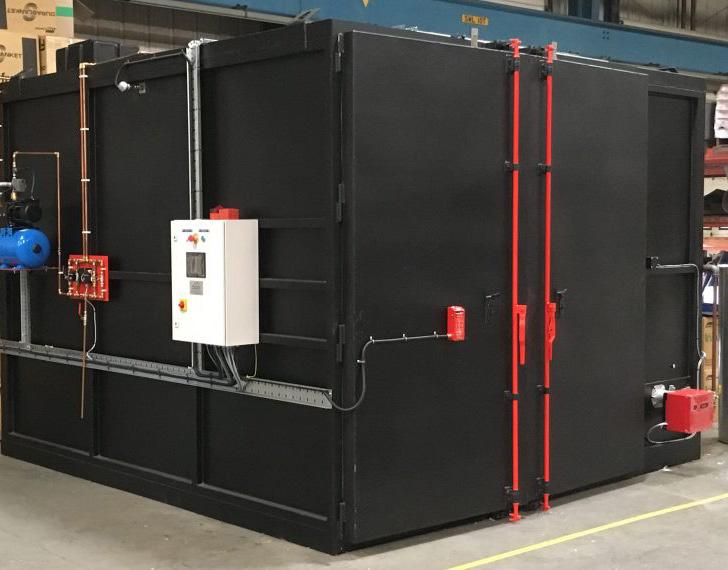
2 minute read
Burn off ovens offer effective process to remove plastic, paint coatings or contaminants
Burn off ovens (also commonly known as pyrolysis ovens or burnout ovens) offer an extremely effective process for the removal of plastic or paint coatings and contaminants from process machinery and components. This burns off the unwanted residue and preserves the original machinery part with minimal damage, offering prolonged lifetime and multiple usage. Our burn off / burnout ovens are custom built here at Longworth and can therefore house and clean a wide range of items and sizes.
How does a burn-off oven work?
Burn-off ovens use a process known as pyrolysis. They remove or break down organic materials t hat have adhered to metal parts. This works by heating the parts in a reduced oxygen atmosphere where a reaction takes place and reduces the contaminant to a residue that is richer in carbon. Any emissions that are given off during this process are put through an afterburner that heats these gasses to 850°C for a minimum of half a second. By heating these gasses to such a temperature turns them into H2O and CO2.
Longworth burn off ovens are constructed to exacting standards to suit the particular requirements of individual clients. To achieve the precise control our customers expect, each oven features a number of distinct burn-off or pyrolysis temperature profile settings. These profiles can be used to gradually break down the contamination whilst preventing the overheating of the component being processed.
Although our standard selection includes several models in various sizes – on the rare occasions that our selection doesn’t offer something to suit your requirements, we will design an oven to address your specific needs.
Features
Several models which come in various sizes, bespoke options available to suit requirement.
Incorporates PLC control, Touch screen HMI and on screen fault finding facility.
Oven interiors can be lined in stainless steel to avoid damage to internal insulation sustained via everyday knocks and scrapes.
Online oven maintenance option allows remote maintenance and fault finding from engineers in our Blackburn (UK) office.
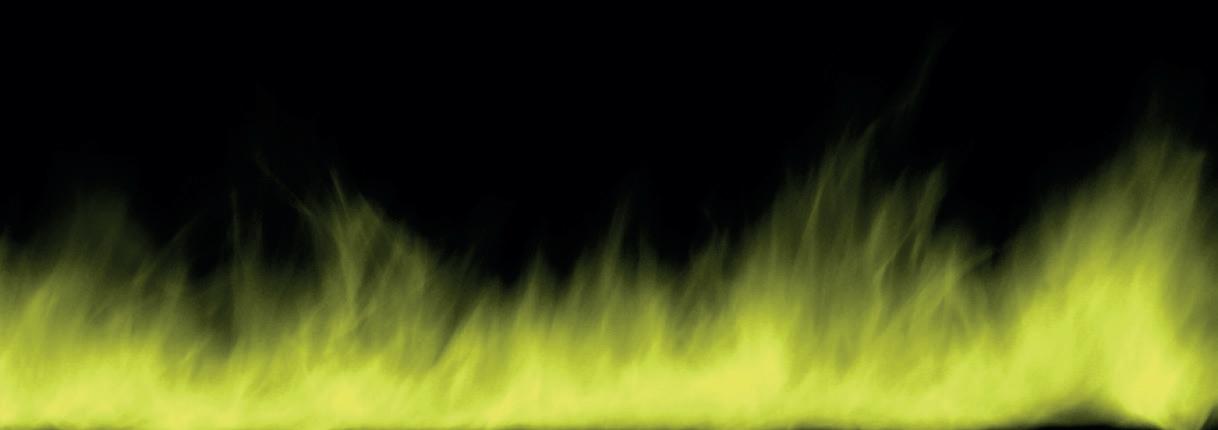




Benefits
Our skilled and responsive team of engineers will ensure that your pyrolysis oven is maintained to perform at optimum efficiency.
The robust design and construction of our burn off ovens means they offer years of reliable performance even in the harshest industrial conditions.
Built using 20 years of knowledge and experience gained from the cleaning of components from many different production processes and industrial cleaning environments.
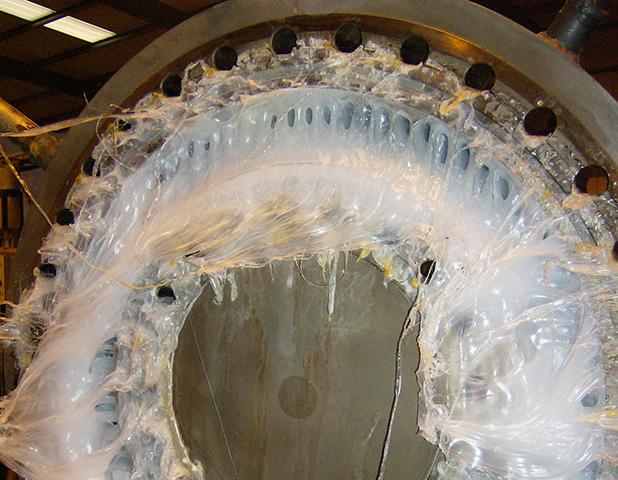
How Does Pyrolysis Work?
Burn off processing involves heating a contaminated component at a controlled temperature in a low oxygen environment. This has the effect of vaporising the volatile constituents of the contaminations.
We also sell our burn ovens for customers to use within their own facility, and we only ever sell the same specification ovens that we use ourselves for on-site processing, giving peace of mind that the same results can be achieved.
Benefits
Less damaging than traditional cleaning processes
No expensive chemical disposal costs
Custom designed PLC control including ramped temperature control
Who Is Burn Off Processing For?
Industries and Processes:
Powder and paint coating
Polymer extrusion and moulding
Commercial bakery tray refurbishment
Electric motor refurbishment
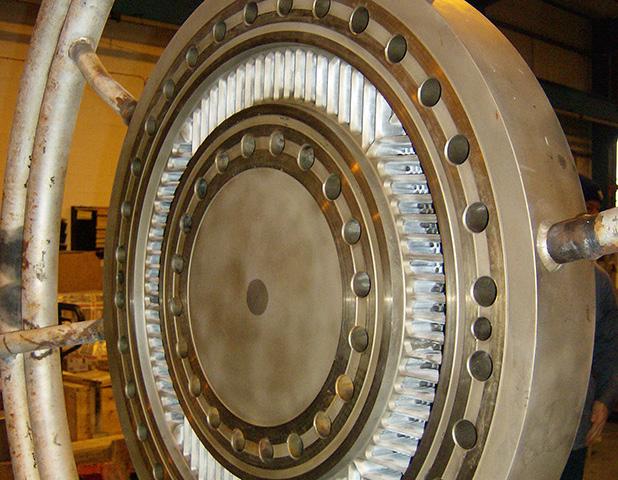
Process component refurbishing including pumps and pipework
Components and Parts:
Paint jigs & frames
Car & bike parts
Food trays
Filter housings
Automotive and railway brake pads
Commercial storage shelving
Telephone: +44 (0) 1254 680501
Email: enquiries@bmlongworth.com
Visit: www.bmlongworth.com
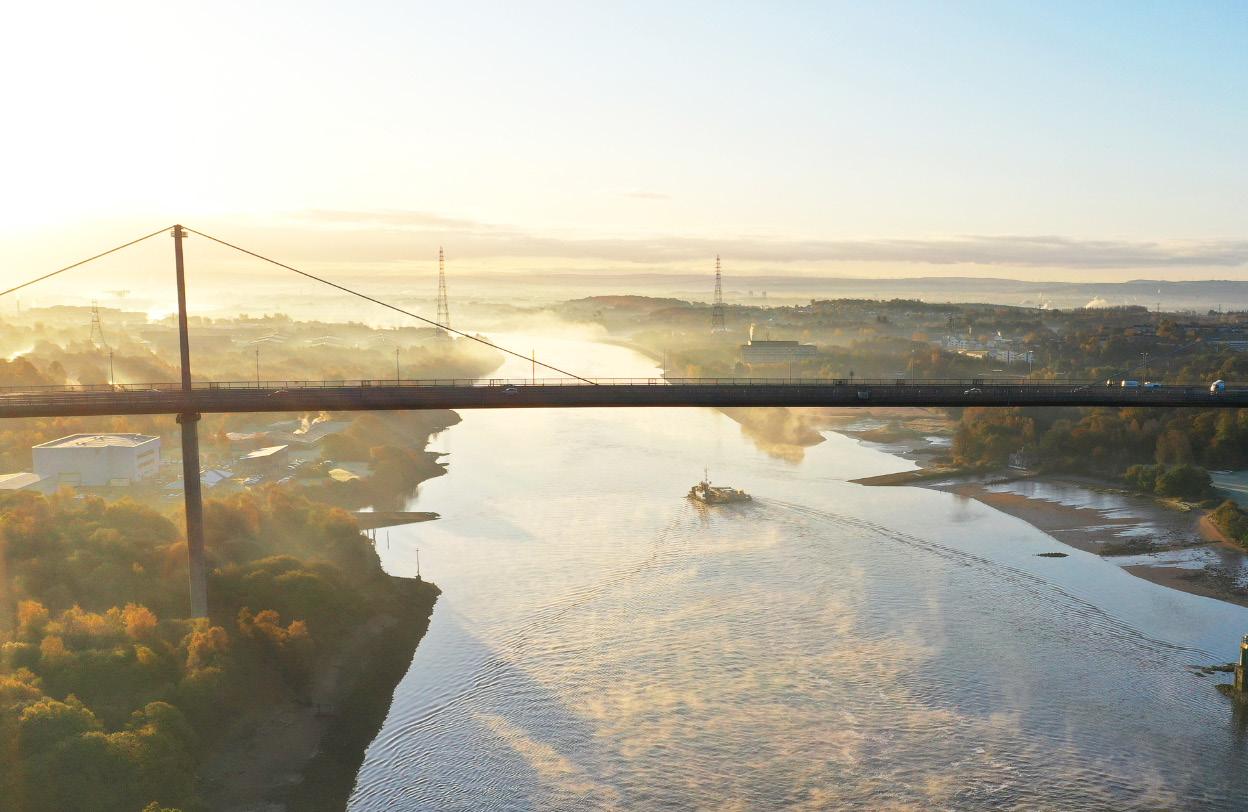
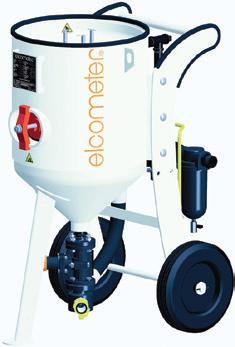
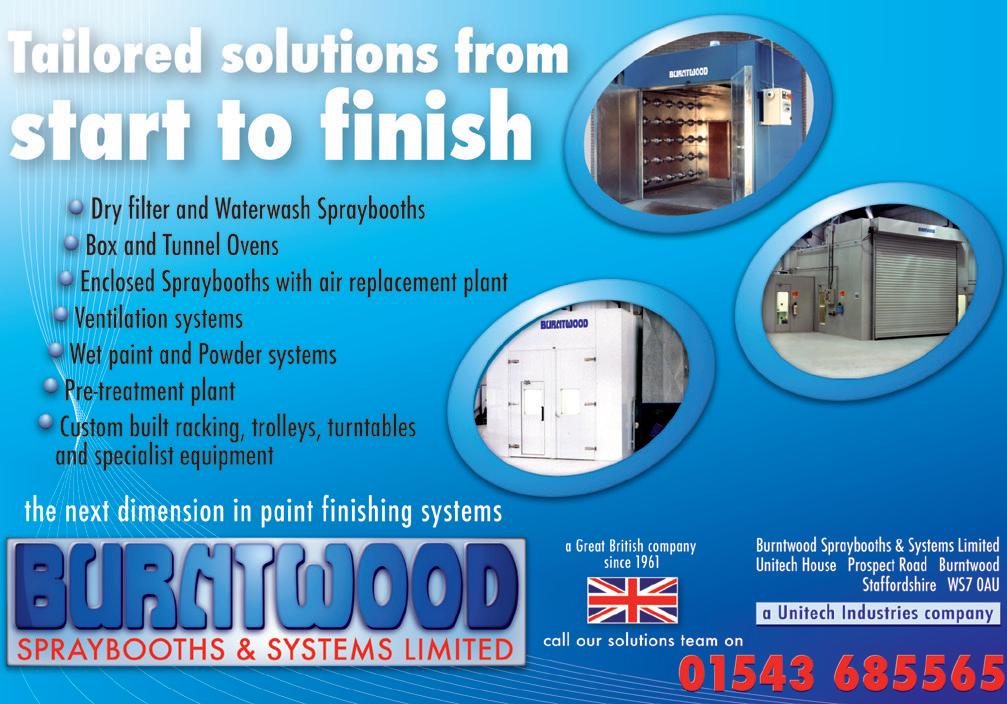
OVENS, SPRAYBOOTHS & PROCESS HEATING
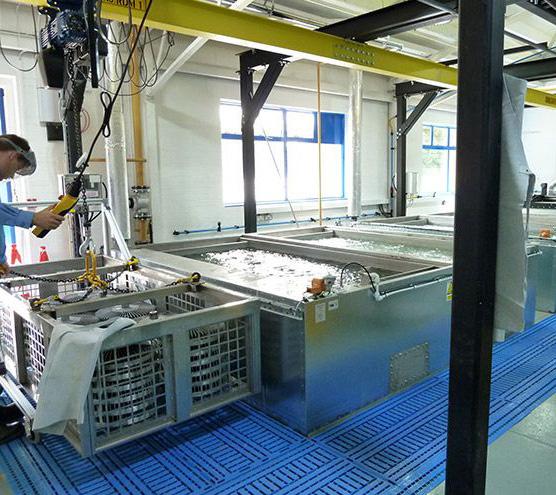
