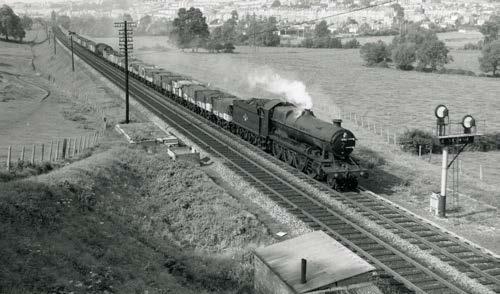
10 minute read
Part 3 – Paul Perton
Paul Perton, Marketer, Writer, Photographer
It would be easy to imagine that re-creating a century-old steam locomotive would be pretty straightforward, given the technology available today. It surprises many people that it’s not.
Advertisement
Railway preservation is beset with problems that can be mountain-like, impeding progress. It goes without saying that the finance to re-build, recreate, maintain and run steam locomotives is hard won. Money has to be spent wisely, carefully and for the maximum benefit of the project. Yet, despite that, the plans often turn out to be in conflict with personal ideas, loves and agendas.
Clearing the money hurdle is just to be confronted with even more problems that have to be negotiated, before that first release of steam into the cylinders can be anticipated.
A good idea ought to morph into design and action, but all too often, an argument develops on day one; which loco? What will it do - preservation services, or main line? Where will it be designed, built, stored and run. What era of its history will it represent? What colour should it be? Lined or not? Is that even possible, given the resources available?
The work of the steering committee designated to start the decision making can last many months. If all goes well, a strategic plan will eventually emerge.
The searching for information, drawings, photographs and available components then gets underway, alongside an initial round of prequalification discussions with potential engineers, builders and other interested parties.
In the case of 4709, the Barry Ten assisted with some critically important components, most needing renovation themselves. Drawings were sourced, with a huge effort from the Great Western Society’s archive at Didcot. That left us about a third of the way into the project to re-create a giant G.W.R. 2-80. What next?
Swindon’s drawing office was renowned for its prodigious output, much of which has been lost over the years, or found its way into landfill sites. Some drawings hide determinedly on shelves and private collections, though.
New CAD technology has enabled us to recreate many designs, especially for 4709’s huge cylinders. Currently underway, the casting of these multi-tonne monsters as driven by a CAD design, modified to allow for the changed loading gauge, is now necessary to run 4709 on the main line. Being computer-based meant those drawings could be used to drive the profiling machine used to cut the necessary casting patterns from massive, solid blocks of polystyrene. In a bygone age, this would have required hand making wooden patterns, adding many months and considerable cost to the project. Today’s technology definitely has a place.
But not everywhere. Donor parts arrive in many different stages of wear, tear and corrosion. Headed for re-engineering, the level of detail and often non-availability of original drawings for these components, quickly necessitates a trip back to the drawing board. There, we often learn that the
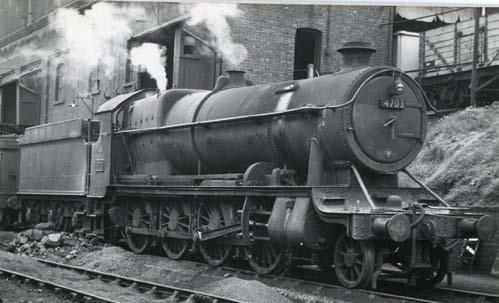
benefits that experience, hands-on observation, measurement and design bring can still largely outweigh modern CAD technology. 4709’s pony truck languished in pieces until work on the chassis reached a point where its renovation and use became a critical part of the project. Work has started in earnest on this component and subsequent stripping down has revealed many missing and worn out components. The team also discovered that simply fitting the 41XX truck to the larger and heavier 47XX was not possible. Recently recruited preservation specialist Bob Meanley, set about the task of re-engineering the pony truck, opting for a drawing board, parallel slide and his pencil, to speed and detail the project. Like any preservation project that has main line aspirations, we are required to conform to the current Network Rail (NR) loading gauge, which has required considerably more work than just changing the width of the cylinders. From the 4709 project’s earliest days, Don Ashton spent months poring over many drawings, checking the implications of compliance with the revised loading gauge.
Given the age of the technology it employs, it’s probably surprising to discover that a steam locomotive is an excellent example of a complex system. So, every component has interdependencies and thus, making a design change to any one part will invariably cause a cascade of changes elsewhere in the system.
In our case, the first obvious change was to the height of the locomotive. 4709 is classified as a Rebuild Project, rather than a new build, meaning our original 13ft 4in height had to be reduced to
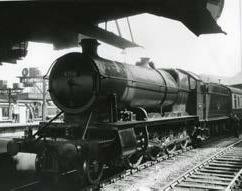
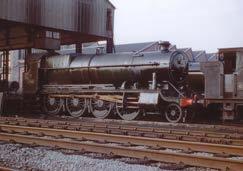
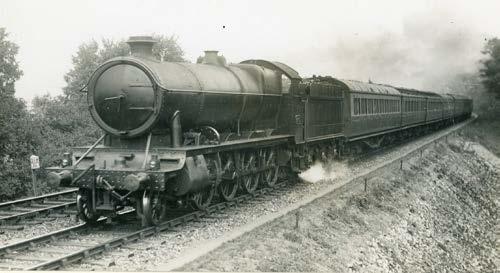
13ft 1in (instead of the 13ft 0in specified for new locos). With Dennis Howells’ help, we realised that to comply, the height of the boiler needed to be lowered by 2in. Fortunately, the gap between the top of the frames and underside of the boiler on a 47xx is 8in, so this small change would be virtually invisible and would not impact on the overall look of the engine.
Could it be that simple? Of course not. We studied the frame and stretcher plans and immediately realised that the resulting repositioning of the firebox throatplate would make it necessary to also move two frame stretchers. In turn, this pushed the lower stretcher extremely close to the adjacent horn block. More problems to overcome.
To successfully achieve the change, it was also necessary to reduce the height of the saddle by the same 2in, but it’s a critical part of the loco’s cylinder casting. Originally, we had planned to use the cylinders recovered from 2861, however this saddle was not only at the wrong height but would be the wrong radius for 4709’s boiler.
Don Ashton came up with a solution which resolved both of these issues. However, costing the work needed to restore the old cylinder block and given that it could still cause unforeseen problems, it was decided that new cylinders would cost more, but represent a much reduced risk and deliver a much longer service life.
Cylinders.
Our saga of polystyrene patterns for 4709’s cylinders, the associated difficulties and the closing of specialist foundries has been discussed extensively elsewhere. Suffice to say that at the time of writing, one cylinder is cast, the second due towards the end of April 2021.
By now, we’d achieved a height reduction of 2in, but 4709 still needed to lose a further inch. Again, Don spent months on his drawing board sympathetically reprofiling the chimney, bonnet and cab sides to fit within the new loading gauge. It was critical not to detract from the overall look of the

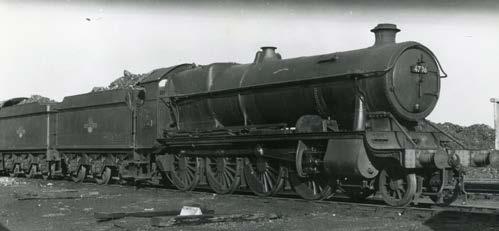
47XX and Don was very successful in providing us with working drawings, detailing these minor, but vitally important changes.
There still remain some issues to be resolved. Due to the lowering of the cab floor, the vacuum brake cylinder and several other vital components also need to be slightly relocated, doubtless setting off another chain of interdependency-related issues to be solved.
Nearer the time, we will be paying similar attention to the height of the blast pipe in the smokebox. Its critical relationship with the petticoat pipe choke diameter is the basis on which 4709’s good steaming will depend.
In addition to the build and fabrication work, these many and time consuming adaptations have been necessary to accommodate refurbished ‘donor’ parts and the overall savings they represent. It will also mean that 4709 will then be in the so-called Barry Condition, ready for restoration to commence.
4709 Front End Progress
After half a century at Barry, exposed to the elements and sea air, parts of what is intended to become 4709’s pony truck, have predictably, corroded. Now, they need to be replaced.
The pony truck resembles the letter ‘A’, and was originally fabricated from many components that were common steel sections at that time, or heavy items which had been forged, bent and curved in three dimensions. Understandably, many of these sections are no longer available and so, renovation
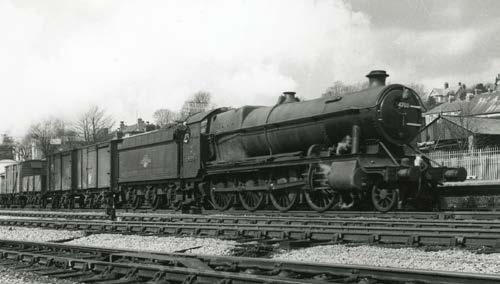
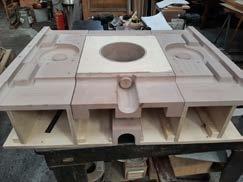
4709 centre stay pattern under construction 4709 centre stay pattern ready for use
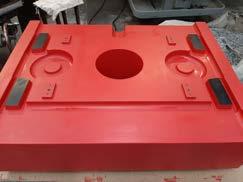
for mainline use involves a detailed and thorough assessment of each and every component.
Then comes the challenge of whether it would be more economic to replace with new, rather than repair. Interestingly, no modern day fabricators are able to bend the 5”x 5” x 5” x ½” T sections with which the pony truck radius bars were fabricated and so the originals have had to be sent away for specialist weld repairs to meet the approval of the VAB. Clearly Swindon had no problems in bending these sections in the day; providing a good indication of the capability and knowledge that has been lost.
It was always intended to fit the entire front end of donor loco no. 4115 to 4709, so we could be confident that it would work as a proven and selfcontained unit. However, a general arrangement drawing of the proposed configuration quickly showed that this plan was unworkable; at 6 cwt, 4115’s leading frame stay was too light for a 47xx. The original 47XX stay weighed some 2 tons. Back to the drawing board - literally.
Making the New Frame Stay Casting
A new frame stay casting is needed as the function of this huge block of cast iron is to stabilise, stiffen and dampen the entire front end of the locomotive. In addition, the stay will contain a 10 inch diameter hole through which a heavy cylindrical counterweight will rise and fall as the wheels follow the track, moving compensating beams that connect to the front of the leading axle springs. This arrangement enables the leading axle to allow for the deflection encountered by the pony truck’s wheelset. On 4709, this casting will be hidden under the running boards ahead of the smokebox. A bell shaped cowling will cover the 10” hole for the counterweight. A 3D model was produced for the pattern. Caddick and Moss of Bristol – the company that previously produced patterns for 4709’s wheels and dragbox, has subsequently completed these patterns, which are due to be cast shortly. Patterns have also been commissioned for the compensating beams themselves which will be cast in steel in the next few weeks. In the meantime, work on 4709 is progressing with the machining of fourteen new spring hanger brackets and the ongoing refurbishment of the (re)usable components from the loco’s pony truck assembly.
Cylinder No 2 Successfully Cast!
There was a great exhalation from the 4709 team this week (w/e 14 May), when the brandnew casting for the loco’s second cylinder emerged from its giant sand mould.
Preparing to pouring the melt at around 1300C
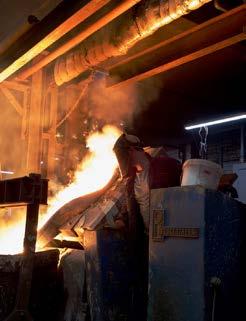
Poured on Thursday morning 6th May, Boro Foundry in Smethwick filled the mould with 2,646kg of molten metal, at an average temperature of 12800C. The pour took less than five minutes; the culmination of many weeks of work, planning, testing and preparation. Throughout the pour, flames leaked spectacularly from every joint in the sand box, as the hot metal ignited the gases generated by the burning of the polystyrene pattern.
The massive cylinder then sat for the best part of a week; “We’ll strike the mould next Tuesday or Wednesday, but expect the metal to still be red hot,” said Boro’s Sam Edwards at the pour. “It’ll take several more days to cool sufficiently for us to examine and check that the pour was successful.”
It was and the cylinder was shot blasted and had its running (pour) system removed. It will now join its sibling, cast several weeks ago. Both will be heat treated to relieve internal stresses, after which they will be machined and joined as a pair.
Completed and installed in 4709’s chassis, the cylinders will be a critical part of 4709’s front end. “In addition to their role in converting steam to motion, the cylinders will also provide a physical datum for measurements and alignment for the hornguides, wheels, axles and motion. Once we’ve got this casting in place, we can start planning for 4709 to become a rolling chassis,” adds Paul.
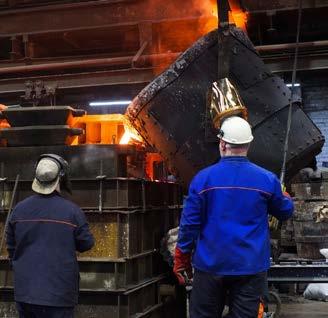
(Above) Pouring the melt (Paul Perton) (Below The Casting ready for inspection, machining and heat treatment (Sam Edwards, Boro Foundry)
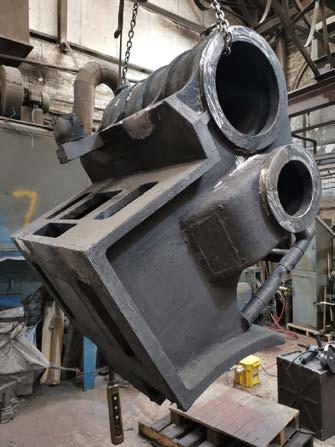