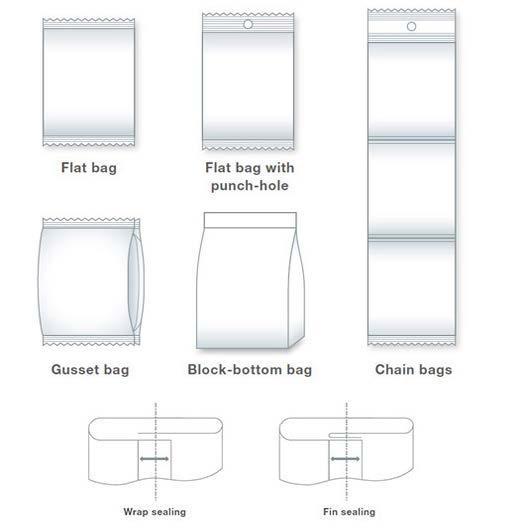
4 minute read
INSPIRA: WORLD’S BEST PERFORMING SNACK BAGMAKER
BOX MOTION OR ROTARY MOTION?
Inspira offers box or rotary motion film feed and sealing options to suit different products, bag types, and bags per minute speeds requirements. Box motion is ideal for high-speed lines that need to form multiple bag shapes, including high-speed pillow and chain bags, and is also suitable for thick film. Rotary motion double jaw is best for ultra-high speed, while rotary motion single jaw is best for medium-to-high speed. Thin sealant film is recommended for rotary motion which stops end seal leakage by utilising a hot knife and high seal pressure.
The Ishida Inspira Snack Bagmaker (Inspira) is a vertical form fill sealing (VFFS) machine, an automated packaging system that fills and seals products in formed bags from roll stock. Inspira incorporates next generation snack packaging technology and offers a new level of automation and efficiency to consistently produce quality bags, dramatically increasing production efficiency for snack food manufacturers.
The Atlas Series (Atlas), the previous snack bagmaking model series, revolutionised snack bagmaking technology and became an industry benchmark in high-speed snack operations. Atlas’ versatile twin-jaw system and innovative continuous back seal system were key to its success in the industry. Always seeking to improve, Ishida continued to invest heavily in R&D and tasked their engineers to continue to explore and to refine their machines in order to provide a solution to industry’s call for more automation and for better communications between weigher, bagmaker, and other packaging room equipment.
Ishida has released to market the result of their extensive R&D, including groundbreaking design improvements: Inspira Series, the next evolution of VFFS technology.
Auto Splicer Innovation
Inspira has many new features which improve film changeover times and reduce film waste when changing over to a new roll. The auto splicer feature keeps production running by automatically joining the end of the expiring web roll to the leading edge of the new roll, removing the need for operator involvement. Auto tracking enables the new roll to track correctly, and registration mark recognition splices the two rolls together to minimise film waste during changeover. The auto splicer helps prevents human error and reduces film loss. Rapid ROI is possible because of increased productivity and automation.
Multiple Bag Types And Sealing Options
Most snack food processors produce a variety of snacks. Choosing packaging equipment that can cater for a range of shapes, sizes, seasoning, and densities is best practice.
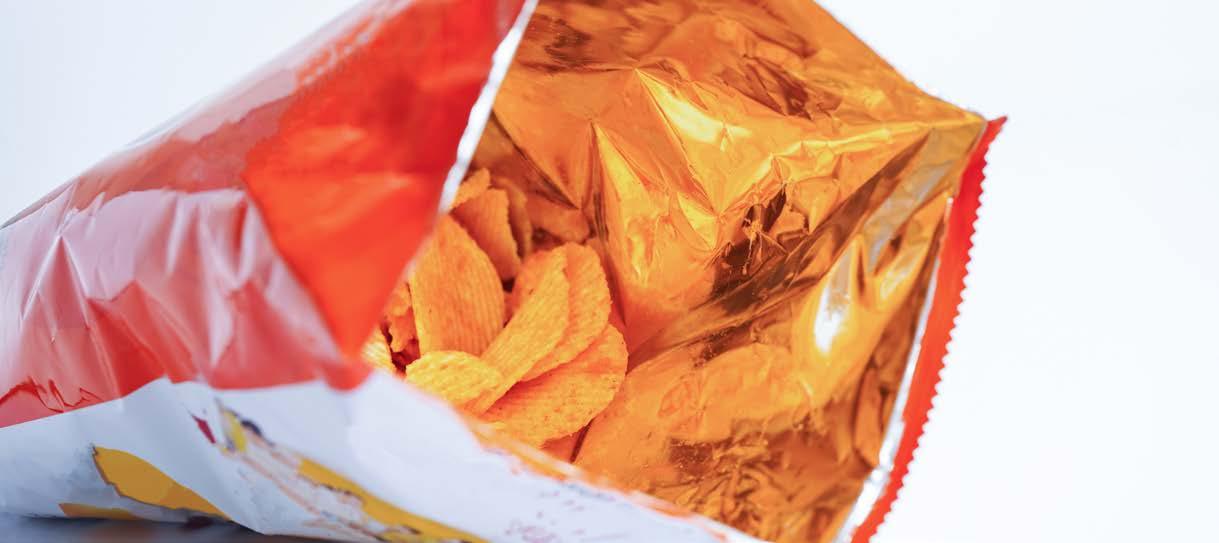
The Inspira snack bagmaker provides this versatility and is designed to form flat (pillow), flat with punch-hole, block bottom, gusseted bags and offers two sealing options, lap or fin. Inspira also handles modified atmosphere packaging and paper packaging.
This feature enhances production efficiency by reducing splicing time by 85%. An accumulator (festoon) holding material storage keeps production running while the splice is taking place. When the splice cycle is complete, the accumulator is re-filled, and the expired roll can be changed while the new roll is running.
The new splice table light-bar provides easier/faster film splicing, simpler film-feed with fewer rollers, and error-free forming tube insertion and removal.
Other features include film pattern alignment function and film positioning mechanism which facilitate automatic adjustment in the machine, removing wait time when film ends. Film splicing only takes 20 seconds, significantly reducing production downtime.

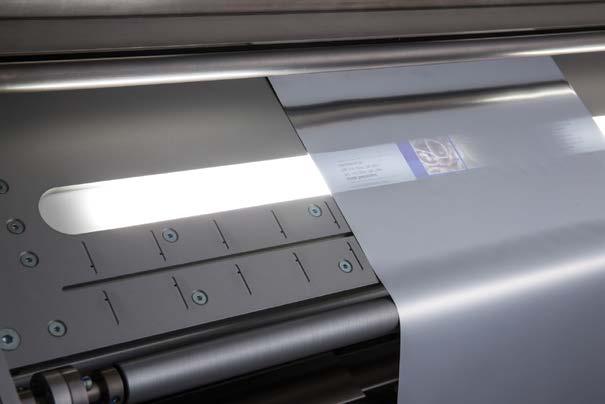
Packaging System Integration
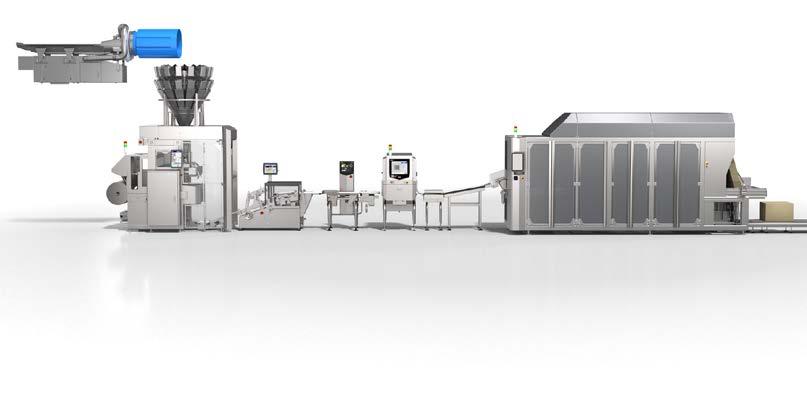
A key factor in the overall efficiency of a high-speed packaging system is integration with up- and downstream equipment such as a seal checker and automatic case packer.

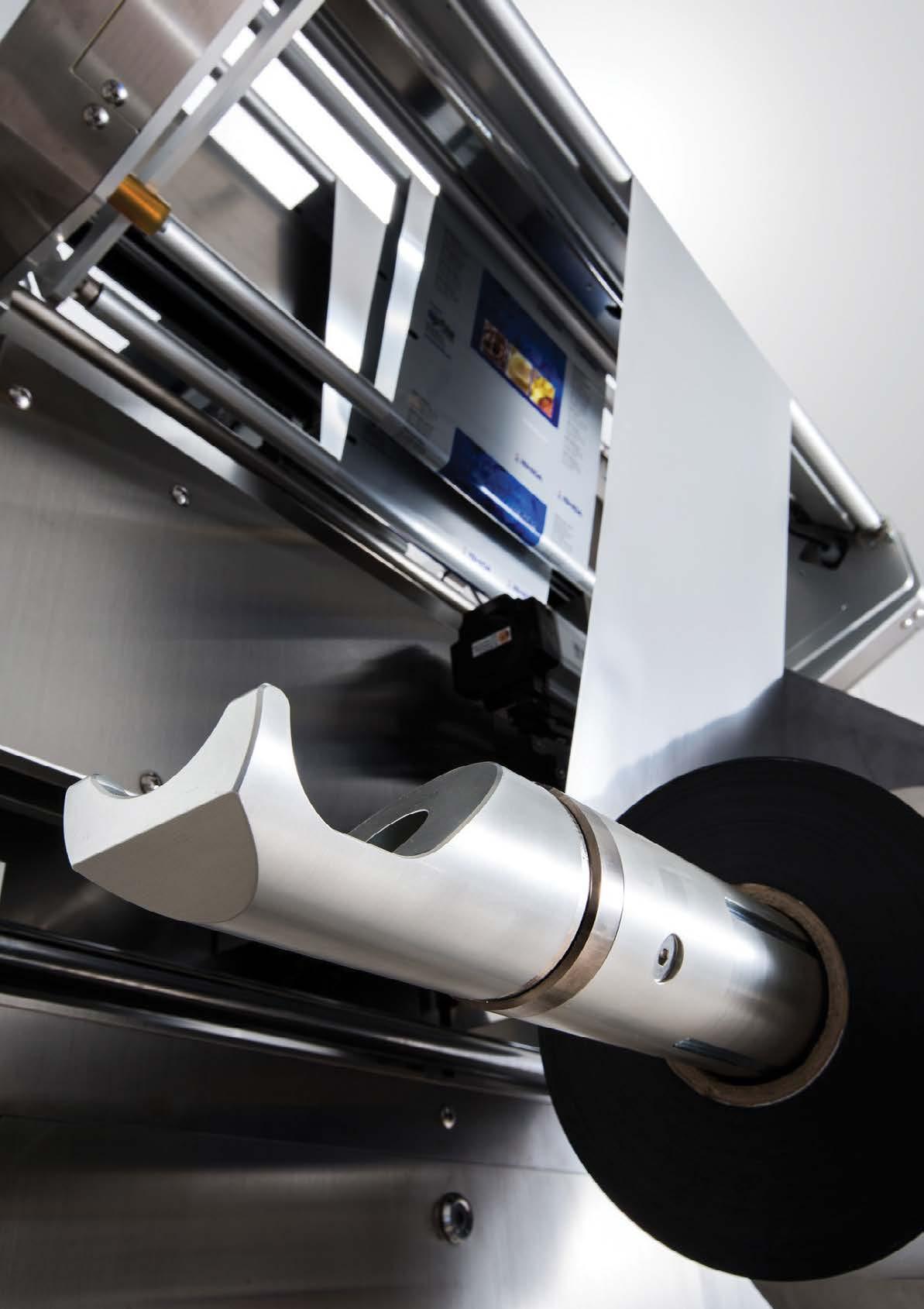
Ishida’s in-line seal checker, TSC-RVS, utilises feedback communications to the Inspira to manage bag thickness. The TSC can continuously monitor fill level and compare bags to the targeted value. In manual operations, an operator can compensate for variations in bag fill and bag thickness by applying increased pressure or manipulating the bag into a pack pattern. The combination of seal testing with bag thickness measurement with results being fed back to the bagmaker enables production of consistent bag thicknesses because the bag air fill is automatically adjusted.
For lines that incorporate an automatic case packer, thickness consistency is essential. Over or under filled bags can lead to line downtime to remove incorrect thickness of bags from a packed box. Underfilled bags can cause a poor appearance, and underfilling a case can result in damage to the product in transit due to bag movement. The Ishida Automated Snack Food Case Packer (ACP-702) receives pack air-fill data directly from the Ishida TSC-RVS seal checker, making instant adjustments to ensure reliable pack handling.
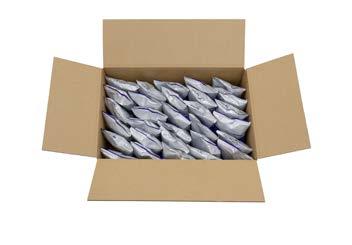
Market Success
Ishida’s bagmakers are already recognised by snack food processors as the industry benchmark in packaging technology. New features on this already market-proven equipment shows clear industry leadership from Ishida and displays a carefullyconsidered response to real customer feedback.
Inspira’s design innovates all the most critical areas of the snack bagmaking process: product and film handling, seal quality, accuracy, efficiency, weigher interface, changeover, and control and communication functions. By incorporating the latest technology available, Inspira significantly improves its performance, and its new features are earning it market success in the snack food industry.
Food Processing is a fiercely competitive market and consumer demand for new and different product varieties continues to grow. Expanding your product range can present challenges — when choosing the right inspection equipment — to cope with a variety of product characteristics.
As the complexity of packaging and processing lines increases — food processors are seeking strategic partnerships — to optimise their inspection process, and run multiple products through the same lines.
Choosing the right Metal Detector
Choosing the right metal detector can be a complex process. Especially when product characteristics such as salt content and temperature variations are involved. This is when it becomes critical to choose the correct model of metal detector, so you can be sure it will cope with numerous variations.
Our Packaging and Inspection Systems Manager, Robert Marguccio, says many processors are expanding product ranges to remain competitive and/or capture new markets.
“The pandemic saw many of our customers add subsequent production lines,” says Marguccio.
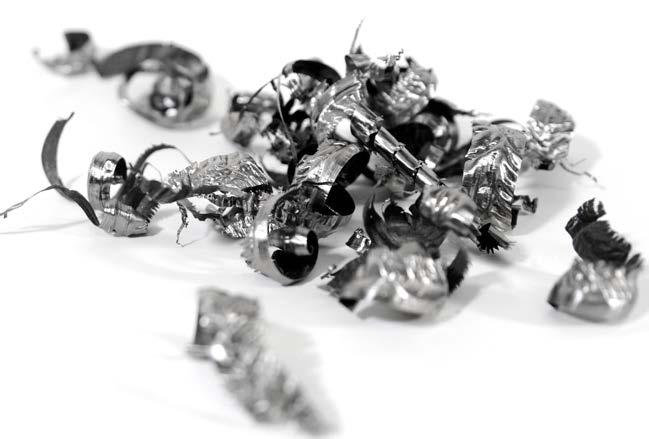
“Doing so helped them pivot their operations and meet demand for new and different products”.
“But as production increases, many operators discover their standard metal detector is no longer able to cope with the variety of products running down their new lines.”
Choosing the right metal detector is an important choice and will be based on the type of product you intend to run. But, there are highperformance inspection systems which can successfully manage a variation of products, and a range of new systems based on cuttingedge multi-spectrum technology are now available.
CEIA is the world’s largest manufacturer of metal detectors — and the only company to make metal detectors using patented cutting-edge multi-spectrum technology. Their innovative technology uses multiple frequencies simultaneously — meaning they can increase sensitivity — reduce false rejects — and detect thin metal fragments.