
11 minute read
THE VIRUS
A Spring Unlike Any Other
Dealers grapple with health concerns, business impacts as the coronavirus pandemic affects the lawn and garden industry.
BY DAN SHELL & PATRICK DUNNING cross the country, the lawn and garden industry and power equipment dealers are adapting to drastically different operating conditions in a spring season unlike any other as the coronavirus pandemic works its way throughout North America. Plans have changed, and different states and regions have different restrictions on business operations.
In most of the country, power equipment dealerships remain open as part of a Dept. of Homeland Security guideline (with discretion left up to states and localities) that lawn and garden equipment suppliers and dealerships are part of the country’s “critical and essential” agricultural infrastructure.
In Washington state, Angela Longnecker, who works at the Yelm location of J&I Power Equipment, with headquarters in Olympia, says “It’s too soon to tell and it’s ever changing,” when asked about the impact the coronavirus is having on the dealership.
Located in one of the early virus “hot spots” in the Puget Sound area, Longnecker says when news broke about a potential lock-down of business and much activity, it seemed to generate a spurt of business as some customers made buying decisions with that in mind. She adds that since the virus began spreading and precautions have increased, the stores have followed suit. Originally they were wiping surfaces frequently, putting up barriers to keep A
customers 6 ft. away from the counter, closing public restrooms and adding hand sanitizing stations; but now they’ve closed their doors to the public, doing curbside pickup and drop-off only and selling Kubota equipment by appointment only.
“We still have a lot of customers reaching out via email, texting us or through our web site for tractor packages so we want to be available to them,” Longnecker says. More recently, they made the decision not to accept any more service jobs for the time being. If government restrictions tighten, “We aren’t sure if we will be able to remain open or if our vendors will continue to ship parts to us,” she explains. “We don’t want to have our customers’ equipment and then be shut down and not know when we will open.”
The dealership recently adjusted hours to 10-4 Monday through Friday and 10-2 on Saturday.
Longnecker says the dealership is committed to paying employees 40 hours a week even though hours are reeration according to customer demand and the health and safety of employees. “We’re just crossing our fingers that we have a hundred days of hell this spring,” Longnecker says.
Bob Odom, owner, B & H Odom’s Mower Shop in Sacramento, Calif., says he’s still trying to work employees at least half a week. “We’re staying open a less amount of time and taking phone calls, but people are still coming in to have their equipment serviced,” he says, adding that his staff is holding reservations for people to bring their equipment in.
Odom has cut his open hours to just Friday and Saturday; employees are wearing masks and gloves. “We have wipes to wipe down equipment as well as stay a good distance away from customers and wear masks. We have to make our employees less susceptible to get the virus.”
The coronavirus’ impact to his business is hard to gauge, Odom says, because spring season is in full swing— such as it is. “The ones who have been
Angela Longnecker with J & I Power Equipment in Washington state says that since the virus began spreading and precautions have increased, the stores have followed suit. Originally they were wiping surfaces frequently, putting up barriers to keep customers 6 ft. away from the counter, closing public restrooms and adding hand sanitizing stations; but now they’ve closed their doors to the public, doing curbside pickup and drop-off only and selling Kubota equipment by appointment only.
duced, and also if they have lost childcare, are ill or caring for someone with coronavirus. “We are committed to paying our employees full time through the Washington state ‘stay at home’ order,” Longnecker says. “Once that is lifted, we are hoping our normal spring season is here and we will be busy enough to employ everyone full-time.”
In the meantime, there are plenty of internal projects around the business, such as organizing, clean up and even some landscaping that needs doing. “We feel this will be a good opportunity to get to them and prepare for the upcoming ‘hundred days of hell’ that we call the spring season,” Longnecker says.
The family-run business is a longtime premium equipment fixture in the south Sound area. Going forward, the family is meeting weekly to adapt to any changes in operations, adjusting the oplaid off or are working from home, they are working on their yards in their free time,” he says. “Therefore, people are still needing their equipment tuned up and repaired and are a little bit more proactive with the extra time that they have.”
He adds that he hasn’t experienced any delays in shipment of parts as of yet. “The equipment is staying wiped down. We just have to monitor things and be as careful as we can be.”
Just north of New Orleans in Slidell, John Fortenberry, owner of PJ’s Lawnmower & Bicycle Repair, a mostly service-only business that sells some used equipment, says he’s seeing a bit of a silver lining from the business closures. “Everybody here has been ordered to stay at home so they’re cutting their grass,” he says, adding that lawnmower mechanics are the busiest guys in town Longnecker: staying safe

right now. “I’m three weeks behind.” The business services everything. “When they drop it off, I’ll look at it and make sure it’s worth working on,” Fortenberry says, adding that he works mostly on Echo, Stihl and RedMax handheld. “Sitting here right now I have close to 40 repair jobs; so I think we’ll be fine moving forward.”
He adds that as of the end of March, there were still a lot of businesses open in his area ands lots of traffic. “I’m sorry to say, it doesn’t look like we’re heeding the governor’s advice to stay home, but we live week to week so it’s hard to stay closed waiting on a stimulus package.”
He’s cut store hours and concentrates on staying healthy and inside. Right now, “This whole ordeal is kind of in my favor, I just have to do my part and produce and stay healthy.”
In Livingston, NJ near hard-hit New York City, Susan Kalweit, Vice President of Fred’s Small Engine Sales, says the dealership is open but the doors are locked.
“We want no human contact so when a customer drops something off we’re telling them to just leave it on the side. We go, disinfect the machine, we’ll repair it and work on it,” she says, adding that they’ve hired a person to do nothing but disinfect machines. “Then when it’s fixed we call them, tell them how much it is, ask for credit card information and schedule when they can pick it up. We have a pick up site and we put the receipt on the machine. We’re not dealing with cash at the moment.”
The dealership is working hard to maintain a close to sterile environment, she says. Some employees have been sent home and it’s being emphasized they stay as close to home and safe in their off hours. “We’re 15 miles from the epicenter in New York City. We’re doing okay, but it’s scary,” Kalweit adds. “We almost wish there was a national shutdown so we didn’t have a choice. We have a choice to stay open but at what point do you jeopardize con
The Equipment & Engine Training Council (EETC) annual conference cancellation and changes to online testing are two impacts of the coronavirus. In March, EETC canceled its 24th annual conference, scheduled to take place April 1-4 in Green Bay, Wis., at Lodge Kohler, with Ariens Co. and Fox Valley Technical College serving as co-hosts, the EETC Executive Board called it off due to health concerns and travel restrictions caused by the coronavirus.
“The safety of our conference attendees and guests comes first,” says EETC Executive Director Erik Sides. “We sincerely apologize for any inconvenience this may cause and look forward to seeing you next year at our 25th annual conference.”
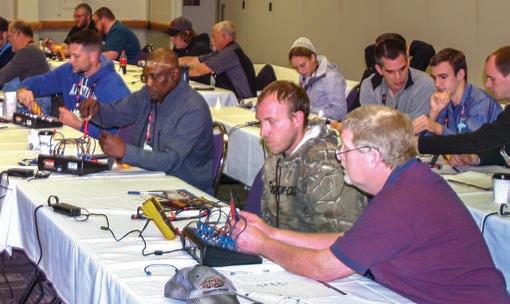
Test Changes
The EETC is also taking necessary measures to maintain continuous operation of its technician certification program. Effective immediately, the EETC is administering all of its online certification exams without a proctor for the next 90 days (with an automatic 90-day extension if necessary). Exam pricing for non-members is $59 (versus $49 for members) and for students to receive the $39 discounted test price schools must have an active school membership.
“We know the effects of the coronavirus have impacted everyone, and we wanted to make sure our students and technicians have access to our online testing without the need of a test proctor,” EETC Executive Director Erik Sides EETC certification session at GIE+EXPO
says. “EETC was already transitioning to proctor-less testing, says this just made the most sense to us.”
EETC annual membership fees for colleges/universities and high schools are only $250 and $100, respectively, and student sub-accounts can be added for $12 per student. This is also includes access to the EETC’s technician portal, which houses 15 online courses and seven study guides (valued at more than $400 for non-members). Dealers have the opportunity to access the same resources within the technician portal and receive a $10 discount on certification exams for a $60 annual membership fee. Additional sub-accounts for technicians can be added for $12.
ducting your business and getting sick? It’s an uneasy time right now, you talk to people as if they had the virus.” She says residential sales have picked up. “Things are up and moving with our landscapers on the East coast, but New Jersey had a snowless winter so landscapers are hurting for money and they’re not buying anything new.”
She notes this year is Fred’s 50th in business. “We’re pretty well stocked. I hope it stays that way but depending on how long this goes on, its survival of the fittest. Hopefully we get a hold of this virus. Wash your hands and social distancing is key!”
In central Florida, Chuck Stull, CFO of Trail Saw & Mower Service in Orlando, says the virus doesn’t seem to be affecting operations that much, with customers still coming in. “We’re disinfecting things around here to stay on the safer side,” he says. Things like the computers, the credit card machines, the doors and other things.
He says right now the biggest impact has been “super dry” weather the first two months of the year. “That’s hurting us more than the virus is.” However, he adds that some customers have called and been thankful that the business was still open. “We’re seeing people come in who are working from home, and they’re getting tune ups because they have more free time,” he says. So far, “We haven’t cut back hours or reduced staff,” Stull says hopefully. “We’re telling our employees and customers that we’re going to operate as we always do and continue to monitor the news for updates. If things get worse we might have to think about cutting back how many people are allowed in.” He adds that the business was already seeing a slowdown in sales and floor traffic last year and its continued into this year with the dry weather.
Family-run dealership Barney’s Hardware in Elmont, NY is open with all family members working, says Donad Katz, president. “Its definitely slowed business down,” he says of the coronavirus impact. “It’s day to day. The Home Depot down the road is limiting the amount of people who can come into the store at one time, so that’s helped us some.”
Even so, Katz says, business has been slow. “Foot traffic is way down from what it should be. It’s too early to tell right now, we’ll see our sales reports in a few weeks and be able to tell.” He adds that in his area of New York City, “There’s not a lot of traffic on the roads, a lot of stores have closed, people aren’t going outside unless they have to. But we’re considered a vital business, as a retail hardware store, so were keeping our doors open.” PET “We want no human contact so when a customer drops something off we’re telling them to just leave it on the side. We go, disinfect the machine, we’ll repair it and work on it,” she says, adding that they’ve hired a person to do nothing but disinfect machines. “Then when it’s fixed schedule when they can pick it up. We have a pick up site and we put the receipt on the machine. We’re not dealing with cash at the moment.”—Susan Kalweit, Fred’s Small Engine Sales, Livingston, NJ
