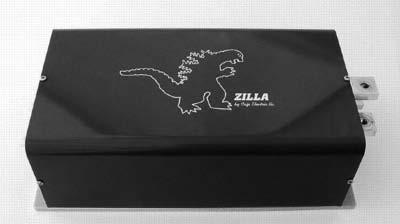
5 minute read
Today’s Best Controller Solution Zilla Controller (One of the Best DC Controller for Conversions)
Figure 7-4 AC controller design objectives and block diagram.
Unfortunately, since most of our names are not Tesla or Steinmetz, all this additional complexity means a lot more sleepless nights in the garage for even the most enthusiastic build-it-yourselfers, and is the real reason why three-phase AC induction motors— despite their enormous advantages—will probably not reach the do-it-yourself EV converter. Meanwhile, let’s look at the best solution for your EV conversion project of today.
Today’s Best Controller Solution
If you’ve previously read Chapter 6 on motors, you already know this book recommends a series DC motor as the best motor solution for today’s EV converters. This greatly simplifies our choice of motor controllers—we only have to choose from those in the DC motor universe. But there are still numerous DC controller vendors and models to
choose from, and you have to figure out which one to use. The same words of advice apply in the controller area as in the motor area: If someone tells you there is only one controller solution for a given application, ask another person. Like motors, you can probably find three or four good controllers for any application because there are only shades-of-gray controller solutions. And, as with the recommended motor, the controller recommended here is not the solution, it is just a solution that happened to work best in this case.
While the series DC motor and PWM controller are unquestionably best for today’s first-time EV converters, the bias of this book is toward AC controllers and motors. However, one of the best EV technologies today is a DC controller. On one side, AC induction motors are inherently more efficient, more rugged, and less expensive than their DC counterparts. This translates to more driving range from a given set of batteries, and less probable failures and the possibility of graceful degradation when one does happen, but not less expense! The package isn’t cheap and the motor alone isn’t either. These benefits come at a price. That’s why nearly every newly designed commercial EV today utilizes one or more AC induction motors or its closely related cousin, the brushless DC motor.
No new electric car uses DC drive. However, some of the greater conversions out there use DC controllers. DC is cheap and very suitable for a budget conversion. Again, for a conversion that is less expensive, a DC motor works.
What’s in the labs today will be available to you in the not-too-distant future and, beyond that, continued improvements in solid-state AC controller technology could put AC motors in every EV conversion of the future. Let’s look at developments in two areas—systems and components—that virtually guarantee this outcome.
Now, let’s look at the future—today!
Zilla Controller (One of the Best DC Controller for Conversions)
The Zilla controller (Zilla), shown in Figure 7-5, is by far one of the most popular and powerful motor controllers available for electric vehicles. The Zilla has exceptionally high power density. According to the conversion specialists and people in the EV community today, the Zilla is ranked as one of the best controllers out there on the market. This controller can make your EV have the most amazing pickup and torque like no other on the market (or even on your block).
We like that Zilla cared about safety in their literature because it shows that a reasonably priced, efficient, and off-the-shelf controller can still be safe. From carefully monitoring that the controller comes up to voltage, communicates properly, and checks the integrity of the output stage before engaging the main contractor, to the dual microprocessors that cross-check and have independent means of shutting the system off, there is no other DC EV controller that approaches this level of security.
It is no surprise that all of the world’s quickest electric vehicles use Zilla controllers, but the safety features allow them to also excel in street applications. The Z1K in particular has become very popular for street conversions due to its superior feature set and low price. Table 7-1 shows the specifications of this popular controller.
Zilla Models
The Zilla comes in two current ratings and up to three voltage ratings:
Figure 7-5 Zilla Controller Model Z2K-HV (Cour tesy of Café Electric, LLC).
• The Z1K-LV is the lowest cost unit. While it regulates up to 1,000 amps of motor current to run on lead-acid battery packs of 72 to 156 volts, this unit is more than twice as powerful as the common type of controllers for most “normal” car conversions. Because Café Electric wants people to convert cars to have affordable options, they use “the sales of higher voltage controllers to partially subsidize production of the Z1K-LV units.” This keeps the amount of these units delayed for a reason. • The Z1K-HV can regulate up to 1,000 amps of motor current and run on leadacid battery packs of 72 to 300 volts nominal. This unit in a typical car with a shifting transmission and a powerful battery pack of at least 200 volts will result
Maximum nominal input voltage range for Lead-Acid batteries: 72 to 348 volts Absolute maximum fully loaded input voltage range: 36 to 400 volt s* Maximum motor current at 50°C heat sink temperature: 2000 Amps for Z2K, 1000 Amps for Z1K Maximum Battery Current at 200V: 1900 Amps for Z2K, 950 Amps for Z1K Maximum Battery Current at 300V: 1770 Amps for Z2K, 885 Amps for Z1K Maximum Battery Current at 400V: 1600 Amps for Z2K, 800 Amps for Z1K Continuous motor current @ 50°C coolant temp and 100% Duty Cycle: o ver 600 Amps for Z2K, 300 Amps for Z1K Peak Power: 640,000 Watts for Z2K, 320,000 Watts for Z1K PWM frequency 15.7 kHz Power devices IGBT Voltage Drop: <1.9 volts at maximum current.
* At this time we are suggesting not exceeding 375 volts on the EHV models; we hope to bring that back up to 400 volts with further testing.
Table 7-1 Zilla Specifications