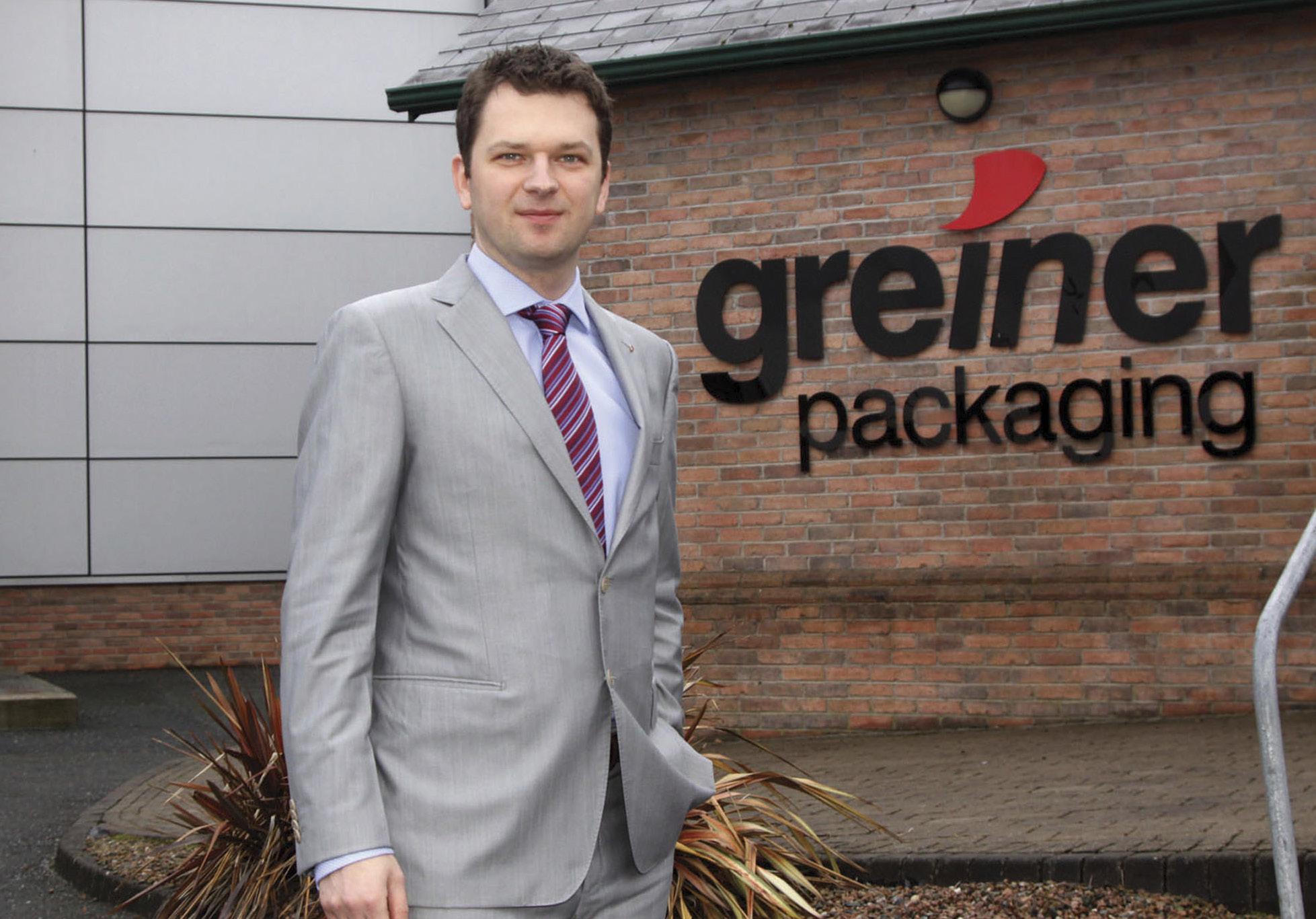
8 minute read
Greiner Packaging – Celebrating 50 Year Of Dungannon Plant
EyeonInnovation
Greiner Packaging Celebrates 50th Anniversary Of Dungannon Plant
Advertisement
Greiner Packaging UK & Ireland has celebrated its 50th anniversary in Dungannon, Co Tyrone with a visit from the Austrian parent company’s senior management as well as local representatives and investors.
Director of operations at Greiner Packaging International, Jarek Zasadzinski.
The original plant was established 50 years ago as Wilsanco Plastics before the local company was acquired by Greiner Holdings AG in 2006. The company manufactures some of the world’s most sustainable packaging for food and non-food applications and employs some 300 people.
Its end products are in almost every households – in the form of yoghurt pots, convenience food containers, even the familiar purple tubs used to hold Cadbury’s Roses at Christmas.
At the 50th anniversary event, the company announced new investments totalling over £10 million, for the installation of new bespoke machinery, the commissioning of a new manufacturing hall, and the expansion of the warehouse from 3,000 to 11,000 spaces.
“For fifty years, we have produced some of the world’s most sustainable packaging for food and non-food applications at our factory in Dungannon,” says director of operations at Greiner Packaging International, Jarek Zasadzinski.
“As we celebrate this important anniversary, we are proud to announce these new investments which follow the more than £35 million we have invested since acquiring Wilsanco in 2006.
“Sixteen years ago, the site was turning over £15 million and today we are achieving £60 million. Our goal is to grow this site to £100 million over the next five to seven years.
“These investments, by Greiner Packaging International, were partly funded by Invest NI, UK government, and EU regional development funds, and have contributed to building a highly successful and sustainable manufacturing business which services hundreds of customers across the UK and Ireland.
“We are so proud of our achievements, of our loyal and committed workforce, and to be celebrating 50 sustainable years in Dungannon in 2022.”
To mark the 50 years, five trees were planted, one for each decade.
Born in Poland, Jarek Zasadzinski joined Greiner Holding AG in 2004 and took a leading role in the acquisition of Wilsanco in 2006.
In 2008, he became the youngest CEO in the history of the Greiner
EyeonInnovation
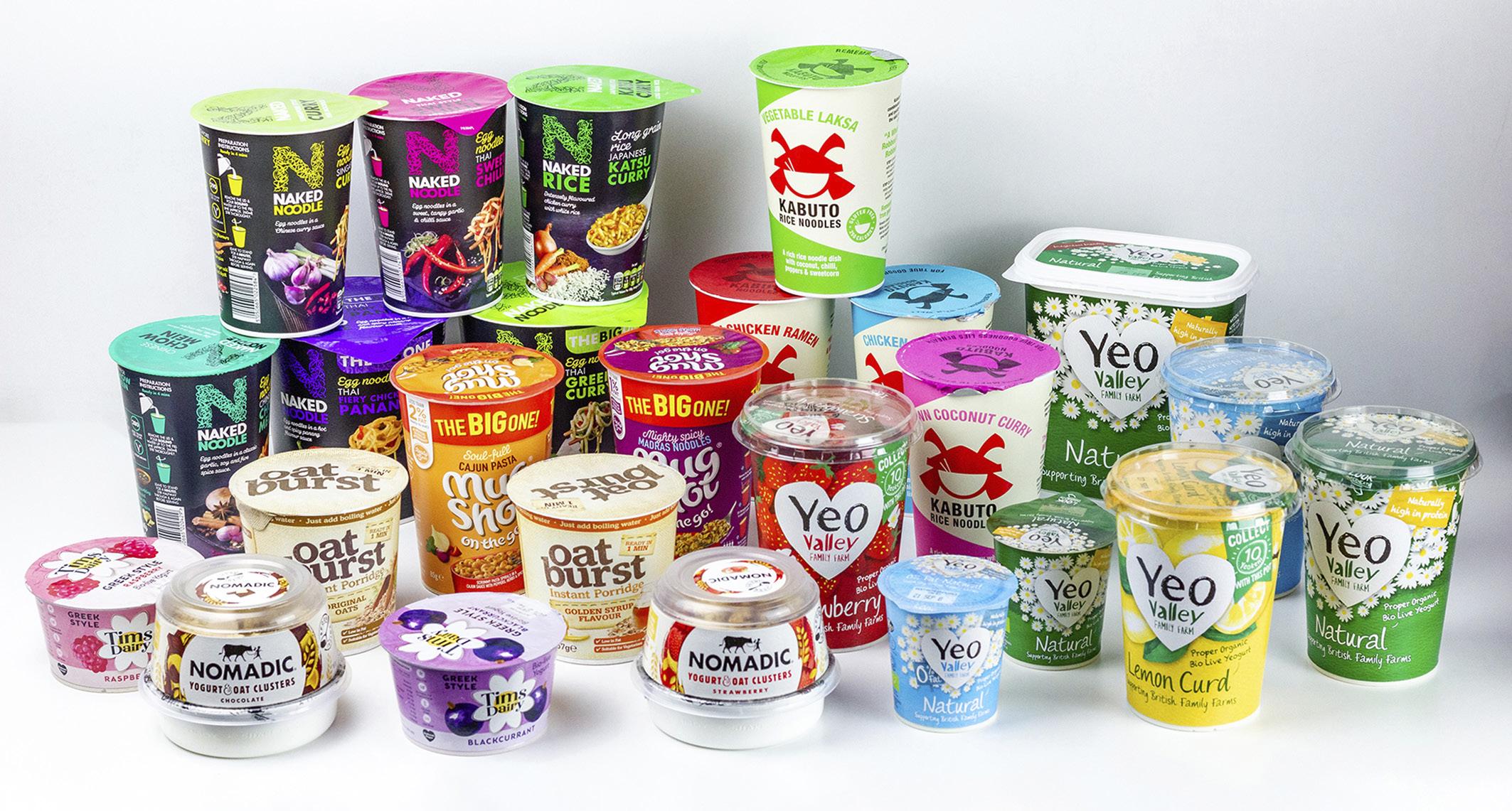
Group. He led Greiner Packaging UK and Ireland into the league table of the 100 most profitable firms in Northern Ireland, doubling the company size to over £30 million, and achieved five major industry awards for the innovative projects introduced in the factory.
In 2013, he won the Young Business Personality of the Year Award at the UTV BusinessEye Awards; and in 2015, he won Aer Lingus Viscount Awards Business Person of the Year, accepting the award at the House of Commons, Westminster as the first Polishborn business leader to win.
The company recently invested over £3.7 million in a new PET decontamination and extrusion line to enable the use of more recycled materials in its marketleading packaging ranges.
This is the latest step in Greiner Packaging UK and Ireland’s continued commitment to innovate, increase capacity and reduce its carbon footprint.
The European Food Safety Authority has now approved the decontamination process to recycle post-consumer PET into food contact materials.
Globally, Greiner Packaging employs a workforce of over 4,900 people at more than 30 locations in 19 countries around the world. In 2021, the company generated annual sales revenues of €772 million (including joint ventures), which represents almost 35 per cent of Greiner’s total sales.
“There have been a lot of firsts for this factory and for this company,” says Jarek Zasadzinski. “It has led the way in the production of plastic packaging for the off industry over quite a number of years.
“The previous owners, with the support of the government, invested more than £20 million in the Dungannon plant.
“Since Greiner took over, turnover has quadrupled and there has been a lot more investment in the site. Back in 2007, we built a new state of the art warehouse and we’re about to triple its size in the coming years. More recently, we’ve invested in
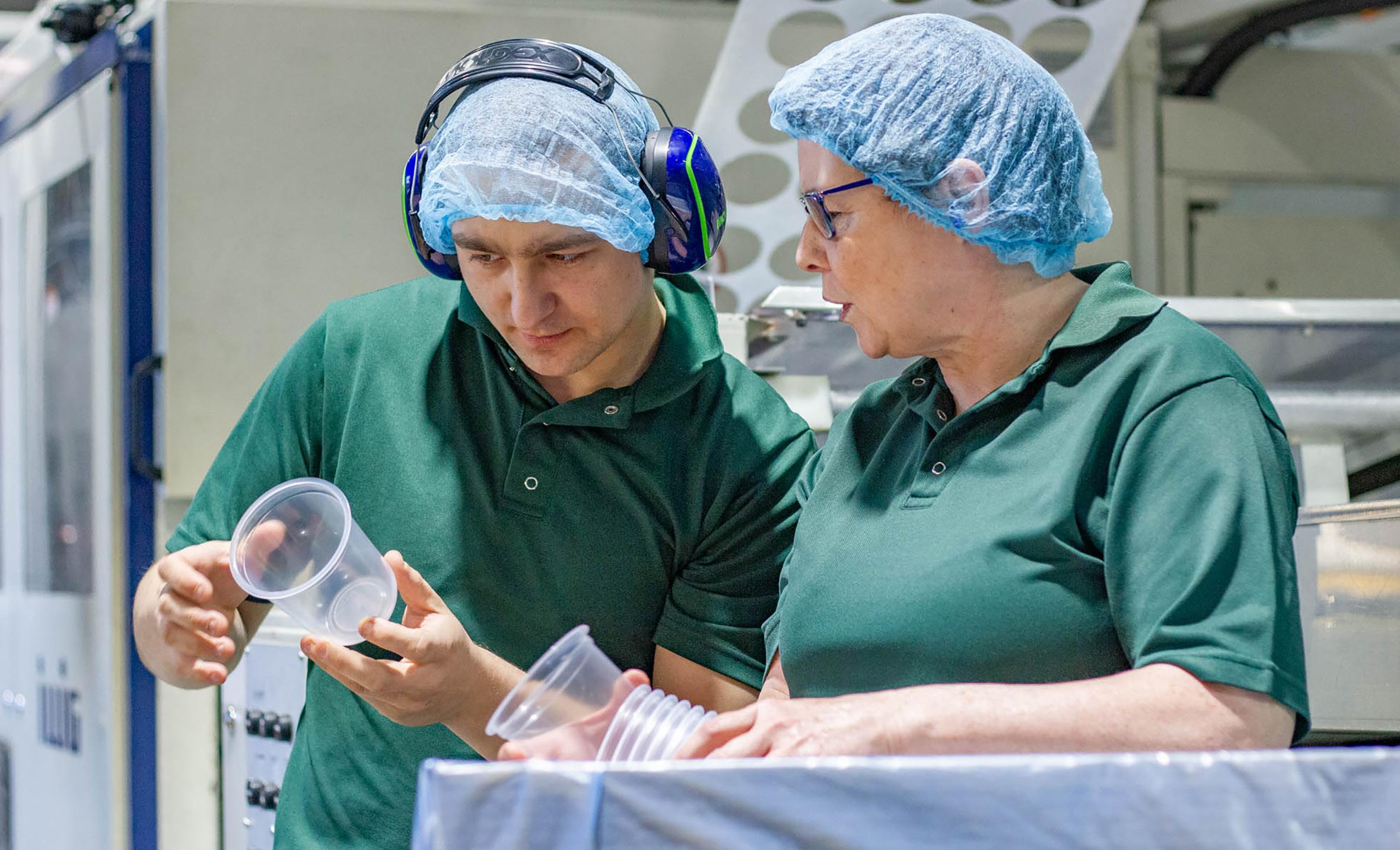
EyeonInnovation
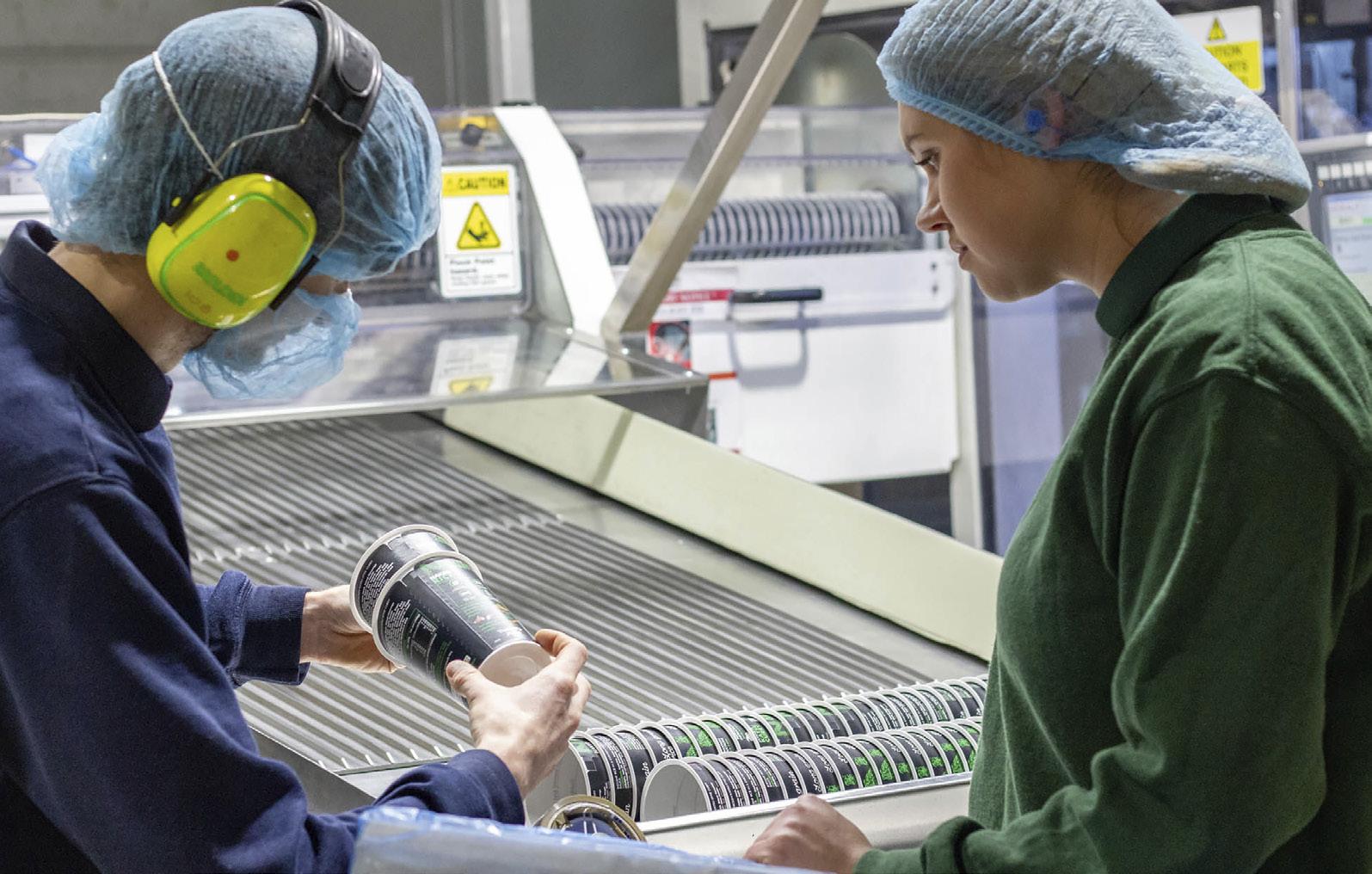
technology enabling us to produce combined plastic and cardboard packaging. The new investment that we’ve just announced is for the latest generation of the same technology.”
A circular economy strategy lies at the heart of Greiner’s operations in Dungannon, as well as globally. The new combined plastic and cardboard products aren’t just 100% recyclable. They also self separate during the sorting process.
“Another key investment has been in technology that enables us to re-use recycled PET. It’s a really exciting development, a UK first, allowing us to put recycled plastic flakes in at one end and produce finished packaging pots at the other. Closing the loop in a very real sense.”
The current tax legislation around sustainability means that packaging must contain at least 30% of post consumer waste, otherwise it attracts higher tax rates. “Here at Greiner, our aim is that 100% of our packaging is recyclable and 100% of our packaging contains at least 30% of post consumer waste. We’re well on the way to getting there.
“The whole business model changes to meet sustainability targets,” Jarek explains. “We work closely with the UK recyclers who supply us with post consumer waste material. At a global level, we recently purchased one of Europe’s latest recycling companies based in Serbia. In addition, we have certain types of of our own packaging coming back to us post-use.”
Post-Brexit, the Dungannon plant became more important as far as UK customers are concerned. “They need security of supply, so we see it as a big opportunity, and our goal is to grow from our current £60 million turnover to £100 million.”
“It’s much more cost effective now for our UK customers to source their packaging from within the UK,” says Greiner’s Sales & Marketing Director, Julie Eller, who works directly with those customers all over the country. “It also takes away the risks of currency fluctuations.
“Traditionally, almost 80% of our products went to the diary sector, including all of the big names and lots of local dairy producers,” says Julie. “In the last few years, there has been a push to diversify out of dairy and into different markets. We’ve been very successful. We now lead the market in instant snacking – soup, porridge, noodles, etc – and we also have some confectionery sales, including the big purple tub.
“From the Dungannon plant, about 80% of output goes to GB customers with 20% staying on the island of Ireland. It’s a stable business to be in. Even during Covid, demand increased as more people bought and consumed products at home.”
The company works across the board on improving its carbon footprint. One example is a move alongside transport partners to ensure that the firm’s products are transported to customers using bio fuels.
Jarek Zasadzinski pays tribute to a loyal and hard-working team at the plant in Dungannon. Staff retention, he says, is important because Greiner’s operations require a number of specialist skills.
“The biggest challenge for us now is around energy costs. Clearly, we’re a big energy user so rising costs are a major concern for us. Political uncertainty, meanwhile, isn’t helpful to anyone.
Looking forward, both Julie Eller and Jarek Zsadzinski say the Greiner’s UK plant in Dungannon will continue to innovate and continue to diversify. “We’ll also continue to work towards our recycled product targets, although that has its own challenges,” says Julie. “Recycled material has gone up in price, and cost is still king as far as our customers are concerned.”
“This company and our industry is all about circularity,” says Jarek. “We’re already doing things differently and we’ll continue with our focus on that innovation. We all have to change our behaviours, ourselves included.”
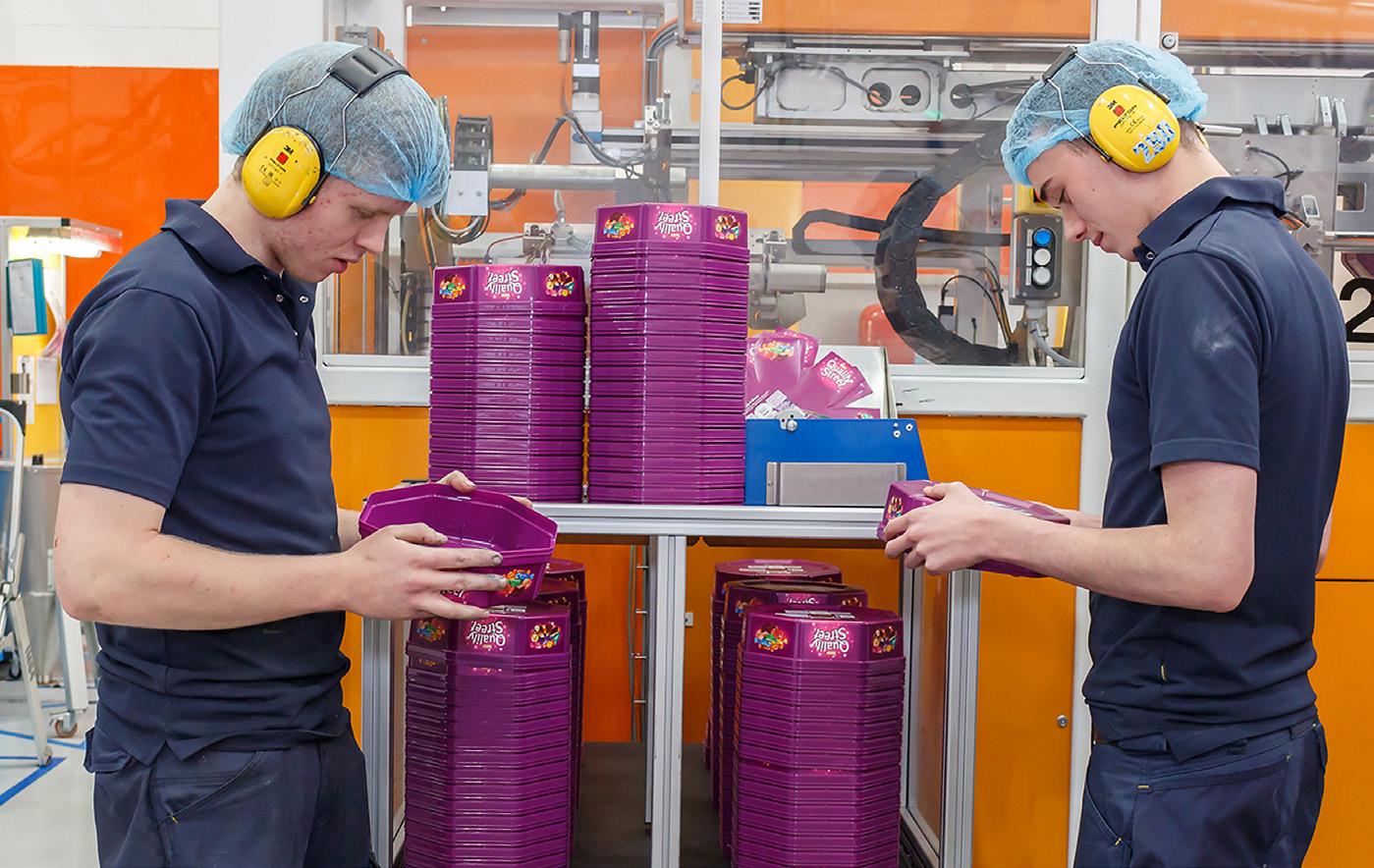
EyeonEvents
Muldoon & Company unveils new office expansion
As Belfast-based accountancy practice Muldoon & Company approaches its 30th anniversary it has officially opened its newly expanded offices in the Queen’s Quarter in Belfast.
Led by partners Sean Muldoon, Robbie Barr and Raymond Tiffney, the practice has grown to a team of over 40 accounting, tax, audit and advisory professionals.
To accommodate the growth of the business, Muldoon & Company has increased its office space by another 2,500 square feet, adding 20 Mount Charles to its existing offices at number 16 and number 18.
The latest expansion has seen the company refurbish its offices and add several new features designed to enhance the client and employee experience. A café style break-out area has been added along with showers, a gym, a new boardroom and private parking for clients.
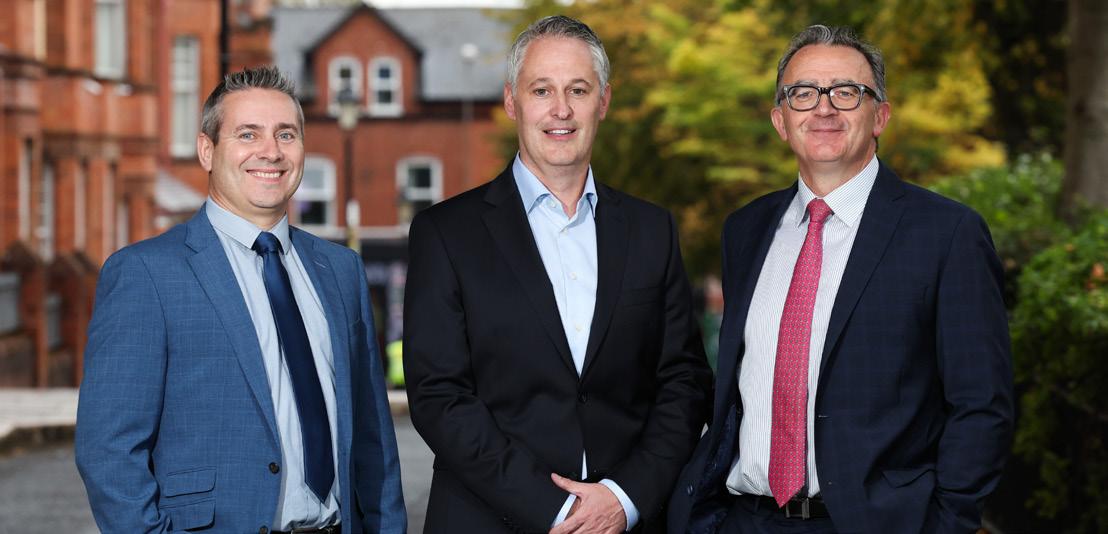
Pictured marking the opening of their newly expanded offices are Muldoon & Co partners Robbie Barr, Raymond Tiffney and Sean Muldoon.

Muldoon & Company has officially opened its newly expanded offices Brian Conway, Sarah Andrews and Conor Walsh
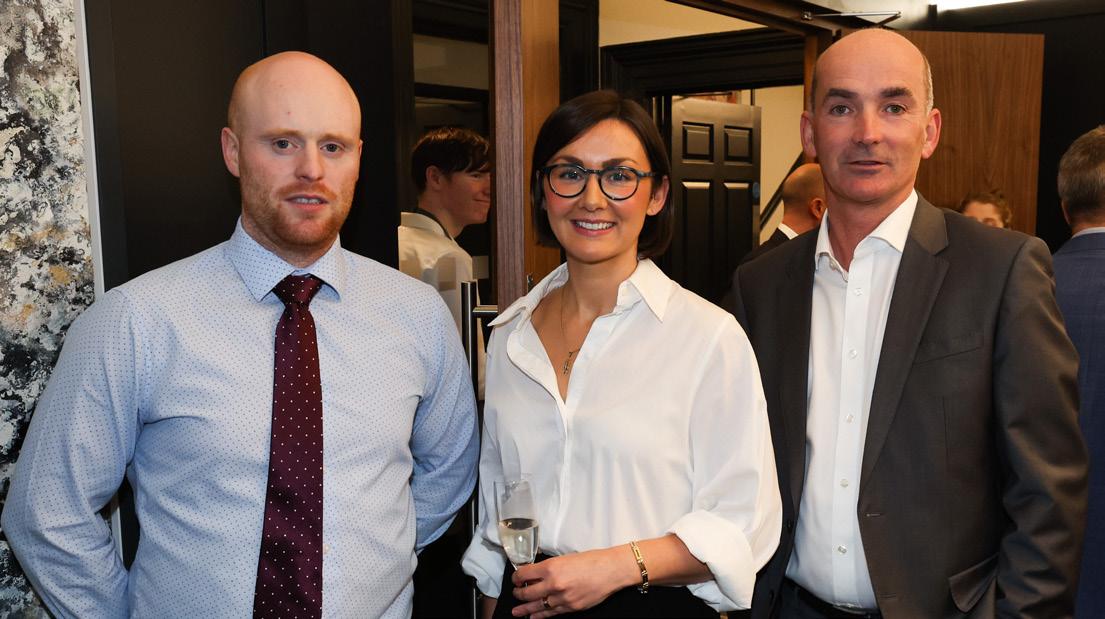
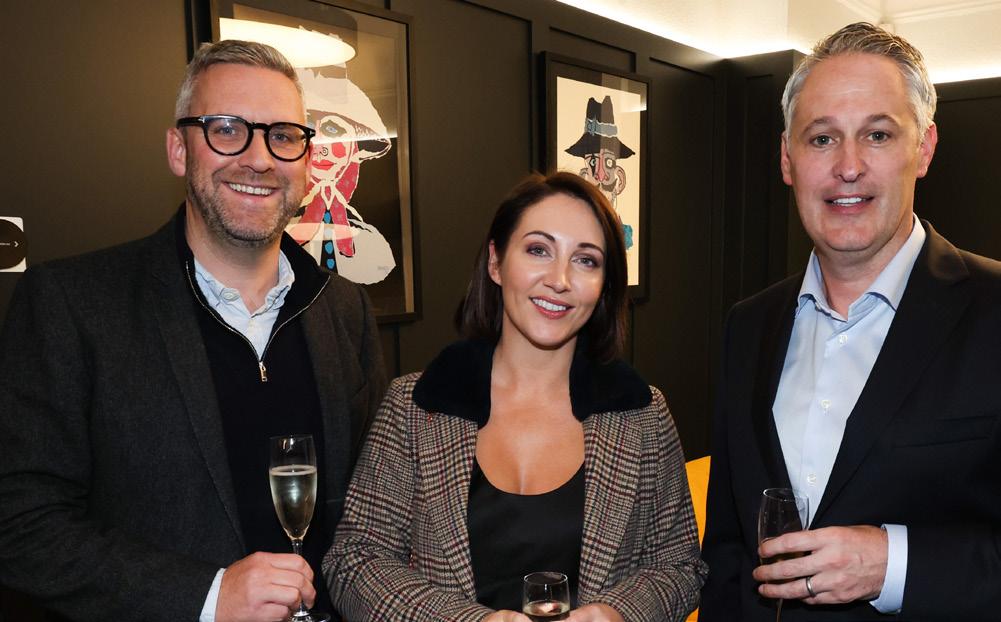
David McCurley, Sarah Orange and Raymond Tiffney Theresa Nixon and Robbie Barr Sam Baird and Paul McGuire
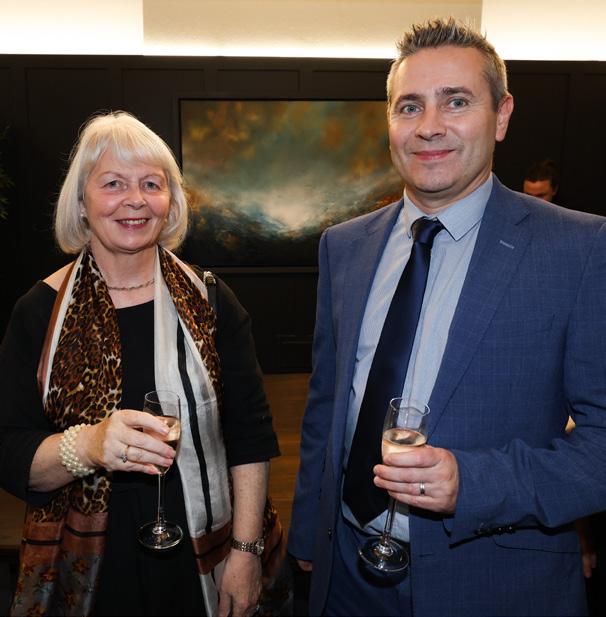

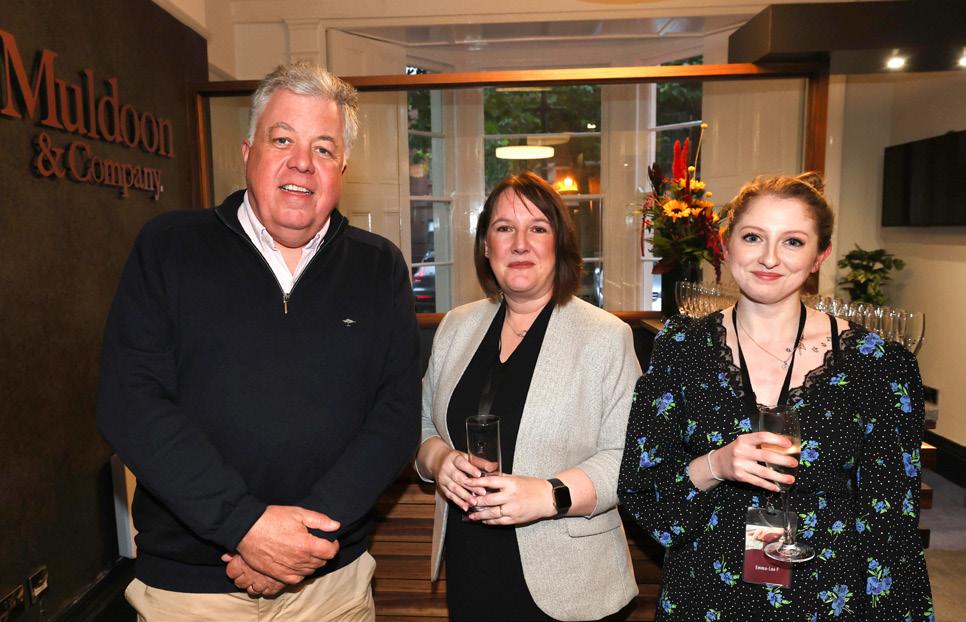
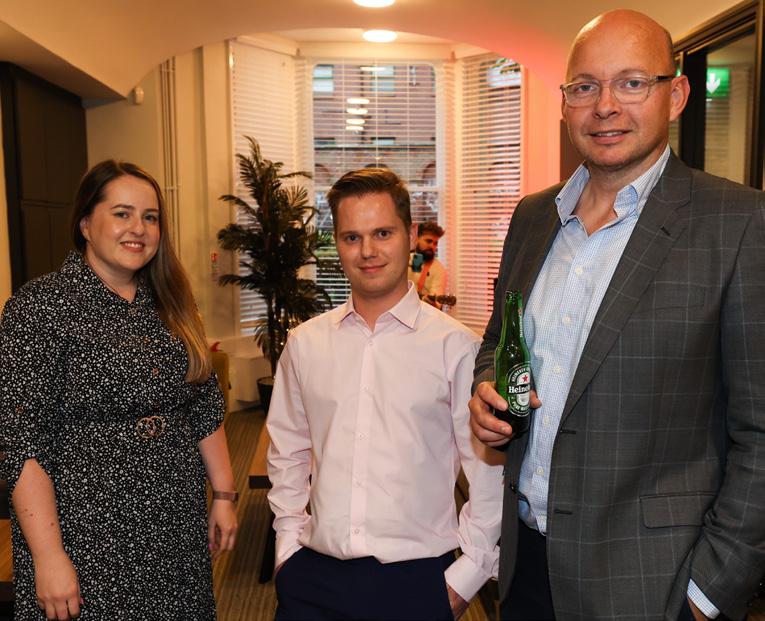