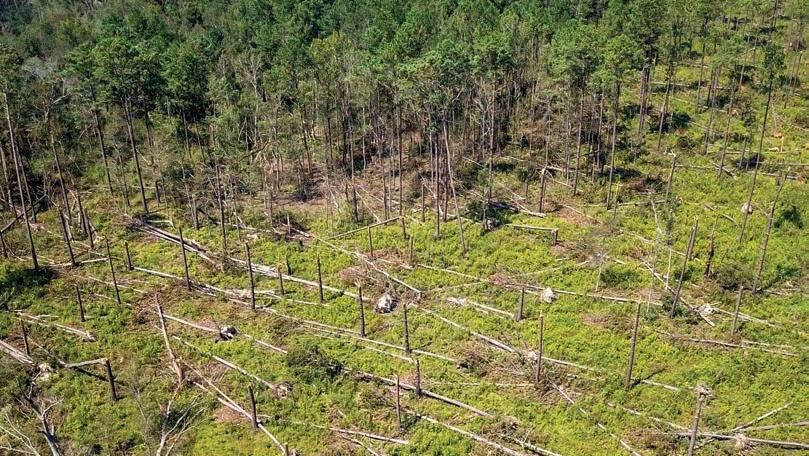
40 minute read
Southern Stumpin
SOUTHERN STUMPIN’ Storm Season
NOTE: Editors Jessica Johnson and Dan Shell contributed these hurricane damage reports, versions of which previously ran in other HattonBrown digital and print publications, including Timber Harvesting magazine, the Logger News Online e-mail newsletter and the Southern Loggin’ Times web site.
Laura Lashes Louisiana When Hurricane Laura slammed into the shoreline near Cameron, La., on August 27 as a Category 4 hurricane, it brought with it 160 MPH winds and maintained hurricane status (80+ MPH winds) all the way to the Arkansas state line. It’s been more than 150 years—before the Civil War, even—since the last time this region experienced such powerful wind speeds. Before Laura, the Last
Laura hit Louisiana hard.
Island Hurricane in 1856 was the strongest storm to make landfall in Louisiana history, and the fifthstrongest to hit the continental U.S. on record.
The damage for loggers and timberland owners equaled a year of timber harvests in a single night. More than 758,000 acres of timberland were badly damaged, including more than 3.5 billion BF of sawtimber (pine: 2.8 billion; hardwood: 740 million), with heavy timber damage reported in 20 parishes. According to a report by Jeff Zeringue in the Louisiana Logging Council’s Louisiana Log ger publication, more than 39 million tons of wood came crashing down.
In an economic impact study that cited reports from the LSU AgCenter, industry analysts Forest2Market pointed out that the storm’s $1.1 billion impact on timber inventories was al most double that of 2005’s Rita and Katrina, combined.
LSU AgCenter economist Kurt Guidry figures that, based on the amount of infrastructure damage and timber-related losses, “The total economic im pact to the food and fiber sector from Hurricane Laura will be as large as or larger than
Salvaging wind-blown timber is slow and danHutchins, extension forester for the LSU AgCenter loggers should look into the federal Small Business Administration disaster loan program that offers low-interest loans up to $2 million for businesses impacted by the hurricane. The Louisi ana Treasurer’s Office also administers a small business grant program for businesses affected by the coronavirus that could also be helpful, he added.
The USDA Farm Service Agency (FSA) in Louisiana is accepting applications in eligible parishes for the Emergency Conservation Program (ECP) and Emergency Forest Restorarestore damaged farmland to pre-disas-

any storm that I have developed estimates for ter conditions and may provide up to 75-90% of since my time with the AgCenter.” cost-sharing. The EFRP provides payments to eli-
On the ground, loggers are looking to salvage gible owners of nonindustrial private forest (NIPF) what they can, but over-saturated timber markets land to carry out emergency measures to restore mean a big drop in prices. According to Forest2 - land damaged by a natural disaster. Local FSA Market’s report, Laura will drive stumpage prices County Committees determine land eligibility and, down in the near-term as too much wood, much of if applicable, an on-site damage inspection to it low grade, chases too few market outlets. Long - assess the type and extent of damage. Eligible forer-term, the report predicts, “Stumpage prices will est restoration practices include debris removal, become more volatile and likely trend higher there- such as down or damaged trees, in order to estabafter—once the market works through the usable lish a new stand or provide natural regeneration; salvaged timber—and the regional supply chain site preparation, planting materials and labor to adapts to new operating conditions that reflect the replant forestland; restoration of forestland roads, loss of over $1 billion in timber resources.” fire lanes, fuel breaks or erosion control structures; fencing, tree shelters and tree tubes to protect trees Unsalvageable from wildlife damage; and wildlife enhancement to
gerous, and standard mechanized logging equipment isn’t designed for horizontal stems. Robbie Michael: 2 Years Later provide cover openings and wildlife habitat. Extension Service, says it’s not as simple as just bringing in chain saw crews because of how the Recovery from Laura in Louisiana is just getting started, but two years after her cousin Michael wood is twisted. “It becomes a safety nightmare,” hit Florida, loggers in that state are still dealing he says, and that will balloon insurance costs. with the damage. When it made landfall on OctoMoreover, a report from the AgCenter determined ber 10, 2018, Hurricane Michael raged at 160 that only 10% of the downed pine and none of the MPH. Barely missing the major Panama City pophardwood can be salvaged. ulation center that would have made the human toll
The same dynamics came into play two years much worse, the storm churned through north ago after Hurricane Michael hit northwest Florida Florida and southwest Georgia for 150 miles and southwest Georgia: huge amounts of timber in before furious hurricane-force winds finally dissibarely salvageable condition, with overall market pated. It was the fourth-strongest wind speed landconditions making it barely worthwhile to cut and fall hurricane in contiguous U.S. history. haul any of it. Noting that the parishes hit hardest Michael’s eye ripped right through the center of contain the most productive timberlands in Loui - a 98,000-acre tract in the Bear Creek watershed, siana, Louisiana Forestry Assn. and Louisiana Log- leaving in its wake a scene of blast-zone devastaging Council Executive Director Buck Vandersteen tion. In mere hours a thriving, working forest that says “Unfortunately, most of this will be unsal- had been growing everything from seedlings to 35vageable. Making matters worse is most mills are year-old sawtimber was reduced to an epic disaster already carrying a full wood inventory.” of downed and windblown trees. According to a report by industry analyst ForAvailable Help est2Market, the most heavily affected areas lost the
Several relief programs are available. Vander- removals, all concentrated into several hours. steen reported in his Louisiana Logger column that TIMO Forest Investment Associates (FIA) man-
tion Program (EFRP). The ECP helps to Disaster drove innovation in Florida's Bear Creek. equivalent of 10-15 years of timber inventory

ages the Bear Creek tract. With a 33year track rec ord and $4.7 billion in timberland assets un der man agement in North and South America, FIA’s largest investment area is the Southeast U.S., where it manages 1.7 million acres. Roughly 37% of those assets are within 60 miles of the Gulf or At lantic coasts. There have been plenty of hurricanes over the years, but the damage to the Bear Creek tract “was unlike anything ever experienced on our properties,” says Mike Clutter, FIA Vice President, Director of U.S. Investments and Operations.
According to Clutter, at Bear Creek 3.4 million merchantable pine tons were removed due to storm damage, and 7,500 acres of pre-merchantable plantations were lost. Overall, he says, Michael took about 92% of the tract’s standing inventory.
It took the better part of a month’s hard work for American Forest Management (FIA’s on-site field service pro vider) and the Florida Forest Service to reopen the primary woods roads and allow up-close inspection. The closer all involved got to the disaster, the bigger the challenge grew.

Once assessments were made and inspections completed, the magnitude of the task became clear: the complete re-establishment of 55,000-60,000 acres of bedded plantations on low wet ground—as soon as possible. In spring 2019, the FIA team hoped the job would take five years to complete.
Hammered
“The eye of the storm centered (the tract), so you had wind going east to west, then the eye went over and you had wind going west to east,” says Frank Corley, forest engineer, longtime logging industry veteran and owner of Corley, Inc., who was brought in as a consultant for the recovery project.
Corley and Clutter have worked together several times over the course of their careers, including 14 years when both were with Union Camp.
“I had no clue what to do the day I arrived,” Corley admits. “Nothing was obvious. Only some of the youngest stands, about five years and younger, were able to carry forward.
The rest of it was gone.”
Forestry specialists Larson &
McGowin used digital modeling software to predict debris loads remaining on the ground, and the
Silvics Solutions S2 program identified many areas of older merchant able plantations that had 150-200 green tons of debris per acre that had to be otherwise dealt with be fore plantations could be re-established and the tract placed back into production.
Much of the merchantable timber was broken off in snags, jumbled on the ground in pieces, extremely unsafe to log conventionally and virtually unsalvageable. Working with local contractors, AFM was able to harvest a small amount, but with the WestRock paper mill at
Panama City down due to storm damage and other wood consumers either operating at greatly reduced capacity or not operating at all, wood prices dropped drastically.
Corley says even if more could have been salvaged, “People don’t realize how the mills were impacted too, so the markets weren’t really there for a while.”
It became apparent that the remaining timber and debris, snags and leaners had to be taken to the ground before anything else could happen. And the tremendous amount of debris made windrowing unfeasible because of handling and piling costs and lost planting space. Trying to devise a plan of action, Corley brought in several others to give perspective, among them Mark Sauer, President of
Savannah Global Solutions, and
Johnny Boyd, district manager with Tigercat Industries.
Disaster drove innovation as the group developed systems to handle the various conditions on the tract and ultimately re-establish plantations in the debris fields. For example, a modified Tigercat sawhead was developed with the bunching arms removed and a custom housing with v-blade added atop the tower to take down much of the smaller pre-merchantable material. The machine goes down each row, “mowing” as close as possible to the ground and letting

the trunks and snag stems just fall away. This leaves the bed in place and makes for quicker replanting.
Another example: a push-bar system—simply a 22 ft. piece of heavy square-tube steel with a slight bow on each end mounted to the front of a D6 dozer—is being used to take down material that’s just at thinning age or a bit below. Some of these stands were the toughest to deal with, Corley says.
Presenting the biggest overall challenge were the older age stands, some up to 35 years old. These had the highest debris loads.
Savannah Global has a reputation as a major mass land-clearing specialist, having worked typhoon recoveries in Australia and reservoir land clearing in Africa among other recent offshore jobs and projects in 35 countries. Sauer advised the group to try chaining: dragging a large ship chain between two D8s to knock the debris onto the ground.
The recovery team settled on a 450 ft. deep sea ship anchor chain pulled between two Cat D8s running parallel roughly 60-80 ft. “You pull it behind in a u-shape, and the chain sort of sags behind,” Corley explains. He bought the massive chain from a shipyard in Louisiana, and it weighed only a couple hundred pounds short of highway weight limits to get it hauled to Bear Creek.
“It’s a slow process and can be dangerous,” says Quint Crager of Quinco Contracting in Chatom, Ala. “Ground conditions are pretty rough; there’s lots of really heavy debris in most areas.” Noting the extra guarding all around the dozer,
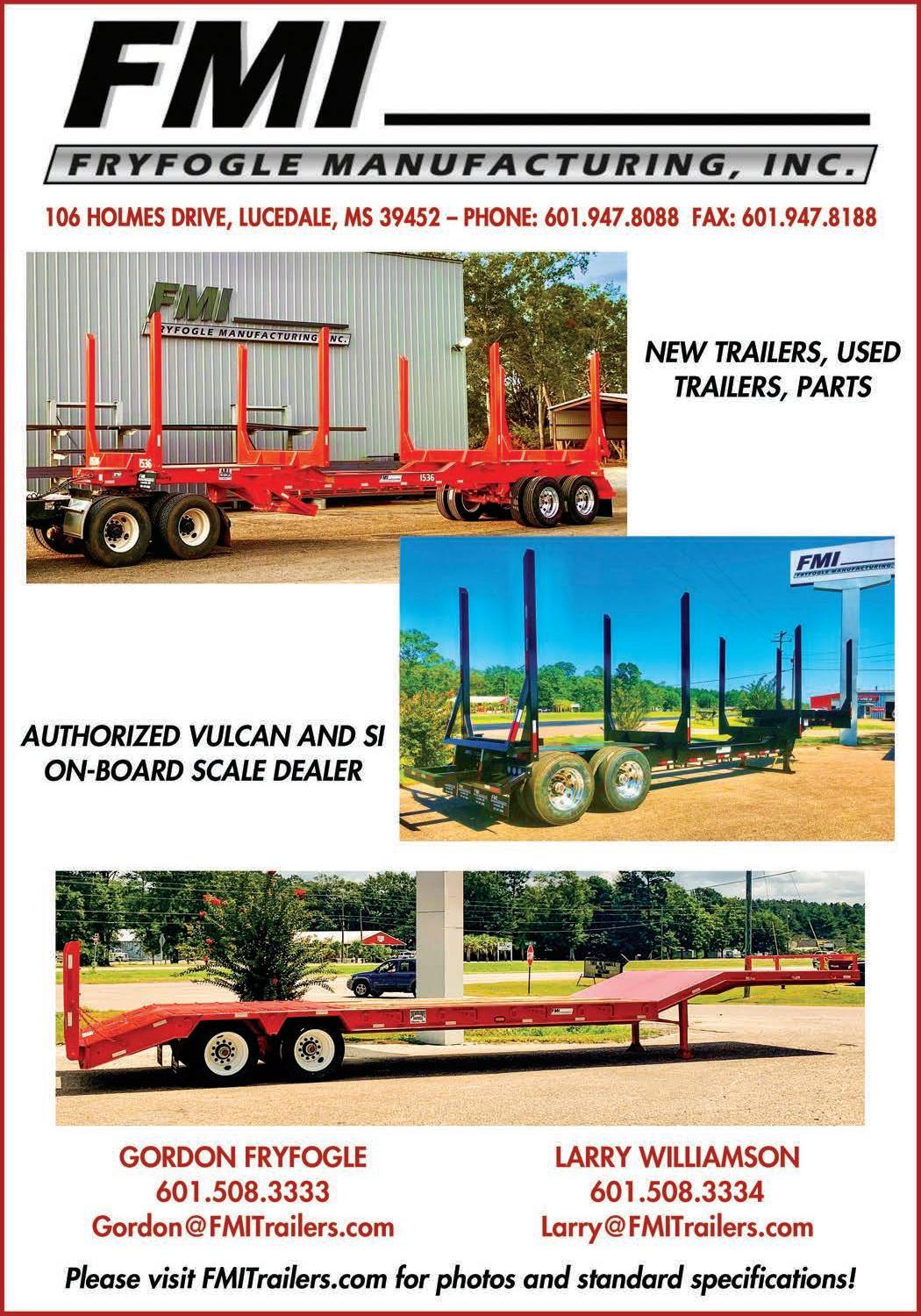
he adds, “A main concern is safety of the guys operating. We’ve never done the chain pull before.”
Crager says that as time has progressed and the timber has deteriorated, it’s lighter and can work easier; some of the wetter areas where fallen material has more green volume continue to be a hard, slow pull. Another issue is keeping equipment cooling systems running smoothly in all the debris. “You can’t take just anybody who operates a machine and put them in this, but we’ve got some really good operators,” Crager notes.
This summer there were five main contractors on the site doing chaining, push bar or sawhead work. As each system is applied to the tracts where it works best, the big chunk of remaining work continues to be the areas that need chaining.
Wet ground is a big issue yearround for all the crews. Super low elevation and flat terrain make any form of precipitation problematic for operations, and some areas are wetter than before the storm be cause there’s no timber and cover to help absorb groundwater. Taking advantage of any short-term dry conditions, crews try to cover as much of the low ground as possible, when possible, but some areas may have to wait for an extended dry spell to be worked.
“This is by far the biggest project we’ve ever taken on,” says
Travis Buck of Tree Farm LLC in
Fosters, Ala. “Trying not to get stuck—that’s the biggest issue because there’s mud and water everywhere and it’s all flat ground.”
Once all material is on the ground, there’s at least one pass with a shear v-blade required to open it up, and another pass with a bedding plow to get the row ready to replant. The crews are going with slightly wider row spacing due to the remaining debris, which is several feet high on each side of some planting rows.
Looking ahead, there’s plenty of work left to do. Clutter believes it’ll take four more years to completely regenerate the 55,000 acres of plantations that had to be put back into production, and the project is moving along roughly on schedule.
He notes that even with years of hurricane impacts around the Southeast, an event like what hit the Bear
Creek tract emphasizes that geographical diversity is important for timberland investors. Strategies like standing timber insurance policies and pursuing shorter rotations to re duce hurricane exposure are other options to consider, he says. “Very large contiguous holdings close to the coast need to be viewed as more risky than those that are geographically dispersed,” Clutter adds. SLT

Brotherhood
■ Marine vet Kirk Sanders specializes in CTL logging, and honors his late brother/partner Bill.
Photo courtesy of Ponsse North America
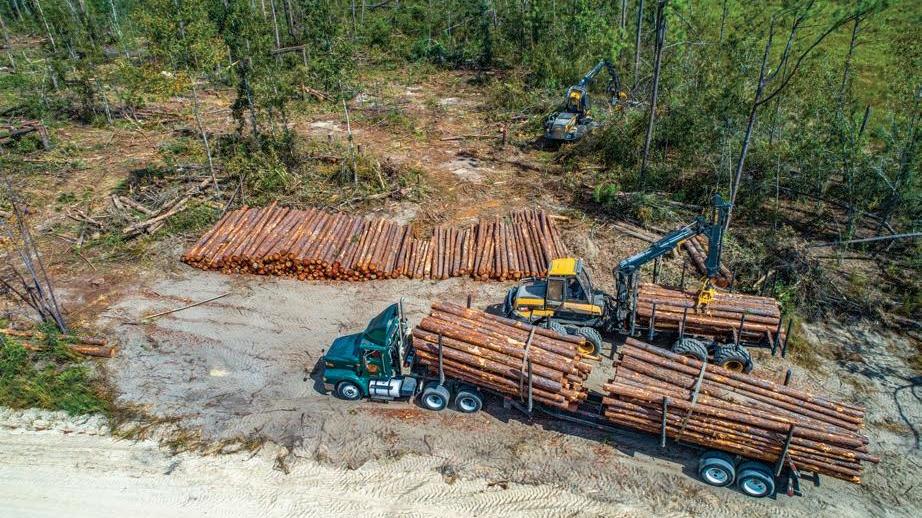
By Patrick Dunning
PINSON, Ala.
When he was young, not so ★ very many years ago, Kirk Sanders didn’t foresee his future being in logging. He and his big brother Bill had spent some summers working for forester Ken Smith, who was employed at Buchanan Lumber in Montgomery at the time. But a summer job wasn’t necessarily something he envisioned turning into a long-term career.
When he was still a freshman studying mathematics at Montgomery’s Huntingdon College in 1981, Sanders enlisted in the Marine Corps Reserves as an infantry rifleman attached to the 3rd Battalion, 23rd Marine Hotel Company based in Montgomery.
After earning his bachelor’s degree in 1984, Sanders went active duty as a commissioned infantry officer. Similar to numerous infantrymen trying to boost their real-world experience on the civilian side, Sanders put in for a lateral move to change his MOS (military occupational specialty) to data systems officer—now referred to as IT (Information Technology).
“I figured it would be worthwhile for me to have some additional knowledge and experience when I got out,” Sanders says. After the request was approved, he transferred to I MEF (Marine Expeditionary Force) in San Diego, Calif.
Sanders targets high-grade logs.

Sanders was later relocated to Air Station El Toro in Irvine, Calif., where he worked for the automated service center and ultimately was placed in charge of the information resource center for five years.
“IBM-PC were talked-about items coming online so we were right in the middle of that development,” he reflects on his time there. “Microsoft was bidding for the operating system, which ended up being Microsoft DOS 1.0.”
Down Range
The Marine Corps paid for Sanders to go to graduate school at Auburn University if he drilled with the local reserve unit once a month and two weeks each summer. He had been in grad school less than a year and home from desert training northeast of Twentynine Palms, Calif., for scarcely 48 hours when he got the call. “We came home from the desert on the last day of July and August 1, Iraq invaded Kuwait,” Sanders recalls. “I said wait a minute, I’m a student! They said no you’re not, you’re a Marine. Pack your bags and let’s go.”
In August, 1990, the Iraqi military invaded the sovereign country of Kuwait under Saddam Hussein’s dictatorship in a bid to gain more control over oil supplies along the Persian Gulf coast. Hussein refused to withdraw his troops from Kuwait after being condemned by the United States and UN Security Council, igniting the Persian Gulf War.
Sanders deployed overseas to Riyadh, Saudi Arabia, attached to the 8th Marine Regiment, 2nd Marine Division, Hotel Company, 1st platoon. His company was transported five miles from the Kuwait-Saudi border around 9 p.m., rucked at pace-count to the border, established a right flank for the battalion and dug in.
“We were close enough that you could see the Iraqis across the border in daylight,” Sanders says. “We lived in a hole all day.” At night they provided interlock patrols or relocated positions and dug new foxholes before the sun came back up. Sanders says his command in Saudi Arabia referred to them as the “speed bump” because they were non-mechanized infantry displaying a show of coalition forces. “We were strict infantry so if they would have attacked with armor they would have went right through us without slowing down.”
The 8th Marine Regiment was in Kuwait longer than any other U.S. combat unit, Sanders says, not leaving till June 1, 1991, even though President George H. W. Bush had declared a ceasefire on February 28. “We went 91 days without hot food, light, no heat, and no change of clothes, living in a hole in the ground,” Sanders says. “You find out pretty quick you can’t get any nastier. But it was a wonderful lifestyle, believe it or not; I enjoyed the hell out of it.”
Sanders received the Navy Achievement Medal, given to junior officers for outstanding achievement, and retired as a Captain.
New Direction
When Sanders got back from his tour, his brother Bill asked what he was going to do next. Kirk admitted he didn’t know. The Sanders brothers were considering options over a few beers when Bill had an epiphany. “We had what I like to call a once a great notion,” Sanders laughs, referring to the 1971 logging movie Sometimes a Great Notion (also released under the alternate title Never Give An Inch), starring Paul Newman and Henry Fonda. (Notably, the movie is an adaptation of the 1964 novel by author Ken Kesey, whose first published work was 1962’s One Flew Over the Cuckoo’s Nest. Though that earlier story is of course more famous due to the Jack Nicholson film, many critics considered this novel about a family of stubborn Oregon loggers to be Kesey’s finest work, and the film adaptation was also wellreceived, garnering Academy Award nominations.)
The great notion the Sanders brothers had, Kirk explains: “Bill suggested we get into the logging business and I figured, why not?” They bought a loader, a Mack truck, one skidder and a cut-down machine. Buchanan Lumber donated a trailer and just like that, the newly formed Sanders Timber started logging for the Montgomery mill.
Bill had cruised timber for Buchanan Lumber in the past but other than those summers spent working for Ken Smith, neither of them had a tremendous amount of experience in the woods. They hadn’t grown up in it; their dad was actually a prominent physician. But there was no reason for that to stop them. They were both smart and well educated— both were Huntingdon graduates. Both were artistically talented—Bill was an accomplished painter and Kirk is a writer. Both had served in the military—Bill was an Army Green Beret with the 20th Special
Forces group, Birmingham, one of two National Guard groups for the U.S. Army Special Forces. There was no doubt they could succeed here as they had done elsewhere.
Hard Hit

In the spring of ’96 an F2 tornado hit Montgomery, resulting in loss of life and damaged timber. Buchanan Lumber owned a parcel of land along the Macon/ Montgomery county line by Line Creek in Shorter that was damaged. While helping clean up the tract, Kirk was walking through the woods when a wind gust shook a 30 in. pine log out of the canopy above him. It drove him into the ground, immediately knocking him unconscious and into a two-week coma.
The crew had carved a road with a dozer that wasn’t on any map. Even so, “from the time Leroy Howell called 911 to the time I was in the back of the ambulance was eight minutes,” Kirk says. Paramedics conveniently received the call while refueling at a truck stop off the same exit where the Sanders crew was logging. Just as fortunately, the ambulance driver had a hunting lease adjacent to the tract and knew exactly where Kirk was located. They transported him to Jackson Hospital in Montgomery, where he was admitted to intensive care. Once they had him stabilized, he was moved again to the UAB (University of Alabama Birmingham) hospital for surgery.
When he came out of the coma, Kirk couldn’t walk or use his hands. “The doctors thought I was going to die so they didn’t bother amputating my arm,” Sanders says, noting the 19 pins he now has in his right arm. On heavy doses of pain meds, he was under hospital care for the first year-plus of his rehabilitation. He made good use of the time, though: he wrote a book.
It started with audio recordings he made dictating his memories of his life. Later, to rebuild dexterity in his fingers, he typed a transcription of those tapes. The typing helped repair nerve damage in his hands, he says. The eventual result was a manuscript entitled C.O.T.F.C.: Short Stories of a Marine, a raw and vivid account of his time in the service. The book is now in the Library of Congress.
It took him about five years to fully recover from his injuries, but his outlook on the entire experience remains tellingly sanguine, revealing a lot about the man’s character. “I tell everybody, I had a good day,” he sums it up. “But that tree died.”
CTL, Ponsse

At the turn of the century in 2000, Sanders heard that Finlandbased cut-to-length machinery manufacturer Ponsse was looking to expand its presence in the southeastern United States. The logger jumped at the opportunity presented by Ponsse North America President Pekka Ruuskanen. “Pekka said, ‘Why don’t you come with us to Finland,’ so I went.”
At the time, Kirk’s friend Deck Trevitt, the owner of Georgia’s Quality Forest Products, had Ponsse machines but, like many Southern loggers who have tried it, struggled to make the CTL system work in his markets, Sanders says. “I was in a meeting together with the company owners and told them, ‘I’ll go back to Georgia and show Deck how to run the Ponsses if you will make Deck the representative for the Southeast and when you need to do a demo, use Deck’s machines and don’t worry about transporting machinery because we already got the crew.” They struck a deal and Kirk went to work for Ponsse.
Later, in 2016, Bill bought a Ponsse harvester/forwarder team and the brothers went to work conducting high-grade thinning prescriptions exclusively, which Kirk believes is the future of logging. “We supply grade and preserve a stand of timber,” he says. “We can go in and cut all grade hardwood and in 10 years come back and do it again.”
Now 59, Sanders prefers not to be locked into a fiber contract with surrounding mills, a trick he learned from his brother. “Bill always dealt in hardwood and realized it’s the only way to make money,” Kirk says. “When you have a machine that can find a log in a tree that heart problems a few years back would otherwise be put in a pulp- and went to the UAB hospital to wood stack, that tree just went up have a stent put in. The doctors 10 times in value. The way we cut a concluded that only three of his tree, we cut the logs out and leave valves were functioning; the fourth the tops sitting there. Only thing was closed off. “The doctors told coming out is the grade log.” him he had some sort of heart trau-
The harvester, a Ponsse Bear 8WD ma as a young man and the valve with two bogies, weighs 62,000 lbs. scarred over and rerouted the blood Its 300HP Mercedes-Benz engine somehow,” Kirk says. “The doctors burns about four gallons an hour. told him they didn’t know if he had Kirk says he uses no more than 500 five days or five months.” In fact, gallons of fuel a week in both Bill lasted another three years. machines combined. A 33 ft. C5 crane boom supports a 4,000 lbs. H8HD processing/harvesting head with four top-andbottom knives cutting both directions and 10 knives total. Equipped with a gyroscope that keeps the machine level, the H8HD has up to 36,000 lbs. of pulling force and can process 17 ft. a second.
The 40-ton capacity Elephant forwarder is Ponsse’s Elephant can carry a truckload each trip. capable of bringing out a full truckload at a time. Its KL100 When Bill was alive, the brothers crane features 36 ft. boom reach owned Sanders Timber equally, but and 17,000 lbs. of lift capacity with they had an agreement that after a 48 in. wide bunching grapple. Bill’s death, Kirk would sign full “It’s way easier when you’re stack- ownership of the company over to ing wood, and then you separate Bill’s daughters, Lou Anne Owens your high-end logs and next lower and Mary Buxton, and he was logs,” Sanders explains. happy to do so. Mary has followed
Kirk typically mans the harvester in the family’s other tradition— while John Porter drives the for- she’s a First Lieutenant in the U.S. warder, but both men can run either Marine Corps, 5th Marine Regimachine. Jamie Parnell at Equip- ment stationed in Hawaii. Lou Anne ment Linc Inc., in Maplesville rep- handles all the bookwork for resents Ponsse for the Southeast. Sanders Timber. With primaries Sanders changes oil and filters Richie Smith and John Porter superevery 300 hours with Mobil 1 syn- vising the crews and their uncle thetic 10w-40. They use ISO-68 Kirk describing his role now as hydraulic oil, grease the head and “support,” the girls’ inheritance and fill up bar oil daily. their father’s legacy seem to be in
Sanders adds that workers’ comp good hands. is considerably less on the CTL When Bill and Kirk went to work operation than with conventional for Ken Smith all those years ago, equipment because there’s only two he was good friends with timber machines in the woods, thus fewer cruiser Buddy Fuzzell. Those two people, lowering the chance of men had gone to college together, injuries. and they maintained a friendship
Sanders Timber also fields a tree- with both Sanders brothers through length crew with three Tigercat cut- the years. Even after Smith’s death, ters, two Tigercat loaders with Fuzzell continued to serve as a mendelimber/slasher packages, five Cat tor to the Sanders. Now, Kirk says, skidders and a Cat dozer, motor the long-time family friend is taking grader and excavator. While the an active role in seeing Bill’s daughCTL crew does strictly select cuts ters succeed as well. “He’s helping of high grade logs, averaging 15 guide them down the steep and narloads a week, the conventional crew row path.” hauls 15-20 loads daily of pulp- Through all he’s done in his life, wood, chip-n-saw and everything Sanders has maintained the same else. Foreman Richie Smith super- worldview that sustained him in that vises the treelength side. hole in the desert almost 30 years ago. “It’s all a matter of belief,” he Not Forgotten confesses. “I believe in God, country and family. There are three things in
Bill Sanders died in May this every man’s life: faith, hope and year at age 60; Southern Loggin’ love. And the greatest is love. Faith Times published a tribute to him in in God, hope in your country, love the July issue. He’d been having for your family.” SLT
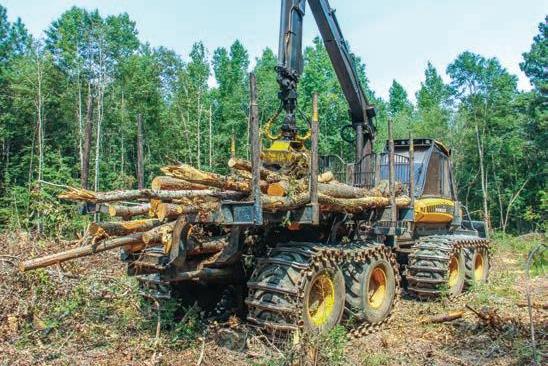



Hands On


■ Tennessee’s Hooper operation is growing despite changes in market demand.
By Patrick Dunning

TOONE, Tenn. T he Hooper family and kin are renowned in the ★ Tennessee Valley region for being a friend in each step of the wood harvesting and sawmilling process. Their port able saw mill tradition began almost a century ago with Malcolm Hooper, fa ther of Tony Hooper, 64, own er of Tony Hooper Sawmills, Inc., hauling logs in an old pickup truck to his all-manual groundhog diesel sawmill.
Tony has built on his father’s foundation and pursued crosstie markets heavily since the company’s founding in 1970, including the installation in 2018 of a second sawmill company and site, Northside Lumber & Sawmill LLC in Bolivar, Tenn., only seven miles to the south of Toone. Crossties are revered as their bread and butter and for good reason: the area’s Hatchie River bottoms are perfect for large growth and the Hooper sawmills are set up to take advantage of the big logs to produce crossties as well as cants.
“We learned a long time ago that we like to take the tree to the finished product,” Tony’s nephew and timber procurer Timmy Hooper, 54, says. “That’s our goal.”
Tony’s two sons-in-law manage his sawmills: Blake Sowder at Northside Sawmill & Lumber in Bolivar, and Richard Crowley at Tony Hooper Sawmill in Toone.
The family dynamic works well for the business. Two of Tony’s nephews oversee hauling procedures from the logging site. His brother-in-law is a foreman, and Tony’s other nephew, Timmy Hooper, is the company’s timber buyer.
The Hoopers capitalize off owning sawmills, but their presence in the woods is making the difference with soft red oak markets steering Tony’s logging crew toward tracts dense with a white oak population. “It works better for me to buy land, timber and all, turn around and harvest the wood, then resell the land so somebody can see what they’re getting,” Tony says. He owns several thousand acres across Tennessee.
Species harvested include red and white oak, gum, beach, birch, cottonwood and other mixed hardwoods. The crew targets timber 14 in. on the stump and greater, sticking to hardwoods that will make at least a crosstie.
Operations
Southern Loggin’ Times found Tony Hooper Sawmills, Inc. in Au gust doing a select-cut on a 620acre hardwood tract along the Tennessee-Alabama state line.
The stand is divided down the mid dle by a creek and in cludes a portion of crop land.
Timmy says they’ve been trying to avoid tracts with red oak and had to change up the area where they purchase property. “The tracts we’ve been buying lately are in this region because of the white oak that’s on it.”
The region’s Hatchie River bottoms are perfect for producing cross ties, and gum trees grow faster than in Missouri, Arkansas and Kentucky, Timmy suggests.
“It’s a hotspot to grow tie trees, that’s one thing that’s helping us,” Timmy says. “The gum grows fast so tie companies target this area. There’s a little more toward middle Tennessee and we are having to travel farther because of the markets but we’re steadily going after it.”
Machinery Row

Tony’s equipment lineup in cludes: ’18 and ’19 model John Deere 948L skidders, ’19 Tigercat 234B loader, ’18 Tigercat 726G cutter, ’19 John Deere 544L dozer, and their newest addition, a ’20 Tigercat 635G six-wheel skidder equipped with Eco-Tracks.
“Our Tigercat skidder is made to
climb those rough hills, it’s nies owned or operated in kind of unstoppable,” Tennes see,” Timmy says. Timmy says. “It works very To compensate for the gap well in swampy terrain but be tween consumer and supalso very well in these hills. plier, Tony recently completIt’ll go where other skidders ed installations of a two-line, wouldn’t think about turnkey stave operation feagoing.” turing Brewer equipment.
Tony deals directly with The 13,000 sq. ft. facility is Donnie Kirk at Stribling attached to Northside LumEquipment, Jackson, Tenn., ber and will begin producing for John Deere and Clint stave logs early next year. Mont gomery at B&G Tony Hooper Sawmill and Equip ment, Iuka, Miss., for Northside Lumber sell 7x9, Tigercat. 8x6 crossties, and 10 ft.
All woods equipment is switch-ties to Classic Ameriserviced every 250 hours using Rotella. Truck oil is From left: Soul Garcia, Sergio Garcia, Steve Hooper, Placipo Rubio, Kevin Elders, Javier Servin, Mathew Simmons, Tony Hooper, Timmy Hooper, David Pichard can Hardwoods Inc., Memphis; Somerville Tie Compachanged at the 10,000-mile mark. round shafts, pins; we can use a plas- ed to 7x9s and 8x6s for cross tie nies, Holly Springs, Miss.; and KopTony has a couple mechanics on the ma cutter or weld some parts togeth- markets. pers, Inc., Jackson, Tenn. payroll, Craig Wilson and Chris er, tap some holes, it’s too easy.” “Selling lumber two years ago Lumber is sold green to Ashley’s Kelly, who have been with the com- brought in twice what it brings now,” Furniture manufacturing plant, Ecru, pany for decades and work at the Markets Tony says of recent red oak depreci- Miss. and Bruce Hardwood Flooring, shop in Toone. ation. Effects of the US-China trade Cape Girardeau, Mo. Local pallet
“When Tony buys a new piece of Tony’s crew targets 75-80 loads war bleeding into the novel coron- stock companies purchase 4x6 cants. equipment, whether it’s John Deere, weekly and occasionally gets up to avirus pandemic were felt by North- Sawmilling has been in their famiTigercat, whatever, he brings it in 100 loads a week when harvesting side Lumber. In spite of soft red oak ly for generations. “The sawmills are here and our guys beef it up,” bottom timber. markets, Timmy believes white oak something we’ve always done,” Tony Timmy explains. “They put brush Their fleet of trucks includes two markets are the hottest he’s ever says. When it’s cold and wet his logguards on machines to keep them ’15 and ’16 Freightliners, ’19 and seen. “The white oak market is really ging crew builds 2 in. thick, three-ply from getting scratched up, beef up ’20 Western Stars, pulling a collec- hot right now,” he says. “It’s kind of heavy-duty mats. “It gives my guys the blades, bumpers on the back of tion of Pitts and McClendon trailers been saving us.” something to do in the winter time dozers in case you back into a tree, to the Hooper and Northside saw - Majority of stave and veneer logs because we use so many of them. I all kinds of neat extra stuff to the mill locations. go to American Stave Co., Marshall use them a lot for my trucks where machines.” They supply their own mills that County, Ky., to make stave logs for it’s muddy so you don’t have to
Between both mechanics they’re produce 4x6 cants, grade lumber, whiskey barrels. The de mand for worry about getting stuck. In the winresponsible for servicing 10 trucks, and random lengths and widths that stave logs is a major reason white oak ters we stay close to the road anyway 20 trailers, and all woods equipment are sold green to cabinet, flooring, markets are thriving, leaving the fam- and mat the whole road.” as recommended by manufacturer. furniture and stave markets while a ily wondering why there aren’t many Tony spends his days on the log-
Tony’s mechanics use a computer portion of the Hooper and North- in-state stave markets. ging site, at the sawmill, or in his to administer oil changes to their side Lumber product mix is dedicat- “There’s barely any stave compa- truck going to-and-fro. He says peoequipment. “If the dozer holds 10 ple in the area prefer both gallons, you hit a button and it auto- sawmilling and logging to eliminate matically puts 10 gallons exactly in the middle man. “A lot of mills are the tank,” Timmy says. “It’s pretty dependent on gatewood from other neat and saves a lot of waste and loggers, and loggers are hard to when they drain oil they process it come by so that’s why we have our and sell it back to refiners.” own,” he says. “We’re in a comfort-
Wilson and Kelly also have the able niche.” ability to make certain parts, a plus The company’s insurance is with the increase of back orders and through Forestry Mutual. late deliveries due to supply chain Tony’s logging roster includes: disruptions related to COVID-19. David Pichard, foreman; Michael
“If we need a part and can’t get Simmons, Kevin Elders, Eric Cartaour hands on it, we can simply build gena, skidder operators; Steve Hoopthe part,” Wilson says. “Most of the er, nephew and loader operator; Jav times it’s simple parts, something we Together the sawmills produce an average of 250MBF a week. ier Servin, Soul Garcia, Sergio Garcan manufacture pretty quick, like cia, Placipo Rubio, saw hands. SLT
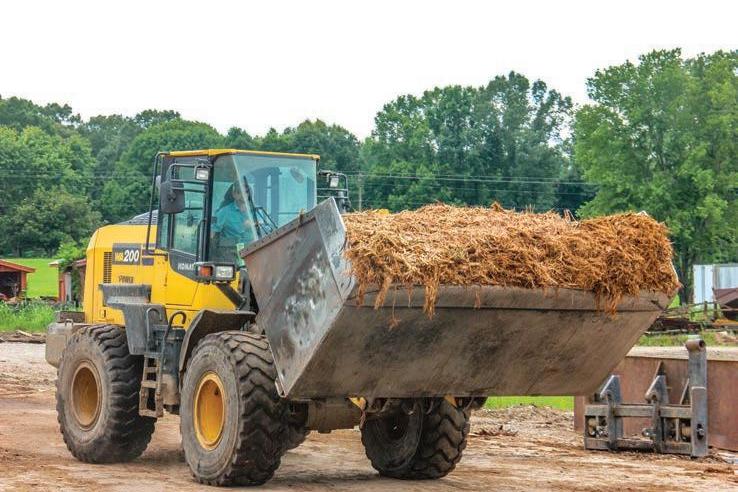

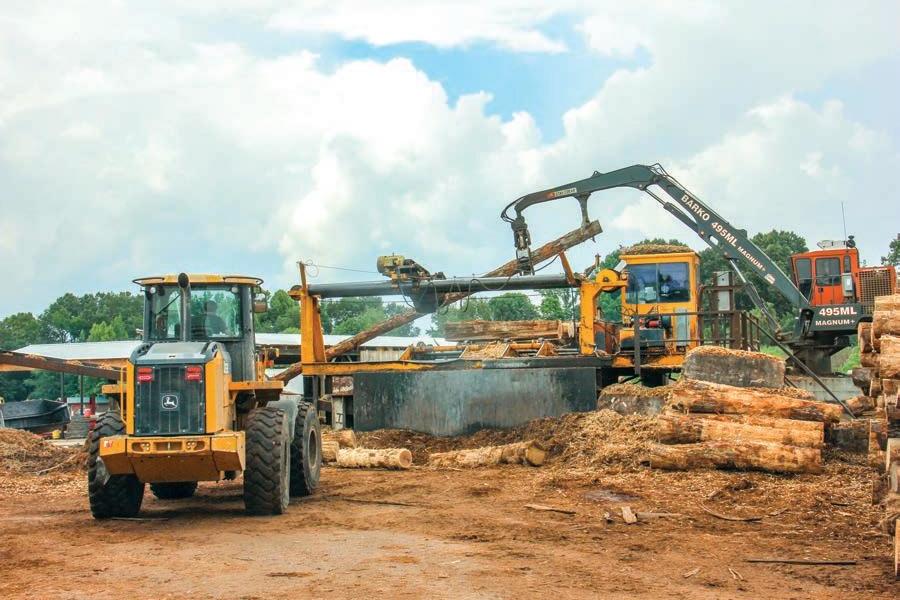
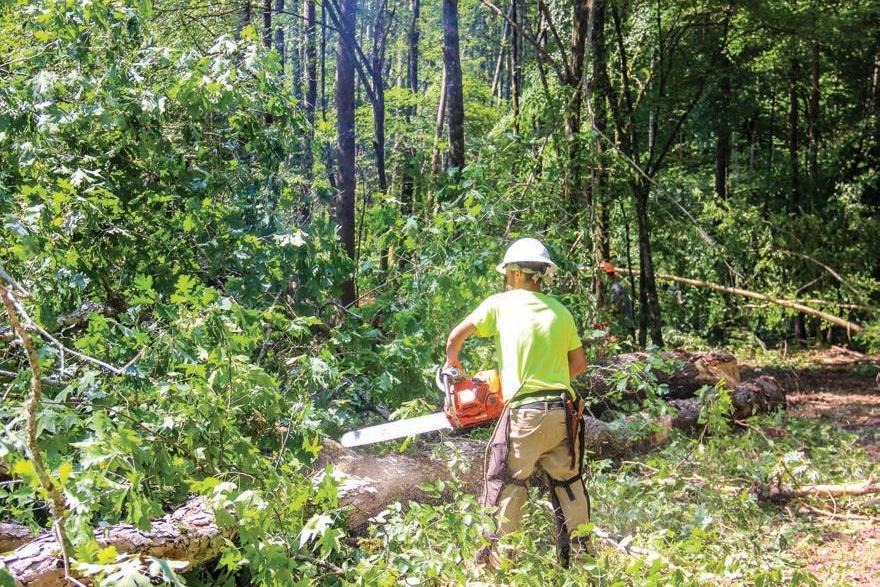


Spotlight On: Transportaion
SLT invited manufacturers/dealers of forestry transportation products/services to submit information about their offerings.
American Truck Parts

American Truck Parts, Inc., established in 1997, located in Douglas, Ga., is a worldwide supplier of new and used heavy duty truck parts. We specialize in used and rebuilt engines, transmission and rear ends. We also carry body parts including a full line of new and used hoods. We clean DPFs for trucks and heavy equipment as well. Our full service shop also repairs, balance and manufactures drive shafts. Our heavy duty wreckers and lowboys provide 24-hour service. Owned and operated by staff formerly in the timber business, we appreciate loggers and understand the business. Check out our website at americantruckparts.com to search our inventory or call us with your truck part needs at 888-383-8884.
Big John Trailers
Big John Trailers has been manufacturing some of the finest trailers for the forest industry since 1973. Because we have been around longer than many of our competitors, and because of the fact that we work directly with loggers on design and customized options, Big John is the obvious choice for your log trailer, loader/delimber trailer and lowboy needs. Products offered by Big John include log trailers, lowboys, knuckleboom loader trailers and self-propelled loader carriers. These products are marketed mostly by a dealer network throughout the United States and Canada, with the strongest market area being in the Southeast. The log trailers offered by Big John cover a wide range of designs. However, the most popular are the “Full Load Series,” or lightweight, low profile plantation and four bolster styles. Lowboy trailers manufactured by Big John range from 10-ton tagalong style to 50-ton fixed neck lowboy style models. The standard lowboy for most loggers and contractors is the 35-ton fixed neck lowboy. All log trailers and lowboys come standard with unimount hubs with outboard brake drums, D.O.T. spec lights and reflective tape, radial tires, and one of the best warranties in the business. Big John also offers custom building for those customers who have special trailer requirements. Loader trailers and self-propelled carriers are another very important part of Big John’s product line. These trailers are primarily sold to equipment dealers and range from a basic chassis to more complex designs to handle heavier loaders and delimbers. After over 30 years of manufacturing trailers, Big John has become a well-known name in the logging industry and continues to manufacture at its facility in Folkston, Ga. For more info, call 912-496-7469 or 1-800-771-4140 or email info@bigjohntrailers.com.
Carter Enterprises
Carter Enterprises, LLC specializes in truck and trailer on-board scale systems, roll over tarping systems, fabrication, and welding repair. We are an authorized Vulcan and SI on-board scale dealership. We are also an authorized Roll Rite automated covering system, Shur-Co tarping system, and Mountain Tarp tarping system dealer. We have expanded and now have two locations in Alabama: in Grove Hill, Ala. and Stanton, Ala. We have also developed an online store (carterscalesandtarps.com) for all our customers from across the United States to purchase any part they may need! We want online shopping to be easy for this industry. We also offer free shipping on all

SI and Vulcan scale parts in the United States. We try our best to keep everyone in the logging and trucking industry moving no matter where they are. Our employees are greatly experienced in tarping system installs and servicing them when needed. Carter Enterprises also has experienced employees in the welding and fabrication field and will always make sure the customer is satisfied with their work before they leave. We hope you are interested in the services we provide for not only our local customers but also new and distant customers. Thank you for your time and we hope to hear from you soon!
FMI Trailers
Fryfogle Manufacturing Inc. was established in 2018 under the operation of Gordon Fryfogle as president and Larry Williamson as sales manager. Together, they have over 65 years experience in the forestry trailer market. Located in Lucedale, Miss., FMI carries a full line of new and used trailers as well as parts and is an authorized Vulcan and SI on-board scale dealer. Please visit FMITrialers.com for photos and standard specifications, or call Gordon at 601-508-3333 or Larry at 601-508-3334.
Kaufman Trailers
Since 1987, our products have become the standard of excellence for the industry. If Kaufman sells it, you can depend on it being the best value available. Our rigorous internal standards as well as NATM certification assure you of a durable, long-lasting, great investment. We specialize in the following:
Gooseneck—We offer gooseneck trailers in multiple types. These include a flatbed version with the floor over the tires, equipment hauler style with fenders, and tilting deck in both deck-over and floor between the fenders configuration.
Flatbed—We define this family as a trailer having the floor over the tires. These models start at 14,000 GVWR with electric brakes and go up to our 62,000 GVWR tri-axle air brake model.
Equipment—All our equipment trailers have fenders and swing-up ramps in ratings ranging from 7,000 to 17,000 GVWR. With our extensive range of models, we have an equipment trailer to fit every need.
Dump—Low profile dump trailers are available in bumper pull and gooseneck hitch options. Weight ratings range from 10,000 to 17,000 GVWR.
Heavy Haul—We offer a full range of heavy haul products ranging from 30-ton capacity lightweight commercial trailers up to 55-ton commercial trailers and everything in between.
Logging Trailers—We offer a full range of forestry trailers with about any option you can dream up: 2-axle, 3-axle, plantation, straight frame, sliding bolsters, scales, multiple suspension styles, the list goes on and on. It will be hard to find something we can’t do.
Kaufman Trailer’s friendly, specially-trained customer service staff can help answer your questions and assist you in finding the perfect trailer for your needs at a price you will love. Call 336-790-6807 or visit kaufmantrailers.com for more.
Magnolia Trailers
Established in April 1993 to service the forestry and equipment hauling industry, Magnolia Trailers Inc. builds all types of forestry, logging and equipment trailers. We also offer a complete line of conventional pole, loader, delimber or your own specially designed trailer, including a great inventory of used trailers. Principals Robert and Connie Langley welcome you to call today to discuss your equipment needs. Call (601) 947-7990; toll free: 800-738- 2123; fax: (601) 947-4900; e-mail: info@magnoliatrailers.com or visit magnoliatrailers.com for more.
Maxi-Load Platform Scales

free. They come with a comprehensive 2-year warranty. We have 24 years of proven performance weighing log trucks. The first scale we built in 1996 is still weighing log trucks daily. Our scales are working on over 800 logging jobs throughout the southeastern United States.
Mills only pay for what crosses their scale. Under-loaded trucks are a missed opportunity. A fully loaded truck would have paid more money. Overloaded trucks are a liability. If one has an accident you can be dealing with a serious issue. Tally your weekly load tickets. What tonnage did you get paid for? What could you have been paid for? The difference between being almost loaded and fully loaded: about $1,000 per week.
A Maxi-Load platform scale can be installed on your job in two hours. From that point on you can safely maximize the payload on every truck serving your job, your trucks, and contract trucks. Financing is available. Delivery and installation are part of the sale. Contact your forestry equipment supplier or Maxi-Load at 1-877-265-1486 or on the web at Maxiload.com.

Pitts Trailers
For decades, Pitts Trailers has pulled the industry forward with innovative designs and high quality products built for optimal performance. According to President and CEO Jeff Pitts, every innovation, every manufacturing advancement starts with a single person in mind—the customer. “The people who use our trailers go to work every day in one of the toughest, most demanding industries,” Pitts explains. “Our number one goal is to supply them with high performance trailers to make their work as efficient, convenient and safe as possible.”
The most recent Pitts innovation, Lock ’N Go landing gear was introduced in 2018 to significantly enhance operator safety and convenience.

The four-pin auto-lock system allows a driver to easily ensure that both sides of the landing gear are securely engaged without circling or crawling under the trailer. It also helps secure the load and protect the trailer from unnecessary wear and tear.
The pioneering Load Payin’ Series, introduced in 1994, is the number one selling logging trailer in North America. This line introduced a fully fabricated frame made of high-yield materials with a continuous submerged arc welding process, allowing customers to haul more wood and less steel, while maintaining the highest performance standards available in the industry.
Pitts revolutionized loader carrier manufacturing with the development of Crawler Suspension, providing the smoothest, most stable transport available for safety both on- and off-road. The military-derived, patent pending design delivers double the ground clearance of traditional spring singlepoint suspension. And the rocking beam construction eliminates spring bounce effect, protecting the load from unnecessary impact and vibration.
Family owned and operated since 1976, Pitts Trailers is the world’s largest and only complete-line forestry trailer manufacturer. Pitts offers a wide variety of truck trailers, including logging trailers, hydraulic elevating loader carrier trailers, open and closed top chip vans, moving floors vans, hydraulic removable neck lowboys, fixed neck lowboys, hydraulic folding tail lowboys and construction grade tagalong lowboys.
“Pitts Trailers has made many contributions to the industry over the years,” says Pitts, “but what we’ve really done is take care of our customers.”
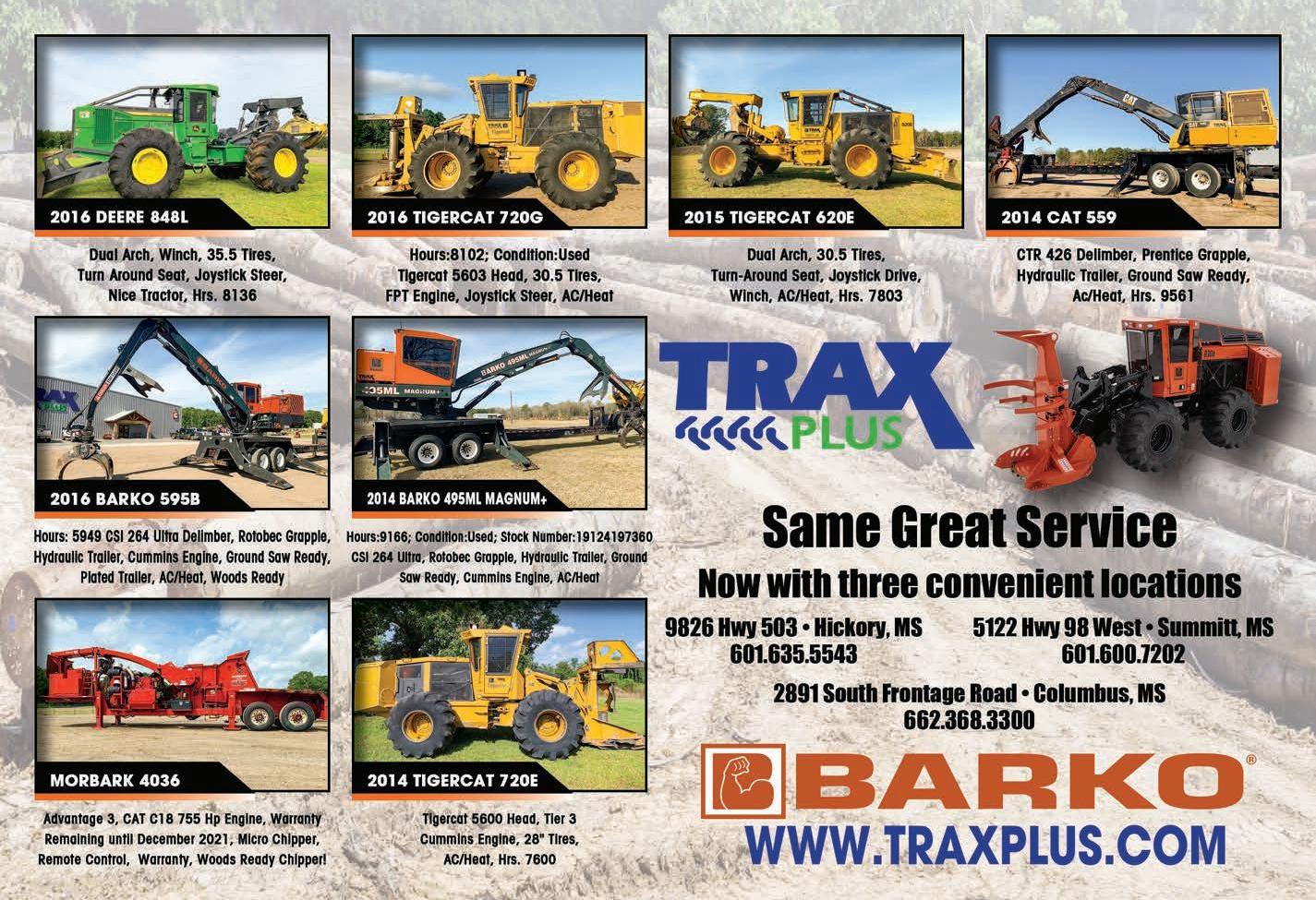
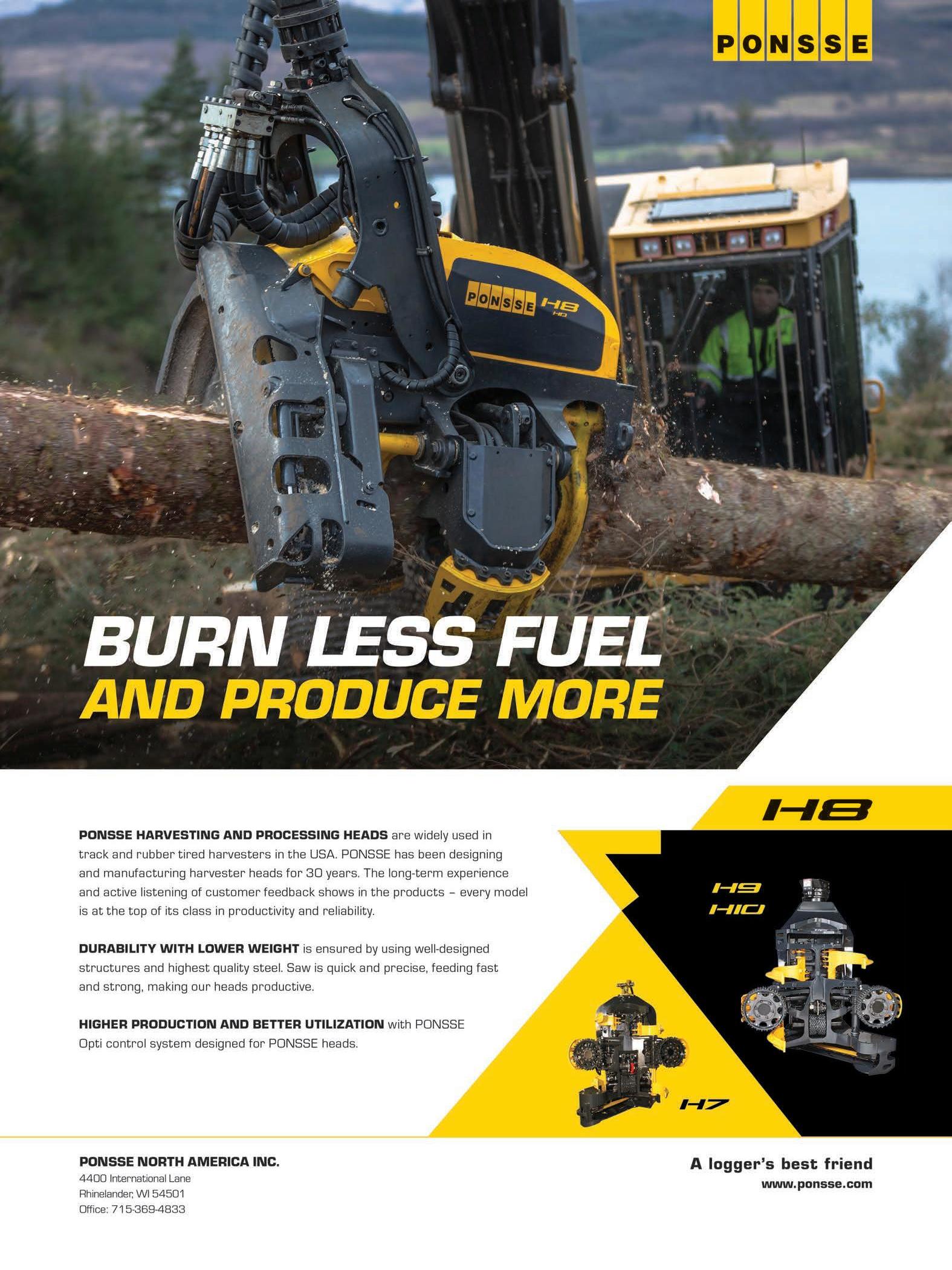