The Ability To
Implement A System Of Continuous Improvement In Your Company
It's beneficial to evolve. There are many who insist that it is inevitable, or that each of us must "be" the transformation we wish to witness in the world. No one, however, has ever said that effecting change will be easy. In the same way, enhancing corporate procedures is always a good idea. If companies constantly adopt the mentality of "If something isn't broken, why fix it?," they may never get around to improving their processes. Assessing current processes and improving procedures, however, becomes inevitable as businesses develop and strive to innovate to remain competitive.
It's not just expansion that necessitates constant tweaks to corporate procedures, either. Broken systems and outmoded business procedures lead to dissatisfied customers, stressed-out employees, missed targets, and increased costs. If you are in the midst of a process audit and redesign, give this some thought.
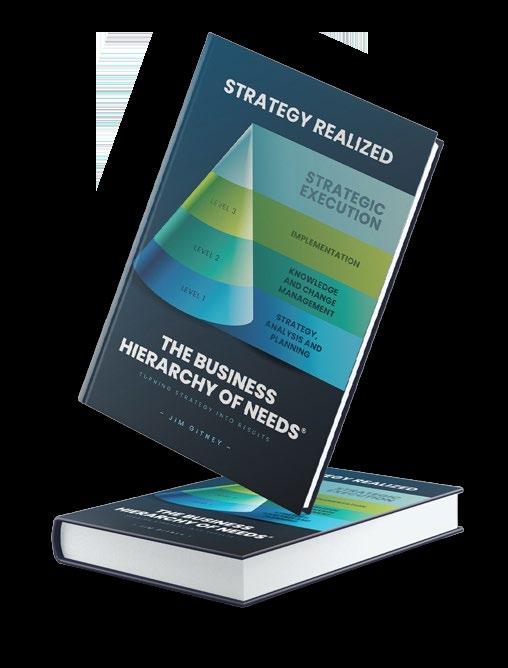
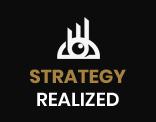
Promoting a mindset of constant self-improvement
Excellent customer service begins with identifying the customer's priorities and working to fulfill those needs. The foundation laid by lean and continuous improvement can be used to better understand what customers value and cut down on unnecessary steps in the value creation procedure. Businesses that implement lean methods are better able to cater to customers' underlying desires. This will lead to "predictive" products and services that meet consumer needs before they are articulated.
It doesn't take long for information and tools to become obsolete in today's modern workplace. In the long run, your company will collapse if you keep doing
it the same way you did five or ten years ago. Managers and employees alike benefit from a culture of constant improvement because it encourages them to try new things. Current methods can only be improved by trial and error. This new item may be scary at first and be too much for the company to handle right now. An infrastructure for organizations to achieve sustained excellence is provided. Organizations that strive to improve all the time are never satisfied with how things now stand. Change and development are constant companions to progress.
The only way to establish and maintain a culture of continuous improvement over the long run is to place a premium on the acquisition of new competencies. By instituting a system of continuous development, businesses may encourage their employees to expand their horizons and learn new things. In the end, this will help the company keep its edge in the market.
Highest Standards Better Product
If you work to refine your process, you'll inevitably see an uptick in your results. Errors are reduced and the quality of output and service is improved. Reduced amounts of customer complaints and returns are the end outcome. Customers place a high value on consistency, and your brand's credibility will grow as quality improves.
It is acceptable for just a subset of businesses to implement a formalized program or technique for improving processes. No preexisting program is required to take advantage of CPI. All that's needed is some introspection and good old-fashioned common sense applied to your procedures. Observing a procedure might help find inefficiencies that drain money and time.
If you are familiar with formal process improvement methodologies, though, you can boost your results. The Lean Six Sigma courses offered at USF will provide you with the knowledge and skills necessary to cut down on start-up and improvement times.
Because of this, Strategy Realized: The Business Hierarchy of Needs is a mustread if you're interested in learning more about continuous improvement with the goal of developing your firm. Therefore, rush in. Quick, read it!
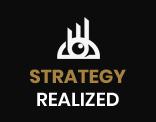