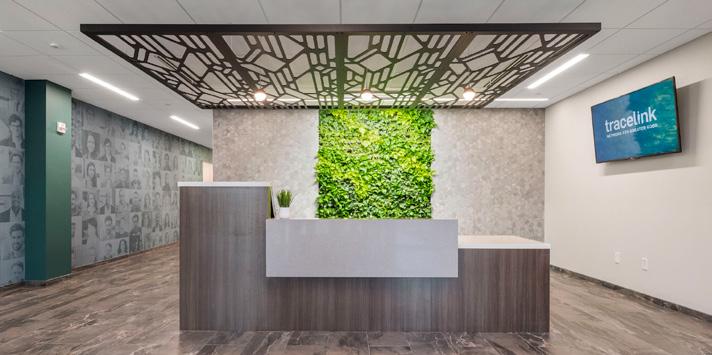
6 minute read
Corporate
Ebbrell Designs TraceLink Corporate Headquarters
Wilmington, MA – Ebbrell Architecture + Design announced it designed supply chain software company TraceLink’s new 70,000sf global corporate headquarters in Wilmington, which opened in the spring. VBA Construction Management was the builder on the project.
TraceLink began designing its new headquarters in December 2020, which the company’s representatives said was a challenging endeavor mid-pandemic, in needing to anticipate the unknowns of the future of the workplace while addressing the company’s need to relocate. The design team at Ebbrell, led by interior designer Jessica Cargile, NDICQ, LEED AP, said they knew that TraceLink wanted a fexible/hybrid workspace that could accommodate 65-70% of its workforce at once.
“They didn’t want a sea of workstations,” said Cargile. “By creating fve pods that each included breakout spaces, private telephone rooms, conference and copy areas, and a kitchen, each team has its own area, but no one feels left out or like they don’t have the same amenities as another group because it’s all equal, while still providing variety throughout the space.”
Miika Ebbrell, AIA, LEED AP, founder and principal of Ebbrell Architecture + Design, said, “Our goal was to foster employee engagement with
Trace ink corporate lobb design, and we accomplished that by creating fexible spaces that accommodate all work preferences.”
Phil Putnam, director, global, facilities & real estate at TraceLink, said the successful design includes important aspects to help employees, when in the offce, be comfortable, while still
continued to page 37
Create an experience that makes guests feel comfortable and keeps them coming back for more with open and future-ready solutions. Let AEM & CTC design a custom solution just right for you!
200 Friberg Parkway, Suite 1004 Westborough, MA 01581 508-480-8200 aemsolutions.com
500 Corporate Row Cromwell, CT 06416 800-890-2022 cttempcontrols.com
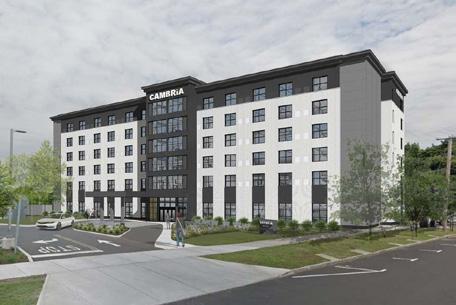
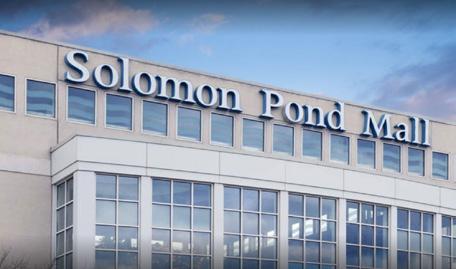
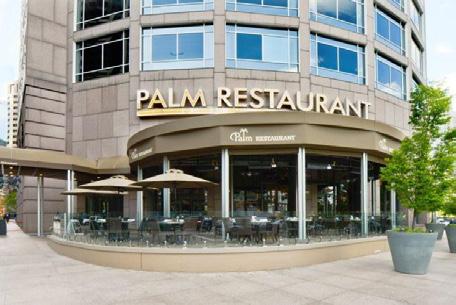
JME Opens Innovation Center in Woburn

lectrical o pan staff
Woburn, MA – As part of its ongoing expansion strategy, M Electrical Company, Inc. (JME) unveiled the new JME Innovation Center on June 30 in Woburn.
The center includes 10,000sf of workshop and storage space, an additional 5,000sf of dedicated training and offce space, and a conference room where clients and JME colleagues can meet and collaborate. The building, a former machine shop, has been completely overhauled and now features many energysaving systems, from LED lighting with occupancy sensors to insulated roofng.
This new facility was designed to house all offsite prefabrication projects, from the production of wiring assemblies to full panel prefabrication. Managed by a full-time team, the JME Innovation Center will help streamline projects,

l r ohn Guarracino principal and atthew Guarracino a or cott Gal in of Woburn da al er and ndrew Guarracino pro ect anager
minimize work on job sites, and introduce greater effciencies. The new building, which is easily accessible from Routes 93 and 95, offers 24-hour drop-off and pickup for deliveries.
JME leadership believes that as much as 50% of all projects will beneft
NE Firm Expands to Texas
from the services provided at this new facility. “We believe this new venture will increase productivity by creating greater effciencies, abbreviating project timelines, and allowing for work schedules that accommodate the changing needs of our employees, all in a safe, controlled environment,” said Matthew Guarracino, principal and CEO at ME. “Equally important, prefabrication and modular construction offer many green’ benefts, including the ability to recycle materials more easily while also eliminating waste.”
“With an emphasis on precise advanced planning, prefabrication is both innovative and economical, allowing for greater consistency and uniformity,” said Adam Palmer, director of operations and project executive at ME. “Our commitment to the prefabrication process will allow us to assemble countless components offsite – from Terminal Box Controllers to Full DDC Panels – and deliver completed units to the job site for installation. This will expedite project timelines by allowing us to work simultaneously on-site and at our facility.”
In addition to offering new services, the company will be adding staff to meet growing demand from commercial contractors. The new facility will allow ME to hire additional staff, expand its apprenticeship program, and give students real-world experience.
Boston – NEI General Contracting announced the opening of a new offce in the Houston area to support its Southwest operations. Led by project executive, Mike Myers, the offce is located at 13360 S. Gessner Road in Missouri City, Texas.
“As part of our continued growth, we are excited to open our new offce in the Houston area, where we will continue to offer general contracting services, specializing in affordable housing with extensive experience in ground-up, moderate rehab, elderly, veteran, historic rehab, historic tax credit and tax credit projects,” said Joe Rettman, president of NEI. “In addition, we are proud to have Mike Myers leading this new venture. We are confdent in Mike’s proven leadership ability coupled with his keen business sense and industry insight to competitively position NEI to drive our growth across the Southwest.”
The Texas offce features an expert team of professionals that serve clients across the Southwest U.S. by delivering high quality service in the affordable housing market. NEI’s Southwest portfolio includes two senior living facility rehabs including Elevation Financial Group’s 170-unit Serenity at Dallas, and the
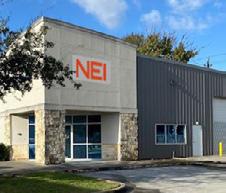
I General ontracting’s Te as offce
180-unit Serenity at Briarcrest located in Bryan, Texas. Between the two projects, NEI worked closely with the client from conception to completion, developing creative solutions to the challenges presented with converting assisted-living environments into independent senior living communities.
NEI is currently hiring project superintendents, project admins, project managers, and estimators. NEI prioritizes equity and inclusion with initiatives that are designed to engage and maximize the participation of diverse local contractors and community-based workforce on all of its construction projects.
Performance/Payment Bonds: Owner’s Concerns
continued from page 20
subcontractor “if it sought recourse for the default from Arch.”
The Massachusetts court stated:
“We acknowledge the diffculty contractors may face in navigating between the risk of premature termination of a subcontractor and the risk of failing to comply with the requirements of Section 3 of the A312 Performance Bond.”
And further that,
“Pursuant to the unambiguous language of the performance bond, any obligation of Arch to provide the window warranty was condition on Graphic’s termination of RCM, an action Graphic chose not to take.”
And further that,
“The performance bond required Graphics to terminate RCM to trigger Arch’s obligation to provide a window warranty…”
Conclusion
Utilization of the A312 has a burdensome responsibility of an owner pursuing a surety in relation to a general contractor or CM’s bond or a general contractor or CM’s pursuit of a subcontractor in relation to the AIA A312 bond. To effectuate coverage under the AIA A312, it is clear from the cases that the owner or contractor must declare that the general or subcontractor is in default and terminates the contractor or subcontractor as the case may be and agrees to pay the balance of the contract price and to the surety in accordance with the terms of the contract.
Termination of a contractor or subcontractor is fraught with risks in that there must be “justifable termination,” a fact-fnding issue to be determined by a court or arbitrator.
Thus, it is this author’s opinion that the A312 should not be utilized by an owner either as a public entity or private entity and that a simple statutory or simple surety bond without the three-step process as noted in the AIA A312 be utilized.
Girard isconti s is partner at a age aw artners