
9 minute read
SUPPLY-SECURITY Growing appetite for silicon forces German automotive to take control of production
GROWING APPETITE FOR SILICON FORCES GERMAN AUTOMOTIVE TO TAKE CONTROL OF PRODUCTION
SUPPLIERS AT FOREFRONT OF EUROPEAN CATCH-UP OPERATION
Advertisement
The global shortage of semiconductors has put the handbrake on car production in Germany. With trends like e-mobility and self-driving cars, the German appetite for silicon will only increase, so manufacturers want to take back control. The aim is for Germany to become the global centre for semiconductors.
BERTUS BOUWMAN
Since the start of the pandemic, the production lines of Germany ’ s car industry have regularly been idle. This has mostly been caused by the global shortage of semiconductors –a problem that will not yet be resolved this year. On top of that, in the coming years the car industry will only need more microchips, argues Dutch chip machine manufacturer ASML in its ‘ position paper ’ on the EU Chips Act launched by the European Commission in February. The Veldhoven-based high-tech firm expects a radical shift driven by the move away from the internal combustion engine and the rise of self-driving systems. These trends have been on the horizon for a long time, but due to the shortage of chips the manufacturers have now discovered how vulnerable they are to geopolitical changes. The Chips Act is designed to bring a bigger share of semiconductor production to Europe in order to assure strategic autonomy. With a total of €43 billion in investments, Europe wants to increase its market share of the global chips industry from 9% to 20% by 2030.
COMPETING FOR CHIPS
Like ASML, the German automotive sector expects global demand for chips to increase, so a survey reveals. Nearly every technical device contains semiconductor chips. That means cars have to compete with consumer electronics like TV sets, smart phones and fitness armbands. Modern cars no longer work without semiconductors. And in the coming years, driver assistance systems, infotainment and electrification of propulsion systems will mean even more chips will be needed. The development has taken place at lightning speed. Research by the German electronics and digital industry (ZVEI) has revealed that the average car built in 1998 contained microchips worth €120. In 2018, that value had The production line of the BMW-plant risen to €500, in München. Photo: Harry Zdera and by 2023 it is expected to be €600. For a supplier like Bosch, this has meant a doubling in the number of its chips in cars over the course of a few years. In 2016, each new vehicle built worldwide contained more than nine Bosch chips on average, for example in the airbag control system, the braking system and the parking assistant. By 2019, the figure had risen to over 17.
MISCALCULATION BY CAR MANUFACTURERS
The global increase in demand for chips from the automotive sector was clear even before the pandemic. Nevertheless, car manufacturers were not prepared for the shortage. In early 2020, there didn ’t appear to be a problem. The semiconductor industry was experiencing a strong economic upturn. But when the Covid-19 pandemic broke out, car sales briefly collapsed. Panicking, car makers cancelled their orders with large chip manufacturers. This proved to be a major miscalculation. When car sales revived, they found that the semiconductor industry had reserved their production capacity for manufacturers of consumer electronics. During lockdown, consumers ordered smartphones, tablets, laptops and games consoles on a massive scale in order to make the experience of being at home more pleasant. Leaving the car manufacturers out in the cold.
INCOMPLETE CARS
This is why Mercedes-Benz had to cut back production last summer, for example. Beside its factory in the south of Germany, there are car parks full of cars that cannot be delivered because chips are missing. It therefore regularly delivers cars which are not fully equipped to customers at a discount. In practice, however, it is not always possible to upgrade later. The problems faced by Volkswagen in Wolfsburg are even more severe. There, night shifts for the production of the Golf model were cancelled in early 2022. One production line for the popular Tiguan is at a standstill. In 2021, VW produced 8.1% fewer cars than the year before due to the shortage of chips. For all brands of the VW Group, the figure was 4.5%. At a press conference late last year, CEO Herbert Diess put the figure for the number of cars they had been unable to deliver due to the shortages at 600,000. BMW, too, faced major problems and responded by significantly adjusting production programmes, explains spokesperson Sandra Schillmöller. Even so, in factories in Oxford and Regensburg that normally build nearly 1000 cars per day, production has sometimes had to be halted for several days at a time because components were missing. In certain cases, BMW has delivered new models without touchscreens for a lower price. BMW was eventually able to work away the backlog in the second half of 2021, says Schillmöller. ‘In fact, we are producing more vehicles than in 2019. ’
GERMAN SUPPLIERS TAKE CONTROL
So German automotive needs to take control. Like all the other manufacturers, BMW does
not expect the shortages to be resolved this year. The Bavarian marque is focusing on adjusting its own organisation in order to be able to respond to the fluctuations even more flexibly. ‘We have faith in our own flexible production system and working hours models. They allow us to adjust quickly when necessary ’ , says a spokesperson for the company. Automotive giant Robert Bosch is taking a different approach, relying on the strategy it was pursuing before the pandemic. The manufacturer based in Baden-Württemberg is the only supplier that also produces its own chips. For instance, it makes its own application-specific integrated circuits (ASICS), power semiconductors and, micro-electromechanical systems (MEMS). It is investing billions in their production. The new chip factory in Dresden that opened its doors in summer 2021 cost €1 billion, making it the biggest investment in the supplier ’ s history. Partly driven by the chip shortage, construction was accelerated and the firm was able to commence production of car chips six months ahead of schedule. In late October 2021 and in February 2022, the company announced new investments in production locations for semiconductors. For instance, it is currently building a new testing centre for semiconductors in Penang, Malaysia. The fully automated smart factory will be used for testing semiconductor chips and sensors from 2023. Bosch also plans to expand its existing semiconductor factory in Reutlingen around 2025. A new, ultramodern cleanroom covering 3600 m² will be built there.
CONTINENTAL: CHANGES IN PROCUREMENT
Continental, by contrast, will not be producing its own semiconductors. CTO Gilles Mabire told Automobilwoche that the company did explore that option but consciously rejected it. The Hanover-based supplier wants to be able to respond flexibly
to major fluctuations in supply and demand, and to this end it has launched the Strategic Project Semiconductor Management. This digital system is designed to restore the equilibrium within regular contracts between customers and suppliers. In this way, Continental aims to fix orders for the long term. This will also involve reserving capacity throughout the supply chain, including alert mechanisms that can flag up problems at an early stage. Continental is also looking at new methods of procurement within the chain. A rolling forecast looks ahead 24 months in order to estimate the demand for components. For strategic components, the company projects a full five years into the future. This planning process is intended to digitally link the entire chain together. Mercedes-Benz is also developing new procurement processes. Head of the works council Michael Brecht told the press agency DPA that he expects all car manufacturers to do the same. Diversification is the most important principle. ‘Car manufacturers will start buying raw materials and strategic components globally themselves in order to become less dependent on the big suppliers. ’
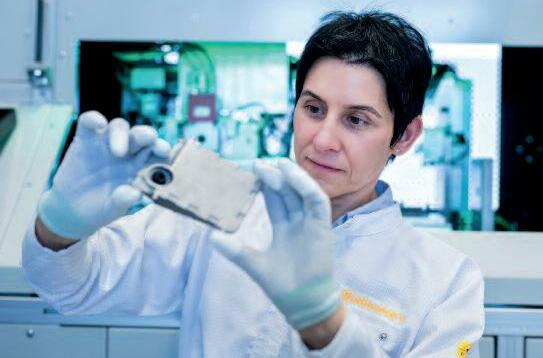
Impression of the Continental-plant in Ingolstadt. Photo: Joerg Koch
SILICON SAXONY: BIGGEST CHIP CLUSTER
INVESTMENT CLIMATE CRUCIAL
Even so, more is required than individual efforts on the part of firms, say the manufacturers. A good investment climate for the semiconductor industry is crucial in order to unleash the chips offensive which the European industry hopes will make it more autonomous, says Stefan Joeres, director of Business Development and Semiconductor Strategy at Robert Bosch GmbH. ‘Innovation in microelectronics is the key to the green and digital transformation of Europe. So it is crucial that we increase our production capacities in all areas of semiconductor. ’ At Continental, they point to the importance of investing in foundries for semiconductors in Europe, in order to ensure that the European automotive sector can avoid similar fluctuations in the supply chain in the future. But that will take time, even if everything goes well, says spokesperson Susanne Einzinger. ‘When you make big investments in new facilities, it takes 18 to 24 months to effectively increase production. ’
THINKING IN VALUE CHAINS
In order to be able to compete with the rest of the world, Europe more than ever needs to think and act consistently in terms of digitisation in resilient value chains, says Joeres on behalf of Bosch. ‘The pandemic has shown us that much. Digital sovereignty is a key factor for Europe ’ s competitive position and welfare. ’ At the same time, it is also clear that Europe cannot eliminate its dependence on the rest of the world in all areas, says Joeres.
‘Europe will only be able to successfully compete globally if we are able to bring our own technological core competencies to the table. Otherwise we risk our economic competitive position and ultimately our welfare. ’ In concrete terms, that means the European semiconductor industry needs to invest not only in the manufacture of chips with the smallest structures, says Joeres. ‘We also need to invest in chips which the car industry needs most, now and in the future. ’
The European offensive is also in line with the aims of the new German government under Chancellor Olaf Scholz to make the country the top global location for the semiconductor industry. The ink was barely dry on the coalition agreement that spelled out this goal before the American conglomerate Intel announced it would be building two new chip factories in Magdeburg, which are due to be ready by 2027. Germany is able to subsidise Intel’ s arrival to the tune of billions thanks to the EU Chips Act. Chair of the European Commission Ursula von der Leyen described the multibillion euro investment as the first major milestone for the European directive. Taiwanese chip giant TSMC is also exploring opportunities in Europe. In Dresden, a two-hour drive from Magdeburg, Intel’ s arrival has been welcomed. Industry body Silicon Saxony called it a major victory for Europe ’ s leading high-tech cluster. That cluster consists of 400 firms including chip manufacturers like GlobalFoundries, Infineon, Bosch, X-Fab, Siltronic, Zeiss and Jenoptik AG. These high-tech businesses are located in central Germany in a triangle between the cities of Magdeburg, Erfurt/Jena and Dresden. The region is also home to various research institutes with a focus on semiconductors. As a result, central Germany already has Europe ’ s biggest chip cluster and it hopes to define the European semiconductor industry in the near future.
• • • w w w ww. ww. ww. bosch.com continental-corpora silicon-saxony.de tion.com