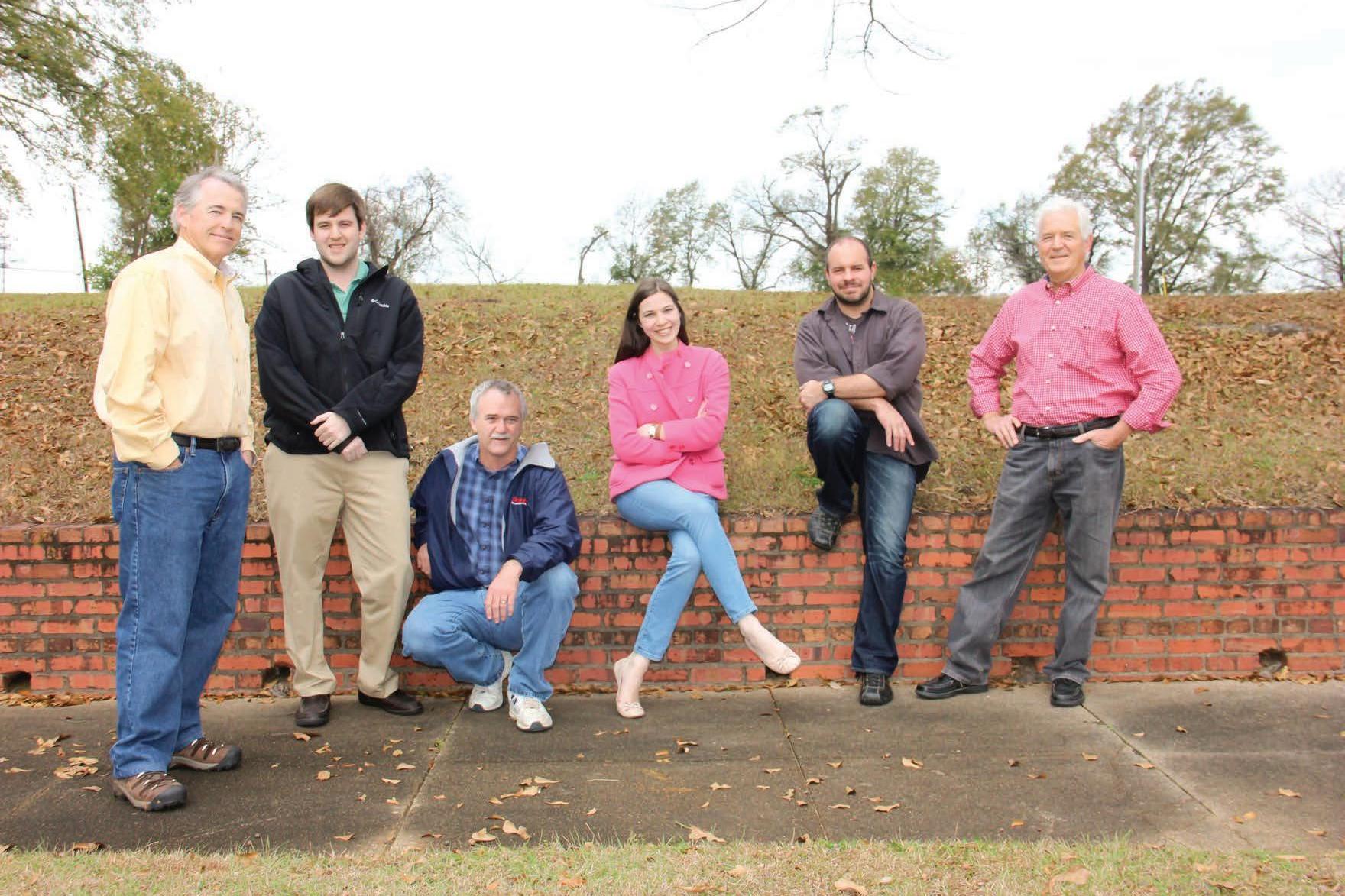
30 minute read
Stumpin’
SOUTHERN STUMPIN’
By David Abbott • Managing Editor • Ph. 334-834-1170 • Fax: 334-834-4525 • E-mail: david@hattonbrown.com
Odds And Ends
As we do in every December issue, to end the year, let’s take a look back at some of the best quotes we’ve printed throughout 2021. Merry Christmas, Happy New Year, and see you in 2022. Excelsior!—Dave
“I had a fellow who worked on my stuff as long as I have been in business, an independent contractor. But he died in 2018, and I realized then there are no more mechanics out there. It dawned on me that I had to start keeping everything under warranty.”—Charlie Carden, Carden Timber Harvesting, LLC, Orchard Hill, Georgia, page 10, January issue
“If a man will work then he’s all right in my book, or it will give him the opportunity to be around me long enough for me to find out if he’s all right. The way these guys work reminds me of how people used to work when I was growing up. These boys look after me; if I had a crew like this when I started there’s no telling where I’d be now.”—Carden again, page 14, January issue
“When I get to where I can’t get up and do what I need to do, I’ll retire. I can still run with the best of them, but Mother Nature will let my body know. I don’t ever want to not do anything.”—Robert Kirby, Kirby Sawmill, Inc., Doniphan, Missouri, page 16, January issue
“Some of these guys seem like they make pretty good money buying their own wood, but I tell you, this business, you ain’t gonna get rich doing it the way I’m doing it. I love it, I reckon. I’ve thought about it and I can’t think of anything I’d rather be doing. If I had to do it the way my dad and uncle and papaw had to do it, I wouldn’t be doing it or I wouldn’t love it near as much, I promise you.”— Chris Cates, W. Cates Logging, Bremen, Alabama, pages 12 and 14, February issue
“One thing I try to do is take care of my men. God told me one day, ‘If you take care of your men, I’ll take care of you.’ And for the most part I have had some good workers over the years.”—Dennis Wiseman, Wiseman Logging, Niota, Tennessee, page 9, March issue
“You’re still going to have wear and tear on the machines, either way. I am not going to make payments and work on the machine. I am going to pick one of the two.”—Russell Scott, Coastal Forestry Services, Marianna, Florida, page 8, May issue
“We purpose to work. Our dad taught us two things can never be taken away: faith and work ethic.”—Chad Schwab, M.A. Rigoni, Perry, Florida, page 20, May issue
“An old school logger mentality would be, you have a log truck and you drive it till the doors fall off. We just got rid of a 1986 chipper. We had parts in here for that, and we haven’t run that chipper in 10 years. You can’t afford it today. It’s overhead, and it’s overtime sometimes. If you think you might need three mechanics one day but you really only have work for one mechanic, you still got those other two you’re paying just because of that one time you might need them. You have to cut all that out to make it work.”— Chad Schab again, page 21, May issue
“We haven’t been one dimensional in many years. We were raised not to be and have taught everyone under us to be flexible. We try to keep as much diversification with our footprint as we can, and we have a huge footprint today.”— Chad’s brother Richard Schwab, also of M.A. Rigoni in Perry, Florida, page 22, May issue
“You start off Monday morning with Plan A, by the time Friday gets here, you’re working on Plan AAA; you’ve been through the whole alphabet, A-Z, twice. How often do you have to reinvent yourself? Almost daily.”—Chad Schwab again, page 24, May issue
“Our passion, and who we are, we were trained in school to make a difference, not just for our little kingdom but to make the world a better place. Our company spends a lot of time and money being involved with making policy for the industry nationwide. But I see that as an investment for loggers everywhere. I wouldn’t put a price on it. The commitments I have with all these organizations, you would be surprised how much business value I get out of that. I’m out developing new business.”—Richard Schwab again, page 28, May issue (still)
“I was freaked out. I was scared. I didn’t know anything about what goes on out here in the woods. I was nervous about it. You have to have a confidence in the people who are running the machines. It is hard to get good people who want to do anything. To have a good crew is essential to running a logging operation, and I feel like I have some of the best.”—Samantha Bull, Bull IV Logging, Fouke, Arkansas, pages 8-9, June issue, on taking over the business after her husband’s death
“We were just trying to survive. Our production was down about 60% in the middle of March (2020). I just tried to maintain and keep our workers on the payroll with some cash flow. It was hard to make it each week and a big difference in volume when you’re used to pushing 60,000 ft. weekly. We should have been in high production putting back for the winter months, but it wasn’t there. I have a feeling things are going to get better and I’m going to be ready when they do. We’re going to put the hammer down.”—Brandon Brock, BBrock Enterprises, LLC, Mayking, Kentucky, pages 14-16, June issue, on the pandemic-related difficulties he faced in 2020
“It won’t take but one thing to move me and that’s money…I don’t mean this in a smart aleck way, but I’m not going to work if I can’t make any money. If people see me going there, they know there is money there. All I am interested in is dollar bills with ‘In God We Trust’ on it.”— Donnie Reaves, Donald E. Reaves, LLC, Coleman Falls, Virginia, page 19, July issue
“I think you either have to be pretty small or pretty large. The middle man has a whole lot of the same expenses as the big man but doesn’t have the income. If I pay too much for the timber then I’ll be out of business. If you price yourself so close you can’t make any money, whose fault is that? We don’t need twice as much money as we are making, but the industry needs to pay us 10-20% more. But as long as somebody will work for nothing, they’re not going to do it. So we are kind of our own enemy. There is plenty of work out there for all of us. I wish for anybody working hard and trying to treat people right to do well.”—Reaves again, page 22, July issue
“I look at it in the long run: if we destroy the Earth, what are my boys going to cut 40 years down the road?”—Michael Hutchins, Hutch Trucking, Inc., Livingston, Alabama, page 8, August issue
“We prefer to buy our own wood; that way we can control where we haul our wood to maximize production. Some of the bigger timber companies beat prices down so much there’s not much skin left. You can make a living contracting but you’re not going to make money.”—Rickey Pitts, Pitts Logging, Inc., Waycross, Georgia, pages 13-14, August issue
“She pinches pennies and makes dollars out of them.”—Greg Lovorn, Lovorn Logging, Slate Springs, Mississippi, page 22, September issue, on his mother Suzye
“My motto is that I try to make the money in the woods and keep it in the office. Always try to find a better deal on things.”—Bradley McDowell, Pineland Contracting, Jena, Louisiana, page 9, December issue
Happy Holidays from SLT
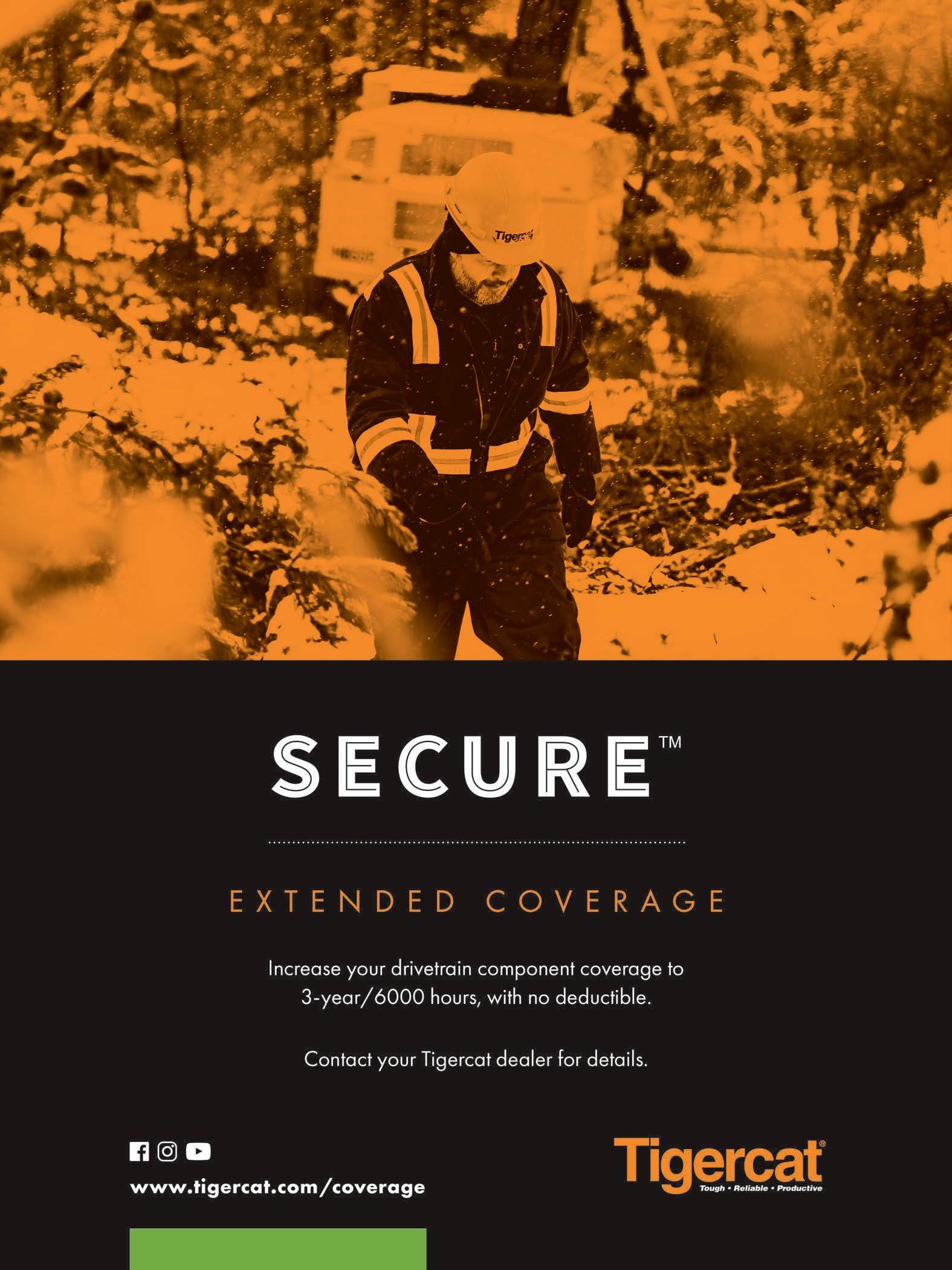
Middle Ground
■ Louisiana’s Bradley McDowell stays the course—while using innovative machinery.


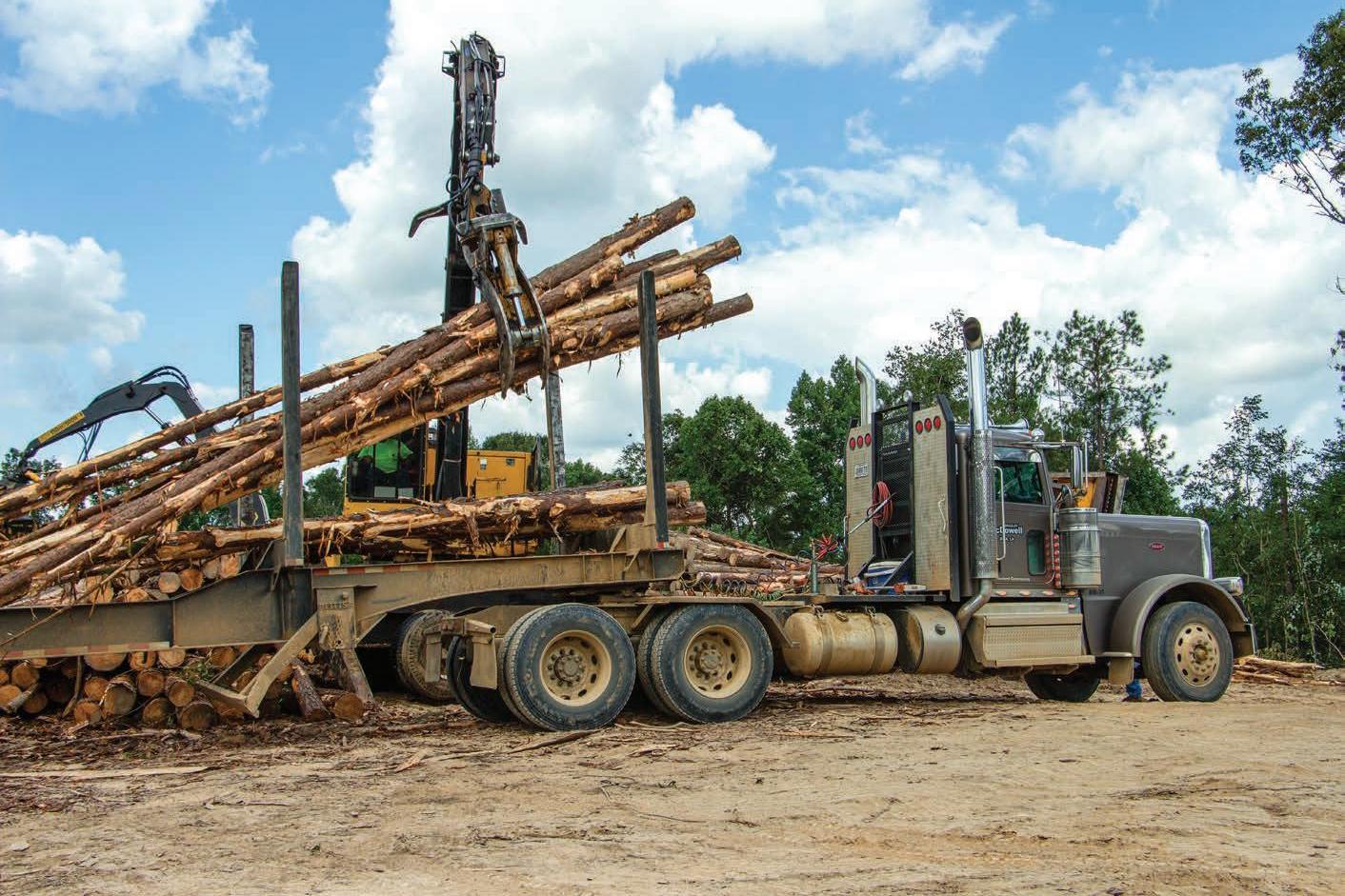
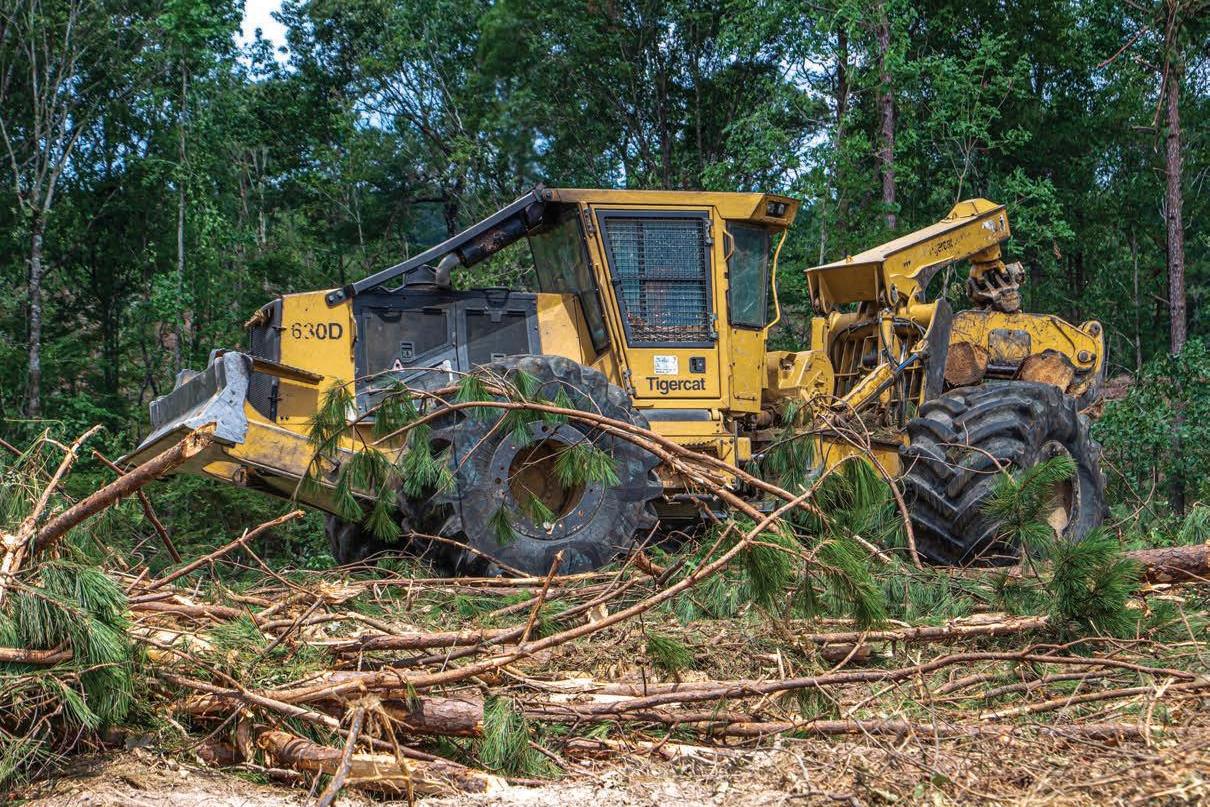
McDowell's crews use 234 Tigercats to load trucks and 250s with dangle heads to process stems.
By Jessica Johnson
JENA, La.
When Bradley McDowell started logging in 1992, he didn’t know he would be considered an innovator. But after a trip to the Canadian Rockies in 2004, and an introduction to “dangle head” machines, McDowell knew he wanted to do things a little different down in Louisiana. It surprises him that the processor machines never caught on in the South—but after he thinks on it, he knows why, he says. “It is the investment: You can buy two loaders for what one of these costs. But you eliminate other costs,” he adds. “This thing will take the place of three loaders, and I thought it might catch on. It makes logging so much easier.”
McDowell operates by looking at tons per man that the crews produce. Because of the dangle head processor, each man on the fourman crew puts out at least 20,000 tons. “Everything else is irrelevant,” he believes, saying that looking at the tons per man in the woods tells truly how efficient an operation is; it will show how many skidders are needed, trucks, everything. It was a lesson McDowell learned years ago and has helped him greatly.
“My motto is that I try to make the money in the woods and keep it in the office. Always try to find a better deal on things,” he says. Sure, a better deal means cheaper fuel or better rates on insurance, but it also means truly maximizing production of men and machines.
Running a tight ship in the office, assisted by his wife Leslie, helped McDowell weather more than a few storms, including the housing crisis in 2008, where he made the hard decision to shut down McDowell Logging Co. Thanks to not just borrowing the Canadian way of using machinery, but also the idea of running a double shift crew, cutting and hauling both in the daylight and at night, McDowell was able to pay off his equipment faster and bring it all home when the crisis hit its rock bottom. “We shut down for three years because we were hauling 35 loads per day, and then they cut us to 10.” He says that forced his hand financially. “Being diversified is the only way we survived.”
His diversification stream— Pineland Contracting, which prior to the logging restart was simply a sister company to McDowell Logging—is a road and bridge operation that works primarily for timber companies. Now, Pineland Contracting is the umbrella for both the road and bridge crew McDowell’s son runs and the logging side that McDowell looks after. “I am a logger. But we’ve been doing that for 20 years. It kept us afloat a lot of weeks when the logging didn’t float,” he says of the construction.
After the restart, Mc Dowell purchased all new equipment, and it drove everyone crazy. Suddenly they weren’t able to work on machines like they were used to and things just weren’t as smooth. So, they made a change again, finding pieces the woods crew could maintain themselves aided by a fulltime staff mechanic. McDowell purchases late model used pieces; nothing in his registry is older than 2016. When the crew needs something, they go to a variety of sources, including dealer Gaar Equipment Sales. Processors are still purchased new from Tigercat dealer Patrick Miller.
He explains, “I feel like we got to
Bradley McDowell
Machines are purchased from a variety of sources.

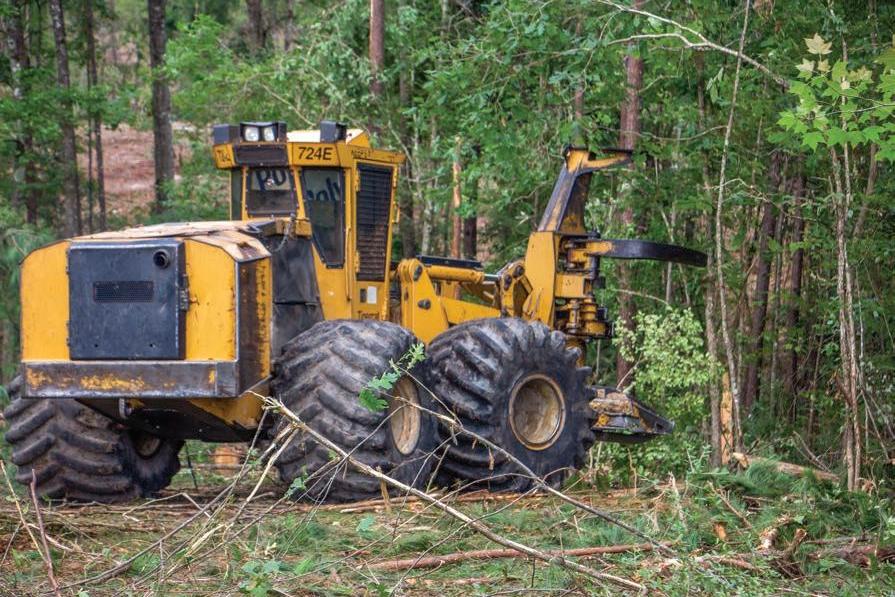
Both crews target 18-20 loads a day.
a point where you’re paying more to the parts house than you are equipment notes…But if you finance it for 48 months, you’re going to be dealing with breakdowns anyway. So we would rather be able to work on it ourselves.”
In The Woods
The two woods crews are set up identically, with four men and four machines. They have access to a floating skidder. McDowell’s crews are mainly younger, with both foremen being in their early twenties, one being McDowell’s nephew. “They all want to work and they will get it done. I pay them well and we work for good companies,” he says of Weyerhaeuser and RMS. “They’ve got timber; they’ve got ground and they’ve got the market. If it wasn’t for these employees, I wouldn’t be in the logging business.”
McDowell has taught the crew to be as mindful of production as he is—making it almost like a competition between the two crews as to who gets the most. The two crews share trucks and the floating skidder, but McDowell says sometimes there is some jawing back and forth over trucks, especially on close hauls or weeks with tight quotas. “I’ve heard it, ‘Oh no, I’m not sending you a truck today!’ We have a lot of fun,” he adds, “They make the day go by.”
Set up with the same equipment, the desire to outdo each other is natural for the younger men. Depending on the timber and haul distance, the number of trucks might change, but the woods equipment is all Tigercat and all the same. The crews use 724 feller-bunchers, 630 skidders, 234 loaders and H250D model “dangle” harvester head processors. With this set up the crews consistently hit their target of between 18 and 20 loads per day. Once, McDowell proudly says, the crew was able to put out 35 loads in a single day running just six trucks—all because of the processor. If the markets would support it, McDowell says he would go back to double shift logging in a heartbeat. “This is the world we live in now,” he says. “That’s the thing about a big crew and having 10 trucks and gear up to haul 100 loads a week: There’s not enough stability in it. We’re in the middle and that’s our little comfort zone.”
Like most, the crews try not to leave the woods for anything during the day. Each foreman drives a ¾ ton
pickup that hauls fuel and at the landing is a “doghouse” trailer with a welder, compressor and hose machine. What the woods hands can’t fix themselves, the crew mechanic will handle, or one of a few contract mechanics. McDowell notes that one benefit to using Gaar Equipment for their used needs is the dealer’s mechanic—and they will stand by their machines if there are ever any problems. A dozer is kept on each crew to assist with roads, BMP work and other odds and ends.
McDowell says succinctly, “Logging has been good to us.” SLT
Trucks float between the crews
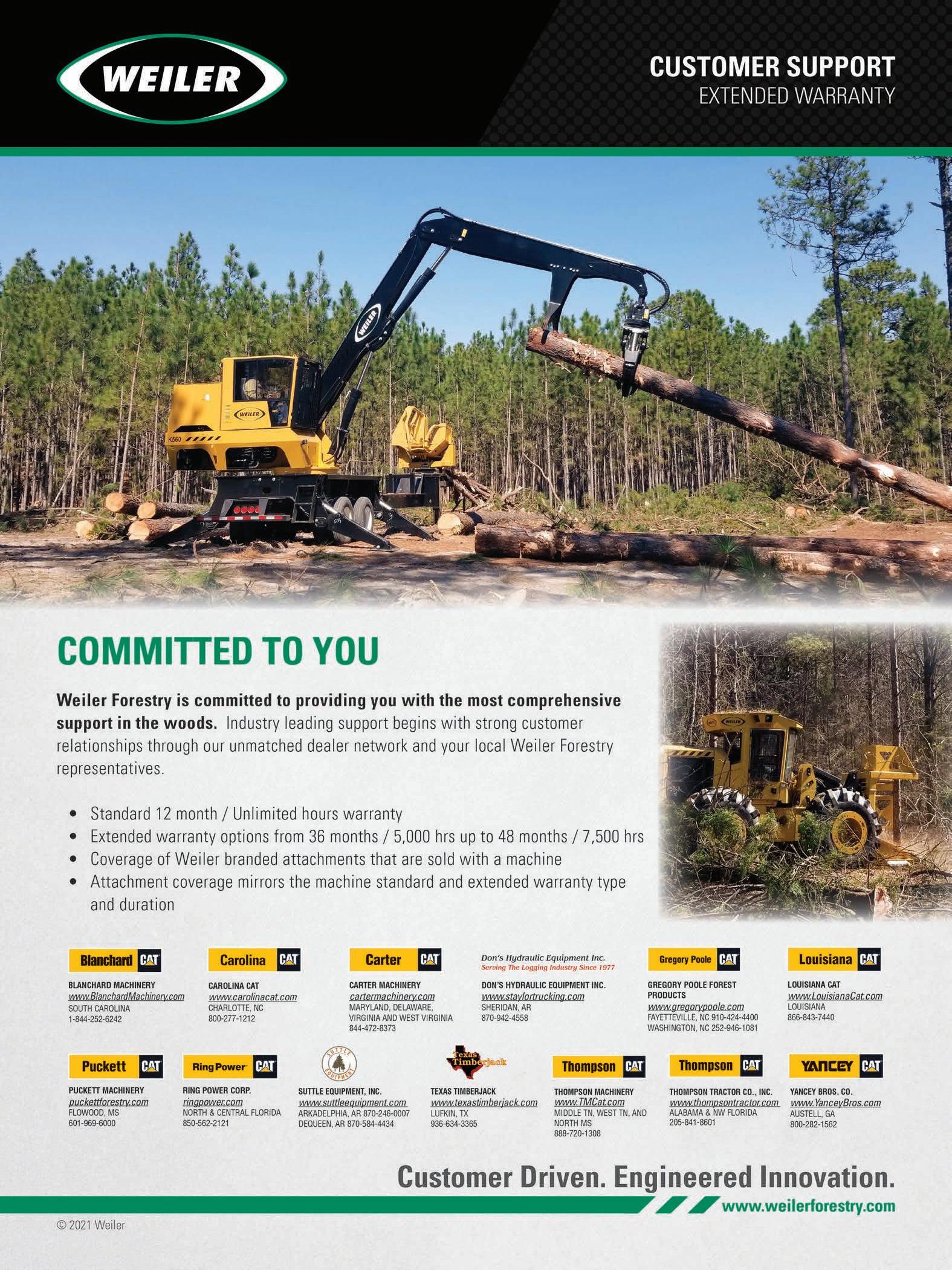
Bright Horizons
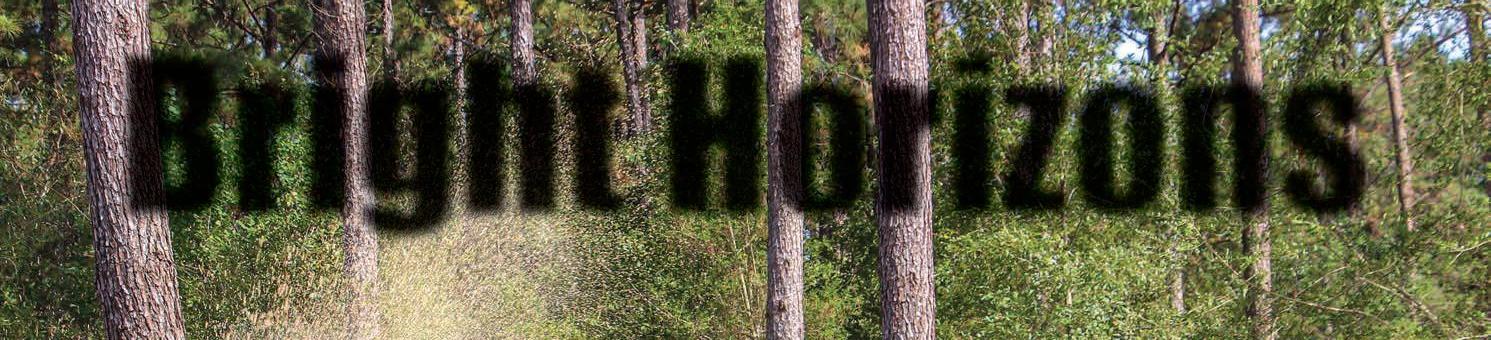
■ Upbeat and optimistic, logger Anthony Stuart offers his forecast: clear skies ahead.
By David Abbott
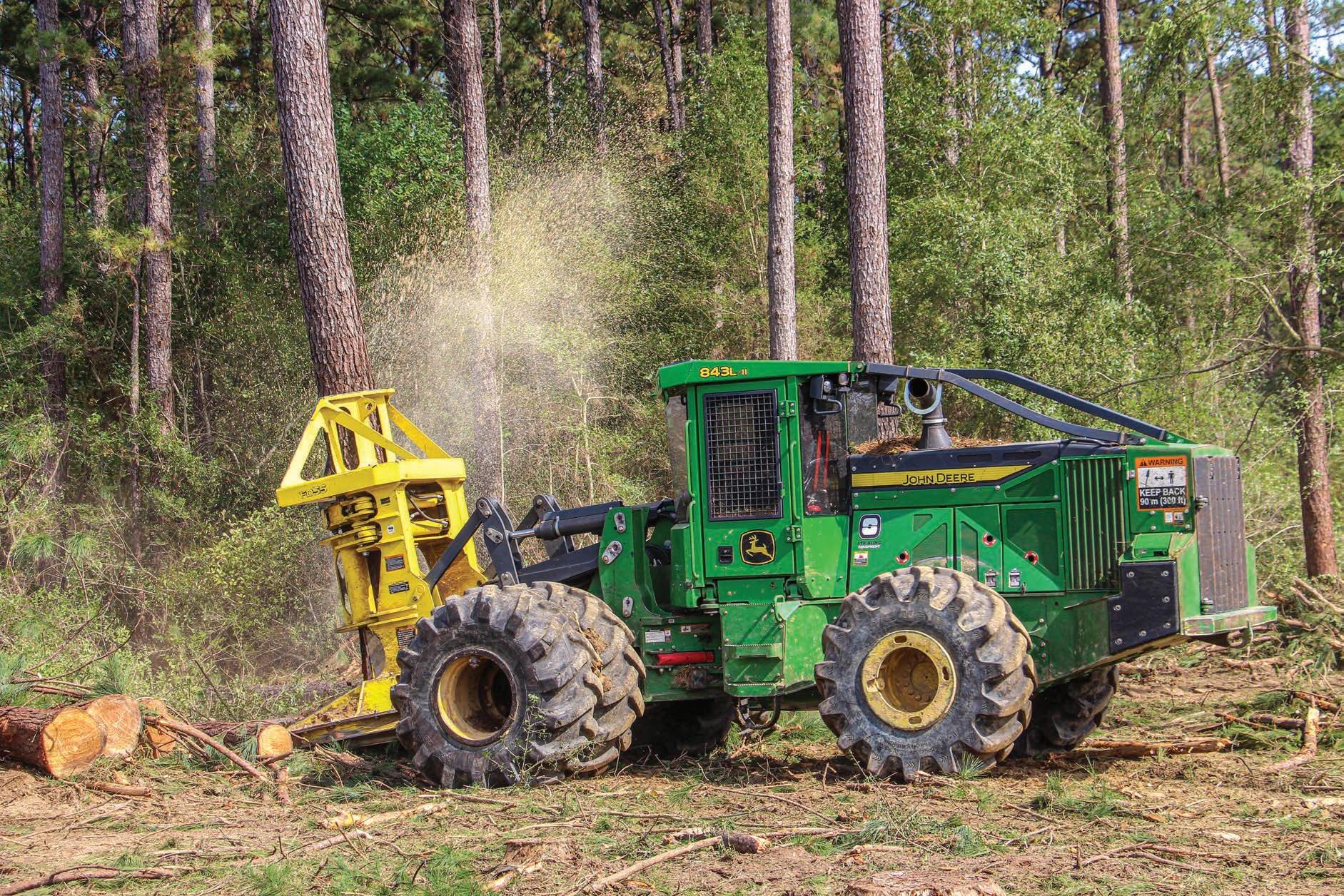
CARSON, Miss.
Espousing a sunny outlook somewhat the opposite of what might be more typically found among many of his peers, Anthony Stuart, 48, clearly has a positive outlook on the state of the industry these days. “I have never been a doom-and-gloom type person,” he admits. “There have been some good times and some bad times but with the weather how it has been and mills needing wood and talk of new mills coming online, it is kind of exciting right now to see what is going on. I really think there are good things to come.”
As if reflecting the logger’s optimism, the weather was calm and the skies bright and clear on the unseasonably warm early November day when Southern Loggin’ Times came calling. In Stuart’s words, “It’s a good day to be here.”
The owner of Stuart Timber, Inc. points out that there are several new or recent mill projects in various stages of development in his neck
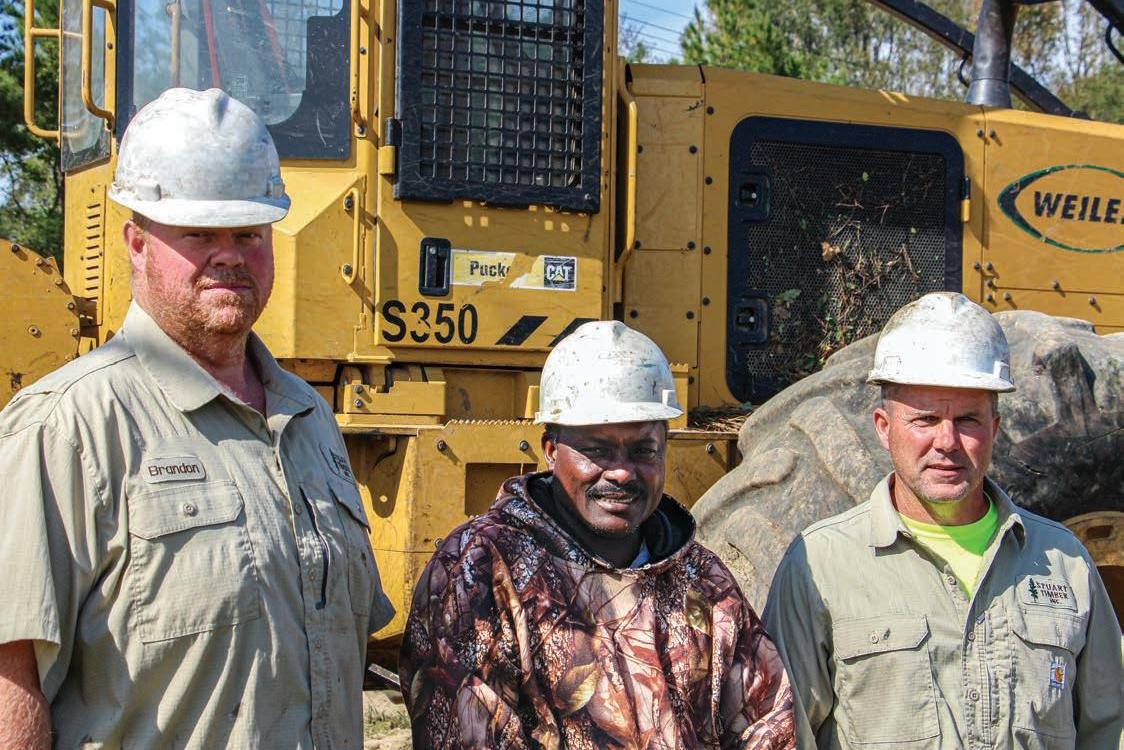
From left: Brandon McRaney, Charley Buckley, Anthony Stuart
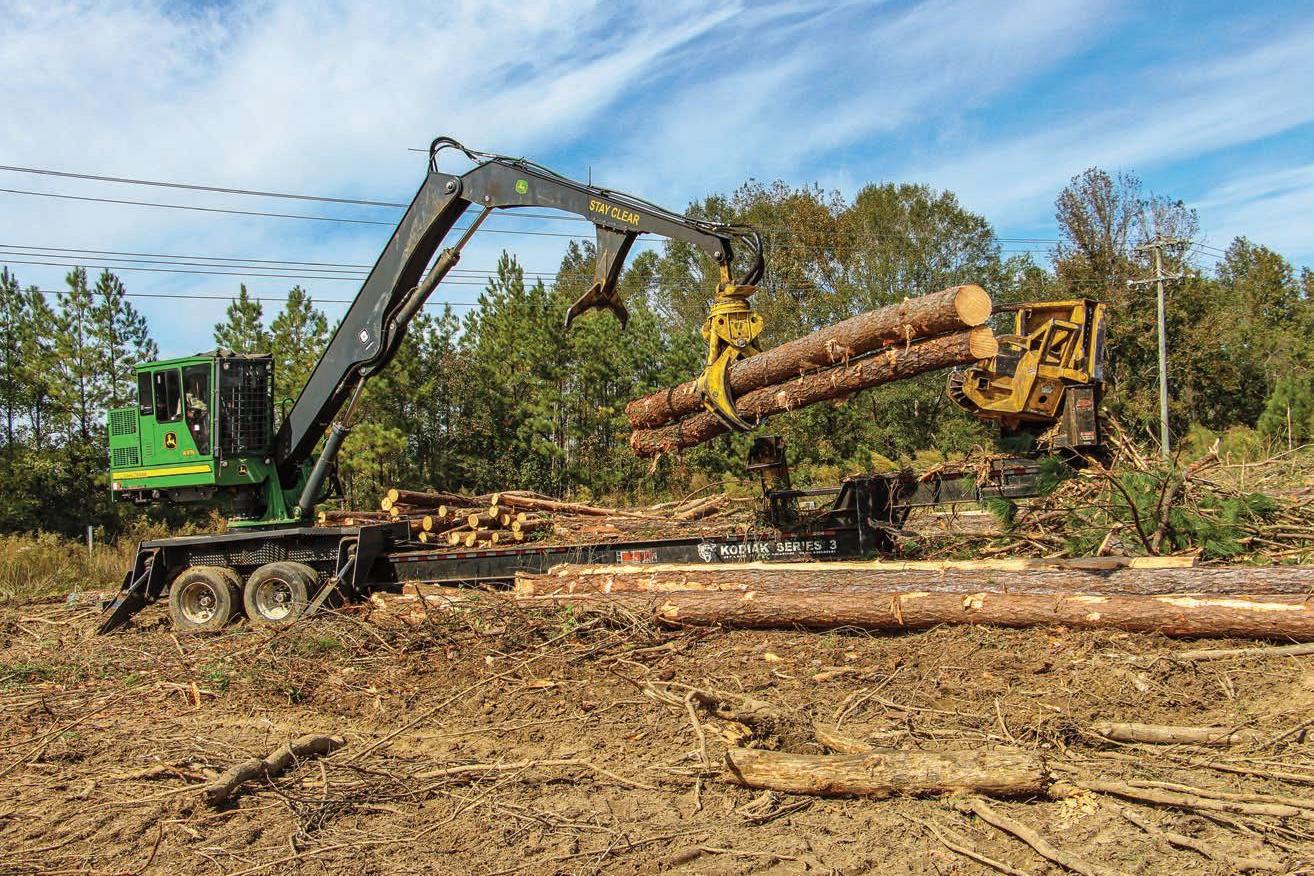
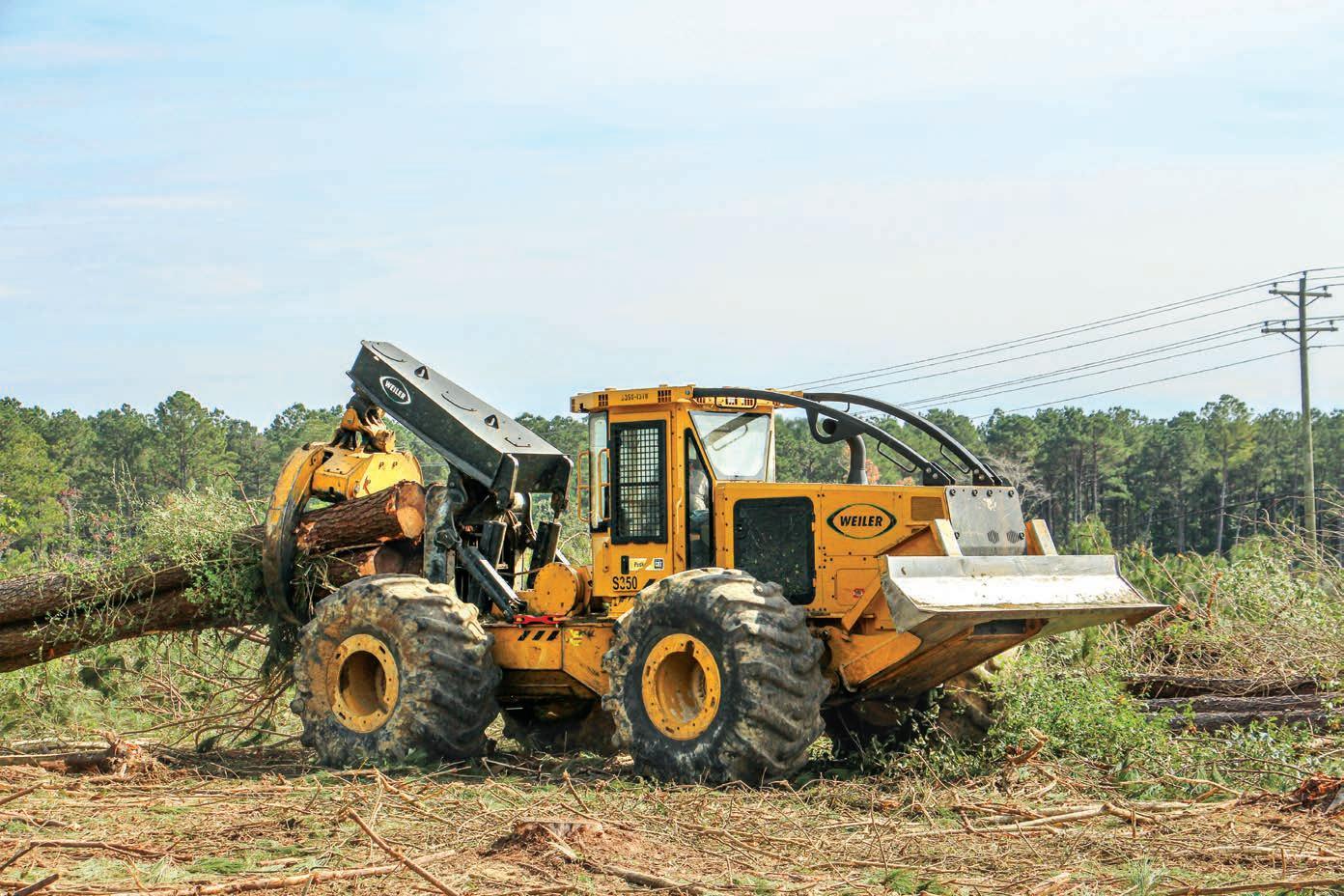
of the woods: Idaho Forest Products in Lumberton, an Enviva pellet mill in Lucedale, some others further north of his territory, not to mention that a lot of the existing mills are talking about expanding. If all that new mill capacity presents him with an opportunity to expand his operations, he wouldn’t expect to turn the chance down.
Record high lumber prices might not have trickled down to bring up logger incomes much, Stuart admits, but he adds, again looking on the bright side, at least the high demand from mills is keeping them busy. “We have been six days a week probably for the last two months now, all we can haul,” he reports.
Equipment
Stuart Timber fields two crews. One features a John Deere 648L-II skidder and 437E loader with a Tigercat 720G cutter. The other crew uses a John Deere 843L-II feller-buncher, only a few months old, another Deere 437E loader and Weiler 350 skidder.
Stuart bought the Weiler about a year and a half ago, shortly after they became available; he thinks it was the first one Puckett Machinery at Hattiesburg sold. “We had a Cat skidder years ago, but we mainly have been John Deere, and Tigercat every now and then,” Stuart says. “We needed a skidder and at the time Weiler was available, so I decided to try it and see.” His experience with Weiler has been good so far, he reports. “It is engineered well. When they first started talking, before they even bought them, Mr. Hood (Weiler VP Bill Hood) came out to my job site and we sat there and talked probably an hour. He seemed like he was interested to know what loggers wanted and I think they are headed in that direction.”
The crews also use a Deere 648L skidder in reserve, keeping it set up with dual tires year-round so that it is ready to go when they need it. “This area has a lot of sensitive areas,” the logger explains. For either crew, Stuart keeps Caterpillar D5 and D6 dozers for road building as well as site prep and maintenance. They have Husqvarna pole saws and Stihl chain saws, though they haven’t done much hand felling in a long time.
Stuart buys Weiler and Caterpillar from Puckett and Deere from Stribling Equipment, both in Hattiesburg, while he looks to B&G Equipment in Magnolia for Tigercat sales and support.
Stuart always orders his cutters with the center of the wheels offset so the tires sit closer to the machine; that helps clear the narrow corridors in thinning applications, he believes. “We started doing that years ago,” he says. On skidders and loaders, Stuart prefers bigger grapples; he recently
Stuart was impressed with Weiler's interest in logger input.
Stuart Timber has been primarily a John Deere customer, with some Tigercat in the mix.
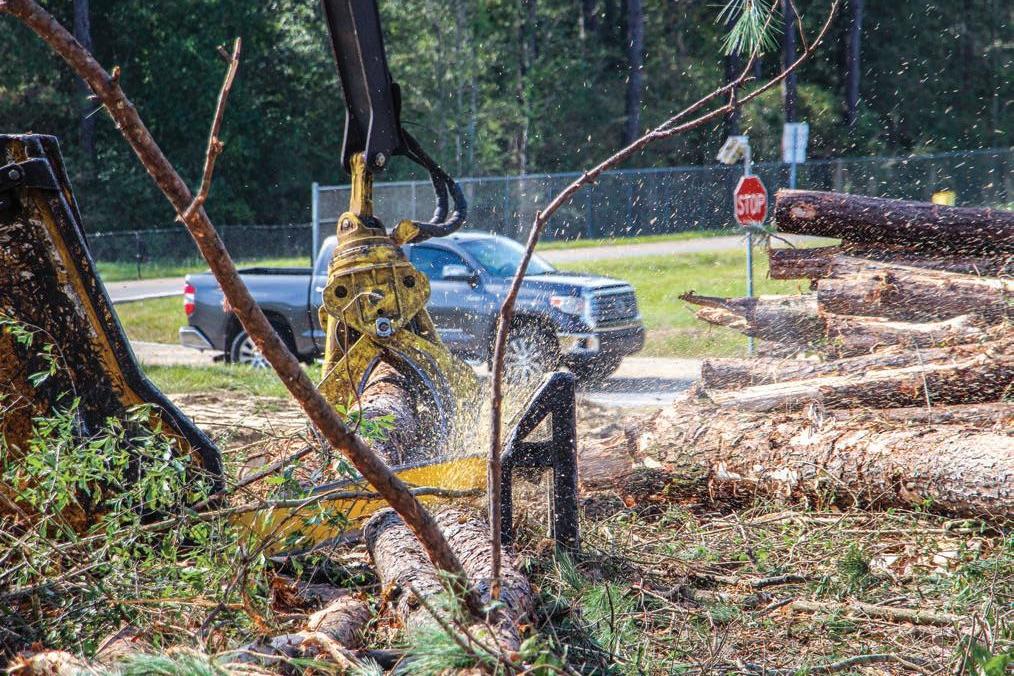
Both Stuart crews work mainly in pine.
Stuart uses Samsara dash cams in his trucks.
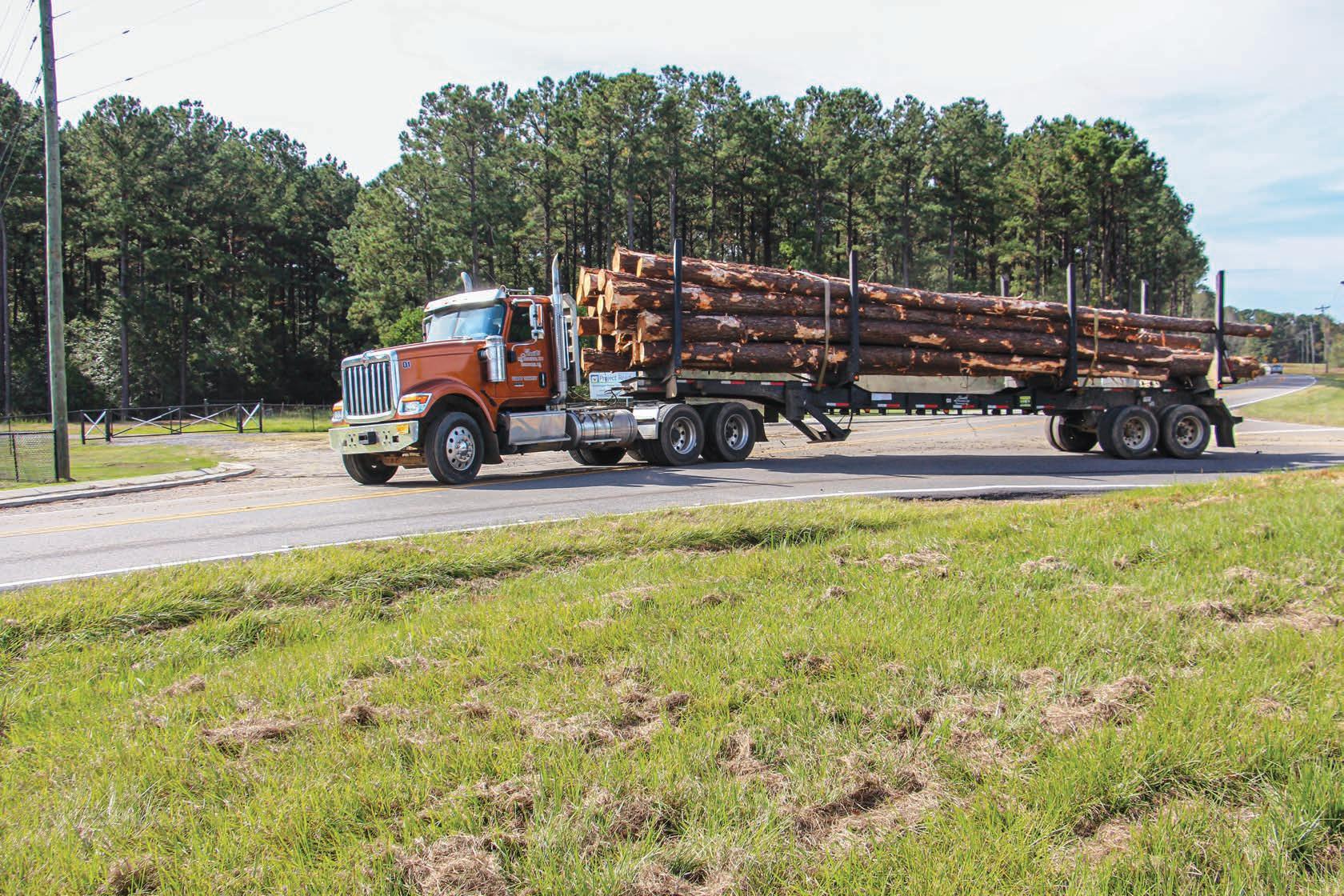
ordered a Deere 748L-II skidder, soon to be delivered, with a 19 sq. ft. grapple.
Stuart’s brother Lewis mans the loader and serves as foreman on one of the two crews. Other Stuart Timber team members include loader operator Brandon McRaney on the crew Anthony supervises with Charlie Buckley on the Weiler skidder (Anthony’s crew), Jamey Norris on the John Deere skidder (Lewis’s crew) and Adam Lucas on the Tigercat cutter (Lewis’s crew). The boss himself often runs the Deere cutter on his own crew.
Hiring truck drivers has long been a challenge for loggers. Stuart has several older drivers who have been with him a while, and a few younger ones too—if late 30s to early 40s counts as young, the logger chuckles. BITCO (Bituminous Casualty Corp.) covers all his insurance needs. The crews hold safety meetings in the woods on the tailgate every week, covering topics and addressing problems as they arise, and they use TEAM Safe Trucking training for their drivers. “You do it so long it becomes a habit so you need to refresh and keep it on your mind,” Stuart notes.
Stuart owns several trucks: five Internationals from Waters International in Hattiesburg, and a Freightliner and a Western Star from Empire Truck Sales in Hattiesburg, pulling Magnolia and FMI trailers (he shops local; both trailer manufacturers are Mississippi-based companies). A cousin also hauls for him on a contract basis. The crews send 120-140 loads a week with both crews combined, usually in a range of 60 miles but sometimes as far as 90 miles to the mills.
Stuart has been using Samsara dash cams and fleet monitoring systems in his trucks for the last few years. The system allows him to access information about the trucks in real time: how fast they’re going, what route they’re taking, and so on.
Timber
When it comes to finding stump age, Stuart Timber works closely with forester Billy Daniels of Southern Timber out of Collins, Miss. “We mostly just cut what he buys for us, but we do buy some of our own,” Stuart says. “We have landowners whose land we have cut on for years, and get repeat business.”
The crews haul pine logs and chipn-saw mainly to the Hood Industries plywood and lumber mills in Wiggins, Beaumont, Silver Creek and Bogalusa. Pine pulp goes to International Paper. On the relatively rare occasions they have hardwood to haul, pulp often goes to Masonite Corp. at Laurel, logs to Jones Lumber Co. in Hazlehurst or Marion County Timber in Columbia, whichever is closest to wherever they happen to be working at the time.
The crews work predominantly in pine, both thinning and clear-cuts, but cut very little hardwood. The tract they were working in early November is a final harvest that will be replanted by the state of Mississippi. Stuart Timber was clearing 150 acres here. On this site, Stuart had some truckloads of sand delivered to help with ground conditions in anticipation of heavy rain. With an eye to public perception, he noted that they were loading right off the blacktop,
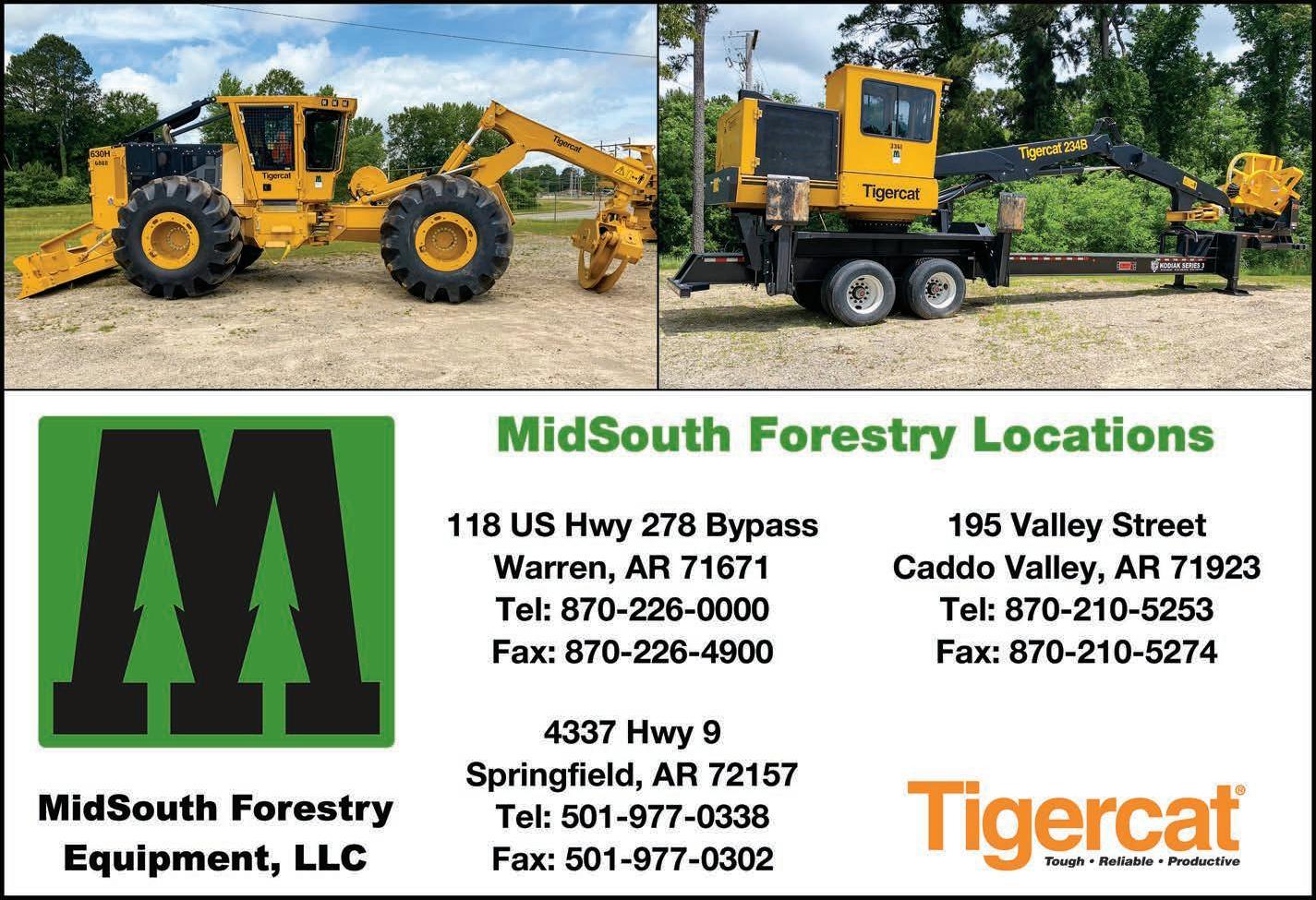

on the side of a relatively high-traffic highway, and he wanted to avoid dragging much mud onto the asphalt. “We just do the best we can to make it look the best we can; that’s about all you can do,” he says. Fortunately, he doesn’t have to deal with too many complaints. “This area is rich in the timber industry, so most folks around here are happy to see (logging).”
The crews did some storm cleanup work in the area last year, when tornadoes came through around Easter of 2020 and tore up thousands of acres of timber. They worked on those salvage jobs till the wood got to the point that the mills didn’t want it anymore.
They had some down time attributable to Covid last year, but were bless ed not to have suffered a tre mendous amount of loss, the logger re ports. “I won’t say it wasn’t bad, be cause it was, but we made it through.”
“I was going to the woods with my dad since way before I should have,” Stuart laughs. “It is just a family thing.” His dad, Harvey, started out stumping with his own brothers and father, and when that played out they all got into logging, and have stayed with it ever since. “It is what we were meant to be, I guess.”
Anthony and his brothers grew up in this area of Mississippi, but they also have ties in neighboring Loui siana. “Years ago when my dad and uncles were stumping, when it played out over here, they went to DeRidder to stump for a while, and some of them stayed over there.” His brother Brian went to Louisiana Tech, married a girl he met there and stayed in the DeRidder area, where he now runs his own logging business.
After studying forestry at Jones Junior College in Ellisville, Anthony bought timber for his brother
Brian in DeRidder for a little while, but decided that wasn’t what he wanted to do with the rest of his life. He went into business for himself in 1999 at age 26.
Anthony has been married to his wife Holli for 23 years. They have four children. Oldest son Tanner, 26, just started his own logging company, Red Stuart Logging; he’s the Stuart family’s fourth consecutive generation in the timber business. Next is Riles, 20, following his dad’s footsteps as a forestry student at Jones Junior College. Hayes is a senior at Col umbia Academy, and youngest brother Carson, 13, is also a student at the private school in Columbia.
The family is actively involved at Greens Creek Baptist Church in
Carson, close to their home. Stuart
Timber is a member of the Mississippi Loggers Assn. and of their county’s forestry association, and they attended the Mid South For estry Equipment Show in Stark ville in September. Even in their off time, the family likes to be in the woods; Stuart says they have a deer camp in Jefferson County where he and his brothers and sons like to get together to deer hunt, from November to the end of January. SLT
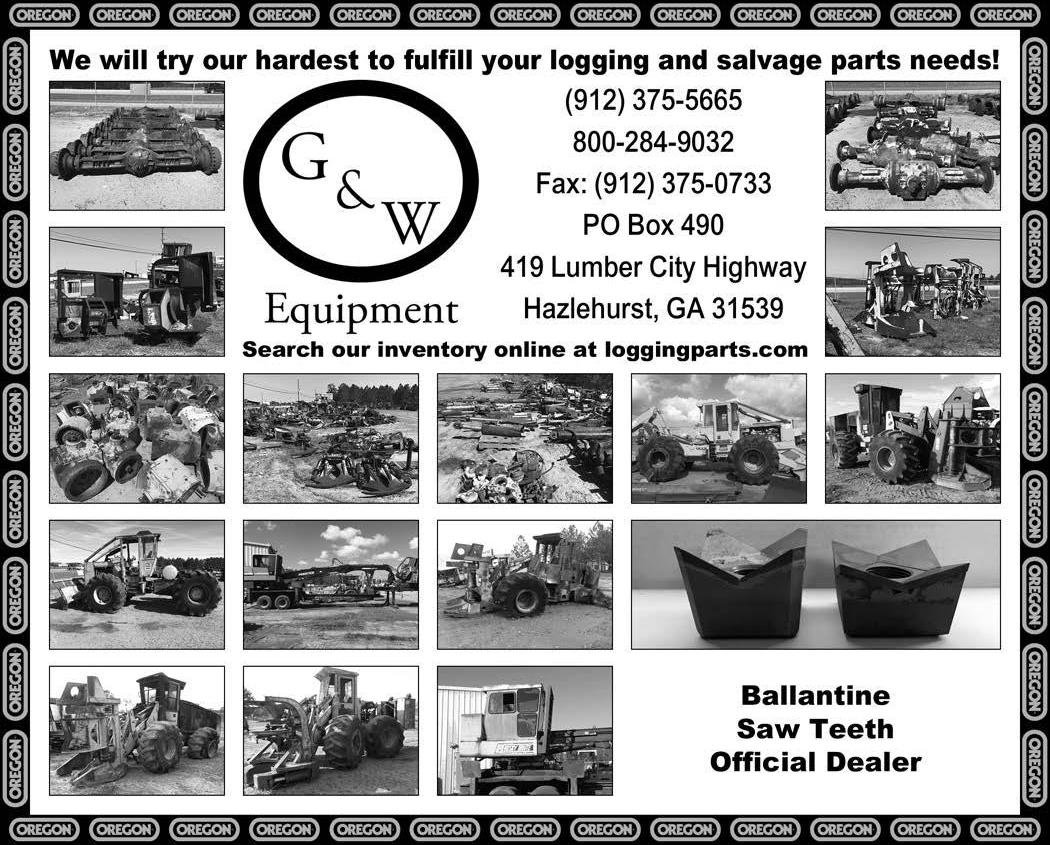
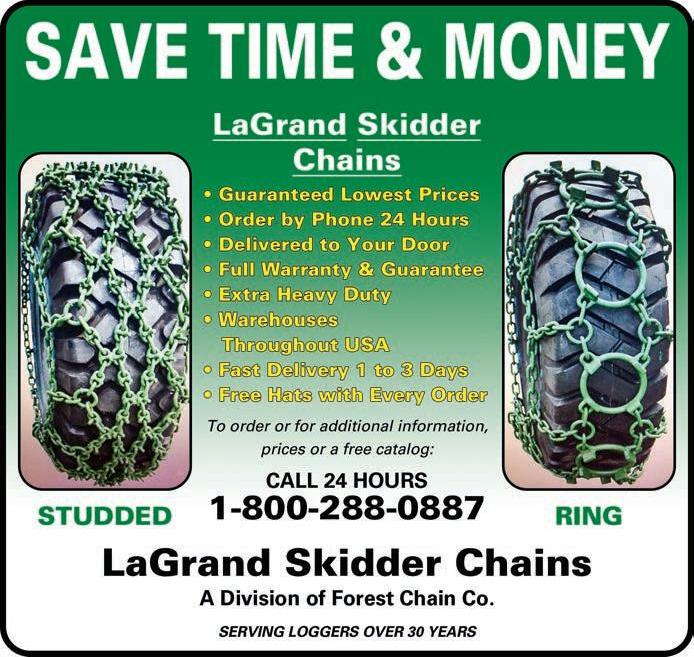
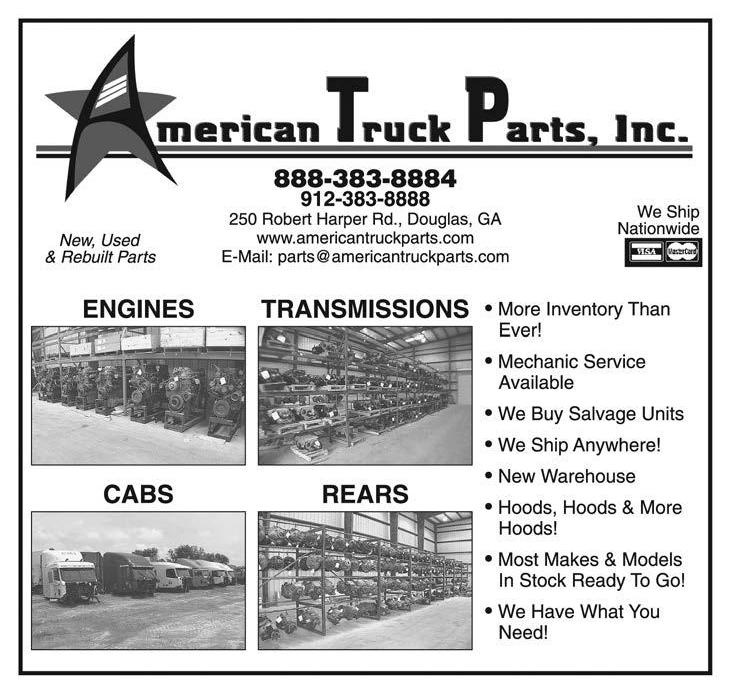
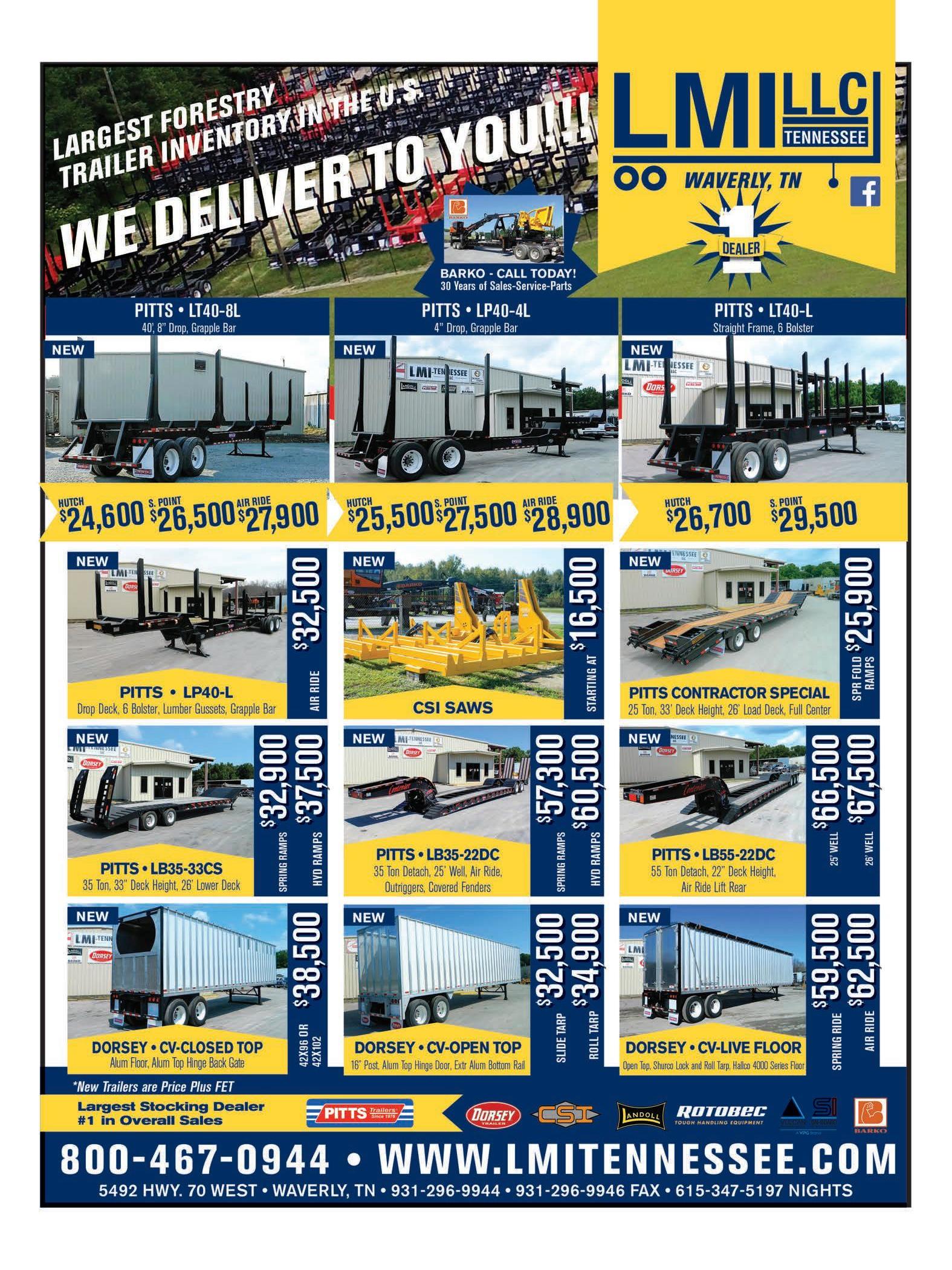
Southern CTL
■ Ponsse and Southern dealers Knight Forestry and Equipment Linc hosted a live cut-to-length demo.
The Ponsse Ergo is a stable machine thanks to its low center of mass and balanced structure, particularly on steep slopes and in uneven terrain. The crane is located on the back bogie, providing an excellent balance between the front and rear frames. Any stress directed at the operator remains low, as the cabin stays stable, regardless of the tree size.
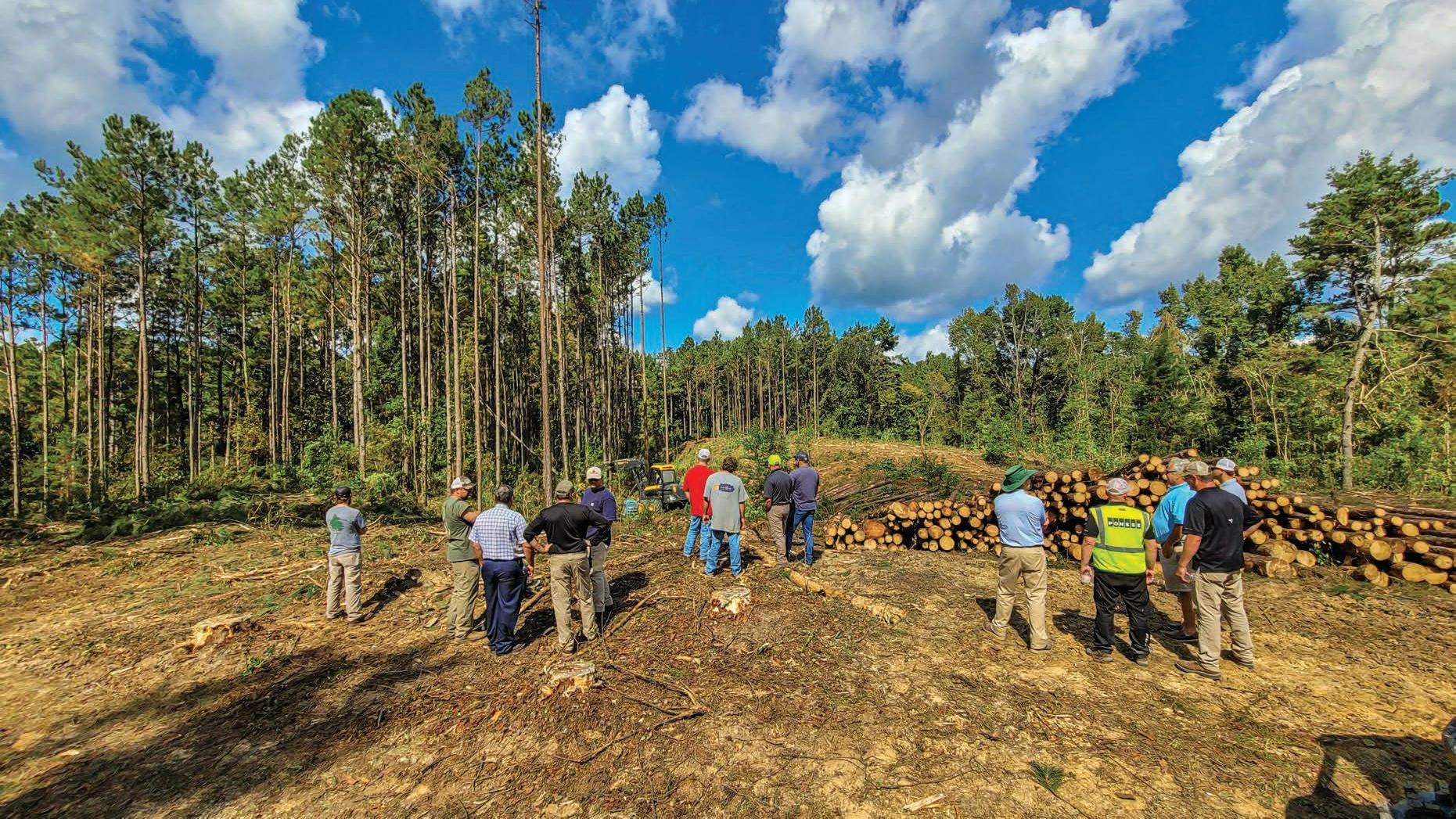
NOTE: The following was submitted by Ponsse North America.
HAVANA, Fla.
On October 22 and 23, 2021, Knight Forestry from Georgia, Equipment Linc from Alabama and Ponsse North America, Inc., joined forces to host a cut-to-length (CTL) live demo on Coastal Plywood land in Havana, Fla. Spectators came to the demo from all around the southern U.S. to watch the efficient team of a Ponsse Ergo harvester and Ponsse Elephant forwarder operate on rolling hills. Also highlighted was a Barko 495 loader with a Ponsse H8 HD harvester processing head with a top saw.
This was not the first CTL demo this year that the team has organized. The same group also hosted a demo in February in southern Alabama.
“We thought it went extremely well,” says Tommy Moore, President of Equipment Linc, Inc., a dealer that represents both Barko and Ponsse, among other brands, from its locations in Alabama. “Turnout was good and they were all prospective buyers and good contacts. The topography of the ground was diverse so it gave an idea of all of it, and it couldn’t have been a better demo site. We’ve gotten a lot of good feedback from it in terms of customer interest, so it was time well spent.”
Pekka Ruuskanen, President and CEO for Ponsse North America, Inc., states, “The mentality in the South is changing from tree length to cut-to-length. CTL is the wave of the future. We are excited to have more and more machines in the South and help the loggers through the transition. It is a big leap and difficult to make the change, but we offer the best forest machines in the industry to make the transition smooth. You can trust in Ponsse!”
Ponsse specializes in forest machines designed for the cut-tolength method and in related information systems. The cut-to-length method allows significantly more logs and chip-n-saw to be produced in initial thinning than the tree-length method. This is because the harvester optimizes each trunk accurately before cutting it. Therefore, visual estimation is not used for cutting the trunk.
Additionally, when using the cutto-length method, even a small amount of special wood can be separated and transported cost-effectively to the mill. Examples of this include different log qualities, veneer log and poles. Due to this, the cut-to-length method enables better volume and value yield because the whole tree is utilized effectively. In tree-length, wastage is often higher.
Please visit ponsse.com/en/cutto-length#/ to read more about CTL. SLT
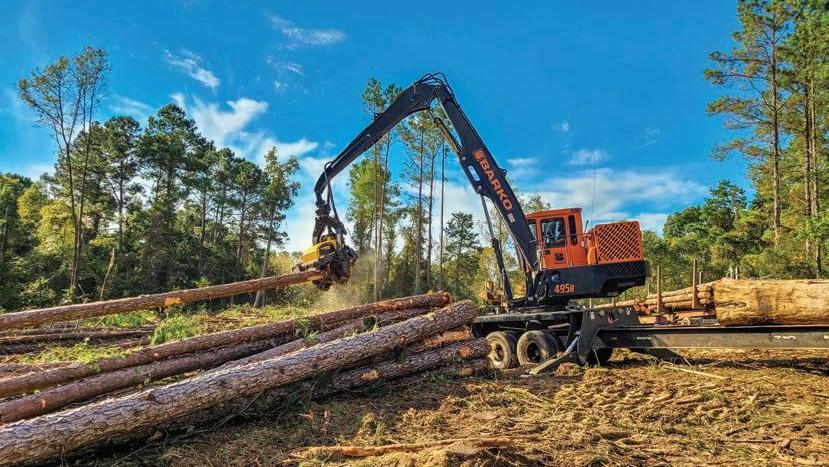
The Ponsse Elephant represents the larger end of Ponsse’s forwarders in terms of power, load capacity and productivity. The Ponsse H8 HD is a tough-built harvester and processor head with high power and excellent geometry for the most demanding logging operations. It is designed for trackbased machines and loaders.
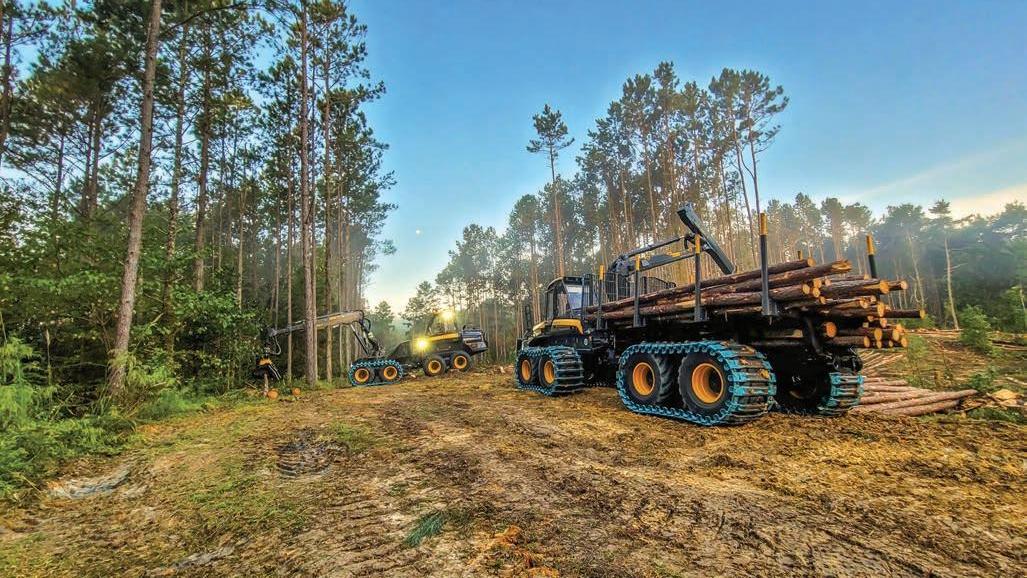
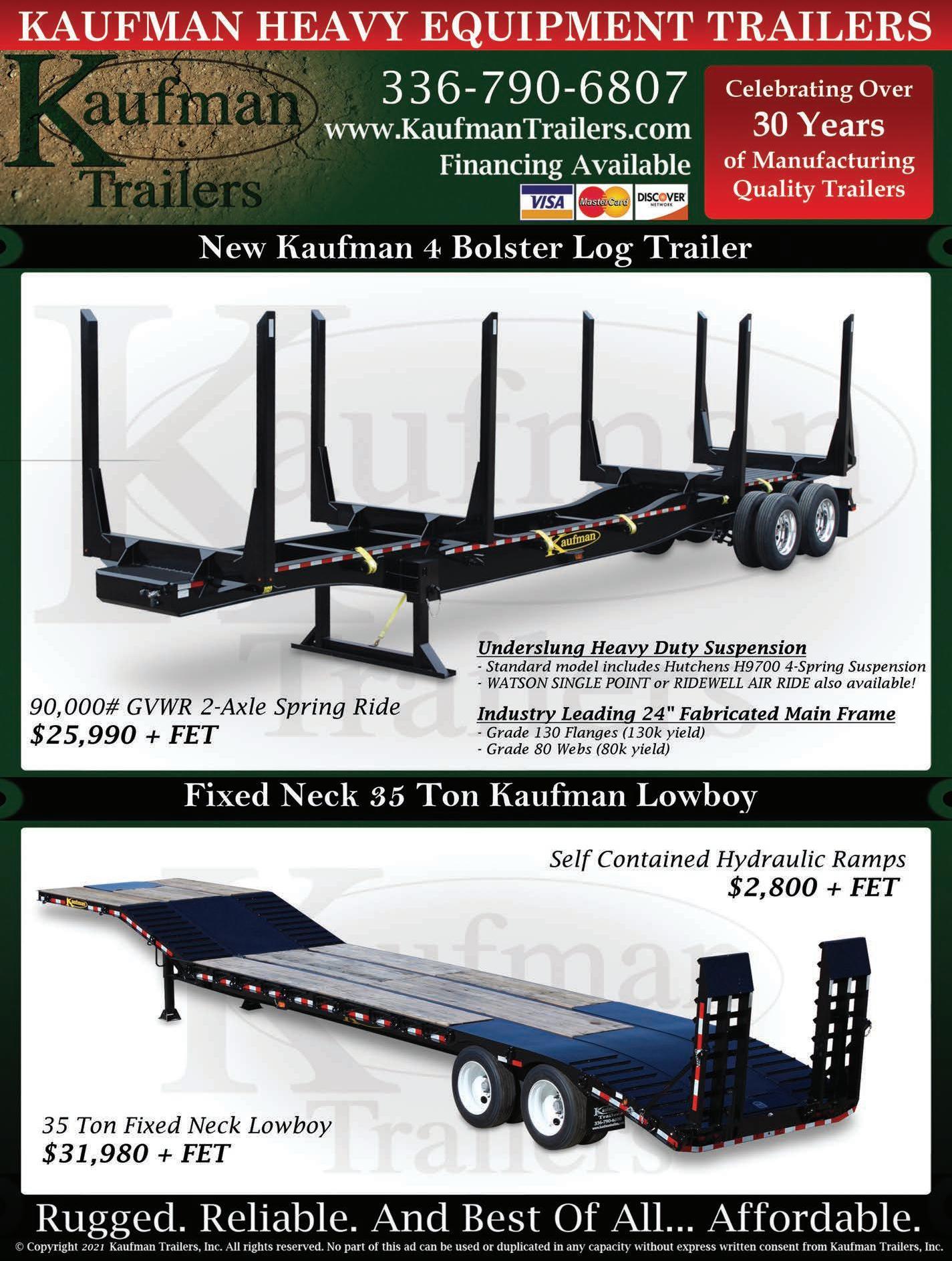
■ Maintaining specs is key to durability, lower costs.
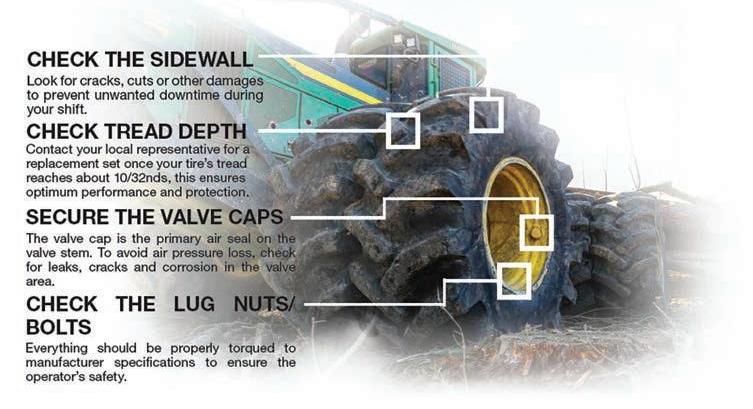
Forestry tires are a big investment for logging operators, and in a business where small increases in efficiency can add up to the difference between profit and loss, it is important to take care of your tires.
Skidders, forwarders and drive-totree feller-bunchers all operate in the most extreme off-the-road and environmental conditions. Therefore, forestry tires experience drastic changes: from hot to cold temperatures, mud to rocks, and abrasive soil, causing them to wear prematurely or fail if not properly maintained. Some key signs that indicate opportunities for improvement are: l Lack of traction l Rapid tread wear l Excessive punctures or cuts l Tire separation l Tire-rim slip
Fortunately, by following simple precautions, operators can increase their logging operation’s investment return, efficiency, and site safety along with decreasing downtime, tire wear and fuel costs.
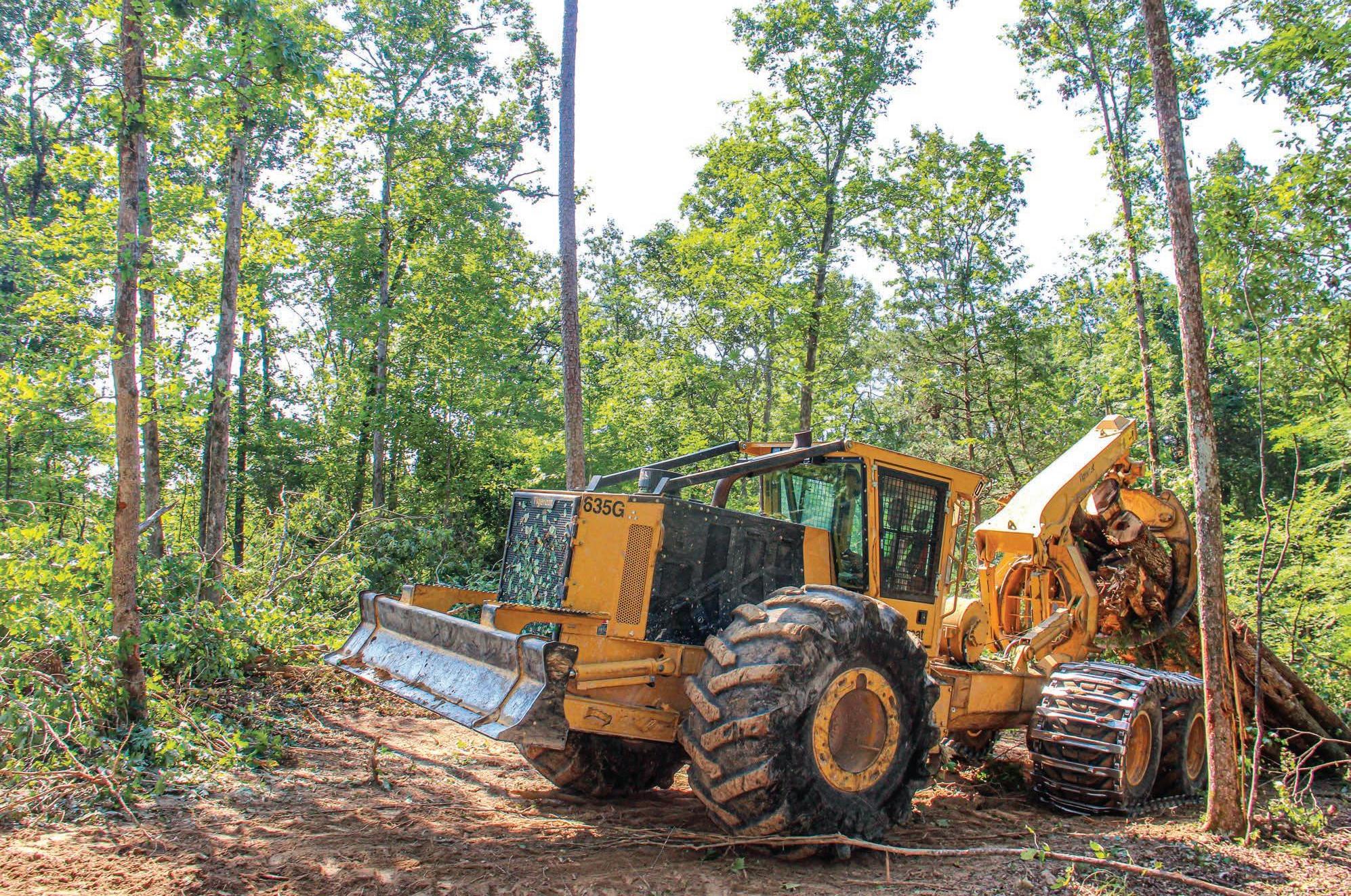
Check Air Pressure
Tire pressure is the most important factor in tire maintenance. Over time tires will lose pressure naturally and need to be pressure checked/adjusted daily. Running machinery on tires that are not inflated to the manufacturer’s recommended levels of air pressure causes excessive wear, tire separation and tire-rim slip. The result is reduced tire life, loss of productivity and increased operating costs.
Keep in mind that under-inflation can cause excessive heat buildup leading to damage of the sidewall, beads or lining of your tire. A drop of 5 PSI can lower a machine’s load carrying capacity by 10% and a drop of 10% will shorten tire life by no less than 10%. Alternatively, an over-inflated tire is more vulnerable to impact damage as the additional pressure stresses the casing.
Operators need to be checking tire pressure regularly, preferably before each shift. Many operators do a walk around, kick the tires, check the fluids, and go to work, but not stopping to check your air pressure can cost you valuable tire life. Please note, for example, the minimum cold air pressure requirement for the Maxam LOGXTRA tire is 45 PSI. If the tire is run under 45 PSI you will encounter problems. Many companies like Maxam will void workmanship and materials warranties if run under the recommended air pressure. To protect your tire investment, only operating with the required minimum pressures must be strictly enforced.
Cold inflation checks are the best and most accurate. A cold tire is generally defined as one that has been sitting idle and not used for a minimum of 24 hours. From this point, the pressure can be monitored more accurately. Hot inflation checks, in most cases, are the norm. Therefore, knowing the cold inflation pressure of the tire will help track the rise in pressure in a working tire. This will then help to set the correct standards for warm inflation checks.
As a tire works, its internal temperature will increase, as will its air pressure. A hot tire must never be deflated. If the air pressure increases by 20% or more from the cold inflation reading, it is a signal that the tire is overheating and should be
Key Maintenance Points
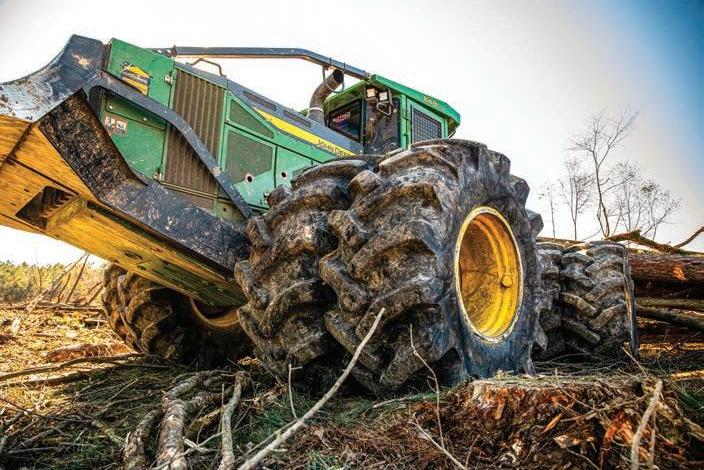
stopped. The tire, then, should cool down or be moved to an operation that is less demanding. If there is any question regarding the continued operation of the tire, consult with a tire manufacturer representative.
A tire operating at the incorrect air pressure, either under- or overinflated, might not show any immediate issues but may fail later, even after its air pressure was corrected. Operating a tire with insufficient air pressure causes the tire’s operating temperature to rise. This can lead to irreversible damage to the tire’s internal components and will shorten its life expectancy.
Over-inflation, on the other hand, is not good either. It can cause rapid and irregular tire wear. In addition, the tire will be subjected to a greater chance of sustaining cuts in the tread and sidewall due to improper flexing of the tire
Excess Loads
Due to the specialized nature of forestry usage, actual loads more than those stated in the appropriate load tables listed by the tire manufacturer are often encountered. Excess loads can be a result of the actual vehicle weight exceeding the design weight. This can be due to different attachments being added, varying density of the materials being moved, load transfer and other factors. Under these conditions, the actual tire load may exceed the load rating noted in the manufacturer’s load table. An example of excess load situations would be transporting the loader from one deck to another.
If excess loads are encountered, the cold inflation must be increased to compensate for the higher loads. As noted in the manufacturer’s data books, the excess load allowed is 15% with a maximum PSI increase of 30%. The customer must be advised that if they are running continually with excess loads, the tires will not perform as well. Questions on proper tire inflation should be discussed with both the tire and rim manufacturer to obtain their approval.
Regular tire pressure checks are highly recommended.
Inspections Are Key
Tires should be visually inspected before every shift for cuts and impacts that could lead to tire failure. Routine maintenance inspections can lead to discovering deeper cuts that have exposed plys. In these cases, removing the tire and repairing it immediately can extend the life of the tire, increasing the machine’s profitability.
During these routine checks, it is important to look at both the valve caps and the lug nuts/bolts. Securing your valve caps will avoid air pressure loss, cracks, and corrosion in the valve area. All lug nuts/bolts should also be torqued to the manufacturer’s specifications to avoid downtime.
Operator training and behavior are both critical to extending tire life. The operator who avoids unnecessary backing up, spinning of tires, and erratic movements will extend tire life on the site and increase production.
Operators should also select the best driving path whenever possible. Operators need to be aware of the layout in the working area and carefully plan their routes. How steep are the slopes? Are there areas of deep mud or hard-to-spot hollows? Going around an obstacle or mound or steep incline may take longer, but the savings in fuel and tire damage may well make it worthwhile. SLT
Submitted by Maxam Tire. For any questions on this article or on proper air pressure, please contact maxamtire.com.
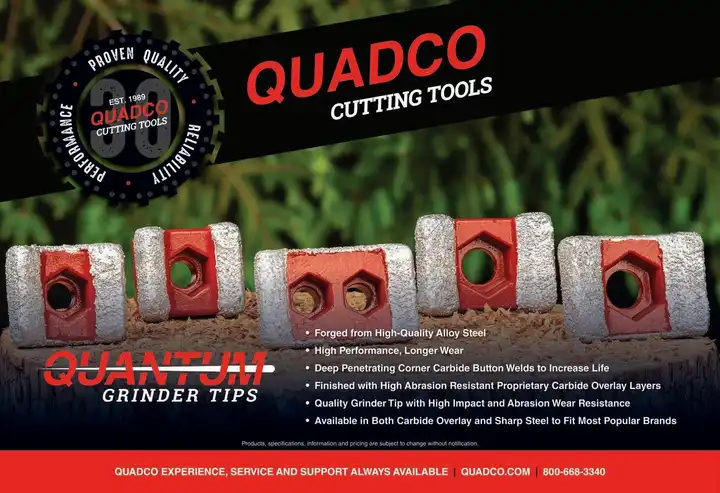