
8 minute read
Milling
from Everything Lab 2021
Milling Units
Z4 Chairside Milling:
Advertisement
The digital workflow makes it happen: you and your patients can benefit from more pleasant treatments with first-class restorations in just one session. The Z4 is an investment that will pay off for you: high-quality restorations with maximum independence. The number of machinable block materials constantly increases as well as the number of scanners and CAD software packages that are validated with the Z4.
When it comes to wet machining blocks, the Z4 sets unprecedented quality standards. Fabricate glass-ceramic, PMMA, zirconia and composite restorations in mere minutes and finish highly accurate prefabricated titanium abutments. A scientific study at the University of Washington proved that using the Z4, users can drill screw-access channels for hybrid implant restorations into ceramic blocks with no significant difference in flexural strength compared to factory-fabricated materials, known as “meso” blocks.
These blocks are significantly more expensive, and the laboratory design method requires a more sophisticated CAD process. Thus, processing standard blocks with the Z4 means less cost for material and less material inventory necessary. Jack M. Keesler, DDS, MSD. Effect of milling screw-access channels on flexural strength of CAD/ CAM ceramic materials. MSD Master’s Thesis, University of Washington, 2019.
Z4 stats:
Highest precision
Milling and grinding in ultra HD Proven industrial quality 3 microns repetition accuracy
Fastest production
Restorations in under 10 minutes
2-second block insertion
100,000 RPM electrical high frequency spindle
Extremely economical
Clear water – no additives necessary Mill screw-access channels, to save costs for “meso” blocks
Automatic changer for 6 tools Self-opening working chamber door and drawer Easy to learn, easy to operate 24 months warranty CAM software included
Tool starter set included
Complete independence
38 block materials from 20 manufacturers – and growing 800+ prefab titanium abutment blanks from 11 manufacturers
Validated with all established scanners and design software
Fully integrated workflow with TRIOS Design Studio (3Shape), DWOS chairside (Dental Wings) and exocad ChairsideCAD*
Integrated PC with touch screen and Wi-Fi – no laptop or tablet necessary Built-in compressed air – no compressor needed
Outstanding reliability
Day and night operation 100 % engineered and manufactured in Germany 24-month warranty * Material and indication availability may vary by
CAD provider. Full range of indications and materials available in STL workflow
S5 Milling:
The S5 is a highly versatile dental milling machine. It has five simultaneously operating axes, a blank changer for eight blanks and is designed for both dry and wet machining. With the optional wet grinding module, you can grind all common types of glass ceramic. 8 Discs, 24 Blocks, 48 Abutments The second rotary axis (B axis) with a tilt angle of up to ± 30 degrees enables the precise milling of undercuts.
Thanks to the eightfold blank changer, you get performance that won’t stop. The changer can be loaded with blanks via a small flap in the front and the correct blank for your milling job is then automatically inserted into the clamping device when needed. As a result, you can mill around the clock.
The S5 can be equipped with a wet grinding module. Liquid nozzles are already mounted to the spindle to cool the tool during grinding. This module allows you to grind materials such as glass ceramics.
With the three integrated ionizers, users of the S5 considerably reduce their cleaning effort, as static charge of acrylic chips, such as PMMA, is neutralized largely. Air nozzles distribute the ionized air in the working area for excellent results.
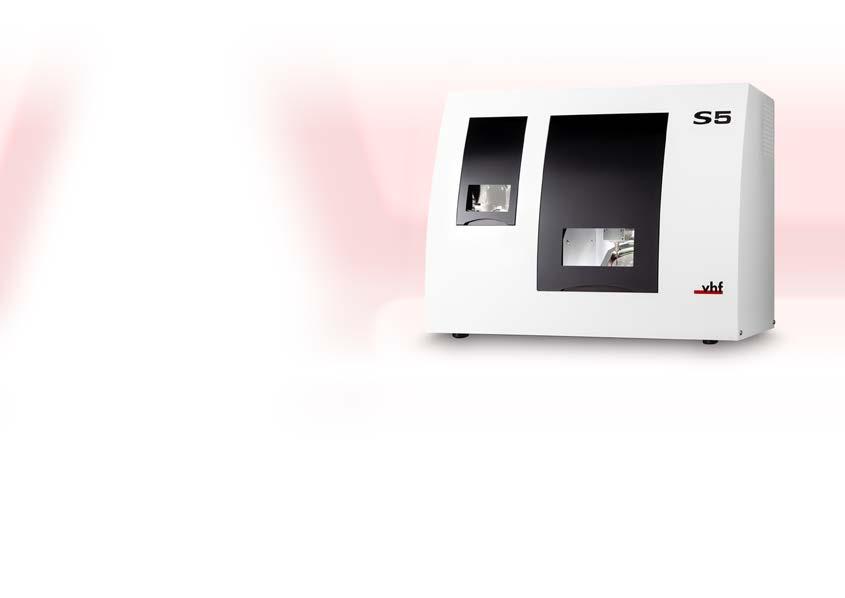
S5 Stats:
Highest precision
Restorations in ultra HD
Premium spindle with precision bearing, a powerful 600 watts and 60,000 RPM
3 microns repetition accuracy
Tremendous stability
Processes all types of materials, including CoCr, titanium, and glass-ceramics Solid cast-body for minimum vibration
Maximum efficiency
Milling and grinding around the clock due to automatic changer for 8 discs, 24 blocks or 48 prefabricated abutments Automatic changer for 16 tools 3 ionizers neutralize the static charge of acrylic chips – for a clean working chamber Very easy to operate via DentalCAM software with DirectMill function – included in scope of delivery and without license fees
Maximum variety
Almost unlimited material accessibility in 98 mm disc format as well as 38 block materials and > 800 prefabricated titanium and CoCr abutment blanks Large indication diversity due to a ± 30° rotation angle in the 5th axis, and up to 30 mm blanks Optional wet-grinding module converts the S5 into a wet-processing machine
Outstanding reliability
Day and night operation 100 % engineered and manufactured in Germany 24-month warranty
PrograMill
Click here to view more on our Youtube page
PM7
PrograMill PM7 sets new industrial standards for the digital production of restorations in the dental laboratory. The powerful performance and dynamics of this unit make it a highlight in the PrograMill portfolio. The high-power machine is capable of processing a variety of materials in wet and dry mode and is suitable for a wide spectrum of applications. The high dynamics and efficiency of the machine result in precise and fast production results. The 5-axis machining process is controlled via the integrated PC with touch screen monitor. The good cooperation of material and tool changer allows independent and consistent production. The central management of max. 8 discs / 48 IPS e.max blocks in the material changer and up to 20 tools in the magazine ensures that the right, individual processing strategy is used. The integrated ionizer reduces the cleaning time to a minimum after PMMA has been milled.
The PrograMill PM7 offers you a future-proof high-end solution for the precise and efficient production of dental restorations.
Features
• Hybrid operation: automatic change between wet and dry operation. • Integrated ionisor and automatic cleaning function. • 20-position tool changer for independent processing. • Fully automatic materials management. • Intuitive user interface for convenient operation.
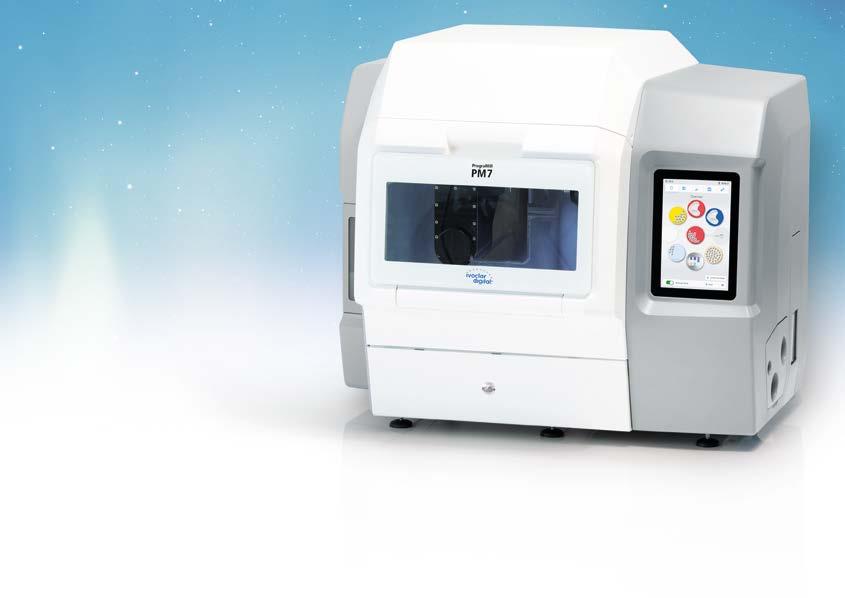
PM3 & PM5
Both machines, PrograMill PM3 and PM5, deliver ideal performance for the digital dental laboratory. These units are suitable for wet and dry processing and offer a wide range of materials and indications.
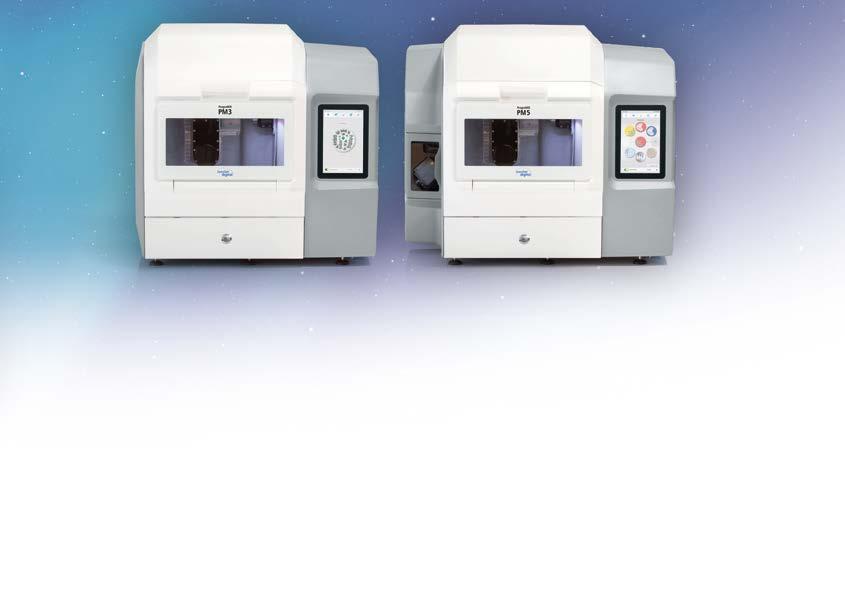
The precise 5-axis machining process is controlled via the integrated PC with touch-screen monitor. The fully automatic materials management checks whether the tools correspond with the respective machining strategy. The tool changer ensures that the production is carried outindependently and consistently. The PrograMill PM5, with its 8-way material changer, provides perfect automation for your laboratory. The material changer allows several production orders with different materials and types of restorations to be processed. Individual machining strategies are used depending on the material and the area of use. This allows short processing times for the respective restorations.
Your Benefits
• High precision and consistent results • Intuitive operation and touch-screen display • Integrated CNC PC and intelligent machine management
Features
• Tool changer for independent processing • Intuitive user interface for convenient production • Wet and dry operation for a versatile range of options
Model
Materials magazine
Block/disc processing
Automatic toll changer
Harmonic drive
Stepper motors
Servomotors
Zero-point clamping system
Spindle
Ionizer
Automatic machine calibration
Internal PC
Internal, high resolutiojn display
Weight (kg)
Dimensions (mm, WxDxH) PrograMill PM3 PrograMill PM5 PrograMill PM7
1 disc/IPS e.matrix holder 8 disc/IPS e.matrix holder 8 disc/IPS e.matrix holder
4 / 4
13 4 / 4
13 4 / 4
20
4 4 4
4
4
Jäger 390 W / 60,000 rpm
optional
4 4
4
Jäger 390 W / 60,000 rpm
optional
4 4
4
Jäger 970 W / 60,000 rpm
4
optional
4
4
195 4
215 4
220
870 x 695 x 818 979 x 695 x 818 979 x 695 x 818
6 Adapters Included Easy set-up with a snap-on clamp system
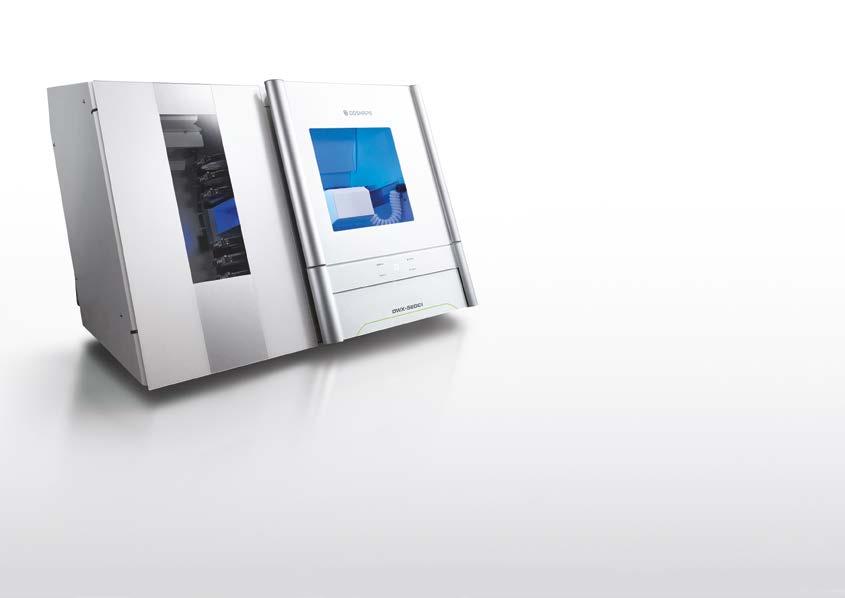
Intelligent Tool Control (ITC) Knows which tool to automatically swap out when tools have reached their designated lifespan
Ioniser
Reduce dust and static when working with PMMA
5-axis Milling
Ball screw-driven system with 5-axis positioning or simultaneous operation
Roland DWX-52DCi Dental Milling Machine
The ultimate in ease, material flexibility and unattended production, the DWX-52DCi dental milling machine expands your lab production and profit. With new DWINDEX performance monitoring software, a 6-slot Automatic Disc Changer, 15-station Automatic Tool Changer and other automated features, it gives users of all skill levels an exceptionally powerful, efficient and affordable dental restoration solution.
Automatic Tool Changer (ATC)
Load the 15-station ATC with a variety of diamond coated and carbide DGSHAPE by Roland tools to continuously mill jobs in different materials and multiple shades of zirconia without stopping production.
Intelligent Tool Control
Part of the simplified VPanel operation, an Intelligent Tool Control function automatically swaps out tools that have reached their user-defined lifespan with a designated “partner tool” without needing to pause production.
5-Axis Milling
The DWX-52DCi simultaneously rotates and tilts discs for deep undercuts and milling large arch restorations with ease.
Automatic Air Pressure Control
An automated regulator eliminates the need for manual air control adjustments by changing air volume based on material data via the CAM software.
User Replaceable Spindle
The DWX-52DCi features a spindle that can be replaced in a matter of minutes, without needing to call out an engineer. No special tools, testing or training is required.
Additional features
Virtual Machine Panel (VPanel)
A user-friendly VPanel enables easy production and device monitoring – including advanced email notification
Clean Milling Environment
Automatic cleaning brush for clean milling and an optimised structure for dust collection when connected to an extraction device
Air Pressure
Automatically changes air pressure based on the CAM material data