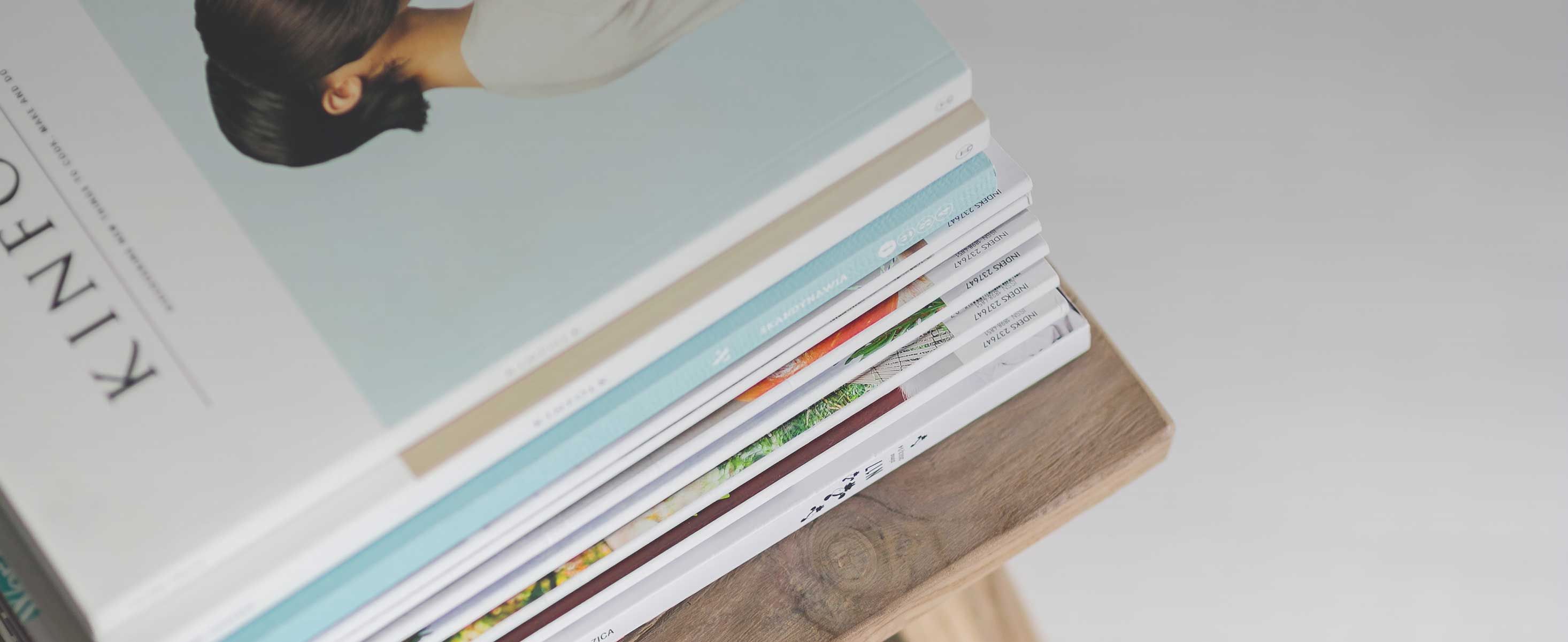
5 minute read
A STORY ABOUT SLUDGE
by Abby Bauer, Managing Editor
It lurks beneath the surface of every manure lagoon or anaerobic digester. Sludge, an unavoidable part of manure storage and treatment, is a manure by-product that is lower in organic matter but higher in solids and nutrients. This makes it more dense, and it settles to the bottom of a manure storage structure. Eventually, this sludge builds up, and it can interfere with the primary function of the structure. It reduces the overall volume of the storage that would otherwise be occupied by the microbial community that treats the manure, leading to brief, incomplete treatment or digestion of the manure. For this reason, sludge removal should be part of a manure management plan.
Advertisement
Built up over time
During a Livestock and Poultry Environmental Learning Community webinar, University of Missouri extension professor Teng Lim shared an example of a farm that found themselves with a bad sludge situation. On this dairy in Missouri, manure was flushed from the freestall barn three times per day into a lagoon that was 400 feet long by 280 feet wide, with a depth of 10 to 12 feet. The estimated volume was 7.5 million gallons.
Lim said an elevated screen system failed and was eventually abandoned, which led to more solids entering the lagoon. The pit was agitated each year prior to emptying, but there was significant build up of sludge over time, and by 2020, islands of manure could be seen in the middle of the lagoon.
To remedy this situation, a plan was created. First, the sludge was sampled and the volume was estimated. Lim said this sampling was done by an experienced crew. In all, 24 readings were planned with an estimated cost of $2,600. Unfortunately, the sampling boat repeatedly got stuck in the lagoon, limiting the number of samples that could be taken.
From the samples that were collected, moisture content was found to be 86%, 94%, and 88% for the sludge mounds, the lagoon center, and the shore samples, respectively. This means the sludge contained between 6% and 14% solids. The contractor hired to do the job normally pumped at 5% to 8% solids, so water from a nearby pond would be brought in to dilute the lagoon effluent and prevent clogging the system.
The farm’s fields were also sampled to determine application rates for 200 of their own acres, according to their nutrient management plan. Manure would also be applied to 400 acres on a neighboring farm.
Moving the manure
To start the job, the lagoon was agitated using a remote control boat and two PTO-run agitation pumps. A trailer mounted pump was used to remove manure, along with a dilution pump to bring in the pond water. Booster pumps were used for fields farther from the farm to maintain a flow of 1,800 gallons per minute. The manure was transported to fields using draghoses and was injected with a toolbar pulled behind a tractor.
Lim said it is important to sample the effluent during application. In this case, samples were collected at the primary pump at least once a day, measuring nitrogen, phosphorus, potassium, pH, moisture content, and more. Even with agitation, there was still a significant amount of fluctuation in nutrients applied day to day. Lim noted that real time nutrient measurements taken in the field would be valuable for adjusting application rates more quickly.
The effluent was applied at an average rate of 25,000 gallons per acre. Over eight days, around 8 million gallons of manure were applied. The overall cost of the removal was $151,000.
Looking forward
Lim said one lesson learned was that complete agitation and homogeneity was very difficult to achieve with this amount of sludge, which was recognized by the varying sample results. Furthermore, the nutrient management plan and land application piece is very important to ensure effective recycling of the nutrients. He stressed the need to work with a custom applicator that has the equipment, experienced crew, and reputation to get a job like this done.
The moral of the story is to not let solids build up to this level. This dairy installed a pull-plug sediment basin system (on.hoards.com/pull-plug) to help remove solids from the manure flush water and keep them out of the lagoon. Lim said this system, which cost the farm about $26,000, is relatively easy to operate and, along with scheduled lagoon clean outs as needed, should help prevent this sludgy situation from happening again. ■
U.S. GAIN SECURES DAIRY RNG OFFTAKE WITH ENTECH SOLUTIONS
U.S. Gain, a division of Wisconsin-based U.S. Venture Inc. and a leader in the development and distribution of alternative fuel and renewable energy, recently announced a new offtake agreement with EnTech Solutions at their agricultural biodigester near Madison, Wis. This project is a partnership between EnTech Solutions, Northern Biogas, and four local Dane County dairy farms where agricultural waste is processed in digester tanks to produce renewable natural gas (RNG) that will be used as an alternative fuel in the California transportation market.
The digester facility had previously produced electricity but has been repurposed to produce RNG that can be easily injected into the natural gas pipeline and distributed throughout the nation.
In this case, U.S. Gain is sending RNG from Madison to their fleet customers in California where transportation-related emission reductions are a priority.
Chonex Offers An Affordable Solution To Skyrocketing Fertilizer Prices

Alabama AgTech firm CHONEX produces STRONGSOIL, a microbial concentrate that restores a thriving microbe population to soil. “Healthy soil is living soil. Unfortunately, decades of chemical-intensive agriculture have depleted agricultural soil of the microbes that are essential to plant growth,” said Michael Lynch, CHONEX founder and CEO.
Some growers are cutting back on fertilizer to save money, knowing that they might sacrifice yield at harvest. Lynch recommends that farmers maintain crop quality by using STRONGSOIL alongside their reduced fertilizer application.
Now in its second year of field trials, STRONGSOIL will be used in 50 trials in 10 states, including Grand Farm Education and Research Initiative in North Dakota, which is focused on developing the future farm.
STRONGSOIL is produced from layer chicken manure in egg production. CHONEX has developed a proprietary process utilizing the black soldier fly to consume the manure, converting it to frass and destroying the harmful pathogens that can inhabit manure. The result is a granular, lightweight product that is brewed into a STRONGSOIL Tea, which is then applied to soil, inoculating it with hundreds of millions beneficial live microbes per milliliter. Key to STRONGSOIL’s functionality is the consistency of the product and the breadth of microbe biodiversity.
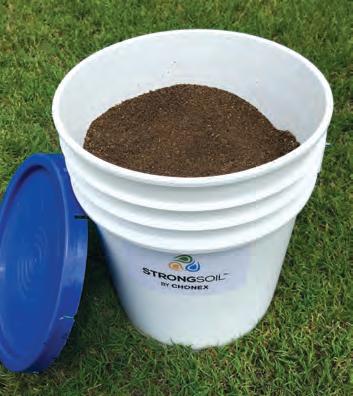
In addition to benefiting farmers, STRONGSOIL benefits the environ- ment in multiple ways, by upcycling layer chicken manure, reducing the amount of fertilizer used, and reducing reliance on agricultural pesticides and herbicides. Reducing the amount of fertilizer used also reduces the amount of fertilizer that is washed into waterways and solubilized into the air. By adding microbes to the soil, STRONGSOIL enhances the soil’s ability to absorb and store CO2 and counter greenhouse gas emissions.
A unique attribute of this project that amplifies its positive environmental impact is the incorporation of a renewable energy microgrid onsite. Featuring solar panels and batteries, this microgrid has an output of more than 2.8 megawatts (MW) of clean energy generation — the equivalent of powering more than 400 homes. This increases energy efficiency and further reduces the RNG’s carbon intensity (CI) score. Microgrid use in agricultural applications is still a relatively new concept, but as projects like this come online successfully, other digester operations will see it as a viable solution.

U.S. Gain continues to find innovative ways to optimize gas production at their more than 30 RNG development sites. For more information on partnering with U.S. Gain, visit usgain.com.
More information is available at STRONGSOIL.com.