
31 minute read
Bulletin Board
Woodworking Network Has Interesting Report
Located in Fredericton, New Bruns wick, Canada, Fiddlehead Casket Co. has added a modern-day twist to the old pine box. The small outfit’s caskets are manufactured and shipped ready-to-assemble for the dearly departed.
Fiddlehead’s owner, Jeremy Burrill, says anyone who can assemble IKEA furniture can easily put together one of his caskets in about 30 minutes. The only tool skill required is the ability to pound wood dowels into the pre-drill ed holes of the pine components. Instead of an Allen wrench, a rubber mallet is included with each RTA casket kit, along with 10 pine panels, 38 cherry pins and step-by-step instructions. No glue or metal fittings are required to construct unembellished units, which also make them fully biodegradable.
The company’s website notes that the RTA caskets are “ideal for both im me diate use or future planning.” It adds that the caskets are “the only handcrafted, environmentally friendly option for your loved one. Locally made with New Brunswick pine.”
As of mid 2020, the caskets cost about $700, but by now have likely gone up. Fiddlehead more recently added an RTA bookcase that can be converted into a casket. “Love the idea of a simple pine casket but won’t need it for a while? Put it to work right now! This bookshelf option adds five adjustable solid pine shelves.”
For more info, email burrill@fiddleheadcaskets.com or phone 506-262-2211.
Fiddlehead Casket Co. owner Jeremy Burrill assembles one of his caskets.
Monday Motivational Quotes From YourPositiveOasis.Com
1. Learn how to be happy with what you have while you pursue all that you want.—Jim Rohn 2. Why fit in when you were born to stand out?—Dr. Seuss 3. If I have seen further than others, it is by standing upon the shoulders of giants.—Isaac Newton 4. Go for it now. The future is promised to no one.—Wayne Dyer 5. There are two ways to live: you can live as if nothing is a miracle; you can live as if everything is a miracle.—Albert Einstein 6. Negative people need drama like oxygen. Stay positive; it’ll take their breath away.—Tony Gaskins 7. There is a direct correlation between positive energy and positive results.—Joe Rogan 8. People are capable, at any time in their lives, of doing what they dream of.—Paulo Coelho 9. I do not fix problems. I fix my thinking. Then problems fix themselves.—Louise Hay 10. You have within you right now everything you need to deal with whatever the world can throw at you.—Brian Tracy 11. If I cannot do great things, I can do small things in a great way.—Martin Luther King, Jr. 12. Always do your best. What you plant now, you will harvest later.—Og Mandino 13. Yesterday I was clever so I wanted to change the world. Today I am wise so I am changing myself.—Rumi 14. There will always be someone who can’t see your worth. Don’t let it be you.—Mel Robbins 15. Decide what you want. Believe you can have it. Believe that you deserve it, and believe it’s possible for you.—Jack Canfield 16. Today’s a great day to behave as the person you’ve always wanted to be.—Robin Sharma 17. Things turn out best for the people who make the best of the way things turn out.—John Wooden 18. The most important conversation is the one you have with yourself.— David Goggins 19. True happiness occurs only when you find the problems you enjoy having and enjoy solving.—Mark Manson 20. People rarely succeed unless they have fun in what they are doing.— Dale Carnegie 21. You will never change anything that you are willing to tolerate.—Myles Munroe 22. You never know how or when you’ll have an impact, or how important your example can be to someone else.—Denzel Washington 23. Let your hopes, not your hurts, shape your future.—Robert H. Schuller 24. Strong minds discuss ideas, average minds discuss events, weak minds discuss people.—Socrates 25. We cannot become what we need by remaining what we are.—John Maxwell 26. Each day is an adventure in discovering the meaning of life.—Jack Canfield 27. Expect the best, plan for the worst, and prepare to be surprised.—Denis Waitley
28. The secret of getting ahead is getting started.—Mark Twain 29. Success is liking yourself, liking what you do, and liking how you do it.—Maya Angelou 30. Every action you take is a vote for the type of person you wish to become.—James Clear 31. You don’t get in life what you want; you get in life what you are.—Les Brown 32. Life’s biggest tragedy is that we get old too soon and wise too late.—Benjamin Franklin 33. We can only love others as much as we love ourselves.— Brené Brown 34. Success does not consist in never making mistakes but in never making the same one a second time.—George Bernard Shaw 35. Every day, some ordinary person does something extraordinary. Today, it’s your turn.—Lou Holtz
Innovative Farmer
Farmer Jack once lived on a quiet rural highway, but as time went by, the traffic built up and eventually got so heavy and so fast that his free-range chickens were being run over at a rate of three to six a week.
So he called the local police station, complaining, “You’ve got to do something about all these people driving so fast and killing my chickens,” he said to the desk sergeant.
“What do you want me to do?” asked the policeman.
“I don’t care; just do something about those crazy drivers!” the farmer declared.
So the next day the policeman had the traffic department erect a sign that said: SCHOOL CROSSING.
Three days later farmer Jack called the policeman and said, “You’ve still got to do more about these drivers. The ‘school crossing’ sign seems to make them go even faster!”
So up went a new sign that said: SLOW: CHILDREN AT PLAY. But it did little good, leading the farmer to ask if he could put of a sign of his own, which he did. When a week went by with no call from the farmer, the desk sergeant became curious and called the farmer. “How is the problem with the speeding drivers?” he asked. “Did you put up your sign?” “I sure did and not one chicken has been killed,” the farmer replied. The policeman became so curious that he went out to see the sign for himself. His jaw dropped the moment he saw the sign, which boldly proclaimed:
NUDIST COLONY. SLOW DOWN AND WATCH FOR CHICKS!
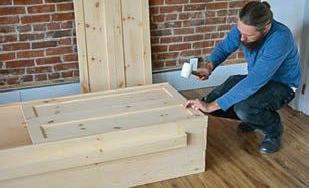
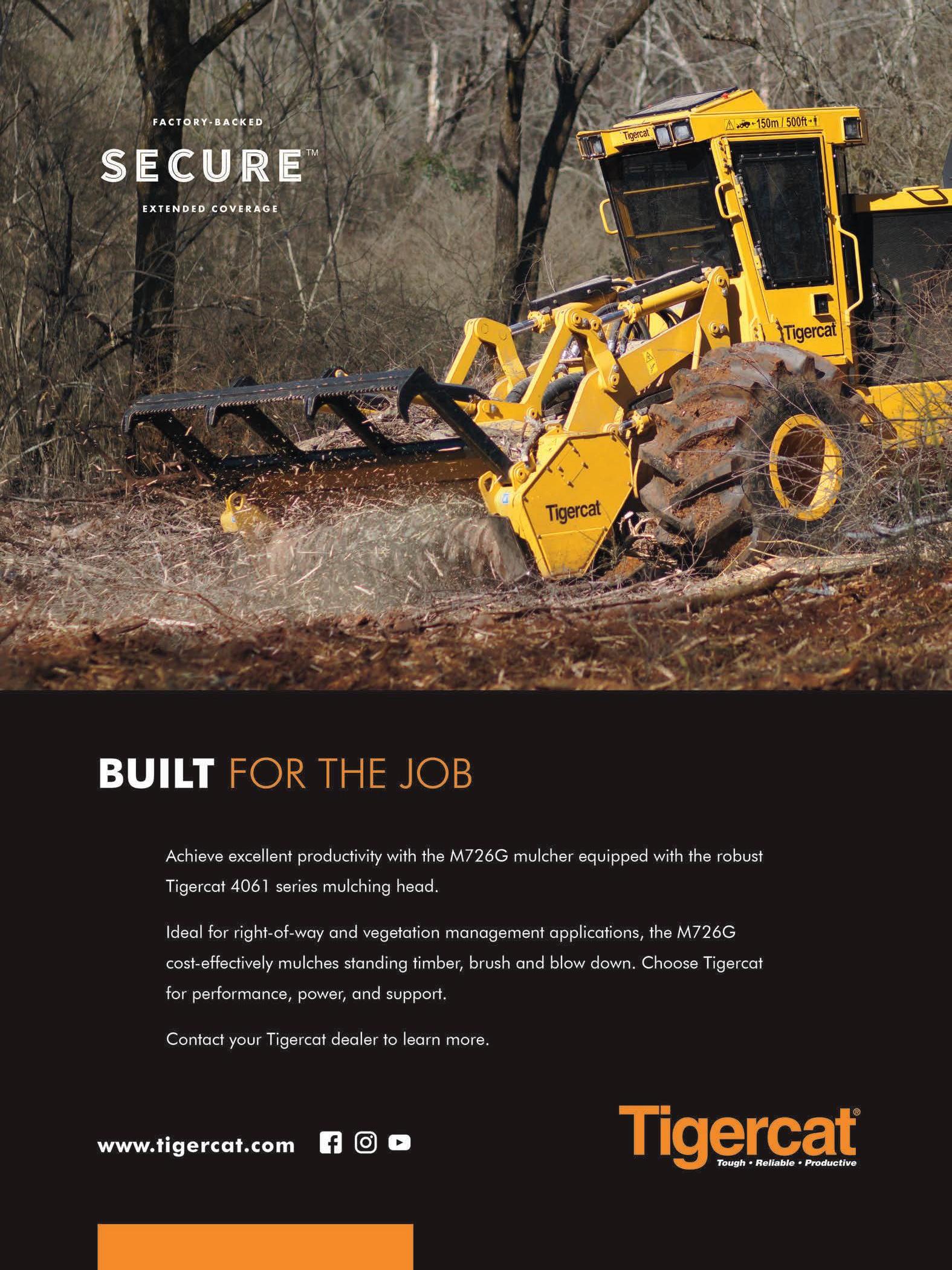
Family Values
■ Michael Hutchins was FRA’s Southcentral Region Logger of 2020.
By David Abbott
LIVINGSTON, Ala.
Felling pine 30 miles west of Eutaw, and about five miles east of the Mississippi state line, logger Michael Hutchins counted himself lucky to be working the day Southern Loggin’ Times caught up with him in early July. “We were fortunate,” says Hutchins, 53. Unlike a lot of other loggers in the Southeast that week, the owner of Hutch Trucking, Inc. was able to work in between thunderstorms that brought heavy rainfall while Hurricane Elsa made her way up from Florida through the MidAtlantic region. “The last few days both our crews have been able to work when everybody around us was rained out.” A lot of times it’s been the other way around for him.
It’s easy to see why Hutch Trucking was selected as both the Forest Resources Assn.’s Southcentral Re gion Logger of the Year and as Ala bama’s Outstanding Logger of the Year for 2020. For one thing, Hutch ins takes special care to look out for SMZs and to protect against erosion. “I look at it in the long run: if we de stroy the earth, what are my boys go ing to cut 40 years down the road?”
Hutchins has been helping manage this 500-acre privately owned tract for 24 years. The owners, he says, never want to cut any of the hardwood here, just the pine, which they replant. This summer, Hutchins was removing some of the older standing pine. “It’s like this old pine is sitting in a nursing home, just waiting to die. First good wind that comes along will blow it down.” Hutchins has salvaged storm-damaged wood off this property many times.
Taking care of the land is good business in more ways than one. Landowners for whom he’s been cutting for years keep asking him to come back.“We had so many land owners calling who didn’t want to advertise it, they wanted me to cut it,” he says. He’s established relationships and a good reputation, with much of three decades of logging behind him, and it pays off. “I am probably 10 tracts behind right now.”
To keep pace with all the demand, he started a second crew last fall, though he had to shutter it for a while due to wet weather and quotas. They just fired it back up this summer. He also wanted to set the second crew back up to help his sons, he says, “So that when I get ready to re tire, I can just walk out the door. Maybe in eight or 10 years when they have a good foundation under their feet and can run it, I’ll be out of it.”
Markets
Michael Hutchins
The newer crew stays busy taking on jobs from landowners who know him from past experience, while the old crew has been working on Westervelt land for 18 years.
In his experience, logging was largely unaffected by the pan demic. “It didn’t slow down, and then lumber markets got great, better than they’ve ever been,” he notes. Still, even with the lumber boom this year, loggers and landowners haven’t benefited. “I was real concerned stump age might go up, but it didn’t,” he reports. “It irritates me that logging rates haven’t gone up. It would have helped, and with fuel and everything else going up, I would have they thought they would see it. There’s nothing you can do but keep rolling with the punches, though.” Speaking of rolling, Hutch Trucking keeps three trucks rolling on the main crew and two on the newer crew. The main crew hauls 50-60 loads a week, and the new crew 20-30.
It’s about 70 miles from the tract the new crew was on in July to all of the mills to which Hutchins hauls: Lassiter Lumber in Silas, Ala., Westervelt Lumber in Thomasville and Moundville, and Rooster Bridge in Cordoba. The main crew stays on Westervelt jobs all the time, and they generally have to make only about a
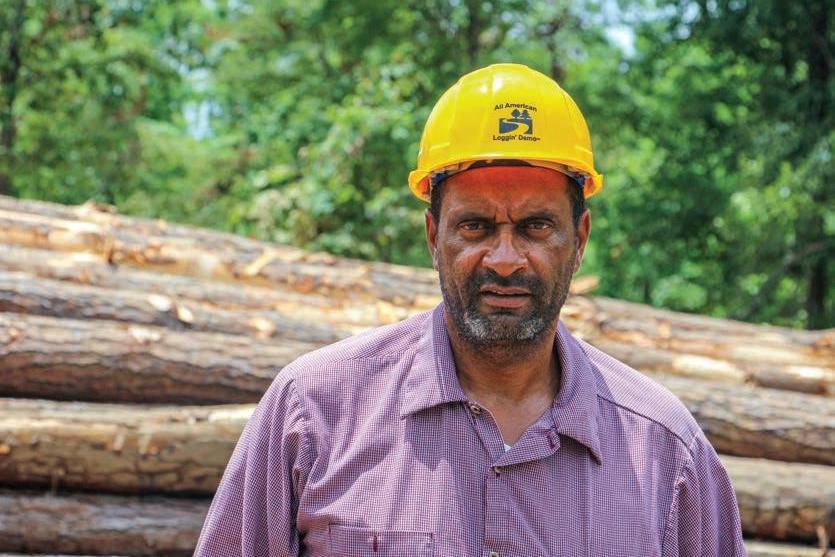


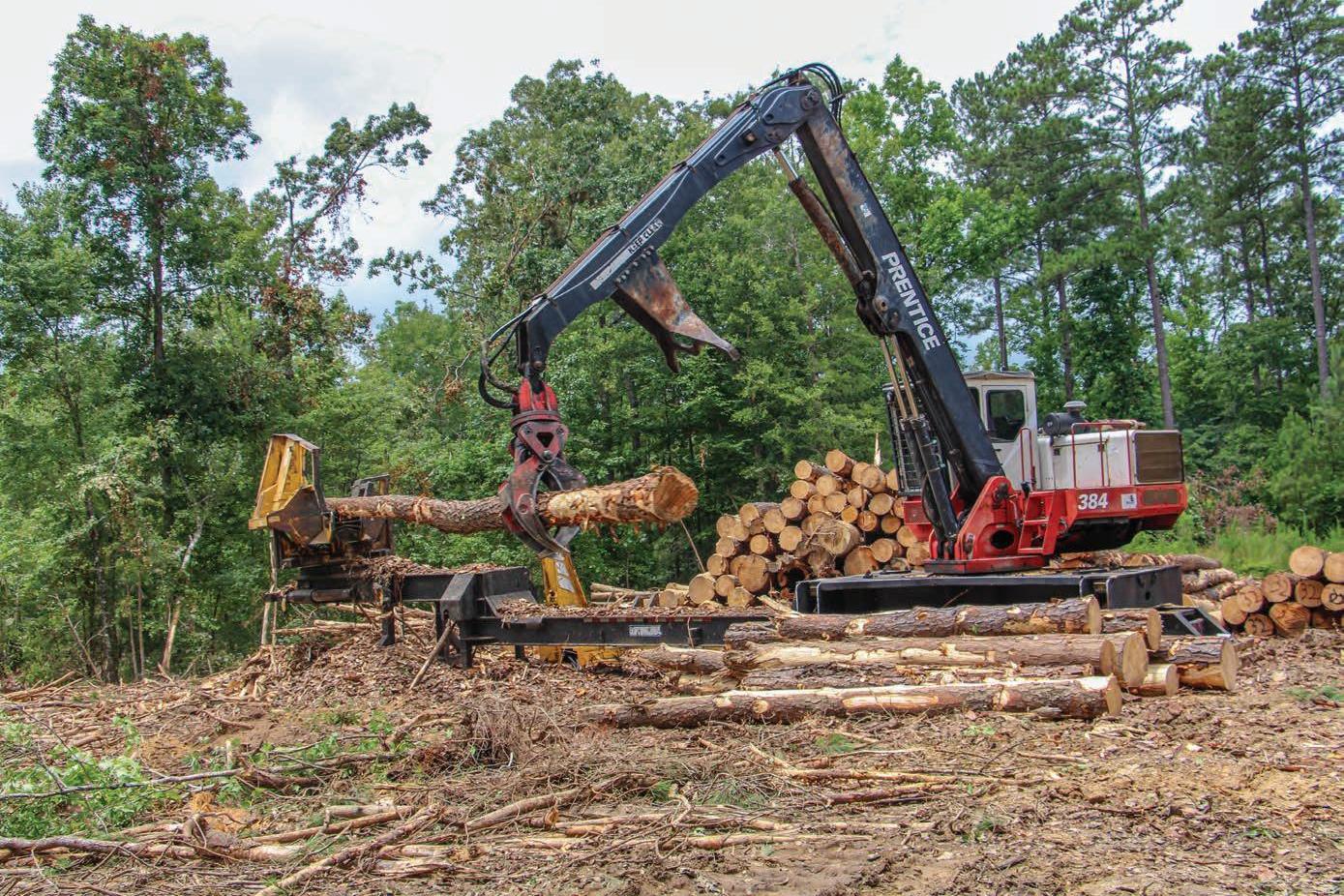
35-mile trip to the mill.
The logging business can’t help but have its ups and downs, Hutch ins admits. “Mills still put you on quota; it has always been that way and that is never going to change. If they don’t need the wood, they don’t need it; if you can’t move it finished then there’s no need to put it in unfinished.”
Labor
Finding good help—or any help at all, it sometimes seems—has never been harder, the veteran logger la ments. Asked where he finds operators, Hutchins shakes his head. “You don’t find them; they’re not out there. You may have somebody out of the blue call you wanting to work, but 90% of the time he just wants a hustle.”
It used to be that when he stopped at a fueling station in the mornings, younger guys would flag him down to ask for a job. Nobody does that anymore, he’s sad to report.
He’s not sure why it’s this way, but he has a few theories. “I think the younger generation just hasn’t been raised up around logging and they just don’t know anything about it,” he reasons. “They get out of school and go another way, or to an easier job. And the older employees have retired. Nobody wants to get up and come to work anymore out here in the woods.”
He can’t understand it, either; seems to him they’re missing out. “You make a good living out here; that’s the reason the older employees stayed out here as long as they did. They took care of their families out here. It’s a little difficult sometimes when you get a rainy week, but you can work pretty much as much overtime as you want and make a good paycheck. So I don’t understand.”
With that in mind, he feels lucky to have the crew he has. On the main crew, loader man Darren Danner serves as foreman, working with cutter and skidder operators James Giles and Whitney Brown, Jr. On the new crew, Hutchins runs the cutter and loader, and he has a part-time skidder driver to help out. Oldest son Michael Hutchins, Jr., also drives a skidder and a truck, along with three other drivers.
The crew wears hard hats and green safety vests. If anything needs to be cut with a chain saw, Hutchins handles it himself. “You wont find anybody to do that anymore,” he says, pointing out that few people today have the experience to run a chain saw skillfully and safely.
Machinery
Other than a 700J Deere dozer, the main crew runs exclusively Tigercat machines: a 250 loader, 630H and 630E skidders, and 726G fellerbuncher. Equipment on the new crew is a Prentice 384 loader, Tigercat 632 skidder, Tigercat 726 feller-buncher, and John Deere 850J dozer.
Hutchins buys from B&G Equipment in Moundville, Ala., and he only buys new machines.“I don’t buy used; I don’t want anybody else’s worn out equipment,” he explains.
Once he has it, though, he gets his money’s worth. The Prentice loader on the new crew has over 40,000 hours on it and still works every day. He bought it new in 2005—bought two of them that year in fact. “I bought one and the next day I called the salesman and told him to bring another one just like it,” Hutchins recalls. “It was so phenomenal, I had never run a loader as good as that one and I wanted another one just like it.” He ran both of them till 2016 when he sold one, and even then there was nothing wrong with it, he says. “My loader man just wanted to try something different, so we got a Tigercat.” He sold the Prentice to a logger from Kentucky, who called back wanting to buy the other one, too.
What’s the secret to keeping a 16year-old machine running smoothly for more than 40,000 hours? Simple maintenance, Hutchins says—routine service at regular intervals and greasing twice a week. He has operators grease machines on Tuesdays and Thursdays. “I figured it out a long time ago,” he says. “On Monday he’s still on the weekend time, and on Friday he’s ready to go start his weekend.”
Hutchins prefers Tigercat machines, buying from B&G Equipment in Moundville.
Roots
After working other jobs here and there, Hutchins and a partner, Wayne Springfield, started their own company, S&H Logging, in 1993. They worked together for four good years before deciding to go their separate ways in 1997. Springfield kept S&H Logging while Hutchins branched off to start Hutch Trucking. He had in mind at the time to start a trucking business; it only took one load to convince him that hauling for others wasn’t the right direction for him. He started logging operations again the very next day.
Why did he choose logging? “I grew up around a sawmill and that was pretty much the only job after farming and cotton picking and plowing a mule, and that was disap-
The Prentice is a 2005 model with 40,000 hours on it and still going strong.
pearing. I would go around that sawmill and tinker with a font-end loader or measure a log for the boss. I got used to running knuckleboom loaders and running power saws. I learned how to merchandize pine and hardwood there.”
As he got older, he grew to hate school with a passion. The way he saw it, “It was holding me back because I had another goal I was working towards.” He left school after 9th grade to work at the mill, and says he never missed school at all. “Everybody told me, you need to go back to school,” he recalls. “I had a girlfriend who told me I needed to go get my GED; I said, what does it pay?” Instead he did it his own way, and that’s worked for him. “If I had to do it all over again, I wouldn’t change a thing.”
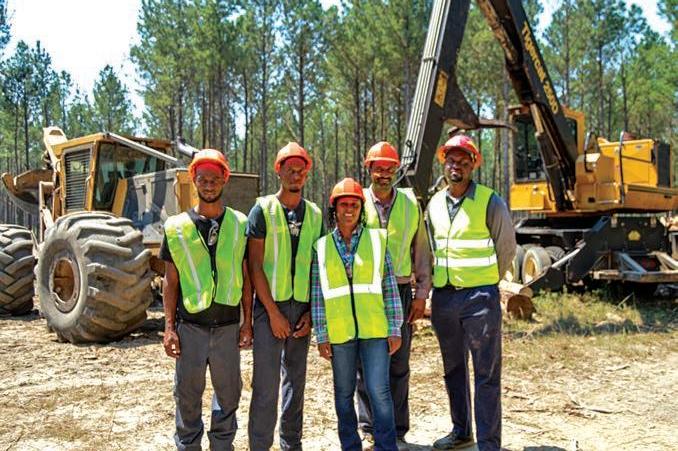
The Hutchins family, from left: Chanse, Kannon, Tonya, Michael Sr., and Michael Jr.; photo courtesy of Alabama Forestry Assn.
Family Matters
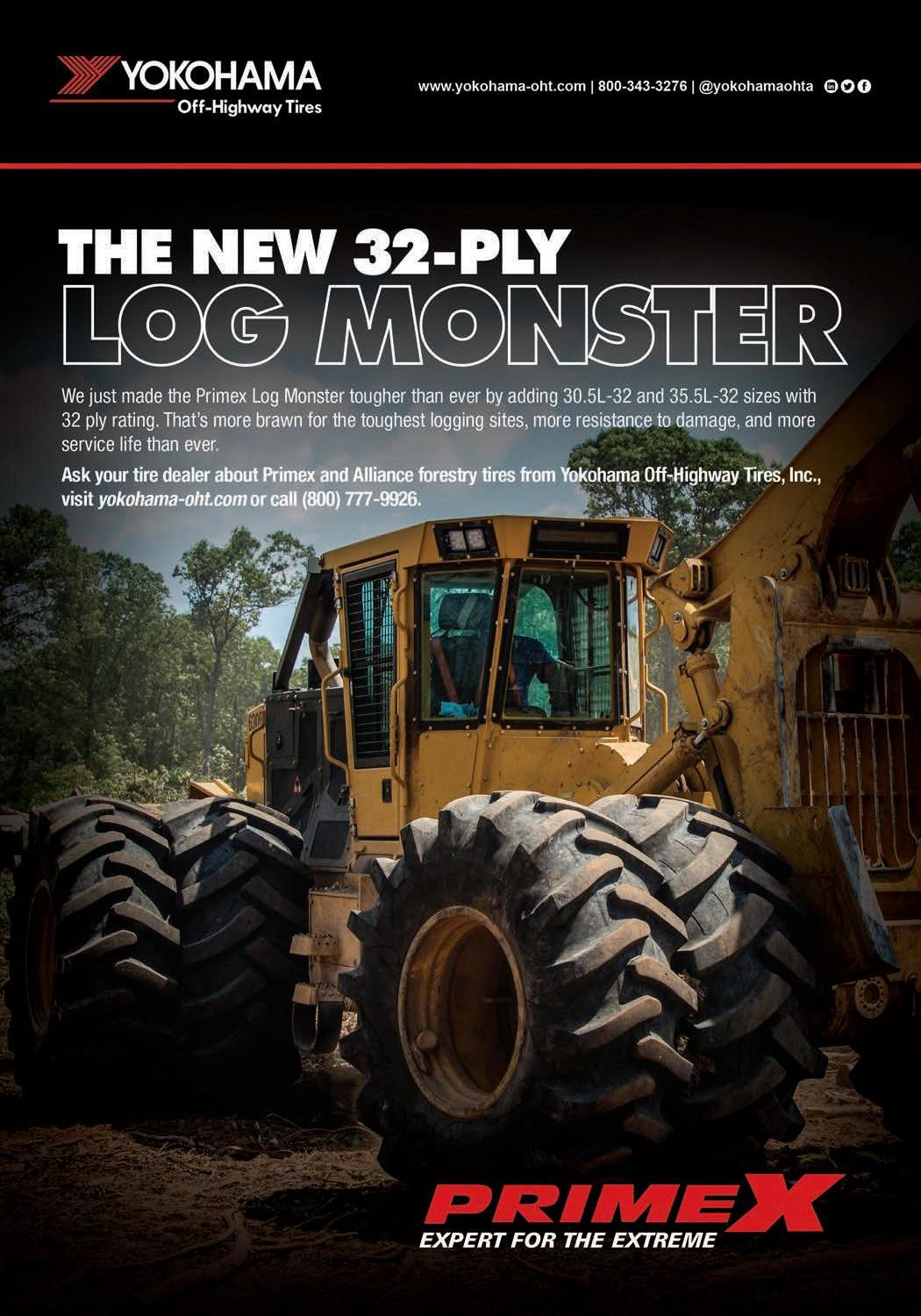
Hutchins and his wife Tonya have three sons and a daughter; they had a fifth child, a daughter they lost. All three sons are active in the logging business. Michael Hutchins, Jr. has been a skidder and truck driver for a while, while middle son Kannon just came on board and youngest
Chanse is now old enough to help work on things or run for parts.
Along with logging, the Hutchins family farms and cuts hay on the side. “We were doing it because the boys were underage and couldn’t come to the woods, and that kept them busy and out of trouble,” he says. “All the boys are old enough now to come to the woods, so I’m telling all my customers we are not selling hay out of the field next year. We will have our barns full, so there will be some hay for sale. But we are not going to be running day and night.”
Cattle, horses and hay fields cost a lot, but he’s not really do ing it primarily as a business venture.
“There’s not much money in cows but it is a lot of enjoyment,”
Hutchins says. “People need to be raised on a farm to learn common knowledge. A cow will pretty much teach you what you need to know; a horse will too. If you don’t have common sense, they’ll teach you some.”
Hutchins suspects an addiction to technology is part of the problem with today’s young work force: people are too much into their phones. Practicing what he preaches, Hutch ins uses a flip phone only for making calls, not scrolling social media.
He didn’t allow his sons to have video games or toy guns when they were growing up. “I didn’t want them to learn to shoot anybody and
I didn’t want them to get caught up in technology when they were kids till I can’t teach them anything.”
Looking to the future, Hutchins plans more of the same: keep plugging along and training his boys how to work safely and make a living from the land. He expects to put another decade or so into Hutch
Trucking and then sell it to his sons.
Hutchins and Tonya are the proud grandparents of two boys, ages six months and six years, and a three-month-old girl. “They might come out here one day, too,” he hopes. SLT
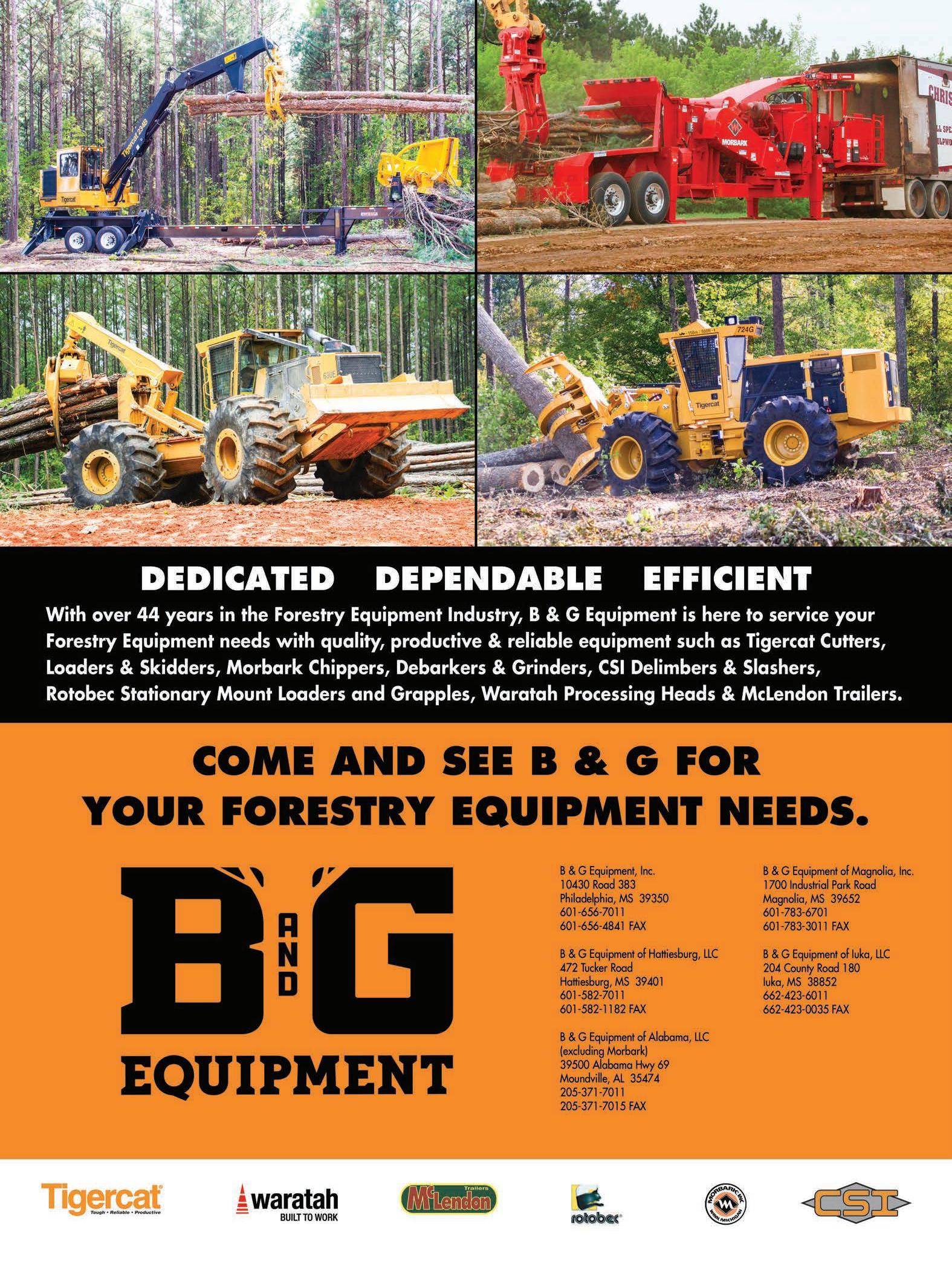
Family Heirlooms
■ Brothers Mack and Rickey follow their calling in the timber-rich Peach state.
By Patrick Dunning
WAYCROSS, Ga.
Third generation logging company Pitts Logging, Inc. has deep roots in southeast Georgia. Brothers Mack, 43, and Rickey Pitts, 46, manage four pine crews and 16 trucks each day. They always keep in mind their family’s motto: give credit where credit is due.
Their grandfather incorporated the business in 1956, topping pine trees with a chain saw and dragging logs with mules and oxen. “That’s the old-fashioned way,” Mack says. “Granddaddy worked on the railroads until our dad was born in ’55. He didn’t like staying gone all the time so he bought a shortwood truck and started hauling logs to be closer to home.”
The boys’ uncle, Ben Jolley, had worked at a container pulp mill in Fernandina, Fla., but came home to work with his dad, their grandfather, Mack recalls. When their father, Richard Pitts, Sr., graduated high school, he and his brother, their uncle Jolley, stepped up and ran the day-to-day operations of the business together for several years. Back then, the elder Pitts brothers were using a 1980s Franklin hydraulic felling shear, which was state-of-the-art at the time, the brothers recall. The business was known as Pitts and Jolley Logging Co., Inc., until Jolley passed away from cancer.
Now having stepped up to follow in the footsteps left by their dad and his brother, Mack and Rickey also run the business together equally as co-owners. The brothers procure the company’s timber and oversee their dedicated fleet to maximize productivity efficiently. “We’re still in the woods every day,” the brothers agree. “We buy the wood and keep our trucks running and if somebody’s out we jump on a piece of equipment.” At the Pitts Logging headquarters, located in the western portion of Brantley County, the brothers have decorated the halls with vintage photos of the company’s humble beginnings. Blown-up onto canvases, the visual history serves as a daily reminder to Mack and Rickey of their heritage.
Part of that heritage is their faith. Yes, hard work is necessary and making a living is important, but their top priority is to serve Jesus Christ and be an example for their families and workers. “We love to work and make money but our number one goal is to serve him and give him all the glory because we didn’t do any of this,” Mack declares. “God has given us the ability to grow the business to what it is now and we never forget that. Without him, we are nothing.”
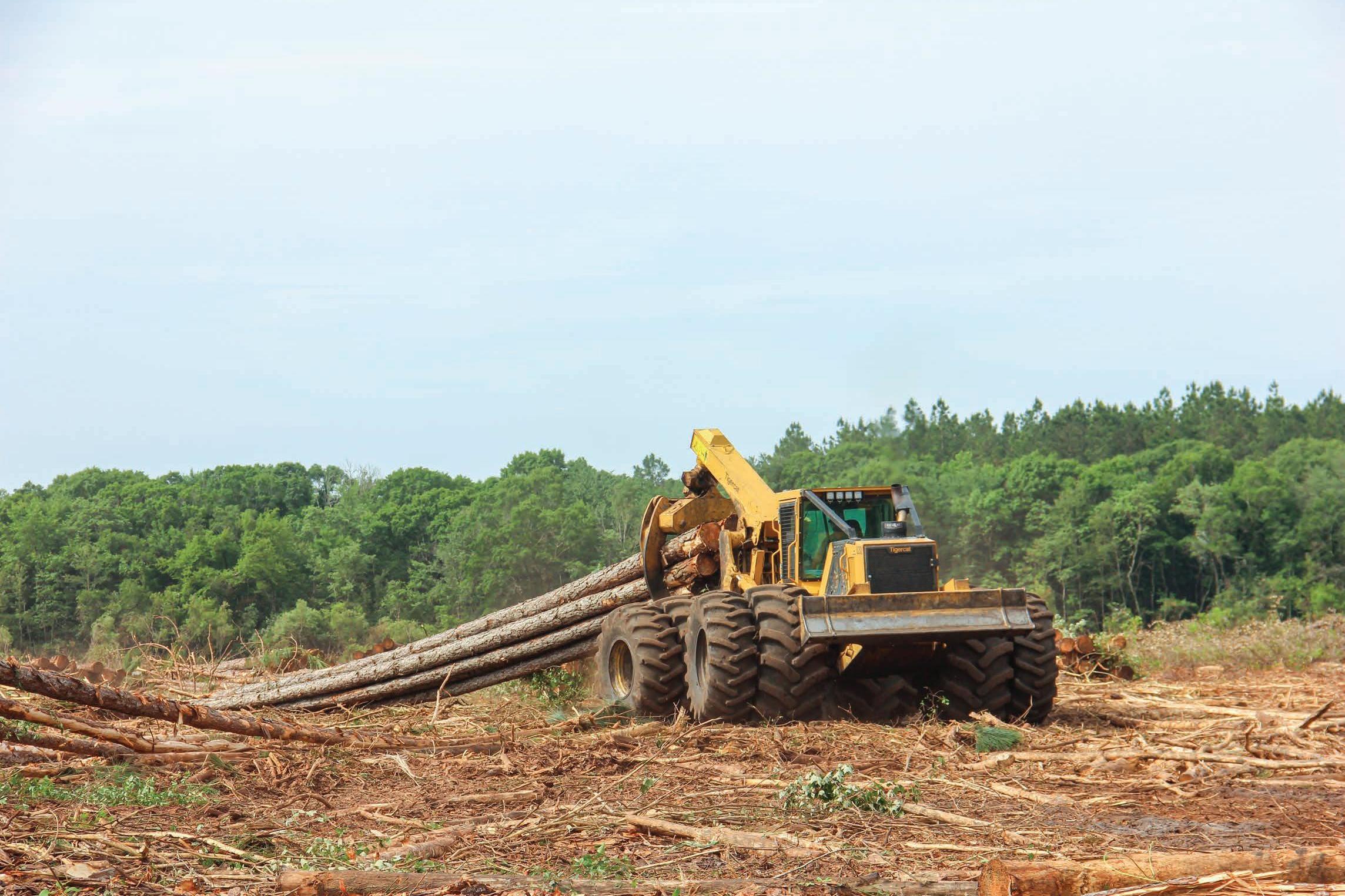
Trucking
The Pitts brothers started building their own dedicated trucking fleet in 1993 to circumvent higher contract freight prices and insurance premiums. “Trucking insurance was a big deal four years ago when our rates jumped 75% because of Hurricane Irma,” Mack says. “But having our own fleet alleviated some of that cost and gave us more freedom to send our drivers and maintain low gatewood prices.” A collection of Big John trailers complement their Peterbilt lineup.
Of the company’s 16 total trucks, the last six are Western Star with glider kits purchased through Four Star Freightliner of Valdosta, a Western Star truck dealer. The remaining 10 trucks are 389 model Peterbilts. When they found out that Peterbilt (like Mack, Volvo and Kenworth) would be discontinuing glider kits after 2019 due to emissions regulations, the brothers jumped at the chance to stock up, in an effort to avoid regen cycles, DFP and EGR, before it was too late. “Last year was the last time you could buy them,” Rickey says. Glider kit trucks matched a brandnew shell and rear ends with a remanufactured transmission and engine, offering a product the Pitts brothers very much liked. “You get a new truck but it’s the old Detroit engine so it’s easier to work on them,” Mack says. “You don’t have all the DEF fluid and electronics.”
Pitts Logging runs four crews, each averaging 70 loads per week.
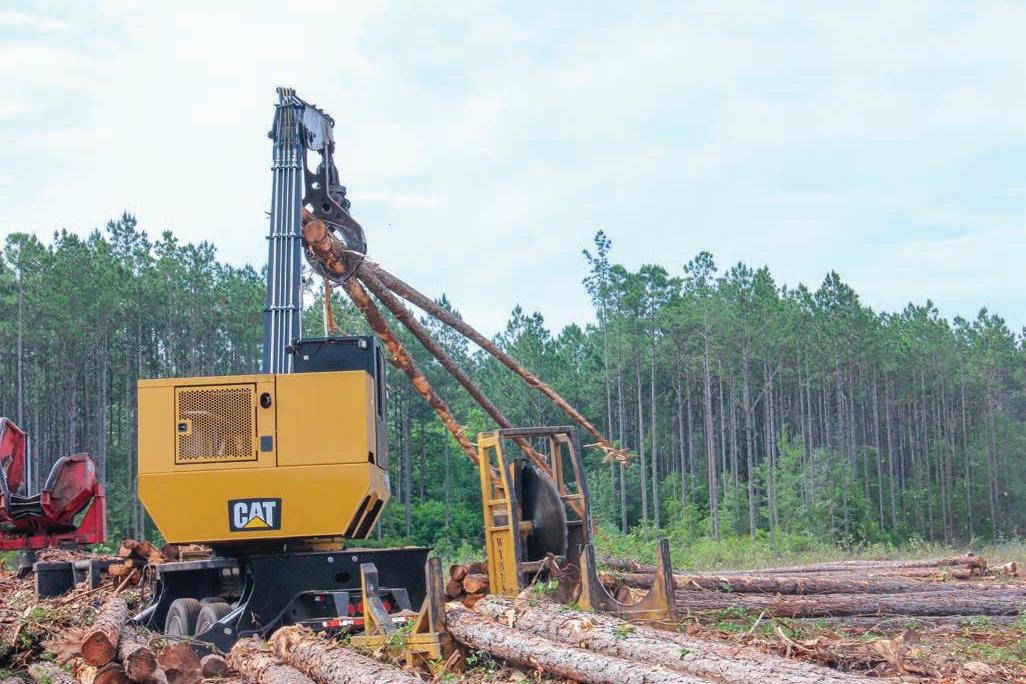
From left: Ricky Pitts, co-owner; Allen Mercer, skidder operator; Joe Still Jr., cutter operator; Dalton Lee, loader operator; Brian Howell, setout man; Mack Pitts, co-owner
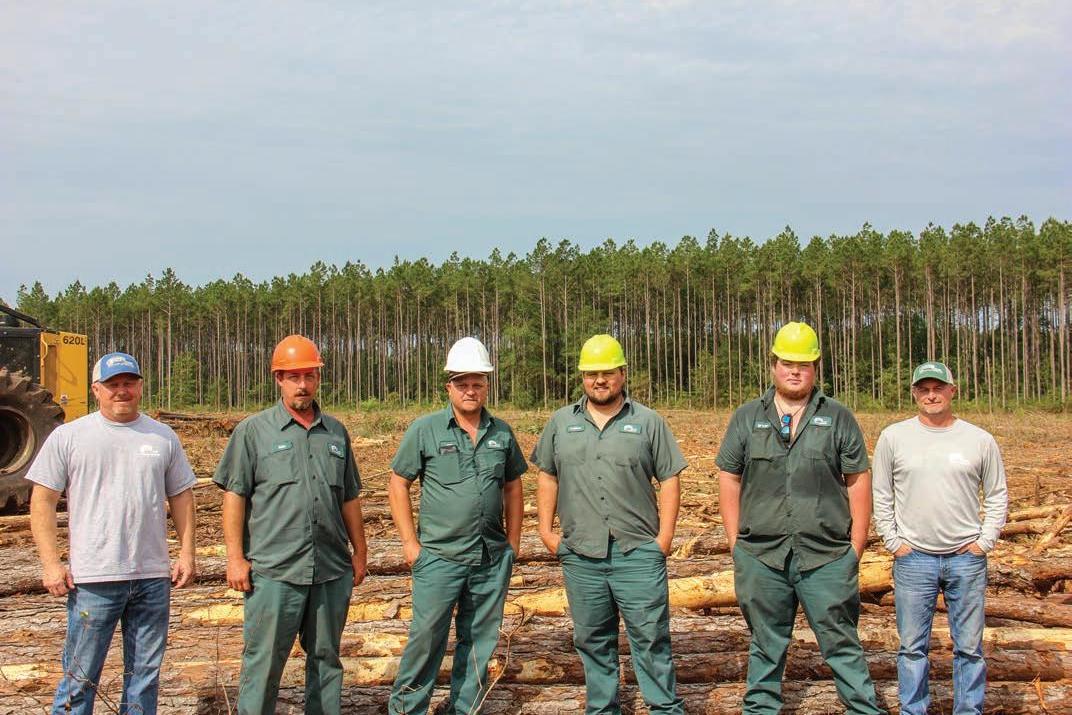
The Cat 559D loader is outfitted with a circle saw slasher package.
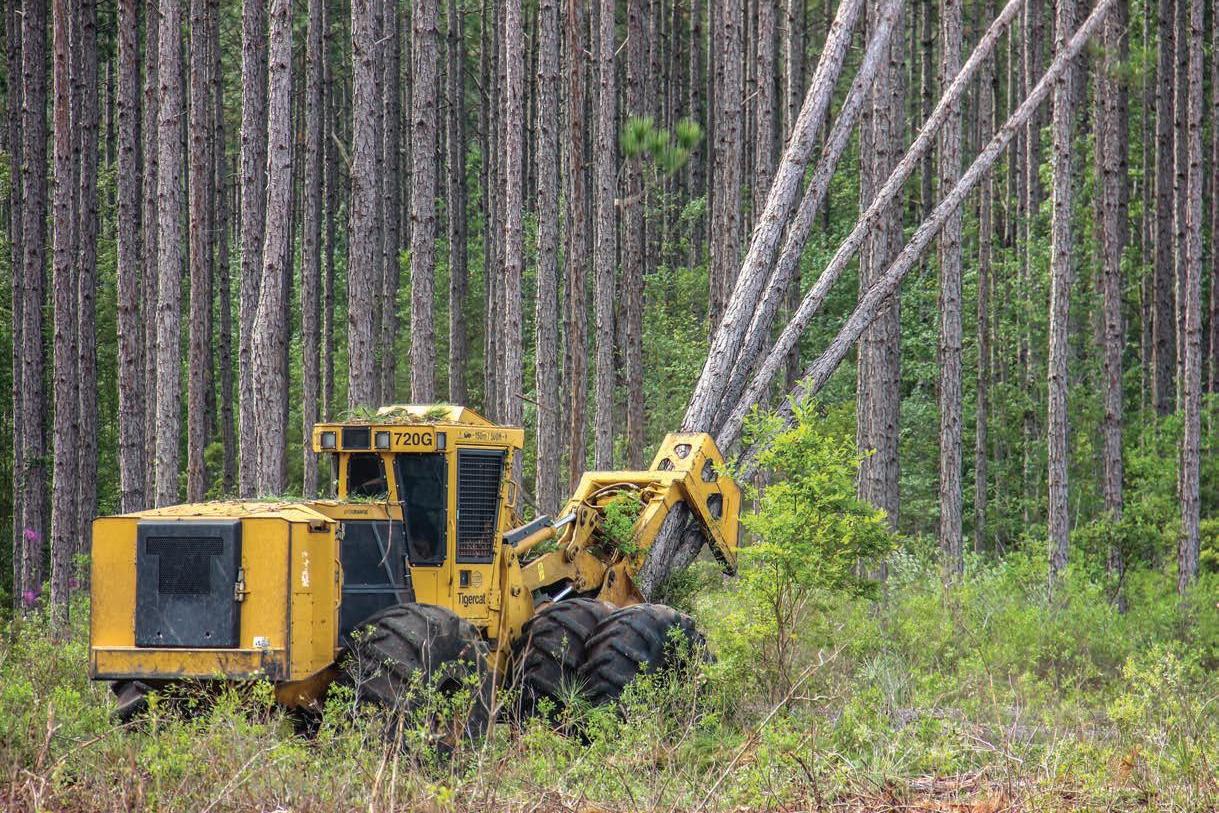
Rickey adds, “These are the engines they put in trucks 15 years ago.”
Each crew averages 70 loads per week and supplies a variety of mills. Pulpwood is hauled to pellet producer Enviva Biomass in Waycross, West Fraser in Blackshear, Langdale Forest Products in Valdosta, Georgia Pacific in Brunswick and Dupont Yard, Inc., in Homerville and Alapaha. Hardwood logs go to Rayonier Inc. in Patterson, while larger DBH logs go to Ace Pole Co. in Blackshear and Meredith Pole & Timber Co. in Fitzgerald. Local pulp markets have been fair lately, Mack says, and it helps being able to negotiate timber sales and transportation.
Timber
The company began purchasing its own timber in 2006. Rickey says it allows them to negotiate commission on tonnage and not be under another’s thumb. “We prefer to buy our own wood that way we can control where we want to haul our wood to maximize production,”
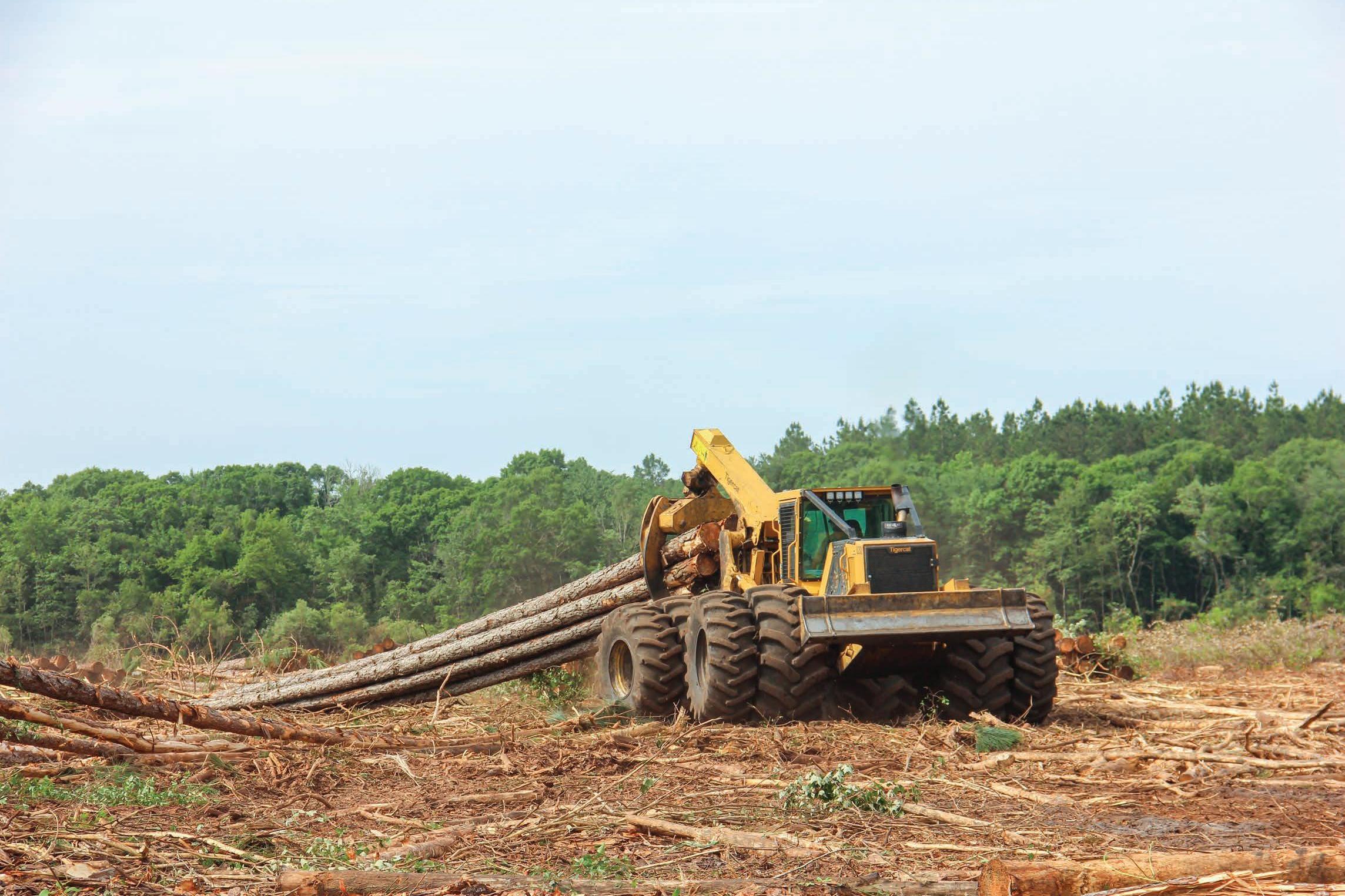
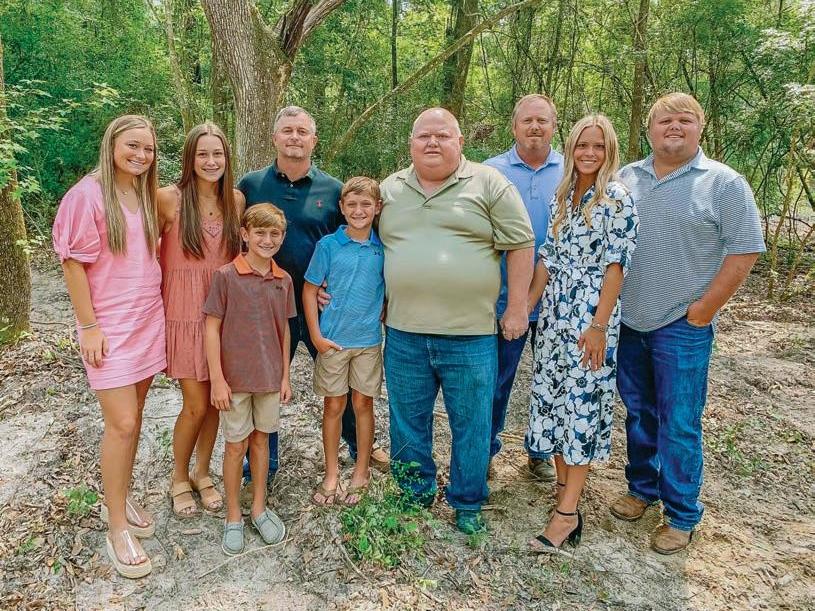
The Pitts family
Rickey says. “Some of the bigger timber companies beat prices down so much there’s not much skin left. You can make a living contracting but you’re not going to make money.”
When Southern Loggin’ Times visited Pitts Logging in May 2021, crew number three was operating on a 270-acre private tract in Ware County, conducting a clear-cut prescription on 40-year-old slash pine.
The company’s biggest hurdles recently haven’t come from fuel shortages or supply chain breakdowns, but instead from Mother Nature. “We try to stay on hills but with all the rain we’ve had recently it looks more like a swamp,” Rickey says. “The weather has been a challenge. We have one crew sitting on a hill and got eight inches two weeks ago. We’re having to mat on the hills to get wood and if we get in a spot that’s 15 acres of swamp we can use our track cutter so it doesn’t slow us down.” Last year they had to run their Tigercat 822 track cutter six months to keep wood moving.
Machinery
Six months ago they purchased a 2019 Cat 559D loader, finding a good deal on the used market, Mack says. They use it on crew number three. Otherwise, everything else is Tigercat. They believe the brand makes a durable machine that holds its resale value longer.
Equipment currently in service for Pitts Logging ranges from 2016 to 2020 year models. Each of the four crews is outfitted similarly, with a Tigercat 620 skidder with dual tires (35x5s inside and 24s on the outside) and a 720 feller-buncher. Crews one, two and four each use a ’19 Tigercat 234B loader with a circle saw slasher package and CSI delimber; crew three uses the Cat loader. Pitts Logging also keeps dozers and backhoes for culverts and road maintenance.
Mack and Rickey buy all their Tigercat machines from Tidewater Equipment Co. in Brunswick.
“We try to swap out equipment every three years to keep things new and under warranty,” Mack says. That gets harder to do, though, as new equipment prices keep going up. “I started in 1999 and the first skidder I bought was $122,000. We got a quote yesterday for almost $300,000 and you’re not moving any more wood today than you were then and get about the same rate to log.”
Maintenance
Woods machinery under warranty is serviced by Tidewater every 250 hours either on the stand or at their Brunswick location. All truck maintenance is done in-house at Pitts’ 100x175 service shop. They keep three full-time maintenance technicians. Oil is changed in trucks every 15,000 miles using CAM2 15W-40 synthetic. Machines get greased every two weeks.
To help with routine daily maintenance and repairs on the job site, the brothers retrofitted a 20 ft. container box to store a 1,000-gallon fuel tank, hydraulic oil, grease, air compressors and an assortment of tools.
A multitude of fuel dealers keeps Pitts’ trucks and equipment moving. The brothers look to Murray Oil Sales Inc., in Surrency, Lewis & Raulerson Inc., in Waycross, Bennett Oil Co. in Waycross and Perry Brothers Oil in Americus.
Pitts Logging’s insurance is through Forestry Mutual and Swamp Fox Agency, based in Moncks Corner, SC. Pitts Logging company secretary Renee Berry handles the company’s books and other administrative duties. Accounting firm Higginson & Paulk in Waycross also assists with managing the business’s finances. SLT
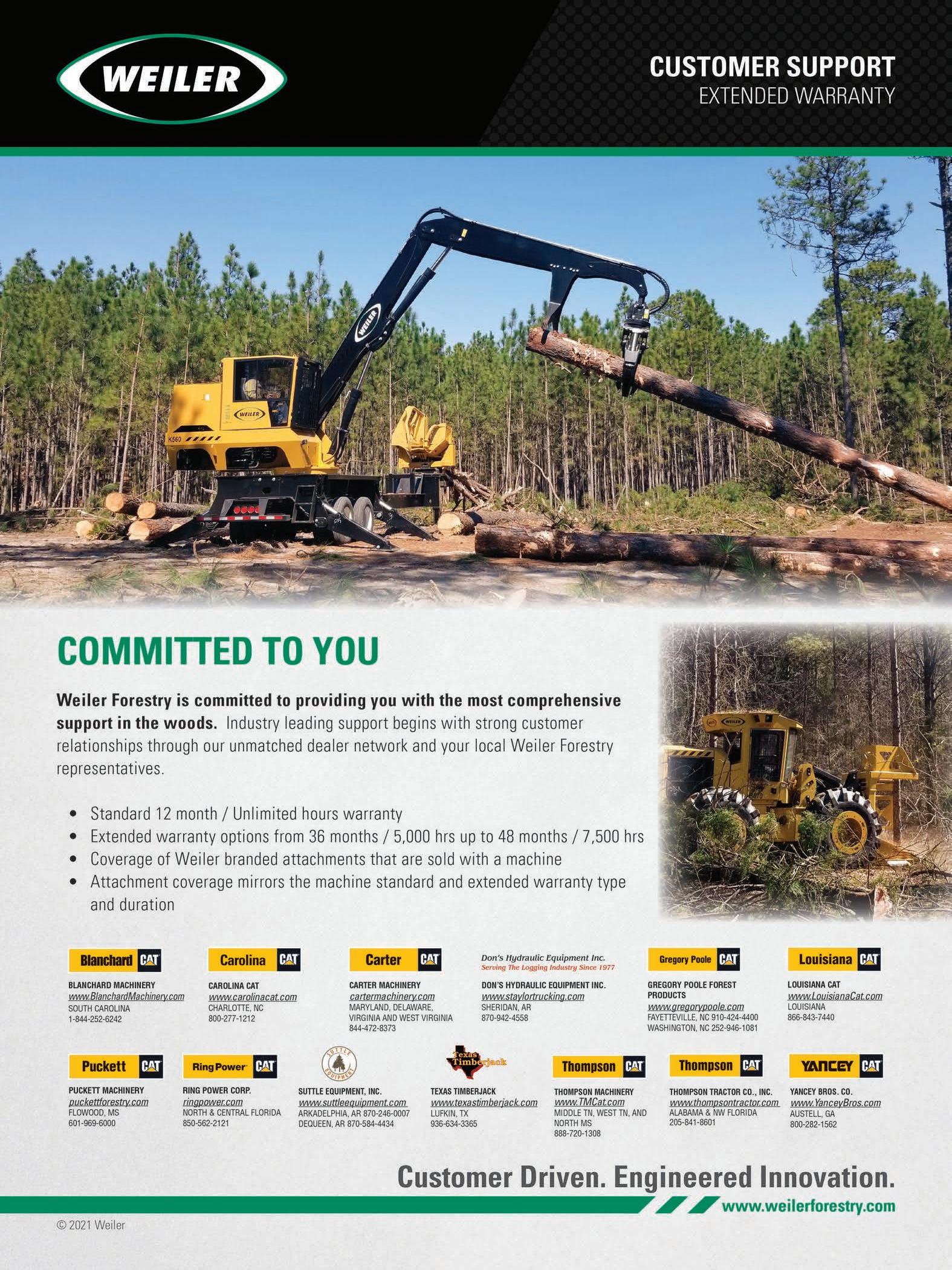
Power Up
■ Father-son duo Bill and Tripp Harrison find success in chipping.
Note: A version of this article previously appeared in the June 2020 issue of Wood Bioenergy.
By Patrick Dunning
WILLISTON, Fla.
What began as a swamp and hill operation in 1971 has diversified into a substantial chipping-for-biomass operation in recent years for William “Bill” Harrison, 69, and his company Harrison Logging Co. What brought the change? A variety of factors, but the biggest being the opening of a new market near Harrison’s home, a municipal electric utility burning wood chips for power, now operating under the name Deerhaven Renewable Generating Station. First brought online in late 2013 as Gainesville Renewable Energy Center (GREC), the 102.5 MW facility burns biomass chips sourced from the region Harrison cuts, so it was a natural fit.
Harrison has crews that contract cut for Columbia Timber Co., and have since the 1980s. Columbia had the first contract to provide wood for the Gainesville plant, and through that contract, Harrison was introduced to chipping-for-biomass. The logging company operated a Bandit 2590 chipper that Columbia purchased for a while, but it quickly became evident that the market demanded a heavier-duty machine, and an increase in production. Now, Harrison operates three Bandit chippers, one 3590XL for M. A. Rigoni and two 3590s for Columbia Timber Co. producing a total of 250 loads of chips a week. In total, the crew sees an average of over 300 loads per week—chips and logs.
“The 3590 Bandit chipper helps us diversify our market and the landowners love it. Their land is clean when we leave,” Harrison explains of the machine and its reception since being added to the equipment list as the biomass power plant’s demand rose. What might have taken months to cut now takes Harrison a matter of weeks, and leaves the land cleaner.
“There is just not a lot of debris left when we leave,” he adds. “I wish there were chip mills everywhere. It would change the way people look at loggers. Sometimes we go behind pine crews and chip their block and it looks terrible. Not that they are doing anything wrong, they just don’t have a chipper.”
Tripp, left, and Bill Harrison, right
On The Job

Harrison has always known what he wanted to do. “My mommy told me the first toy I asked for when I was a baby was a log truck.” At 18, he stepped out on his own and founded Harrison Logging. In ’87, he added a second crew. A few years after son Tripp, 45, joined the company.

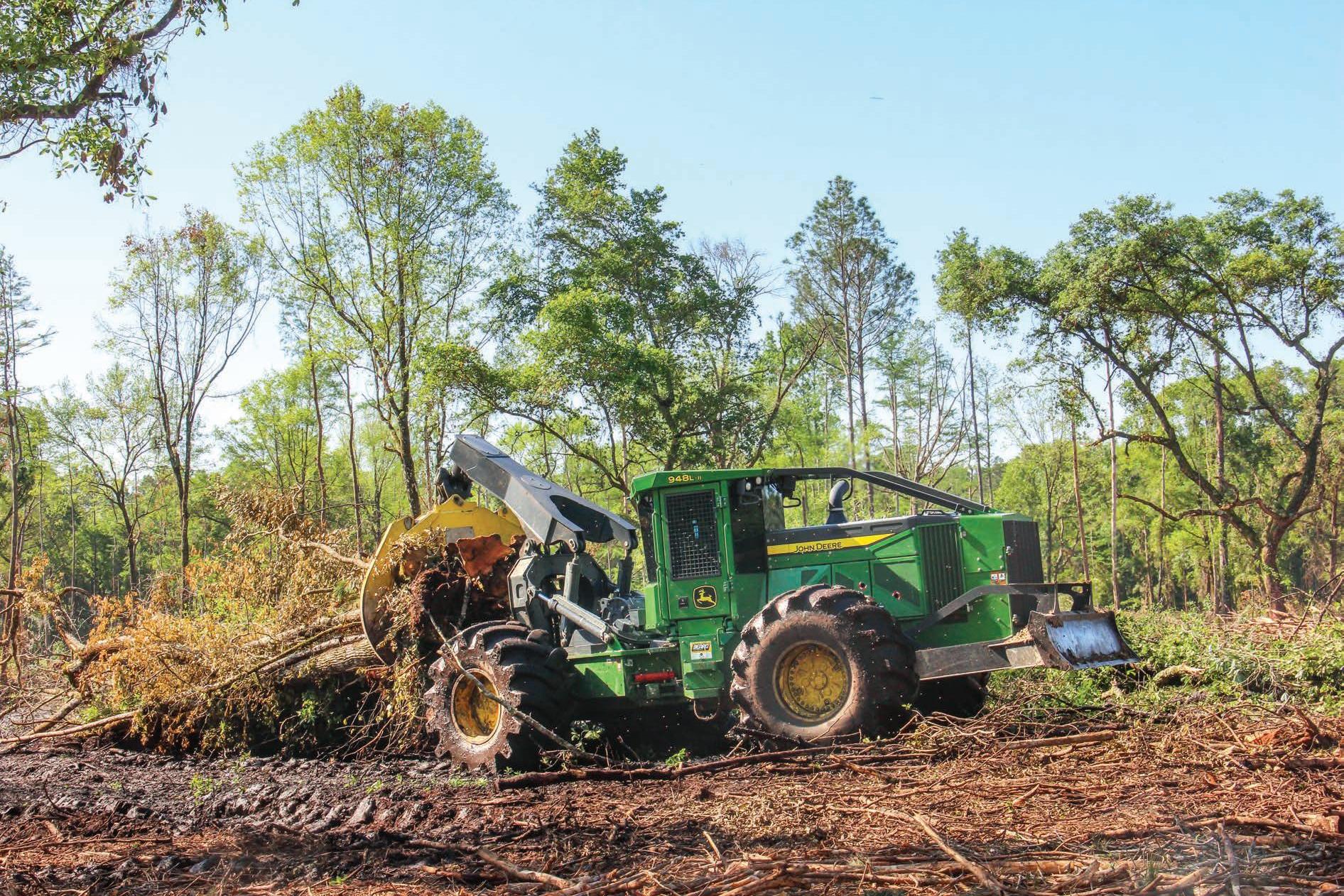
In total, the company operates five crews (three chipping and two conventional logging). The chipping crews are set-up similarly, but not identically. One crew runs a 595 Barko loader, two 643L John Deere feller-bunchers, 948L John Deere skidder and 3590 Bandit chipper. One crew runs a Caterpillar 595B loader, DelFab three-wheel fellerbuncher, Cat 555D skidder and 3590 Bandit chipper. The other chipping

Gainesville Still Likes Biomass
Construction on the Gainesville Renewable Energy Center (GREC) started in June 2011 and, when completed in October 2013, the $500 million, 102.5 MW biomass power facility began a nearly 10-year roller coaster ride of shutdowns, full-speed operation and acquisition. When the facility began commercial operation, with the intent to use 1 million tons of woody biomass annually, it faced significant scrutiny locally because of the costly and lengthy power purchase agreement between the city and the developers.
It then was plagued with other issues ranging from noise complaints to a lawsuit from one of its primary biomass suppliers over feedstock requirements. In late 2017, GREC was sold to Gainesville Regional Utilities (GRU), a municipal electric utility, owned by the city of Gainesville. This acquisition brought desperately needed diversity to GRU’s power generation portfolio—which has an aggressive long-term renewable energy goal.
Renamed Deerhaven Renewable Generating Station (DHR) following GRU’s acquisition, the plant provides reliable markets for fuel providers like Bill Harrison and is helping GRU towards its goal of becoming 100% renewable by 2045 across all generating sites.
“The DHR biomass plant is very important to the resolution. When you look at renewable energy in the state of Florida, your two options with current technology are solar and biomass,” Dino De Leo, GRU’s energy supply officer, says. “Biomass is clearly a large portion of the renewable portfolio and will become even larger as we move towards our resolution.”
An independent energy services company operated and maintained the plant for two years from 2017-2019, until it transitioned to full GRU staffing in late 2019.
Reaching 100% renewable is currently impacted by natural gas pricing. GRU was 42% renewable in 2019 and 32% in 2020, due to the price point of natural gas.
“We have a responsibility to our customers to operate as efficiently and economically as we can, so when natural gas prices fell it did not make sense to run the biomass plant at higher loads,” De Leo says. “We still run it every day, just not at higher loads because we can economically generate those megawatts at a lower cost with natural gas. Our obligation to our customers is to have renewable aspects of our generation but not to the point where it burdens them with higher rates.”
De Leo says they tuned down the plant in 2017 from its previous minimum 70 MW load to 30 MW over the span of two months to preserve energy and associated costs.
“The plant used to operate anywhere between 70-102.5 MW and did not fit our system very well,” he adds. “When everyone went to bed and load decreased we were dumping power into the grid below the cost of making it.” The plant now uses 30-35 MW on average in the mornings during lower loads and occasionally tops 100 MW in the afternoons based on customer demand and weather patterns.
At any one time there’s typically 30,000-40,000 tons of wood on-site that averages 19-30 days of operation—2,400 tons a day full load average.
“We can’t keep wood in large quantities because of the decomposition of wood and we have to control the inventory based on needs,” De Leo says.
GRU’s integrated resource plan executes different goals and projections for higher renewable percentages with the understanding that technology evolves every seven years or so.
He explains, “When you think about the Deerhaven plant, it was put in service in 2013 as a 30year plant and is scheduled to retire in 2043, so you could be looking at possibly two more biomass plants, based on the retirement of Deerhaven. Right now, our integrated resource plan does not call for another biomass plant; we won’t project that until we get there because we want to take advantage of the technology we have.” SLT
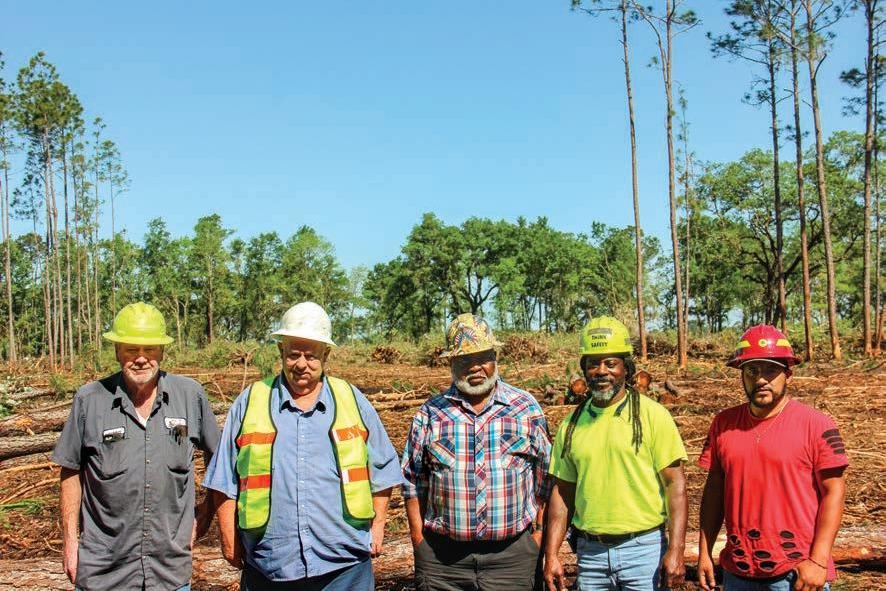
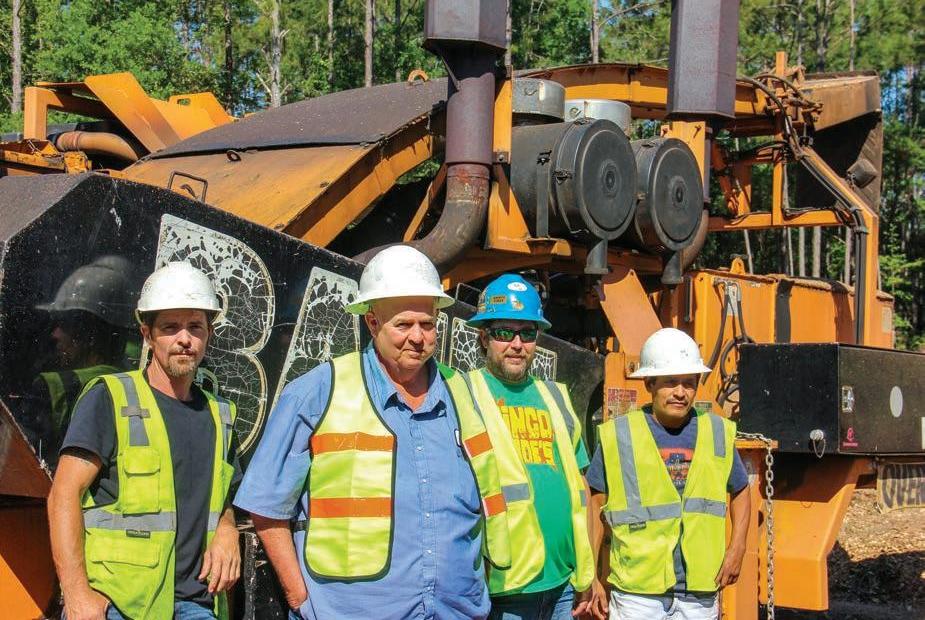
One of Harrison’s crews, from left: foreman Kenny Brown, Bill Harrison, Henry Frazier, contract hauler Cedric Maxwell and Gudiel Mendez The other Harrison crew, from left: foreman Ronnie Aldridge, Bill Harrison, Lonnie Jennings and Juan Cervantes

crew runs a Cat 595B loader, John Deere 843L and 643L fellerbunchers, two 525C Cat skidders and a 3590XL Bandit.
Dealer support comes from Ring Power for Caterpillar, the Maxville, Fla. branch of Tidewater for Tigercat, Quality Equipment & Parts in Lake City for Barko, and multiple locations of Beard Equipment for John Deere.
Harrison prefers running two crews (one chipping and one conventional) on the job site simultaneously when a clear-cut block is available. “I like to have two crews on the same job; that way the feller-buncher operator can cut everything as they go, put chips in one pile and pine in another, then carry it to whichever loader it needs to go,” he explains. “Pine is too thick to actually go through there and get the chipping wood out first. If you cut the pine first you’ll tear all the chip material down, which makes it a nightmare to pick up. We prefer to run them together.”
Harrison Logging utilizes 22 Peerless and ITI chip vans, which under good conditions can be filled in 13-15 minutes. Eight company trucks (a mix of Mack, Western Star, Peterbilt and Kenworth) and 20 contract trucks get the production hauled.
In addition to Deerhaven, Harrison hauls pulpwood to GeorgiaPacific, Palatka; WestRock, Maxville; a shavings mill in Cysero, and occasionally Rayonier, Fernandina Beach. Sawlog markets include Resolute Forest Products (Suwanee Lumber), Cross City; West Fraser, Lake Butler; West Fraser, Maxville; and Cross City Lumber, Cross City. Cypress logs are hauled to Cracker Style Log Homes, Williston; South Eastern Timber Corp., Lady Lake, takes mat logs.
While the crew hauls to many area mills, it’s clear both Bill and Tripp enjoy producing biomass chips. Tripp explains, “Futurewise were trying to produce more chips as long as the mills are wide open. I was out of town looking for a new chipper just a few weeks ago.” SLT
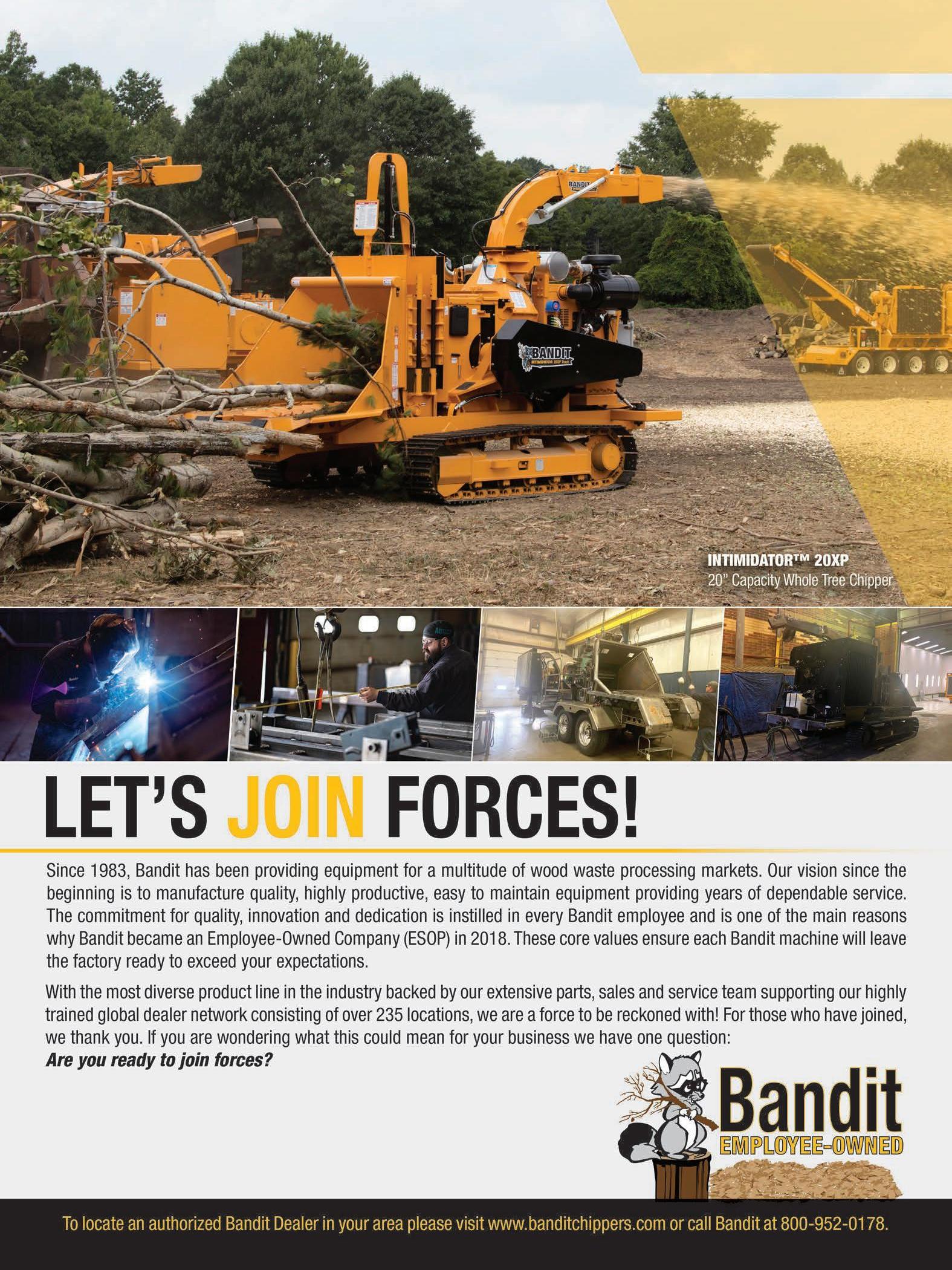
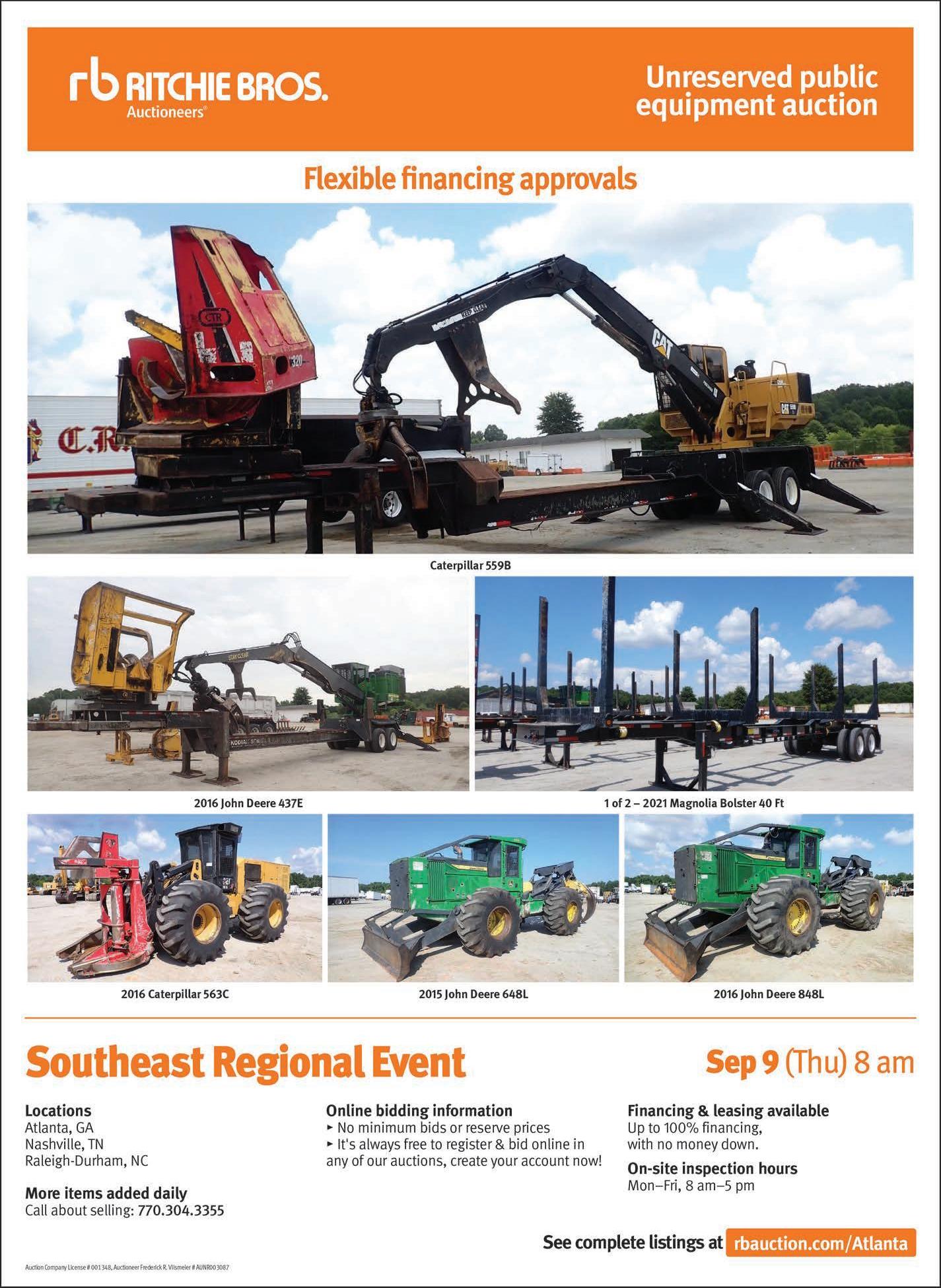
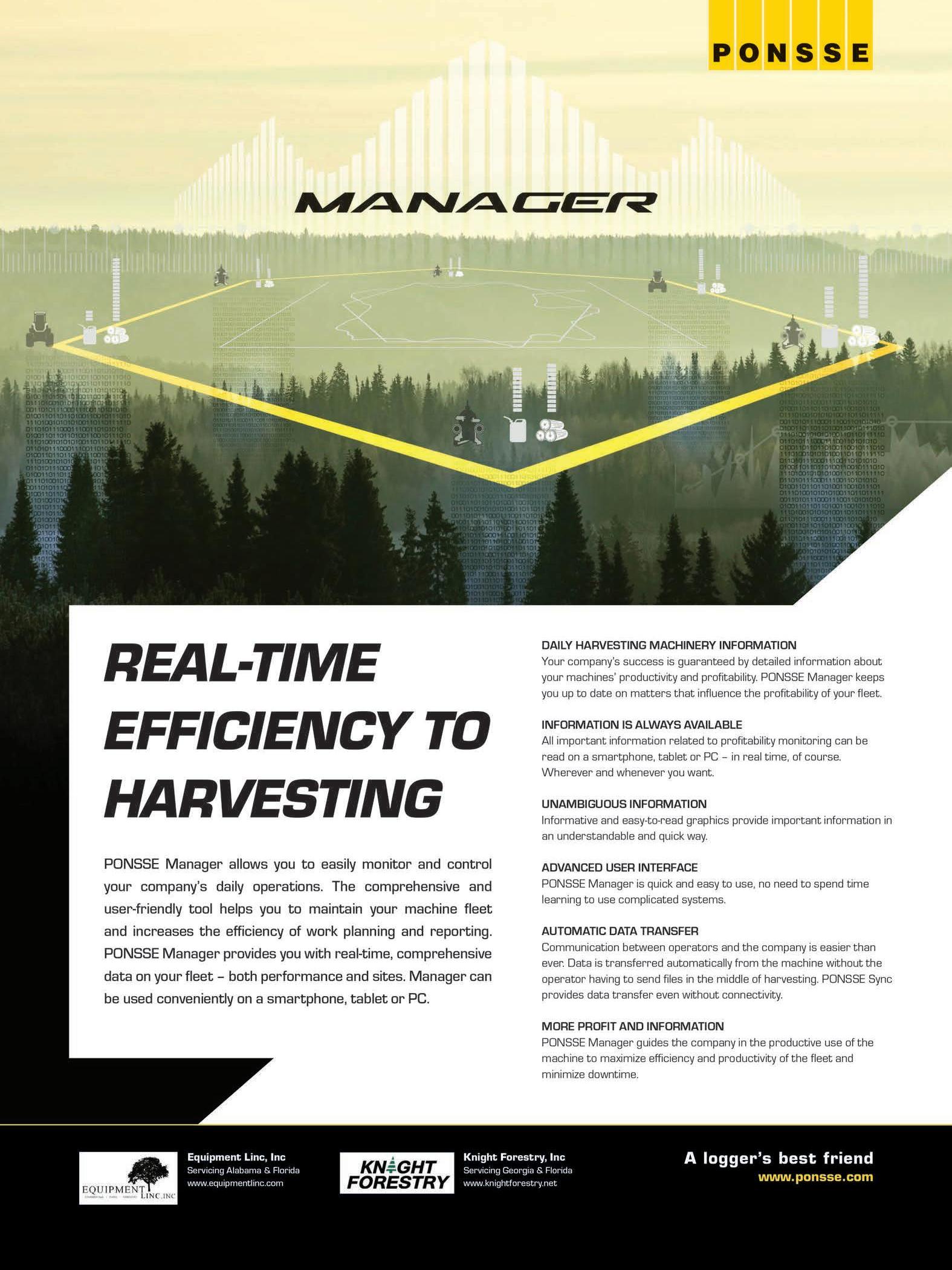