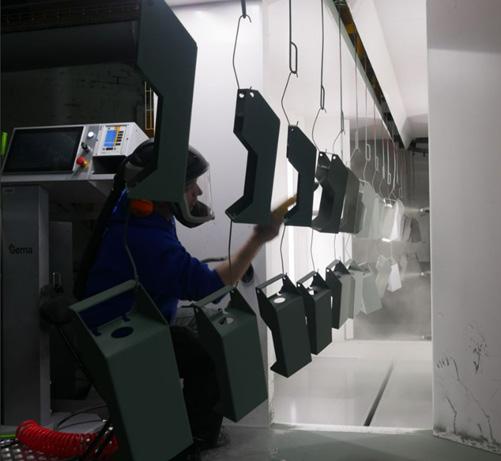
2 minute read
Ritherdon have recently invested in the purchase of a Magic Compact powder coating system
Established in 1895, Ritherdon have been manufacturing a variety of electrical enclosures and related products for many decades. A passion for innovation with close working relationships with their customers means that they are continually developing and expanding their product ranges.
These products are used across a wide variety of industries such as Industrial metering panels for the electricity supply industry, EV Charger Enclosures, Data and Fibre cabinets & Passive Fire Protection Products.
Their stainless steel electrical enclosures are also used in many other applications where electrical or electronic equipment needs protecting from the elements, from solar photovoltaic farms in the UK to oil wells in Saudi Arabia.
Ritherdon have recently invested in their coating process with the purchase of a Magic Compact powder coating system from Gema UK & Ireland. After viewing various manufacturers, Gema was the chosen supplier due to the reputation Gema has for market leading after sales, low running costs, quality and equipment reliability. saving significant cost, and reducing the carbon footprint.
Gema supplied their premium Magic Compact line, complete with SIT dense phase pump technology, with batch management and energy optimisation system. Gema Powder Coating’s dense phase technology is a proven way to improve the efficiency and quality of powder coating applications. If you are looking for a way to improve your powder coating process, dense phase technology is a great option to consider. The advantages of a consistent controlled powder cloud, less powder degradation and exceptionally long service life are key factors in maintaining repeatable outputs day after day.
The new state-of-the-art powder coating plant keeps Ritherdon providing the best powder coated finish, quality and performance.
We look forward to increasing our capacity, providing the best paint finish for our products and most importantly doing so in an eco-friendly way.
The new powder coating paint plant will also boost efficiency and help Ritherdon further reduce the environmental impact of their manufacturing process due to the exceptionally efficient powder recovery circuit which can reclaim up to 97% of powder. The additional inverter-controlled filter drive system only consumes the power needed and automatically drops to idle mode when no part is detected,
The Management Team at Ritherdon proudly shared that “We look forward to increasing our capacity, providing the best paint finish for our products and most importantly doing so in an eco-friendly way. Making use of the advanced technology that allows the OptiCenter to reclaim up to 97% of the powder used, after being recovered and filtered, with minimal waste at the end of the process.
We pride ourselves in our quality powder coated finish of all Ritherdon Enclosures: cabinets, feeder pillars, meter boxes and FireSeals. The powder coated finish make Ritherdon stainless steel enclosures achieve the ‘smart look’ we are known for!”
John Wright, Operations Director (left) with Operator Matthew Bradley. Matthew is delighted with new system and how it is transforming the coating operation for him and his colleagues.
Visit: www.gemapowdercoating.com
