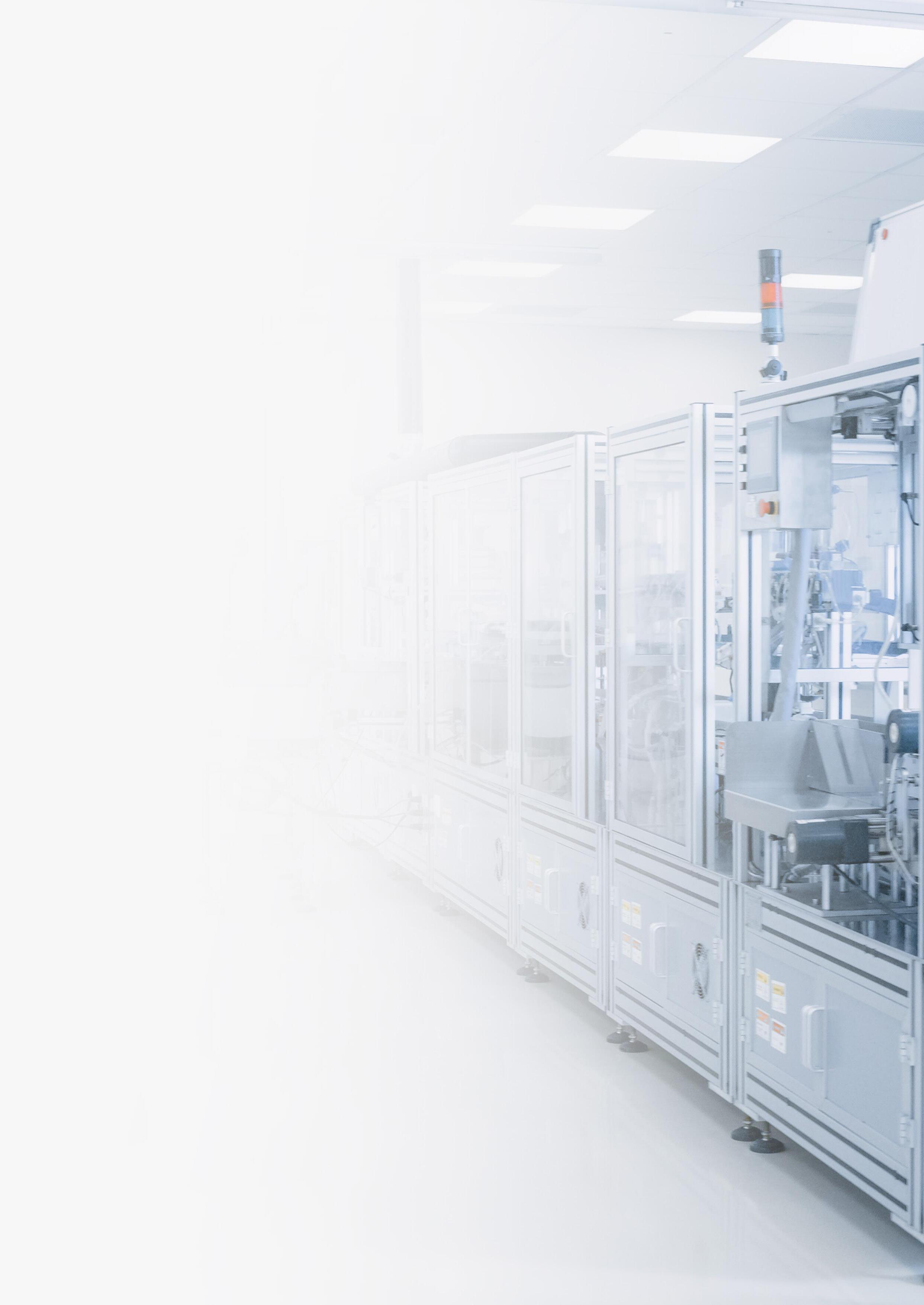
4 minute read
Fuel breakthroughs
The life sciences industry continues to experience unparalleled innovation as investment and talent flow into the sector and breakthrough discoveries happen at a rapid pace.
Named the 2021 BD Sustainability Supplier of the Year, JLL helps life sciences companies create compelling real estate and facilities strategies that improve efficiency, mitigate risk and deliver a sustainable workplace. Lay the groundwork for rapid growth →
Advertisement
KEVIN NELSON SENIOR VP & CPO, BD
Creating a socially & environmentally responsible supply chain BD knows its customers want them to provide high-quality products at a fair price and that they expect more than the basics. Improved resiliency, visibility and agility are adding value, but the company is also focusing on sustainable business practices that are environmentally, ethically and socially responsible.
“At BD, we stay true to our values, including doing what is right. We set up the Responsible Sourcing Program to ensure we embed supplier responsibility and sustainability in every purchasing decision we make,” Nelson explains.
This includes partnering with ethical and diverse suppliers, helping protect human rights and working to ensure environmental stewardship.
“Our customers want to understand the bigger picture, too,” Nelson explains. “Are they buying a product from us that is sourced from an ethical and responsible supplier paying fair wages to its workers?”
BD ensures compliance in these areas through ongoing assessments, desktop and face-to-face audits and close partnerships across its supply base. This is all to ensure that suppliers understand exactly what BD expects when doing business with them, while also making sure risks are anticipated and managed effectively.
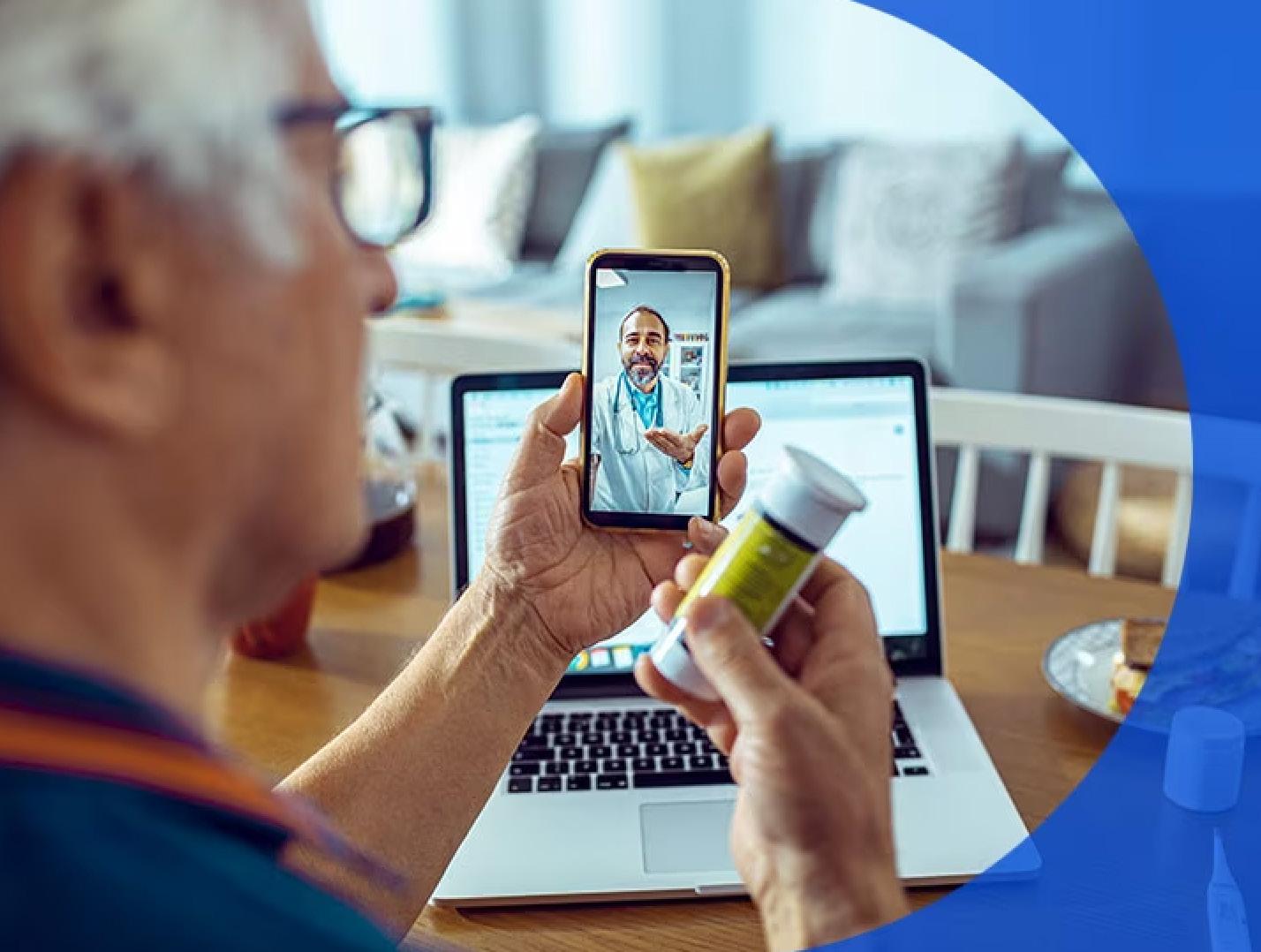
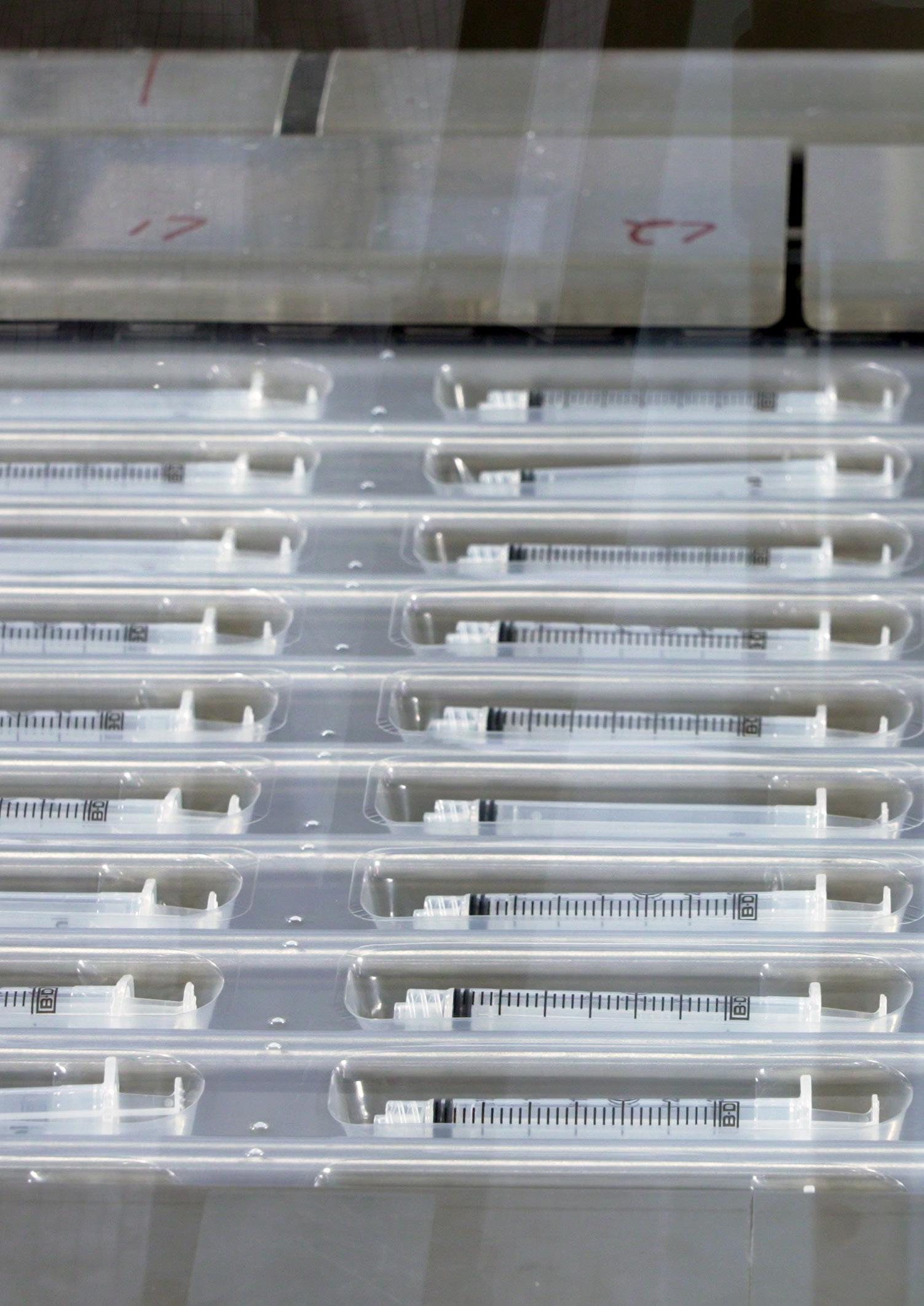

Like most companies, Nelson and his team have certainly found some areas of concern in their network that need to improve.
“Instead of moving away from that supplier and letting it be someone else’s problem, we’ve tried to see how we can work with them to identify an area they need to improve in. If they’re able to, that’s great. If not, then we’d have to move away. So far, we’ve been successful in mitigating issues. We’re working to help improve human rights around the world while ensuring important medical products get to those who need them.”
Another focus area of BD’s Responsible Sourcing Program is supplier sustainability. This examines where suppliers are driving reductions in greenhouse gases, diverting waste away from landfills and understanding how much renewable energy they use. The Responsible Sourcing team is also working internally with product stewardship and category management to develop and implement strategies to eliminate materials of concern where possible.
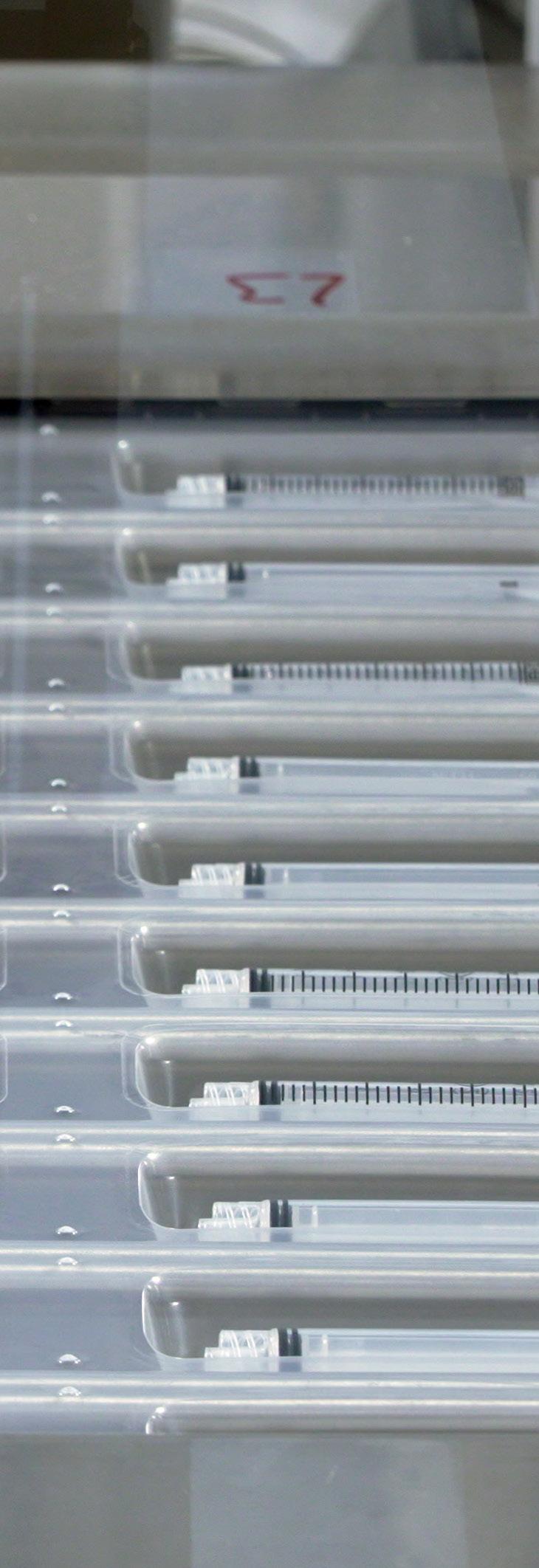
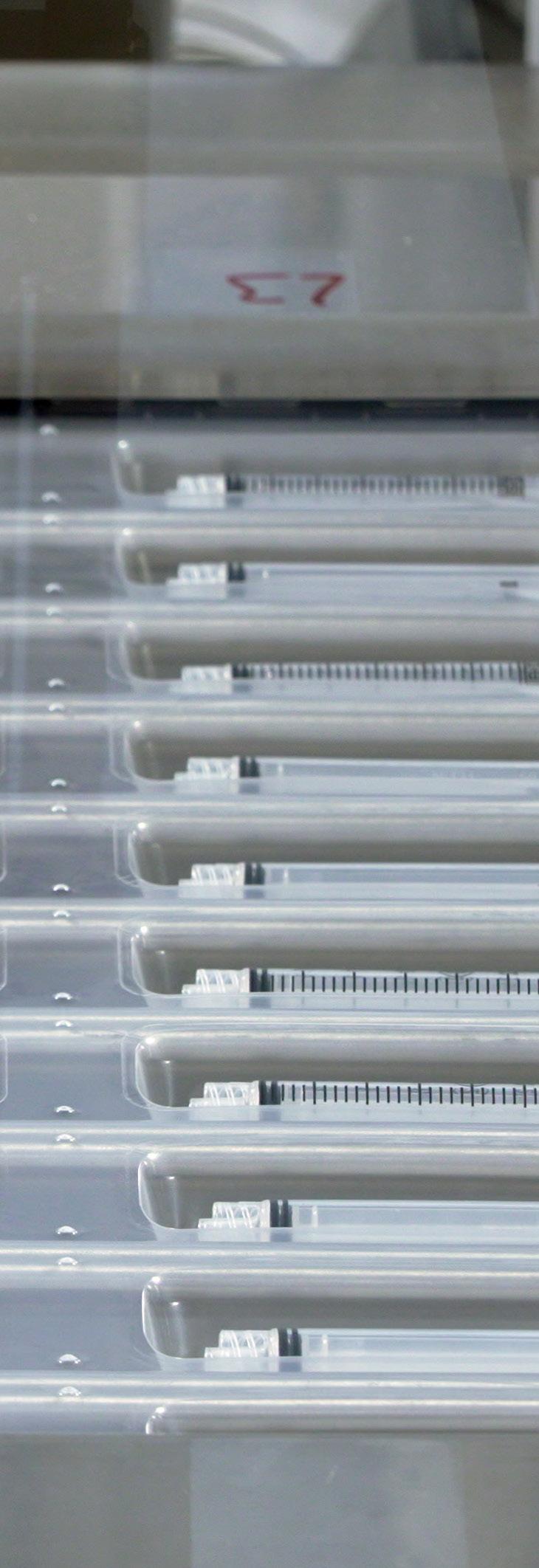
How well do you know your suppliers?
Or even your suppliers’ supplier?

Get clear visibility and unmatched intelligence to make faster, smarter supply chain decisions. Everstream reveals supplier, material, and revenue risk before anyone else. With the world’s most accurate and reliable data, network graphing, and human analysis, Everstream empowers supply chain leaders to build strong, agile, and sustainable supply chains.
Take control of your supply chain with Everstream everstream.ai everstream.ai/demo
KEVIN NELSON SENIOR VP & CPO, BD
sustainable sterilisation technologies, and addressing materials of concern (MOC).
The third area of focus of the Responsible Sourcing Program is supplier diversity, which has gained a lot of momentum in the US.
“We pivoted our supplier diversity focus from one that historically assessed our spend with small businesses and diverse suppliers, which was more of a reactive approach. Today, we are looking at economic impact in terms of how we’re helping different regions and local economies by using diverse and small businesses that are truly making an impact. We’re looking at how we can help a community where our customers are living,” explains Nelson.
“The Supplier Sustainability pillar includes working alongside our R&D team and business units to identify products, materials and components that are ‘greener’ in nature while also making products that are more effective, efficient and economical,” Nelson explains. “This might be a packaging component that uses less energy to make or is recyclable.”
In 2022, BD launched the Sustainable Medical Technology Institute, a model of practice within the organisation that brings together BD researchers and engineers, as well as quality, regulatory, policy, sourcing and operational expertise, to focus on reducing the environmental impact of the company’s product portfolio in three areas: adopting sustainable product design strategies, developing and deploying
Finally, there’s end-to-end transparency, which is connecting back to the customer and providing enhanced visibility to them. “The key is providing this information proactively and transparently to the customers, to the patients, before it’s a problem, so they have the ability to do something in advance.”
Medical manufacturing partnerships & resilient supply chains
As with any medical manufacturer, BD’s partner ecosystem is vast.
“Partnering with our customers upfront is a key priority for BD. We aim to identify the customer requirements and expectations and build those into our long term strategies and initiatives,” he explains.
From day one, BD’s style has been to collaborate and work with its partners, which was essential during the pandemic.
“We came in working together, wanting to figure out a solution with our supplier partners, as opposed to demanding, ‘Shift this or I’m going to move away from you’.

“The partnership is a three-legged stool: our customer, our suppliers and our internal stakeholders that includes business units, Quality and Regulatory, among others.”
This work is further strengthened through strategic collaboration and public-private partnerships with government agencies, including the FDA, HHS, POTUS/White House – and industry collaboratives like Advamed – to address supply chain and sourcing issues that plague the broader healthcare industry.
Being able to incorporate those areas into BD’s strategy has allowed what Nelson sees as a resilient end-to-end supply chain.
The momentum of BD’s procurement supply chain team has been exciting for Nelson and his team.
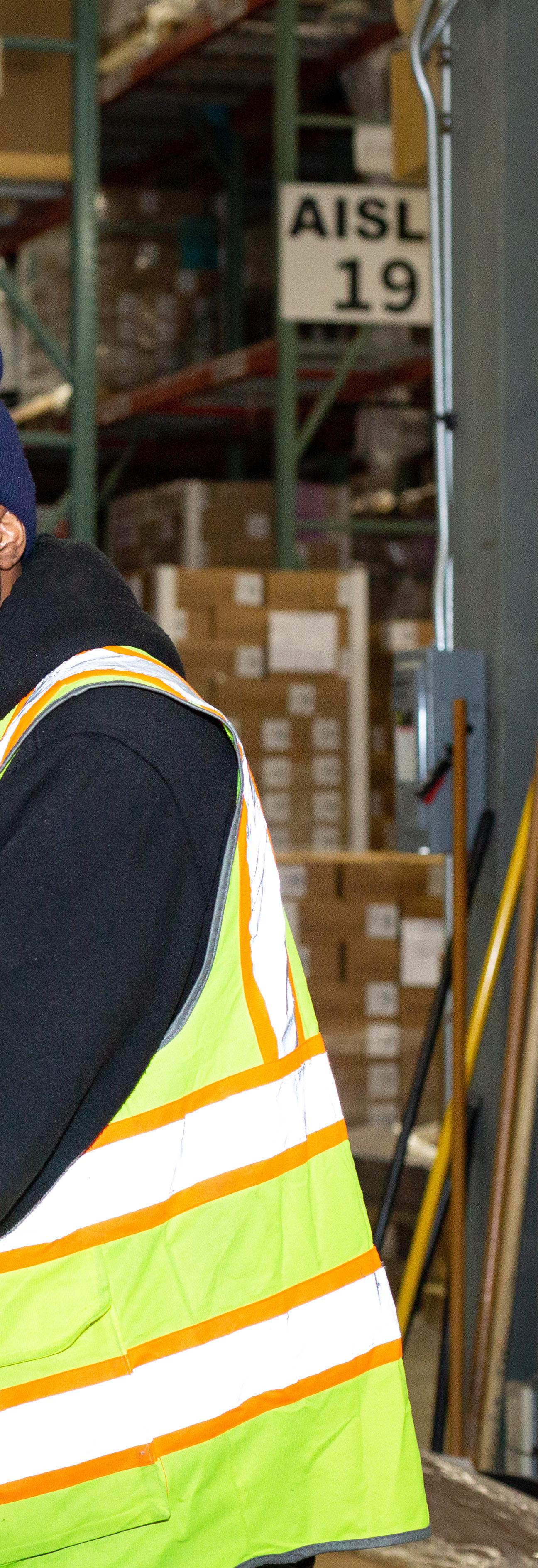
“We’ve experienced very little turnover in our function, and I think a big reason for that is that people see the movement we are driving and understand we have become extremely vital to BD, our customers and the patients they serve. We are on the frontlines; we are helping shape strategy as we go forward here.”
Nelson views this as an entirely different kind of mindset and even acumen, from a team perspective.
“I think it’s been refreshing for the team to pivot away from historical firefighting or cost-reduction to facing the bigger opportunity we’re trying to address.”
“We have more engineers on the team now doing more,” says Nelson. “Our engineers look at an existing product line and see what we can do to redesign elements that can meet the needs of our customer and patients, reduce our overall risk exposure and benefit BD as well.”