
7 minute read
Low alfalfa yields can be tiring
Mike Rankin
by Brian Luck
Advertisement
HAVE you ever driven past an alfalfa field a few days after harvest and noticed distinct tracks where the equipment traveled? Visually, it looks like the plants where the tires ran might have been damaged. They often appear stunted compared to the remainder of the field.
Alfalfa harvest, either for hay or silage, requires an array of machines to complete. The process and equipment we currently use for alfalfa harvest is efficient; however, these machines are applying pressure to the soil and the regrowing plants and crowns, which may potentially reduce alfalfa yield. Researchers at the University of Wisconsin-Madison are working to answer the question: “How much damage to alfalfa are we causing during harvest?”
Our previous research studied machinery movement during silage harvest, including rye, alfalfa, and corn, over an entire season and found that approximately 1,300 round trips between the storage site and the field were made by transport vehicles. In most cases, the transport vehicles being used were trucks designed for on-road travel with tires inflated for highway use. Recent research estimated vehicle weights and their ground pressure applied during alfalfa harvest. It showed that compared to machines with tires designed for agricultural use, on-road-designed vehicles applied three times or more the ground pressure applied by agricultural machines.
Armed with this information, a twopart study was developed to assess machinery traffic impact on alfalfa yield and to determine how much of a commercially harvested field was impacted by machinery traffic during a single year of alfalfa harvest. First, a plot study was conducted at the Arlington Agricultural Research Station involving three different tillage treatments at planting along with seven different wheel traffic applications at each harvest.
The tillage treatments were no-till, spring tillage only, and fall and spring tillage. Wheel-traffic treatments were designed to simulate both alfalfa and hay harvest with traffic being applied at harvest and different combinations of 24- and 26-hours post-harvest for silage and 48 and 72 hours post-harvest for hay. Yield was measured at each harvest with a plot harvester and wheel traffic was applied to the entire plot with a self-propelled swather weighing approximately 13,000 pounds.
The second aspect of this study installed Global Navigation Satellite System (GNSS) data loggers on every machine involved in the alfalfa harvesting process. Data was collected on one-second intervals and mapped using Geographic Information System software. The footprint of each machine was applied to the path it drove within the field to determine the percent area of the field that saw machinery traffic at least once during each alfalfa harvest. Results presented here are preliminary due to only two of the three years of data being included in the reported data set.
Significant yield loss
Preliminary results from the plot study described above showed that a single pass from the 13,000-pound swather reduced yield, but the change was not statistically different. Across the tillage treatments, statistically significant reductions in alfalfa yield were observed when the time between applied traffic and harvest were the greatest. These treatments were the simulated hay harvest with wheel traffic applied at 48- and 72-hours post-harvest. Preliminary average reductions were approximately 0.64 tons per acre across two growing seasons.
Quantifying the area of the field impacted by machinery traffic via GNSS sensors also showed interesting results. Cuttings with the highest yield, generally associated with second alfalfa harvest during the growing season, showed the greatest amount of the field impacted by machinery traffic. Harvests with lower yield showed less of the field impacted by machinery traffic. This result was expected due to the reduction in transport vehicles needed to move material away from the self-propelled forage harvester.
The average percentage of the field having machinery wheel traffic over two harvest seasons was 49%. In a worst-case scenario coupling these two studies, nearly half of the acres within an alfalfa field could have greater than 0.5 tons per acre yield reduction due to machinery traffic.
Some recommendations to minimize the impact of wheel traffic on alfalfa regrowth and yield would be: • Consolidate machine travel paths to in-field roads. • Minimize the number of on-road truck tires in alfalfa fields. • Check that tire pressures on all vehicles are correct for the tire (both agricultural and on-road tires) to ensure proper tire wear is maintained and ground pressure is minimized.
Following these steps, especially maintaining in-field roads, will reduce the percentage of the field impacted by machinery traffic and maintain yield potential during the alfalfa growing season. •
BRIAN LUCK
The author is an associate research/extension professor with Mississippi State University based at the Coastal Plain Branch Experiment Station in Newton, Miss.
Mike Rankin
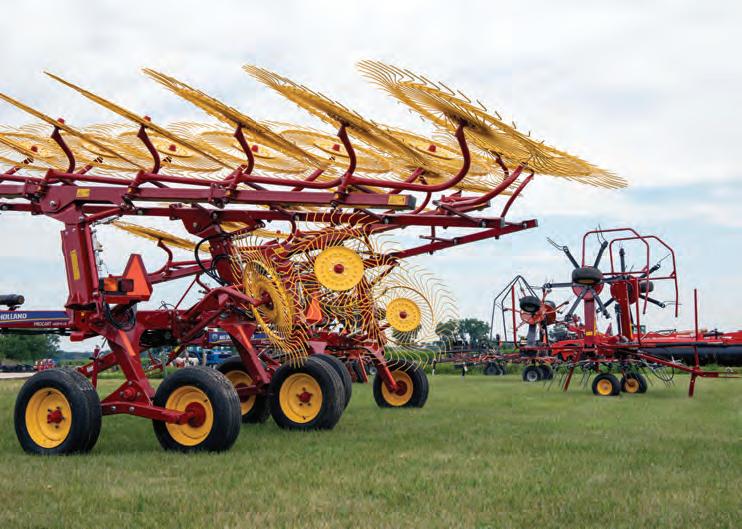
Breaking out the crystal ball
IT’S been fun during the first half of 2022 in the equipment industry (insert sarcasm here). For almost two years, we have seen unprecedented price hikes in all aspects of the agricultural industry. I wish I could tell you that the tables are turning and heading the other way, but that will probably have to wait for a 2023 column!
For the most part in 2020, we operated using the equipment that was already manufactured and with parts that were on warehouse shelves. In 2021, the equipment industry started to realize the shortcomings of “on-time” production schedules, coupled with delivery issues. Now, in 2022, combine the labor shortages, lack of parts to build units, and still strong demand for new products, and it has led us to a precarious and undesirable situation.
High school economics
Let’s figure out how we got here, and I’ll give you my opinion where we are going in the next six to 12 months. Most of the issues fall back to high school when everyone first learned about supply and demand. When everyone was at home during the second quarter of 2020 with a little extra money in their pocket, the landscape side of the equipment industry went crazy. This strong demand remained all the way through first quarter of 2022.
Once our food supply began to tighten in 2020, this led to the eventual rise in the commodity markets. These commodities have remained strong through this summer. There has been some retracting in the cotton markets, but corn, wheat, and soybeans continue to be high-value crops. With the commodities only having a modest price from 2015 through 2020, this newfound wealth led to a great number of farmers who were anxious to upgrade their equipment once markets headed north. The big agricultural equipment demand remains strong as this is written, and I believe will most likely continue through year’s end.
With both landscape and large agricultural equipment being in record demand at the same time, this led to unprecedented challenges for all aspects of the equipment industry. Most manufacturing facilities have outsourced many components of their equipment through the years. This has always been the most cost-effective way to produce these specialty items. Here, I’m referencing components such as hydraulic pumps, valves, fuel pumps, injectors, and even tractor cabs. But with the new labor shortages, post-COVID-19 has left most of these companies struggling to keep up and eventually getting way behind.
Some of the parent manufacturers have brought a portion of their production back “in-house.” As of this summer, they are starting to make a little progress on equipment being consistently produced.
Where are we heading?
With interest rates and inflation rising rapidly, I believe the consumer/ landscape product demand will begin to slow in the last half of 2022. This will allow the manufacturers to get some units in stock and back on dealers’ lots in time for the spring selling season. Personally, I would be surprised if costs remain at their current levels and expect demand will subside in 2023 compared to what we have seen in the lower horsepower tractor market the past few years.
In the large agricultural equipment market, orders are currently being placed for summer and fall of 2023. For the most part, production is still behind when compared to prepandemic numbers. I believe demand will continue to outpace production well into next year. The rising cost of equipment and interest will definitely play a factor, but if customers can harvest a bumper crop of $7 corn, $15 beans, and $12 wheat, there will undoubtedly be some equipment traded by year’s end. I would hold on to equipment until the new machine is sitting in my shed. Delays are still the norm for the foreseeable future. Planning a year ahead will likely become a normal practice with equipment purchases for progressive farmers in the next few years. Hope this helps, and have a great fall harvest. •
ADAM VERNER
The author is a managing partner in Elite Ag LLC, Leesburg, Ga. He also is active in the family farm in Rutledge.