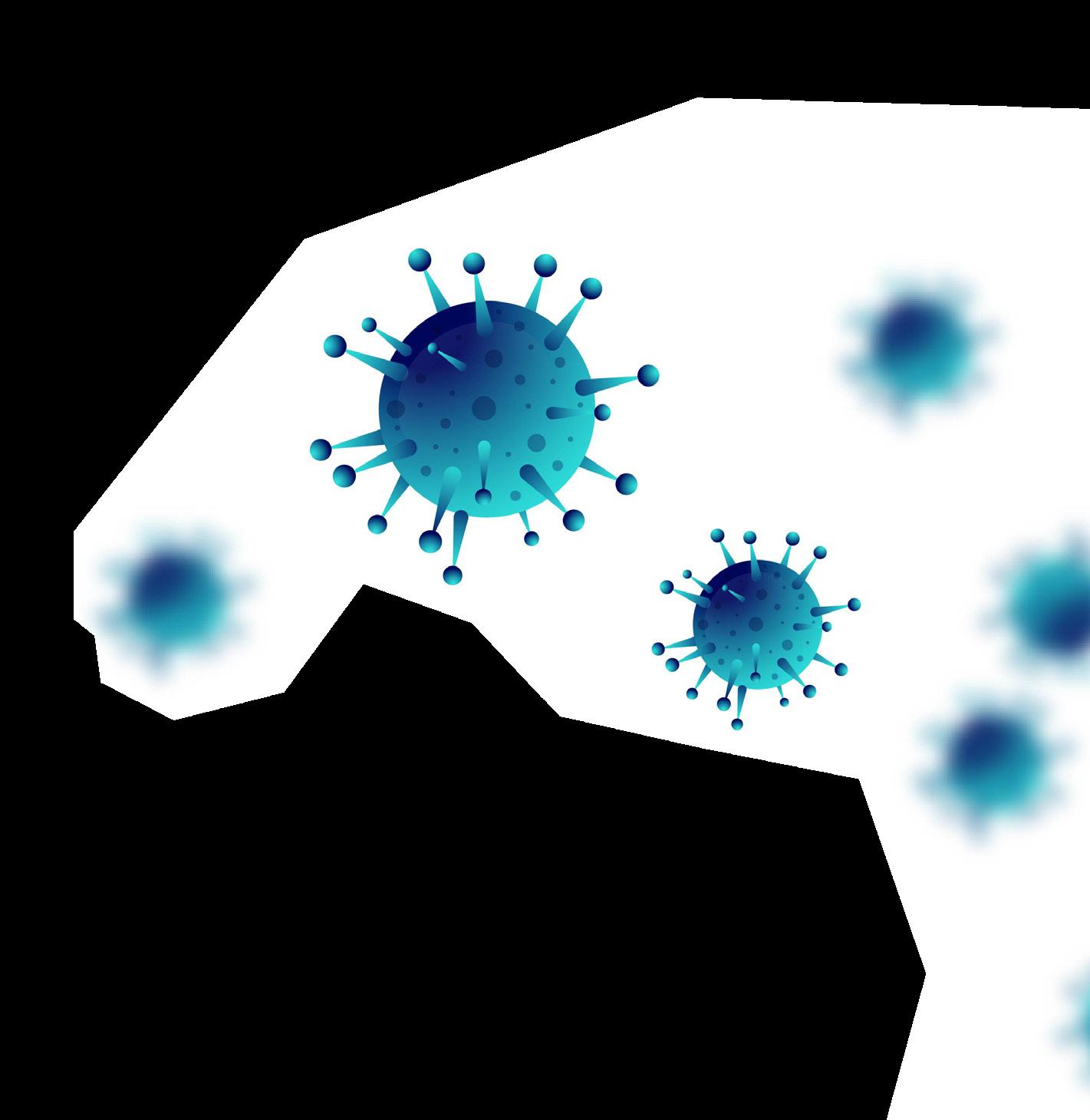
22 minute read
Corona and agriculture
Corona and agriculture The impact on our industry

Advertisement
This is the first time, for all of us, that we are experiencing a pandemic like coronavirus. The impact was difficult to estimate but measures had to be taken and choices made. Now that the pandemic is more or less under control, the time has come to take stock. What are the consequences for our sector?
Antoon Vanderstraeten Antoon Vanderstraeten & Fabrikanten
In December 2019, several people fell ill in Wuhan (China), with symptoms of pneumonia. One and half months later, the first cases in Europe were diagnosed and then it went extremely fast. In just a few days, the infections increased by thousands at a time around Europe. On 11 March 2020, the WHO officially recognised the outbreak of COVID-19 as a pandemic. A few days later, most European countries made the decision to close their national borders as part of a lockdown. The agricultural sector, and its related sectors, was considered a key sector, in which work could continue. Initially this meant that not much changed for farmers, although the restrictions had a number of consequences, nonetheless. Some manufacturers of machines and materials chose to close their plants to prevent possible contamination and the spread of the disease. In many cases, the choice was prompted by the rules that were imposed by the different countries.
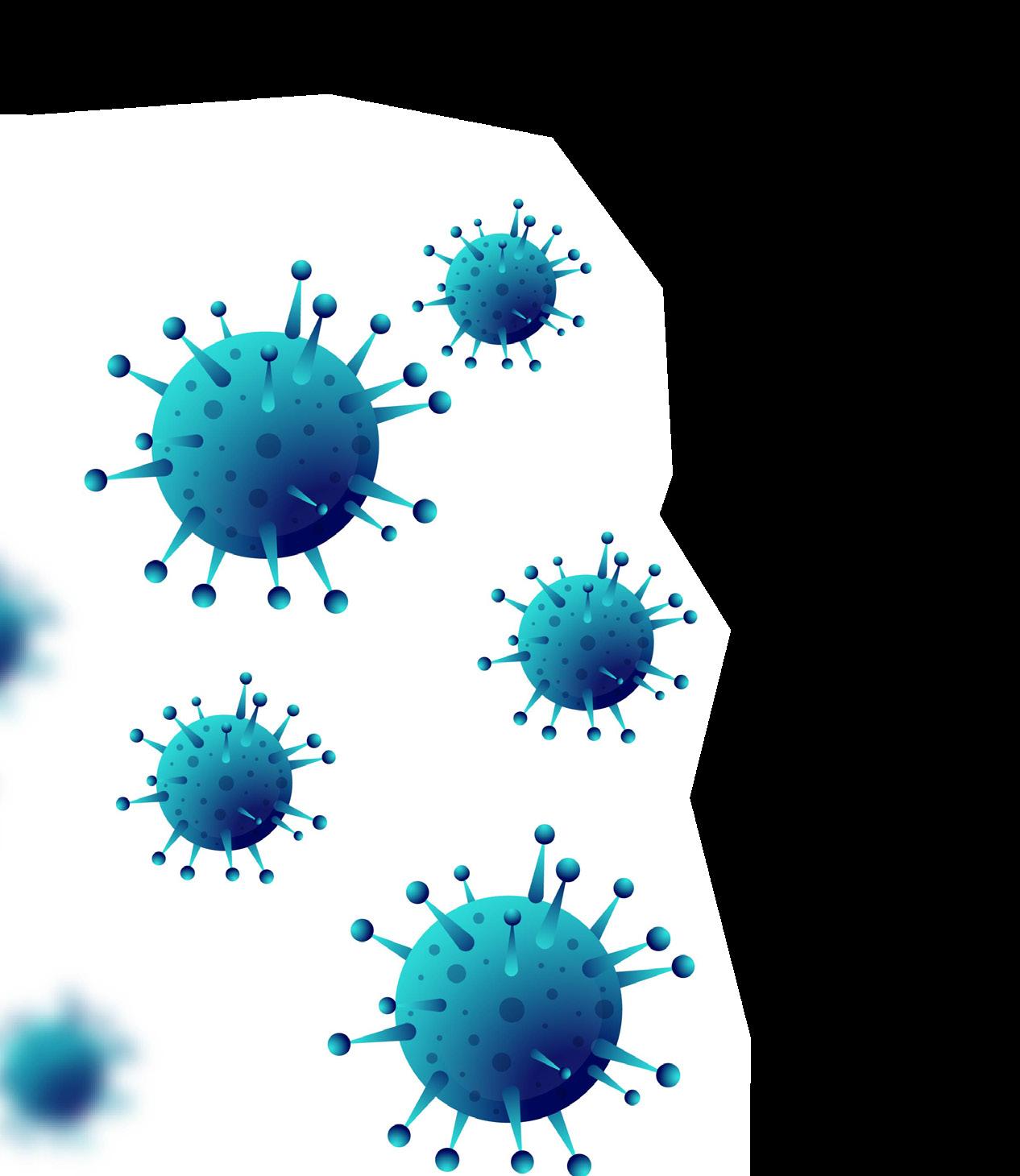
In the field
As most grains, rapeseed, and roughage are sown before winter, the pandemic had no impact on this. Nor did it have much of an impact for crops that are sown and planted in spring. Because this is done mechanically, with machines, farmers and contractor workers were able to respect the necessary social distancing, ensuring that work could continue without too many problems. The situation was quite different in the fruit and vegetable sector, however, where workers often sit very close together. Many Western and Southern European companies depend on Eastern European workers for the planting and harvesting of their crops. Suddenly they had no workers to rely on, because the borders were closed and due to the fear that the workers would become infected. Companies, often assisted by national or regional federations, tried to find workers on the national level, but many vacancies remained unfilled. The national governments of Germany, Belgium, and the Netherlands supported them, calling on people to step up. To avoid jeopardising the strawberry and asparagus harvests, among others, the German government enacted special measures to transport 40,000 seasonal workers to Germany by plane. The special rules also meant, among other things, that these workers were quarantined on the farms where they worked and that they were not allowed to have any contact with other workers. In Belgium and the Netherlands, an airline called The Aviation Factory operated special charter flights to fly in Romanian workers from Cluj and Iasi to Eindhoven to assist Belgian and Dutch horticulturalists.
“The fact that Europe chose to let seasonal workers fly in again fairly quickly is positive in itself. Unfortunately, there were differences between the various Member States”, says Jo Lambrecht, Manager Sales & Marketing at Belorta, one of the largest cooperatives in Europe, with 1,100 Belgian and Dutch affiliated growers.

The asparagus harvest seemed compromised at the start of the season, but the situation quickly stabilized.
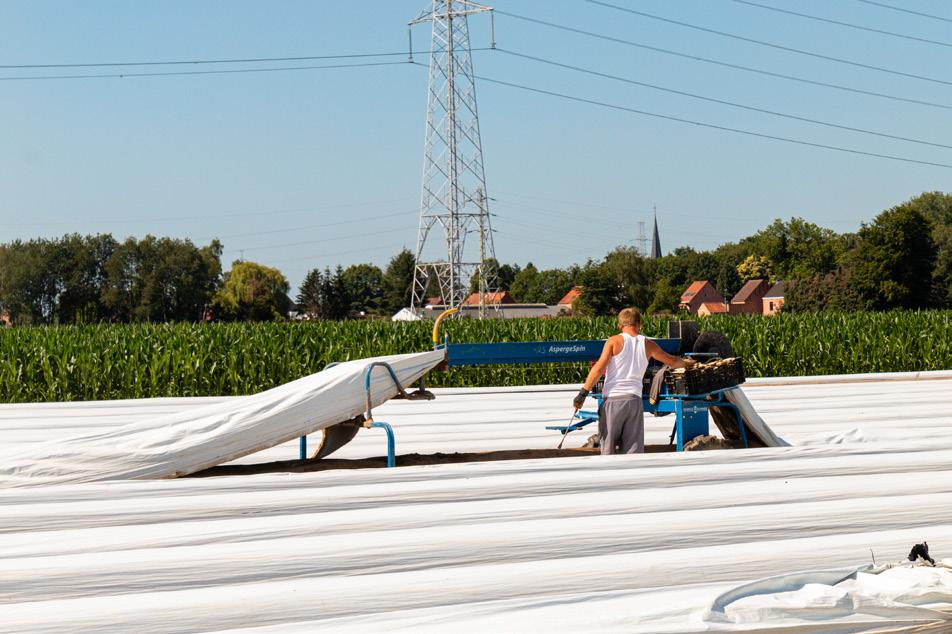

The activities in greenhouses was able to continue despite the pandemic.
“Based on the supply figures, we can conclude that the majority of the affiliated growers were able to maintain their production during the lockdown. The impact of the weather seems much greater than that of the pandemic, I think. In terms of product marketing, the first weeks were a real rollercoaster. We noticed an increase in turnover (up to 30%) during the first week of the lockdown because people started to hoard. This happened in Belgium and abroad (Belorta exports 55% of its products, ed.). Consumer sales soon stabilised, albeit at a higher level than in previous years, because people were forced to cook themselves as all the restaurants were forced to close. The demand for packaged products also increased substantially, probably because people were afraid of contamination.” There were a number of logistics and transport problems in the early days of the lockdown too. Trucks could not cross the border, but these rules were soon relaxed on the European level. For more distant destinations, the lack of containers proved problematic, as these were stuck in Chinese ports that had come to a standstill, as did the fact that cargo planes were grounded.
The additional turnover that was generated during those first weeks of the crisis does not mean that European farmers and horticulturalists did not suffer as a result of the crisis. A quick check reveals that a large group is being paid a lower price for its products, while raw materials such as seeds, animal feed and medicines have increased in price. This has consequences for the company’s turnover, undermining the company’s desire or opportunity to invest. In addition, the situation also caused a lot of stress and worries.
Professor Sebastian Lakner, who lectures in Agricultural Economics at the University of Rostock, thinks the corona crisis will have a number of consequences for the future. “This crisis has revealed a number of problems in terms of working conditions in the agricultural sector”, he says. “In Germany, for example, there were three slaughterhouses with high infection rates. Further investigation revealed that the workers lived together in poor conditions. In addition to this, many farms and slaughterhouses engage in rather questionable practices, registering workers as self-employed persons or charging them high prices for the accommodation that they provide. The German government therefore banned the use of subcontractors in this sector from January 2021 onwards.” So far other claims, such as the fact that agriculture would be seriously affected or that this would compromise the EU’s food supply, have not been confirmed. Lakner did point out that that mutual trade and well-functioning supply chains played an important role in securing supplies during the lockdown. World trade issues therefore still have all the potential to become critical if some exporting countries decide to impose export restrictions. Finally, the reform of the CAP after 2020 will become an important topic for discussion in the months to come. The EU Commission has presented its biodiversity and Farm to Fork strategies. Both have major implications for agricultural policy. Currently attempts are being made to take environmental themes off the
All manufacturers implemented special measures to prevent transmission of the virus.

Several manufacturers, including JCB, used the freed production capacity to make tools to battle Covid-19.
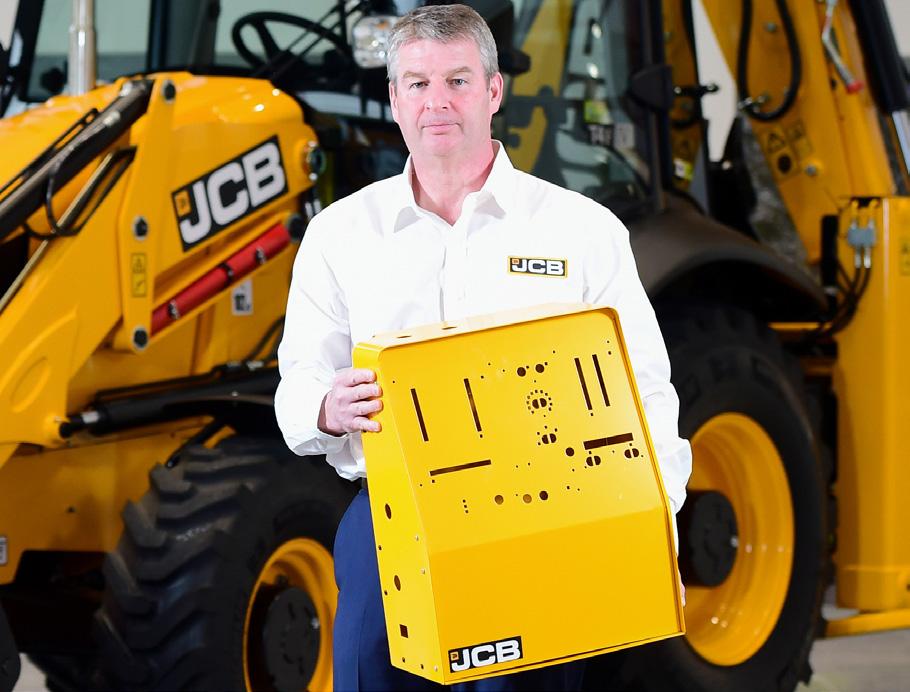

CNHi closed all of its factories at the start of the pandemic. Today, all production sites are active again, with the necessary precautions.
agenda, citing the COVID-19 crisis as a reason, but the published facts do not support this argument. And while this argument is largely made up, it is fair to say that the climate and biodiversity crisis continues unabated. So there is a lot at stake for the next reform. Currently it is completely unclear whether the reform of the CAP will be an ambitious one, or whether we will have a business-as-usual CAP in the coming years.
In factories
Whereas the direct impact of coronavirus was not that substantial in the field, the situation was completely different in the plants that produce agricultural machinery and accessories for this sector. Because a number of European manufacturers work with Chinese suppliers, production was delayed in various plants, during the first weeks of the crisis, such as at JCB, due to an expected lack of parts. Shortly after the WHO labelled the corona outbreak a pandemic, a number of manufacturers made the decision to close down their factories. “On 20 March, our management made the decision to suspend the majority of our European assembly operations, in light of the supply chain constraints caused by the COVID-19 pandemic”, says Silvia Kaltofen, PR Manager Case IH Europe at CNH Industrial. Since then the majority of our plants are operational again, but the health and safety of our workers continues to be a priority when making decisions about suspending or restarting assembly activities. To this end, our company is following all national directives by implementing stringent measures. We continue to share and leverage internal best practices globally. This latest decision was reached in agreement with all the social partners in the countries in which our company operates.”
Spanish company Ovlac also suspended all production. “Because of the Spanish government’s measures, we were forced to close our factory for eight business days”, says Pablo Gutierrez, Director of Communication at Ovlac. “The consequences of this closure, and of the coronavirus crisis as a whole, are negligible for us. None of our employees fell ill, our suppliers continued to supply us with parts and orders have also picked up again, returning to normal levels after a minor dip during the first few weeks. If we have learned anything from this crisis, it is that teleworking is a workable option for our company. It enables us to work more efficiently while also saving time because people no longer lose time commuting to and from the office.” According to Gutierrez, the pandemic will not have any major consequences for the future. “We think that life will return 90% back to the known “normal” after a few months. Whether this is wise, is an altogether different question.”
Other companies that completely shut down production include JCB, Kuhn, Merlo, Deutz-Fahr and Manitou. A number of other manufacturers were forced to reduce their production. Claas slowed down production, while Agco was forced to close its Marktoberdorf and Asbach-Bäumenheim plants due to a lack of parts, while other plants were able to continue producing. John Deere’s engine plant in Saran (France) was forced to
The Belgian company AVR was able to continue its production during the pandemic.

suspend production, which had an impact on the rest of the production line. A number of manufacturers used the freed-up production capacity to produce safety equipment. JCB produced steel enclosures for ventilators in its cab factory in Staffordshire. Both Massey Ferguson in Beauvais (France) and John Deere used their 3D printers to print face shields and fastening material for these face shields. By mid to end April, operations resumed in most plants, in some cases after extensive disinfection.
However, there were other manufacturers who chose not to close their plants, where production continued. “During this pandemic, it became clear that the agricultural sector was a key sector. As a manufacturer in this sector, we made every effort to remain operational”, says Tine Coopman, Marketing & Communications Manager at AVR. “The pandemic did not have a substantial impact on our company. We had already received most of our orders in the period between November and January. None of the contracts were cancelled. We had a few more absentees than usual during the early weeks of the outbreak, but none of them had the virus. To ensure our employees’ health and safety, we took the necessary measures and ensured that everyone followed them to a tee. We have been implementing the new guidelines that were issued by the government for quite some time now. We have enforced minimum occupancy in our offices. Employees who can work remotely work from home. Our production facilities are spacious, ensuring that our production workers do not have to come near each other. Company visits are the exception, but we enforced the COVID measures for this. We will continue to do this for as long as necessary. Obviously, we embraced digital technology. We held a digital press conference, which was a new way of working for us, even though we are machine addicts.”
Slovenian company SIP was also able to keep production going. “Fortunately, the corona outbreak did not hit Slovenia as much as it did other European countries. We were therefore able to continue producing without interruptions”, says Mihael Miheljak, Marketing Director at SIP. All the measures we took to protect our employees proved successful since the onset of the crisis. The SIP plant did not have to suspend production at any time. As we rely on European suppliers for the most part, we didn’t experience any disruptions in terms of parts deliveries. In fact, we even almost used 100% of our production capacity during this period. Several trade shows and demos had to be cancelled, however, due to the travel restrictions that were imposed. Field support was also disrupted by this measure.”
It is unclear whether the pandemic will have long-term consequences for manufacturers. The pandemic did change these companies’ views on how to do business. “Our management is of course evaluating the consequences of this crisis on our business on an ongoing basis”, says Silvia Kaltofen (CNHi). “Based on the evolution of the pandemic and the overall outcome, they will decide on the necessary actions at the appropriate time. We have of course modelled a variety of possible outcomes, so we will be ready to respond in a timely manner.” She adds that “it is difficult to evaluate the situation at the moment, due to its very fluid nature, but we believe that the situation will return to more normal levels in due course”, Kaltofen adds. “The measures have a domino effect. Due to the compulsory closure of hospitality firms, the market for potatoes for chips collapsed, which put a strain on all the underlying links. This also had an impact on our customers, on potato growers, in other words. As a result, our order intake for 2021 will be under some pressure, especially in Belgium”, says Tine Coopman (AVR). “But we had had years in Belgium where the average price for potatoes stood at €2.5/100 kg. This year we expect the average price to be higher. In the long term, this definitely could have turned out much worse for us.”
According to Mihael Miheljak (SIP), the real effect on businesses will be felt during the last two quarters of the year, if a second or third wave will hit Europe. “In the future, the European Union will have to rely on domestic food production. Support for European farmers will be crucial if we want the food supply for its citizens to remain independent”, he adds.
Almost all fall 2020 shows are canceled. 2021 will be a busy year!

TRADE SHOWS
The pandemic has also had consequences for agricultural trade shows around Europe. These were unable to take place due to the various national measures relating to events with more than 100 to 1,000 people. Some were postponed until autumn. In other cases, the 2020 trade show was simply cancelled. Maskiner under Broen (Denmark) has been postponed until 2022. The EIMA Bologna, which was supposed to take place for this year in mid-November, has been postponed until February 2021. SIMA, which was supposed to take place for the first time this year in November, has also been postponed to February. Ordinarily SIMA always took place in February, but the organisation decided to move the event to November during even years. As a result of the pandemic, the organisation was forced to reschedule it to the original date. “Several exhibitors asked us whether we would consider rescheduling this edition to the original date”, says Isabelle Alfano, SIMA’s trade show director. “The coronavirus pandemic has hit firms in this industry hard, including on the financial level. That is why we were happy to respond to their request, which is why the next trade show will take place in February 2021.” In Belgium, the Foire de Libramont was cancelled as a result of the pandemic. In the Netherlands, both the Potato Demo Day and Agrotechniek Holland were cancelled for this year. In Germany, the DLG Feldtage and EuroTier/ EnergyDecentral exhibitions were postponed to 2021, which is shaping up to be a very busy year, with both EIMA and SIMA in February, the DLG Feldtage and Agritechnica in Germany and national trade shows such as Agribex (Belgium), ATH (Netherlands), Maskin-Expo (Sweden), Agromek (Denmark) and many others.
“As organisers of Agritechnica, EuroTier and Feldtage, we are in close contact with the exhibitors throughout the year. This continual commitment to the agricultural sector at the practical level enables us to select suitable dates. This also applies in the case of a postponement of a show”, says Peter Grothues, Managing Director of the Exhibitions Department at the DLG. “The first thing we need to do is get feedback from the companies and farmers, whom we already have access to through our working groups and members. Our selection of dates for 2021 is driven by these two groups, farmers and exhibiting companies.”
“I believe 2021 will be a challenging year full of ‘special editions’ as we are all having to adapt to new conditions. However, in these past four months we have already accumulated a lot of new knowledge about how to handle this situation effectively. The Covid pandemic has also given us the space, if you like, to come up with new and creative ideas for our exhibitions and events, which in the future may mean that we are able to reach even more people. The objective of the DLG – the German Agricultural Society - is to further knowledge and for us, exhibitions are a fantastic tool that enables efficient knowledge-sharing between farmers and equipment makers. We are focused on continuing to make that tool more efficient. No one knows what will happen in the next two years, but I am convinced that as time goes on, we shall learn much that will help us return to a new normal where farmers will still be able to benefit from exhibitions.”, Grothues concludes.
Now that the pandemic is weakening worldwide, we look back on an unprecedented period. The agricultural sector was labelled a key sector, an acknowledgement of the work that so many hands do in the fields, in greenhouses, and in stables. Will we, as a sector, come out unharmed on the other side of this crisis? As far as we can determine, the impact is less than feared. But the impact is definitely there. The agricultural sector is a long-term sector, where choices that are made today will only yield results in a few months’ time. Whereas the consequences are almost immediately noticeable in other sectors, our sector will only be able to assess the real impact of this pandemic in the long term, in the next months or even years.

Vervaet: a small family business transforms into a leading international player
Dutch company Vervaet is definitely the reference in Europe for slurry and manure processing or beet harvesting. The company alternately produces beet harvesters and manure trikes in its plant in Biervliet, depending on the seasons.

Kim Schoukens Antoon Vanderstraeten, Tom Goaverts & Vervaet
A Hydro Trike injects digestate in corn in Italy.

Lifting sugar beets near Brussels (Belgium)


How it all started
The story of Vervaet started in 1957, when Frans and Richard Vervaet, the sons of agricultural contractor Jef Vervaet and his wife Madeleine, decided to set up their own company.
“They repaired and serviced anything with an engine, from fridges and motorcycles to cars and even tractors”, according to the company.
As a result of the explosive growth of mechanisation during this period, there was a lot of demand for their services. In 1958, the brothers became Nuffield Tractors dealers. The customer base and the company expanded and by 1960, they moved into new premises in Biervliet. In time, Vervaet also became a dealer for Simca and McCormick, forcing the company to expand again in 1961.
To ensure the company’s continuity and growth, the brothers acquired several other companies in the early seventies. Vervaet switched from McCormick to John Deere and the rest is history.
Own production
By this time, several of Vervaet’s ten children had joined his contracting business. In those days, Walter and Marcel Vervaet needed a self-propelled machine to harvest sugar beets, which is why they started thinking about how to develop such a machine. In 1974, Frans, Richard, Tonnie, Walter, and Marcel Vervaet joined forces. Together they built a self-propelled one-phase bunker harvester for sugar beets based on the principle of the combine harvester: a header for harvesting at the front with a large bunker at the rear. During the very wet fall of 1974, the new machine proved its worth: it was able to continue operating thanks to its large, simultaneously driven wheels, whereas tractor-drawn harvesters got stuck in the mud. Thanks to the machine, the topping, harvesting and transport could be done by one person. A real revolution compared with the traditional twoor even three-phase harvesting process. The concept of a self-propelled beet harvester proved far from popular, however, and Vervaet ended up investing a lot of energy in convincing people of the concept’s merits. The development of the machine did not go as seamlessly as they had hoped either.
Four years after the construction of the first bunker harvester, the Vervaet family made a second attempt to build a new, improved machine, partnering with Heyens (of Hulst, the Netherlands). Heyens came up with a concept without a topper, but with a better harvesting system. It was a success. The machine performed well in the field and garnered a lot of interest. While the bunker harvester was more expensive than traditional machines, it was also more cost-efficient to use. After a few years, the first machines were traded in for new ones and the used ones were rebuild and adapted in line with the newest techniques. As they were technically new, they were resold, under warranty. An approach that would prove highly lucrative.
By the early eighties, the first hydraulic drive systems were fitted on machines and the operator’s comfort was significantly improved thanks to the modern Claas cabs.
Hydro Trike
To give Robin and Edwin, the second generation who were raring to join the company, the space they needed to operate and further professionalise the company’s operations, Vervaet was split into three entities in 1987: a Mazda car dealership, a John Deere agricultural machinery dealership, and the production of self-propelled beet harvesters.
Two years later, Robin and Edwin joined the family business. In 1990, the two brothers developed a threewheeled vehicle for slurry injection, together with Dany Dieleman, anticipating on the new legislation that would ban the aboveground application of slurry. The Hydro Trike was born.
In the early nineties, a factory was built in Biervliet for the production of these new machines. By 1992, the company produced 15 Hydro Trikes
Beet harvesters for season 2020 in production

One of the first harvesters was restored and can be admired in the showroom.


a year, in addition to the same number of beet harvesters.
As a result of the enormous potential of these machines and growing demand, Vervaet tapped into new international markets, including the UK, Belgium, France, Sweden, and Denmark. Production flourished and soon the existing plant had to be expanded again.
17T beet harvesters
Soon competition increased thanks to new machine launches. The demand for a larger machine with a greater bunker capacity, larger wheels and better cleaning of the beets grew. In 1993, Vervaet struck back with the prototype of the 17T beet harvester. The new concept was such a success that the decision was made to increase production from 13 to 25 harvesters the following year.
Vervaet 2000
In 1999, Vervaet took full control of the production. To achieve this, the plant had to be expanded and the company needed to hire more employees.
Beat Eater and Hydro Trike for XXL
Vervaet was the first company to launch a six-row harvester, as well as the first company to launch a ninerow concept in the 2000s, called the Beat Eater. During this period, the demand for harvesters that could compact the soil evenly increased. The company believed that the only way to achieve this was to develop a nine-row machine, to increase capacity, without increasing the speed too much. The Beat Eater was a huge success in the small beet harvester market. Five machines rolled off the line every year.
The concept of the Hydro Trike XXL was revised, with an additional tank behind the existing trike, increasing the total capacity to 24m 3 .
Vervaet today
A new decade brought new expansion. By 2010, the agricultural machine division operated out of three plants. A new warehouse, showroom and storage shed were added to the premises in Biervliet.
One division that is becoming increasingly important at a modern company such as Vervaet is R&D, which continually monitors the market to develop new variants. All the development is purposefully done in-house.
Since then, the company also developed an umbilical version of the Hydro Trike. This self-propelled slurry injector with a draghose has several advantages, including higher capacity, one wide wheel per track and it can easily turn on the headland, while the pump continues to operate on the suction side. The international market for this machine (Germany, France, Italy, and the UK) became increasingly important. In 2016, the first self-propelled trikes for vinasse were supplied to the French market. These machines can spread small amounts across large widths and can achieve extremely high speeds in the field: up to 35 km/h. The Hydro Trike Universal Spreader was updated and adapted to meet the requirements of the French and British markets, respectively.
At the same time, Vervaet continued to work on the development of its beet harvesters: in 2010, the Beat Eater 617 and 625 won awards at BeetEurope. Six years later, the company designed a new type of beet harvester, called the Q Series. The Q616 is a light-weight vehicle with a 16-ton bunker, whereas the Q621 is heavier because of its 21-tonne bunker.
Third generation
Since then, the third generation has joined the family business. The company premises cover a surface area of 50,000 sqm. of which 13,500 is built up. Ten percent of the turnover goes to R&D and the company produces 75 to 100 new self-propelled machines every year.
What originally started out as a small family business soon became a leading player on the international agricultural market.