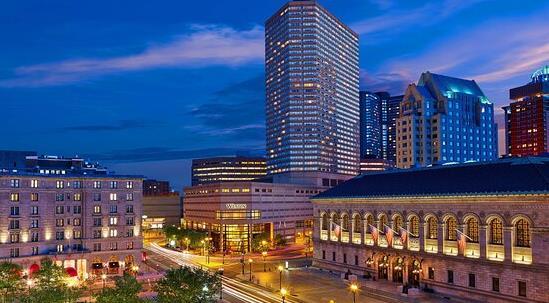
2 minute read
Focus: Restoration and Renovation Repositioning Office to Lab: A Winning Formula
to handle the additional loads imposed by laboratory facilities.
By Caitlin D. Greenwood
Boston’s Fenway neighborhood has become an “eds and meds” neighborhood and a hub for life science companies. This is due largely to the presence of nine colleges and universities and proximity to the adjacent Longwood Medical and Academic Area, home to 21 medical and academic institutions.
Margulies Perruzzi was retained to retroft 20 Overland Street in Boston, transforming it from Class B offce space into a highly desirable location for a variety of life science tenants. Repositioning the 202,167sf building for a new and more demanding use required upgrades to its infrastructure to enable demolition of the adjacent building, core and shell upgrades to the frst and second foors, and most signifcantly, a combination of upgrades to and replacement of existing mechanical, electrical, and plumbing systems (MEP)
The building had been a vehicle manufacturing plant during World War II, and consequently has substantial foor-to-foor heights, ample fenestration for natural light, and plenty of structural capacity. While benefcial, the latter added a level of diffculty when it came to accommodating penetrations for plumbing. The former factory was also equipped with two large freight elevators, which became irrelevant when the building use changed. The design team repurposed one of the shafts as thoroughfares for routing new chilled water, HVAC exhaust ductwork, and generator conduit runs from the frst foor and second foors to the roof instead of running these utilities down the side of the building, which is a more common solution.
Based on the structural capacity of 20 Overland, the roof did not need reinforcement for the additional new HVAC equipment, which included supplemental condensing units for cooling and lab exhaust fans. Dunnage, a structural platform for mechanical equipment, was added to support a new lab emergency power generator. Due to seismic design constraints, diesel fuel to power the generator could not be stored on the roof and instead is stored in a specially-design tank room located in the basement.
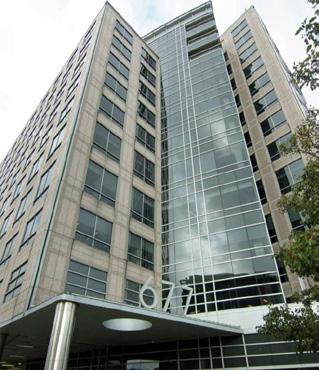
Upgrades were also made to the lobbies and entrances at both the Overland and Burlington Street entrances to entice more foot traffc in front of the building and to connect with future public circulation. The improvements have already attracted new tenants: Margulies Perruzzi recently completed a 60,000sf interior ft-out for Strand Therapeutics.
Not every building is suitable for conversion to labs. In this case, strategic discussions with the landlord took place before and during the design process regarding future fexibility, building and fre separations between 20 Overland and 109 Brookline, limitations on lab control areas, maximizing available space for lab use, and implementing renovations while minimizing disruption to existing tenants.
Owners thinking about making a similar investment must consider the prospective building’s adaptability to the new use. Zoning, local codes and ordinances, building location, and site amenities such as ease of circulation, access to public transportation, and available parking are all important factors. From a physical standpoint, buildings that have generous foorto-foor heights, structural integrity, presence of essential utilities, capacity for enhanced utilities, fexibility to appeal to different types of tenants, and availability of frst foor space for chemical storage, are prime candidates for repositioning.
Caitlin D. Greenwood, AIA is a partner and project manager with Margulies Perruzzi.