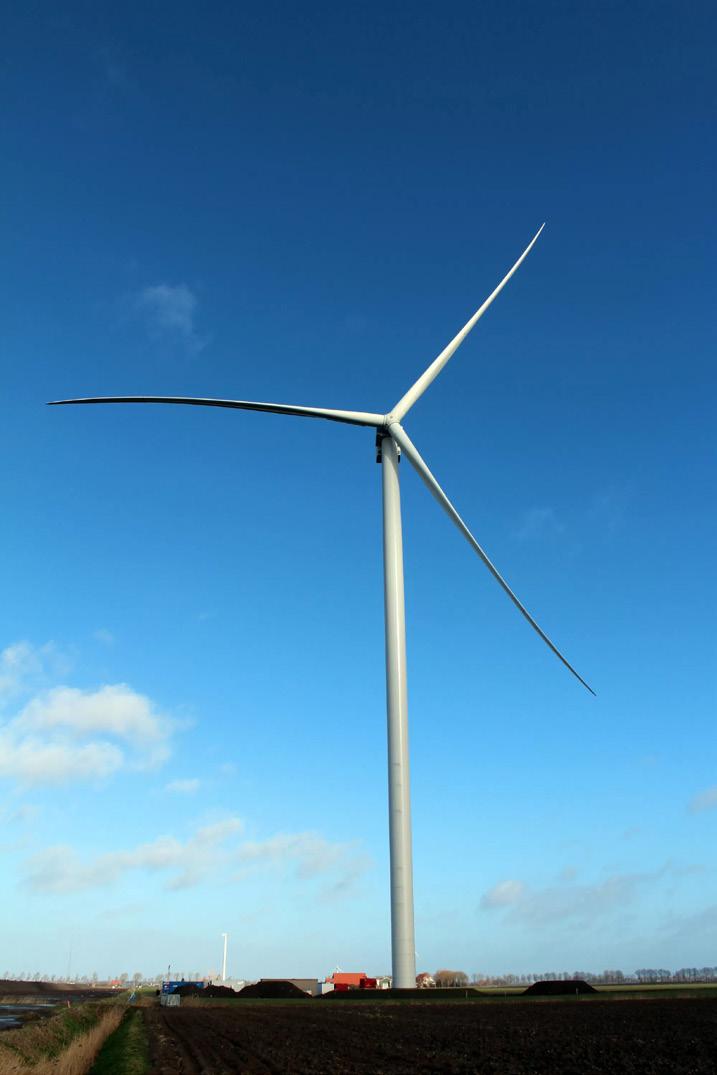
7 minute read
Optimation and GE Renewable Energy: Disrupting Conventional Windmill Wisdom
By Steven Beyer
GE Renewable Energy Additive Manufacturing is developing skyscrapersized wind turbines using massive 3D-printed concrete bases, made right at each wind farm site. Optimation Technology Inc. (Optimation. us) in Rush, NY outside Rochester, is working with GE to engineer the equipment and support the printer and process, and the materials development that will eventually be deployed around the world. Together at the wind farm site, the partners plan to use 3D-printing and customdeveloped high-performance concrete to manufacture turbine bases that could add as much as 80 meters — and possibly more — to the turbines’ height. The technology will print bases up to 20 meters high with additional steel tower sections to be installed to bring total height to 150200 meters (over 650 feet). Traditionally built in steel or precast concrete, wind turbine towers have typically been limited to a height of under 100 meters, as the width of the base cannot exceed a 4.5-meter diameter so that it can be transported by road without excessive additional costs.
To date smaller scale platforms have been printed and tested. Full scale units are planned for the near future. Taller turbines can capitalize on stronger winds at higher altitudes, and the structures support larger blades that generate more power. But building bigger turbines makes transporting the pieces needed to put it together a logistical nightmare.
The major benefits of the proposed tall tower are that it enables bypassing the logistical limitations for steel tower dimensions (diameter < 4.6 m); it decreases the levelized cost of energy (LCOE) compared with the Department Of Energy’s 5MW baseline turbine; it allows the integration of the tower door to the concrete pedestal rather than requiring a penetration of the steel tube section, which further reduces cost; the use of additive concrete technology eliminates formworks, saves labor, reduces construction duration, and allows the tower geometry to be optimized for maximum structural efficiency. The success of this project will pave the path for using additive concrete technology to achieve future ultra-tall wind towers.
The Mobile Concrete Factory
This article describes GE and Optimation’s efforts to develop a mobile concrete factory for efficient deployment/ setup with the ability to produce on-demand concrete for printing operations. As part of this, Optimation is developing equipment requirements for material handling, mixing, pumping, and horizontal rebar assembly and integration, and providing procurement activities.
Since Optimation's start in 1985, its multidiscipline engineers, designers and skilled tradespeople have worked together with clients to successfully deliver thousands of projects throughout the U.S. and the world. Optimation provides mechanical and process engineering and design, automation and systems integration, skilled trades fabrication and maintenance services for a variety of industries. This combination of skills and experience make for a strong partner.
“Optimation is seen as a strategic partner for GE Renewable Energy’s Additive Concrete Technology Development Program, working to develop industrialized equipment and process solutions for on-site construction of large-scale concrete structures to support wind turbine generators. Optimation consistently demonstrates a high level of technical acumen for solving complex equipment and process challenges, along with the flexibility to adapt quickly to the evolving needs of our technology development initiative.”— Chris Kenny, GE Additive Program Leader
Optimation is also determining layout and space requirements for operational setup at wind farm sites. This will include plans for a field deployment team to construct a full-scale field demo, and operation of equipment – printer, mixer, pump, cleaning, etc. Generally, Optimation will provide systems level engineering and integration of all equipment for field operation.
The team will design and establish a full-scale construction system for the pedestal of the hybrid tower. This full-scale construction system is based on the current commercially available printer from COBOD, a Danish partner in the program. This system will be customized to accommodate the unique material properties for our purposes.

Close-up of the business end of a GE “nacelle” housing the turbine and other system elements high above ground.
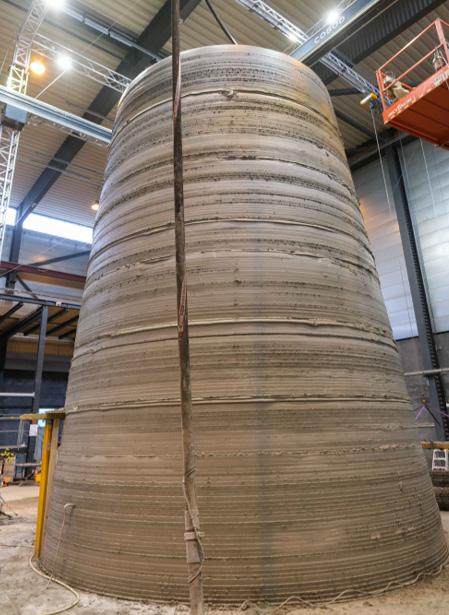
The finished 10-meter pedestal tower 3-D printed in 3+ days in Denmark.”
GE and Optimation plan to 3D print the base wherever they want to place it, and at a significantly lower total cost. This produces positive environmental, financial, technical, and logistical results for GE and its customers.
Printing a variable height base directly on-site with 3D-printed concrete technology will enable the construction of towers up to 150 to 200 meters tall. Typically, a 5 MW turbine at 80 meters generates 15.1 GWh annually. In comparison, the same turbine at 160 meters would generate 20.2 GWh, or more than 33% extra power.
GE Renewable Energy’s chief technology officer Danielle Merfeld told Windpower Monthly that 3D printing - also known as additive manufacturing - allows manufacturers to create prototypes quickly and cheaply. It is already being used in construction to create incredibly precise, single-piece components, she explained.
Matteo Bellucci, GE Renewable Energy’s technology leader for advanced manufacturing, said: “Concrete printing has advanced significantly over the last five years and we believe it is getting closer to having real application in the industrial world.”
He added: “We are committed to taking full advantage of this technology both from the design flexibility it allows as well as for the logistic simplification it enables on such massive components.”
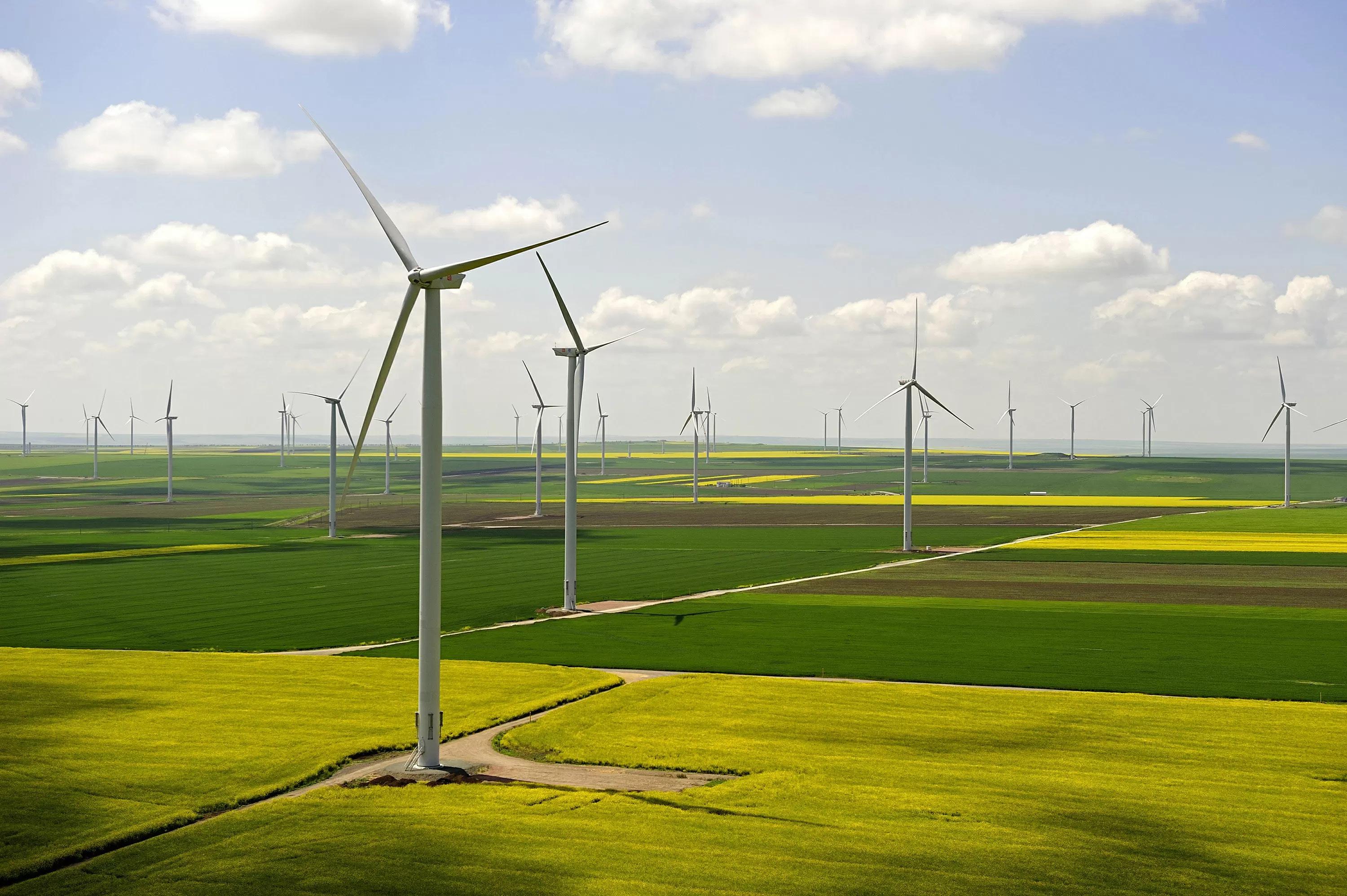
A wind farm with many GE turbines atop traditional steel towers.
A Global Team Effort
The GE Renewable Energy “Additive Manufacturing” team is based in Schenectady, NY, and much of the core group is based there. But like GE itself, their team is global with members around the country and in other parts of the world, primarily in Europe.
A team of external partners including Optimation makes up the balance of subject matter experts and other contributors to this program. As the lead engineering firm and system integrator for all these partners, Optimation plays a key role in unifying the various core technologies and systems into what will become a working mobile concrete printing factory. These partners include LafargeHolcim, the Paris-based global leader in the building materials industry: cement, concrete and aggregates, and largest cement producer in the world, working on the recipe for the concrete mixture that makes up the pedestal tower. COBOD of Copenhagen provides the 3-D printing engine and structure and has managed all the printing related experimental activities including subscale and full scale prototyping. Rapid developments in both materials and printing technologies are happening in real time as this program progresses.
The total network of partners provides testing, certification, and advisory services to the effort, along with engineering, architectural and structural design services.
This global effort has the team simultaneously inventing, testing, enhancing, and producing tremendously innovative materials, techniques, and processes to more efficiently construct these windmill tower bases in an environmentally friendly way. As wind power grows in popularity and productivity across the country and around the world, the demand for these kinds of pedestals is expected to be a game changer for GE in the industry. Optimation is supporting this program and including these European partners in its printing and building efforts, as well as positioning itself to be a key resource in the North American deployment and implementation of the technologies.
Program Benefits
GE’s disruptive technology approach to 3-D printing in the field of concrete pedestals for windmills has numerous economic, environmental, and technological advantages. For the comparison of the additive printed approach compared to the conventional all steel on a concrete slab process, there is a projected financial savings Members of the team that from a variety of sources. These include built the 10-meter pedestal tower in Denmark. optimizing the steel supply chain and buffering the periodic fluctuations in steel prices and supply. GE has also been able to more rapidly supply and erect the structure, reducing labor costs and exposure to weather and other environmental impacts. Other logistical benefits will come from shorter lead times given the program’s essentially “just in time“ model of on-site construction with local raw materials and flexible setup and operation.
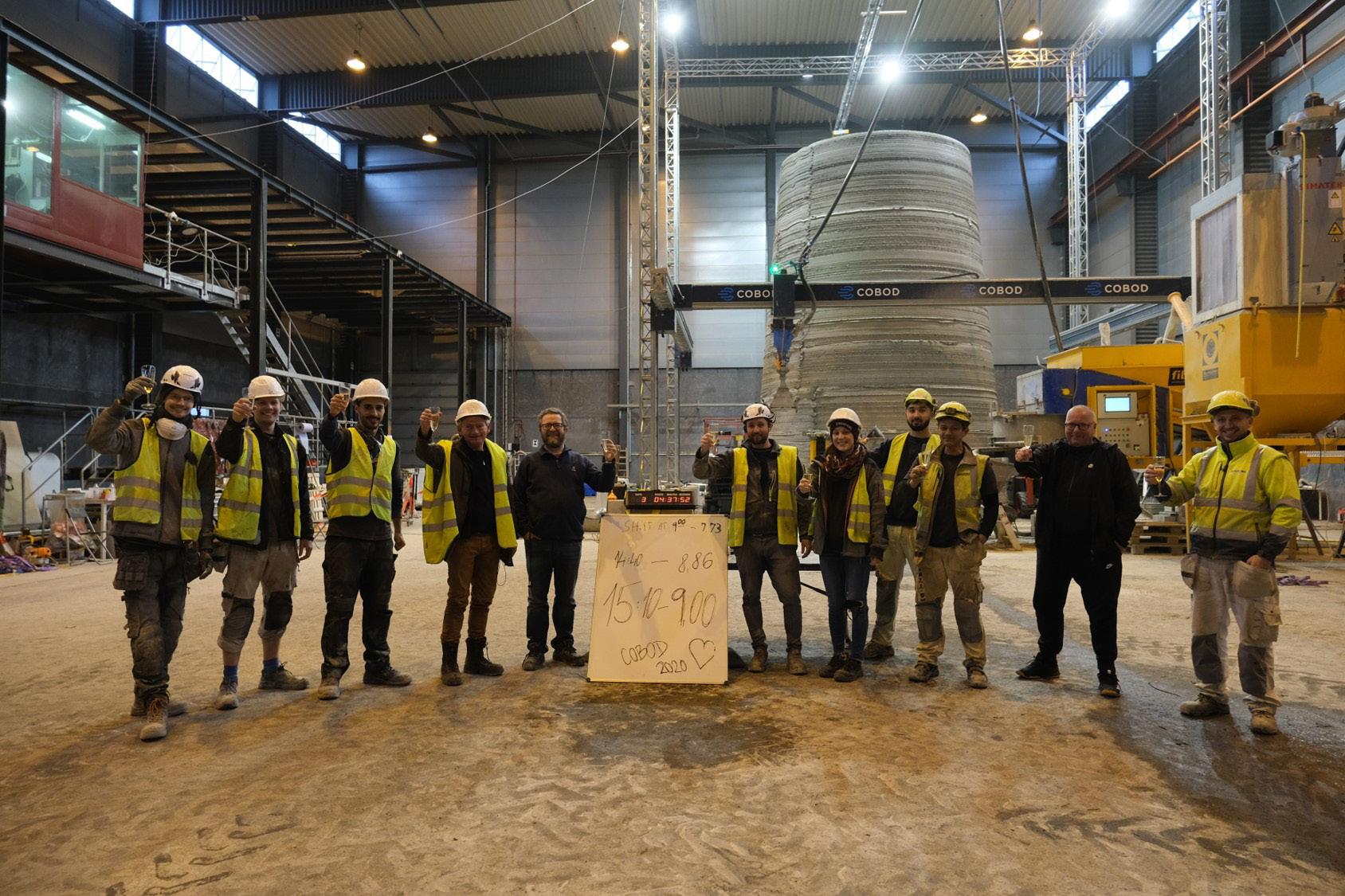
Members of the team that built the 10-meter pedestal tower in Denmark.
With the additive concrete tower pedestal base there is no need for formwork and significantly less need for concrete pouring and post tensioning support. Structural analysis shows that these printed concrete bases can withstand significant environmental conditions and provide flexible configuration prospects as well as a virtual “location on demand” site model.
The solutions are so appealing and compelling that the program has the support of the United States‘ Department of Energy. GE will be the leader in this design for additive windmill base technology, providing a competitive advantage in the marketplace and making their wind turbine systems ever more attractive. This initiative is bringing jobs and high-quality engineering work to Optimation and the Rochester region. Be on the lookout someday for these innovative pedestal bases on a windmill near you! q
Source:
https://www.windpowerengineering.com/ge-renewable-energy-is-experimenting-with-3d-printed-turbine-bases-for-tallertowers/
Steven Beyer is the General Manager and the Director of Business Development at Optimation Technology in Rush, NY. He is responsible for market and client development, broadening and deepening the client base and the Company’s relationships, producing successful project opportunities, and contributing to Optimation’s commitment to constant and continuous improvement. Steve is in his eighth year with Optimation, his career spanning several other high technology firms in software, product development, R&D, logistics. Originally a Systems Engineer with IBM and an early member of the Robotics Institute in Pittsburgh, he has continually sought and found positions of increasing technological interest and responsibility leading these roles at Optimation. He is married to Eleni with three children, residing in Pittsford, has been very active in his church, several philanthropic and business organizations, and in youth sports programs.