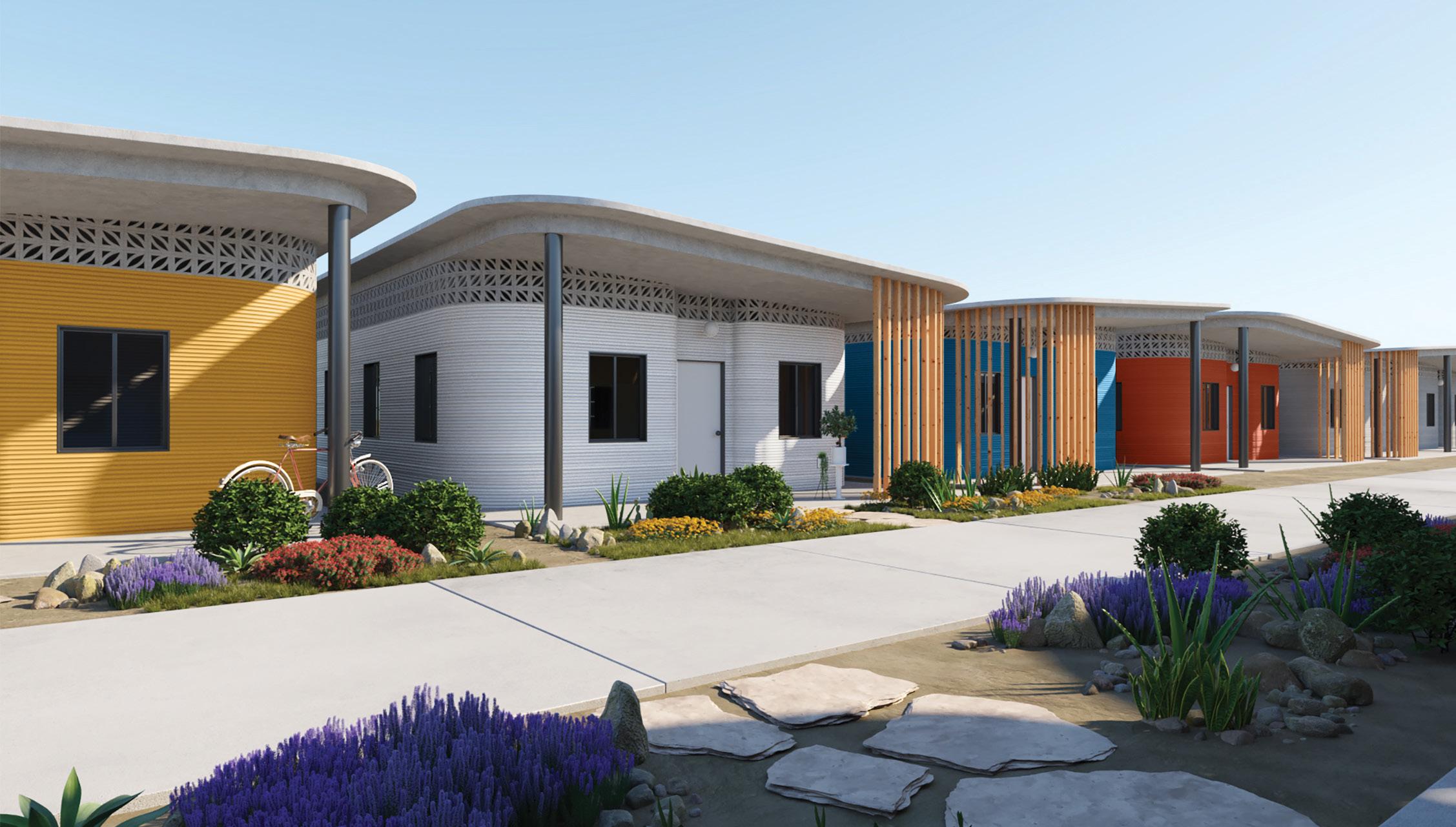
concept is at the root of what drives our work at Fuseproject every day, and it’s something the team has become really passionate about.”
Groundbreaking for the community— consisting of some 50 houses, each 500 to 600 feet square—will begin at the end of this summer. Unlike typical humanitarian housing efforts, this project relies heavily on input from its recipient community. The design team has repeatedly traveled to Latin America to meet with residents. The ideas generated from these meetings, many of which revolved around tight-knit interactions among neighboring families, helped shape architectural details throughout the design process. “We asked the villagers what was important to them in a house,” Hagler says. “They would tell us things like, ‘It’s important for me to see where my kids are playing,’ and that would determine where windows will be placed. Most of the families prefer to cook as a community, so kitchens will be placed outside, where neighbors can cook together. It is vital to us that these houses serve them first and foremost.”
“By working directly with the community to get them involved in the planning process from the start, we were able to use design and technology to respond to their needs,” Béhar adds. “The design reflects this approach. It was centrally important that the design be as responsive to the lived experiences of the community as possible, and was flexible enough to grow with families over time.”
The 3D printer, which uses proprietary technology developed by ICON, will be shipped, mostly in one piece, to Latin America in the largest street-legal tractor-trailer around. There it will churn out layers of cement (think of squeezing icing out of a pastry tube), functioning with near-zero waste and optimized to work under unpredictable conditions such as limited water, power, labor, and supportive infrastructure. The printer also drastically speeds up construction, as the walls and structural elements of each home can be printed in just 24 hours. In areas affected by disasters such as earthquakes and hurricanes, this technology could be truly lifesaving, and it has the potential to get people back on their feet at a pace that was formerly impossible.
“We’re trying to do something that has never been done before,” Hagler says of the forthcoming printed village. “After the first community is built, our goal is not to keep [the methods] for ourselves. The bigger idea is to manufacture more machines and allow other nonprofits and governments access to them. Whatever can have the biggest impact, that’s what we want to do.” It’s rare that innovation serves the poorest communities first, but New Story is proving that when it does, it can be powerful enough to really change the world. h
Glass Act
A waterfront home, marked by an atrium filled with irregularly shaped windows, strikes a balance between minimal and surreal.
Interview by TIFFANY JOW
Located on the eastern shore of the South River in Annapolis, Maryland, this three-floor, 3,000-square-foot home was designed by local firm Kezlo Group with views of the water in mind. The homeowner, Dr. Craig Vander Kolk, and the lead architect, Jason Winters, developed a teardrop-shaped footprint with a defining feature at its tip: a massive triangular atrium, which is open to all floors, leans outward in the plane of the exterior façade. They chose products from Western Window Systems to make it a reality. To better understand the complexity of the project, and why Western Window Systems’ moving glass walls and windows were an ideal fit, we gathered the home’s key team members—Winters, project manager Pete Edmunds of Lundberg Builders, and window specialist Gary Logue of The Sanders Company, which sells Western Window Systems’ products in the area—to discuss how they joined forces to create this statement-making home.
The goal of this house was to capture views of the surrounding natural environment. How do windows and moving glass walls factor into making that vision a reality?
JASON WINTERS: The easy solution to [capturing sweeping views] is to put in all glass, all the time. This project was more nuanced: the client wanted large panoramic openings in some areas, and smaller gunshot views in others. There are different ways to present views to the water, and that’s what this house is all about. Having the flexibility in windows’ size and scale, and the ability to eliminate additional clunky framing that might get in the way of the views, was critical to the project’s success. PETE EDMUNDS: In the residential market, it’s hard to find a window that’s varied enough [in size and shape] to achieve a scale [that builders] can manage. And with commercial windows, you end up with a window that’s too big and can’t fit in a lot of residential situations. Western Window Systems offers the best of both worlds: they’ll create a window that fits into a given space, in any sort of shape. And this project required lots of irregular window shapes and sizes.
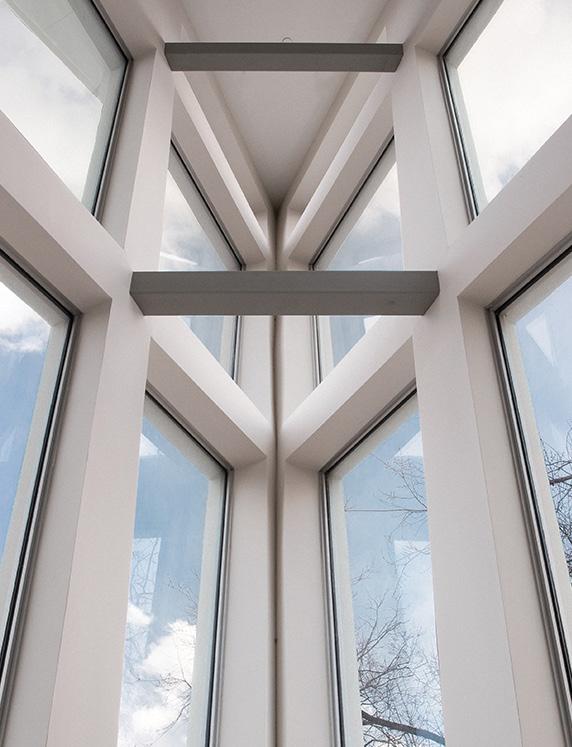
The glass-filled atrium is the crown jewel of the house—it’s 45 feet above grade and sticks out like the bow of a ship. What were the structural challenges of incorporating windows into it?
JW: Because of the atrium’s pointed, triangular shape, the windows sit in walls of varying thicknesses at an eight- or nine-degree angle—we weren’t just setting windows and having everything pair up nicely. So there was an additional technical challenge of finding a window that could achieve that. GARY LOGUE: Right. Each window is leaning outward, in a custom shape—a lot of companies never would have made them due to that. But everything Western Window Systems does is custom. It wasn’t unusual for Western Window Systems to make shapes like this, and that’s what architects like about them.
PE: The windows are actually floating in between structural members, and placed like art on a wall. The glass acts like the curve of an eye, where you are looking out onto a surface that’s not straight. There aren’t too many windows in this market we could do that with.
Beyond Western Window Systems’ penchant for customization, what else made the brand appealing?
PE: Gary’s showroom was key to getting our client to appreciate the versatility of a Western Window Systems product. The scale of its windows is hard to capture unless you can see it in person, and his space is set up so you can see it all: the details of the sill, the size, how it will look in the final analysis. GL: Typically me and the rest of the Sanders team are the representatives for Western Window Systems. In this case, we set the team up with a visit from one of its national sales representatives, so he could see the unusual aspects of this project. He helped us through some of the communication [between the client and the brand]. JW: Craig and I visited Gary’s showroom several times. From the front end, it was helpful for Craig to ask questions about how the windows are made. Cost was also a factor. That’s what the allure of Western Window Systems was: its price point and performance were consummate with the variety of applications we needed. You’re
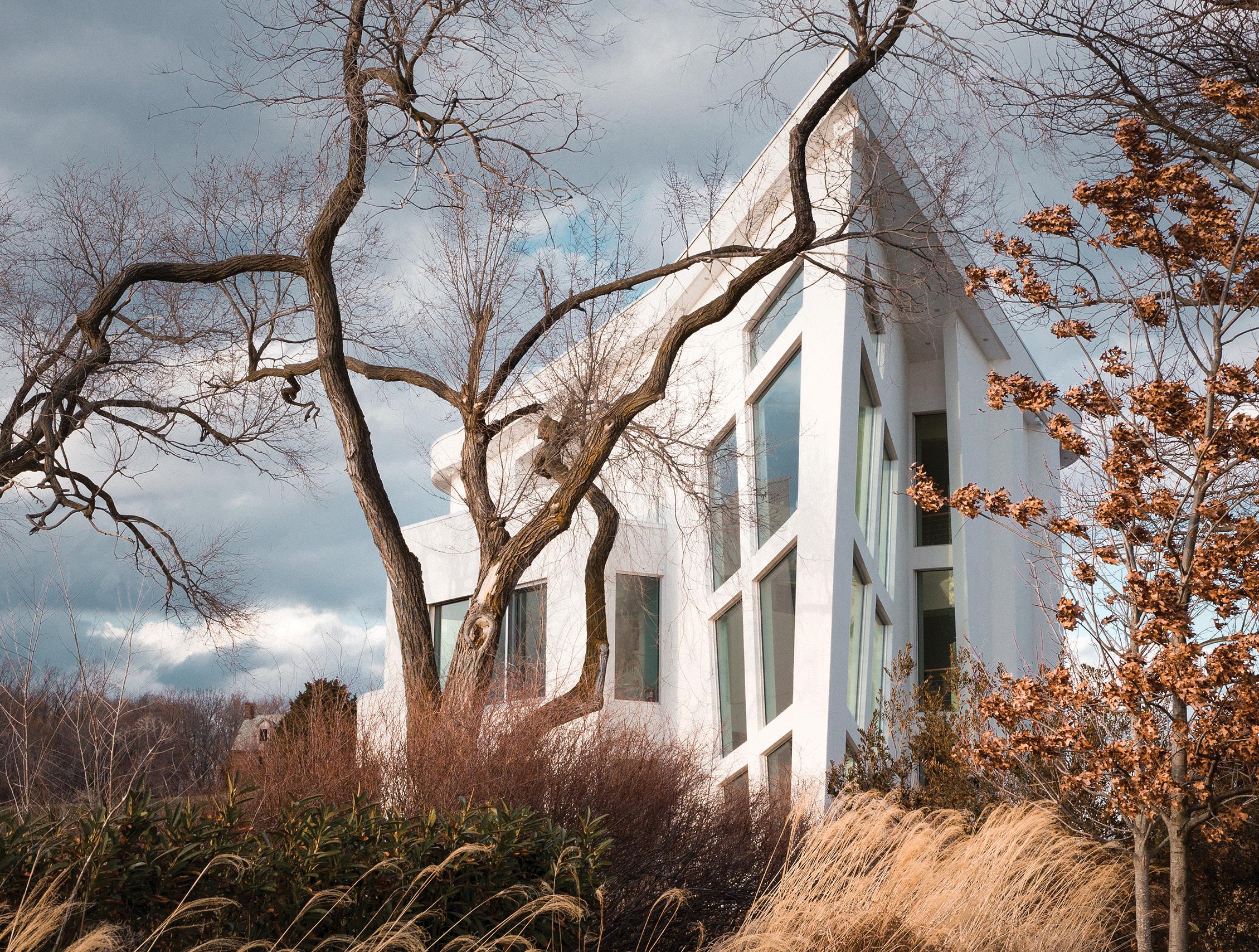
also able to open [all of these windows]. Every time I drive by the house [now], the windows in the kitchen and bathroom are open—but the home still has a clean, contemporary look. There’s something about being able to incorporate a residential window you can engage with instead of just big, fixed windows. It brings the scale of the house down.
What specific products were used in this project?
GL: We used 50-foot-wide Series 900 Hinged Doors and custom Series 600 Multi-Slide Doors that offer expansive views and bring the outside in when the doors are open. We also incorporated the Series 600 Windows combined fixed glass and operating casements, plus custom Series 600 Windows that extend from the first floor to the angled ceiling.
This home sits on the water. How do the windows protect against the elements?
PE: Western Window Systems’ anodized aluminum windows have a finish that the homeowner doesn’t have to worry about. They’re also rigid enough so that once you sit the window properly, there’s almost no way the operable windows can go out of adjustment as the house ages.
What role do the windows play in achieving the project’s surreal effect?
JW: While you have different geometry with the windows, they all look and feel like a collective family. That’s an important part of holding the house together. PE: I’m actually doing another job with Western Window Systems now. We continue to use its windows because of the product. h
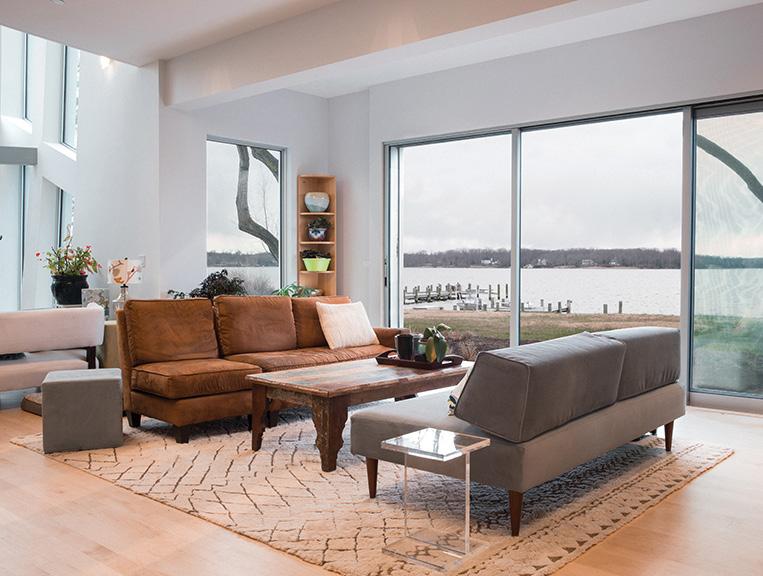
OPPOSITE: A detail of the atrium. THIS PAGE, FROM TOP: The various sizes of custom windows and sliding glass doors used in the project are particularly apparent from the home’s exterior. A view of the project’s interior.