
18 minute read
WOOD BIOENERGY PART III
Advanced Pellets Lead Wood Energy Discussion
EDITOR’S NOTE: This article is the third in a three-part series reviewing the speaking sessions during the sixth Wood Bioenergy Conference & Expo held March 10-11 at the Omni Hotel at CNN Center in Atlanta and hosted by Wood Bioenergy magazine. The seventh Wood Bioenergy Conference & Expo will be held March 29-30, 2022 in Atlanta.
By Rich Donnell, Dan Shell and Jessica Johnson
Apopular session during the Wood Bioenergy Conference & Expo was devoted to Advanced Pellet Technologies, and more specifically: Is It Time to Move to Pellets 2.0? What Is the Technical and Economic Status of Advanced Pellet Technologies?
Bill Strauss, president of FutureMetrics, served as the moderator. Strauss noted that steam exploded or torrefied pellets produced by thermal treatment have been promised
18 Wood Bioenergy / August 2020 for years as a better option to white pellets. They have higher energy per cubic meter, some exhibit hydrophobic characteristics, and in general they require less modifications to pulverized coal power plants that want to co-fire or fully switch from coal to pellet fuel. However, Strauss said, the promises have consistently failed to come true due to technological shortcomings, their inability to compete with white pellets on a dollars per delivered energy cost basis, and to some degree, market inertia in a sector where more than 25 million tonnes of white pellets will be used in power stations in 2020. An illness kept Bjørn Knappskog, CEO of Arbaflame, from attending, but moderator Strauss stepped in and presented Knappskog’s paper, Advanced Pellet Fuel from a Proven Technology.
Knappskog has been head of business development of the bioenergy division at Pemco since 2017, which includes both white pellets production and district heating, and development of next generation wood pellets through Norway-based Arbaflame. He has held the role as CEO of Arbaflame since late 2019, with key focus on commercialization and preparation for large scale industrialization of the technology.
Knappskog explained that Arbaflame Pellets are handled and used as coal throughout the supply chain. He said in addition to emerging demand from Japan, Arbaflame sees an increased demand for this type of fuel in Europe. “Coal is actually being phased out by EU governments and local stakeholders,” he said, pointing to examples such as Italy, which is expected to phase out coal power by 2025, as is the UK, Finland by at least 2029, Denmark, The Netherlands and Portugal by 2030.
Knappskog said Arbaflame has been developing a coal
replacement biofuel at its What is torrefaction? Johnson demonstration plant since asked. “Heat treatment process 2010. The process has included for woody biomass that progresmore than 10 full-scale tests sively decomposes and gasifies together with end-users. the biomass, leaving a higher
Arbaflame demonstrated carbon, higher energy material 100% conversion in 2014 and that can be further processed delivered Arba pellets for sev(typically by densification) into eral years to the Thunder Bay a variety of primary feedstocks generating station, a backup for other products such as bioplant in Ontario. It demonmass fuel.” strated full conversion to bioHe said torrefied pellets can mass with only minor Arbaflame reports signing a long-term supply agreeshow a comparative cost and modifications. Although this is ment with Maasvlakte power station in Rotterdam. Deprofit advantage compared to a backup plant, it demonstrated the difference in capital expediture conversions compared to liveries started in the second half of 2019. This photo is from Oslo Port, just outside the city center. white pellets. He said the process can be tailored to custom fuel properties, offers more carbon large white wood pellets. and less volatiles, lower energy
He said Dong Energy spent €95 million to replace coal density and higher yield, can be blended with coal or other with white pellets, Ontario Power Generation at Atikokan biofuels, is hydrophobic, high density, can be produced with spent €100 million, Drax Power spent between £650-700 or without binders. He pointed to no adverse effect on mill million. Replacing coal with Arba pellets at OPG in Thunand combustion, low dust formation and torrefied biomass der Bay cost only €3 million. can replace coal in power plants.
The key challenge for all advanced pellet technologies Other key points, Johnson said, is the torrefaction of is to prove cost competitiveness versus traditional wood biomass can reduce the organically bound chlorine up to pellets. Arbaflame’s solution is to integrate its process with 90%, and that torrefaction is opening up the energy and chemical extraction, increasing the value of its waste biocarbon market for agricultural byproducts and grassy streams. This will be demonstrated at its new commercial crops with ordinarily high chlorine contents. “This could plant under construction this year. change the equation on both feedstock costs and sustain
The next challenge in order to increase the market peneability concerns,” he said. tration to an even larger scale is to become cost competitive Johnson said the potential encompasses biofuel pellets for versus coal per GJ. Arbaflame plans a full-scale R&D test power production, blast furnace carbon injection, chemical program to verify the use of low-grade fuel in combination compound recovery, concrete production, polymer extender, with chemical production to reach this goal in 2021-22. 3D printing, advanced material production, pretreatment for
Extensive verifications, experience and technology gasification and biochar production. “Biochar not only sells readiness put Arbaflame in a position to sign a larger longfor several hundred dollars per ton, it also effectively seterm supply agreement with Maasvlakte power station in questers carbon into soil for hundreds of years and creates Rotterdam. Deliveries started in the second half of 2019 perfect conditions for permaculture eliminating the need for from the demonstration plant. fossil fuel based fertilizers,” Johnson said.
This demo plant by the way has now been demolished He also talked about the innerworkings of TSI’s Lab and construction of the commercial plant, Arba One, is onTorreactor. going. It will have a capacity of 70,000 metric tons of pelGarth Russell, Vice President of Biomass Conversion lets per year, combined with a biorefinery producing higher and Mechanical Pulping at Valmet, Inc., delivered a paper value products such as Furfural and Methane right away. prepared by Mats Arnberg, Director of Biomass Conver
Andrew Johnson, Vice President of TSI, spoke on the sion Technology at Valmet, entitled Realizing the Green Current Status of Torrefaction Technology. He addressed Gold with BioTrac Continuous Steam Explosion System. briefly TSI’s background in drying and air emissions conArnberg said BioTrac is offered for use mainly in black trol technologies, and pointed to TSI membership in the pellet, bioethanol and biochemical production. He said International Biomass Torrefaction Council (IBTC). BioTrac is adopted to the specific need of each process but
What are the prospects for torrefaction? Johnson asked. in all parts is the heart of the process. First he said there is cautious optimism, and that IBTC is The presentation addressed steam explosion, which he tracking 24 torrefaction projects representing more than 2 said dates back to the 1920s. Basically it is heating biomillion tons of production. “The process is becoming well mass with steam followed by rapid de-pressurization. The developed and products are very flexible,” he said. “The hemicellulose decomposes and lignin softens, making the potential market is huge.” material excellent for pelleting.
Johnson showed a world map of coal fired power and Some key points about black pellets, according to the the various stages of closure, shelving and very modest presentation, is that it’s a renewable fuel that can be used permitting and construction. to replace fossil coal, it is durable and more moisture re

August 2020 / Wood Bioenergy 19
sistant than white pellets, and thanks to its properties it lowers both the CAPEX as well as OPEX in logistics.
“Steam explosion is not to be confused with torrefaction,” he said. “They are two different methods to produce advanced pellets.”
The presentation showed that Valmet has the equipment, technology and expertise to offer a complete black pellet plant, including the energy island and controls center.
Valmet can offer the BioTrac system for capacities going from pilot scale up to about 500,000 t/year from a single unit. He described the continuously operating BioTrac reactor as beginning at the surge bin for storage and to ensure stable feeding of biomass; the plug screw feeds the material into the pressurized vessel, the reactor; the biomass is treated with steam and discharges continuously via a screw system; the reactor has automatic time and temperature control to ensure stable product quality; the steam explosion happens at the bottom where the biomass is discharged to the non pressurized part; after the reactor the biomass and vapor are separated; the vapor goes to energy recovery and biomass to pelleting.
The presentation noted several benefits. The first benefit relates to stable and constant steam consumption. The consumption of steam is continuous meaning that the steam supply system can be standard and simple. The system has automatic control of temperature and time.
The second benefit is the homogenous particulate quality, which in effect leads to a very homogenous pellet quality. The reason is the design of the discharge and the fact it is a continuous process which means that all particles are subjected to the same pressure drop after going from the pressurized zone to the non-pressurized zone. The reactor has automatic time and temperature control to maintain same process conditions.
The third benefit is the economical treatment of steam after BioTrac. Both from an environmental and economical perspective the vapor after the BioTrac needs to be recycled. The flow of biomass and steam is separated in a cyclone. A continuous flow means also the separated vapors are stable and constant and the system to treat or recover the vapors will have a simple and straightforward design. All of these benefits leads to attractive CAPEX and OPEX. And the BioTrac system is based on further refinement of proven technologies in pulping and fiberboard, he said.
The presentation showed two graphics, one of a horizontal BioTrac mainly used for agro-based material, and one of a vertical BioTrac used for woody biomass. Valmet reports it has sold more than 20 of the pretreatment systems.
The presentation closed with the note that Valmet was selected by FICAP to deliver the first continuous BioTrac for the production of black pellets. The plant will produce 120,000 black pellets and startup is scheduled this year. FICAP is owned by investment fund groups and Europenne de Biomasse who developed the project.
Tim Wagler, CEO of Trinity Green Derivative Products, spoke on CE2—Cellular Explosion Technology. He said this technology occurs at the cellular level and does not require a steam boiler; it is continuous, not batch, no long
20 Wood Bioenergy / August 2020 process exposures; creates large volumes of high-value liquid extract; it transforms the pelleting process: no hammermills, no indirect dryers; it enables smaller, federated pellet plants nearer lower-cost feedstock that can be rapidly installed and commissioned.
“Our objective is to produce highly conditioned fiber as a co-product, in concert with liquid extraction,” Wagler said.
He cited various liquid extract products (phytohormones, wood preservatives, adhesives, etc), and the coproduct fiber, noting pine chips that enter the technology at 50% moisture come out within seconds fiberized at 18%. The resulting CE2 pellets offer impressive composition breakdown.
He also showed a slide of CE2 fiberboard produced at Mississippi State University, 1 in. thick, 60 lbs/ft3 with 4% MDI binder.
Wagler emphasized the liquid extract. Each line (40K mt/year) produces 3 million gallons of extract per year, he said. Consider 80,000 mt (two lines) with gate price of $135/mt and $1/gallon liquid extract, requiring $10 million CAPEX at $125/mt and OPEX of $115/mt, delivering a production margin of $7.6 million.
He showed the plant conceptual and noted several partners including Anderson International for lignocellulosics, GLC Consulting for horticulture, Mississippi State University and Idaho National Laboratory.
Next steps? Wagler said two sites have been selected for a pellet demonstration plant; this will be followed by liquid extract commercialization (seeking go-to-market partners, emphasizing horticultural, row-crop applications); and the Phase 2 IP Development, and he said a co-development announcement is imminent.
Wagler said they continue to seek strategic investment partners and fiber demonstration partnerships.
Handling With Care
Cautioning plant operators to take the time to better plan material handling as a part of new plant or expansion project design, Tim Brown, Business Development Manager for Biomass Engineering & Equipment (BE&E), gave a presentation titled Smart Material Handling–Good Designs Are NOT More Expensive.
Brown’s primary point was that considerations for efficient material handling need to be incorporated from the first conceptual meetings, not just tacked on as an afterthought or commodity component.
Smart material handling begins with smart designs and informed equipment selections, Brown said. “Is the goal to build the cheapest mill, or is the goal to produce a mill that is efficient, reliable, and profitable?” He questioned the logic of designing a plant and buying the best dryer, best pellet mills, best hammermills—and then connecting them with the lowest bid for material handling equipment.
Brown examined issues that BE&E sees on a regular basis that cause operational inefficiencies and unscheduled downtime. In general, plant operators work with an engineering group, EPC, contractor, or combinations of the
three to design a new mill. Selections and layout-placement for the major pieces of equipment are done, then the pieces need to be connected. “Material handling equipment will not be optimized unless it’s considered during the layout design phase,” he stressed.
Optimized material handling includes monitoring and screening incoming raw material, and developing an autoreclaim infeed system that reduces reliance on wheel loaders. (Brown cited a recent study at a particleboard plant that showed the total annual cost of operating a wheel loader is more than $400,000.)
Brown gave a detailed example of how a more costly dual input conveyor infeed system is more efficient and profitable than a single input conveyor. In this case, it’s smart to build in redundancy to the system.
As an example, instead of designing an infeed that uses a single input conveyor running at its maximum capacity to move 50 tons/hr., use two conveyors with 35 tons/hr. capacity. That way, the plant isn’t completely down if there’s an issue with the infeed conveyor. Also, both conveyors are running at below capacity, leading to less wear and tear and longer component life. Plus, if one of the conveyors is down for repair or maintenance the mill can still operate at 70% capacity on the full 35 tons/hr. from the other con
Tim Brown of BE&E addressed material handling.
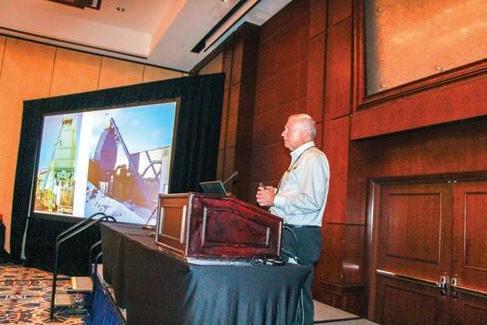
veyor, Brown said.
He concluded that the cost of equipment can be misleading. “Is the least expensive really the best choice?” he said, urging operators and planners to determine factors such as total installed cost, component life and the costs of operation over five or 10 years. Also, don’t forget horsepower requirements and energy use over the life of the equipment.
“So what is the true cost when less expensive fails?” Brown asked, adding that when factoring in the true costs of downtime, good designs are definitely less expensive, more efficient and profitable in the long run.

August 2020 / Wood Bioenergy 21
Dust Management
Jeff Nichols with Industrial Fire Prevention and Greg Bierie with Benetech USA captivated the audience with a breakdown of the hazards relating to combustible dust and how to manage dust while keeping production safe.
Nichols was up first with the presentation, The Combustible Dust Hazard Analysis. Nichols has been providing special hazards protection for combustive dust processes since 1979 and is the author of The Ultimate Guide To Fire And Explosion Prevention, a guide that aptly carries the tagline: a layman’s guide to helping you keep from burning down and blowing up your plant. Nichols, a return presenter to the Wood Bioenergy Conference & Expo, and his company Industrial Fire Prevention, which represents Fagus GreCon, really drilled into chapter 7 of the NFPA standard, 652, on combustible dust and its accompanying requirement to do a dust hazard analysis.
Nichols explained what chapter 7 of the standard meant, what needed to be implemented by plants and when it needed to be done. The standard requires all facilities to have dust hazard analyses done on all new and existing processes and facility compartments that are at risk for dust explosions. The dust hazard analysis must be completed to be in compliance with the standard—and the analysis should be reviewed and updated at least every five years. The responsibility to have this analysis done falls to the owner/operator of the facility where materials are determined to be combustible or otherwise explosive, like a wood pellet plant or biomass power plant.
As an overview of the standard, the dust hazard analysis must evaluate the fire, deflagration and explosion hazards and provide recommendations to manage the hazards in accordance with other NFPA guidelines outlined in a subsection of the standard. The results of the dust hazard analysis review should be documented, including any necessary action items requiring change to the process materials, physical process, process operations or facilities associated with the process. In general, the analysis must include areas identified for evaluation where fire, flash fire and explosion hazards exist and identification of safe
22 Wood Bioenergy

/ August 2020 operating ranges (including identification of currently in place safeguards and recommendations of additional safeguards).
As a refresher, Nichols touched briefly on chapter 5 of the NFPA standard, section 4, which articulates the determination of explosibility. In the event that explosibility of dust is unknown, the standard allows for three approved tests to be done— which includes the “go/no go” screening test methodology described in ASTM E1226. Additionally, as part of the 5.4 standard, owners/operators are allowed to use the worst-case characteristics of various materials being handled as a basis for the hazard analysis.
As required by 7.3, each part of the manufacturing process that could cause combustible dust to be present shall be evaluated, including potential intended and unintended combustible dust transport; fugitive combustible dust emissions and deflagration propagation. Manufacturing buildings are also included in this particular subsection of the standard, which includes each building or building compartment where combustive dust is present shall be evaluated, and the analysis must address potential combustible dust migration between buildings or building compartments, as well as potential deflagration propagation.
Nichols noted that as part of 7.3, the NFPA includes very specific language on housekeeping as it relates to dust accumulation. The evaluation of dust deflagration hazard in a building or building compartment shall include a comparison of actual or intended dust accumulation to the threshold housekeeping dust accumulation that would present a potential for flash-fire exposure to personnel or compartment failure due to explosive overpressure. Threshold housekeeping dust accumulation levels and nonroutine dust accumulation levels (like from an upset condition) should be done in accordance with the NFPA standard.
In closing, Nichols pointed out that the NFPA standards are the primary point of reference for OSHA
and the EPA, as well as insurance underwriters and other assorted authorities that might have jurisdiction over a facility. Additional information, including the exact language can be found on NFPA.org, or by reaching out to spark detection and fire mitigation equipment suppliers and insurance underwriters.
Wrapping up the session, Greg Bierie, Sales & Technical Marketing Specialist, Benetech USA, gave his talk, Total Dust Management—Production Done Safely. Bierie gave an overview of Benetech USA and the tools and solutions provided by the company to reduce dust, prevent spillage, improve material flow and ensure compliance with OSHA, MSHA, EPA and NFPA. Bierie then discussed two major dust explosion incidents in BC in 2012 (Babine Forest Products, Burns Lake, and Lakeland Mills, Prince George) where facilities were destroyed; there were four fatalities and over 40 injuries. According to the findings of Work Safe BC both incidents were because of wood dust acting as a fuel following explosions originating in spaces where conveyors were receiving and moving wood waste. Bierie asserted those incidents gave the industry a chance to change past thinking that one piece of technology or one piece of equipment will fix “it.” Now, he said, Benetech’s approach will be about integrating the right tools for successful solutions—which include a sustainable approach to dust and spillage mitigation.
Bierie went through each of Benetech’s integrated tool solutions, noting before and after progressions in plants, as well as drawings and models that show the benefits of using Benetech branded engineered transfer systems. While Bierie cited Benetech specific systems, of which there are over 450 installations, the advantages of using a transfer system apply to all available systems, which include reducing the generation of dust, increasing the wear liner life, reducing product degradation, reducing plugging, reducing maintenance cost and improving overall workplace safety.
Bierie moved quickly to talking about load zone components and load zone solutions offered by Benetech that increase plant safety, reduce conveyor maintenance and increase operating efficiency. Next up was Benetech’s dust suppression options, of which the company says it can reduce dust levels by over 90% with the added benefit of reducing moisture levels in biomass plants to less than 2% by weight. With lowered water usage, improved application and lowered maintenance of the spray system and cleanup in the conveying system, Bierie says mill personnel have compared the difference to night and day.
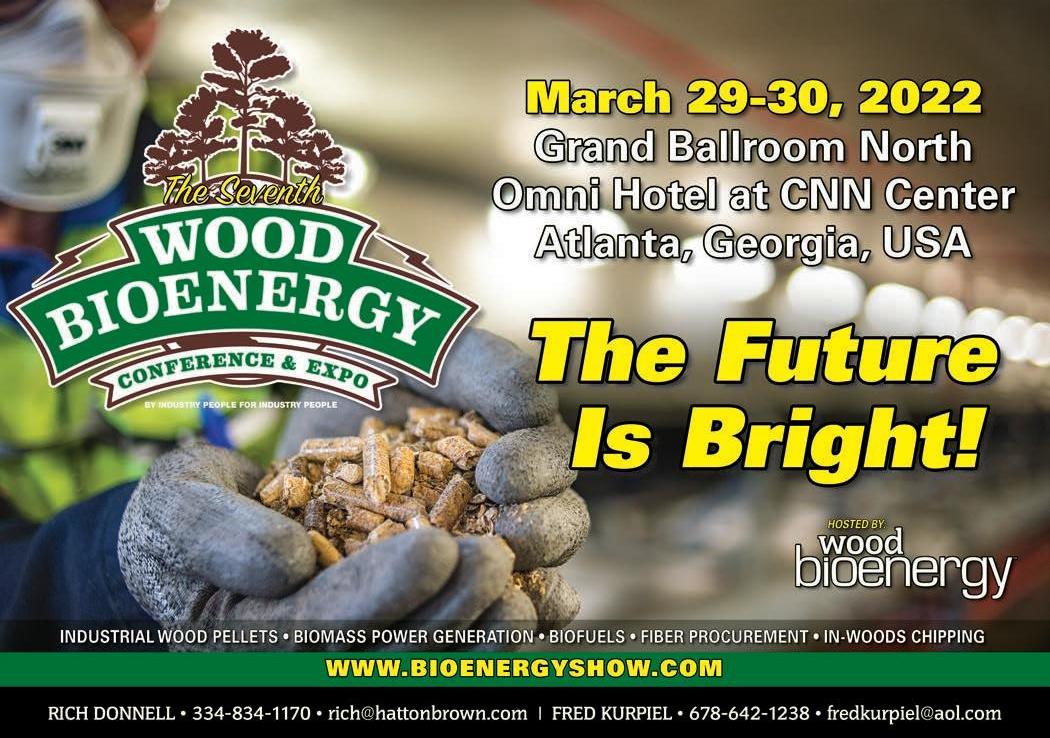
August 2020 / Wood Bioenergy 23