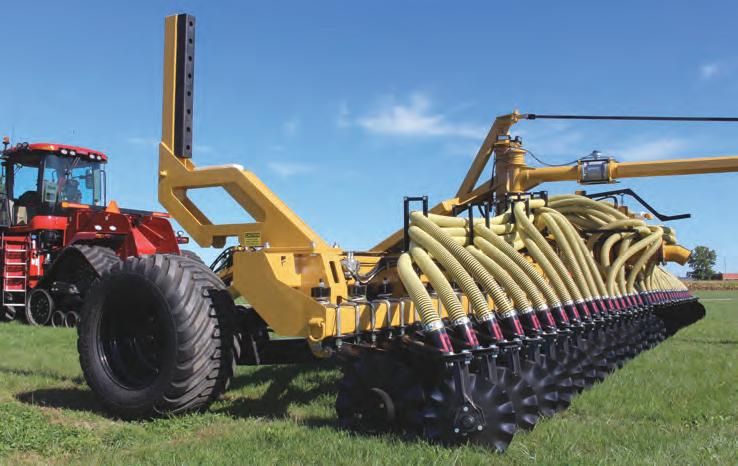
5 minute read
NEW TOOLS OF THE TRADE
Finding the correct machinery to meet the needs of our customers and preserve fields is an important part of a custom applicator’s
by Jesse Dvorachek
Advertisement
s nutrient applicators, we are tasked with having the right piece of equipment for each of our customers. Since most customers have their own ideas for manure application, trying to find a happy medium becomes a challenge.
Some farmers want their nutrients mixed across the whole soil profile. Others want the nutrients in zones as to disturb the soil profile as little as possible.
The minimum disturbance method has been a hurdle because we need to meet the higher rates of application with all the water being collected on these farms. To do that, we need to have soil available to absorb the nutrients we are applying.
It seems there is no one tool that fits all situations. In hilly conditions, one piece of equipment might not work because the nutrients will move down the zones and blow out at the bottom of the hill, potentially causing runoff. Some work better when there is a little moisture to soften the soil, making it easier to penetrate compaction. Some shank units, if used when conditions are wetter, will smear the trench and won’t allow absorption either, which could cause nitrogen striping. Some pieces won’t allow more than 15,000 gallons per acre because they don’t go deep enough.
I’ve been to many field days across the country and have seen different machines work great in soil that makes every applicator look like a rock star. In real life, 95% of the time conditions are never perfect, and we need to work in many different field situations.
In my search for the perfect machine, I stumbled across a unit that works best for me, and it is versatile. I have a bar applicator that is 44 feet wide, and we added a row unit made by TK Ag Works in southern Wisconsin. The bar is wide, so I can use it for topdress applications like a dribble bar if I want. I can also easily change out coulters to go from less aggressive to more aggressive tillage. The unit has been built heavy for the rigors of custom application and is low maintenance with greaseless bearings.
This machine is also capable of high rates. The coulter unit runs straight and has steel fins that are about 3 inches wide. When they enter the ground, they go in vertical, and as the coulter rotates, the fins leave the soil horizontal. This lifts the soil profile, pulling up compaction and leaving a nice, soft zone that is perfect to absorb liquid nutrients.
The coulter has a serrated edge as well so there is no need for a lead coulter. This allows for residue to flow or be chopped up, it does not plug the row unit, and it reduces weight. By using this row unit we find the growers are back in their fields far sooner than when we disturb the entire soil profile. I’m not saying that we don’t have disks and rippers in our yard, but we are trying to move away from those if we can.
As have many other nutrient applicators this year, we also added the John Deere HarvestLab 3000 with Constituent Sensing to this bar. We are able to apply nutrients based on many different criteria, like real-time values for total nitrogen, ammonia nitrogen, potassium, phosphorous, and dry matter.
In the past, we were given a rate for a field, and we put the same rate on the entire field. With all the restrictions on fields today, a field with a limitation will lump the whole field into that rate. If we can prove what is put where with this technology, we can apply a higher rate on parts of the field. The technology will speed up and slow down the tractor as you cross those zones in the field. This makes it possible to apply variable rate manure on the fly — and do it accurately.
This year we are trying a lot of new tools and working with our growers to utilize this technology to its fullest potential. We want to make sure the storage pits are empty at the end of the year and that our customers are more profitable by utilizing the nutrients they produce on farm to the maximum extent possible. ■
Bazooka Farmstar Expands The Titan Series Toolbar
Bazooka Farmstar announced the release of Titan 2, an enhancement to its Titan Series Toolbar, a front-folding manure injection toolbar. On Titan 2, the position of the tower has been moved further forward, making it more closely align with the tires and enabling less resistance when turning in the ground at the end of a pass. Concurrently, the design of the toolbar body has been reinforced to provide an even stronger solution that can withstand rugged field conditions. The new design comes in lengths from 40 to 60 feet, increasing the number of Phantom Units that can be incorporated across the toolbar.
Titan 2 has been equipped with larger flotation tires to counteract the steel that has been incorporated into the new design. The center section tires have been upgraded to 700 series flotation tires, while the gauge wheels have been enhanced to 550 series flotation tires.
Two notable features that come standard on Titan 2 are the Flux Manifold and 3-inch bumblebee drop-tube hose. The Flux Manifold is accompanied with a new lift assist for more convenient clean-out, and a block indicator light that allows operators to quickly detect an obstruction in the manifold. The 3-inch droptubes hold the smartest hose routing to date, minimizing sagging that would otherwise cause sand build-up and hose clogging. For more information, visit www.bazookafarmstar.com
Doda Reveals New Hose Reels
Doda USA is proud to introduce their towable hose reels. With either a small or large diameter option, there is a reel to fit any size farming operation. The hose reels are built on a heavy duty galvanized frame with stainless steel safety guards. They are PTO powered, with a hydraulic tongue stand, removable hose dividers, and large flotation tires. Visit www. dodausa.com for more information.
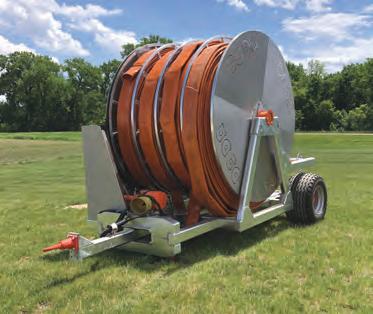
Daritech Introduces Modular Manure Evaporation System
Following years of development, Daritech introduces the ZND system. Utilizing evaporation technology, you can now remove water from manure with 100% pathogen kill, utilizing no chemicals, filters, or membranes.
The heart of this modular system is Daritech’s mechanical evaporation unit, with each module producing approximately 20,000 gallons of distillate per day. With the ZND system, you can now evaporate water from your manure at a fraction of the cost of a standard evaporation system.
Any producer looking for a more economical and efficient manure management system for internal or commercial use will benefit from:
Eighty to 90% of the manure fed to the ZND system will become distillate. The distillate is overwhelmingly water but also contains some ammonia from the TKN present in the manure. The ammonia can optionally be removed by aeration or a stripping tower. If recovery is desirable, a scrubbing tower can be added to produce ammonium sulfate.
The remaining sludge nutrients are at a concentration of 10% to 20% of the initial starting volume. This can be more cost-effectively transported over greater distances than would have been required by the original non-concentrated manure.
With the optional 2nd Stage, the evaporator sludge can be sent to a dryer to produce SuperO organic fertilizer crystals. For more information, visit www.daritech.com.
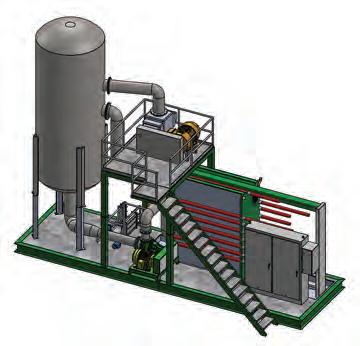