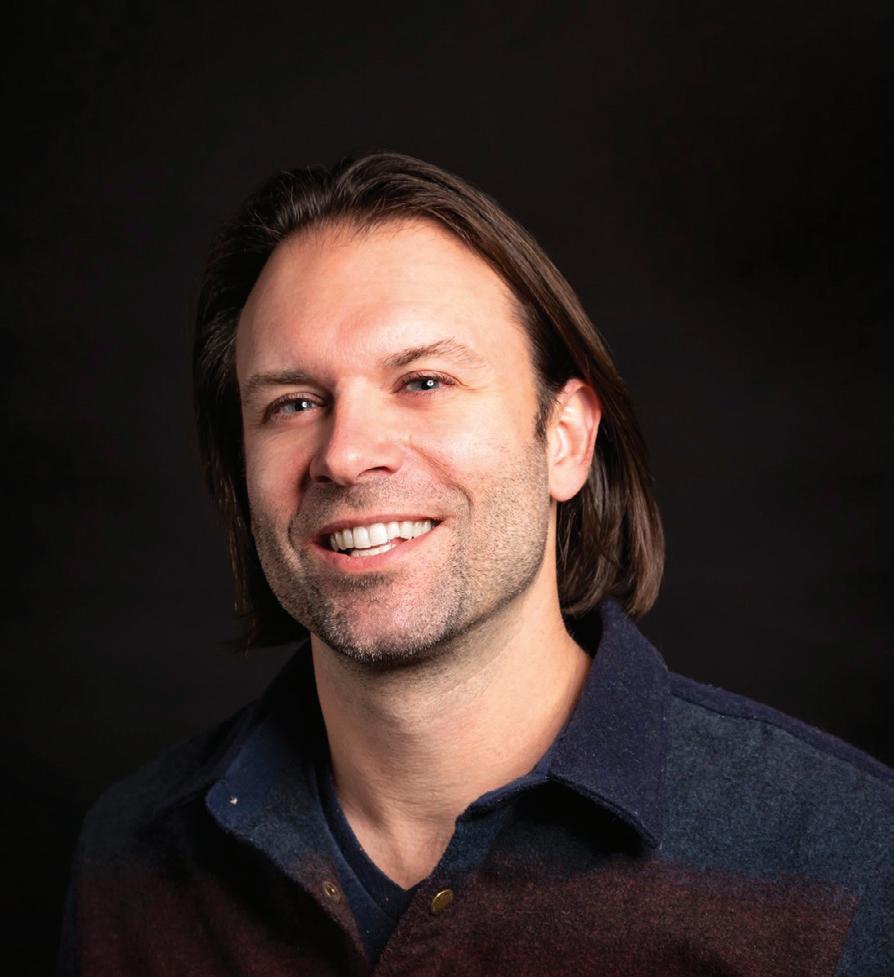
22 minute read
Inside Track
Grumm’s vision takes off during pandemic
Founder, CEO and engineer at Oktober Can Seamers helps accommodate surge in to-go alcohol sales.
Advertisement
Rachel Watson
rwatson@grbj.com
Growing up with a father and grandfather who were mechanical engineers for the aerospace industry, Dennis Grumm has always had an interest in design and engineering — but his passion led him to a different application.
Armed with more knowledge than most about the field due to his family connection, Grumm attended Michigan Technological University in Michigan’s Keweenaw Peninsula — a place he described as “a whole other planet” than Michigan’s Lower Peninsula — graduating with a bachelor’s degree in mechanical engineering in 2005.
“I grew up thinking engineering was a cool thing to do, and I guess I had more knowledge of it than a lot of people,” he said. “If you never have any exposure to it, you might not even know you’re interested in it.”
Grumm, whose family has German heritage, also spent a lot of time in Germany in his youth, referring to it as his “headquarters,” and so he decided to minor in German — a language he has used several times in his career, dealing with manufacturing customers and attending trade shows in Germany.
His Michigan Tech degree stood him in good stead when it was time to job-hunt, he said, as most manufacturers respect that institution and are eager to hire its engineering graduates.
Grumm’s first job out of college was at the Spring Lakebased Campbell Grinder Company, which makes high-precision grinding machines for the aerospace industry.
“One of the ways I’ve described that (company) is they’re the business that made the machine that made the lens in the Hubble telescope,” Grumm said. “It’s a pretty high-tech place, and it was all oneoff projects. The machines were always custom … so everything we worked on was a new problem we had to solve.
“I really got thrown into the fire and had to figure things out and learn pretty quickly.”
During his decade there, despite his youth, Grumm rose through the ranks and ultimately became the research and development group lead, working on high-profile projects for Campbell.
“I was responsible for the complete ground-up design and development of high-precision CNC grinding systems used primarily in the aerospace industry,” he said. “My interest in improved performance and marketability led the company’s modernization and growth in technology, including implementation of many new methods and techniques in the design and production of large, dynamic machines capable of complex 3D surface generation in the 1-micrometers tolerance regime.
“My emphasis on modularization (benefited) the quality, performance, cost, lead times and even appearance of all Campbell grinding systems produced today.”
As he was building his skills, Grumm dreamed of starting his own business one day.
The impetus for his company, Oktober Can Seamers, came in 2014 as Grumm was spending a lot of time in breweries and around home brewers and learning there weren’t a lot of great options for small operations when it came to canning their beverages. Most canneries only will do production on large batches, and bottling can be a pain with the constant need to wash and sterilize.
“I always knew at some point I’d probably start my own company,” Grumm said. “Even when I was going to Michigan Tech, I was already drawing up plans for doing my own thing, just because I always wanted to be in control of my own design projects. I’d been writing down ideas for years, and the can seamer was the first idea that clearly had some customers and there was a market for it.”
Grumm said his idea for the machine was so simple that it didn’t require a huge, up-front monetary investment. He and his business partner, Clint LeaTrea, a childhood friend and fellow Michigan Tech alum, started the company together out of a basement, with no website, and first started selling the invention in 2016. Grumm did the engineering, and LeaTrea wrangled the purchasing and sourcing — roles they continue in today.
Oktober Can Seamers’ flagship product is a hand-operated machine that costs $2,500 and cans one beer — or wine, cider, seltzer, kombucha or wellness drink— at a time. The co-founders source all of their parts locally, leaning on the manufacturing base that already exists in West Michigan.
At first, during the development phase, Grumm continued working full time at Campbell, but it quickly became apparent the business had traction and demanded his undivided attention, so he quit his job and dove in headfirst.
Grumm said he has enjoyed working with customers in the beverage industry, whom he described as a laid-back and collaborative bunch who know a lot about hard work and entrepreneurship.
“Beer City USA” is what gave Oktober Can Seamers its initial business, but the company now has customers around the world, anywhere there’s a concentrated beverage industry, doing direct-to-customer e-commerce and working with international reseller partners.
“(I) definitely enjoy the freedom to make decisions for better or worse,” Grumm said. “If something goes wrong, I don’t have to be annoyed with somebody else about it — at the end of the day, it’s on me. And if something goes right, it’s on me, or on us.”
The company’s headquarters and production are based at 5 Colfax St. NE in Grand Rapids, with another location in Sparks, Nevada, and 16 employees overall.
Oktober Can Seamers currently offers various models of its flagship product, as well as replacement parts and instructions for those to be swapped out with simple hand tools if they wear out. The company also sells cans by the pallet as a service for its clients, since cans usually come by the truckload, which isn’t ideal for small-batch production.
Grumm recently hired more engineers who are working on building more complex machines that can do larger-scale projects, so Oktober Can Seamers can grow with its customers.
While many companies struggled when the pandemic hit, Grumm said it was the opposite for Oktober Can Seamers. As restaurants, bars and breweries were required to shut down unless they could offer to-go food and beverages, suddenly, more businesses needed to be able to can drinks.
“Our machine cans (drinks) to-go, right off the taps. Instead of us shutting down, it was the opposite: Our sales went through the roof for the whole year, basically trying to keep all these breweries from having to close their doors,” he said. “It was madness in 2020.”
The busyness has continued in 2021, with sales far higher than they were in 2019.
Grumm takes his inspiration not only from his dad and granddad — who are both retired but still offer consulting services and occasional advice — but from all the designers, entrepreneurs and engineers in history whose inventions and leadership have powered the world.
Although Oktober Can Seamers has been in business for only five years, Grumm said he still is having fun.
“I’m very proud to have built my business from scratch, with manageable and steady growth over the past five years,” he said. “We currently have two published patents for our products.
“It’s kind of fun to think back on how we started off. If somebody showed me our business right now, I would say, ‘Wow, that looks like a really complicated thing to have done.’ … Step by step, it just kind of grew. Something that I think of is, if you want to do something, you’ve got to just start doing it and see how it grows.”
He said his advice to other startups is that doing everything yourself only takes a business so far. Over time, he added social media coordinators, bookkeepers, accountants and a business-savvy bench of talent, including a team of engineers, marketing and customer relations professionals, manufacturing technicians, and e-commerce and shipping/receiving experts.
“Eventually, (our business) got to the point where we knew word of mouth wasn’t getting out any faster, so then, we started adding some marketing and doing some social media stuff,” he said.
“It was nice, steady growth, but it was good to have that time where it was just word of mouth so we could get our feet wet and learn how to build the machines fast enough, how to make sure that they worked and how to keep our customers happy without growing too fast.”
DENNIS GRUMM
Organization: Oktober Can Seamers Position: Founder, CEO and engineer Age: 39 Birthplace: Shelby Residence: Grand Rapids Biggest Career Break: Landing his first job as an engineer at the Spring Lake-based Campbell Grinder Company in 2006, where he had the opportunity to work on high-profile projects and take on a lot of responsibility for a 24-year-old.
Dennis Grumm knew while he was a student at Michigan Tech he would someday start his own business. Courtesy of Oktober Can Seamers
A late class during her undergraduate career led Shorouq Almallah to turn her attention to information science. Courtesy 616 Media
Autocam Medical recognizes apprenticeship grads
Fourth class of CNC machinist students receive certificates of completion at the AMP Lab.
Rachel Watson
rwatson@grbj.com
The Advanced Manufacturing Partnership (AMP) Lab has churned out another group of CNC machinists from its apprenticeship program.
Kentwood-based Autocam Medical, a global contract manufacturer of precision surgical and medical components and devices, said Dec. 3 it presented 11 students with certificates of completion for their computer numerical control (CNC) machinist apprentice program during a Nov. 10 ceremony at the AMP Lab @ Western Michigan University in Grand Rapids.
The event, recognizing the company’s fourth class of graduates, included a few words of motivation and inspiration by John Kennedy IV, general manager of Autocam Medical, and Bill Pink, president of Grand Rapids Community College.
The year-round program requires students to complete over 700 hours of classroom instruction over a period of 90 weeks. Apprentices are employed by Autocam Medical, maintaining a full work schedule during the training period. In addition to CNC machinist certification, the course of study also covers the necessary schooling required by the U.S. Department of Labor for students to receive a certified journeyman card and puts them on the path to receive an associate degree, earning 27 college credits.
GRCC instructor Andy Beach, an industry veteran with over 20 years of experience, said the program has many benefits.
“Autocam Medical’s apprentice program is a win-win; it’s a win for the skilled trades industry and a win for the students,” Beach said. “The students gain skills that put them on a career path with unlimited opportunity, and it helps build a ready workforce for the manufacturing industry, which is starving for CNC machinists.”
As part of their training, students are challenged to machine two intricate objects. The finished projects are reflective of the caliber of machinists produced by the program, Beach said.
Two graduates, Wrindy Haus-
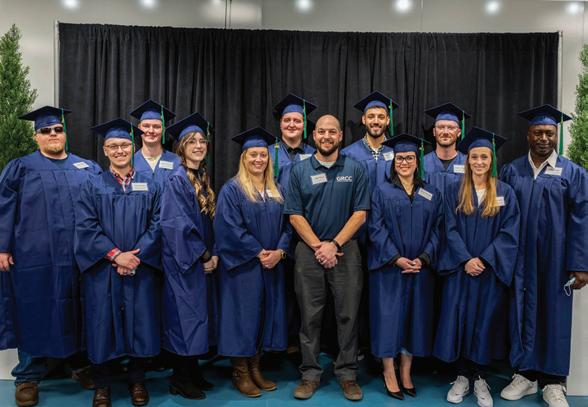
Apprentices are employed by Autocam Medical, maintaining a full work schedule during the training period. Courtesy of Autocam Medical
er and Ethan Richey, recently won a first-place prize in Mastercam’s global Master of CAM Wildest Parts Machining Competition in the teams division for a Thor’s hammer they machined during their apprenticeship.
“Our program is quite uncommon. In addition to the specialized training that our students receive, we pay for 100% of their college tuition and provide them with a full-time job while they are receiving training,” said Kristy White, human resources director for Autocam Medical. “The unique apprenticeship program is a key reason the company was named the Grand Rapids Chamber of Commerce’s EPIC Award winner in the Excellence in Business category this year.”
Autocam Medical is a global contract manufacturer of precision-machined drill bits, drivers, screws, plates, cutting tools and other complex, highly engineered surgical implants, instruments and handpieces, as well as other device components. Its specialties are in CNC milling, turning and cutter grinding.
The company is a supplier to medical device manufacturers around the world that focus on orthopedics; spine; robotics; ophthalmology; vascular; ear, nose and throat; general surgical equipment; and diagnostics.
Autocam Medical has achieved ISO 13485:2016 certification and is a Food & Drug Administration registered facility.
In addition to its facilities in Kentwood, Autocam Medical has operations in Murfreesboro, Tennessee; Plymouth, Massachusetts; Suzhou, China; and Indaiatuba, Brazil.
Autocam Medical is built around investing in employees and their growth within a culture that trusts and respects every individual, the company said, noting its success depends on the knowledge employees bring to the team every day. Autocam Medical provides employees educational opportunities with nocost-to-them tuition, and it offers competitive salaries, quarterly bonus incentives, a 401(k) match and a premium-free health plan.
To keep up with Autocam Medical’s ongoing growth in West Michigan, the company will be expanding its footprint with a new plant in Kentwood, which is expected to be ready for occupancy in January, according to a previous Business Journal report.
The expansion will create 250 jobs, and the company will ramp up hiring of machinists, apprentices, engineers and technicians in 2022. Those interested in job opportunities can contact Kristy White at kwhite@autocam-medical.com.
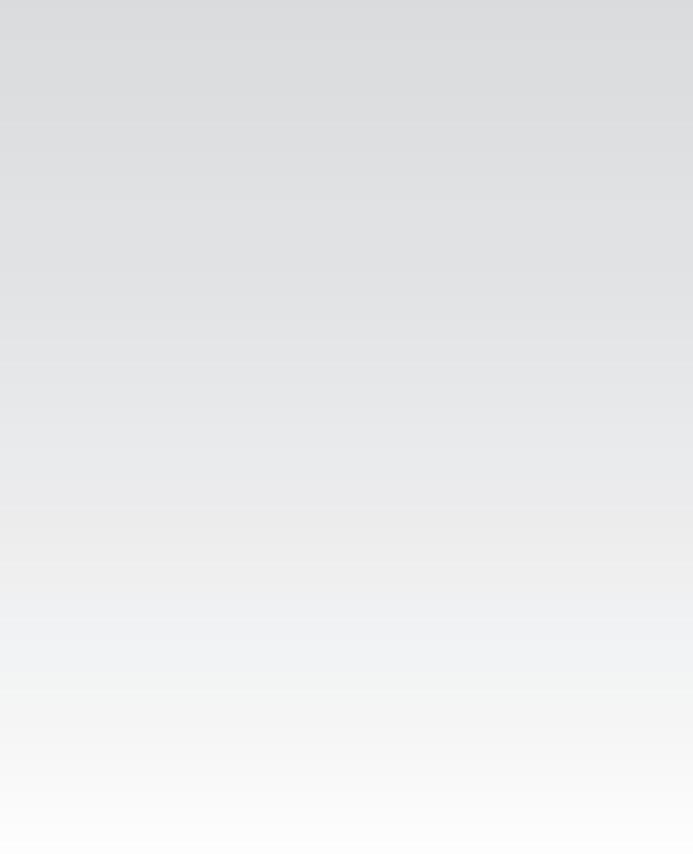
Industrial market bends under weight of demand
CONTINUED FROM PAGE 3
“People want to get into the buildings. I’ve got several people who would like to get into buildings sooner than the building is completed. They are actually signing leases on buildings that have not been built yet.”
To combat the time delay and to meet the demand, Horn said the industry is looking at alternatives such as using different building products during construction. He said precast concrete buildings are becoming more popular in the Chicago and Indianapolis areas than they were in the past. The wall panels in those buildings are cast in concrete, which is more readily available, but the precast-concrete concept has not gained much popularity in Grand Rapids.
Horn said normally the large markets use pre-engineered buildings that have steel wall panel units.
The high demand and lengthening construction times also have led to an increase in prices. Usually, prices change once or twice per year, but now, Horn said, developers are seeing an increase monthly and sometimes daily.
Rantala said due to the postCOVID demand, no one could keep up, and as orders were being filled, ships that transported materials to U.S. ports were waiting to be unloaded.
“They say there’s a shortage of truck drivers but what it is, is there’s only a certain amount of those container flatbeds,” he said. “Once they unload the container from the ship, it gets taken off of the port site, but sometimes they’re stored in fields and that flatbed stays with that container. They need that little flatbed truck to go back to unload more containers and that’s part of the holdup.”
Rantala said he is experiencing the repercussions of that holdup.
“I just had a project where we paid, we knew the ship date, and all of a sudden the manufacturer called the supplier and they called us and said, ‘Oh, by the way, there’s a $4,000 increase in freight,’” he said.
“He was supposed to ship it in three days. We’ve been waiting already for months, and three days before it’s supposed to be shipped, they changed and said here’s a $4,000 change order for freight.
“It’s like we’re being held hostage. That’s how we feel. That is what you have to deal with today, those types of situations. Until it’s actually shipped and on the job site, you have the risk of getting hit with price increases whether it’s on materials or shipping. That’s the reality of today.”
CONTINUED FROM PAGE 3
The GVMC transportation committee handbook indicates deficiencies are identified through a process called the Pavement Surface Evaluation and Rating (PASER) system, where staff representatives from individual jurisdictions collect field data in GVMC’s data collection vehicle. These ratings are then verified by GVMC using data and photos collected concurrently with the automated data collection system.
Federal funds are allocated to projects based on the system’s rating criteria of deficiency severity, and projects receiving funding of any kind are intended to ensure a long-lasting, improved condition. PASER ratings of 8-10 are not eligible for federal funds; a 7 rating is eligible for crack sealing funding; ratings of 5 or 6 are eligible for sealcoat/thin overlay funding; those with a 4 rating can use structural overlay funding; and PASER ratings of 1-3 are eligible for reconstruction funding.
“We have federal performance measures that we have to follow and incorporate into our planning process as well, and so there are performance measures related to congestion and freight, (and) there are performance measures related to safety,” Joseph said. “Each year we have to establish or support targets for different federal performance measures, and safety is one of those measures. We look at the number of crashes, fatalities, and injuries, and the rates of injury and fatality, (along with) non-motorized fatalities and serious injuries and identify where those are occurring. (We then) flag those as safety issues so that we can make sure to incorporate safety improvements in all our projects, as well.”
According to Joseph, 1,547 miles of federal roads were surveyed in the region this year. GVMC also rated 1,037 miles of local roads and the Kent County Road Commission rated 1,014 miles of roads within its jurisdiction. The organization’s deficiency map originally identified 1,517 segments of roadway that are deficient in some way, but Joseph said agencies may split a segment logically or submit a project with multiple segments along a deficient roadway. In addition, there are non-motorized, transit and MDOT needs that are not captured within the deficiency map. New and modified submissions also find their way to committee meetings, and GVMC representatives may move and change projects to meet federal funding targets, making for a malleable number of deficiencies and potential projects, she said.
“Including the current illustrative list, there are over 500 projects total. With the uncertainty related to the additional federal funding that may be coming to our region (from the newly passed federal infrastructure bill), I expect the illustrative list to grow so we are ready if we are able to fund more projects,” she said. “... The number of projects that get programmed really depends upon project costs, but in the last five years we’ve averaged about 115 projects per year in the TIP. … That is one of the reasons why we have really tried to put together a robust, illustrative list of projects so that when we do find out if and how much money we’re going to receive (from the infrastructure bill), that we have good projects to draw from, that we can work fast, and get those improvements in the TIP, as well.”
Joseph said the principal challenge to maintaining pavement in a state of good repair is shortage in funding compared to need. Federal and state agencies provide funding, as well as “locals,” or cities, villages and the county road commission. Locals also have their own funding with a minimum match requirement of 20%.
“So, it’s a lot of federal and state money, but our locals also put in a significant amount. … And a lot of times our locals actually over-match to get more projects into the transportation improvement program so they can stretch those federal dollars. Sometimes, we end up with a 65/35 or a 75/25 match kind of ratio for those.”
All projects using federal transportation funds are required to go through GVMC’s planning process as part of the TIP, with GVMC’s primary goal to use all of those funds, including the Congestion Mitigation and Air Quality Improvement Program (CMAQ), which provides funding to states for projects designed to reduce traffic congestion and improve air quality.
Joseph said the organization encourages public comment and attendance at planning meetings for well-rounded input on transportation priorities and where dollars are spent. More information is at gvmc.org.
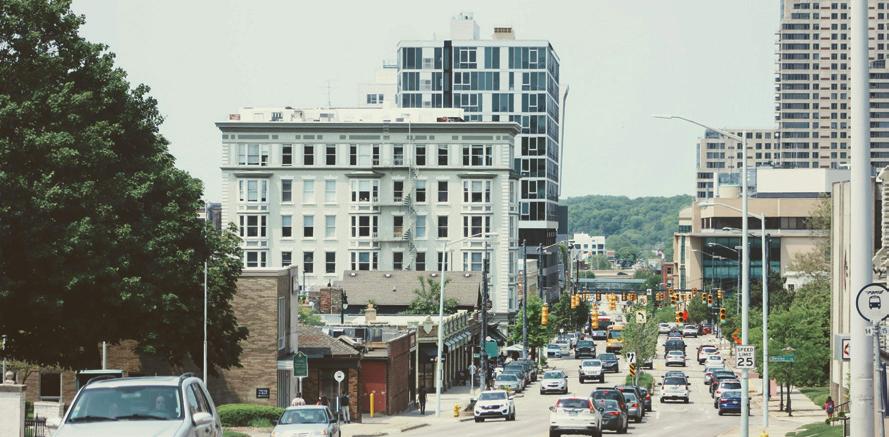
GVMC’s transportation plan includes roadways that are under federal, state, county and local jurisdiction. Courtesy of Kendell Joseph

2021 & 2022
Your #1 choice
BACK 2 BACK HONOR Engineer uses experience to promote STEM in schools
CONTINUED FROM PAGE 4
structors visit two schools, including Dickinson Academy, where she went to school, and Martin Luther King Academy, twice a week for eight weeks.
STEM Scholars is an afterschool program for students who are enrolled in schools that do not have science teachers. Christopher currently is working with four schools.
“We go to the schools that don’t have science teachers for its middle school students,” she said. “The school that I started with is a school that I went to for elementary school. Now it has been converted to a K-8 building but the students still have one teacher all day, just like they were in elementary school. They don’t have a science teacher. They have one teacher trying to teach everything and science is the last thing on their mind. Plus, they usually don’t have a science background and they don’t have any budget for the science supplies. I started with one school and now we’re up to serving four schools, but there are additional schools that don’t have science teachers. There is a lack of science teachers. There is a lack of math teachers in our school systems, just teachers in general. There is a teacher shortage.”
Sankofa STEM Academy is a five-week summer camp program that is held at Davenport University.
It focuses on math and science proficiency for middle school students. The program includes expert speakers in the STEM field, hands-on experiential learning and field trips.
In addition to focusing on math and science, Christopher also incorporates technology and engineering in her programs. During the summer at Davenport, STEM Greenhouse worked with Loop Coding Center and its coding instructors to teach students coding.
The engineering aspect of her program, Christopher said, is applying math and science to solve problems using the engineering design process such as the science method of doing research, creating a hypothesis, testing the hypothesis and coming to a conclusion.
“We give kids real-world problems and tell them to use the math and science that they have learned to solve that problem,” she said.
“We come up with a lot of activities where they have to get creative and utilize what they’ve learned in math and science to solve a problem. There’s all kinds of little problems that we come up with, but we want them to know that there is an engineering design process, and we want them to try to learn how to go through that process as well.”
Nursing shortage renews push for patient load limits
Nicholas Simon Capital News Service LANSING — A staffing crisis at Michigan hospitals has renewed efforts to protect nurses from unmanageable patient loads and too many hours of consecutive work.
The Safe Patient Care Act, first introduced in 2017, has picked up additional cosponsors from both parties in the House and Senate. It seeks to regulate how many patients a nurse can care for and the number of consecutive hours that they can work.
It would also publicize hospital nurse-to-patient ratios.
Nurses are “forced to make painful choices every day,” Jamie Brown, president of the Michigan Nurses Association, said in a statement.
“The hospital industry has been purposely getting by with inadequate (registered nurse) staffing levels for years,” said Brown, who leads the state’s largest nurses union.
“Nurses have long warned that our communities would suffer the kind of dangerous crisis that nurses and patients are facing now. The pandemic has only worsened and exposed hospitals’ emphasis on money above all else,” Brown said.
The union says that those choices are a result of hospitals trying to protect their bottom line. But Brian Peters, chief executive officer of the Michigan Hospital Association, argues that government mandates for every hospital would be ineffective and make it harder for hospitals to operate.
“The one-size-fits-all approach inherent in legislatively mandated decisions impacting clinical care typically fails to recognize the complexity of patient care and the diversity of health care environments,” Peters said in a statement.
Unlike truck drivers, air-traffic controllers, pilots and rail operators, nurses have no federal limit on how many consecutive hours they can be forced to work, according to the Michigan Nurses Association.
Nurses can be fired and have their licenses stripped for refusing forced overtime even if they don’t feel fit to work because hospitals can claim that they are abandoning their patients.
Medical errors are the leading cause of preventable death, beating out smoking and obesity, according to the Journal of Patient Safety.
Nationally, the Nurses Association estimates that 440,000 people in the United States die every year due to infections and
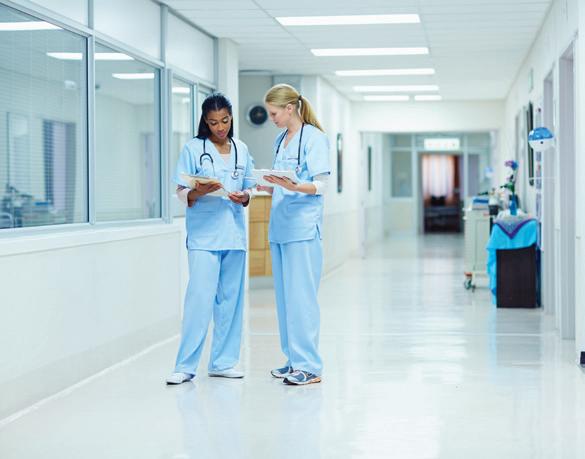
Unlike truck drivers, air-traffic controllers, pilots and rail operators, nurses have no federal limit on how many consecutive hours they can be forced to work. Courtesy of istock
delayed or incorrect medications, problems that proper nursing care could prevent. Studies over the past two decades have linked patient mortality and staffing ratios, according to the union.
In Michigan, even before the pandemic, one in five nurses was aware of when understaffing led to a patient’s death, and half of registered nurses said they are assigned unsafe patient loads at least half the time they are working, according to the union.
Hospitals say that staffing is a collaborative process and fixed ratios “don’t allow for flexibility and innovation,” said John Karasinski, communications director for the Michigan Hospital Association.
“Every hospital in Michigan has a process in place to ensure that each of their clinical units is appropriately staffed,” Karasinski said. “These processes are based on individual patient needs and the training, experience and capabilities of the entire clinical care team, including nurses.”
However, half of Michigan nurses say hospitals rarely or never adjust their schedules, even when they report unsafe workloads, according to a survey paid for by the Nurses Association. The majority (80%) of Michigan nurses are not protected by a union and face harsh repercussions for speaking out against hospital practices. The Nurses Association reports that multiple nurses have been fired over the last two years for trying to raise the alarm over this issue, worsening staffing shortages that already are at crisis levels.
Staffing shortages are affecting hospitals across the state. The Michigan Hospital Association said 80% of nursing groups nationally have reported an increase in turnover due to the pandemic and that there are nearly 2 million openings for nurses across the country.
“Hospitals want to hire more nurses, and they want to retain the nurses they currently employ, but the current national demand for nurses far exceeds the available supply,” Karasinski said.
The Michigan Nurses Association said the Safe Patient Care Act will bring nurses back to work. It points to data from the federal Department of Health and Human Services that indicates
CONTINUED ON PAGE 18
