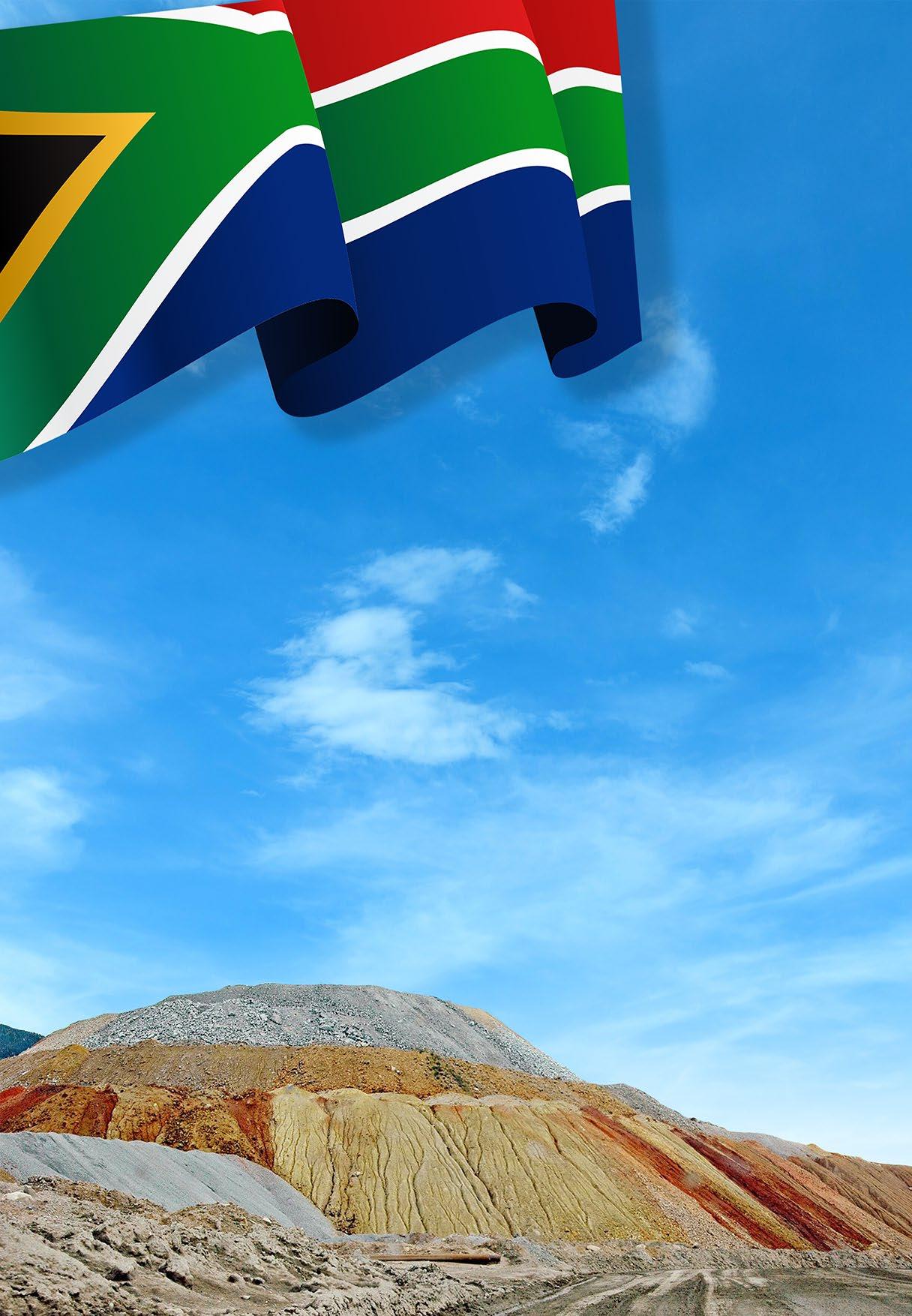
1 minute read
SOUTH AFRICA STEAMS AHEAD WITH SLAG
The South African concrete industry is leading the charge, championing the use of blast furnace slag, resulting in a substantial reduction in its clinker factor without compromising the quality of products.
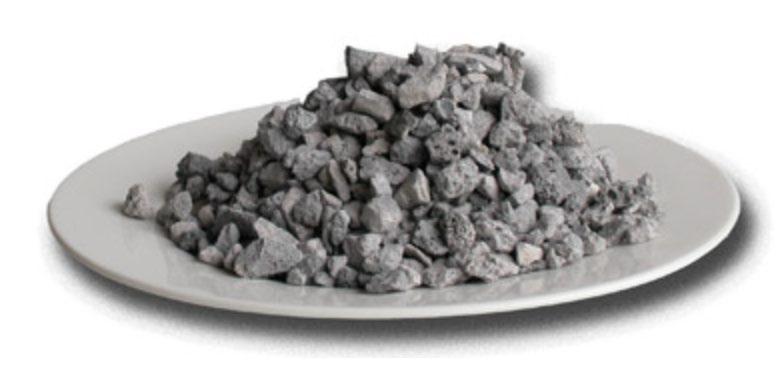
Blast furnace slag (BFS) is formed in a blast furnace with molten iron from iron ore in the reducing presence of heated air, coke and limestone. The resulting molten slag and iron, once removed from the furnace, are subject to further processing to form a crystalline aggregate or ground blast furnace slag (GBFS).
GBFS is an old practice, having been used in the manufacturingof cements since the second half of the 19th century. Back then, it was recommended to intergrind the blast furnace slag with the clinker. However, in the 1950's, companies pioneered the use of separately grinding granulated blast furnace slag (GGBFS) for the construction industry, giving rise to a more popular concept in the South African market. The availability of GGBFS is common place through the major industrialised economies.
By using blast furnace slag in concrete, not only does it reduce carbon emissions and minimise waste to landfill, it provides enhanced long-term strength and durability, advancing the built environment with high quality products that do not compromise the natural environment.
Want to know more about iron and steel slags in South Africa? Get in touch with the Slag Association of Southern Africa https://saosa. africa
According to the Association of Cementitious Material Producers (ACMP), the clinker substitution rose from 12% in 1990 to 23% in 2020, and a staggering 41% in 2009. A 60% rise is anticipated for 2030.
As a result, the industry has witnessed significant year-on-year reductions in emissions, showcasing how the beneficial use of slag can drive strong and coherent action towards achieving net zero.
SAOSA are a non-profit lobby and advocacy group focused on the recycling, repurposing and reuse of slag (stony waste matter separated from mineral commodities during mineral processing) as a reclaimed alternative construction and raw material for the much needed infrastructure development in Southern Africa.