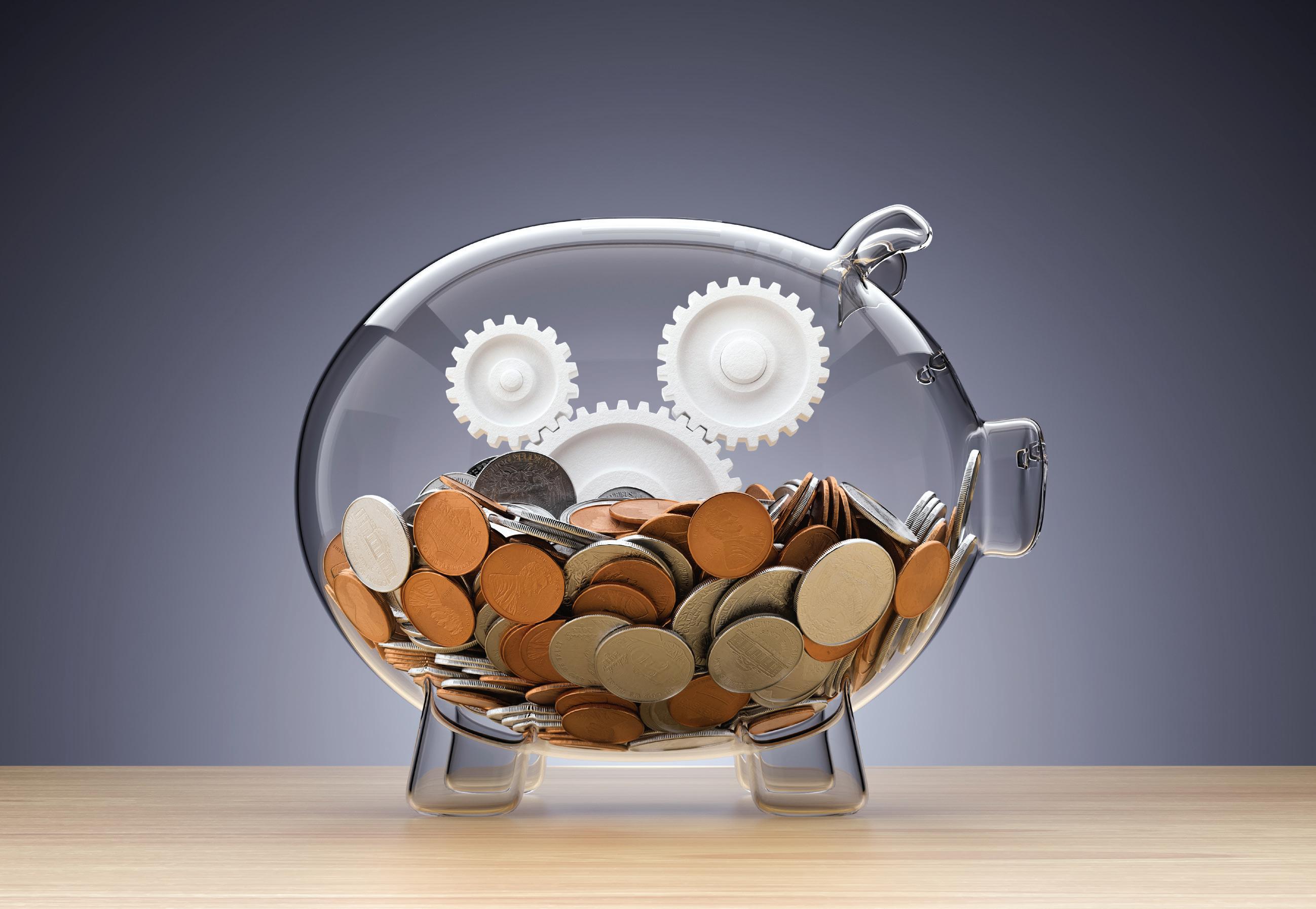
5 minute read
Streamlining Operations
Streamlining
OPERATIONS
New CIO of First Mutual Holding implements Lean Six Sigma at First Federal Lakewood.
By Linda Feagler
Expediency. Efficiency. Excellence.
Kathy Dockery, SVP, chief information officer of First Mutual Holding Co. (FMHC) — the parent company of several mutual banks, including First Federal Lakewood — is excited about bringing Automation and Lean Six Sigma (LSS) to the organization.
As leader of FMHC’s IT division, she’s in the process of developing a digital strategy that will streamline operating systems at First Federal Lakewood and FMHC’s other affiliate banks. Before joining FMHC in July, Dockery was a technology director at Fifth Third Bank. For two decades — prior to joining Fifth Third — she served in a variety of technology roles at Key Bank, including spearheading the development of a Digital Business Automation Center of Excellence. Dockery received her bachelor’s degree in organizational development from Baldwin Wallace University, earned an associate degree in computer science from Cuyahoga Community College and completed the Women in Stem Leadership Program at Case Western Reserve University.
“My focus is on delivering technology business solutions in partnership with key business units and affiliate banks to meet objectives, create agility and improve the employee and customer experience,” she says.
Employing Automation and LSS principles are a driving force to meet those objectives. In order to remain competitive, Dockery explains, an organization must be continuously striving to improve in ways that increase innovation while lowering costs, streamlining processes and adapting new technology.
LSS is not a new concept. It combines Lean and Six Sigma approaches to create an organized solution for process design. Lean is focused on minimization of waste, errors and delays. Six Sigma focuses on quality and consistency through process improvement and reducing variations. Combining both into LSS delivers customer value through efficient operations.
Although applying Lean thinking to


— Kathy Dockery
design processes was born out of manufacturing, it is used in all verticals now. Today, Lean means working smarter. It is, Dockery adds, a tool that’s rooted in systems thinking — a methodology based on studying the system and each of its individual parts in order to make decisions that enable the organization to do its best work.
Another tool in the toolbelt is Robotic Process Automation (RPA). RPA is an automation technology that emulates human action on a keyboard, creating digital workers referred to as bots. RPA makes work more efficient and effective by automating employees’ repetitive tasks, including transferring of data from one system to another. The bots also eliminate human error, thus ensuring the work’s error rate is greatly reduced. Combining the benefits of RPA with the benefits of LSS creates a powerful duo in reducing overall business costs.
“Let’s say I’m a bank employee working through an account dispute with a customer,” Dockery says. “When a dispute happens, there’s a lot of information that needs to be gathered about the case. The old-school way to handle this would be to have the employee investigate the case by gathering information from a variety of places. But once you automate, the bot can gather all of the information and place it in a folder overnight. When the person in charge of evaluating the dispute comes in the next morning, all of the information will be in one spot. The bot has done the research and saved the employee from spending hours of time digging through files. And the customer is happy because the problem has been resolved faster and in a more consistent manner.
“From a business standpoint, you’re saving hours of an employee’s time,” Dockery continues. “From an employee’s standpoint, you’re taking the bot out of the human. You’re taking tasks away from them that can be numbing and mundane and replacing them with strategic items to work on.”
Dockery and her team have begun determining which automation system will work best for the bank. She adds that embracing automation at First Federal Lakewood is key to not only keeping valuable employees engaged, but attracting top candidates now and in the future.
In the past, corporations have had separate LSS and Automation teams. Discovering the synergies between LSS and Automation, the latest trend is to combine these into one team, thus taking advantage of the powerful duo to utilize the methodologies in the redesign of the selected processes before automation.
This is not a one-and-done initiative. In order to be successful, you need to cultivate the mindset of Lean process and automation throughout the corporation. If effective, ideas on which processes to target will begin to come from the ground up and result in a cultural change that sticks.
The first step is to put together the team or Center of Excellence. This team will lead the change throughout the organization and create the framework for process selection and automation. They will be the governing body determining the guardrails and embedding the methodologies deeply and effectively into the organization. The next step is to create a committee of leaders across the different lines of business. These leaders will be the champions throughout the organization and determine the potential target processes within their departments.
“They will be the ones who will evangelize and help those within the organization get behind the process as they see the benefits firsthand,” she states.
The third step is picking your automation platform and selecting processes that are ripe for these practices. Learn from companies in your vertical that have gone before you. Find out what processes they have Leaned and Automated to determine which are easy fruit on the ground for you to start with and which ones have had the highest return on investment to add to your list.
Once the system is up and running, it is important to get a couple of quick wins early. The champions can take these quick wins and show the benefits within their departments so the employees can see how it not only helps the corporation, but also helps them. This is where the cultural shift begins to happen.
“Lean Six Sigma and Automation isn’t just for large or mid-size companies, any business can benefit, no matter the size,” she concludes.
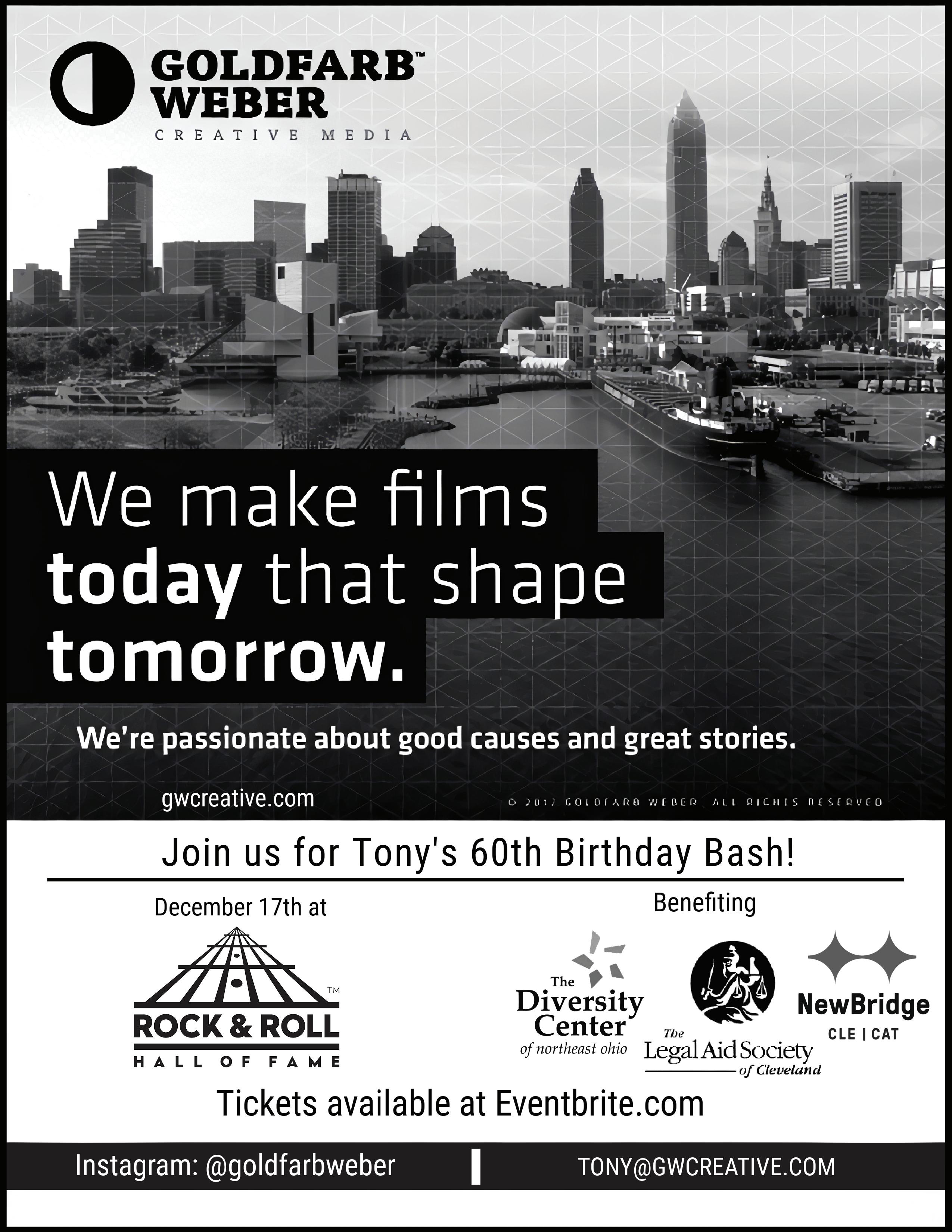