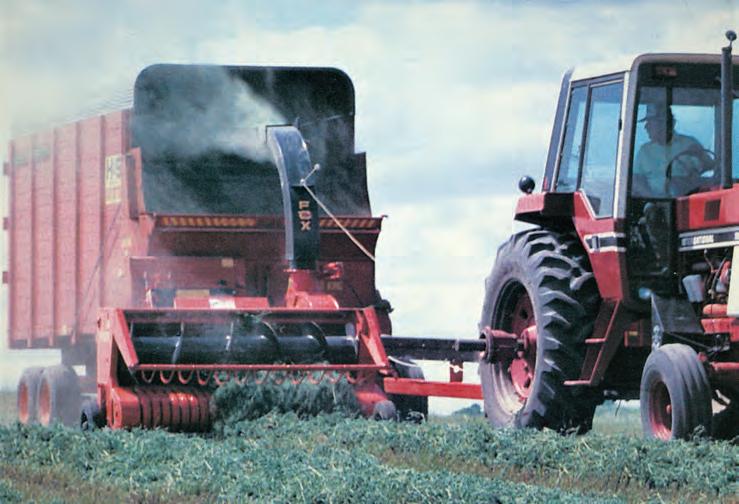
26 minute read
Forty years of forage equipment progress
Xxxxxx xxxxxx xxxxxxx xxxxxx xxxxxxx xxxxxx xxxxxx xxxxxxx xxxxxx xxxxxxx xxxxxx xxxxxx
Editor’s note: Kevin Shinners has been an influential voice, inventor, and researcher during his 40-year career at the University of Wisconsin-Madison. Here, he looks back and chronicles the changes in forage equipment that have taken place during his career while also eyeing the future.
Advertisement
by Kevin Shinners
IN MANY ways, hay and forage equipment remains fundamentally the same as when I began my career 40 years ago, but today, equipment is more sophisticated, intelligent, and productive. In the next 40 years, engineers will continue to pursue new machine forms and adopt technologies to make hay and forage harvesting even more efficient and productive.
Cutting and conditioning
The biggest change has been the shift from sickle to disc cutterbars. Throughout the 1980s and 1990s, there was a steady move toward disc cutterbars. Now, sickle cutterbar machines are almost extinct. Much greater productivity has more than offset the greater expense of the disc mower-conditioners. End-wise transport now facilitate cutting widths up to 20 feet.
In 1981, windrowers had less than 80 horsepower (hp) and a conditioner and cab were not even standard. Today’s windrowers exceed 200 hp and can easily cut up to 20 acres per hour. Tractor-mounted, wide-area mowers now offer cutting widths in excess of 34 feet and can harvest over 35 acres per hour — more than four times the typical productivity of a windrower from 1981.
Guidance systems on tractors and windrowers have helped reduce fatigue and improve efficiency. Mower-conditioners are good candidates for autonomous operation, so we could see fleets of smaller width, electrically driven, autonomous mower-conditioners in the future.
Slow, inconsistent drying continues to frustrate hay producers. Despite much development effort, engineers have never been able to make substantial improvements to conditioners and hay drying. Current development efforts to enhance drying rates are limited, so we likely won’t see major improvements in this area in the near future.
Harvesting and storage
Forage harvesters still perform the same basic machine functions as 40 years ago, but the market has strongly migrated from pull-type to self-propelled machines. In 1981, there were nine manufacturers of pull-types, and now only two manufacturers remain. Self-propelled harvesters have grown immensely in size and complexity. The largest machine in 1981 had 325 hp and could harvest six rows. Current machines approach 1,000 hp and can harvest up to 12 rows.
The introduction of the kernel processor (KP) in the late 1990s was a game changing development. This mechanism enhanced ruminant starch utilization and allowed longer length-of-cut to enhance effective fiber from the stover fraction. There is no doubt that the KP helped accelerate the greater use of corn silage in the dairy ration.
Forage harvesters have not only increased in size but also sophistication. Near infrared reflectance spectroscopy (NIRS) technology now provides on-board accurate estimates of moisture content and forage constituents. Combined with mass-flow sensing, forage yield maps are possible. Bacterial inoculants can be accurately applied to enhance fermentation. Sensors and controls now guide the machine path and direct the spout to uniformly fill the transporter. None of these technologies were remotely possible in 1981.
Since forage harvesters unload continuously, autonomous harvesting will be challenged by the need to manage both the harvester and the continuous fleet of transporters that also need to be moved from field to storage via roadways. Improved fiber digestion from advanced processing systems is being investigated, which could fundamentally change how forages are harvested.
In 1981, the tower silo dominated the way we stored ensiled forages and there were an amazing 16 manufacturers selling forage blowers. Today, many tower silos stand as empty monuments to a bygone era. Bunk and bag silos dominate because of greater productivity at filling, lower capital and operating costs, and less daily aggravation. These storage systems helped expedite the adoption of
Pull-type forage harvesters dominated how silage was chopped in the 1980s.
KEVIN SHINNERS
The author is a recently retired professor and agricultural engineer from the University of Wisconsin-Madison.
the total mixed ration (TMR) system, perhaps the most important change in dairy nutrition in the last 40 years.
Baling
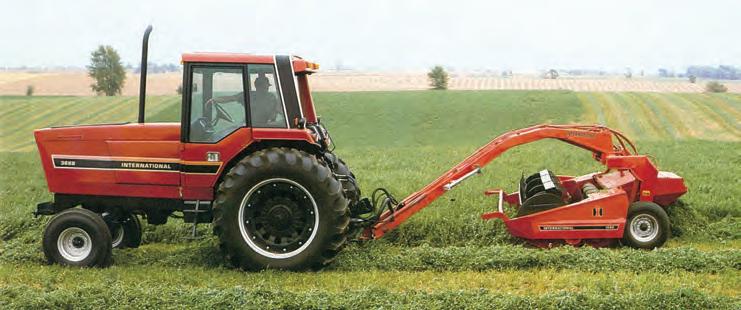
In 1981, baling was dominated by the small square baler (SSB). Large round balers (LRB) were beginning their ascendancy, and the large square baler (LSB) had only recently been introduced. There was a strong move to the LRB as manufacturers of loose hay stacking wagons declined to five and sellers of LRB climbed to 13. Today, the SSB is mainly used to make hay for the equine and export markets, and the manufacture of loose hay stacking wagons has vanished. The dominant way hay is packaged today is with the LRB.
Net wrap became widely available in the 1990s, and this development greatly improved productivity and reduced storage losses. Precutters now allow size reduction at baling, which enhances feeding and mixing. Most of our harvest machines have grown in size, but surprisingly, LRB bale size has not changed at all. We still use 4 or 5 foot wide and 4- to 6-foot diameter bales, the same sizes offered 40 years ago. Bale size has a large impact on the cost of gathering, storing, and feeding hay, so it is possible that new LRB sizes could be coming.
A major shift in hay packaging was the adoption of the LSB. The development of the intermittent feeder and double knotter were game-changing technologies that helped make these machines possible. Interestingly, offering smaller bale sizes — from the initial 4x4 to the 3x4 or 3x3 — helped spur greater use of the LSB. Steam application now allows hay producers in arid regions to bale even when dew is not present.
Wrapping and fermenting baled silage was virtually unheard of in 1981. But baleage is common now in response to producers’ desire to reduce the time between cutting and baling and their frustration with slow drying.
Non-stop round baling has been a Holy Grail for baler manufacturers for decades. Although a few such machines are now offered, they have not been widely adopted. Tractor-implement automation and a host of productivity improvements have reduced the demand for a nonstop baler. Self-propelled machines lend themselves to autonomous operation, but currently only one such baler is offered in the U.S. Autonomous bale gathering and staging may be more widely adopted before autonomous baling.
A typical sickle mower-conditioner from the early 1980s.
Hay conditioning
Side-delivery and wheel rakes dominated the way we windrowed hay for chopping and baling in 1981. Although wheel rakes remain popular due to their low cost and simplicity, side-delivery rakes are fading in importance. Mergers were unheard of in 1981 because they were unnecessary for the low-capacity pull-type harvesters that dominated chopping. It would have been unthinkable to produce the windrows that consolidate 30-, 60- or 90-feet of material that are used to satisfy the appetite of today’s large self-propelled harvester. Rotary rakes and tedders first developed in Europe are now common ways to improve drying rates and windrow crops.
Lost along the way
Systems that were in-practice in 1981 but have greatly faded include alfalfa dehy, in-field alfalfa cubing, in-barn bale drying, and loose hay stacker wagons. Some technologies promised great changes — like the rapid-hay drying maceration and mat formation system and the International Harvester alfalfa juice Probine system — but were unable to overcome technical and economic hurdles.
Technology and cost
Electro-hydraulic controls, engine load management, on-board moisture and constituent sensors, machine guidance, yield mapping, and inoculant application are just some of the technologies that have made equipment more productive, intelligent, and efficient. Application of these technologies is one reason why machine costs have risen greater than the rate of inflation (Table 1).
The cost of windrowers and forage harvesters has risen greater than the rate of inflation because these machines are so much larger, powerful, and more prowductive. Interestingly, when adjusted for inflation, the cost of tractors, windrowers, and forage harvesters is about $1,000 to $1,200 per hp, about the same in 2021 as it was in 1981. •
Table 1. Cost comparison of equipment in 1981 and 2021
Equipment Prices for equipment in 1981
1981 Dollars 2021 Dollars
Tractors
85 hp 190 hp
Mower-conditioners
Pull-type Windrower
Forage harvesters
Pull-Type Self-propelled
Balers
Small square Large round 31
71
14
31
27
98
13
14 94
218
43
96
82
300
41
44
2021
Actual
92
228
49
217
130
700
48
70
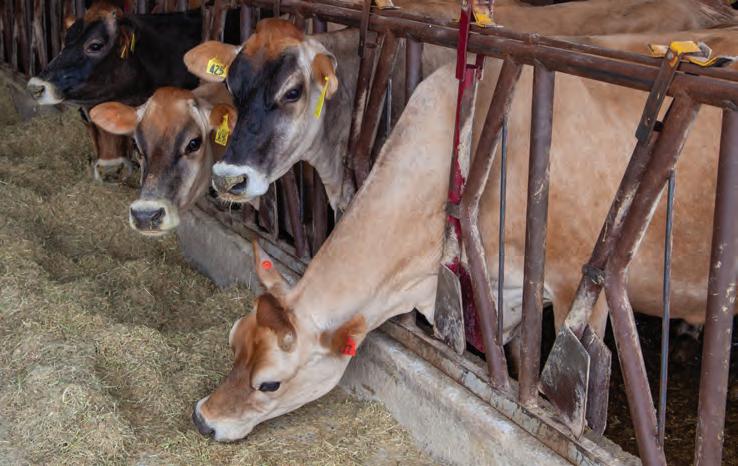
Uneaten forage is now more expensive
HOW much feed is left behind in the feedbunk? Is it mostly forage? Is it 1 or 2 pounds per head? What did that forage cost?
These questions demand consideration during a time when the market value of hay is at record levels.
Feeding alfalfa at its current price might be adding 8.5 to 17 cents to the daily costs of feeding each cow in a dairy herd. If you are feeding 500 cows, and if this leftover feed is discarded, this could be costing your operation $1,275 to $2,550 each month. So, what can you do if the cows are not consuming all the forage in their ration?
First, examine the refused feed. If it is mostly hay particles, look at their length. To stimulate rumination, particles only need to be 2 inches. Particles that are longer than this and left behind in the bunk are of little rumination value.
Next, look at the width or coarseness of the hay particles. Are the particles something other than alfalfa?
Other plant types may simply be unpalatable to the cows. If the alfalfa is contaminated with weeds or it has coarse stems, you may need to consider a different hay source. This might raise the cost of hay in the ration, but if the cows consume all of the particles, you can afford to spend a little more on purchased hay.
Using the example above, if you are feeding 10 pounds of alfalfa per head each day, you could spend $17 to $34 more per ton on your alfalfa and not raise your actual feed cost. If you are currently feeding 140 to 150 relative feed value (RFV) hay and discarding 1 to 2 pounds from the bunk, improving the hay quality may solve the issue. This could also boost milk production.
If improving hay quality is not the answer, further processing will likely reduce the particle size to 2 inches. This could be accomplished by grinding the hay through a smaller screen. If you are currently using a screen with a 4-inch opening, reducing to a 3-inch opening would likely be a solution.
Check your mixer
If you use your total mixed ration (TMR) mixer to process hay, it may be time to do some maintenance and replace worn knives. While replacing the knives, also look at the condition of the corners that move feed into the screw or reel. Many times, these parts are not replaced, and forage tends to remain in these areas rather than mixing into the load. Adjustment of these corners may also be necessary. Attention to the condition and setting of the corners is an important part of TMR mixer maintenance.
You may also need to extend the processing time for the hay. Sometimes adding as little as five additional minutes to the mixing time can significantly reduce hay particle size.
In addition to checking the particle size of the forage, you might need to consider the overall dry matter of the TMR. Recent research has shown that reducing the dry matter of the TMR of lactating dairy cows to 45% resulted in higher intakes and milk production. This is wetter than past recommendations, but it is working on many farms. Adding water to the TMR only requires a little more time, and the water is inexpensive.
With rising feed costs, many dairies have greatly reduced the amount of refused feed that is discarded or have utilized it for other animals. Feeding for a clean bunk is possible, but you will need to pay additional attention to hay quality and hay processing. Watch the feedbunk carefully or consider installing some game trail cameras along the bunk so that you can review what happens in the bunk over time.
If the cows are sorting out longer pieces of hay, the bunk may be effectively empty for several hours each day while the animals consume the remaining pieces of hay. If this is the case, you are likely reducing the cows’ dry matter intake. Forcing animals to consume feed can be a costly practice.
With lactating dairy cows, boosting feed intake by 1 pound generally results in 3 pounds of additional milk. If milk is worth $20 per hundredweight, this is a 60-cent daily opportunity for each cow in your herd. Yes, it will take a little more feed, but this is likely a 3-to-1 return on the investment.
Forage costs will likely not decline over the next year, and with higher fuel and transportation costs, we may see feed prices rise. Make sure that animals are willing to consume the forage that is fed by directing additional attention to the quality and processing of your forage. •
MIKE BROUK The author is a professor and extension dairy specialist with Kansas State University.
Photo Credit: APostersView Forage growers across the country are invited to participate in the 2022 World Forage Analysis Superbowl. Awardwinning samples will be displayed during Trade Show hours in the Trade Center at World Dairy Expo in Madison, Wisconsin, October 4 - 7. Winners will be announced during the Brevant seeds Forage Superbowl Luncheon on Wednesday, October 5.
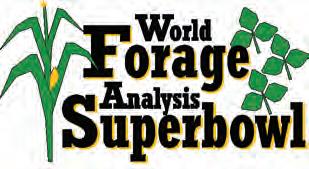
Contest rules and entry forms are available at foragesuperbowl.org, by calling Dairyland Laboratories at (920) 336-4521 or by contacting the sponsors listed below.
$26,000+ in cash prizes made possible by these generous sponsors:
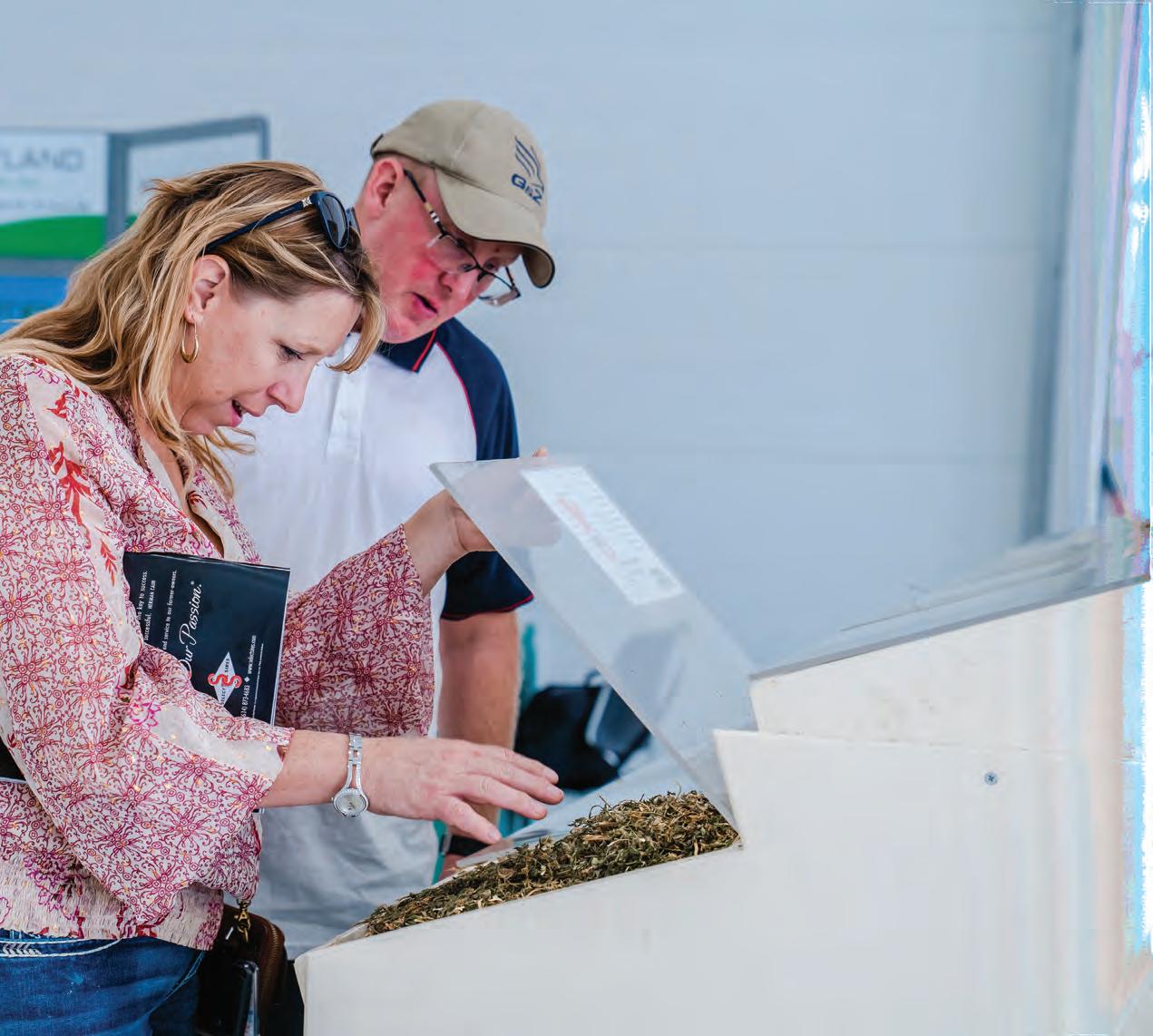
Entries Due Harvest Year Category Crop/plant/sample specifications
August 25 2022 Dairy Hay >75% legume; grown by active dairy producers
August 25 2022 Commercial Hay >75% legume; commercially grown and sold in large lots off the farm All hay samples: Must be from a bale, any type or size; use of a preservative or desiccant is allowed.
August 25 2022 Grass Hay >75% grass
August 25 2022 Baleage Any mixture of grass/legumes Baleage: Must be processed and wrapped as baleage and show signs of fermentation.
August 25 2022 Alfalfa Haylage ≥75% legume August 25 2022 Mix/Grass Hlg <75% legume
July 8 2021 Standard Corn
Silage (non-BMR)
Must be whole plant, recommended chopping height 6”-8”. Must contain >75% standard variety. July 8 2021 BMR Corn Silage Must be whole plant, recommended chopping height 6”-8”. Must contain >75% BMR variety. All silage samples: Must be ensiled in a normal preservation process and show signs of fermentation. Use of a preservative is allowed. Additives affecting fiber content or any other adulteration will disqualify the sample.
Samples analyzed for
(expressed on a dry matter basis):
Hay, Baleage, Haylage: Dry matter, crude protein, acid detergent fiber (ADF), neutral detergent fiber (NDF), neutral detergent fiber digestibility (NDFD), relative forage quality (RFQ) and milk per ton.
[RFQ is a ranking of forage quality based on NDFD and should not be confused with or compared to Relative Feed Value (RFV).]
Corn Silage: Dry matter, crude protein, acid detergent fiber (ADF), neutral detergent fiber (NDF), neutral detergent fiber digestibility (NDFD) and milk per ton.
Beef benefits from alfalfa
Hay & Forage Grower is featuring results of farmer-funded research projects through the Alfalfa Checkoff, officially named the U.S. Alfalfa Farmer Research Initiative, administered by National Alfalfa & Forage Alliance (NAFA).
GRADUAL movement toward beef production — by southern U.S. farmers transitioning from crops or dairy farming and others turning to country life — could spur additional on-farm alfalfa production and hay purchases, said Ray Smith, University of Kentucky (UK) Extension forage specialist.
A change in mindset toward alfalfa is needed, he said. “People automatically think of alfalfa for dairy cows, and, in Kentucky at least, the common adage is, ‘Beef cows? Any old hay will do,’” Smith added. Hay cost, not hay quality, has been the determining factor when feeding beef cattle, particularly by small-operation producers.
“The top beef producers know what quality is and the importance of ration balancing. But so many smaller beef cattle operators are either feeding based on tradition or are new to the market, maybe transitioning out of crop production or moving to the country and wanting some beef cows,” the specialist explained. “That average producer often isn’t thinking about forage quality.”
To help shift their thinking, Smith and his colleagues completely revised a 30-year-old publication called Alfalfa for Beef Cows using Alfalfa Checkoff funding. They added detailed information on alfalfa’s value as a homegrown protein and energy source that can also provide cattle needed vitamins and minerals.
The specialists highlighted new research showing the nitrogen-fixing legume can be successfully interseeded into bermudagrass to extend stand life, boost forage production, and improve quality. It can be harvested as hay or baleage or be grazed. Adding alfalfa to the mix can extend the grazing season.
If alfalfa is at least 30% of the stand, no supplemental nitrogen is required, even though bermudagrass and cool-season grasses need substantial nitrogen applications for top production. An alfalfa-grass mixture can improve forage intake, dietary nutritional value, and animal performance, according to the 12-page publication. It also cuts back on the amount of feed supplementation needed.
The booklet recommends matching forage quality to animal class to ensure nutritional needs are met. Beef cows in early lactation, growing heifers, weaned calves, and low body condition adult animals — all with higher nutrient needs — thrive on alfalfa or alfalfa-grass mixes. Alfalfa can also be fed to young nursing calves through creep grazing or in creep pens to boost nutrient uptake and limit-fed to mature animals during winter for additional protein and energy.
“Often, I get the comment, ‘I don’t really need a high-quality hay because I’m just trying to maintain my animals,’” Smith said. “There are a number of ways you can limit-feed high-quality hay. Limit the amount of time they have access to it. Many people are unrolling the hay and calculating how much of the ration that’s going to be.
RAY SMITH Funding: $9,464
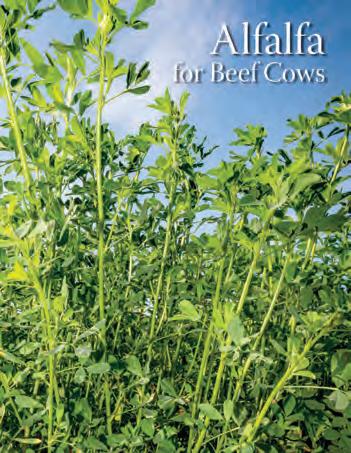
PROJECT RESULTS
Completely revised the 1991 publication, Alfalfa for Beef Cows, offering detailed information on the value of the legume, best management practices, updated photographs, and recently published data.
Matching nutrient supply from three alfalfa quality levels to the needs of classes of beef cattle
Alfalfa Quality1
Animal Requirement
Class of Cattle Dry matter intake, lbs. Crude protein, lbs. Low Medium High
TDN, lbs. 18% CP, 57% TDN 21% CP, 61% TDN 24% CP, 64% TDN
Calf, 500 to 700 lbs., 2 lbs. ADG
Calf, 750 to 1,000 lbs., 2 lbs. ADG 15.5
21 1.74
2.0 9.8
14.1
Calf at finishing 3.5 lbs. ADG Cow, Early lactation Cow, Dry mid-gestation Cow, Dry late gestation 26.5
31
28
28 2.6
3.4
1.6
2.0 18.8
19.7
11.0
13.7
“Beef cattle don’t need nutrition maintained at high levels on a daily basis like dairy cows. They can be given a high protein through alfalfa one day and then reduced protein the next day,” he said.
The publication includes information on alfalfa harvest management, summer and fall grazing, grazing throughout the growing season, and stand persistence. It also gives a concise list of agronomic strategies for producing alfalfa on beef operations as well as resources that contain further information.
Smith acknowledges the contributions and expertise of lead authors Jeff Lehmkuhler and Katie VanValin, UK Extension beef specialists, and gives special thanks to other authors, including UK’s Jimmy Henning and Chris Teutsch, extension forage specialists, and Krista Lea, extension research analyst. Jennifer Tucker, University of Georgia Extension animal scientist, wrote the section on integrating alfalfa with bermudagrass.
“This publication is telling producers around the country that they should consider a high-quality forage like alfalfa on some of their acres if they have the soil to grow it. When buying hay, look at the top-quality offerings. There’s a pretty good chance it will be alfalfa,” Smith said. •
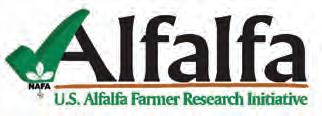
SUPPORT THE ALFALFA CHECKOFF!
Buy your seed from these facilitating marketers:
Alfalfa Partners - S&W Alforex Seeds America’s Alfalfa Channel CROPLAN DEKALB Dyna-Gro Fontanelle Hybrids Forage First FS Brand Alfalfa Gold Country Seed Hubner Seed Innvictis Seed Solutions Jung Seed Genetics Kruger Seeds Latham Hi-Tech Seeds Legacy Seeds Lewis Hybrids NEXGROW Pioneer Prairie Creek Seed Rea Hybrids Specialty Stewart Stone Seed W-L Alfalfas
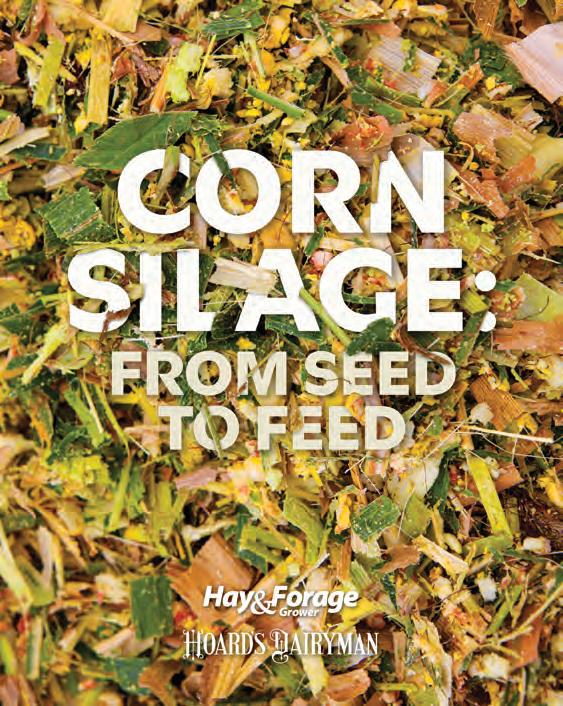
NEW RELEASE!
An ideal book for dairy producers, farm consultants, and dairy or agronomy students!
Corn Silage: From Seed to Feed
Every ration needs a strong foundation. This 80-page, perfect bound manual explains best practices and references for each stage of corn silage management. Five expert authors detail guidelines for:
• Production • Harvest • Storage • Feeding
Order Today!
$24.95 plus S&H
Available at: www.hoards.com/silage or call 920-563-5551.
Hoard’s Dairyman Books P.O. Box 801 • Fort Atkinson, WI 53538 920-563-5551 • hdbooks@hoards.com
Mike Rankin
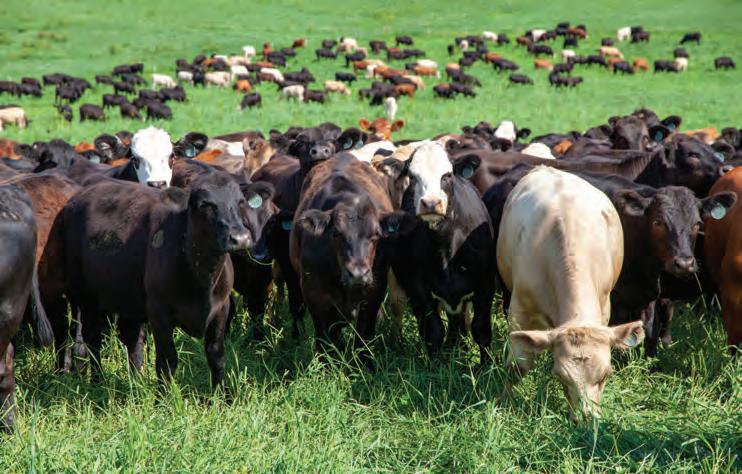
Move cattle, rest grass
by Hugh Aljoe and Steve Smith
REGENERATIVE grazing is a set of practices, guided by ecological principles, that uses the benefits of grazing livestock to rebuild soil health and may also help diversify the enterprises and income a farm or ranch produces. In the second installment of this three-part series, we’ll get into the importance of resting grass and how to get started rotating cattle as a precursor to adaptive or regenerative grazing.
One of the primary goals of regenerative grazing is giving plants the rest and recovery time they need following grazing, fire, or other disturbances. Plants need time and enough green tissue to be able to photosynthesize, which helps build energy reserves and grow their root systems as well as new leaves.
Recovery time will differ depending on the time of year of the disturbance, being more rapid during favorable growing conditions and slower during dry or cold periods. In the dormant season, recovery is on hold until spring. Ideally, before grazing begins, allow all pastures or paddocks to attain “full-flush” conditions, so the plants, and particularly root systems, are strong for the growing season.
Even as environmental conditions affect the recovery period, so does the severity of the graze, which is dictated by the amount of plant removed during grazing. The goal is maintaining plenty of plant residual, and that’s where the “take half, leave half” rule of thumb comes in, allowing the herd to consume no more than half of the forage that is readily available.
The reason we never want to graze more than half of a plant’s leaf area is that the root systems stop growing after being defoliated more than that; this slows recovery time. During the early growing season, the ideal is “top-grazing,” using only a third or less of the leaf material to attain the most rapid recovery of grazed plants.
Concerning plant recovery with regenerative grazing, don’t turn cattle back in when the grass looks lush. Pastures need to fully regrow past full flush and become a bit mature. In the ideal regenerative system in the southern Great Plains, plan for recovery periods for perennial grasses of about 60 to 75-plus days during the active growing season (early spring and summer). In late summer and moving into fall, recovery periods of 90 days or longer, which may extend into the next growing season if growth was stopped by frost prior to full recovery.
Keep palatable plants
In addition to managing the overall residual of growing plants, grazing each pasture or paddock for a short time is essential to keep the most palatable plant species healthy and plentiful. Livestock naturally want to consume the most palatable plants, so they will graze preferentially, especially on fresh growth from the most desirable plants. The repeated regrazing of the same palatable plants prevents rest and recovery, and over time, most of the palatable and productive forage in the pasture will be lost.
If livestock are regrazing plants within a pasture during a grazing event, grazing periods are too long. During the growing season in the southern Great Plains, most plants start to regrow after three to four days of being grazed. Ideally, with regenerative grazing, livestock need to be moved out of a grazed pasture within three to four days (preferably every one to two days) during the active growing period and five to six days during conditions of slower growth.
Another reason to manage stocking rates (number of livestock grazing an area for a set amount of time) and grazing periods so that plants can fully mature during recovery is to grow enough organic matter to feed both the livestock and the organisms in the soil. In this “Phase 3” of the plant’s life, the livestock will seek out and graze the higher quality parts of the plant.
The low-quality, top growth biomass that animals leave behind is trampled for other organisms at and below the soil surface to feed upon. The trampled residual matter contributes to rebuilding the organic matter in the soil over time.
Start small
To let pastures rest, you’ll need a system of moving cattle from one area to the next. We encourage producers new to rotational grazing to start small, using existing pastures. When ready to try higher stock density grazing using electric fence, consider starting at a small scale to learn the new system. This means starting with one or two smaller pastures that are easily observed. At the end of a season, you’ll at least have an area on which you’ve implemented regenerative grazing techniques that can be applied later to additional acres.
Begin by training the cattle to respect an electric fence, since you’ll likely be using temporary polywire electric fencing to separate grazing paddocks. Purchase a high-quality fence charger that will last, and consider adding a high tensile electrical wire offset fence to carry the electricity around the perimeter of a starter pasture where you and the cattle can learn about this new tool.
Select a small pasture, and then put
in a short length of test electric fence that runs out from the perimeter to separate the water source from the rest of the pasture so the animals have to learn to walk around the fence or almost into it to be able drink. Attach some flagging on the wire so they can see it, be curious, and walk up to it slowly. It’s temporary, so expect them to knock it down. Put it back up, and after a few days, they’ll build respect. Then, move that fence to a new location and see how they adjust to it.
Once cattle know what the fence is for, use polywire to create a temporary grazing paddock with access to water and large enough for a few days of grazing. Take time to watch the cattle and observe the grass and its recovery. Be sure you’re grazing to the desired intensity, but not overgrazing. With time, livestock will soon learn that every move to a new paddock means something better to eat.
Don’t be late
As we’ve transitioned the Noble Research Institute’s herds to adaptive grazing, the cattle learned quickly and now readily follow us into a new paddock with fresh grass as soon as we grab the polywire reel or gate handle. It’s works far better than trying to push them!
The more time spent with livestock, the more they will communicate to you when it’s time to move. If they begin to look at you, wanting to move, you’ll know either forage quantity or quality is limited. If they meet you at the gate, then it’s an indication that the move came too late.
When you start small, and apply short grazing events followed by long recovery times, any “missteps” have only a temporary impact on the forage, livestock, and soil. The key is being observant and adjusting as you go.
Be sure to keep good records about grazing and recovery times and how they differ with weather and season of year. What stocking rate and stock densities seemed to work best? What didn’t turn out as well as you thought it would? What did you learn? The notes you make the first year will be invaluable during future years.
Once your livestock are somewhat accustomed to use of the electric fences and you are becoming comfortable with basic rotational grazing management, then it’s time to move into what we would call adaptive or regenerative grazing.
In Part 3 of this series, we’ll go deeper into planning for and managing adaptive multi-paddock (AMP) grazing and the option of using high stock density grazing when you have abundant quantities of forage. •
HUGH ALJOE
Hugh Aljoe (pictured) is the director of producer relations at Noble Research Institute (NRI), Ardmore, Okla. Steve Smith is a wildlife and fisheries consultant with NRI.
IN FUTURE ISSUES:
Part 3: AMPing it up using high stock density grazing
Tell Us Your Rozol Story


and get a Groovy T-Shirt
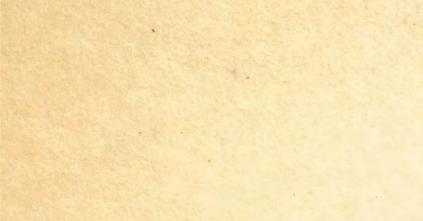
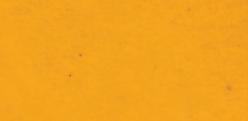

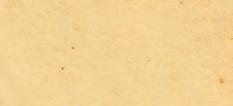

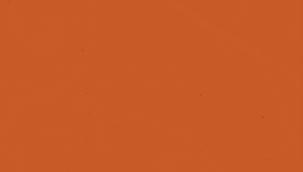

Rozol Rockin' Rebate
Earn $0.25 per pound, up to $500 on qualifi ed Rozol Products
Prairie Dog Bait*, Pocket Gopher Bait (PGB), Vole Bait*, Ground Squirrel Bait*, PGB Burrow Builder*, & Pellets. Whether it’s helping protect your crop, taking out a bad infestation, seeing results, or relying on Rozol for 50 years…we want to know. Tell us about your experience with any Rozol product, and we’ll send you a limited-edition t-shirt!
We want to hear from you! Visit Liphatech.com/Rozol50
*Restricted Use Pesticides For full rebate details visit Liphatech.com/Rebate
800-351-1476
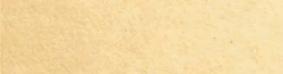
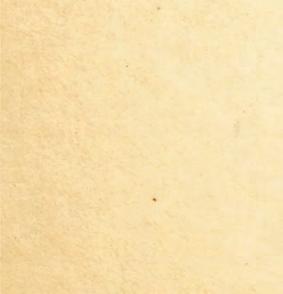
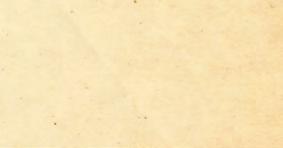
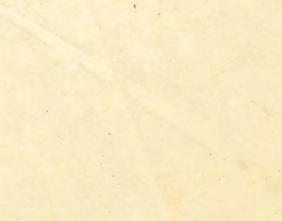

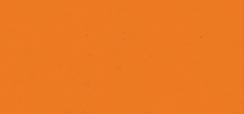
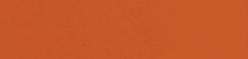
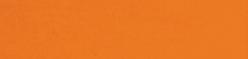
