
2 minute read
Creating a Complete Workspace Solution Through Innovation and Technology
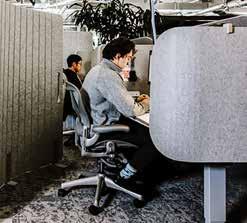
Written by: Jonathan Webb, Director of Workplace, KI
No two customers have the same needs when it comes to workspace design. Unfortunately, many workspace design manufacturers take a cookie-cutter approach, attempting to create a one size fits all solution that gets applied to every client. Yes, it may solve “a few” of each client’s challenges, but ultimately, it will not meet all the desired outcomes of each individual client.
KI has taken a revolutionary approach with its Infinity process, one that provides each client with a unique, personalized solution that utilizes innovative designs to expressly meet each client’s individual challenges. This is due to KI’s vertical manufacturing process that allows complete flexibility in design solutions. This is vital today as the newest generations entering the workforce are choosing to work for companies that place an emphasis on workplace design that is conducive to a more holistic view of health and well-being, important aspects that often weigh more heavily on a potential new hire’s decision of where to work than does pay and vacation time.
The Infinity process takes a collaborative approach that starts with listening. It’s more than just hearing what they are saying, but instead, truly listening as the client highlights the challenges they face and needs they are looking to meet. This involves asking probing questions to fully explore and drill down for a complete picture of each client’s workspace needs and challenges.
From there, the client and design team exchange ideas, clearly define objectives and then continually tweak ideation that results in new discoveries, which more often than not, leads to new, innovative products specifically designed for that client.
In fact, through the Infinity Program, more than 20% of KI’s products are modified or co-created with the clients, making them distinctly unique to achieve the client’s needs. Once the design is created, they are then prototyped, tested and refined to ensure it meets the desired needs.
That’s where technology comes into play and KI is at the forefront, incorporating new technologies throughout its facilities, allowing for even greater innovation. One such technology is the addition of a 950-ton, “two-shot” injection molding machine to its Green Bay facility, allowing it to mold two-color, polypropylene shells. This was a first for the industry, creating a new process to add two different colors into one mold. This not only streamlined the manufacturing process for this style of chair but created a two-tone chair that has a sleeker design, with no seams. Robotics also play a key role in the process, and KI strategically utilizes robotics to complement work completed by its team members. Whether it’s a part of the molding process, welding, the coating process or during assembly, robotics are integrated to streamline the processes and reduce opportunities for workplace injury. They are also used in quality control testing to ensure each new design created can withstand the rigors of daily use.
The culture of innovation instilled throughout KI has allowed it to remain an industry leader by designing products specifically to address the individual needs of large companies such as Meta to smaller companies that require unique designs to meet their need. Ultimately, KI remains focused on designing new products that align with, and define, the workspace of the future.
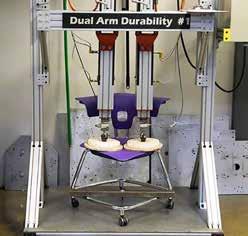