
4 minute read
ELECTROPLATING, ANODISING & GALVANISING
renewals. By increasing the maximum tolerance value for aluminum in the anodizing bath, bath renewals need to be conducted less frequently, thereby reducing the volume of acidic effluents and the volume of fresh water required for new bath make-up.
So how can efficiency be improved while at the same time reducing the direct costs of anodizing? Is there a way to speed up the anodizing process to increase productivity, but without compromising the structure and quality of the anodic coating?
Theoretically, it is easy to raise productivity by increasing the current density provided that sufficient rectifier capacity is available. An (excessively) high current density and/or the higher anodizing voltage needed to this effect, would generate a lot of heat that can lead to soft coatings and burns. Additional cooling would thus be necessary.
Additives from Chemetall
Nowadays, it is possible to work with modern additives to the sulphuric acid in the anodizing bath. To this effect, the Surface Treatment global business unit of BASF’s Coatings division, operating under the Chemetall brand, offers innovative additives from its Gardobond range.
As a further development of the well-known oxalic acid, it reduces the redissolution rate in the anodizing process and increases the tolerance to dissolved aluminum. This allows for anodizing at a higher temperature, a higher aluminum content and a higher current density at unchanged voltage and/or at a reduced anodizing voltage with the same current density.
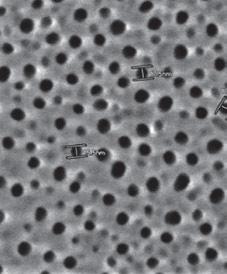
Chemetall offers a new generation of highly efficient additives. Added to the anodizing bath, they afford a very consistent surface and reduce the aluminum and temperature sensitivity of the anodizing process.
Gardobond® Additive H 7526 thus yields coatings of perfect quality with a high aluminum content (max. 30 g/l), at higher temperatures (max. 30°C) while at the same time requiring a lower sulphuric acid concentration.
Temperature factor
A higher treatment temperature means that the anodizing voltage can be reduced to achieve a specific current density (e.g., for 1.5 A/dm2 the following was observed in a reference lab test: 19°C - 18 V, 25°C - 15,5 V, 30°C - 14 V). This already provides a possibility for significant energy savings. Moreover, basically the same amount of cooling energy will be needed. Thus, the use of an adequate anodizing additive will allow for energy savings of ca. 40%.
Furthermore, a reduced consumption of sulphuric acid is possible, also combined with a reduction of the waste water flow due to reduced acid carryover into the rinsing baths.
Furthermore, a reduced consumption of sulphuric acid is possible, also combined with a reduction of the waste water flow due to reduced acid carryover into the rinsing baths.
Further potential effects can also be achieved with regard to the speed of the anodizing process. The following applies for the growth of the layer thickness during anodizing with standard parameters, for example those for architectural anodizing: the thicker the layer, the slower its growth until it stops growing because layer growth and acid attack have come to equilibrium.
The empirical formula to calculate this is: thickness (μm) = 0.3 x current density (A/dm2) x time (minutes)
The most important technical effect of the modified anodizing process, however, lies in the significant improvement of the surface and sealing quality. Higher anodizing temperatures also mean higher layer dissolution caused by acid attack, leading to an increase in anodic pore diameter while the oxide content in the layer decreases which causes the overall surface quality to drop considerably.
The most important technical effect of the modified anodizing process, however, lies in the significant improvement of the surface and sealing quality. Higher anodizing temperatures also mean higher layer dissolution caused by acid attack, leading to an increase in anodic pore diameter while the oxide content in the layer decreases which causes the overall surface quality to drop considerably.
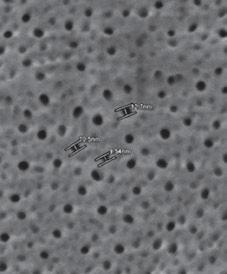
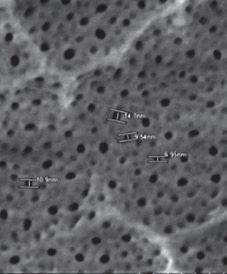
For the standard 1.5 A/dm2, practical experience has produced the following approximate values:
This in turn affects the sealing quality as well as the abrasion and corrosion resistance. The effect can be countered by using the appropriate additive.
This in turn affects the sealing quality as well as the abrasion and corrosion resistance. The effect can be countered by using the appropriate additive.
10 μm anodizing layer = approx. 20 - 22 minutes,
20 μm anodizing layer = approx. 40 - 44 minutes.
The pictures show the surface structure at different temperatures and aluminum contents: with Gardobond® Additive H 7526, the same pore sizes can be achieved at 25°C as in a bath at 19°C without any additive.
The pictures show the surface structure at different temperatures and aluminum contents: with Gardobond® Additive H 7526, the same pore sizes can be achieved at 25°C as in a bath at 19°C without any additive.
This calculation formula clearly shows the effect a higher current density can have on productivity enhancement (due to shorter treating time).
Gardobond® Additive H 7526
Positive side benefits
Another possible “side benefit” are less frequent bath renewals. By increasing the maximum tolerance value for aluminum in the anodizing bath, bath renewals need to be conducted less frequently, thereby reducing the volume of acidic effluents and the volume of fresh water required for new bath make-up.
Gardobond® Additive H 7526 can thus significantly improve the surface quality. The chart on the next page shows the options for improving the surface quality taking the example of the loss of mass as per ISO 3210 in an anodizing process with and without additive:
Possible benefits with Gardobond® Additive H 7526:
Lower overall process costs for energy (power and cooling)
Filter cake disposal: less sulphuric acid in the effluent
Productivity: reduced anodizing times
WEDGE GROUP GALVANIZING Your Galvanizing Partner
Hot dip galvanizing provides you with long-term protection against rust and corrosion of steel products. With 14 plants across the UK, Wedge Group bath value renewals need reducing the fresh water
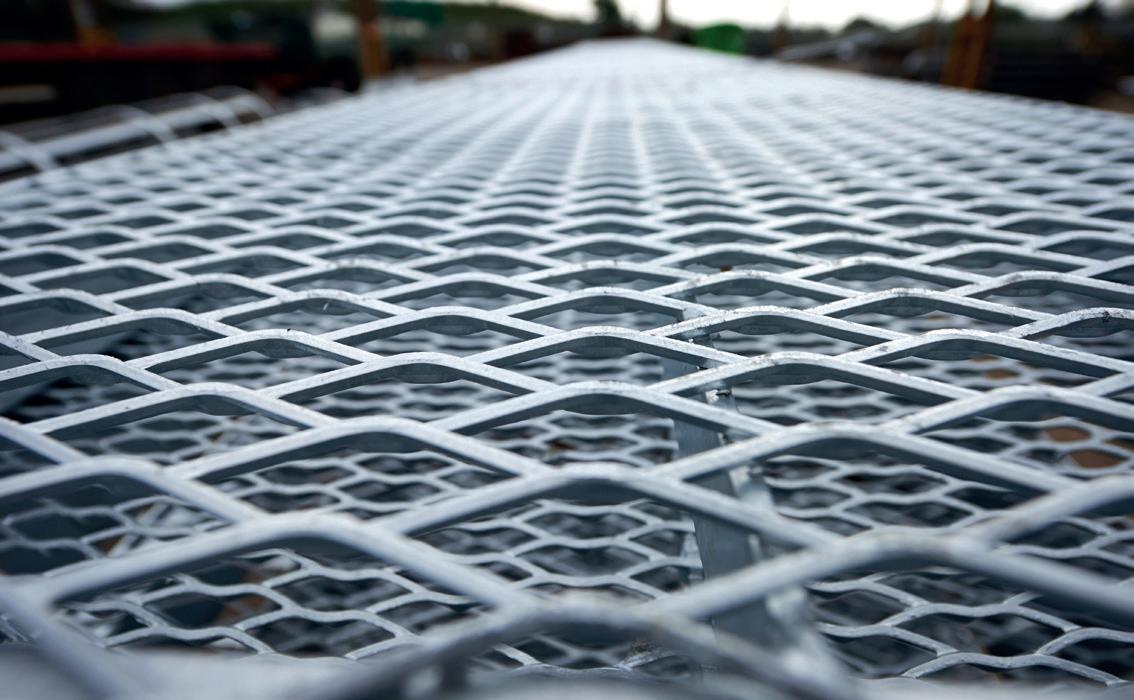
Galvanizing is the UK’s largest hot dip galvanizing organisation offering a national service, collection and delivery and 24hr turnaround on request. The group can process anything from small components to 29m structural beams.
Gardobond® Additive H 7526 can thus significantly improve the surface quality. The chart below shows the options for improving the surface quality taking the example of the loss of mass as per ISO 3210 in an anodizing process with and without additive:
ELECTROPLATING, ANODISING & GALVANISING
sulphuric acid the waste rinsing modified layer increase in surface the can be different Gardobond® achieved at
Possible benefits with Gardobond® Additive H 7526:
Anodization with the technology developed by Chemetall does not only improve the treatment processes, but also the characteristics and benefits of the aluminum proper. As a tried and tested technology supplier, Chemetall develops and optimizes customized technologies for all anodization applications – worldwide.
Contact and further information:
Gary Mothersole
UK Sales Manager Aluminium Finishing
Telephone: 07825 319214
Email: gary.mothersole@basf.com
Visit: www.chemetall.com
Gardobond ® 7526
PAINT & POWDER
Lower overall process costs for energy (power and cooling)
Filter cake disposal: less sulphuric acid in the effluent
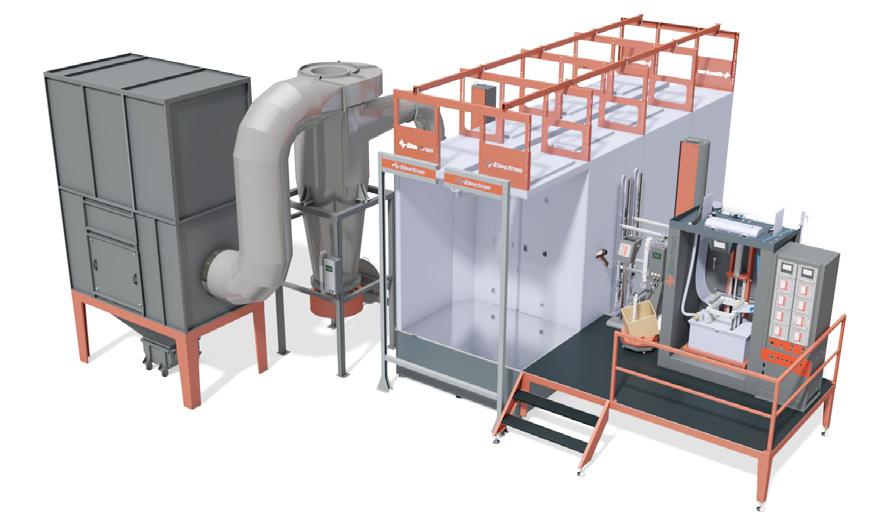
Productivity: reduced anodizing times