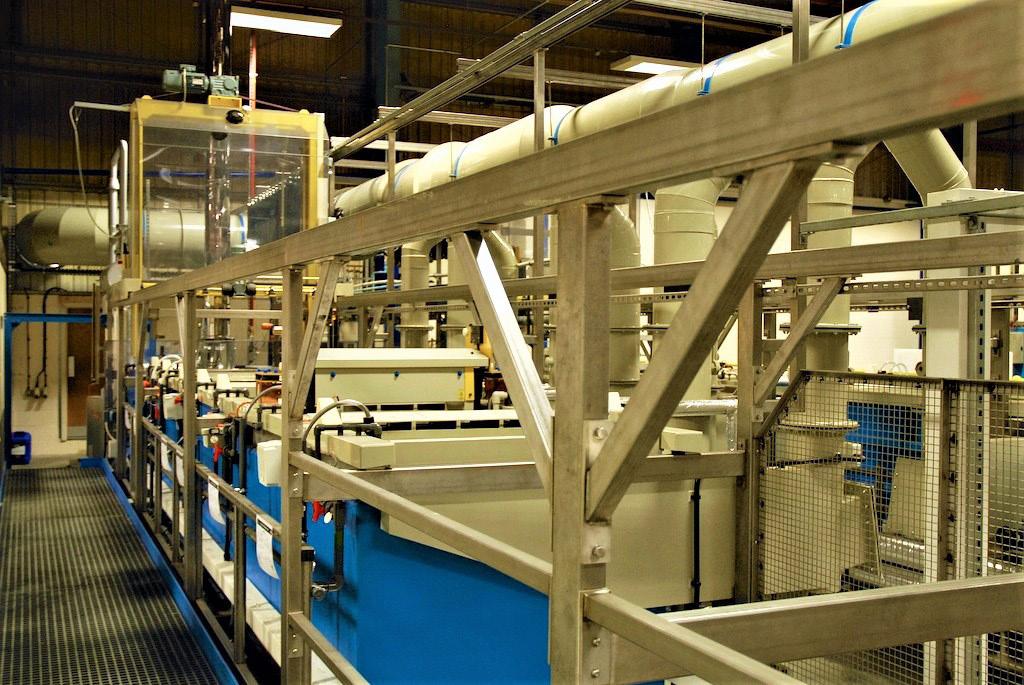
2 minute read
NOVEL HANDLING SYSTEM REMOVES JIG MARKS FROM ELECTROLESS NICKEL PLATING APPLICATION
Plastratum Ltd, the Metal Finishing Equipment and Chemical Engineering Company was approached by a major manufacturer of automative components to design, manufacture, install and commission two fully automatic plants, one for the acid zinc plating of brake calipers and one for the electroless nickel plating of the integral associated pistons. Both plants were complete with the supply of effluent treatment plant equipment and fume extraction with fume elimination.
The two plants were heated by Thermal Fluid systems
The twin transporter Acid Zinc plant was of high volume output and with Plastratum’s proven integrated and standard scope of supply for the application. Both plants were complete with the Plastratum operational control software and management data output. The electroless nickel plant for the pistons had to be provided without any jigging marks and the components could not be barrel plated. Plastratum application engineers evaluated many design opportunities and developed a rectangular polypropylene jig based on a clam shell principle of a base tray and a hinged top lid. Both component parts of the jig were provided with holes to promote the efficient and rapid flow of the electroless nickel as well as flow holes around the vertical perimeter for the same application principle. The pistons were located in the base tray on vertical tubes which were champhered at the top to ensure that the touching surface area presented to the piston was minimised and also had four vertical slots in order to create a high velocity fountain inside the piston. The top lid of the jig was fitted with a small and minimal spherical contact with a 3 mm gap between it and the top of the piston. To mechanically provide the electroless nickel deposition and solution flow, a conventional barrel drive was used which had a central cylindrical polypropylene mandrel between each side of the rotational gears which enabled the provision of two insulated stainless steel bars, to eliminate any plate out, affixed at 90° intervals. The rectangular clam shell jigs were located onto the bars which passed through the jig and were locked off by stainless steel nuts on the front outer edges. When the assembly rotated the force of the solution flow lifted the pistons off the vertical piston location tubes which induced the solution to flow inside the piston with the top of the piston touching the small minimised spherical contact located on the underside of the top lid. As the rotational angle was continued the piston fell back onto the vertical slotted location tube and at the top of the piston the 3 mm gap to the sperical contact was re-established. Both aspects allowing increased solution flow with no surface jigging irregularities. The rotational velocity ensured that there was an exceedingly low contact time of the piston with the jig components and there were no jigging marks whatsoever on the piston which was exactly the customers requirement.
Telephone: 0121 314 1191 Email: mike@plastratum.com
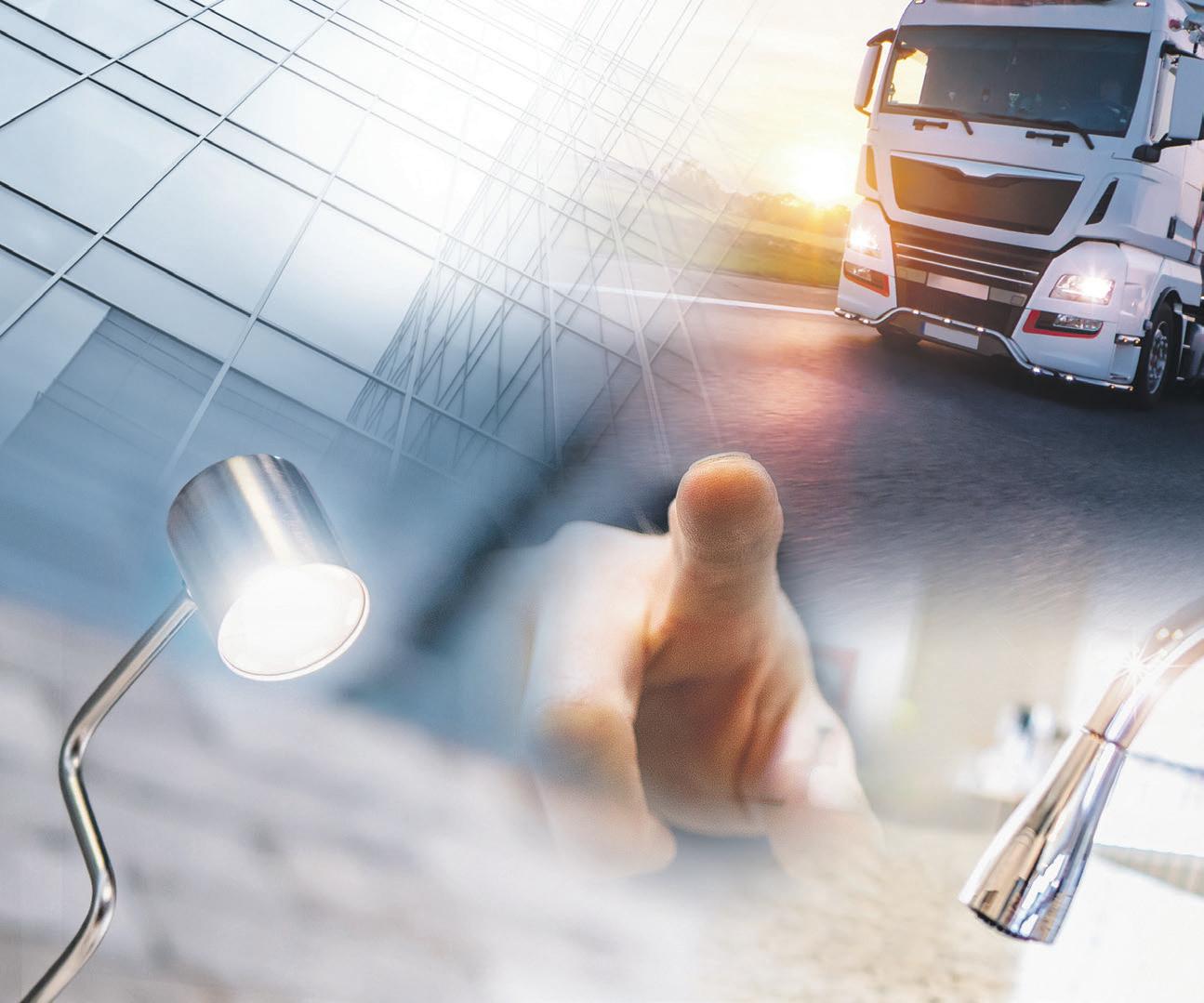
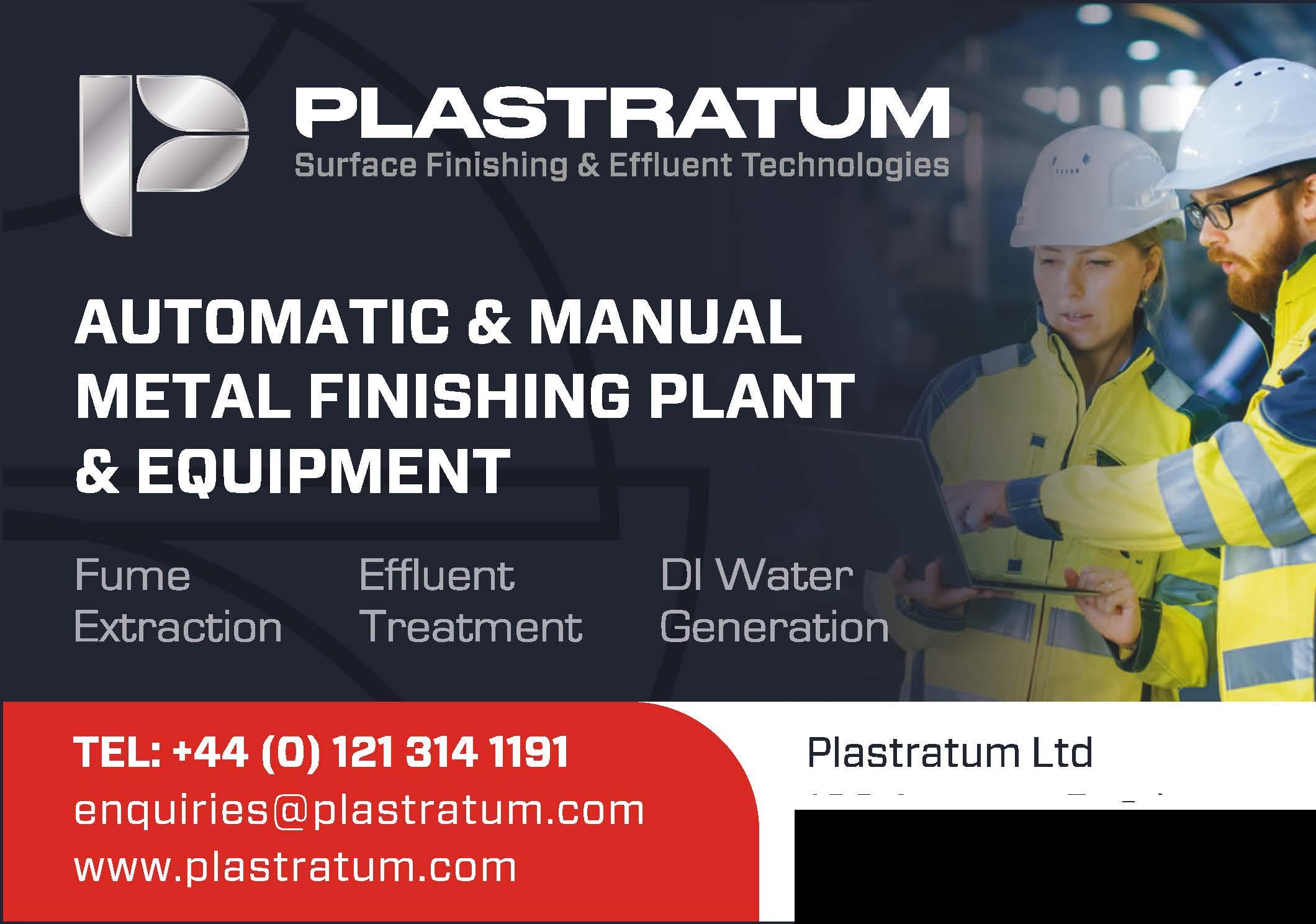
100 Armoury Road Birmingham 811 2RH
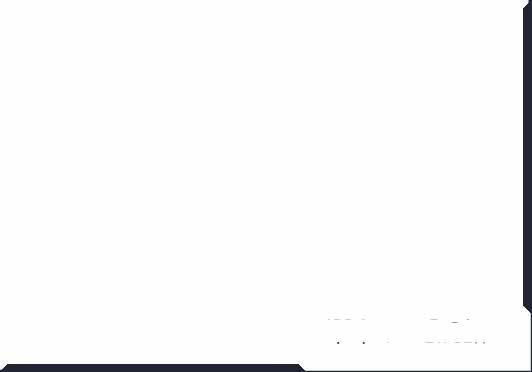