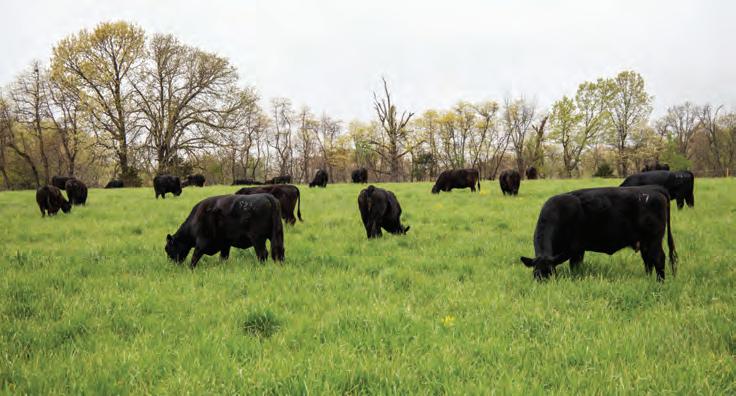
9 minute read
FROM SPECIAL OPS TO A SPECIAL FARM
by Mike Rankin
RON Locke has been to almost every country in the world, but few people knew exactly where he was or why he was there. He won’t tell you — even if you ask. But for the past 24 years, it’s been much easier to locate the amicable and loquacious cow-calf producer. You’ll find him in the foothills of Missouri’s Ozark Mountains near the rural community of Long Lane; it’s the only so-named community you’ll find on a U.S. map. Locke’s childhood was spent just outside of Chicago in urban Hammond, Ind. When he was 8 years old, he spent two weeks of the summer visiting his aunt and uncle’s beef farm in Missouri. He never missed another summer of vacating the city for the country and eventually stayed in Missouri for the entire summer between school years. According to Locke, “I got hooked on farming and beef cattle pretty early. I didn’t know it at the time, but I was being groomed to farm.” He still has his uncle’s 8N Ford tractor that he learned to drive as a kid.
Advertisement
Immediately after high school, Locke married his high school sweetheart, Judi, and within two months, packed up for their trek to a beef farming career. “We rented an apartment in Buffalo, Mo., not far from my uncle’s place, and I was going to be a farmer,” Locke recalled of his thought process at the time.
Into the wild blue yonder
The young couple got a loan from the bank and bought 40 acres next to his uncle’s farm. Locke soon learned that a steady paycheck wasn’t part of the deal, and they needed money to live on. While visiting with a different uncle who was in the Air Force, Locke became convinced that he, too, should enlist and build some financial equity.
Locke joined with the promise that he’d be trained as a heavy equipment — think bulldozer — operator. This was a skill that would be useful when he came back to the farm. While still in basic training, he was offered the opportunity to become an explosives specialist. He accepted the offer, and out of basic training in 1973, Locke was sent to Korea for a year to blow up unused munitions that remained from the Vietnam War. As you might expect, Locke interjected, “We had a blast.”
Once back in the states, Locke was trained as an Air Force combat controller. This was a group known as the “quiet professionals.” Little of what they did was public knowledge, and Locke led a life of secrecy for 26 years, providing air cover and support for units such as Delta Force and the Navy SEALs. Not even his wife and young family knew where he was, although they, too, found themselves living at various military bases throughout the world. “After retirement from the Air Force in 1998, I was ready to come back to Missouri and grow grass,” Locke reflected.
Learning grass and beef
Upon returning to the Show-Me State, Locke and his family had a recently-built house on his 40 acres, a pond that was dug before joining the Air Force, and lots of toxic tall fescue grass. His aunt and uncle also had their farm, but they were elderly by this time, in declining health and needing help, which was a major reason why Locke retired from the Air Force and came home.
In the military, a lot of time is spent training, either in the classroom or field. Unfortunately, there wasn’t a coordinated boot camp for grazing beef cows, at least at that time.
“I was always a big believer in education,” Locke noted. “I immediately hooked up with extension and the USDA. They put me on to the Show-MeSelect Replacement Heifer Program, and I bought a dozen animals at their sale to start my herd.” Eventually, he started operating his uncle’s 200 acres as well.
Early on, Locke attended a grazing school and became sold on rotational grazing. Like most beginning graziers, he admitted to making his fair share of mistakes and chuckled as he recalled the first fence he built. “I had posts every 6 feet with three strands of electric wire. It’s still out there, but now I build a fence with posts every 90 feet and one strand of polywire. One strand is all that’s needed to turn a cow if you have a good charger,” he added.
After years of trial and error, the Air Force officer turned beef producer is steadfast in his grazing philosophy. “I don’t understand why a cattle producer wouldn’t rotationally graze once the water infrastructure is in place. The only other limiting factor is time, and that’s only 10 minutes a day to move a polywire. Other than that, there are no excuses, and the benefits are ten-fold.”
Through the years, Locke has added some unique features to his beef grazing system. He has lanes that easily allow him to move cattle and get to paddocks that are ready to graze. The water infrastructure is also such that it can be tapped from any paddock, regardless of size. Both above and below ground waterlines are used.
For years, providing shade in some of Locke’s paddocks proved to be a in the Air Force, is now applied on his farm in the Ozarks. Locke’s holy grail book contains historical information on every field and paddock, including soil test data that is updated every three years.
To estimate and monitor forage availability across the farm, Locke uses a front-mounted sensor on his UTV, which is coupled to a software app called PaddockTrac from the University of Missouri. With the forage availability challenge and limited his ability to move cows to certain areas during the hot Missouri summers. Trained to be a problem solver, Locke found his solution with a heavy-duty portable shade unit that he’s been utilizing for the past four years. As the cows move, so does the shade, which he can hook to his utility task vehicle (UTV), move, and set up in a matter of minutes.
These days, the Lockes’ R&J Ranch consists of 400 acres with multiple fields and paddocks. He’s had as many as 100 brood cows, but currently the herd consists of about 50 cows plus some registered Black Angus bulls that he sells for breeding. His calves are backgrounded for at least 60 days before being sold. The fall-born calves are genomic tested to determine which bulls or heifers will be kept and which ones will be sold after backgrounding.

The holy grail
Military personnel usually don’t go anywhere without their dog tags. On R&J Ranch, Locke doesn’t make a move without what he calls his “holy grail book.” The need for detail and Locke’s desire for as much information as possible, which was no doubt learned while estimates, the app generates a grazing wedge graph to help guide cattle movements. Locke strives to keep his cool-season grass paddocks below 2,000 pounds of dry matter. “At that point, I feel I’m losing quality,” he said. All of this information is kept in his holy grail book. Locke also tracks cattle move- continued on following page >>> ment, inventory, and performance with the CattleMax record-keeping system.
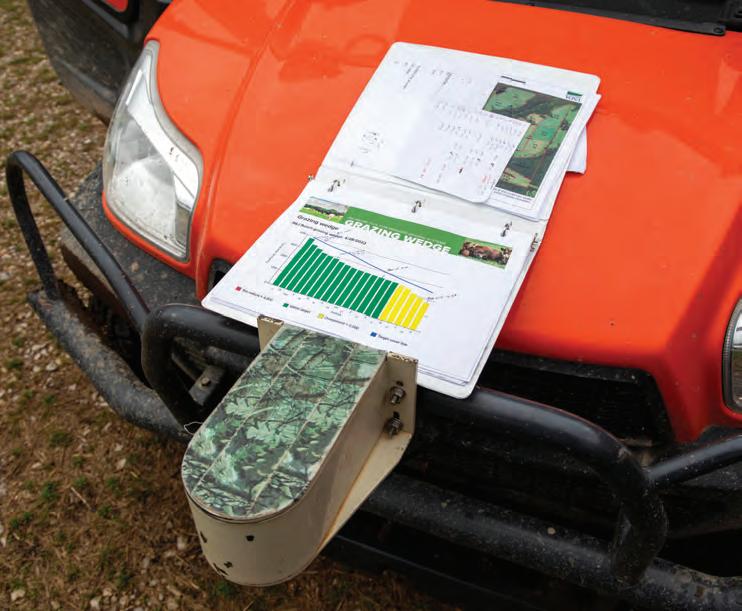
Recently, Locke began working with USDA Agricultural Research Service soil scientist Alan Franzluebbers to monitor the soil health and quality of his paddocks. Several sets of soil samples have been taken in the past few years. This information, too, resides in the holy grail book and helps guide nitrogen applications on pastures. “I find this information extremely useful and interesting, but there’s still a lot to learn in how it can be applied and interpreted,” Locke noted.
Goodbye toxic fescue
Like most mid-South farms, toxic Kentucky 31 tall fescue comprised nearly all of Locke’s initial forage inventory. That remained the case up to the point where he attended a seminar on how to renovate pastures with new novel endophyte fescue varieties. At the same program, he was shocked to learn the amount of production he was losing by grazing his toxic fescue.
Before making the financial commitment to convert his pastures to novel endophyte varieties, the meticulous Locke was determined to find out how bad his fescue really was. After all, it’s important to know your enemy. Following detailed instructions, he collected plant crowns from numerous pastures and drove the samples to the University of Missouri in Columbia.
“My samples were hot, nearly all above 85% toxic,” Locke said. “That was the clincher, and starting in 2005, I vowed to kill and reseed a field per year to a novel endophyte variety until I got it all done. I still have a few (fields) that are not done yet, but they aren’t that productive anyway, and I just manage around them.”
Locke has perfected his renovation technique through years of terminating Kentucky 31. “I spray with glyphosate when the fescue is boot-high in May,” he explained. “In June, I seed pearl millet, graze it once or twice, spray again after some regrowth, and then broadcast seeds the novel endophyte tall fescue in early September. I don’t graze it in the fall, flash-graze once in the spring, then it’s usually in full production.”
Locke stockpiles some of his fescue each year, applying about 60 pounds of nitrogen per acre in mid-August.
Warm-season success
Novel endophyte tall fescue isn’t the only thing that currently comprises his farm’s forage base. Any good battle planner knows you need Options B and C. After all, the toxic fescue issue is one thing, but there are still the Big D’s to contend with — dormancy and drought. That’s where warm-season grasses come into play.
Locke uses the same tall fescue establishment approach for seeding perennial warm-season pastures of bluestems and indiangrass, but he doesn’t seed until December. The seed is mixed with fertilizer, broadcasted on the field, then rolled with a cultipacker to enhance seed-to-soil contact. The native warm-season grass doesn’t germinate until the next spring. He currently has about 60 acres of perennial warm-season grasses in production.
“Plateau herbicide revolutionized establishing warm-season grasses,” Locke said. “I usually cut the warm-season grass fields for hay once in early July, before heading, and then graze them in late September or October.” He also has a field of eastern gamagrass, which was established in 2007. “I strip graze the gamagrass with a back fence, and by the time I get across the 14-acre field, the first strip is ready to graze again. That stuff really grows fast,” he exclaimed.
Another recent feature on the R&J Ranch is milo (sorghum), which Locke now plants each year on a designated 8-acre field. After heading and grain development, it’s strip-grazed and feeds 50 cow-calf pairs for nearly 60 days. It’s during this time that the fall-stockpiled fescue is growing.
Lespedeza love
Legumes are also on the ranch’s roll call. Locke frost seeds lespedeza every spring, although not every paddock is frost seeded every year. He is especially partial to Legend lespedeza, a warm-season annual and prolific seed producer. Locke has some set survey sites that he photographs each spring and fall to determine legume status and whether a particular paddock needs targeting for the next year’s lespedeza frost seeding. He explained that he rarely needs to frost seed clover, as white, ladino, and red clover seem to be ever present. “If you graze clovers right and don’t overgraze, they will always come back,” he noted.
In the spring, Locke likes to flash graze, beginning with his few remaining Kentucky 31 pastures. “I want the cows to get a bite and keep moving,” he said. “Hopefully, we can prevent some of those seedheads from developing, which are really toxic.”
His pride and joy
Although Locke can easily be classified as an early adopter of technology and operator of a high-end grazing system, his pride and joy remains an Allis-Chalmers Roto-Baler. “It’s worth its weight in gold,” Locke asserted. He then continued to explain why the vintage machine still holds value beyond an antique farm equipment show. “When we get rain in July, there’s usually a tremendous amount of lespedeza in August. I will bale with the Roto-Baler, leave the bales in the same field, and use these fields for bale grazing in the winter after the stockpiled fescue has accumulated around the bales. There are generally only one or two cows around a single bale, causing very little damage to the pasture. It’s amazing to watch cows grazing these fields. Some of them go right to the lespedeza bales while others much prefer the stockpiled fescue,” noted the observant cattleman.
Locke also has a standard-sized round baler. The winter of 2022 to 2023 will be the first one that he tries bale grazing the larger bales. Because Locke artificially breeds his cows and heifers with a timed synchronization protocol, he needs some stored hay to feed when he brings his herd up to a small pasture next to his corral and working facilities. He also unrolls hay when needed so young calves have a dry place to lie down during periods of ice or the occasional Missouri snowstorm.
Locke has a lot of life stories and experiences that he cannot expound upon with any detail. That’s just the way it is for an Air Force Special Ops Command combat controller. Ironically, the polar opposite is true regarding his experiences as a beef producer and pasture manager. Few people are willing to share more than Locke when it comes to his farm operation and decision making. Through the years, he has benefited from others’ knowledge, and he is more than willing to reciprocate. Locke has been a featured speaker at numerous grazing meetings and hosted many educational events on his farm.
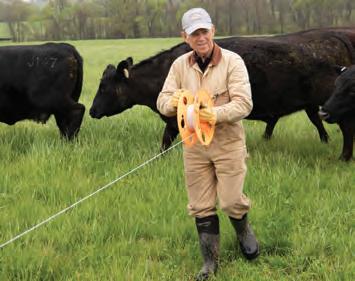
The Missouri farmer attributes much of his farm success to education, training, and experience — the same things that served him well in his military career. However, Locke readily admits that there’s always more to learn and try. And when he does uncover something new, you’ll probably find it in his holy grail book. •
