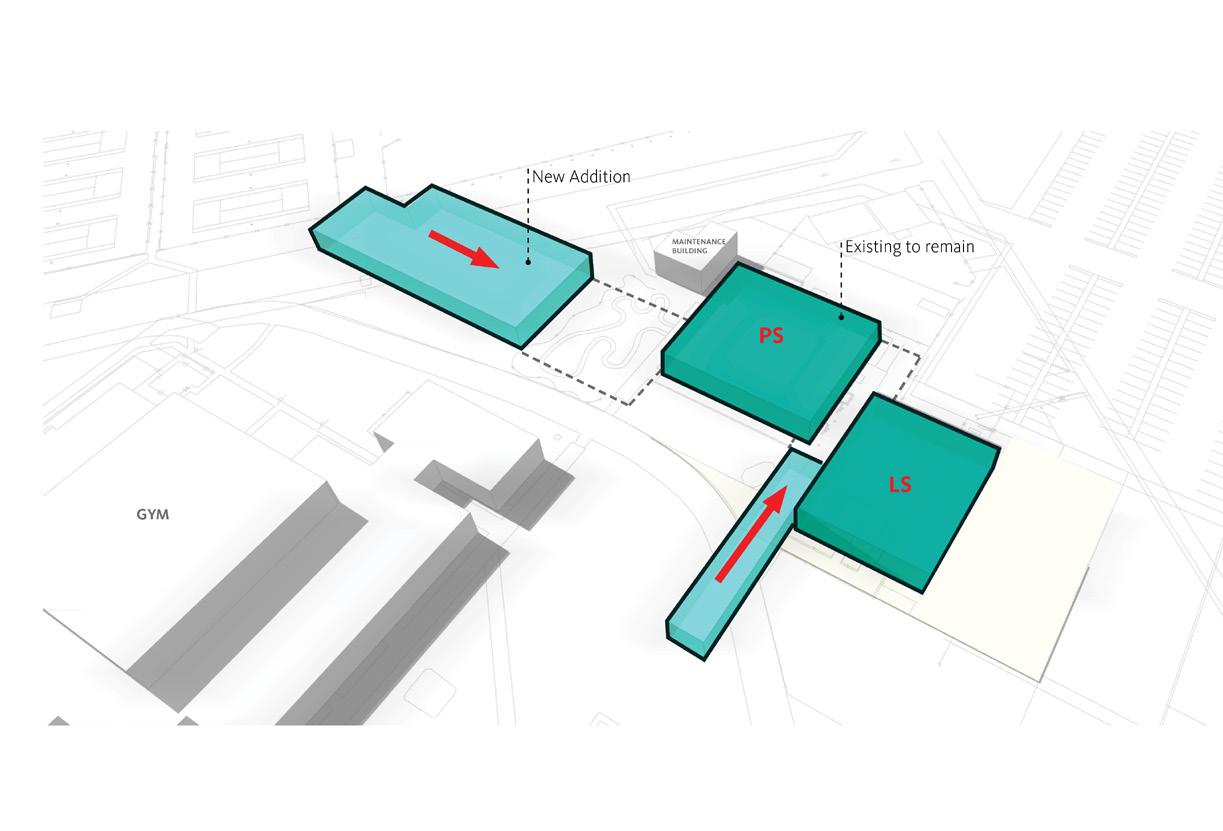
5 minute read
COP26 Strategies for Decarbonization & Impact on the Environment
COP26
Strategies for decarbonization and impact on the built environment
BY JOHANNA COLLINS
TThere is a direct relationship between carbon dioxide emissions and global warming. It is of great importance therefore to get carbon dioxide emissions to zero.
The real estate industry makes up 49% of global carbon emissions when accounting for construction and building performance. Most carbon-reduction efforts in the building sector have focused on operational carbon — the carbon dioxide emitted when a building or systems are in operation — so that properties consume as little energy as possible. And while these efforts have advanced the industry's goal of getting buildings closer to net zero operationally, we can no longer ignore that building materials account for half of a building's total lifetime carbon footprint. At COP26 – UN Climate Change Conference, Gensler, a global architecture, design and planning firm, with offices in Phoenix, announced its green-materials initiative – a move that has the larger goal of shifting the real estate value chain towards net zero carbon emissions. This year marked the first time the annual conference had a showcase on buildings; and only the second year where an entire day was dedicated to discussions on the built environment and real estate development. Enlai Hooi, the Copenhagen-based head of innovation at Schmidt Hammer Lassen Architects, said, “An architect who creates just three typical buildings over their career will be responsible for carbon emissions equivalent to the lifetime emission of 162 typical Americans.” This illustrates the critical role and responsibility architects, engineers and anyone in the real estate and construction sector carry in combating climate change. STRATEGIES FOR DECARBONIZATION IN BUILDINGS During a typical lifespan of a building 72% of carbon emissions are associated with operational carbon and 28% are associated with embodied carbon. This is the carbon emitted during the sourcing and production of a material and ending with the completion of construction. To lower this number, materials must be selected and specified by evaluating their life cycle and look at environmental product declarations (EPDs) for specific products or product categories, which document product global-warming potential. We must also work with our clients and partners and strive to reuse whenever possible, right-size and build only as much as we need. By building only when we need to, at Gensler, we reduced 95% of embodied carbon emissions in 2020. By building only as much as we need to, by working with our clients and employing strategies to truly understand how they use their space, we achieved 60% of space savings that same year. REPOSITIONING – STRATEGIES AT SOUTH MOUNTAIN COMMUNITY COLLEGE (SMCC) – LIFE-SCIENCES/ PHYSICAL-SCIENCES (LS/ PS) PARTIAL RENOVATION AND NEW ADDITION While knowing that reusing an existing structure is an important first step in lowering carbon emissions associated with our work, we wanted to quantify the amount of carbon diverted from the atmosphere by preserving an existing structure. We were interested in studying the carbon footprint associated with each material, in the existing structure, as well as the new addition.
To do this, our Phoenix team collaborated with our structural engineering partners Meyer, Borgman, & Johnson, in creating a case study project. The SMCC – LS/PS project consists of a partial renovation of the LS/PS building, a total of 15,665 square feet and a new 18,164 square-foot addition. We are preserving the exterior EIFS envelope, steel structure and slab as much as possible, to accommodate the new program and adding a steel structure, masonry walls, windows and storefront throughout, new roof throughout, and slab as a new addition and expansion.
The analysis was performed using Tally - a Revit plug-in and a cradle-to-grave life cycle assessment (LCA) tool. We began our study by creating a baseline, a from-theground-up building using the same materials and area, as the existing LS/PS buildings and the new addition, as designed. The new construction of this building envelope and structure would result in a total of 740 tons of carbon dioxide equivalent (CO2e). To help illustrate this, we use the average carbon footprint for a person in the United States, 16 tons per person per year - one of the highest rates in the world. The global average is four tons per person per year – this would equate to an annual carbon footprint of 46 Americans. We analyzed the embodied carbon of the existing structure and envelope and learned that by doing so we are diverting 220 tons of CO2e from the atmosphere, a 30% reduction of carbon emissions in comparison to new construction. This equates to the annual carbon footprint of 14 Americans. Those numbers are significant, considering the amount and rate of construction in our valley and globally. While we anticipated a high embodied carbon associated with steel and concrete, what was interesting is that the highest embodied carbon in the existing building was associated with the insulation of the EIFS enclosure. This discovery led us to a “deeper dive” of the environmental impact of this category and by using EC3 (Embodied Carbon in Construction Calculator) the team selected a material with the lowest embodied carbon. This case study is just one example of the impact design strategies can have on a project by collaborating with our partners, asking the right questions, being curious and using the tools already available to us. At Gensler, we strive toward the elimination of all greenhouse gases associated with our work and the announcement of our new green-materials initiative at COP26 in 2021 marks an important next step in meeting our goals. We, like our clients and other industry leaders, share a commitment to exceed previous sustainability commitments and 2050 goals, and to accelerate decarbonization efforts over the coming decade. This will require collaboration with partners from all sides of the building sector, from finance and insurance to construction, operations and design.
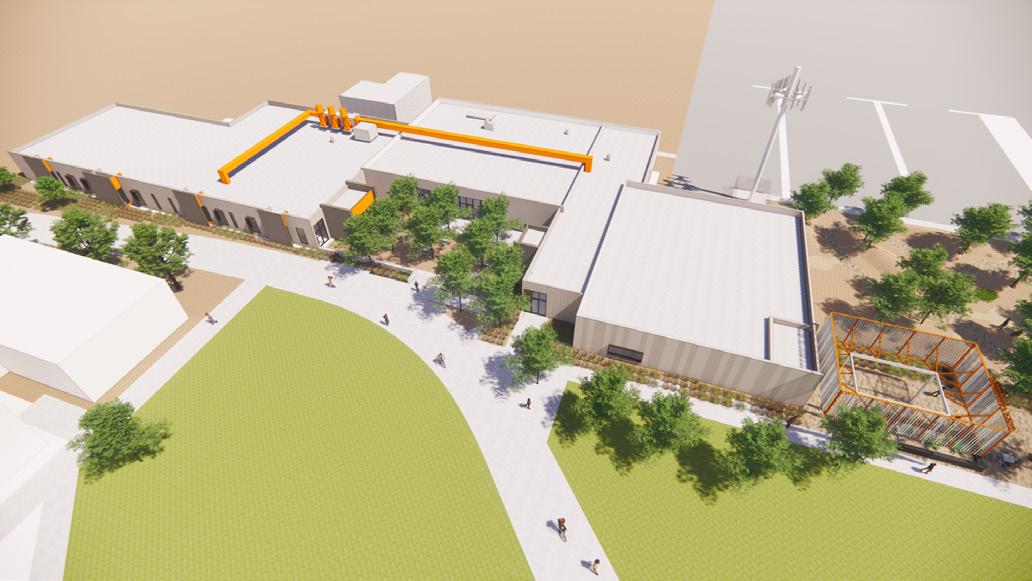
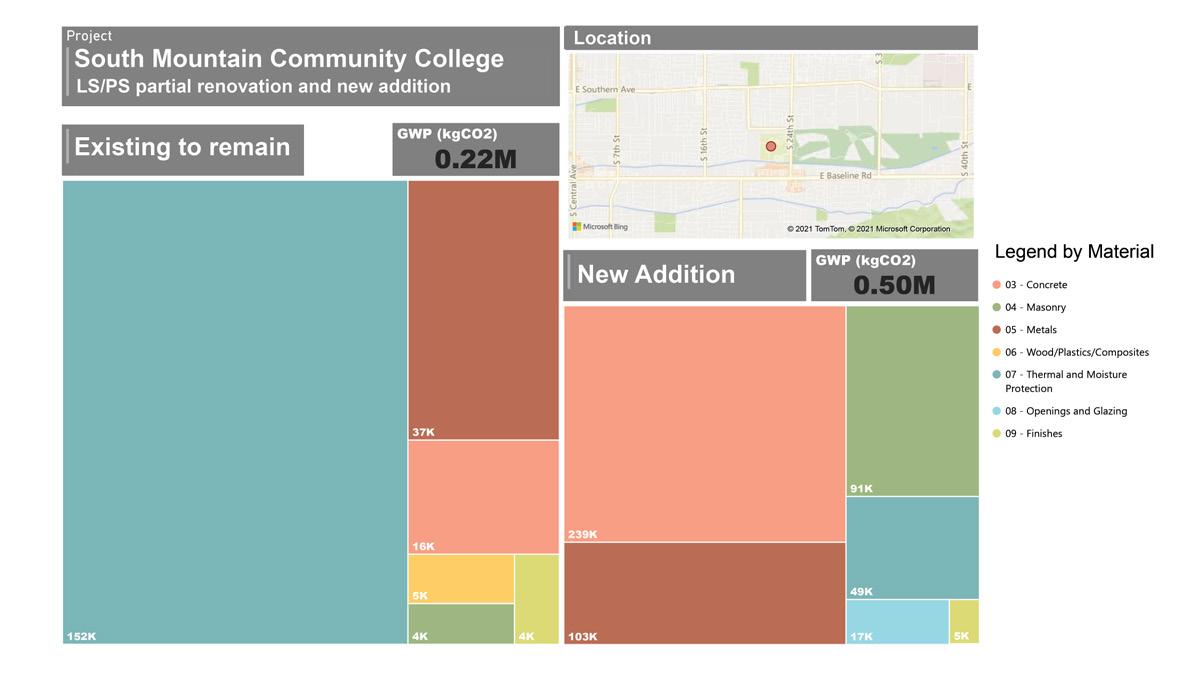
