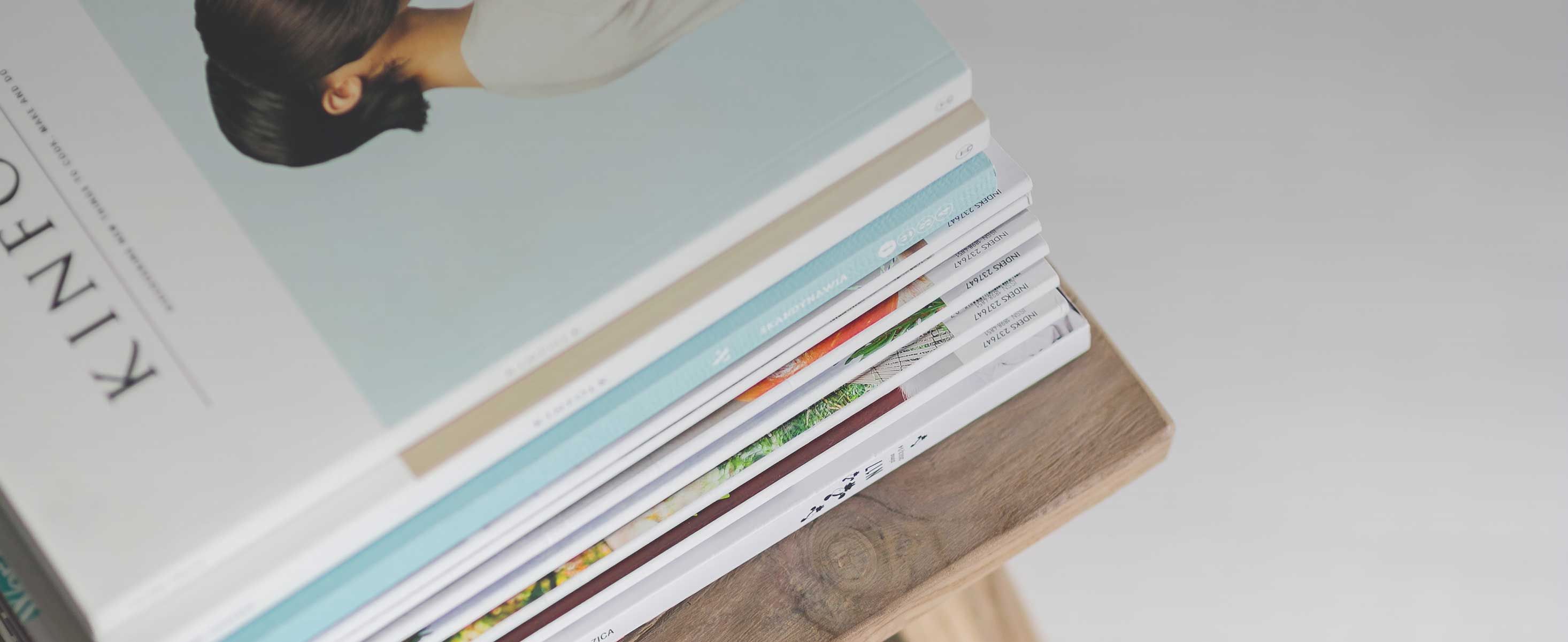
1 minute read
QUALICOAT Chair
from SW February 2023
Architectural Aluminium Powder Coating is applied using the well known methodology of spraying electrostatically charged fine polyester based powders onto a product. Coated aluminium products are then heated to an optimum temperature to melt the powder which allows it to flow and chemically cross-link into a sustainable coating. As the product cools the coating sets and the finish is complete. The problem is, like most applied opaque coatings, the finish may look good, but the coating can hide a multitude of problems on the surface of the metal. If contaminants are present, or a pretreatment process is lacking, a failure of the coating will become evident over time.
A powder coated finish is generally porous, this allows some air and moisture to reach the aluminium surface. When the aluminium eventually begins to oxidise, any applied powder coating will lose its adherence, no matter the quality of the coating itself.
Newly formed aluminium, as soon as it is exposed to the oxygen in the air, begins to oxidise. Corrosion forms quickly into a very thin layer and slows down as the layer becomes thicker. Invisible to the naked eye at first, the process continues until the oxygen in the air is effectively stopped from gaining access to the exposed aluminium surface. This naturally occurring oxidisation builds up over time to completely seal the surface and form a protective layer, this is why aluminium is sometimes specified unfinished for external metalwork. Whilst a natural finish, this oxidisation is often not seen as an attractive finish and therefore aluminium is either powder coated or anodised prior to being used externally. Anodising is simply a rapid and controlled oxidisation of the surface of the aluminium. Typically just 25 microns in thickness, anodising is very hard and wear resistant, but colours are limited generally to bronze, grey finishes or limited dyed colours.
Prior to powder coating architectural aluminium, it is crucial that the aluminium surface is subject to a ‘pretreatment’ process which includes an etch process to remove contaminants and then a passivation or conversion coating to ‘seal’ the surface of the aluminium which also provides a ‘key’ for the adherence of