
38 minute read
Bulletin Board
Nature At Work: Remarkable!
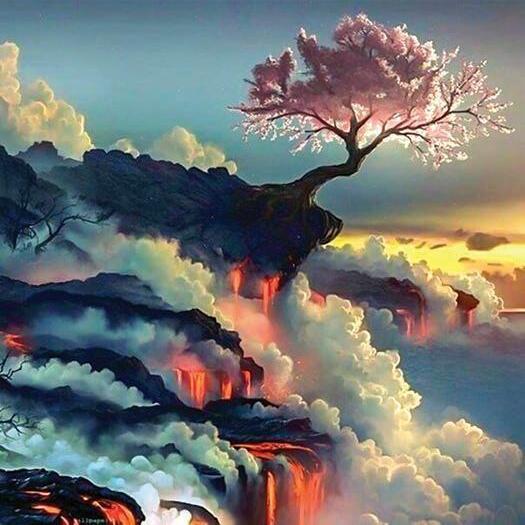
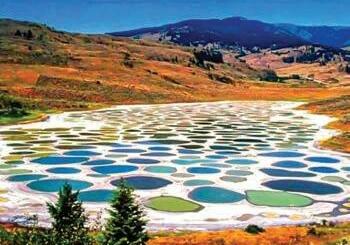


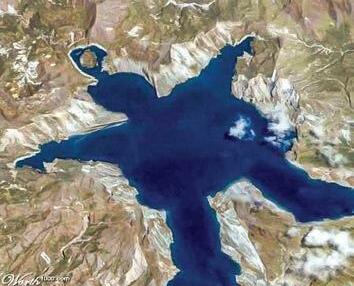
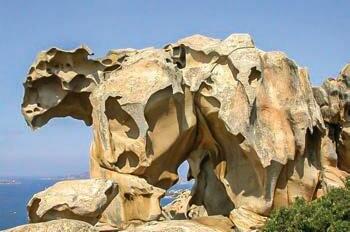
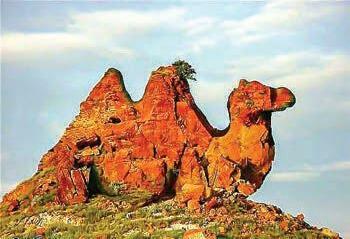
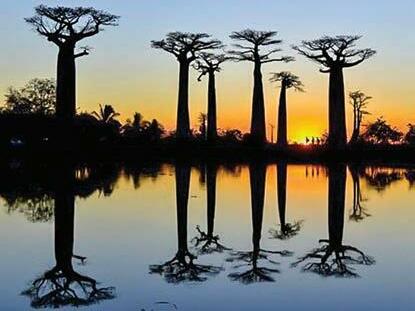
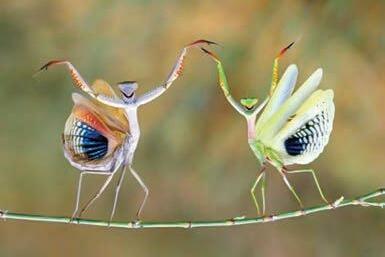
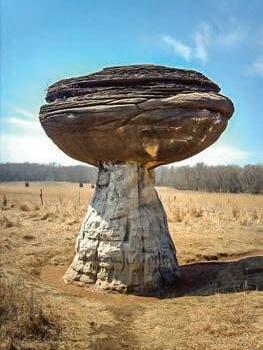

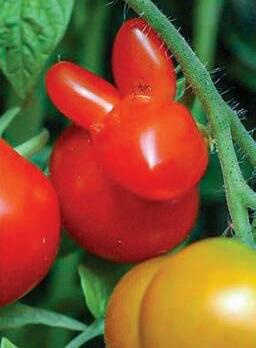
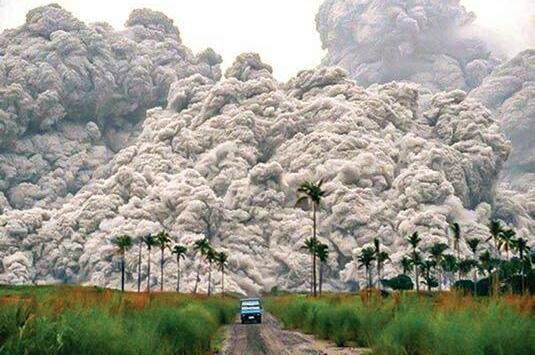
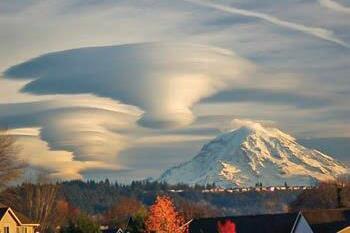


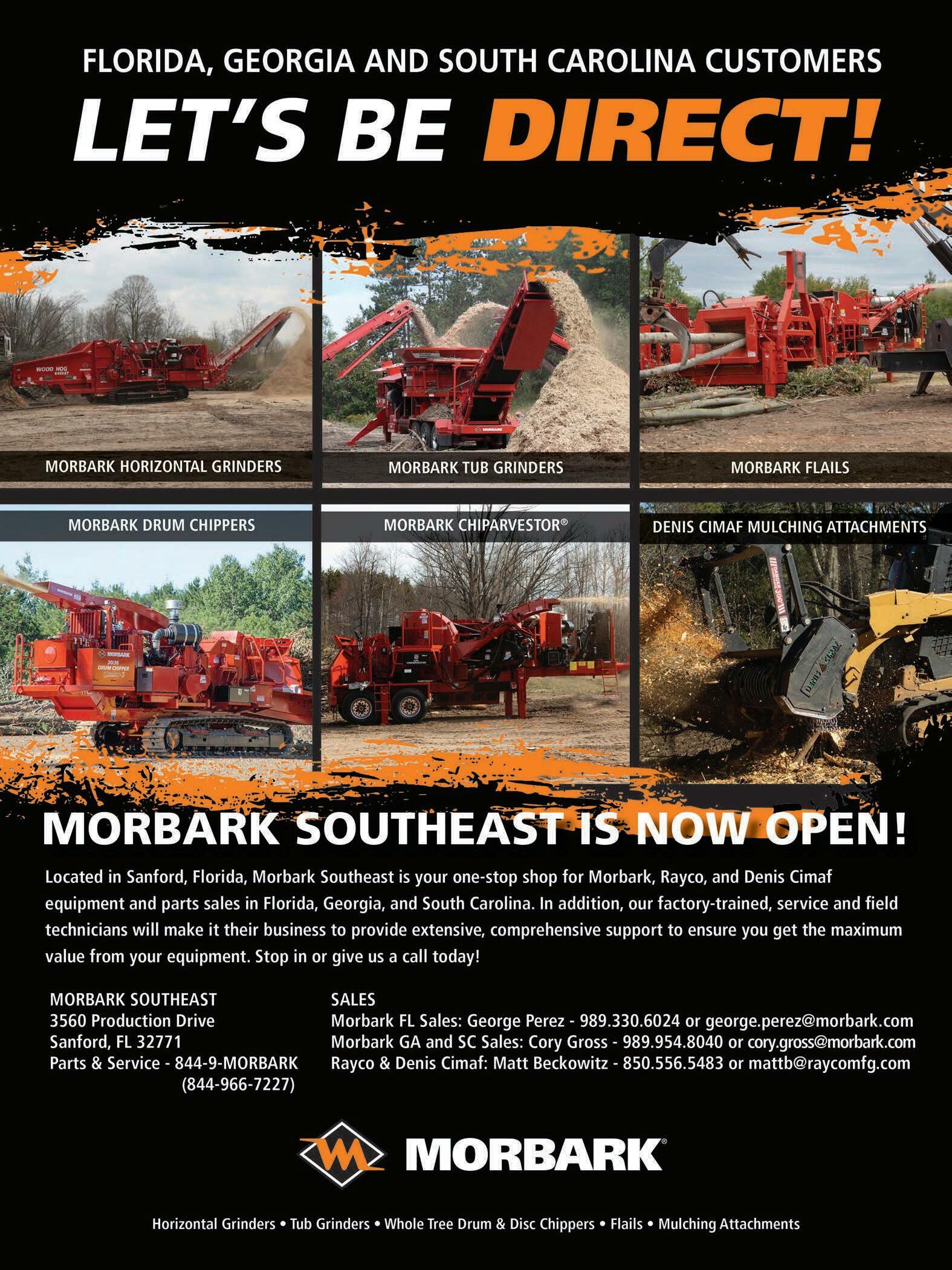
Not All Old And Gray
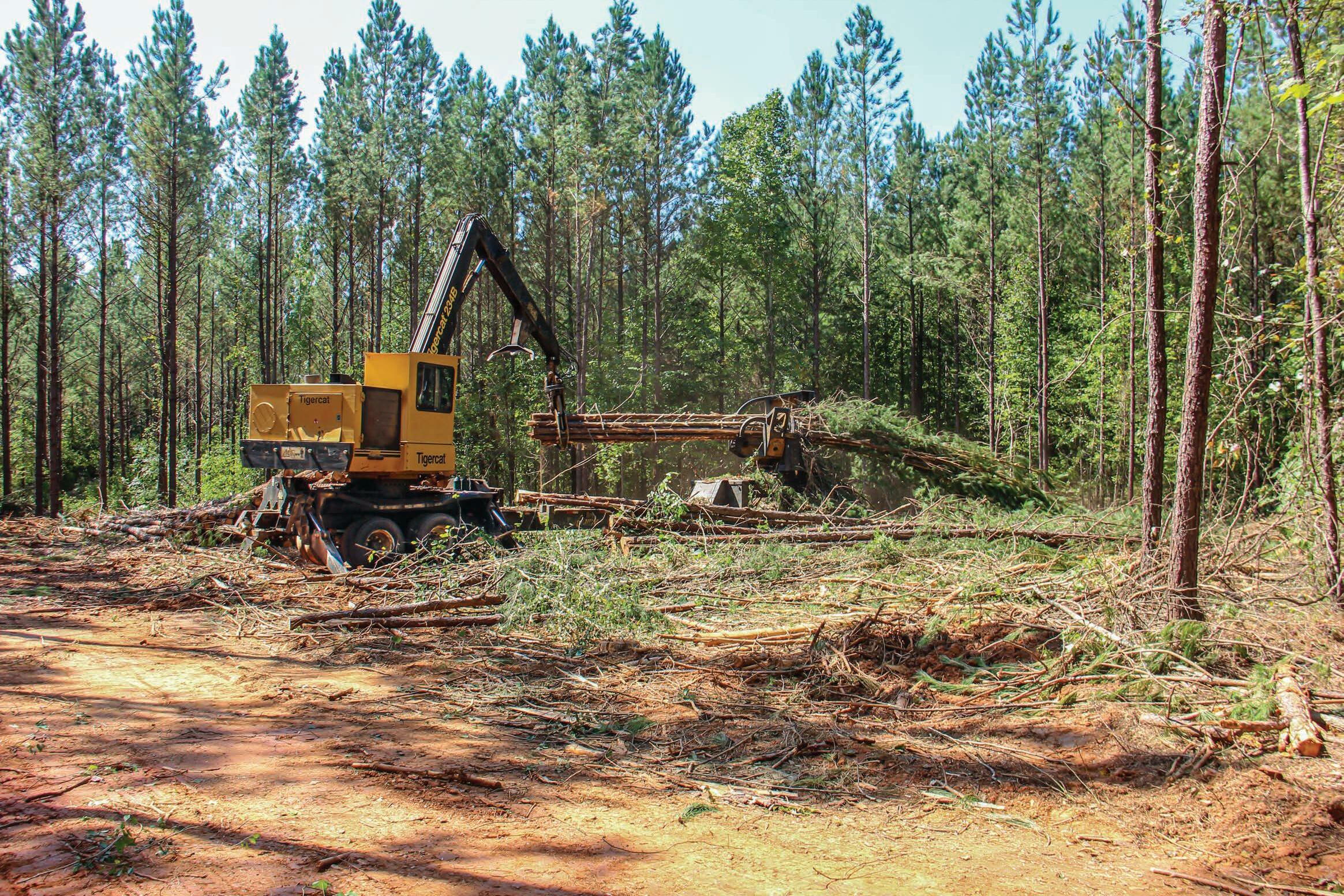
■ Griff Wilson is a prime example of younger loggers making a go of it.
Griff and Caroline Wilson have steadily built an impressive business.

By May Donnell
LOWRYS, SC
Griff Wilson, 28, began his logging career in the summer of 2012 with a chain saw and old-school chain near the farm in Lowrys, in Chester County, South Carolina, where he grew up. He had just graduated from high school and was headed in the fall to North Carolina State University in Raleigh. By that time he was a seasoned farm hand, having gone to work baling wheat straw at age 12. He managed to put together 10 log loads that summer and with the proceeds and help from his father, he purchased a used skidder. Each summer for the next four years, he worked that skidder.
He’s upped his production considerably since that time. And then some. The company now averages 80 loads per week, 45% sawlogs and 55% pulpwood. Wilson estimates his crews cut or thin some 40 to 50 acres

Growing Up
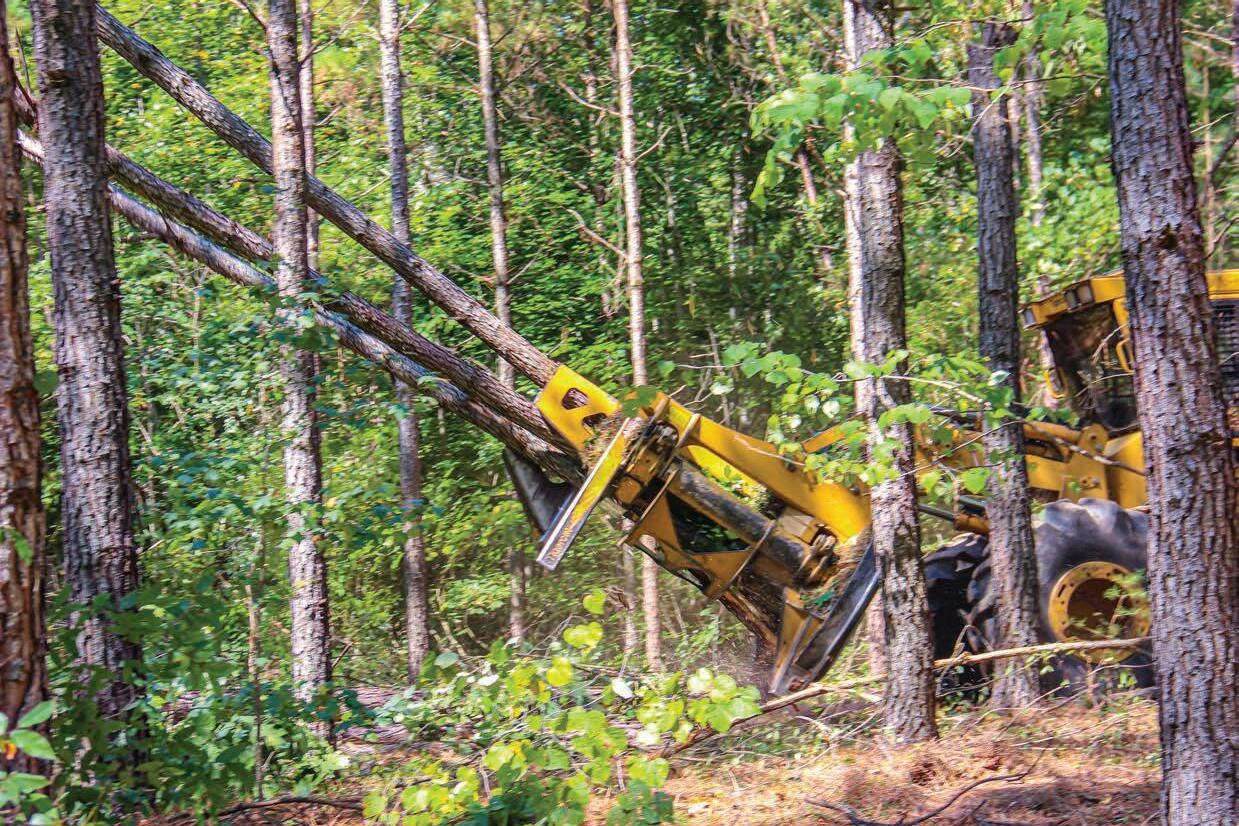
Wilson earned a degree in forest management at N.C. State, graduating in June 2016. He had spent all of his summer vacations in the woods, learning the business as he went along. He determined while still in school that he would go into logging and timber procurement and didn’t mind sharing with others his dream of joining the industry.
“I remember when I met Griff Wilson at a logging expo in Smithfield, North Carolina,” says Kevin Wright of Tidewater Equipment Co. in Newberry. “He was fresh out of N.C. State and he was intent on going into logging full time. He was young and enthusiastic and I predicted he’d make a go of it even though he was pretty much starting from scratch.”
Wright and Wilson over time became friends and business associates, with Wright furnishing Wil Ridge (Wilson’s company) with its inventory of mostly Tigercat for estry equipment.
“After graduation, I sold the skidder I’d bought just before college and that’s the money I started with,” Wilson says. He has had help all along the way from his very busy father, a successful crop farmer, cattleman, feed store proprietor and trucking company owner.
“My dad had helped me get started by giving me the money for a down payment on that first 1991 Timberjack 380B skidder. His father had done the same for him when my dad needed farm equipment during the years he was just starting out.”
Griff’s dad is Joey Wilson. Joey contracted his trucks to WilRidge in those early days to do the new company’s trucking since he knew the business and still shares his shop with Griff.
Griff was a young upstart for an industry where the average age of owners and crews keeps going up. But if there was any skepticism about Wilson’s ability to make a go of it, that died down when, still in his 20s, he started his own wood dealership, purchasing stumpage and marketing the timber that his company crews harvest.
WilRidge Forestry LLC was formed in 2016. A year later Griff formed the wood dealership, with both the logging and dealership operating under the WilRidge Forestry name.
“I had to build relationships with mills in order to supply them directly,” Wilson says. “It was a tricky situation. The mills didn’t know me yet. They didn’t know if I could produce in a reliable way and keep up with the quotas. I mean, we had to be really, really careful. We didn’t have a 20-year reputation behind us so we knew we had to quickly prove ourselves and keep proving ourselves.”
Wilson’s forest management de gree at N.C. State provided some credibility, especially for someone starting out in the logging business with limited experience and no existing family connections. “I needed credibility to make a name for my self in this business. Also, it gave me an advantage as a timber buyer be cause I am a registered forester and allowed me to understand the silvicultural goals behind logging operations.”
Wilson, who started with two em ployees, now runs two crews within a 50-mile radius of Lowrys, including Chester, York, Lancaster, Fairfield, Union and Kershaw counties.
Timber buyer Brennon Lipscomb soon joined the team as a procurement specialist. “My job is to stay in touch with landowners and others who might need our services,” Lipscomb says. “So far we’ve been able to find good tracts by keeping our ears to the ground. We’re proving ourselves with each job we do.”
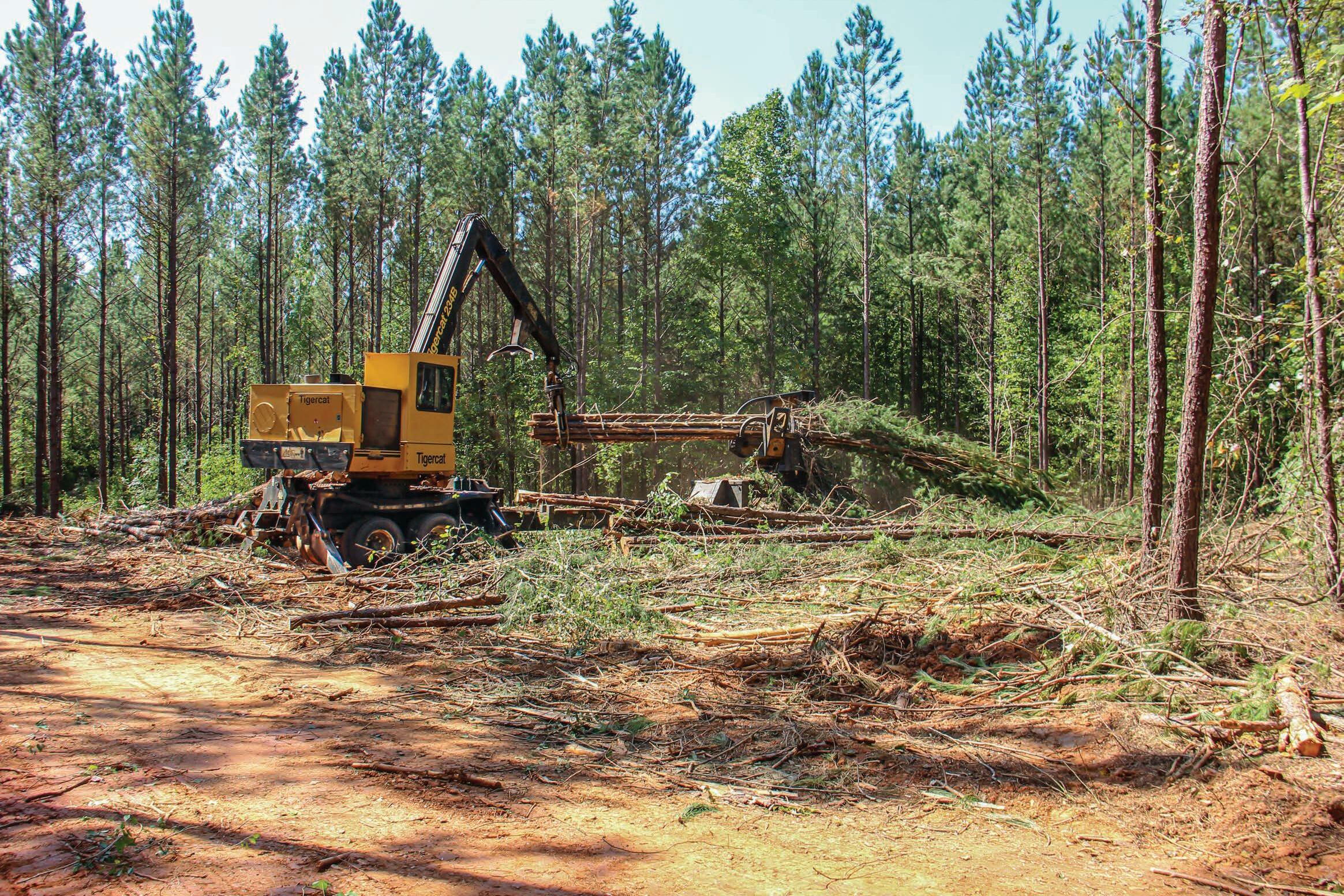
Three feller-bunchers are available to the two-crew operation.
Operations
SLT caught up with Wilson at work with one of his two crews on a vast pine plantation just a few miles outside of Chester. This crew had been at various sites on this tract for the past several months, second thinning as well as clear-cutting. There was still much more to do and Wilson was hopeful they could get finished and out before the rains of November turned the “black jack”
Left to right: Jim Comer, Morris Montgomery, Griff Wilson
Tidewater Equipment had a hunch WilRidge Forestry was on the right path.

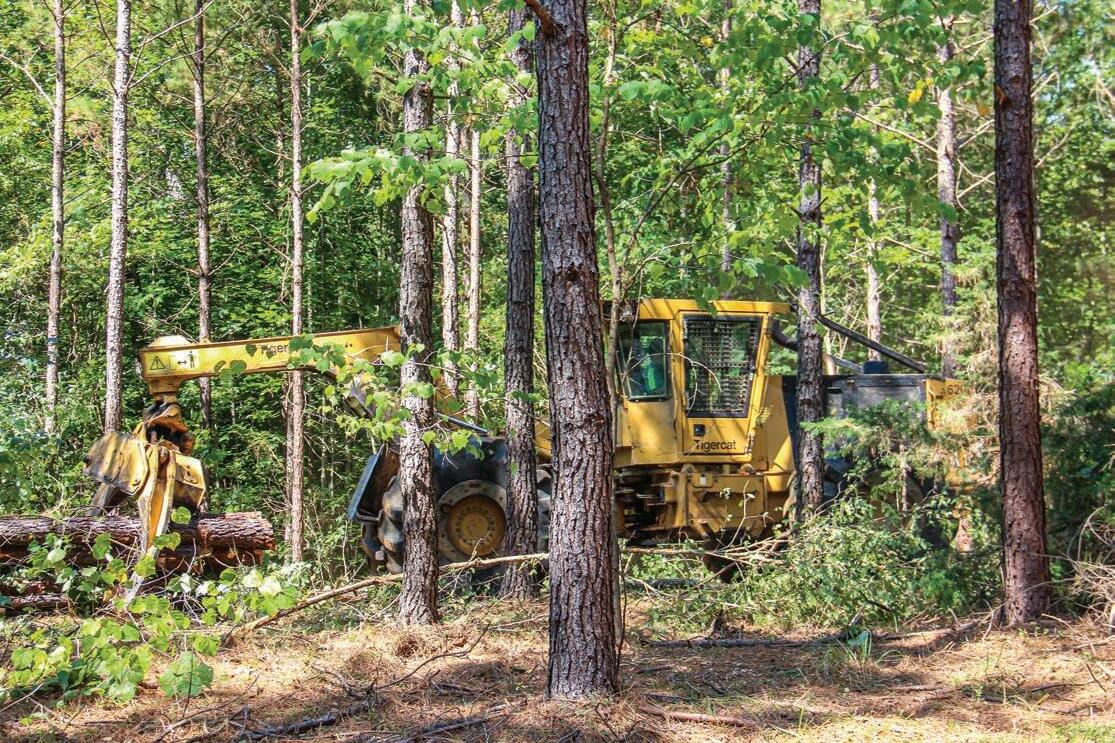
soil here into a hopeless quagmire.
Mission accomplished! By the end of the year Wilson had moved that crew to a pine stand in Union County, with the other crew continuing to work in York County.
Wilson says there is no market for biomass in the area. The nearest pellet mill is north of Charlotte, NC, which means having to deal with hauling past the sprawling metro area.
“There’s not a chipper anywhere within these three counties,” Wilson says, referring to Chester, Fairfield and York counties. “There’s no economic sense in hauling to a pellet mill 100 miles away.”
And speaking of economic sense, Wilson admits it’s a daily challenge keeping up with rising costs. “Seems like everything we use has gone up by 20% over the past several years,” he says. “Oil, parts, labor and insurance, you name it. We have to be so careful, especially because being young, you’re paying on everything you’ve got.”
Maintenance costs are kept to a minimum at least, because Wilson does about 75% of it. “I usually spend Saturdays in the shop we share with my dad. It is a significant savings that we’re able to do the routine maintenance ourselves.”
The company is fairly self-sufficient in that it handles the oil changes, chain sharpening and even washing its own fleet of Mack trucks. When parts are needed, WilRidge buys from Carquest in Chester or from their dealers. Insurance is purchased through Swamp Fox Insurance Agency in Monck’s Corner.
Fortunately, Wilson is blessed with a talented family. Griff’s wife, Caroline, runs the office and oversees payroll, insurance, trucking and whatever else comes up. She
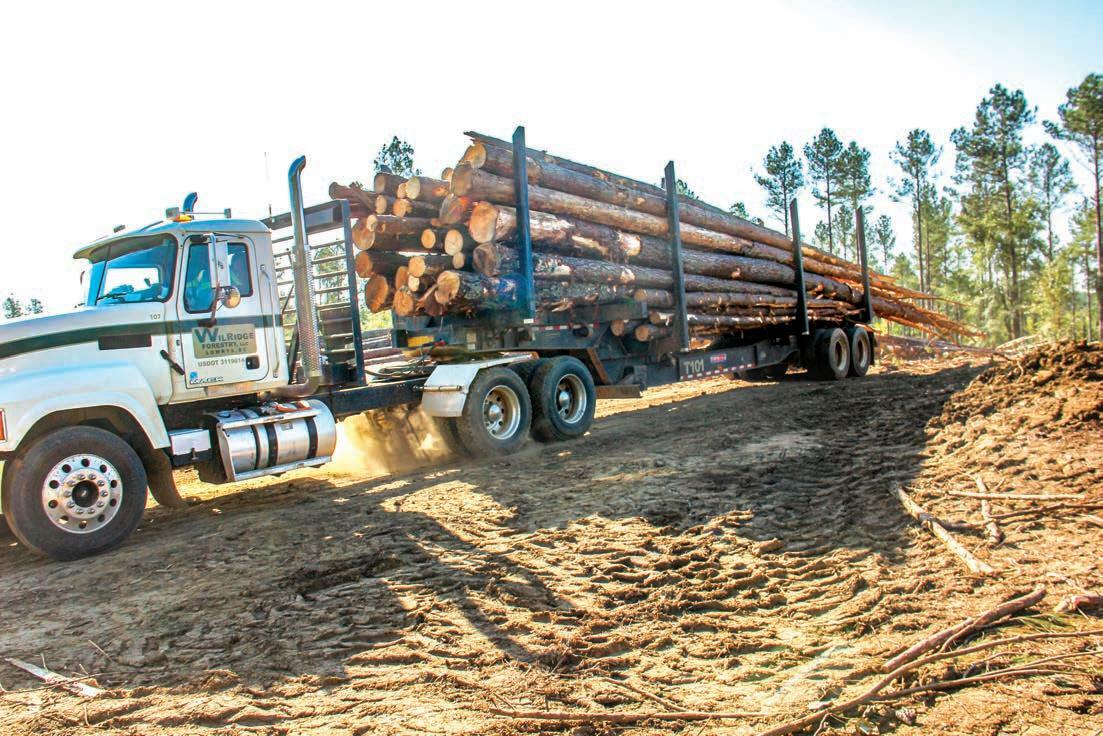
Sawlogs and pulpwood are moved to several mill markets.
WilRidge Forestry was running seven Mack trucks at last count.

has a master’s degree in agricultural and extension education from N.C. State but her own career path took a sharp turn. After her schooling and marriage to Griff she came into the company because there was a need.
“I never thought I’d be doing this kind of work but here I am,” she says. “The job is difficult but we’ve adjusted to it.”
Occasionally, Caroline is also needed to run to Charlotte or Rock Hill for parts. “We had an intern and he did the parts runs when he was with us but he went back to school,” she says with a sigh. Under her supervision, WilRidge began offering benefits like health insurance and 401K options, even though she admits there are few takers. “We do have some who take advantage.”
Caroline may not be quite as active in the business this spring and summer, with their first child due in April.
At the loading deck, it doesn’t take long to notice Wilson’s preference when it comes to hauling vehicles. The outfit operates with seven Mack trucks—model years 2005, 2006, 2007, 2013, 2014, 2015 and 2023. Company drivers are Will Sadler, Robert Prather, Boogey Man, Doug Hawkins and William “Papa Cool” Hemphill.
WilRidge Forestry trucks its goods to the New-Indy mill in Catawba, Boise Cascade in Chester, Stella-Jones in Whitmire, GeorgiaPacific in Prosperity, International Paper in Eastover & Santuc, CM Tucker in Pageland, Canfor Southern Pine in Camden and Associated Hardwoods in Gaffney.
Hauling is accomplished with five 2018 Pitts log trailers and a Pitts lowboy.
Wilson buys his Tigercat logging equipment from Wright and Von Dennis at Tidewater. He splits the equipment between his two threeman crews, which generally operate on separate tracts.
Skidders include a 2020 Tigercat 620E, a 2017 Tigercat 620E and 2016 Tigercat 620E. Skidder operators are Kevin Mock and Jim
Comer.
The outfit has two loaders, a 2017 Tigercat 234B and 2015
Tigercat 234. Loader operators are
Morris Montgomery and Timothy
Bolus.
Feller-bunchers are a 2016
Tigercat 720G and 2019 Tigercat 720G. Crew foreman Wesley Cope operates one cutter and Henry
Glenn runs the other.
Also included in the equipment inventory are three bull dozers, a 2001 Cat D5MLGP, a 2001 Cat
D5C XL Series 3 and a 1986 Cat
D5H. The crews each use a set of
Maxiload ccales. There is a 2005
Chambers Delimbinator, 1982 John
Deere 672A motor grader and two
Ford service trucks, a 2014 Ford F350 and a 2015 Ford F-350.
The second WilRidge crew that
SLT visited is one Wilson calls his
“younger crew.” They were a halfmile from the Broad River in western York County and were first thinning on a 60-acre pine tract. Pulpwood was hauled to the
New-Indy mill in Rock Hill.
Meanwhile, along with daily reminders about individual safety concerns related to the day’s operations, Wilson’s goal is to do monthly safety tailgate meetings.
All company drivers (log truck and service truck) go through a safety training when hired and two additional driver safety trainings each year.
In relatively short order, Griff
Wilson has turned a chain saw and an old chain into a double crew force to be reckoned within the region where he lives.
“I knew early on I wanted to be in the logging business,” Wilson says. “With some help along the way I’ve been able to achieve what I set out to do. Not that it gets any easier.”
Indeed the biggest challenges heading into the new year remain continuously rising operating costs and finding/training quality operators. But Wilson is optimistic.
“We hope that we may be able to continue to develop new operators, strategically grow production and take advantage of potential new opportunities in the market.” SLT
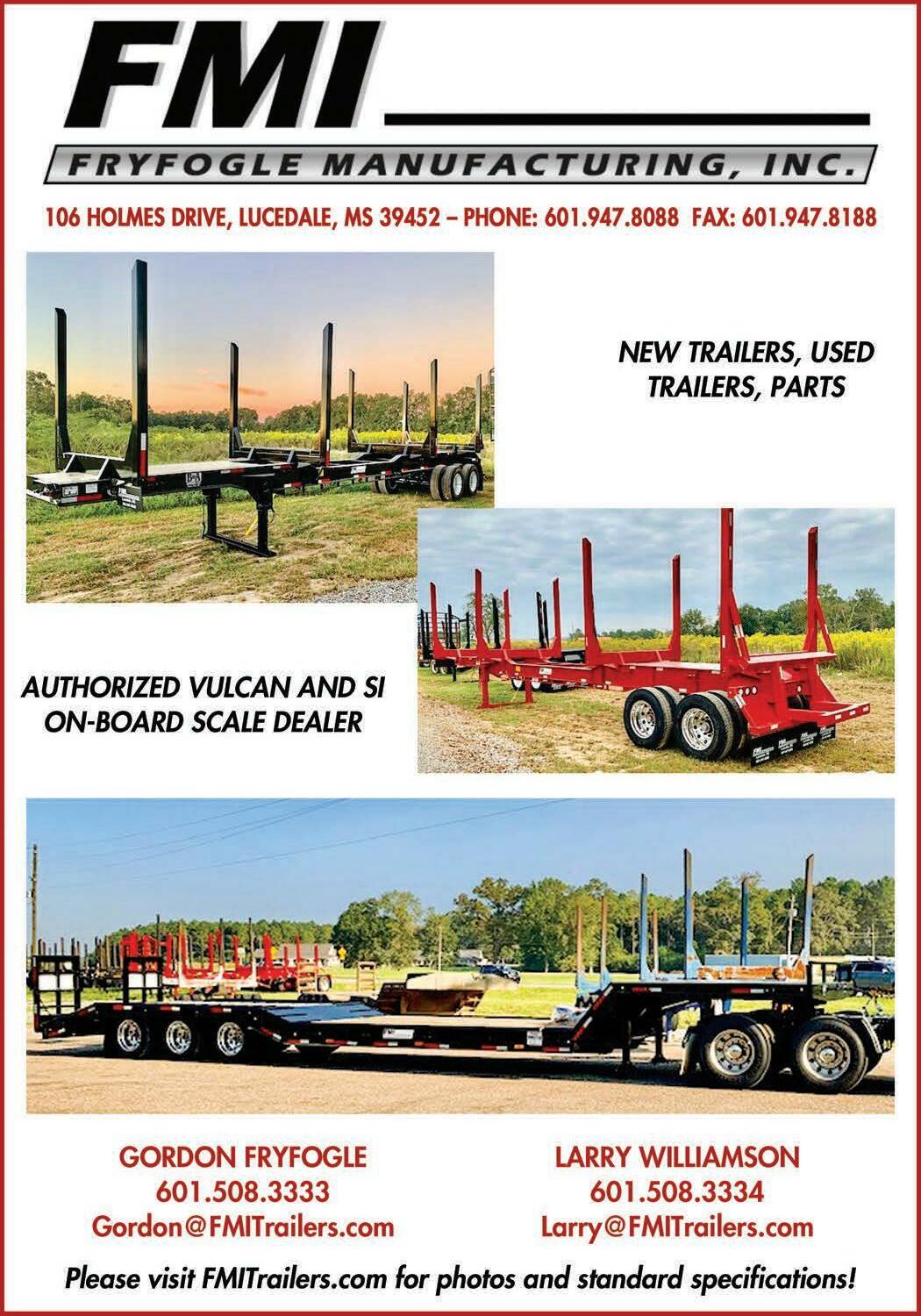
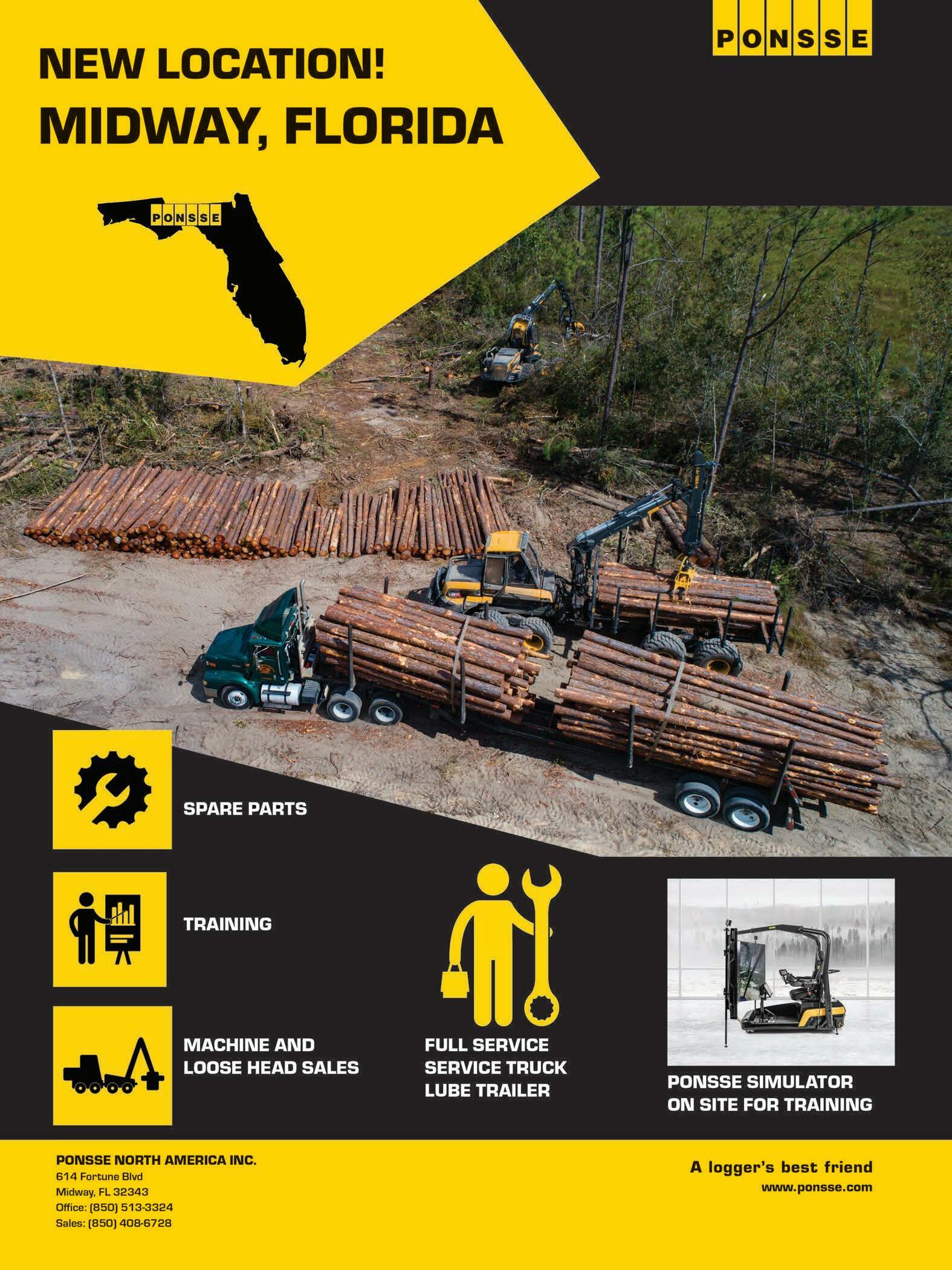
BIG JOB
■ Tackling a monster oak wasn’t too tall an order for Mark Dotson and his Tri Rivers crew.
Not the kind of log you see every day...
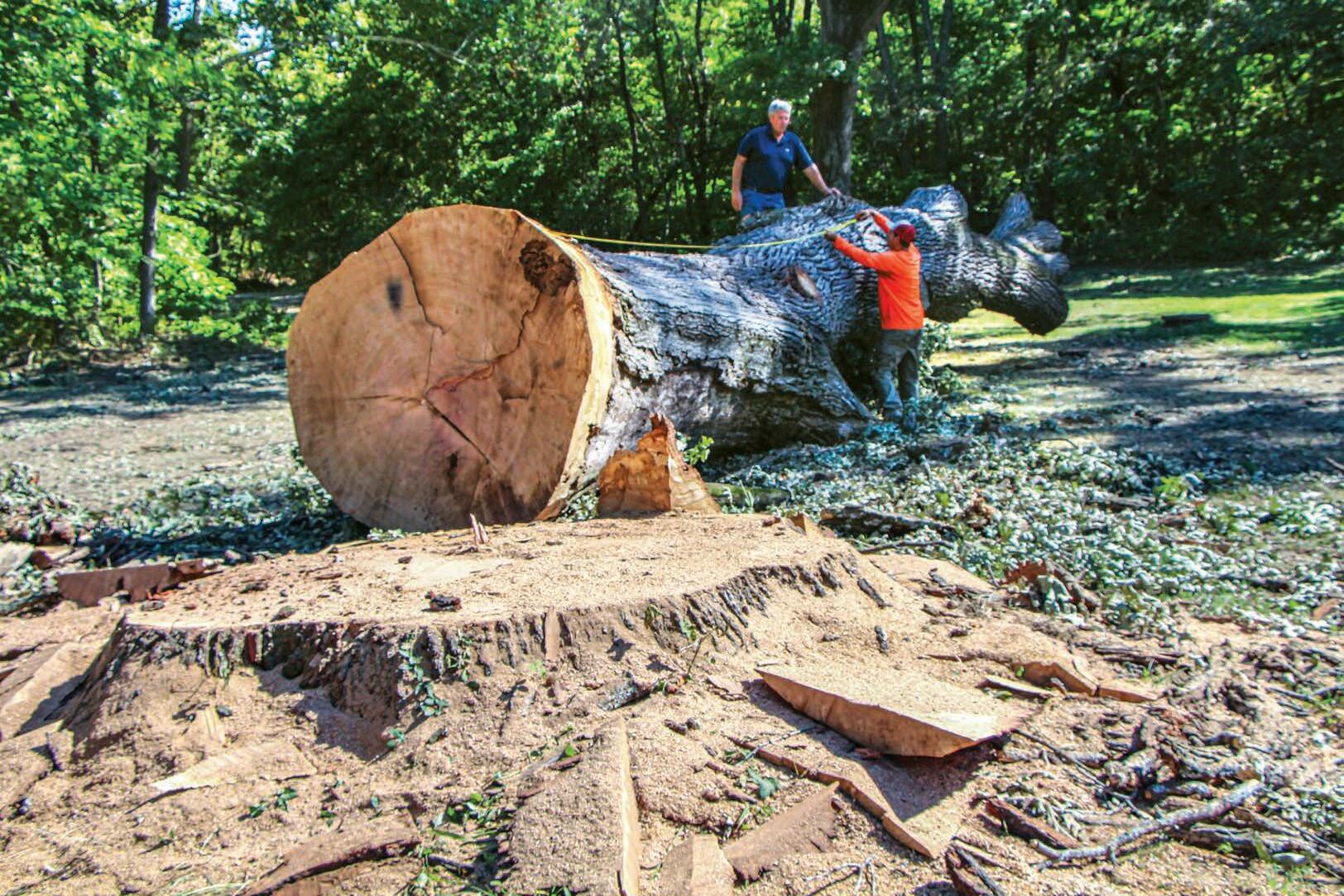
Dotson and his men had to make a plan how to handle this bad boy.

By David Abbott
CAMERON, Mo.
Mark Dotson, 59, the owner of Tri Rivers Enterprise, runs two crews. Both crews work in a variety of tract types, but when Southern Loggin’ Times caught up with them last fall, the Tri Rivers team had a very atypical job. On that day, instead of deep in the woods off of a rural dirt road, SLT found Dotson’s equipment at Lord’s Park in downtown Harrisonville, a suburb of Kansas City. This bid job, with timber marked by private for estry consultants, was full of large walnut trees, and a few oaks. One oak in particular presented an in triguing logistical challenge. Near the back end of the park, this one measured seven feet diameter on the butt.

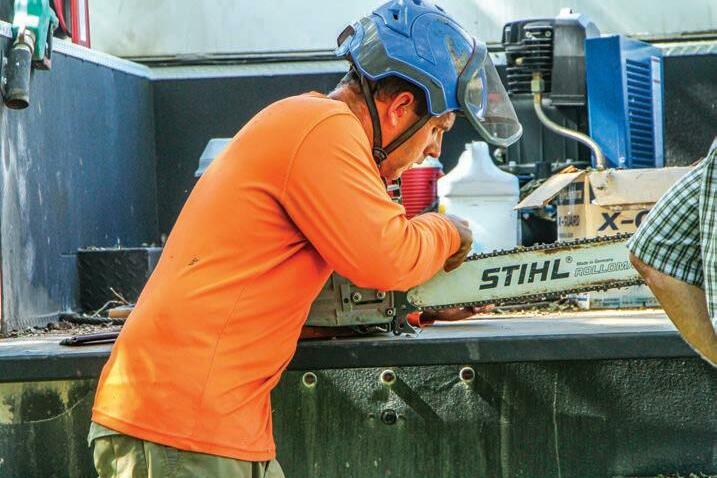
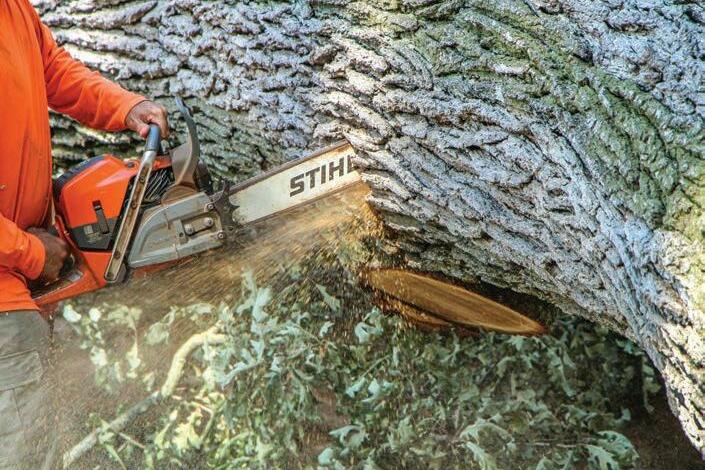
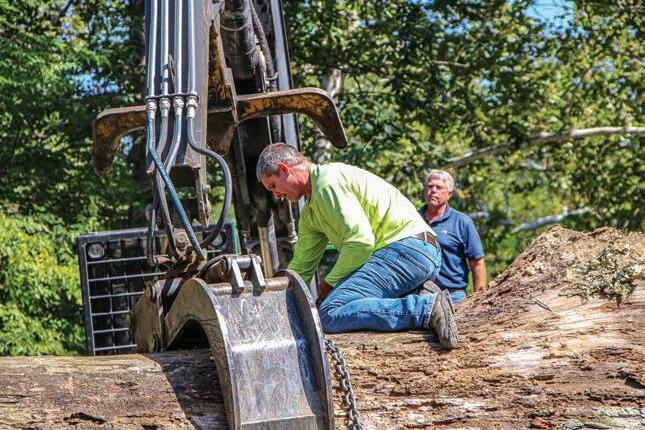
Crew supervisor Blake Sedgwick (left, center) had to keep the teeth sharp and his skills sharper; mechanic Eric Brownlee (right) helped set chains from the loader grapple around the log.
The loader pulled from one end, the skidder from the other.
Coordinated effort got it rolled up onto the lowboy.
By counting the growth rings, the Tri Rivers team estimated the tree to be about 390 years old. If their count was accurate, that would place it having first sprung up sometime in the 1630s, about 20 years after the time of Shakespeare and the first publication of the King James Bible, 10 years after the pilgrims landed at Plymouth Rock, and almost 150 years before the U.S. transitioned from British colonies to independent nation. That’s how long this tree has been sitting there in Missouri—since 200 years before it was Missouri.
Unfortunately, the tree had reach ed the end of its life cycle, so Harrison ville needed someone to re move it before it finished dying and became a problem, along with several others on the site. Dotson won the bid.
The tract wasn’t large in terms of acreage, but with such large trees (this was the biggest but many others were above average), the amount of fiber per acre was well worth the time. “It was a really high-end, unique job,” Dotson says. “We get a few specialty trees. We don’t seek them out but they happen to come up on our job from time to time. It’s hard to get a large amount of them, though, because there just are not a lot of these kinds of trees left.”
It took three tanks of chain saw fuel just to cut the butt; the top had to be taken down with a bucket truck to keep it from breaking; while standing, its estimated height was 100 ft. Chain saws aren’t in common use on this mechanized crew, but it’s a good thing someone still knows how to use one skillfully when it’s needed.
Felling this beast was just half the battle; getting it loaded and hauled away would be no mean feat. No grapple would be wide enough to grip it, no boom strong enough to lift it unaided, and no regular log trailer large enough to hold it. But the team came up with and executed a plan that, eventually, got the job done. A John Deere 437 loader and 648H skidder rolled it up onto a lowboy a little at a time. The knuckleboom used grapple and chains to

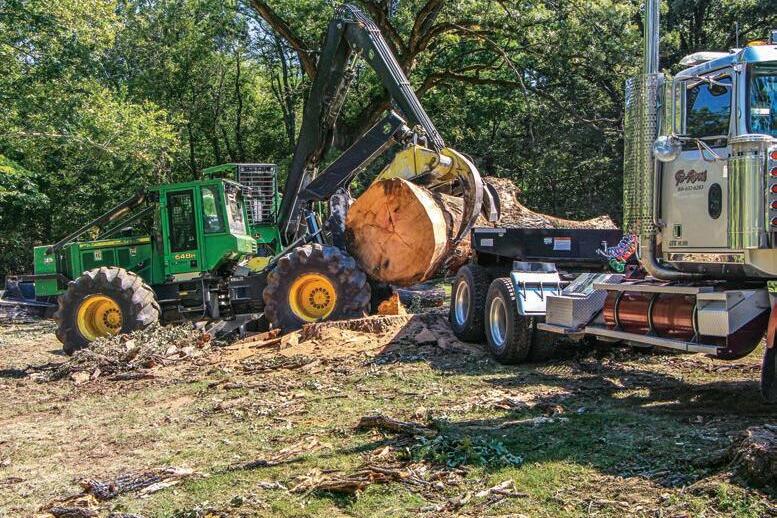
The skidder pulled with the grapple, then turned around and pushed with the blade, with nephew Andy Harper lending his eyes from the ground to help guide the machine operators.

pull from one end while the skidder alternated pulling with its grapple and pushing with its blade on the other end. Finally, they maneuvered it onto the flatbed.
It was an impressive display of skill and coordination by the team; not just any group of operators could have handled it so well. “We have really good help,” Dotson affirms. Eric Brownlee (full-time mechanic), Blake Sedgwick (Dotson’s son-inlaw and supervisor over day-to-day operations in the woods), Huey Jacobs (truck driver) and Andy Harper (Dotson’s nephew) were onsite to help; they represent a lot of years of combined experience.
Dotson didn’t haul this behemoth to a mill; what mill could handle it? He held onto it, planning to market it via social media and see what kind of interest it attracted. He figured a few high-end tabletop makers might put it to good use. He paid the city $3,000 for the tree; it ended up fetching him $12,000.
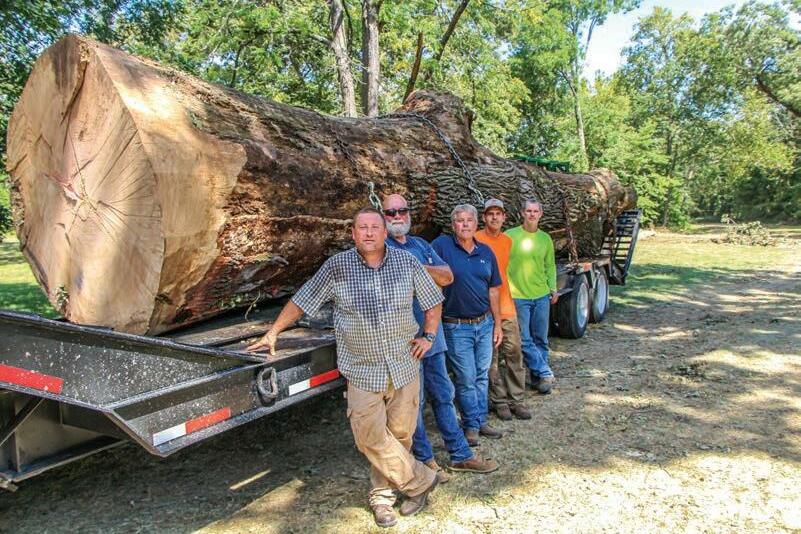
Equipment
Between the two crews, Tri Rivers uses two John Deere 648H rubber tired grapple skidders and another 648L that runs on a forestry track system from G&R Manufactured Solutions. Dotson doesn’t run this machine on every job, but in steep terrain or wet conditions, it sure comes in handy, he affirms. “We have worked it in up to 35% grade,” he says.
On each crew, the skidders pull to either a 437E John Deere loader with CSI slasher/delimber package, or to a self-loader truck. Tri Rivers has 18 trucks all together, mostly Peterbilts with a couple of Western Stars. Seven are quad-axles with Rotobec self-loaders pulling double bunk pup trailers. For felling, Tri Rivers recently acquired a new TimberPro 755D with 2900 intermittent head for one crew; the other uses a Cat 573 with single point hot saw.
Dotson buys John Deere equipment from Murphy Tractor & Equipment Co. in Kansas City, and bought the TimberPro from Bush Forestry in Huntingdon, Tenn.
With those G&R tracks on the skidder and the TimberPro, Tri Rivers is not too limited in terms of when, where and in what conditions they can work. “With the equipment we have today, we just don’t have very many down days,” he reflects. In fact, he considers, “We need more down time to work on it.” Tri Rivers has a shop for routine R&M, and Brownlee also has a Peterbilt service truck to handle urgent repairs in the field when needed.
The logger prefers Mobil synthetic motor and hydraulic oil. “They have a really good blend that can take the heat; we run it in everything we have.” He reports only routine problems with newer Tier 4 machines—DEF tank sensors and such. “Most of the time they don’t act up but once in a while they do. If you are relying on just one piece of equipment you’re in trouble,” he believes; that is why he keeps several spares and backups.
Dotson used to operate seven days a week, but has mostly cut back to five now. “It is hard on the help,” he explains. “I have found out if you work too many days, they are worn out and you don’t get as much production for the time spent, so you might as well just cut it back. Now if it is a rainy season, when it is too wet to work sometimes, then we might run seven days a week to make up for the time lost.”
Left to right: Andy Harper, Huey Jacobs, Mark Dotson, Blake Sedgwick, Eric Brownlee
Timber
Tri Rivers logs private timberland, relying on an established reputation with landowners, who often contact Dotson directly when they want their property cut. He buys a

This one definitely needed to be chained down tight. Ready to roll; Dotson was able to sell it for a sizable profit.

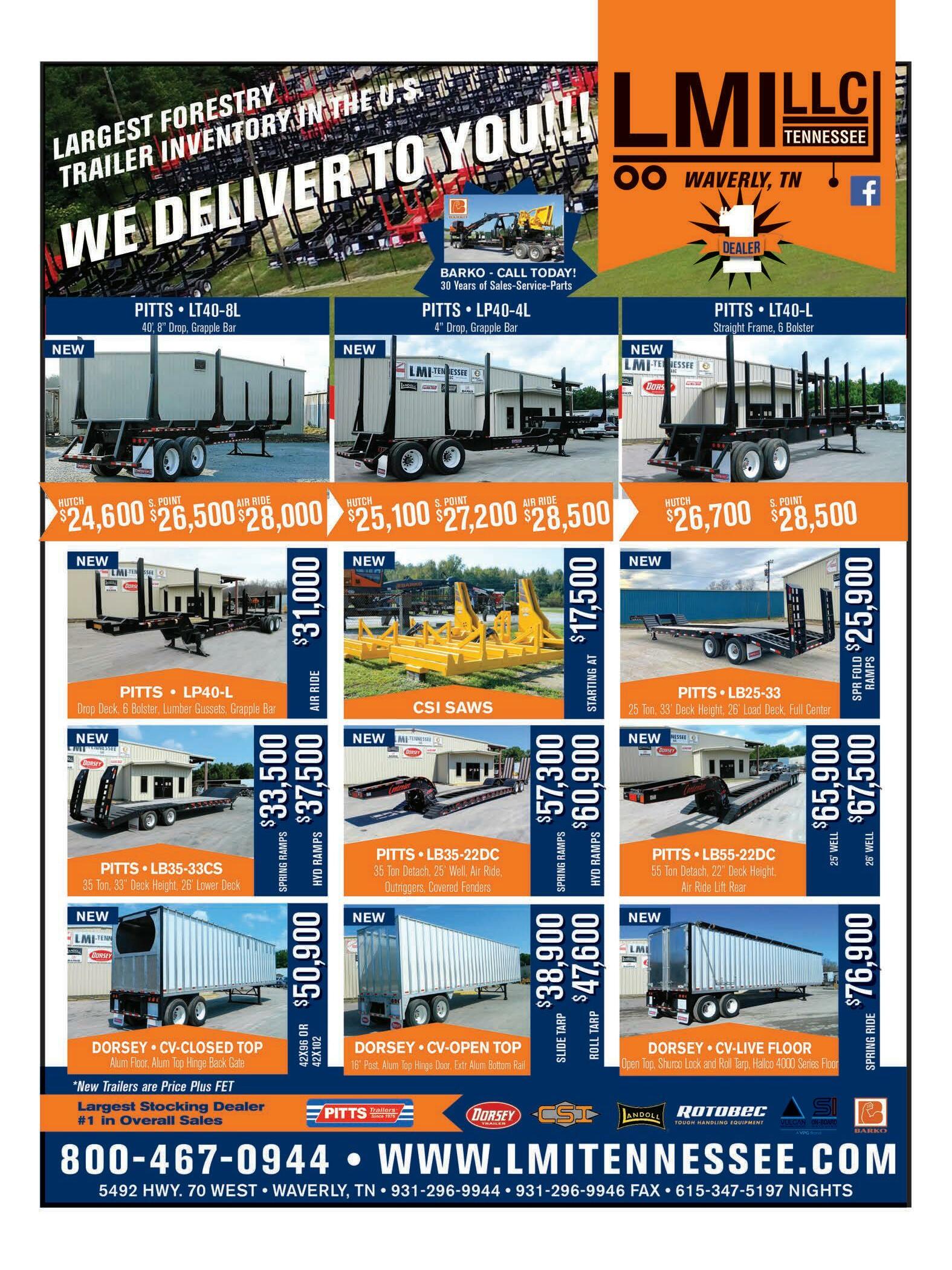

For more manageable logs, Tri Rivers uses self loaders with pup trailers. G&R Tracks keep them working in steep and wet ground.
lot of his own timberland as well, and buys some tracts from consulting foresters.
“Our timber varies so much,” Dotson reflects. “We don’t have a lot of large tracts. It is mostly smaller private land, but once in a while we get on a really good tract of timber where one crew can put out 10 loads a day.”
The crews work within a 200mile radius from home base; Dotson would prefer to stay within 100 miles, but with so much row crop farming in the area, he’s found it necessary to go outside that range and move around a lot to keep busy during the summer.
Dotson also travels to work disaster relief after hurricanes or major tornadoes. Back 12 years ago, he went all the way to Alabama after the deadly Tuscaloosa tornado in 2011, and his brother did the same a month later closer to home in Joplin. Instead of storm timber removal, they focus on debris cleanup, subcontracting under AshBritt Environmental, a national turnkey rapid-response disaster recovery and special environmental services contractor based in Florida.
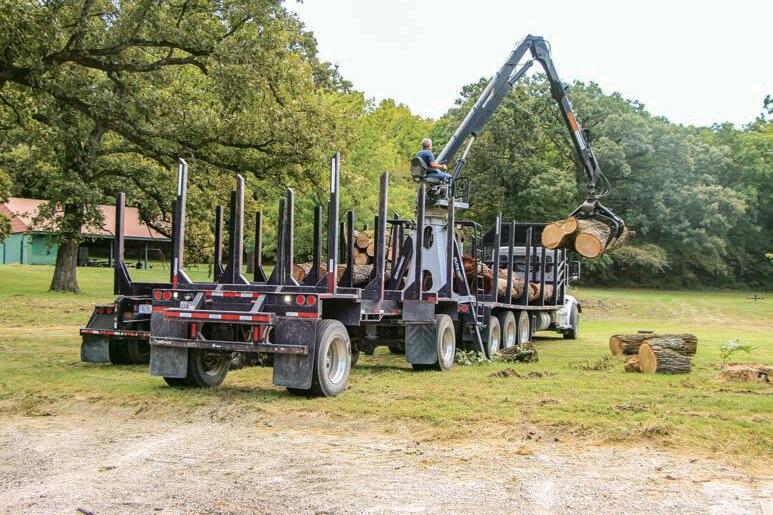
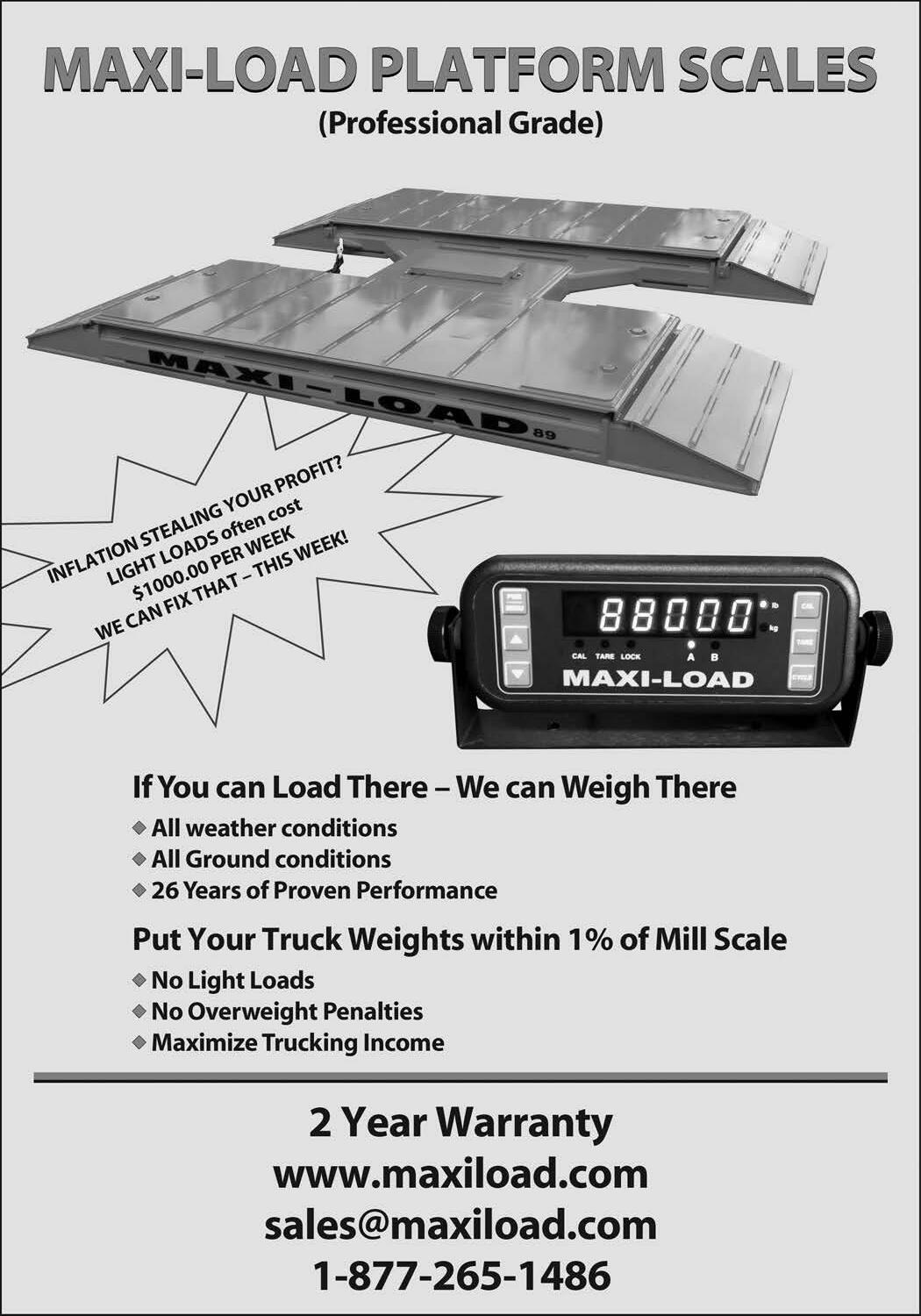
Family Background
Dotson is a third generation logger. “My father and my grandfather sawmilled and logged years ago down in Arkansas, down in the Buffalo River range,” he says. “It was really hard to make a living there, so dad moved to Missouri in the early ’60s. It has been tough at times but we keep trying to find another niche and keep going.” Mark worked with his dad and older brother Mike through high school and for a year or two after. Then he and Mike struck out on their own, working together for about a year before branching off separately. Mike started his company, Timberline Trading, and Mark started Tri Rivers Enterprise. Their younger brother Tim also followed with his own company, Dotson and Sons. Their oldest sibling, a sister, has her own business, too, in catering and formal wear rentals.
Mark and wife Kim have two adult daughters, Ashley and Dan ielle, and several grandchildren. Ashley’s husband Blake (they have three kids) works with his father-inlaw at Tri Rivers, supervising operations in the woods day-to-day. Danielle and her husband Garrett are in row crop farming, working a few thousand acres of corn and beans. Kim serves as secretary for Tri Rivers, handling office paperwork. “She does an awesome job with that,” Dotson says. SLT
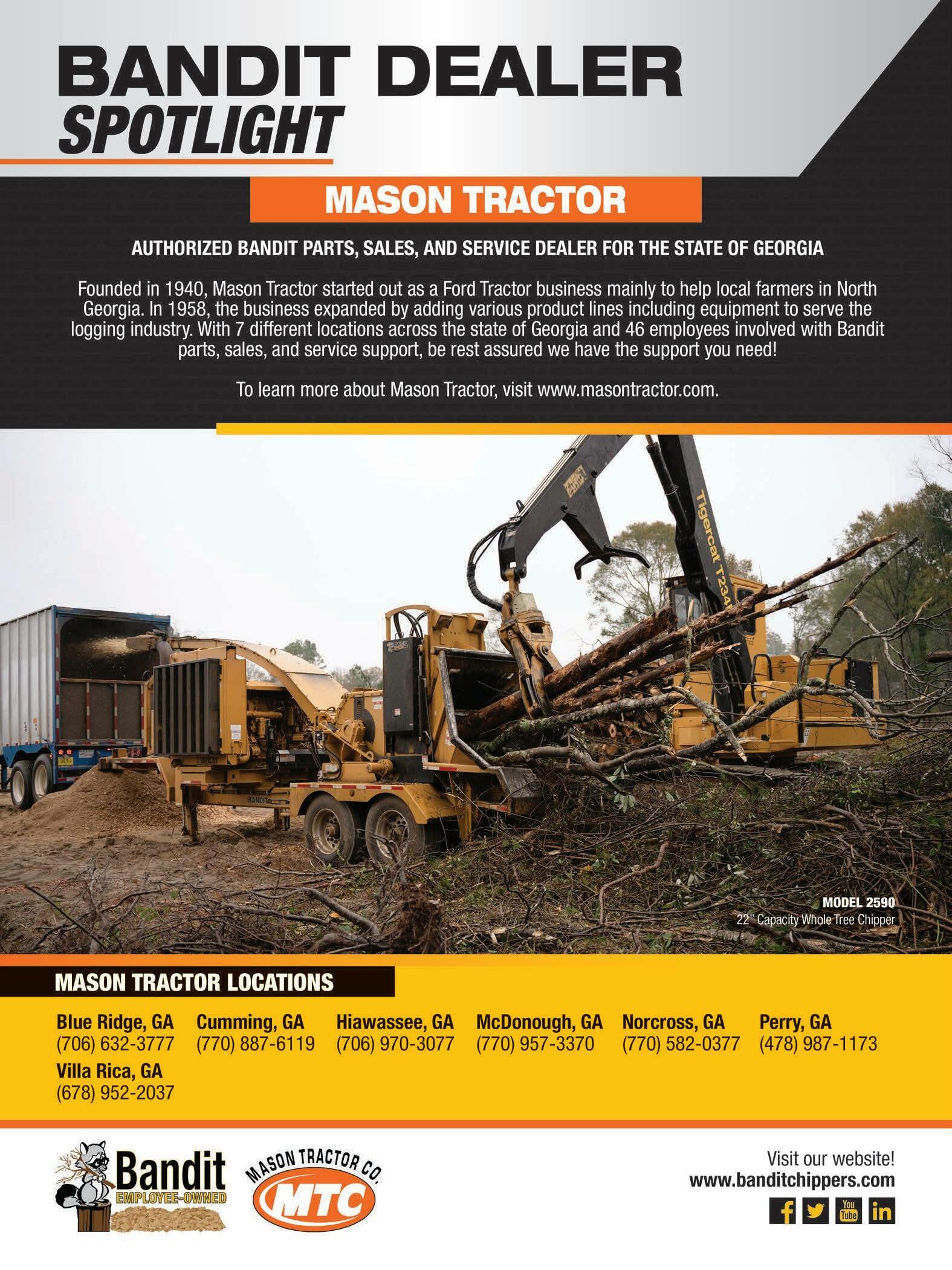
Right Track
■ After a troubled start, Woodville Pellets looks poised for success with new management and buyout.
By Jessica Johnson
WOODVILLE, Tex.
Plagued by neverending drama—from financing to fire—the former Texas Pellets facility here and its nearby port facility never saw the consistency that many other industrial wood pellet operations in the pine-rich U.S. South have experienced over the last decade. Instead, it battled engineering issues, machinery issues, staffing concerns and then finally a bankruptcy.
When Baltics-based Graanul Invest, one of the world’s largest and most reliable wood pellet producers, purchased the mothballed six-year-old plant at auction in 2019, to be blunt, the facility was a mess. Still, it had an untapped potential. But first, some of the lingering legal messes had to be cleared by the administration. Then the familiar song of COVID-related delays killed some of the company’s timelines for re-start. But, as they say, the past is the past and the future, well, the future for Woodville Pellets, as the operation is now called, is bright.
And it starts with recent industry veteran hires Jason Ansley as Vice President of U.S. Operations and Earl Herndon as General Manager of both the Port of Port Arthur facility (which was included in the purchase) and the Woodville site. The pair, having worked together for another manufacturer, have an easy comradery and clear vision of what they want the facility to achieve. Both see what the plant can be and want to get there—while also recognizing the process will take some time.
“The path we are on is going to be bumpy. There are things that will be up and down. We’re going to find something we didn’t expect,” Ansley says of the process to bring the facility to Graanul’s world-leading standards. But he’s quick to point out the team in place is going to help them get there together.
Herndon echoes him by saying that with all transitions there are pain points, and turnover happens, but the knowledge base with the 78 employees, some of whom have been with the facility since commissioning, is unmatched. And the team will stay focused and reach its
aspirations as long as no one, including the two at the top, gets overwhelmed. ★ Adding, “It’s always going to be about people; that triggers everything else. You focus on people and you get everything else done.” Herndon has only been on the job since late summer, but putting people first has already helped the plant actualize some of its goals.
Herndon is also incredibly invested in the team because this is his first facility to manage. He says he had gotten out of the industry when Ansley came calling to chat. Once his steel toes hit the ground and the sweat started coming, he knew he wanted in.
“I love the energy of the facility, but I also love the ability to be active here. You can affect real change here,” Herndon says. “You’re on the ground floor, but there’s also Jason’s leadership. He is really understanding if we want to change something or try something different. He will talk with us about it, get the details and let us go do it.” This perspective and open line of communication has brought the team success in data reporting and becoming much more aware of possible maintenance and processes that can help the plant run more efficiently, and strive to reach its nameplate capacity of 500,000 tons annually.
While Ansley and Herndon are leading the way in Texas, they are not on an island, and are definitely not without support from their head office in Estonia.
European Influence
Although Graanul Invest is a relative newcomer to the North American landscape, the company is wellestablished as the second largest pellet producer in Europe with 11 pellet plants and six combined heat and power plants operating in Estonia, Latvia and Lithuania. The U.S. facility brings Graanul’s pellet production capacity to 2.7 million metric tons. Ansley reports that Graanul has a good balance in that the team overseas is willing to help out, send people over, pick up the phone and support the U.S. team, but also is willing to allow the U.S. operation to take point and work through the process and get things done on their own. Herndon says the Graanul teams in Europe are very conservative in their thinking, and like to think things all the way through before making suggestions—an approach he respects deeply.
Ansley, who has spent time at the European plants, says the culture that Graanul has worked hard to build is evident. Employees are methodical in their approach to the care and upkeep of the plant’s machinery and structures and invested in the work the company is doing. That’s exactly the way he wants Woodville’s culture to become. He says, “You can tell it was not an overnight process; they invested time and money in getting it right and now culturally, they are invested in sustaining it.”
Herndon was not able to make the trip abroad, but from talking with other managers, watching videos Ansley and others have taken, he says he got a good feel for the operations, and loves the way they are organized. He echoes Ansley that it was clearly not an overnight process but something he certainly wants to reach in Texas— even if that means moving deliberately and recognizing the discipline needed to get to the point where everything doesn’t have to run fullspeed all the time. Instead, Herndon is having the team focus on small pieces of the single points of failure that have been identified, or areas that need cleanliness attention, get them handled and reach sustainability. Then move on to the next portion of the process. For Herndon and Ansley, it’s all about the sustainability of the plant—a plant they’ve only been working with for right around six months as a team, and a plant that Graanul has only had control over for three years.
“It’s an interesting spot to be in. This plant is nearly 10 years old. It obviously went through a bankruptcy. Graanul has only owned the facility for three years. In the grand scheme of things, that is not a whole lot of time,” Ansley says. “The facility has good bones with the layout and equipment.” Woodville has to get the right people in place, the right systems in place and then strategically invest in upgrades where it makes sense, he adds.
The European plants put more emphasis on stability, Ansley notes, than on just throwing around invest-
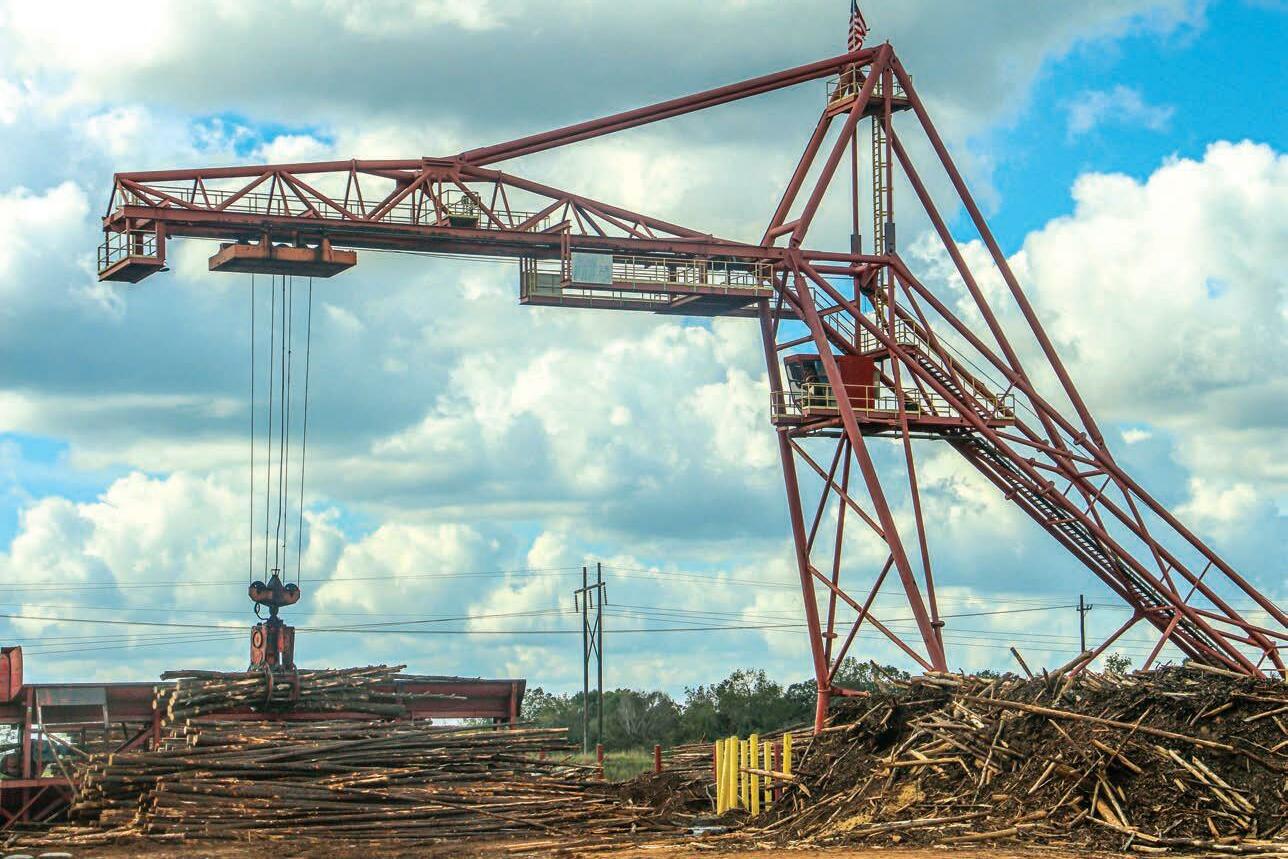
ments. “They do not run around and just tape something up and hope that it lasts for six months. They stop and fix it. They have redundancies built in. Earl and I are going through a list of where our single points of failures are and working through that. But it is too early to commit to next steps on projects. Because they are definitely out there and the company is very supportive of investing in the success of the plant.”
Ansley reiterates that this will not be an all at once process. There have been several projects that have been completed since the purchase, including air emissions control enhancement and upgrading the wet hammermills. The single most obvious project done by Graanul is pouring concrete and building a maintenance shop that wasn’t previously on site. Herndon and Ansley also added stairs to the Port of Port Arthur. Herndon says these projects aren’t, on face value, going to get the company more tons, or reduce costs. But it is about helping people do their jobs and making a better working environment. And that goes a long way culturally in the plant.
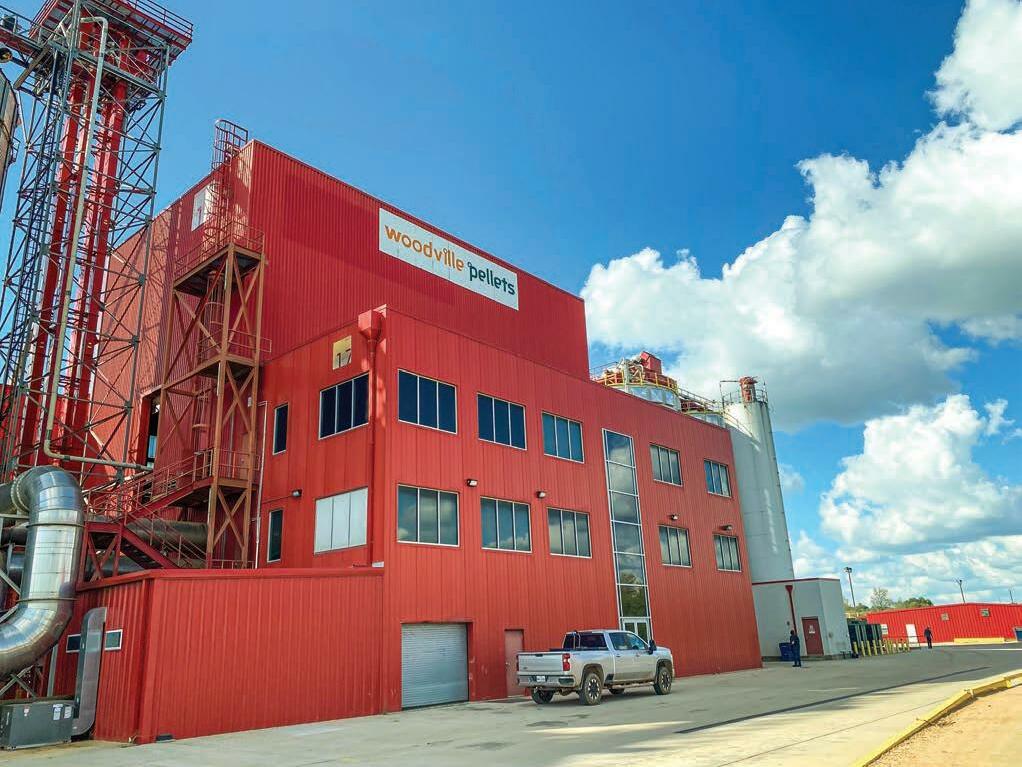
Doing The Work
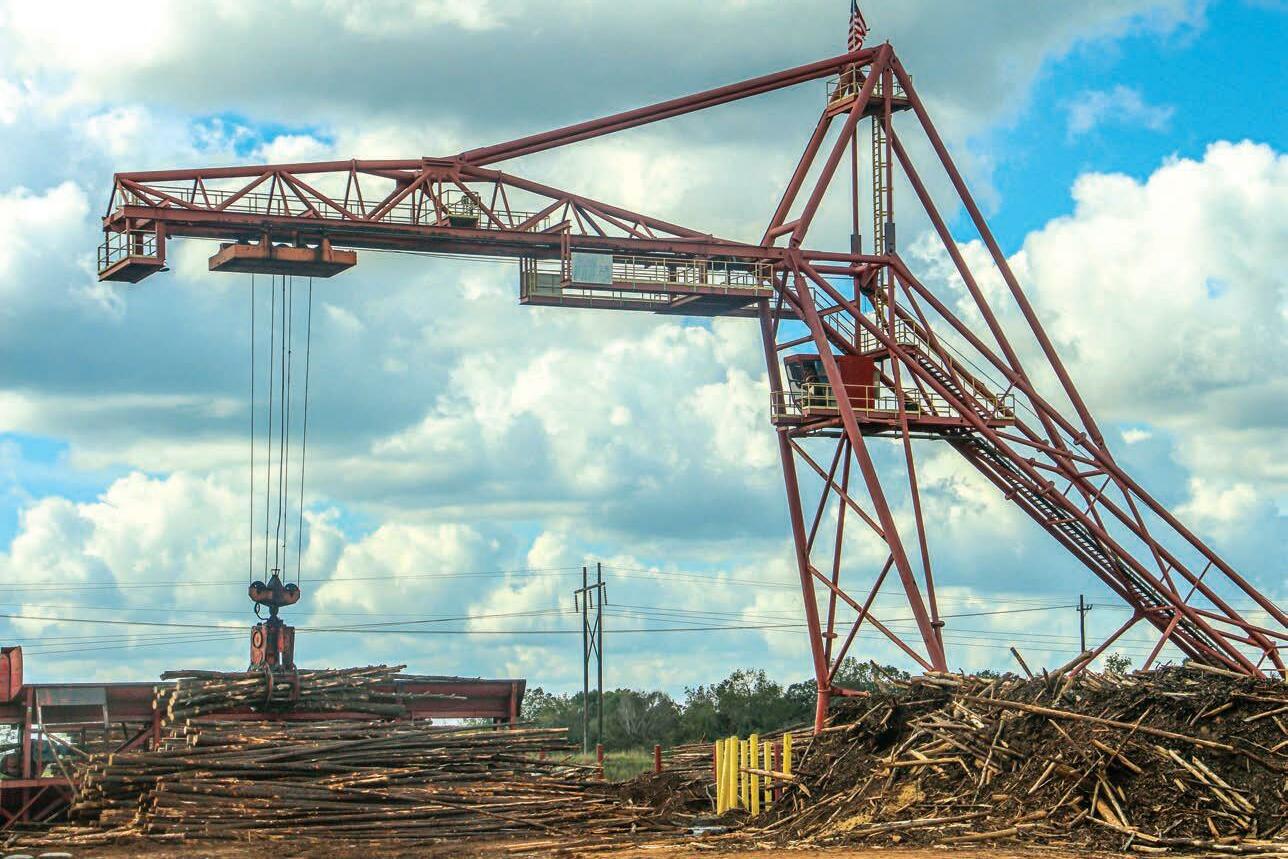
The facility operates four shifts, which gives staff plenty of time to transition from day to night. This includes giving staff every other weekend off, with two weeks on days and then back to nights. “This way you can get your internal clock in order instead of constantly switching shifts. And you always have time to run errands and get those kinds of things done, while still having your weekends back,” Herndon says of the shift change Ansley made.
The changes to the shifts are part of the bigger emphasis Herndon and Ansley put on employee experience. Herndon explains, “We made some key internal moves. A lot of people have been here for years, through the ups and downs. They are really dedicated. If I have a question about a part, Keith Mahaffey has the knowledge. We want to invest in them and make their jobs easier. We want to turn this plant around and we want to sustain it.”
Herndon is an electrical engineer by trade and self-proclaimed super nerdy dude, but he’s not afraid to get his hands dirty. He believes the best way to get buy-in is to show he’s willing to do the work. He admits, laughing, that sometimes the employees don’t want him in the thick of it, but he still shows up anyway: “The only way we get to where we want to be is by us all working together, not me and Jason sitting in the high tower yelling down direction about something. It is us on the ground floor, walking the plant, looking at things and making sure people are staying safe.” Another culture-focused change Ansley and Herndon have implemented is War Room meetings, where each area manager is responsible for reporting their data, written on a white board, and reported on to other managers during a fifteen-minute stand-up meeting. In these meetings, upcoming changes and ideas are discussed and managers are given equal say in what happens—with a twist. Herndon says one of the area managers, Sonny Patrick, was always coming up with different ideas, so one day Herndon gave him the go ahead. But he told Patrick he only had this amount of time to complete the action, a little good-natured competition between the areas, as another area was also trying out an idea that day. Herndon gives cushion for the ideas he thinks are better than others. Explaining, “So, when we are in the War Room, and they say this is how long this action is going to take, if they’ve had a great idea, I will give them a little more buffer. They love that because it makes it a little more lighthearted instead of ‘gotta go do this or gotta go do that.’ Any of these ideas, I look at it from an engineering perspective. I am all about trying different things as long as it is not going to violate OEM constraints that will lead to other issues.”
Ansley loves Herndon’s approach to management, and says they are on the same page at (nearly) most turns. Implementing two-hour reporting, KPIs, and daily War Room meetings are things both were accustomed to at other facilities and helps give better visibility in the process and by using them in Woodville help take this plant to the next level.
Ansley points out that the Estonian head office did a really good job of giving Woodville a good foundation and providing good business systems that are automated. As Graanul has a very lean corporate staff, and each plant staff is relatively small, the company has put considerable time and effort into putting systems together that help operators do their job. Graanul has service programs for PM routes that are integrated onto tablets; items that help automate the scale house, tons tracking, fiber procurement, where typically if you were to come into a situation like this—taking a plant out of bankruptcy—there would be lack of organization. Fortunately, Graanul has already set the foundation for a digital factory, and now it is on the staff at Woodville to use those systems and leverage them.
The building stands tall, ready to hit its nameplate capacity of 500,000 tons annually.
Process Flow
Woodville operates on a 50/50 mix of lower value stemwood to pre-processed material, 100% southern yellow pine, of which 40% is residual chips from local sawmills, 10% is dust. Once trucks are received through the scale house, they are either dumped by a Phelps dumper to the chip pad or unloaded to the stemwood yard using a Caterpillar 990 wheel loader or LogPro crane. Fuel from the dumper goes onto a reversing belt from the chip pad. Lower quality stemwood is debarked using a LogPro drum debarker and chipped by a CEM chipper.
The chip pad is outfitted with an FMW stacker-reclaimer with screw to rake the pile. Chips are conveyed to another belt, where the pulverized material goes to the Champion wet mill island, complete with Vecoplan pre-screeners that are currently being tweaked to reach operational level, then to the dryer island. Woodville’s dryer island is a dual line TSI system. This includes the heat energy system and dryers as well as the emission control system for the dryers, the wet ESP and RTO. The system was originally supplied over 10 years ago as the first of the new generation of TSI dryer islands that featured Sigma Thermal furnaces and TSI single pass recycle dryers along with newly introduced TSI wet ESP and RTO providing a reliable integrated system from a single source.
Currently, dry material does pass additional processing, with four Vecoplan pre-screeners to help reach targeted chip size of between 88-92% 2 mm chips for producing smaller industrial pellets.
After the Champion dry mills, two Tank Connection dust silos act as more of a buffer between process islands. Part of the ➤ 45
Spotlight On: Tires, Tracks, Etc.
Southern Loggin’ Times invited manufacturers of tires, tracks, chains and related components and services to submit editorial for this section.
BKT
BKT is a global player in the Off-Highway tire industry with an extensive product range catering to the most demanding user needs in any off-highway application. The FS 216 tire for the forestry industry has a robust lug design with optimum angle and a wider width to enhance traction and performance for loggers and skidders. It provides excellent cut and chip resistance under the most critical operating conditions and ensures maximum protection against possible damages at any time for a longer tire life. For more information visit www.bkt-tires.com.

Despino’s Tire
Despino’s Tire Service is a family-owned business that opened in 1996 with one truck and one store location. Today Despino’s Tire has 20+ service trucks and serves Arkansas, Alabama, Georgia, Louisiana, Mississippi, and Texas.
We produce customized wheel solutions that complement nearly any type of forestry equipment – including skidders, feller-bunchers, harvesters, forwarders, and log loaders. We’re also the only global manufacturer of both wheels and tires, which means we can offer a complete wheel assembly for your equipment designs.
Exceptional service and customized products have made Despino Tire the leader of off-the-road tires and wheels. Our technicians are available 24/7 to save you time and make your business run more efficiently. All tire techs are OSHA & MSHA certified and receive initiate and ongoing safety
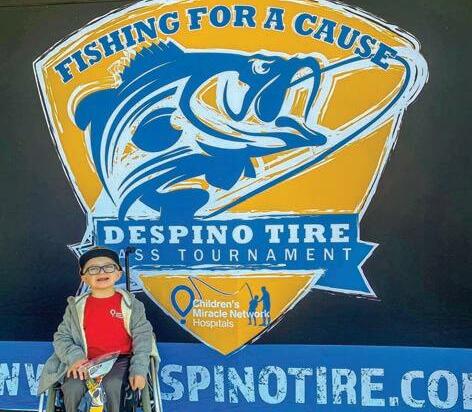
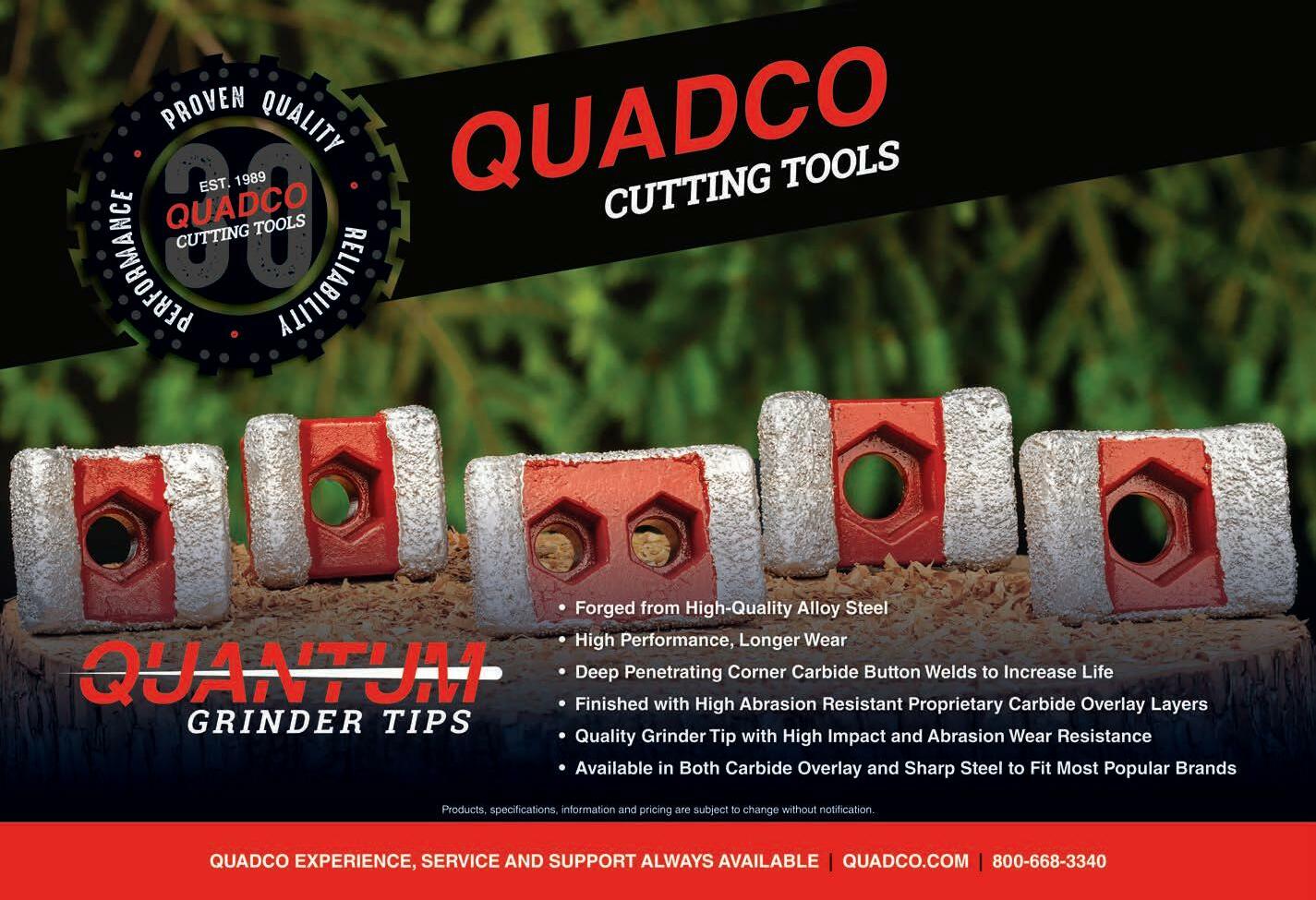

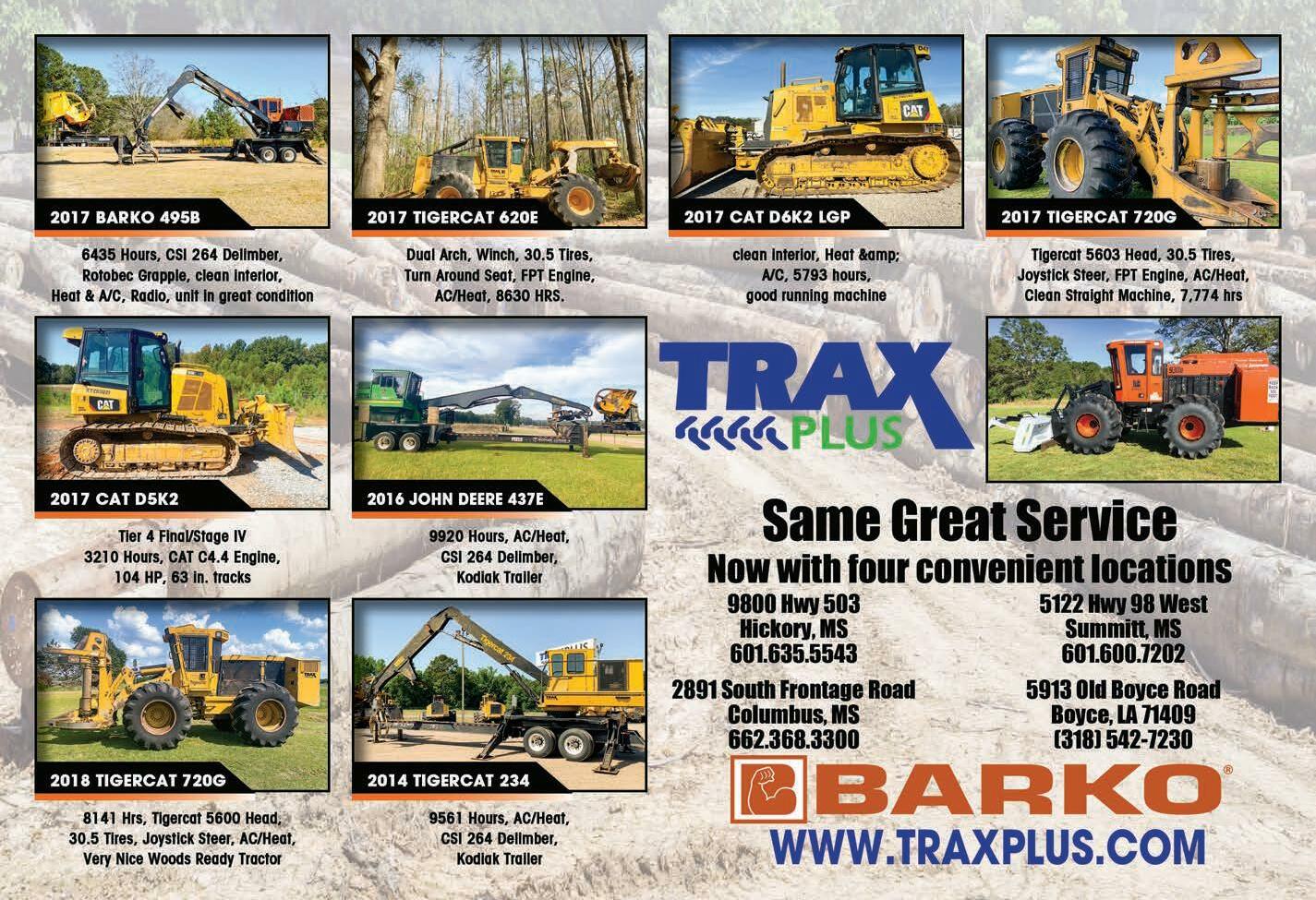
training from our dedicated Safety Manager. Whether it’s on new equipment or installation deep in the woods, our technicians arrive with the replacement tires you need when you need them. Despino’s Tire is a certified contractor through ISNetworld and Avetta platforms.
Despino’s Tire has raised over $250,000 through our Annual Children’s Miracle Network Bass Tournament on Toledo Bend Lake. The 2023 bass tournament will be Sunday, March 12, 2023, Learn more about Despino’s Tire and our annual bass tournament at www.despinotire.com!
Forest Chain Multi-Ring
Forest Chain wide range of ring skidder chains are available in fixed ring, multi ring, and studded with 9/16", 5/8" or 3/4" tag chains to fit all popular tire sizes. Designed to give as much as 60% more traction to your skidder, Forest Chain skidder chains provide quicker skid times, more production and increased bottom line profits. Forest Chain premium multi-ring heavy duty chains offer superior traction and are available in 9/16, 5/8, 3/4, 7/8 and 1 inch. The DoubleDiamond configured chains equipped with U-shaped studs are especially effective in the worst conditions: the deep biting lugs dig deeply into the terrain. Repairs are easy using common welding techniques and materials for longer life. Email forestchain@gmail.com or call 800-288-0887.
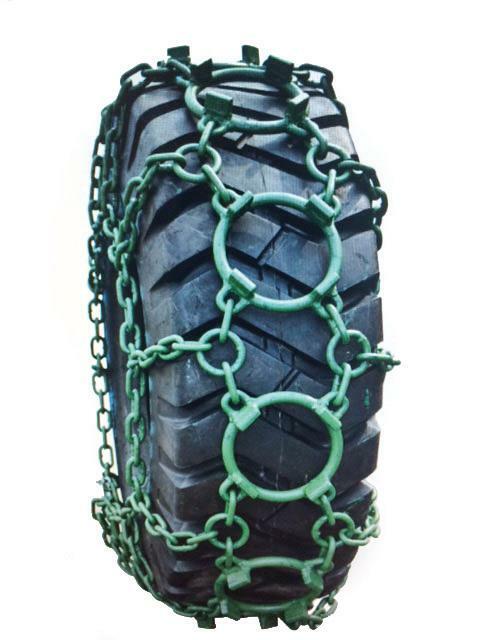
Olofsfors
Olofsfors is a Swedish based company founded in 1762 with North American operations in Brantford, Ontario, Canada. Olofsfors Inc. specializes in attachments and accessories for cut-to-length machinery. The product lines are ECO-Tracks, Iggesund Forest, Hultdins and Indexator.
Olofsfors is the market leader in bogie tracks for CTL machinery and wheel tracks for skidders and wheeled feller bunchers. Under the brand name ECO-Tracks, Olofsfors offers a wide range of track models and linkage systems for various machine configurations and ground conditions. Most track models are now available in the next generation of curved cross members for increased flotation, less ground disturbance and easier machine turning. The track assortment ranges from traction only, flotation only and all around.
A new addition to the expanding link system offerings is the 29 mm (11/8"). The new 29 mm link system features an increased 29 mm link along with a wider and thicker link hook. It has 37% more material compared to 26 mm (1") resulting in increased lifetime of the tracks. The 29 mm link system has been designed for large forwarders and 6-wheel skidders and is a good option for abrasive soil conditions.
Along with the new link system, Olofsfors has two new cross member profiles. ECO HD and KovaX+ are increased in size over ECO-Track and KovaX respectively. With more material and taller grouzer bars, both are stronger options with more traction. They have been designed for the heaviest machines, most demanding ground conditions and suitable with the largest link systems for optimal life.
On the maintenance side, Olofsfors has developed a new tightening tool called the Centre Mount Tool. It is 4x faster than the standard ratchet tool and
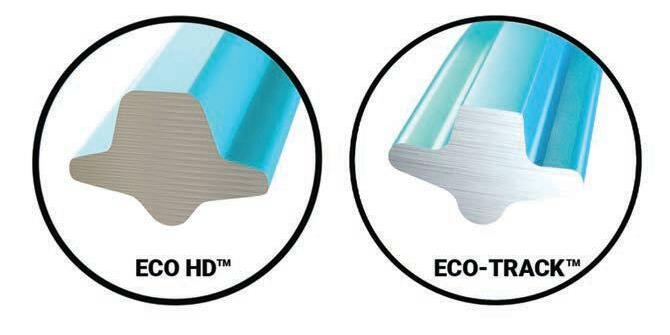
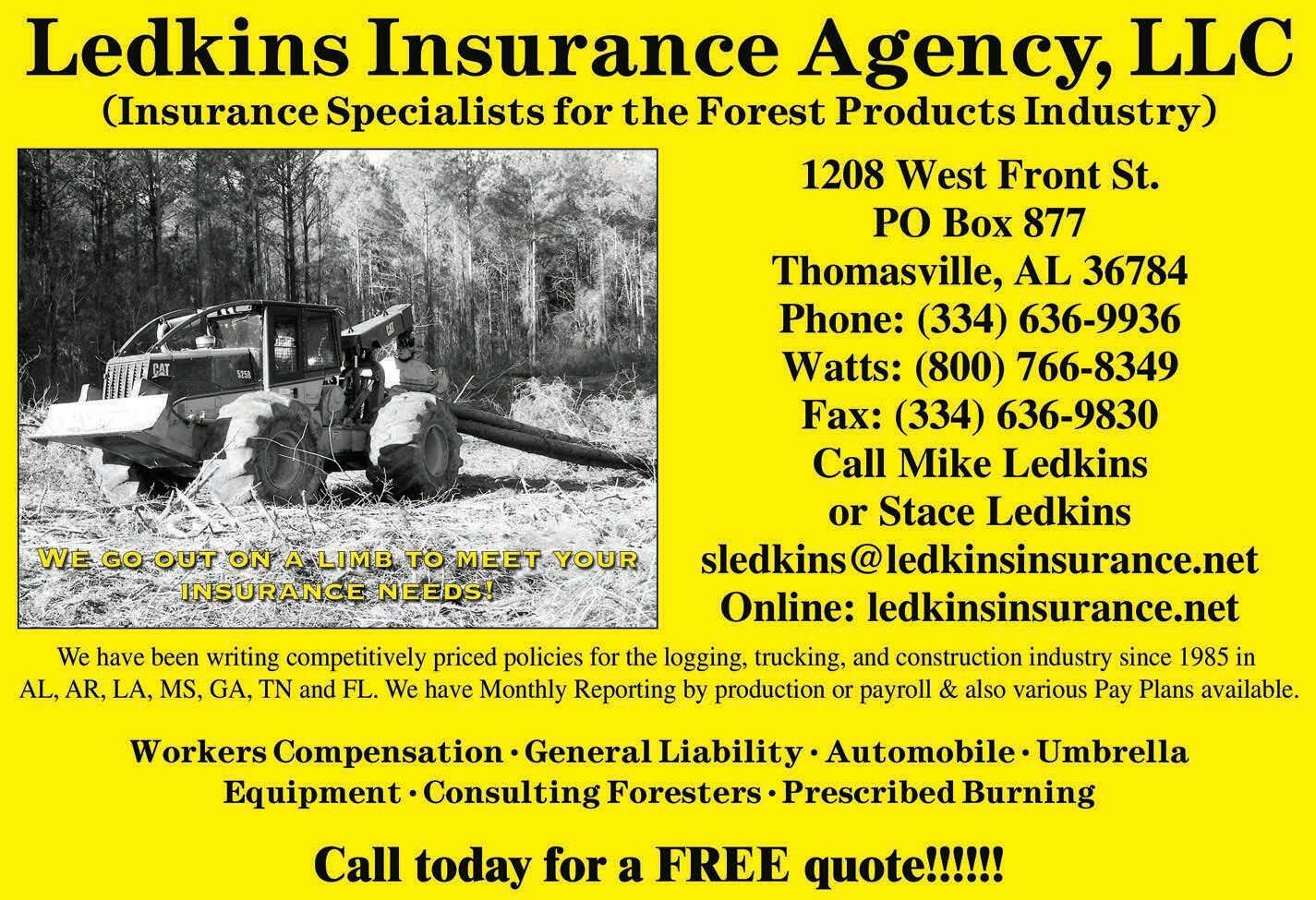
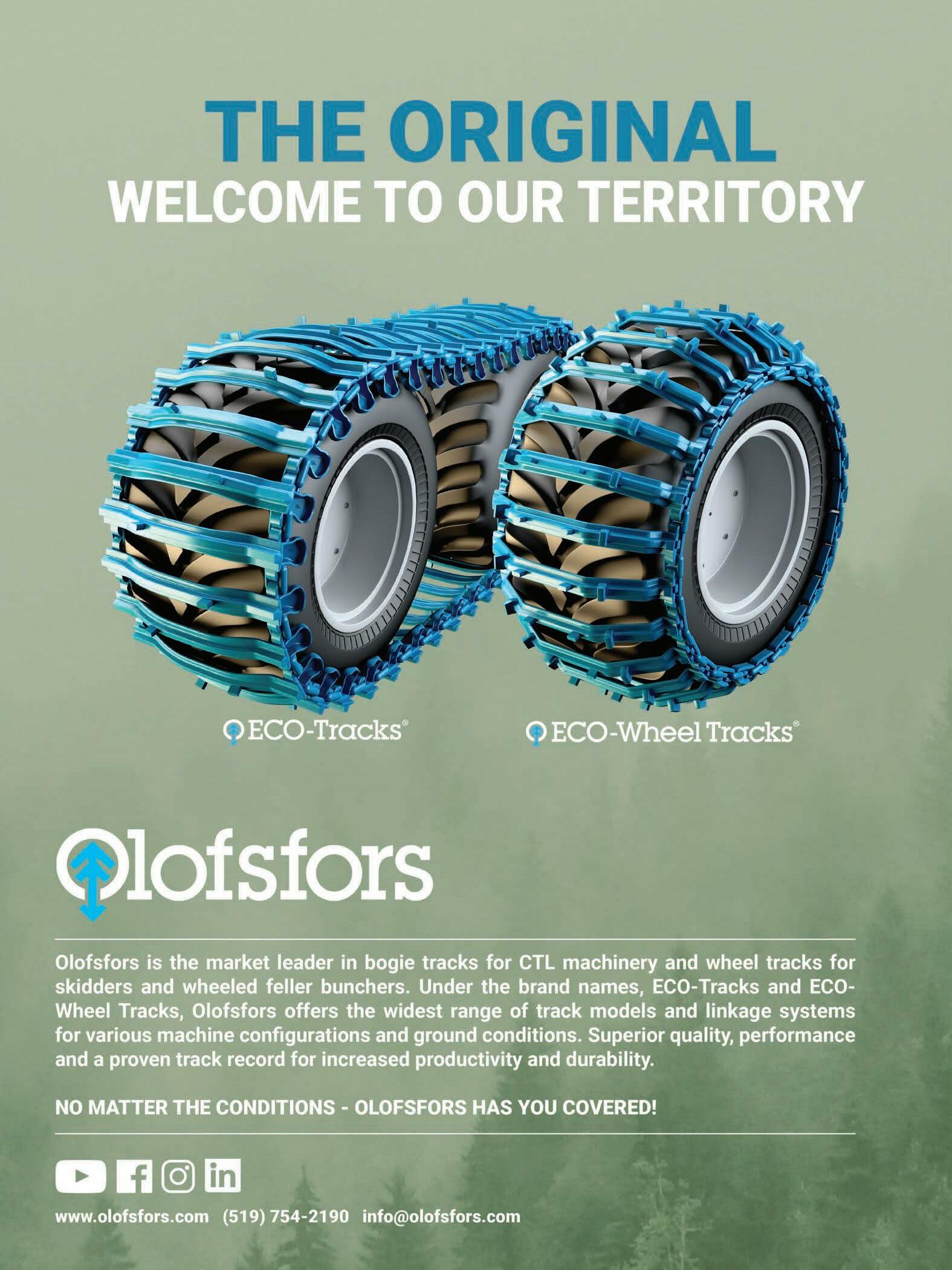
Wallingford’s
Wallingford’s Inc. is now a member of pewag group, and is the North American distributor of pewag forestry traction products. The pewag single wheel tracks are an alternative to traditional tire chains that have been gaining popularity in the southern regions. Pewag builds tracks of exceptional quality, and they are known for the best wear resistance thanks to a special hardening process for the connecting elements. Four horizontal welded on starwave studs provide excellent traction and stability. The innovative starwave profile also provides prolonged lifespan of the studs. Wheel tracks provides excellent tire protection and the broad contact surface helps with floatation on softer terrain. Wallingford’s Inc. offers BABAC forestry and heavy equipment tire chains that are American made and hand assembled for optimum quality control at our factory in Winslow, Maine. BABAC offers a full line of standard tire chain patterns for skidder, forwarder, tractor and heavy equipment applications. BABAC has computer design capability and we specialize in custom tire chain applications and odd tire sizes. BABAC's Ring chains provide excellent traction for operating in mud or other adverse conditions, and have been popular with our Southern logging customers for many years. All models feature alloy lugs that, unlike most other chains, are butt and wrap welded for unsurpassed strength and durability. Tag and cross chains are made from through hardened 10B21 Boron Alloy steel, side chains of 1022 hardened steel. Our slanted half links take out pre-load as the chain goes over the tire. This reduces friction and wear and allows for free tag chain movement. It is a standard feature on all of our ring chains. BABAC also offers a variety of tools and spare parts to properly maintain and repair, when necessary, your chains for long life and maximum performance. Our G200 and G202 chain tensioners facilitate installation and maintenance requirements, resulting in longer chain life from properly tightened chains. BABAC Black Pin Load Rated Shackles are ideal for skidder tire chain applications.
We are currently offering special pricing; give us a call at 207-465-9575 to get more information, or visit www.wallingfords.com
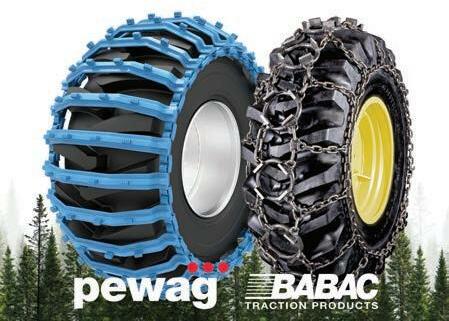
McCarthy Tire Services
McCarthy Tire Services offers complete forestry tire sales and service to loggers in eight East Coast states including: installation and service, warranty processing, trade-in program, repairs, safety training and more. Every piece of forestry equipment requires a special tire suited to its job and environment. We stock a robust inventory of tires and wheels by PrimeX, Firestone and Maxam. No job is too big or small. we have one of the largest boom truck fleets in the industry and they are up to any job; equipped with the latest tire handling technology, run by TIA certified technicians and often offer same day turnaround. Contact Austin Hale (443-602-6636), Forestry Sales Director, today for a complimentary consultation on how our team can best serve you and keep your business rolling. www.mccarthytire.com #KeepAmericaRolling
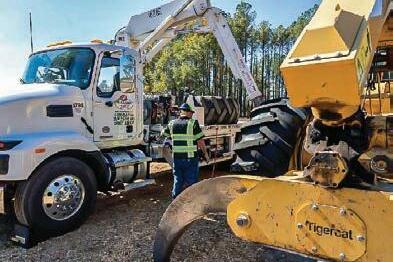

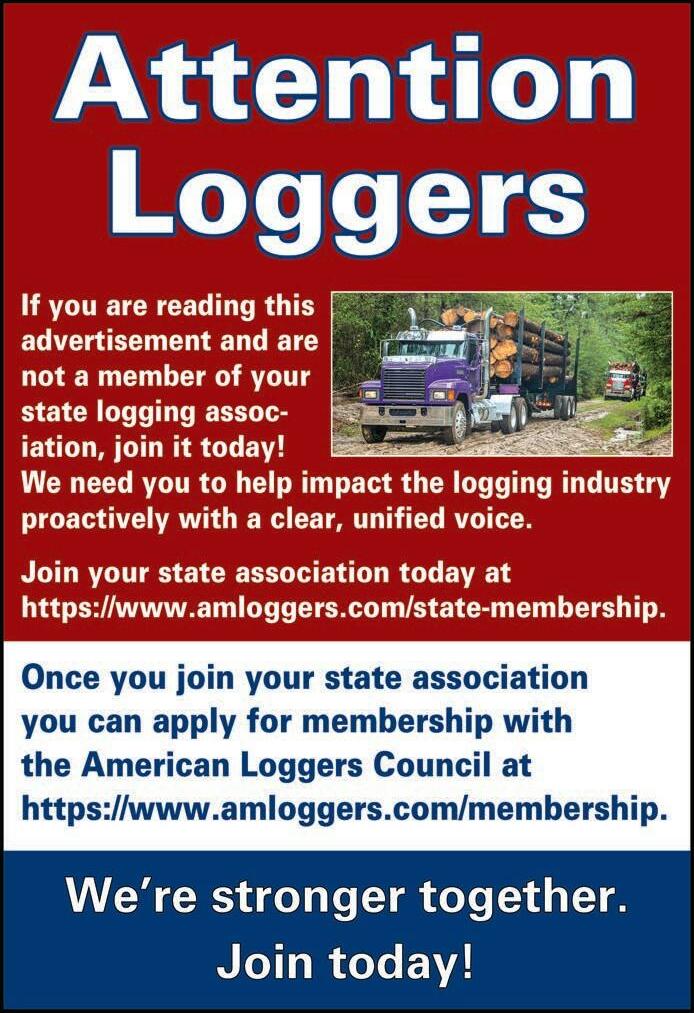


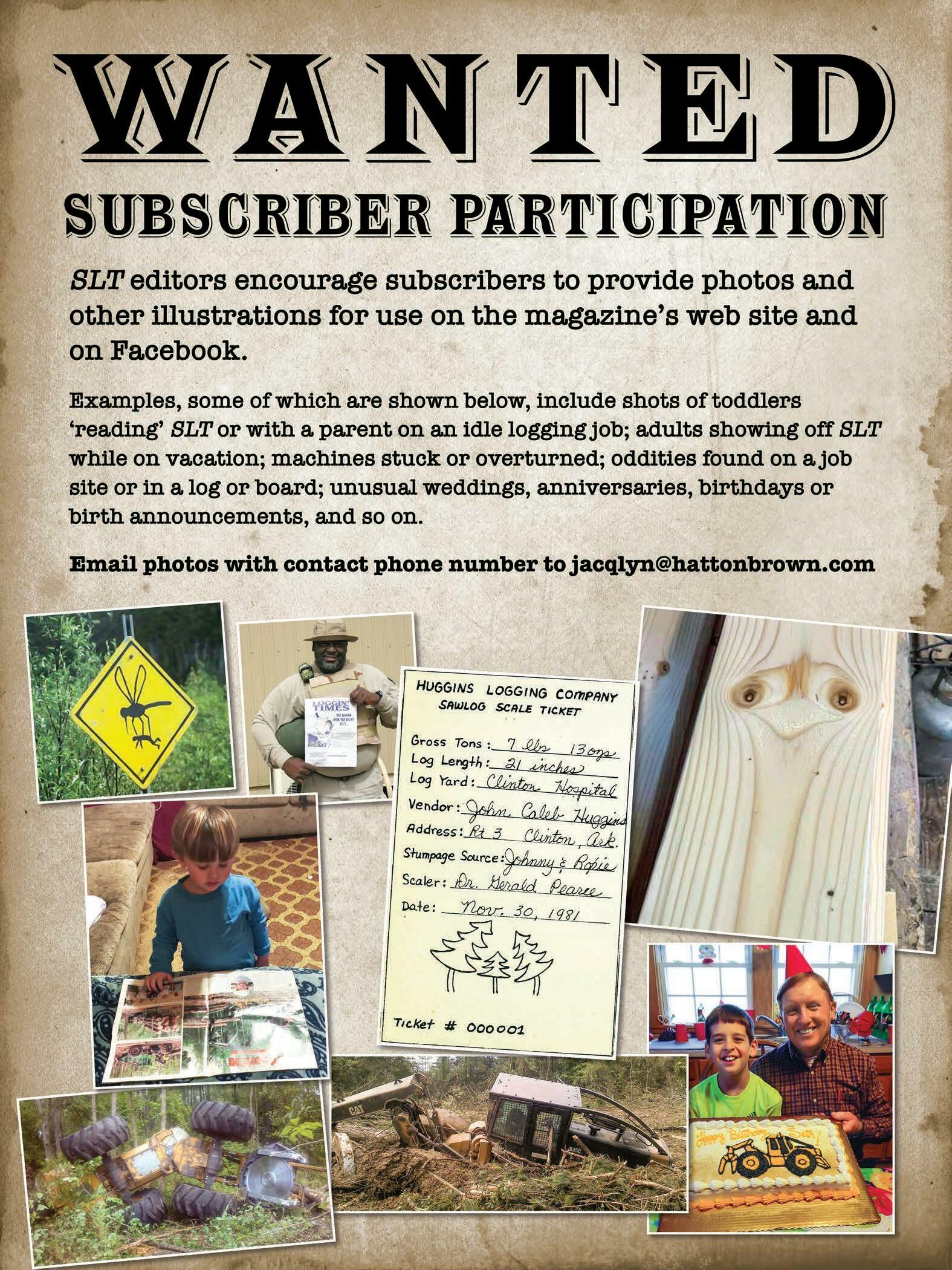
