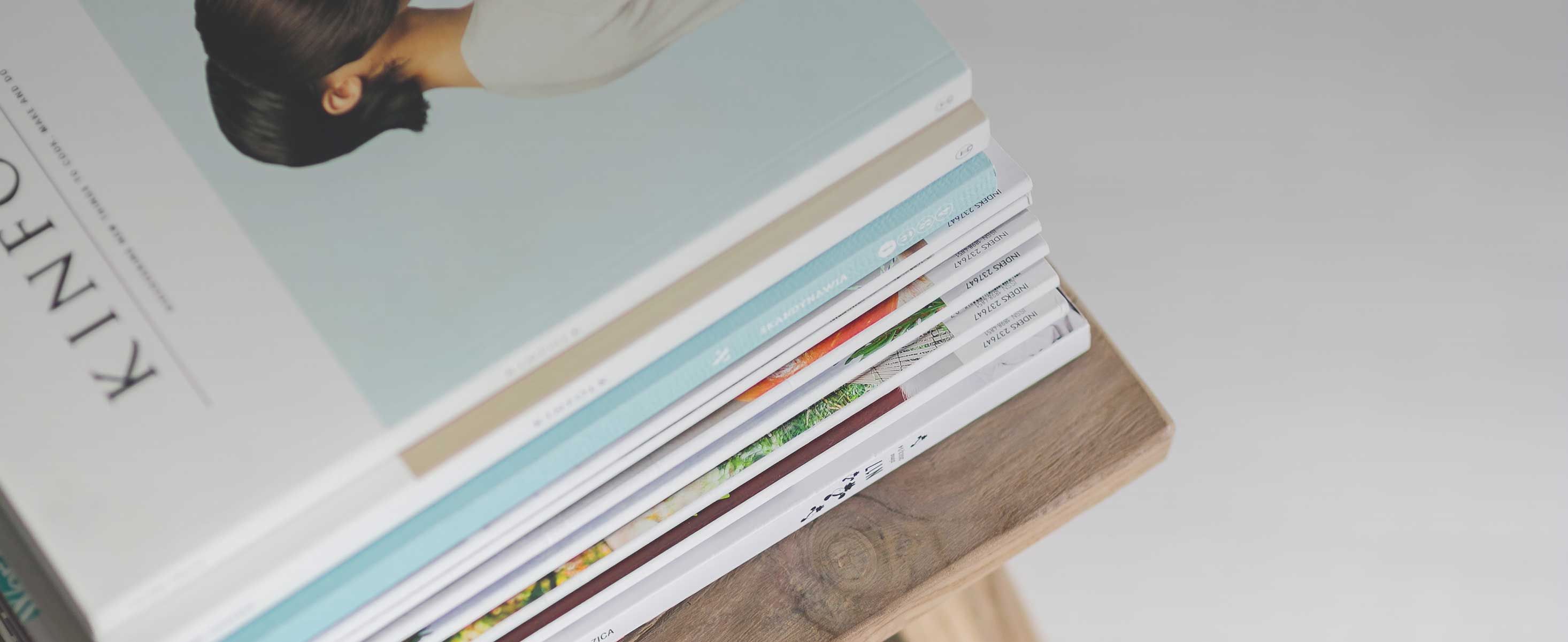
4 minute read
Further Information about “Drone Surveys”
from dangers
by Hagar Talaat
Drones are powerful tools to help in the underground locating, mapping and surveying industry. They can effectively perform work for 3D mapping, land surveys, photogrammetry, and topographic surveying by flying above the ground.
In general, surveying is the science of determining the distances and positions between two points, whether in a 2D or 3D space. This information is used to help make critical decisions about the upkeep of infrastructure, construction site planning, and delineating property boundaries. When you want to complete a drone survey, you take those basic principles but use a drone to gather the information. The drone will fly above the points and record all that information for you.
Advertisement
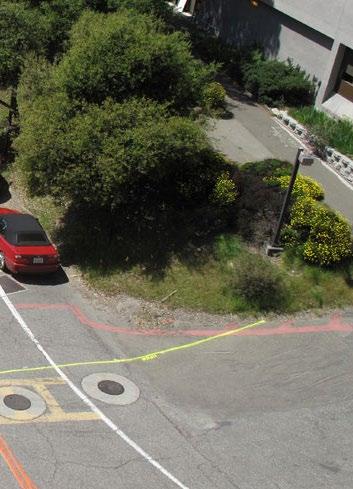
As the drone flies above the ground, it uses downward-facing sensors with a standard drone camera or for better results you could use a multispectral and RGB camera to capture images. Along with that, many drones feature LiDAR payloads to help collect information. When the drone surveys the lands, it will use the RGB camera to photograph the ground at different angles. Each angle is tagged with the exact coordinates.
Drones collect data from the Geographic Information Systems (GSI). They used this information to visualize and map out locations. The GIS is the primary source for collecting data, but other collection tools can be equipped on the drone. In the past, drones were used to capture but not transmit data. All that information had to be retrieved by the operator. With new technology, drones can interrupt data in real-time. You can turn all that raw data into actionable information through GIS technology while the drone is still in the air.
There are many reasons why drones are more beneficial. Drones can acquire data at vantage points that are not accessible to humans, especially those areas with challenging terrains. There is no need for human operators to measure points in hazardous locations physically. However, those traditional methods do require pre-planning before reaching the site. When a drone flies over an area, it can capture the same amount of data in a shorter time frame. Drone surveying allows the surveyor to collect data more safely and quickly than those traditional methods. If you are looking for a more efficient way to survey those areas, it might be time to consider using a drone survey.
Drones are incredibly accurate, in many cases, you can expect drone surveys to come within two centimeters of the actual location. Most drones are even more accurate than those measurements. When you work with a professional drone surveying company, you can expect these types of results. Remember that they have access to better equipment and that always leads to more accurate outcomes. Plus, the kind of drone, quality of the camera, flight height, and ground cover can all influence the survey results.
If you wish to find out more about the course that can be used by “Underground Service Locating Personal” please click on the link below. The certificate issued is AVIY0028 – Operate remotely piloted aircraft in the excluded category sub-2kg operations. The certificate is issued by “Locating Unlimited” RTO: 45518 and delivered by Drone Operations.
https://www.drone-operations.com.au/aviy0028-locating
Itmay come as no surprise that an often-misunderstood technology which has a long history of being oversold, hyped, or just plain lied about. A century after its invention and five decades since its commercialisation, there still remains the sentiment in the utilities industry that it is a “black-box” tool that sometimes works, and sometimes doesn’t. Spurred by manufacturers’ claims of ease-of-use, the last 20 years has also seen a shift from users being predominantly geophysicists, to an everyday tool used by those with little technical background. Concurrently, the utilities detection GPR market has exploded, as has the number of manufacturers vying within a competitive space. New users have little basis to judge inflated performance claims using zeitgeist terms such as “AI”.
There are two principal architectures for a GPR system – either an impulse or a stepped/swept frequency (SFCW). There are further refinements with an impulse system which could yield higher performance (e.g. noise modulation), and which do yield higher performance (e.g. real-time sample). Regardless of the architecture, most modern utility detection radars, when compared side-by-side, perform remarkably similar.
There is nothing new about SFCW radars which were developed during WWII. Although the common misunderstanding is that they produce incredibly wide bandwidth (claims of 40 MHz – 6 GHz are prevalent), what is rarely admitted is that the antenna limits their bandwidth anyway to essentially that of any other radar. Examining the actual data from
SFCW radar shows that it is very similar to that of an impulse system.
There is also nothing particularly new about noise modulation schemes, although they can increase penetration in some scenarios. Real-time sampling with impulse systems has only been possible in recent years due to the availability of low-cost, fast, analogue-to-digital converters, and now nearly all radar manufacturers use such technology, marketed under different names.
The term “AI” for hyperbola recognition is the new technobabble in the industry. AI is a misnomer in this case, as what is really happening is a computer vision (CV) algorithm to match a database of known hyperbolas with those seen on the screen. This concept works nearly perfectly in a sandbox, but in the real world, even the best CV schemes miss a large number of subtle targets and only pick those which the human eye could have easily seen anyway.
GPR has a long history of being oversold, which continues to this day. Those new to the industry as well as seasoned veterans are well advised to research beyond the slick sales talk and enticing promises to appreciate that any improvements to GPR technology are now incremental at best, and that their purchase decisions should be made on more important factors such as overall ruggedness, fit for purpose, controller ruggedness, acquisition and processing software, aftersales repair support, etc. Caveat Emptor!