
6 minute read
Cover Article - L3Harris - L3Harris Technologies - Digital Transformation & Advanced Manufacturing
Across multiple industries, digital transformation is fundamentally reshaping the manufacturing landscape.
Through rapidly expanding digital capabilities, companies are better able to integrate and align the various phases of the manufacturing chain to drive greater collaboration, efficiency, innovation and value.
It’s no different for L3Harris Technologies; more than 1,200 employees at the company’s operations center at Jefferson Road, Rochester, New York – known locally as JROC – work across four shifts in approximately 573,000 square feet of manufacturing space to assemble and test the most advanced radios for military and public safety customers. In fact, L3Harris was recently named the number one manufacturer in the Rochester region with JROC producing approximately 12,000 products per month across 30 different product families.
Both marketplace competition and effects from the COVID-19 pandemic are accelerating the digital transformation of the L3Harris business out of sheer necessity. L3Harris is capitalizing on this as a catalyst to evolve its manufacturing operations into a modern, lean, connected ecosystem to drive increased value for its customers. Through digital transformation, L3Harris is powering operational excellence and continuous improvement. The company can harmonize how its people, processes and technology come together to eliminate waste, shorten lead times and drive quality at the source.
As a trusted technology disruptor for defense, security and public safety customers worldwide, L3Harris is pursuing these benefits to provide operators industry-leading solutions fast, so they can achieve mission success and return home
L3Harris is investing in Advanced Manufacturing, including Augmented Reality solutions, to allow operators to stay "in the loop" but act more like a coach than a player in the operation
safe. Plus, L3Harris’ investment in digital transformation provides rewarding careers in 21st century operations facilities.
The Manufacturing Floor of the Future
“Advanced manufacturing is spurring multiple enhancements in how we do things and the outcomes we can achieve,” said Chris Monoski, L3Harris Senior Operations Director. “It allows us to leverage organizational learning by sharing knowledge and best practices across the corporation. It also enables us to develop proof-of-concept applications using cutting-edge technologies to solve problems, and it provides more robust solutions for all stakeholders.”
L3Harris is embracing Industry 4.0 and strengthening its foundations. The symmetry L3Harris is establishing among its people, Lean principles and the right mix of technology – robotics, Artificial Intelligence, machine learning, automation and the Internet of Things – will lead to consistent and predictable outcomes in the advanced solutions and capabilities it delivers to customers. The current industrial revolution in digital transformation provides a broad range of opportunities for the manufacturing floor of the future, and L3Harris is taking full advantage of those that provide the right utility to bring manufacturing technology to the same level of next-generation product technology.
“We have several examples of advanced manufacturing in operation at our JROC facility,” said Monoski. “We have augmented reality, collaborative robots performing soldering and vision systems tasks, autonomous mobile robots, artificial intelligence vision systems for product inspection and process analytics, and additive manufacturing – including 3D printing.”
Vision equipment with Artificial Intelligence software alerts when it detects slight defects in the assembly
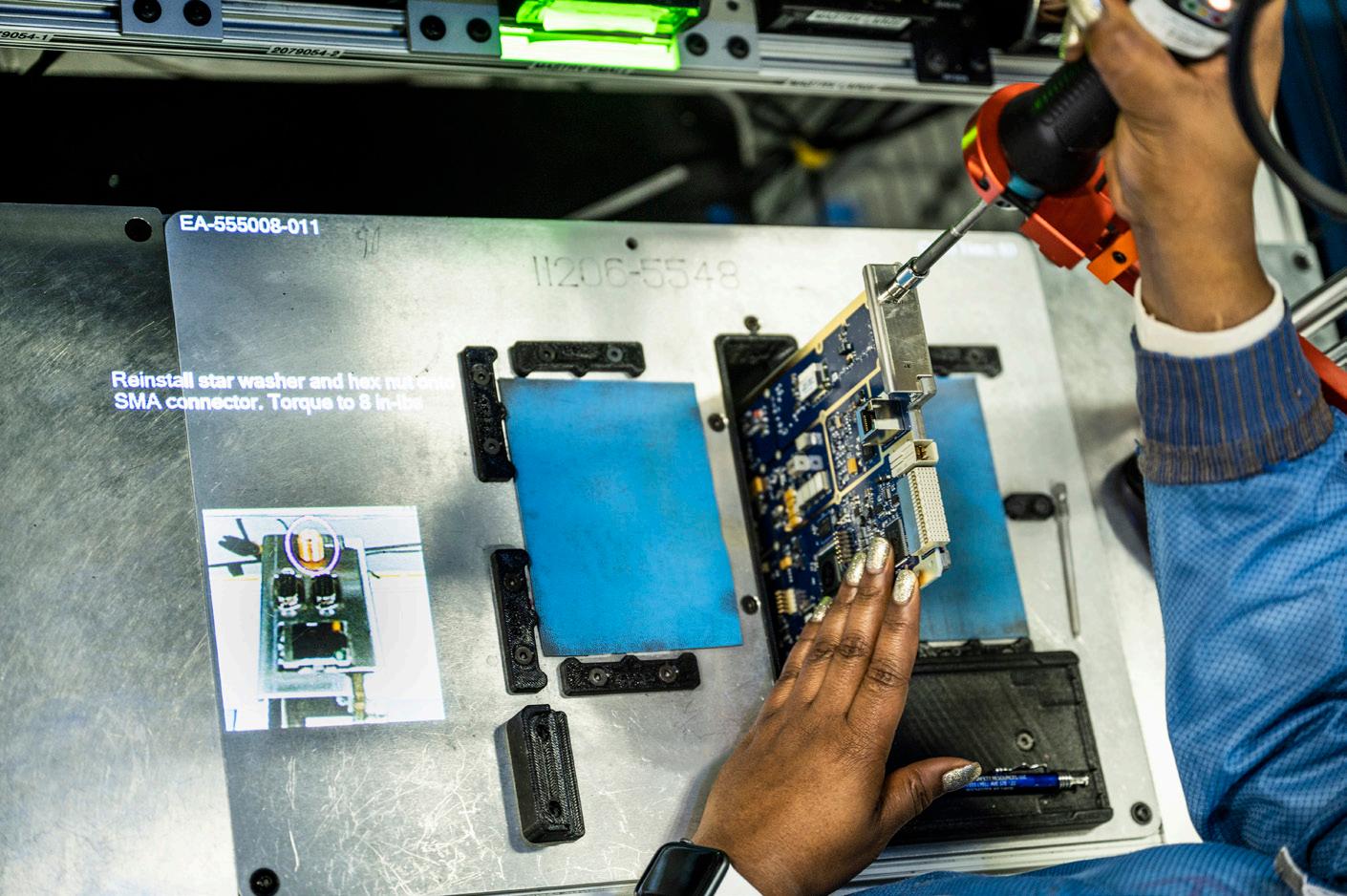
Driving Collaboration & Integration
L3Harris is driving quality upstream, to the source, to ensure it is designing products for manufacturability, which also ensures sustainment and maintenance processes go just as smoothly. The company is deepening the collaboration between Engineering and Operations and strengthening its zero defect escapes mentality to drive quality to the next level.
“Reflecting greater collaboration and integration, we are developing the Intrepid Smart Cell using a fully cross-functional
team working together on the design of the next-generation assembly process,” said Fran Branco, L3Harris Manufacturing Engineering Principal.
L3Harris is reengineering shop floor management to speed communication and translate real-time data into information and action. It is designing moreconnected information systems to implement automated and zero-touch operations. Ultimately, the goal is to create an environment that reduces stress and fatigue on the company’s personnel.
Artificial Intelligence and Augmented Reality allow operators to stay “in the loop” but act more like a coach than a player in the operation – vision equipment with Artificial Intelligence software alerts when it detects slight defects in the assembly, and the location is illuminated by overhead projectors to drive quality at the source and improve the cognitive ergonomics of operations.

The location is illuminated by overhead projectors to drive quality at the source and improve the cognitive ergonomics of operations
What it Means for Customers
The investments L3Harris is making today and going forward are driving enhancements in its ability to deliver the highest quality products and assure customers that they will work the first time and every time.
“Advanced manufacturing enables us to drive greater value for customers, as well as employees,” said Branco. “For customers, we reduce time to market for new product development, and we reduce operating costs through efficiency gains and yield improvements. For employees, we improve the employee experience and engagement through these advanced capabilities and the various benefits they yield.” Spanning four unique businesses, there isn’t a single panacea for the diverse challenges in L3Harris Communication Systems’ manufacturing operations. While elements of L3Harris’ manufacturing system are common, the company adapts and tailors technologies to accommodate the nuances in each of its businesses, spanning high-volume commercial to lowvolume programs.
Sharing an Illustration
As an example, a pilot program in L3Harris’ Rochester Tactical
Communications radio facility has implemented all of these elements to transform a multicell production system into a single, mixed-model line that is paced with high utilization rates and quality at the source. This has led to reduced rework, scrap and downtime for a critical military program.
Activities such as this are building upon L3Harris’ robust and aligned ecosystem – from supply chain to manufacturing, test and sustainment – to create true technology disruption within the company’s operations to maintain its ability to be a partner of choice for customers.
Across the L3Harris enterprise, novel and broadly applicable process and technology improvements are emerging and gaining acceptance every day. The company’s advances in revolutionizing the modern manufacturing space for the digital age, aligned with its dedication to continuous improvement in its people and processes, assures customers are equipped with the highestquality, most-advanced solutions exactly when they need it to successfully complete their missions. q
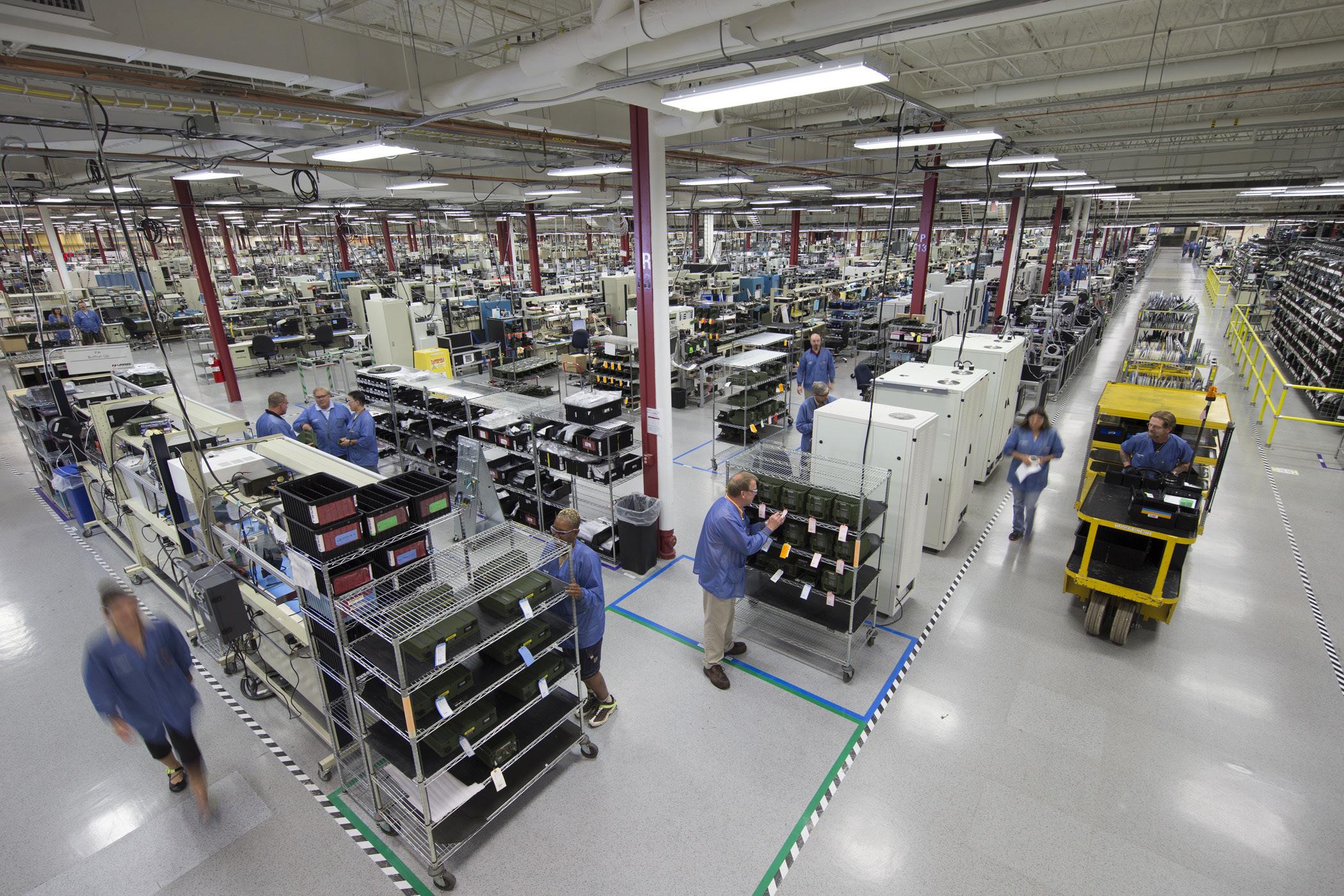
Through digital transformation, L3Harris is powering operational excellence and continuous improvement
In Rochester, L3Harris assembles and tests the most advanced radios for military and public safety customers
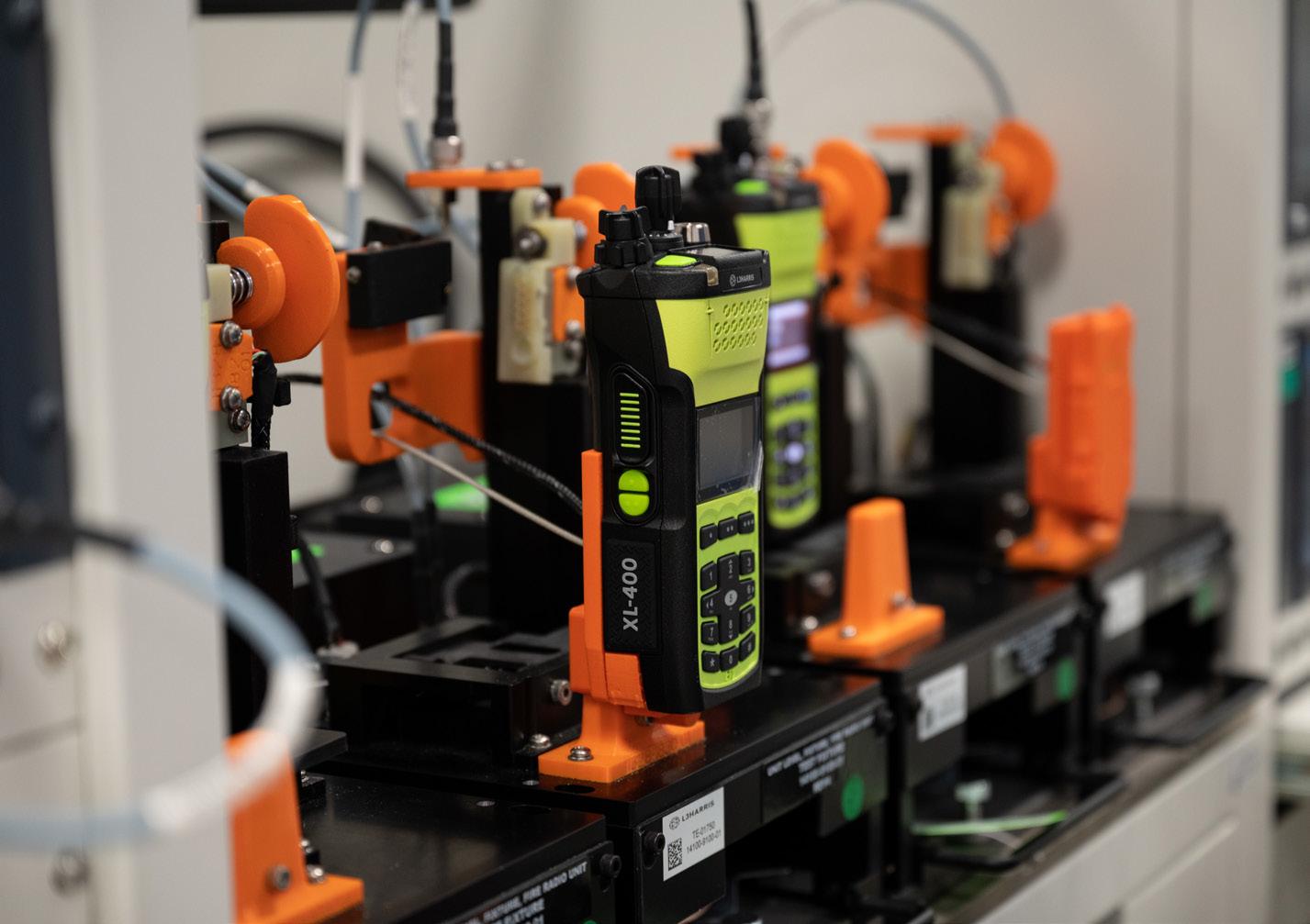