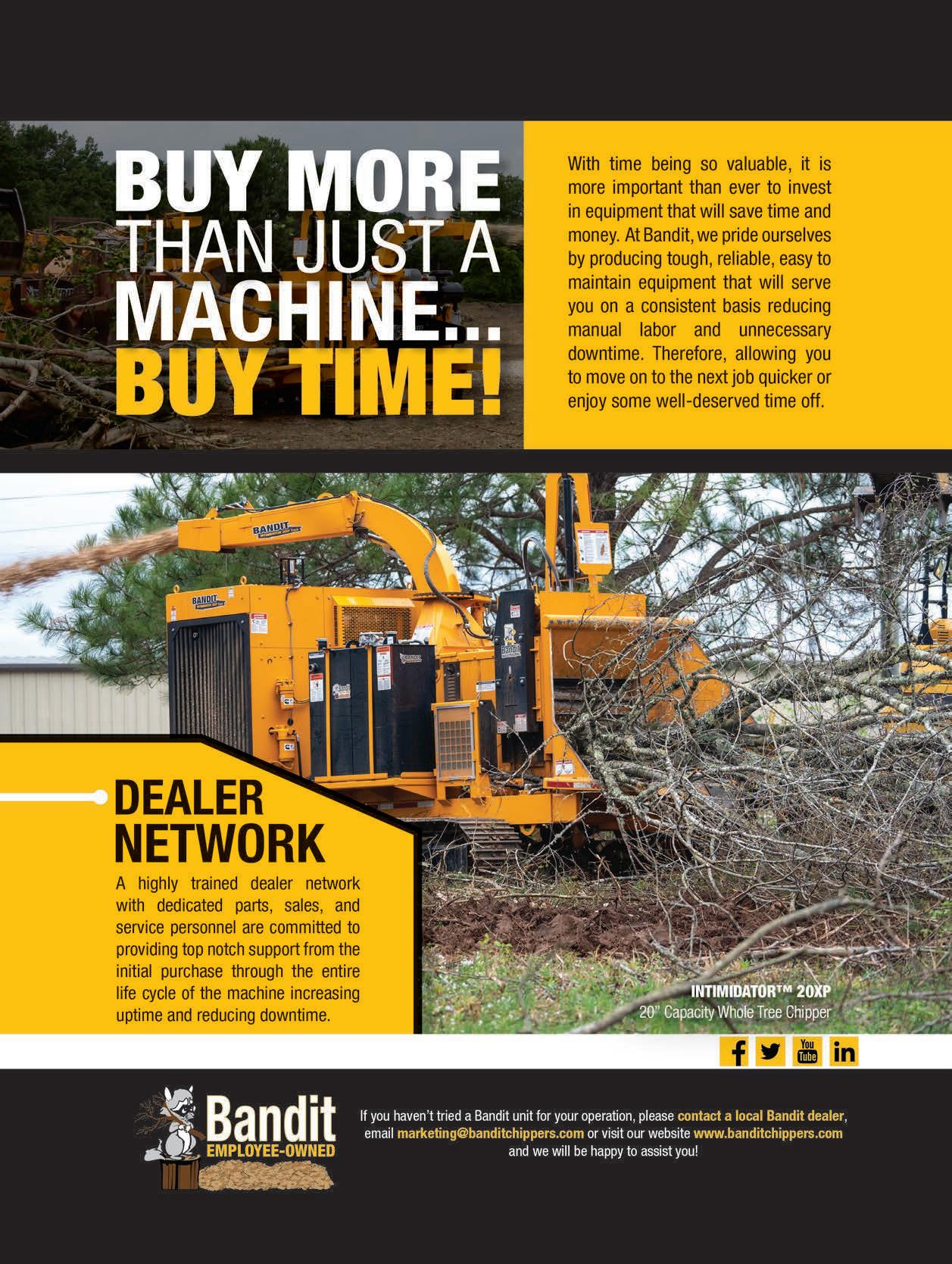
18 minute read
My Take
DAN SHELL
How’s Your Log Supply Chain?
EDITOR’S NOTE: The following editorial ran in the May 2022 issue of Timber Processing magazine and was sent to more than 10,000 mill owners, managers and operators.
In between looking for extra employees to fill out another shift or solidify the one or two already in place, or perhaps looking for larger vaults to hold the cash they’ve been putting away thanks to record lumber prices, lumber suppliers would be smart to take a look at the health of the supply chain feeding their mills. Ensuring all those nice equipment investments meet projections and ROI numbers requires a consistent flow of quality timber.
A mill’s relationship with its contractors or log sources can vary widely as well, from gatewood contractors to “closely held” contractors who work almost exclusively for a given mill or mills. There are also all sorts of financial arrangements with contractors, from cosigning loans to outright buying equipment to fronting repair work—we’ve heard it all.
Most of the time it works as suppliers, customers, vendors and markets mesh. Of course loggers will quickly say they’re getting paid the same prices as 20+ years ago, while procurement people will point out timber is a commodity product. Years ago I remember a forester say the true cost of logging lies somewhere between a company crew and lean-running independent contractor. Probably so.
But no matter how you look at it, both loggers and mills have the same logistical goal: Get the logs to the mills. And just as mills have been hit with labor and supply chain issues, loggers have as well as the entire industry grapples with pandemic impacts that continue, no matter how much we believe and want to be “over it.”
Add the recent inflation run-up and loggers are taking it on the chin: According to a recent survey by the American Loggers Council, in the past year logging contractors have seen an average 25% cost increase across 20 items such as parts and equipment, and some items like fuel much more. Also, more than two-thirds (69%) of loggers have seen labor price increases of 20% or more. Meanwhile, a recent Timber Harvesting magazine 2022 Logging Business survey shows 40% of loggers either broke even or lost money the past two years, and one out of five loggers (21%) rated their business health as poor to very poor. From a list of a dozen different issues, logging rates and log markets finished #1 and #2, respectively, when loggers were asked their top business concerns.
This is not to make the mills out as the bad guys, as almost half (49%) of loggers report price increases the past two years. While it shows some mills are stepping up, it may not be enough across the supply chain. Even with the rate increases almost two-thirds of loggers (60%) reported passing up opportunities to expand in the past two years because of labor issues.
Looking ahead, even more ominous trends are on the horizon: Almost half (46%) of logging contractors are age 60 or over, and almost three-fourths (71%) are 50 or older. It’s those ages that are driving the results of another question, as 37% of those who responded say they are planning to get out of logging in the next five years.
One issue for loggers is there’s no clear path for growth, from the commodity price structure to the inability to pass along cost increases. As one logger commented, what business would make the kind of million dollar investments that loggers do with returns of barely 3% and an inability to pass along costs? Not many.
At TP we’re all about exploring the latest technology and noting the investments mills make to apply it. There’s the old saw among old time sawmillers that the best log is the cheapest log, but as the industry continues to grapple with labor and supply chain issues, perhaps the best log is a healthier one for all segments of the forest industry. TH
2022 Logging Business Survey
Did posting and running an online survey on logging business health during a time of skyrocketing costs affect the “tone “ of the survey’s results? You bet. Is there any way to sugarcoat the results to make it look better? You mean after fuel prices moderated a bit in May then took off again? No way. Read how inflation and fuel costs are hitting loggers hard beginning page 10.
Deere Names Forestry President
Deere & Co. elected Ryan Campbell as President, Construction & Forestry Div. and Power Systems. Campbell leads a team focused on the sustainable, profitable growth of the company’s construction and forestry equipment business around the globe as well as the continued success of the Wirtgen Group. He also has responsibility for the company’s engine and powertrain businesses.
Campbell brings 25 years of wide-ranging experience to his current position. He was senior vice president & chief financial officer, where he had overall responsibility for JohnDeere’s finance functions. In this job, he worked closely with other company leaders in launching JohnDeere’s Smart Industrial strategy. Under Campbell’s leadership, the company also introduced its Leap Ambitions, which align the company’s business and sustainability goals.
Throughout his career, Campbell has spearheaded strategic initiatives focused on enhancing the company’s profitability and strategic positioning, developing future leaders. He has been an unrelenting advocate for driving higher levels of commitment to economic and environmental sustainability through JohnDeere’s digitalization journey. Under Campbell’s leadership as CFO, the company achieved record levels of financial performance.
Campbell earned an accounting degree from Simpson College and an MBA from the Booth School of Business at the University of Chicago.
Forest Service Reveals Immediate Plans
U.S. Forest Service reported it sold 2.87 billion BF of timber sales (compared to the agency target of 4 billion BF) in fiscal 2021, a decrease from 3.2 billion BF in FY 2020, according to the agency’s Fiscal Year 2023 Budget Justification document. The sold volume was valued at $197 million.
The decrease in sales was primarily due to limited staff capacity and nobid sales, according to the agency, adding that the COVID-19 pandemic limited the mobility of timber crews, and field work continued to be difficult to accomplish due to the large fire activity across the Western U.S. Many employees that usually work to prepare timber sales were assigned to wildfire suppression and support. Recovery efforts after large fires, including stabilization work and hazard tree removal, necessitated the involvement of the staff who would typically work on preparing and administering timber sales, the agency stated.
FY 2021 sales included more than 500 contracts greater than $10,000, nearly 66,000 small timber contracts and permits, and 20,000 special forest product permits for products other than timber. Various special Forest Management programs contributed to this volume, including volume sold from salvage sale funds, other permanent and trust funds, and the Collaborative Forest Landscape Restoration Program.
In FY 2023, the Forest Service has targeted 3.4 billion BF of sales. Increased funding will drive more integration with the hazardous fuels program, allowing the agency to manage the treatment of forest resources better. New investments in forest management funded through the Infrastructure Investment and Jobs Act will also allow for planning and preparing new timber sales, stewardship contracts, and good neighbor authority agreements. The agency expects to increase timber volume output because of these investments with additional increases in volume in FY 2025 and FY 2026.
The report notes the agency’s emphasis on innovative uses for wood and wood fiber materials, especially the development of products and markets for small and medium-sized trees, underutilized and low-value forestry residuals, and industrial wood residues.
Wood and biomass extraction are not specifically funded at the national level; however, it is a factor in the agency’s national strategy for improving forest conditions and utilizing material removed during forest management and restoration.
In FY 2023, the National Forest System will continue to make material available for wood and biomass markets (wood energy and wood products) as a byproduct of restoration work. In FY 2021, the agency sold over 1.9 million green tons of biomass (fresh cut woody material at a green moisture content of half water and half woody material) to various wood energy and wood products markets. The National Forest System will continue to work with the SPF Wood Innovations Program and R&D to grow markets and infrastructure for biomass production and utilization across the country.
The Forest Service continues to work with academic and industrial partners in basic and developmental research to find high-value markets for forest biomass. In cellulose nanomaterials, researchers continue to investigate applications in transient electronics, packaging, oil drilling, coatings, lightweight automobile materials, sunscreen, and manufacturing technology of cellulose nanomaterials. Forest Service lignin research is still in the early stages; scientists are investigating UV absorbing, antimicrobial, and antioxidation properties of lignin to develop new markets for this byproduct of pulping wood. Lignin is currently used as in-house fuel, and new markets for lignin may generate new revenue for pulp mills.
PotlatchDeltic Announces Sawmill Upgrade at Waldo
PotlatchDeltic Corp. is investing $131 million to expand and modernize its sawmill located in Waldo, Ark. The project will increase the mill’s annual production capacity from 190MMBF of southern yellow pine dimension lumber to 275MMBF. The company states that the investment will reduce the mill’s operating costs significantly.
“The Waldo investment is an exciting strategic growth opportunity and it will position the mill among the lowest cost producers in the U.S. South,” comments Eric Cremers, President and CEO. “The project reflects our belief that housing fundamentals will remain strong.”
The existing mill will continue to operate during the project. Work on site will begin in the third quarter of 2023 and is expected to be completed by the end of 2024.
PotlatchDeltic owns three sawmills and nearly 950,000 acres of timberland in Arkansas.
Ruling Goes Against Oregon Counties
Oregon Court of Appeals reversed a 2019 jury decision that had awarded 15 Oregon counties $1.1 billion over how the State had managed forest-
lands that had been legally transferred to the State in 1941. The Oregon Court of Appeals ruled that no contract was breached by the State, as had been alleged by the counties.
Led by Linn County, the class action suit against the state of Oregon and State Forestry Dept. had alleged that the 1941 law required the State to not only return to the counties a specified portion of the revenues derived from management of those forestlands, but that the State had a contractual obligation under the law to manage the forestlands in a manner so as to “secure the greatest permanent value of such lands” as cited in the 1941 law. The counties said the State had breached this contractual obligation by failing to manage the forestlands for maximum value.
However, the Oregon Court of Appeals ruled that the provision or phrase was not a term in a statutory contract between the State and the counties, and consequently reversed the lower court and jury decision.
The 1941 Act had authorized the State to acquire by purchase, donation or exchange any “public, quasi-public or private owner” land that was “chiefly valuable for the production of forest crops, watershed protection and development, erosion control, grazing, recreation or forest administrative purposes.” The Court of Appeals noted the Act provided a distribution formula for all revenues derived from these lands.
In its decision, the Court of Appeals noted that over the ensuing decades, 15 Oregon counties conveyed hundreds of thousands of acres of land to the State pursuant to the Act, which then became state forests. Then in 1998, the State proclaimed the Greatest Permanent Value rule with regard to these lands, defined as “healthy, productive, and sustainable forest ecosystems that over time and across the landscape provide a full range of social, economic, and environmental benefits to the people of Oregon,” and which directed the state forester to actively manage them in a sound environmental manner to provide sustainable timber harvest and revenues to the state, but not exclusive of other forest resources and environmental goals.
The Linn County lawsuit accused the state of a breach of contract for implementing management plans in reliance upon the GPV Rule that failed to maximize the potential revenue from the lands.
Before the Court of Appeals, the State argued that a statutory provision is not contractual unless the legislature clearly expresses its intent to make it so. The Court of Appeals, citing previous cases on State legislative language and intent, agreed that the language and the legislation in this question did not constitute a statutory contract.
It’s expected the counties will appeal the decision to the state Supreme Court.
Agency Percolates 4FRI Once Again
In March, the Forest Service released its latest Arizona Four Forests Restoration Initiative (4FRI) preferred plan within the draft environmental impact statement as required by the National Environmental Policy Act (NEPA). Called the Rim County Project, the Apache-Sitgreaves, Coconino and Tonto national forests will implement a suite of restoration activities on 991,000 acres over 20 years, including a combination of mechanical thinning and prescribed burning.
“Restoration treatments will move the project area toward the desired conditions and initiate the reestablishment of fire-adapted, resilient, diverse and sustainable forested ecosystems,” the agency says, adding that its preferred plan “provides the project area with the greatest protection from the undesirable effects of fire by treating the greatest extent of the project area with a combination of mechanical and prescribed fire treatments.” The plan will also improve overall watershed condition.
The agency says the preferred plan “increases forest products supplies to the greatest extent, and will contribute to improve the financial viability of locating forest products industries, including logging firms, sawmills and biomass facilities in northern Arizona.”
The plan calls for the implementation of 12 “in-woods processing sites,” though it doesn’t define the makeup of such sites.
Due to increasingly catastrophic fires on Arizona’s national forests and a general deteriorating condition of those forests, the Forest Service created 4FRI in order to treat more than 2 million acres across four Arizona national forests. In 2012 the agency contracted with a company to mechanically thin 300,000 acres over 10 years, but the project fell extremely short of the stated objectives and a major reason was due to the limited capacity for biomass disposal.
The Forest Service then sought out proposals to restore and utilize more than 500,000 acres over a 20-year contract. Two of the proposals that came in included a sawmill and an oriented strandboard mill, but the Forest Service cancelled the process last September, fearing it would be too risky financially for any one company and possibly for the agency itself. Both of the proposals included Novo Power, a 27 MW biomass power plant in Snowflake, Ariz., as part of the equation for biomass disposal and utilization.
Claw Forestry Plans New Sawmill In Gloster
Claw Forestry Services, LLC announced that its affiliate will build a 250MMBF southern yellow pine sawmill in Gloster, Miss. within Amite County. The project represents an investment of nearly $200 million and will create 131 direct jobs and support an additional 200 indirect jobs when operating at full capacity. The new mill will require in excess of 1 million tons of timber annually to produce the stated lumber output. The facility will be located on 65 acres of land, which includes the former Georgia-Pacific site. In connection with the new sawmill facility, efforts are under way to resume operation of the Gloster Southern Railroad.
Mississippi Development Authority is providing assistance for infrastructure improvements and site development. Amite County also is assisting with the project. Claw CEO Billy Van Devender comments: “This project will employ the best complement of modern technologies to meet our growing consumer demand for the highest quality product, in a region where we own significant timberland acreage.”
Work at the site will begin late in 2022 and startup of the sawmill is scheduled for the first quarter of 2024.
Claw Forestry started in 2000 as a natural resource manager and has evolved as a major timberland owner and investments firm in the U.S. South. Its affiliate companies op- 21
Fuel Cost Analysis
When looking for a fuel adjustment, you’d better know your numbers before you negotiate.
JOEConrad
EDITOR’S NOTE: Earlier this year, as fuel prices took off, the Virginia Loggers Assn. commissioned Dr. Joseph Conrad, Assistant Professor of Forest Operations, Warnell School of Forestry & Natural Resources, University of Georgia, to conduct a fuel cost analysis that includes impact on production and transportation costs, and a fuel adjustment formula. This is a comprehensive third-party objective analysis that producers can apply to their particular operations (report modeled Southern logging operations and may need to be adjusted for other regions) and use as a resource when addressing fuel adjustments needs.
Recently, I have received several urgent emails from loggers, suppliers, and procurement foresters trying to calculate fuel cost adjustments. This is a good sign in that mills and suppliers want to work with loggers to address skyrocketing fuel costs. On the other hand, it suggests that the previous cut-and-haul rates may have been negotiated without careful consideration of the underlying costs involved in harvesting and transportation. (Forgive me if I am too cynical.) Fortunately, calculating a reasonable fuel cost adjustment is simple math. However, it does require data, or without solid data, reasonable estimates. Loggers should have data while foresters may have to rely on estimates.
Calculating Per-Ton Costs
Let’s look at an example using data from one month’s production. During this month the logging crew produced 8,500 tons of timber and consumed 9,909 gallons of diesel (Table 1). Logging equipment consumed 0.38 gal/ ton, support vehicles burned 0.05 gal/ ton, and log trucks consumed 0.74 gal/ ton. All these values will vary from one harvest to another. I would expect in-woods fuel consumption to be most Most trucks and pieces of equipment track fuel consumption data that’s easily downloaded.
Measuring Consumption
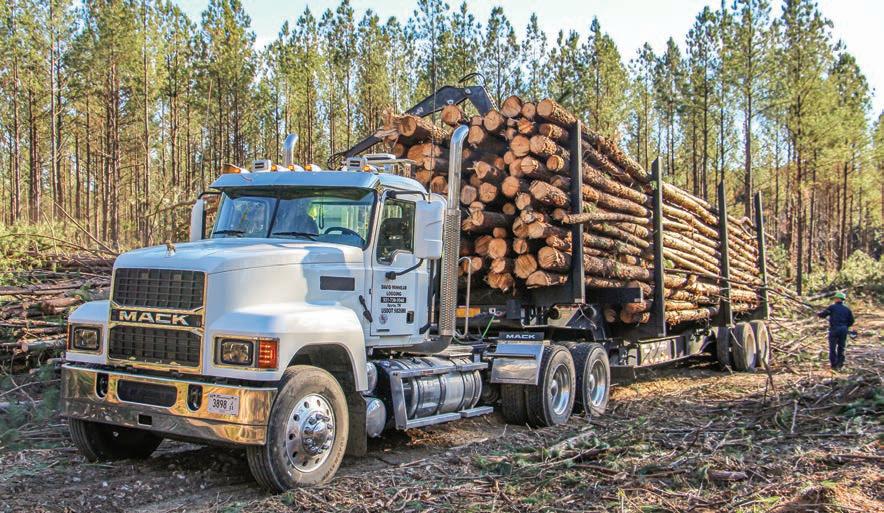
To calculate a fuel cost adjustment, a logger will need to know how much fuel is consumed per ton of wood harvested. Fuel consumption data should include in-woods equipment, support vehicles (i.e., company pickups, fuel trucks, parts trucks, etc.) and log trucks. Fuel consumption by in-woods equipment can be collected easily. Many machines collect fuel consumption data using onboard computers. If machines do not measure fuel consumption, a fuel meter can be purchased for less than $100. Every time a machine is refueled, the operator should record the date, number of gallons pumped, and machine engine hours.
Finally, fuel consumed by log trucks should be measured. It is important to determine the fuel economy of log trucks. Record miles driven from odometers and gallons of fuel consumed. Log truck fuel consumption per ton will obviously vary by haul distance and so it should be calculated on a tract-by-tract basis. Fuel consumption per ton can be calculated using the formula below. Accurate values for tons per load, miles per gallon, and percent-loaded miles are obviously important. Do not assume 50% loaded miles unless there is data to support this value. Log trucks often average 40–45% loaded miles once trips home and moves between sites are counted.
Divide gallons of fuel consumed by the number of tons produced to calculate gallons per ton. Make sure that fuel consumption data and production data cover the same period. Estimates based on a week or a month’s data will be more accurate than estimates based on daily records.
Several studies have measured fuel consumption by logging equipment (Greene et al. 2014, Kenney et al. 2014). While this data is several years old, it can get a company in the ballpark if they do not have their own data. These studies estimated that logging equipment consumed between 0.4 and 1.0 gallon per ton to cut, skid, and load. Loggers have shared log truck fuel economy data with me in the past several years and they averaged 4.5–5.5 miles per gallon. This included a mix of loaded miles, unloaded miles, and idling (i.e., real-world conditions).
consistent, although it would vary based on skidding distance and site conditions. Log truck fuel consumption per ton will vary considerably based on haul distance.
At $2.60/gal for off-road diesel and $3.00/gal for on-highway diesel, fuel costs accounted for $3.35/ton of delivered wood (Table 2). When fuel prices increase to $4.60/gal for off-road diesel and $5.00/gal for on-road diesel, fuel costs increased to $5.69/ton of delivered wood. For this logger, a $1.00 per gallon increase in fuel prices increased onboard truck costs by approximately $0.43 per ton. A $1.00 per gallon increase in fuel prices would raise cut-and-haul costs by approximately $1.15 per ton. Cut-andhaul costs would increase even more if haul distances exceeded the 50 miles used in this example.
For this logger, a fuel cost adjustment should add at least $0.43 per ton to the base cut-and-load rate for every $1.00 per gallon increase in the fuel price, or approximately 4 cents per ton for every 10-cent per gallon increase in the fuel price. The cut-and-haul rate should be increased by approximately $1.17 per ton for every $1.00 per gallon increase in the fuel price, or 12 cents per ton for every 10-cent per gallon increase in the fuel price.
The impact of rising fuel prices on hauling costs varies substantially by haul distance. At a 30-mile haul distance, a $1.00 per gallon increase in the fuel price increased hauling costs by approximately $0.45 per ton, whereas at a haul distance of 70 miles the same increase in the fuel price increased hauling costs by approximately $1.04 per ton. If haul distances are highly variable, the fuel cost adjustment should be structured accordingly. A one-size-fits-all fuel cost adjustment may be lucrative at short haul distances and insufficient at long haul distances.
Conclusions
The first step to negotiating a fuel cost adjustment is to prepare for the negotiation. Having accurate and upto-date data is essential to calculating a fair fuel cost adjustment. As my father used to tell me, the devil is in the details. Measuring the fuel consumption of each machine and truck is worth the trouble to make sure that the business owner understands his costs. Tracking fuel consumption can also help a business owner detect mechanical issues or even theft. TH