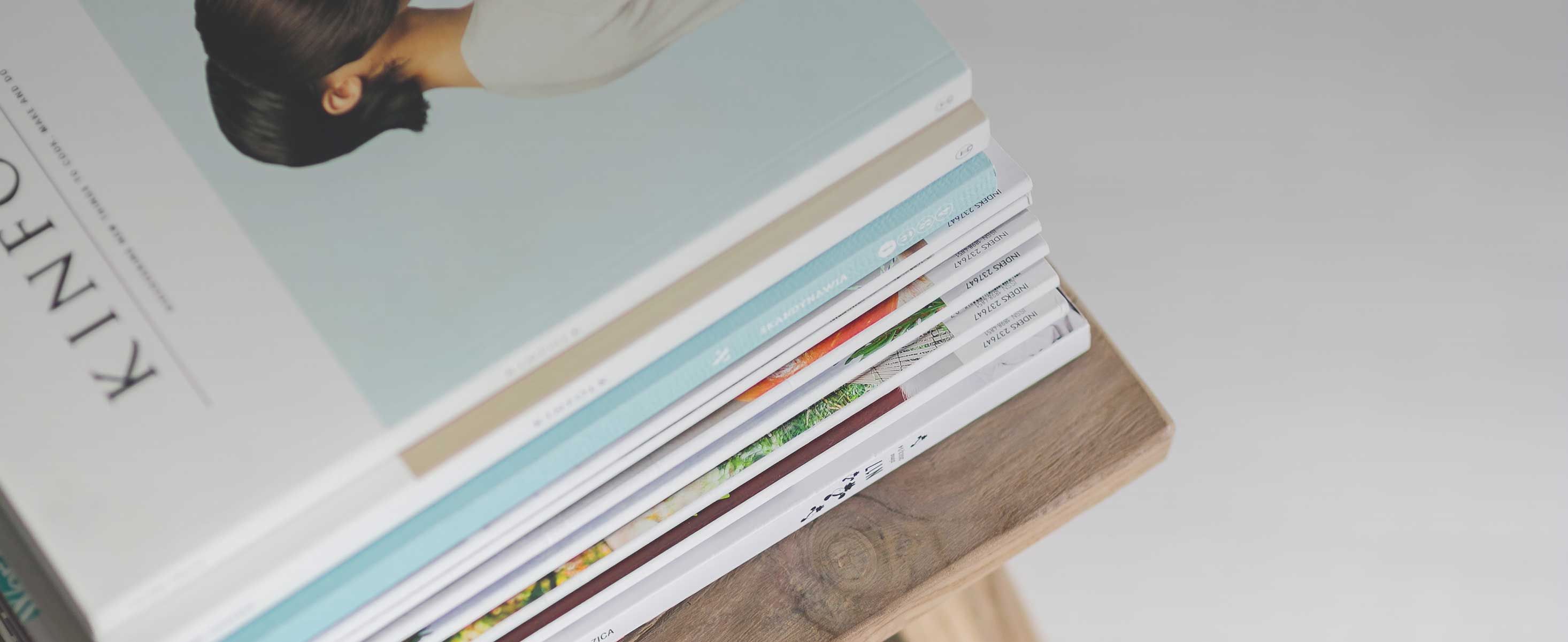
4 minute read
Put it in a pellet
Pelletizing manure solids is one way to condense nutrients for easier transport.
by Mahmoud Sharara
Advertisement
When carefully managed, manure is a low-cost source of nutrients and organic matter that improves soil fertility and crop yields. In regions of concentrated animal production, fields available to use manure are limited and often receive nutrients in excess of crop needs.
In particular, when manure is managed on a nitrogen basis, soil phosphorus increases, which elevates phosphorus losses to surface water. These losses contribute to algal blooms and dead zones in fresh water bodies. Such impacts bring negative attention to concentrated animal feeding operations (CAFOs) and can result in tighter regulatory restrictions on permitting and operation.
To overcome these challenges, livestock producers adopt solid-liquid separation to add flexibility to nutrient use by moving phosphorus-rich solids to fields farther away to use agronomically. At times, however, manure solids need to be transported even farther for use in areas without a nutrient surplus. In such cases, additional processing is required to develop manure-based products that are easily shipped long distances and accessible to a wide range of uses.
Pelletizing manure solids can help achieve this goal (Figure 1). That is because pelletizing increases manure density, which makes storage and transportation more efficient. Manure pellets are also uniformly granular or cylindrical, making land application easier and more precise. In cases where manure solids are rich in energy, as in fresh litter or dairy solids, manure pellets can be used as fuel through co-firing in power plants with coal and/ or woody biomasses.
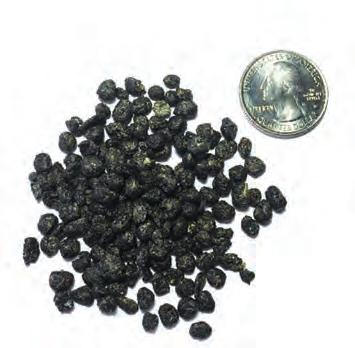
How it’s done
Manure can be pelletized using different techniques. For example, extruders apply pressure to manure solids to form pellets or briquettes, while mixing manure solids with a binder in a pan/ disc granulator or a pin mixer forms granules (balling). Spray congealing is also used to make prills from slurries. In each case, the particle size can be adjusted by the mold size used, the amount of pressure, the type of binder used, and the mixing duration.
The type of manure also affects the optimal method for granulation. For instance, extrusion is suited for fiber-rich manures like poultry and dairy, while granulators are ideal for fine particle solids like digestate solids after fiber removal.
Granulators are typically the least cost technology for manure pelletizing since they consume the least amount of energy and do not involve high-friction moving parts. In granulation, the binding effect can be achieved by one of several different binders, including water, starch, gums, and lignosulfonates. The type of binder affects the process cost as well as the potential for labeling the product as an organic material.
During operation, pan and disc granulators can produce dusty conditions if the manure is too dry. They should be operated under negative pressure along with a dust collection system.
The content matters
Manure pellet quality depends on its nutrient content and physical, chemical, and biological properties. The quality determines market acceptance and value of the product. Without any supplemental nutrients, solid manure pellets have nitrogen, phosphorus, and potassium ratios (N: P: K) around 4: 4: 4.
Maintaining a consistent nutrient value is critical when manure pellets are bagged, labeled, and sold in markets as a fertilizer. This, however, can be a challenge because of manure variability, especially when manure is being sourced from different farms. Supplementing the manure with nutrients is often a good approach to ensure consistency and to meet market demand uses.
Similarly, particle size and size distri-
Dewatered manure
Paddle/Pin mixer
Disc granulator
Rotary dryer
Binder feed achieved by developing cooperatives for sourcing manure from multiple nearby farms. This approach is particularly suitable to areas of high-density animal production.
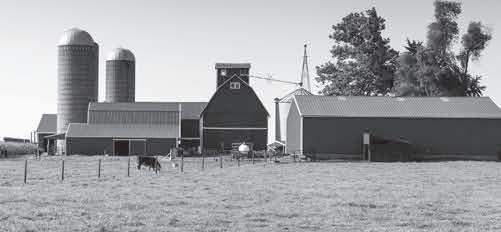
In studying the impact of cooperative size on the cost of pellet production, we found that extending the cooperative radius from farms within 2 miles to 10 miles reduced the cost of producing a ton of dairy manure pellets by more than 6% (on.hoards.com/manurepelletizing). This cooperative model greatly helps reduce the production cost per ton of pellets and allows the facility to hire independent staff to develop multiple product lines and market product.
The growth in organic food production is another lucrative opportunity to implement granulation to provide a renewable nutrient source while reducing its accumulation in animal production regions. Even though cost is a barrier, the ability to pelletize manure has many potential applications on the farm and beyond. A fact sheet with more information can be found at bit.ly/JNM-pelleting. ■
Oversize mill
Vibrating screen
Product (granules)
bution affect land application swath and uniformity. Therefore, the intended application determines the size selected for pellet manufacturing, often between 2 and 6 millimeters to match conventional fertilizer applicators. Specification sheets often report particle size using median particle size (d50) or size guide number (SGN), while particle size uniformity is often reported using the granular spread index (GSI) or the uniformity index (UI).
One of the reasons for poor uniformity is pellet crushing during manufacturing, handling, storage, or transportation. This can be a result of suboptimal production conditions such as low binder ratio or poor binder quality, rapid pellet heating or drying, or excess pressure during extrusion. Therefore, durability is monitored during production, typically using the pellet durability index (PDI). This index reports the percentage weight of intact pellets after a standard tumbling test.
Before the manure pellets are bagged and labeled as a “fertilizer,” it has to be permitted and tested periodically by relevant agencies in the state where it is manufactured and distributed. That is often done to ensure label claims are correct and that pathogen levels and metal content are safe for intended uses, especially when marketed for nonagricultural uses such as gardening and turf care.
Concerns about price
While pelletizing is clearly a promising strategy, it is costly to take on as an individual producer. The scale and cost of equipment required (Figure 2) is often beyond what a typical dairy or swine operation can afford. Larger dairies, with more than 10,000 cows, are good candidates for this technology. Overcoming the scale issue for typical farms can be