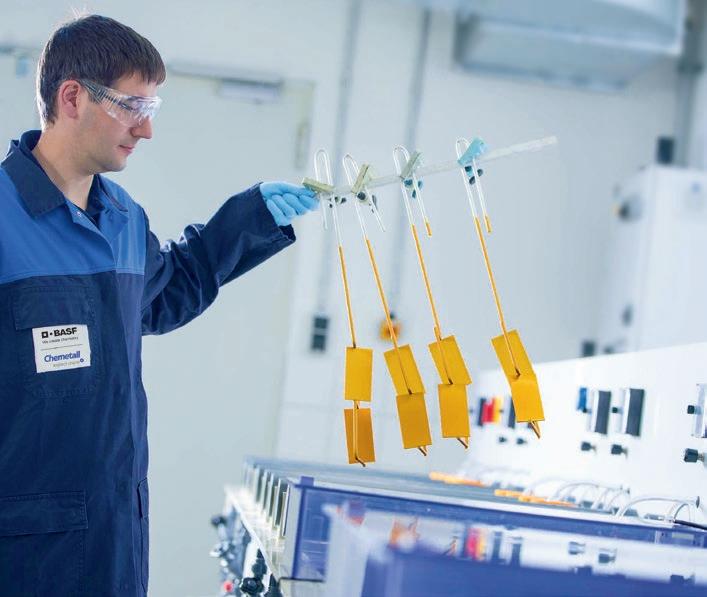
3 minute read
Aluminium Anodizing
Additives from Chemetall
Temperature factor
Chemetall’s Anodizing Technology
Nowadays, it is possible to work with modern additives to the sulphuric acid in the anodizing bath. To this effect, the Surface Treatment global business unit of BASF’s Coatings division, operating under the Chemetall brand, offers innovative additives from its Gardobond range.
worthwhile at first glance. In fact, however, a closer examination and evaluation of the individual process steps reveals possibilities which not only reduce costs but also boost productivity. Chemetall’s anodizing technology demonstrates how this can be achieved.
As a further development of the well-known oxalic acid, it reduces the redissolution rate in the anodizing process and increases the tolerance to dissolved aluminum. This allows for anodizing at a higher temperature, a higher aluminum content and a higher current density at unchanged voltage and/or at a reduced anodizing voltage with the same current density.
The anodizing technology
Chemetall offers a new generation of highly efficient additives. Added to the anodizing bath, they afford a very consistent surface and reduce the aluminum and temperature sensitivity of the anodizing process.
A higher treatment temperature means voltage can be reduced to achieve a density (e.g., for 1.5 A/dm² the following a reference lab test: 19°C - 18 V, 25°C This already provides a possibility for savings. Moreover, basically the same energy will be needed. Thus, the use anodizing additive will allow for energy
From architecture to construction to packaging to automotive – there are almost no limits to the possible industrial applications of aluminum. The processing of this light metal also leaves room for new ideas. Due to the growing competitive pressure, companies are looking for cutting-edge ways to stay ahead of their global competitors with innovative and cost-saving technologies. The solutions to this are closer than you may think: “standard technologies” offer opportunities for saving on costs without compromising on high quality.
Finding potential for improvement in established and proven technologies and processes may not seem good alternatives in practice. This paper presents ideas for optimizing the anodizing process. Experiences and case studies from customer applications around the world have demonstrated the successful implementation of these new solutions in practice. However, it should be decided on a case-by-case basis which technologies are best suited for the respective application, as the applicability should be evaluated individually for each application.
Anodizing is much more than just an optical enhancement of aluminum. The anodized layer that forms using standard technologies reaches at about two thirds into the treated aluminum part and grows at about one third on its surface, thereby affording an attractive, smooth surface and longterm corrosion protection. In addition to these excellent properties, it is also easy to process, making anodized aluminum extremely versatile and suitable for a wide range of applications.
Further potential effects can also be achieved to the speed of the anodizing process. applies for the growth of the layer thickness anodizing with standard parameters, for architectural anodizing: the thicker its growth until it stops growing because acid attack have come to equilibrium.
In this context, a particular focus is placed on the possibilities of saving energy or increasing productivity by reducing the time of the anodizing process and also in the final sealing step.
Gardobond® Additive H 7526 thus yields coatings of perfect quality with a high aluminum content (max. 30 g/l), at higher temperatures (max. 30°C) while at the same time requiring a lower sulphuric acid concentration.
A reevaluation of the anodizing process and of the technologies commonly used in the industry is worth the effort since modified processes have proven to be very
The empirical formula to calculate this thickness (µm) = 0.3 x current density (minutes)
Efficiency improvements and costs
For the standard 1.5 A/dm², practical produced the following approximate values: 10 µm anodizing layer = approx. 20 20 µm anodizing layer = approx. 40
Over the years, almost any anodizer has tried to enhance his productivity by increasing the total number of workpieces to be anodized per day. Frequently, batches are simply increased in size without adjusting other important factors such as cooling. However, an increase of the batch size in many cases also means a drop in current density, which is crucial for surface quality.
This calculation formula clearly shows current density can have on productivity (due to shorter treating time).
Yet, the process temperature, current density and anodizing voltage have a great impact on quality, productivity and costs. As a general rule, higher temperatures result in a larger pore diameter, which in turn leads to less aluminum oxide and thus a softer anodic coating. The same effect can usually be observed at lower current density or (too) high acid concentrations. Coatings with larger pores are generally easier to dye, but in many cases show poorer sealing and corrosion resistance and are generally less durable because the anodic coating may become too soft. Conversely, lower temperatures and/or higher current density usually result in smaller pores that are more durable and thus of better quality.

