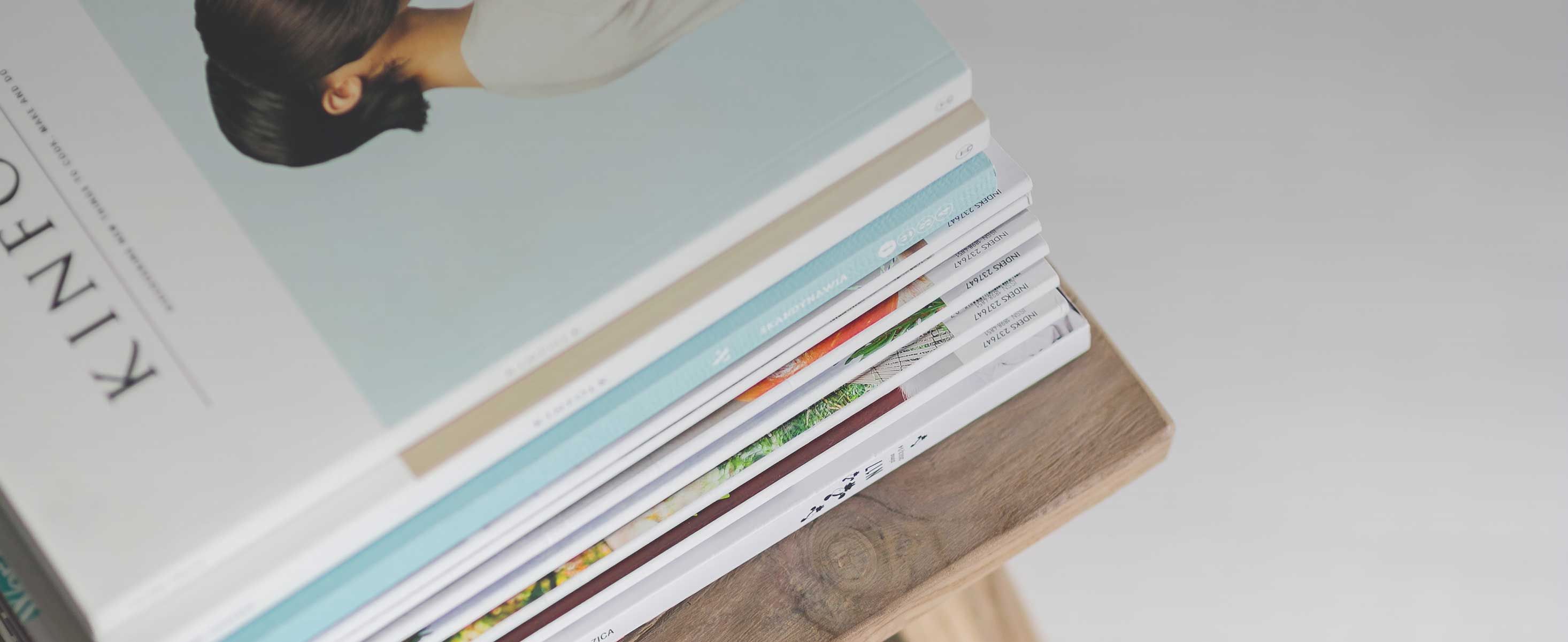
3 minute read
Series DC Motors
• Brushless • Universal
The last three motor types are just variations of the first three, fabricated with different construction techniques. The compound motor is a combination of the series and shunt motors. For the first three motor types we’ll look at the circuit showing how the motor circuit field windings are connected, and then look at the characteristics of the torque and speed versus armature current and shaft horsepower curves that describe their operation (Figure 6-3).
Each of the motor types will be examined for its torque, speed, reversal, and regenerative braking capabilities—the factors important to EV users. The motor types will all be compared at full load shaft horsepower—the only way to compare different motor types of equal rating. Efficiency is a little harder to determine since it also depends on the external resistance of the circuit to which the motor is connected. So efficiency has to be calculated for each individual case.
Series DC Motors
The most well-known of the DC motors, and the one which comes to mind for traction applications (like propelling EVs), is the series DC motor. It’s so named because its field winding is connected in series with the armature (Figure 6-3). Because the same current
Figure 6-3 Summary of DC motor types—windings and characteristics.
must flow through this field winding as through the motor armature itself, it is wound with a few turns of heavy gauge wire.
Torque
As equation (5) showed, Torque 5 K 3 f 3 I a, and the current in the series field is Ia . I a can be substituted for f and the series motor torque equation can be written as
Torque 5 K' 3 I a
2
This shows that in a series motor, torque varies with the square of the current—a fact substantiated by Figure 6-3’s actual torque versus armature current graph. The graph is actually a little misleading because at startup there is no counter electromotive force (EMF) to impede the flow of current in the armature of a series motor, and startup torque can be enormous; with no current limiting, you can start up at torque values far to the right of the full load line for a series motor. In actual use, the armature reaction and magnetic saturation of the series motor at high currents sets upper limits on both torque and current, although you might prefer to limit your circuit and components to far lower values. High starting torque makes series motors highly desirable for traction applications.
Speed
As the following equation shows, Speed 5 (Vt – I a R a)/K4)
Once again, I a can be substituted for f, and the series motor speed equation can be rewritten as
Speed 5 (Vt – l a(Ra + Rf))/Kla where R a and Rf are the resistances of the armature and field, respectively. This shows that speed becomes very large as the current becomes small in a series motor—a fact substantiated by Figure 6-3’s actual speed versus armature current graph. High rpms at no load is the series motor’s Achilles heel. You need to make sure you are always in gear, have the clutch in, have a load attached, etc., because the series motor’s tendency is to run away at no load. Just be aware of this and back off immediately if you hear a series motor rev up too fast.
Field Weakening
This technique is an interesting way to control series motor speed. You place an external resistor in parallel with the series motor field winding, in effect diverting part of its current through the resistor. Keep it to 50 percent or less of the total current (resistor values equal to or greater than 1.5 times the motor’s field resistance). The byproduct is a speed increase of 20 to 25 percent at moderate torques without any instability in operation (hunting in rpm, etc.). Used in moderation, it’s like getting something for nothing.
Frank G. Willey, a member of the EAA, created the first pulse width modulated motor speed controller using silicon power transistors. He was recognized by the IEEE in the early 1980s for doing so.
Offered in kit form or completely assembled and tested, the Model 9 had ratings of 450 amps for traction pack voltages from 24 to 120 volts. Today, most motor controllers