
7 minute read
ASSET PROTECTION
■ asset protection
FLAMEX
Wood pellet production involves operations that are often conducive to the generation of sparks and fire. Size reduction processes, such as the hammermilling of dry wood material, are often a source of sparks that are transported in the material flow through the pneumatic system. Fires and burning embers may also result from the drying process due to the presence of high temperatures and possible upset conditions with the dryer. Other processes such as pelletizing, pellet cooling, screening and product load out may also produce ignition from sparks, overheated pellets and mechanical friction sources. If not addressed, fires and explosions resulting from normal production processes can have devastating consequences for a business large or small. This is an ever-present problem in the industry that requires continual management to ensure workplace safety, asset protection and business continuity. The design, installation, operation and maintenance of automatic fire protection systems play a critical part in the effort to mitigate these hazards. Spark detection and extinguishing systems have long been recognized by the industry and loss control community as an effective measure in the prevention of fire and explosions in dust collection and air filtration systems. Introduced to North America in the late 1970s, the Flamex spark detection and extinguishing system became the first system of its type to gain a factory mutual approval. These systems have proven to be an invaluable part of an overall protection design in wood pellet facilities.
Flamex Inc. has been involved in protecting industrial facilities from the hazards of fire and explosion for over forty years. We specialize in the prevention of ignition in facilities that handle combustible dusts. Our experience in the industrial wood pellet industry has given us a deep understanding of the risks inherent in the production process and how to address them in a manner that eliminates or minimizes production downtime.
As part of a major global fire protection organization, Flamex Inc. has a wide range of detection and suppression components available to meet the specific protection requirements of varied applications that may be present within a single manufacturing facility. We continually strive to improve our product offerings in step with the latest technological advances.
FAGUS GRECON
Preventive fire and explosion protection using new detection technology to identify dangerous ignition sources in and around a dryer. Common causes of fires are heat, sparks, embers, and hot particles. One of the most efficient measures to prevent fire or dust explosion is the early identification of the ignition source. Sparks and embers are often the source of larger fire and explosion events. Preventive fire and explosion protection is an important measure, not only to protect production, but also the company and the people working within. Fagus GreCon’s new DLD 1/9 Spark Detector offers additional protection to industries with new intelligent detection technology (IDT). IDT not only identifies hazardous moving ignition sources before a fire breaks out, but the DLD 1/9 detector is also able to differentiate between dangerous sparks or harmless incidence of extraneous light due to leaky/damaged pipes or an opening of an inspection flap. The system provides excellent preventive protection, as it does not wait for an actual fire or explosion to erupt. The system prevents the development of a fire or explosion by the early detection and elimination of the ignition source. With a GreCon system it is possible to detect and eliminate ignition sources before a fire or a dust explosion occurs. IR detectors monitor the conveying paths and activate high-speed water extinguishing within milliseconds. The diversion or shut-off of product flow is also an option if extinguishing with water is not possible for the application.
Fagus GreCon’s protection concept allows for protection without production interruption, that not only help protect in and around the dryer and grinder, but also protects downstream processes as well.
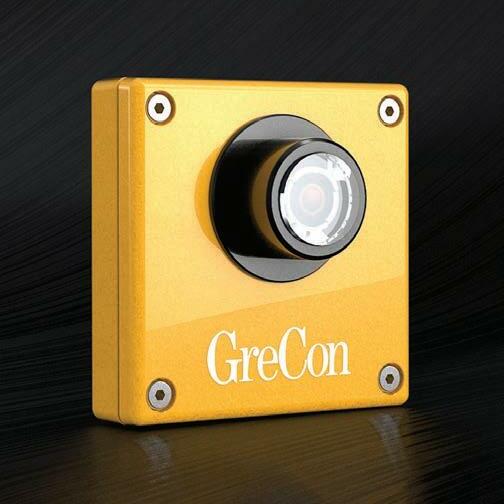
18 Wood Bioenergy / October 2022
IEP TECHNOLOGIES
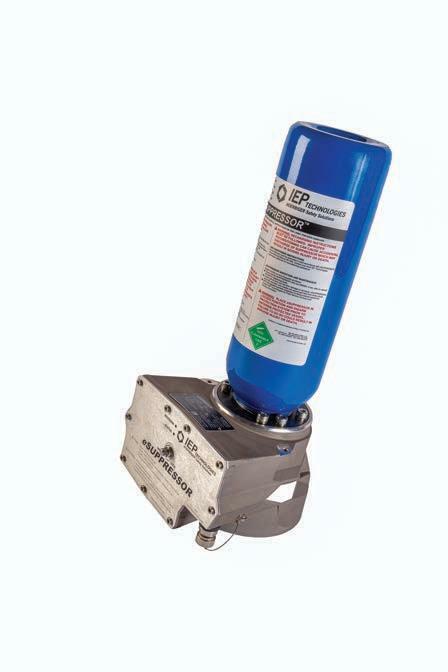
The new eSuppressor by IEP Technologies is a high-rate discharge extinguisher used for explosion suppression and isolation systems. Its electro-mechanical actuating mechanism, using no pyrotechnic devices, is unique to the industry. The eSuppressor features include pressure monitoring, lock-out/tag-out capability and LED indication of device status. A key benefit is that all safety functions are fully monitored, which is not possible for any device employing pyrotechnic actuators. The eSuppressor has full redundancy and third party SIL 2 certification.
The eSuppressor is designed to discharge suppressant in milliseconds within a process vessel or to mitigate the propagation of flame through interconnected ductwork. It is used in conjunction with IEP Technologies’ range of control panels and detectors. IEP Technologies sophisticated computer modeling techniques determine the quantity and size of suppressors to be used. These techniques predict reduced explosion pressures based on actual process conditions and detector settings.

October 2022 / Wood Bioenergy 19
■ asset protection MID-SOUTH
Some equipment in a plant’s process is seen as directly responsible for making product and adding to the bottom line. Other equipment is viewed as necessary support. And then there is dust collection equipment—frequently considered only as a cost which gets little attention unless a safety problem occurs. In our 50+ years in the wood industry, Mid-South Engineering has seen both healthy and neglected dust collection systems. We have the ability to help you review your dust collection considering the safety of plant personnel and the protection of assets while potentially reducing the costs related to system operation. Our expertise and experience allows us to troubleshoot and engineer industrial-grade solutions for deficient dust control systems for a variety of industries. Typical problems can include, a control system not meeting current needs; out-of-balance issues, either due to poor original system design or system modifications; systems compromised by material accumulation, and/or ventilation or filtration equipment whose performance has deteriorated over time.
A properly designed and maintained dust control system will be more operationally effective and efficient using less air than a poorly designed system. Increased dust collection effectiveness means reducing process area dust accumulation mitigating the safety risks associated with airborne combustible and/or harmful dusts. Further, a reduction in airflow equates directly to less fan horsepower utilized, thereby reducing operation expenses.
In addition to improved safety and power demand savings, a properly optimized system may also result in benefits to your employees’ personal health and productivity. The quality of the breathable air in a manufacturing environment has real costs.
The EPA has estimated that the costs of healthcare and lost productivity from workers exposed to poor quality air exceeds tens of billions of dollars each year. OSHA similarly reports that reduced worker efficiency and increased absences because of air quality problems cost U.S. companies upwards of $15 billion annually.
A poorly optimized dust and fume control system has a cost in both operational efficiency and employee health. Mid-South Engineering can provide design services to address these problems and put you back on track for maximized efficiency and performance.
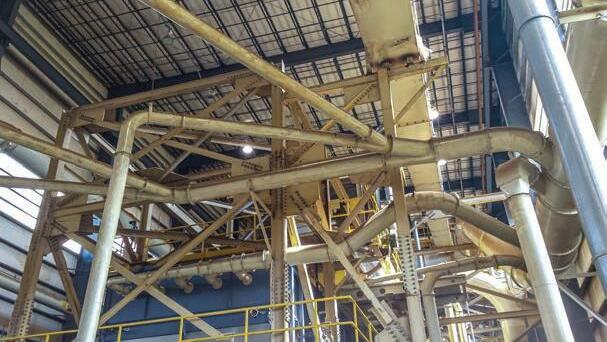
SONICAIRE
In the wood industry, sawdust is inevitable. Because of this, you must mitigate the hazards of fugitive dust in your facility. You already know that wood is highly flammable, but the accumulation of wood dust can be even more dangerous. As soon as your dust dries, it becomes combustible, meaning you must take extra care in its management. It builds up in your rafters, on your equipment, and hides in places you may never consider. To remove it, you have some options which vary in efficiency. You can clean it yourself or hire a crew, but each option comes with steep costs. Daily management of dust is a strain on your operating procedures that can cost thousands in cleaning costs and lost production. It’s far easier (and cheaper!) to prevent the dust from ever reaching those hard-to-reach places. SonicAire fans are engineered to keep combustible dust from becoming a problem. Using BarrierAire technology, SonicAire fans prevent dust from settling in hard-to-reach areas, making it easier to keep your facility clean and safe. Dust settles back to the ground where staff can quickly sweep it up as part of your facility’s daily housekeeping. No extra work is required. SonicAire recognizes your facility is unique. That’s why we have expert engineers create a customized plan just for you, ensuring your SonicAire fan system addresses problem areas and that fugitive dust is a worry of the past. You’ll have the opportunity to ask our engineers all your questions, and with the zone control kit, you’ll fully control exactly where your fans blow.
Of course, your facility is responsible for complying with OSHA regulations in many areas, including dust control. Fortunately, with SonicAire, dust control is one item you won’t have to worry about. We guarantee compliance on dust, so once you install these fans, you won’t ever have to worry about it again.
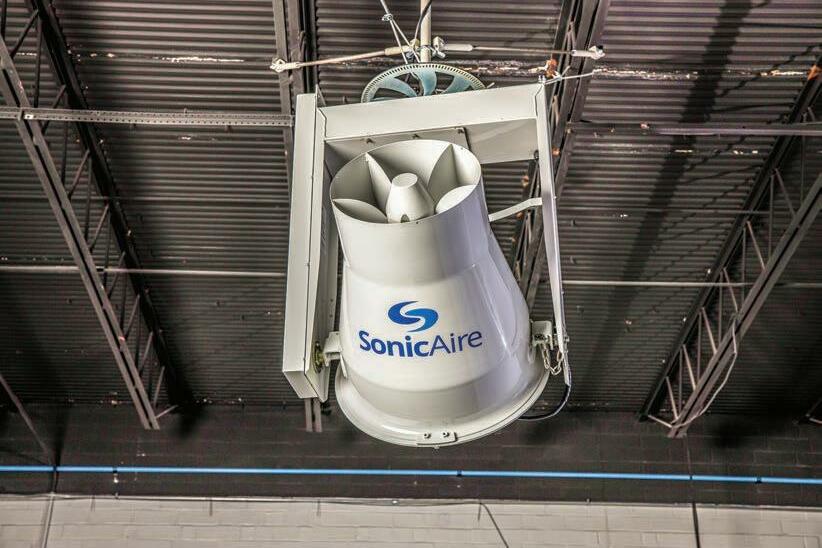
20 Wood Bioenergy / October 2022
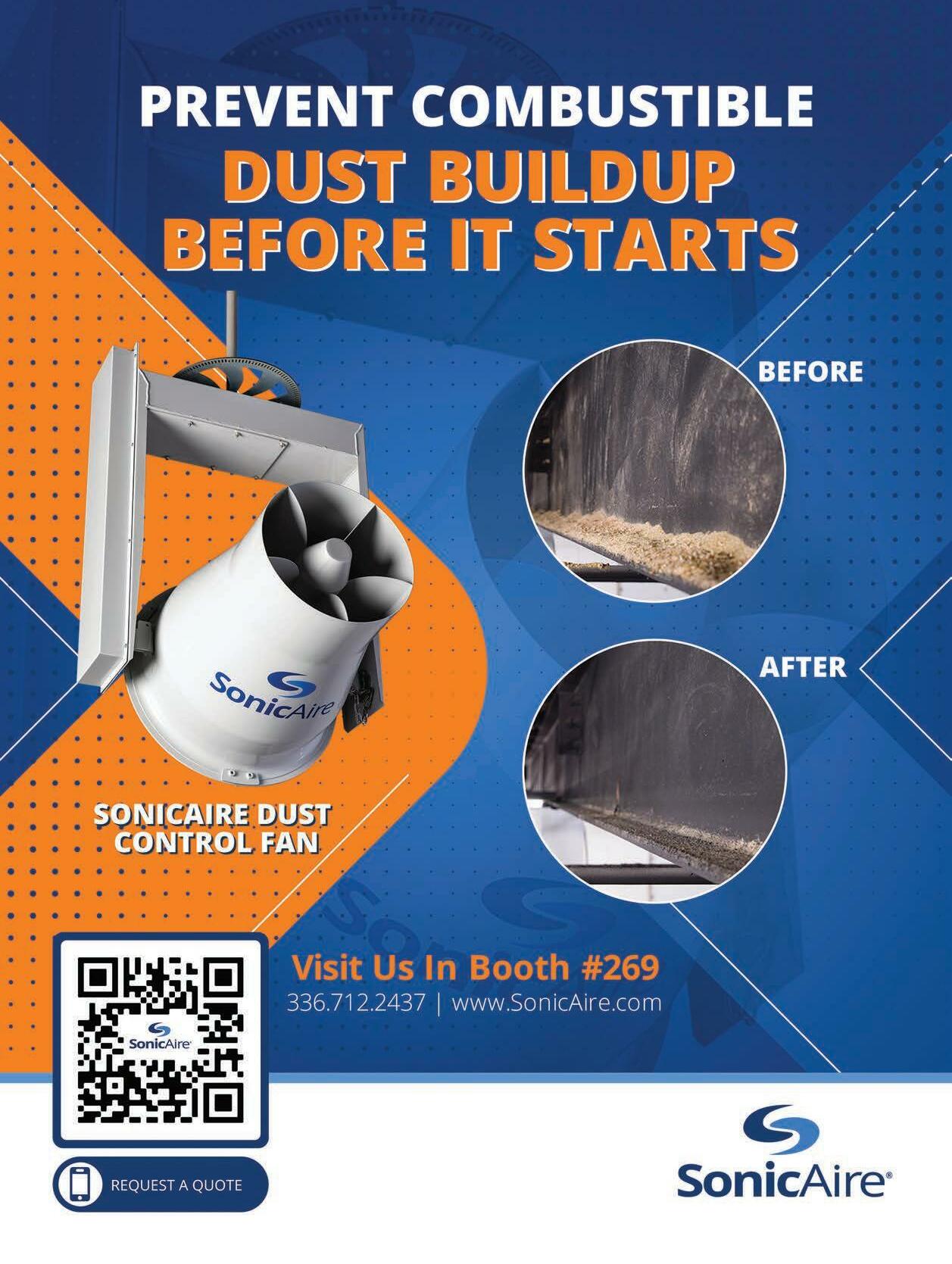