
5 minute read
CLEANING - OWN THE PROCESS AND CUT THE COSTS
Fraser Technologies: Cost of Ownership Cleaning - own the process and cut the costs
With the cost of living continuing to rise and energy prices doubling, businesses are looking for more ways to cut costs and increase effi ciencies, without reducing on quality.
When it comes to component cleaning, compromises can rarely be made on levels of cleanliness, but there are opportunities to make cost savings by ensuring the system being used is the most suitable for the items being cleaned. In many circumstances, investing in the correct equipment and chemistries can lead to a much more efficient and cost-effective process. While it may seem counterintuitive, an investment and initial cost outlay in the short term could lead to significant efficiencies and cost savings in the medium and long term. To understand the cost savings when it comes to owning the cleaning process, it’s important to look at the full process and the associated (and often hidden) costs involved in it. For organisations that currently clean components by hand, there are a number of immediate benefits of automation. Using the right equipment for the job makes the process much more efficient – items can be cleaned in batches; it’s an extremely fast activity (in many cases, just a few minutes!); it is much less labour intensive, freeing up the time of a person – or people – on the factory floor to get on with other jobs; and the level of cleanliness can be controlled, so every item is perfectly clean, every time. We recently started working with engineering client that had been cleaning components by hand after moving away from solvent cleaning years ago due to the negative impact solvents had on the environment. They were finding that the process was a laborious one – with staff often spending an hour or two on cleaning parts to ensure oil and residue was removed from each component, and that they were fully dry before use. They were finding that parts were not getting totally cleaned or totally dried, so were either needing a second clean, or were starting to rust due to the damp. Plus, as some of the parts were plated, if oil residue was left in the folds, it would affect the plating and they would not be fit for purpose and would be scrapped. They began a contract manufacturing high-reliability, plated parts that were retaining a significant amount of grease and residue. In a bid to improve the cleaning quality and save time on the factory floor, they approached Fraser Technologies to look
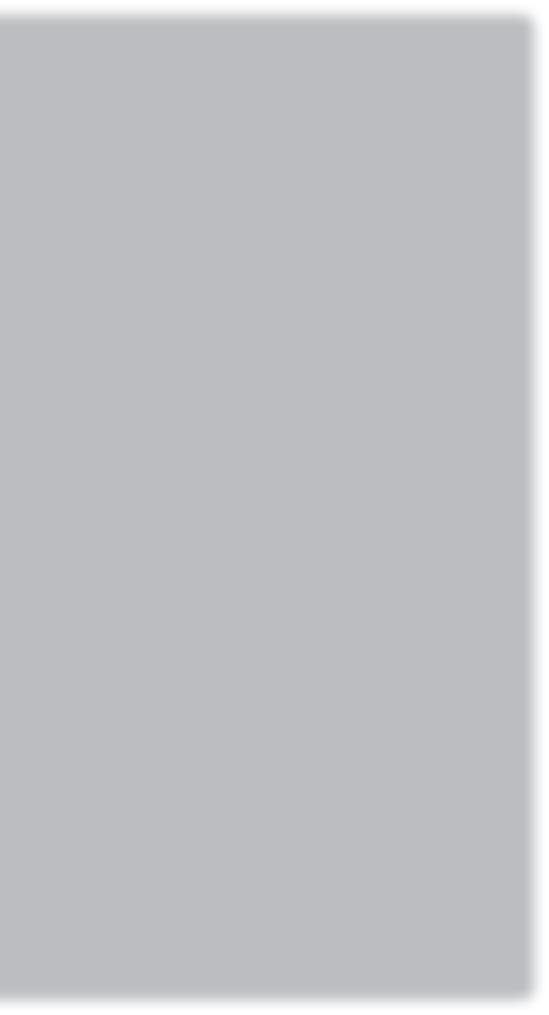
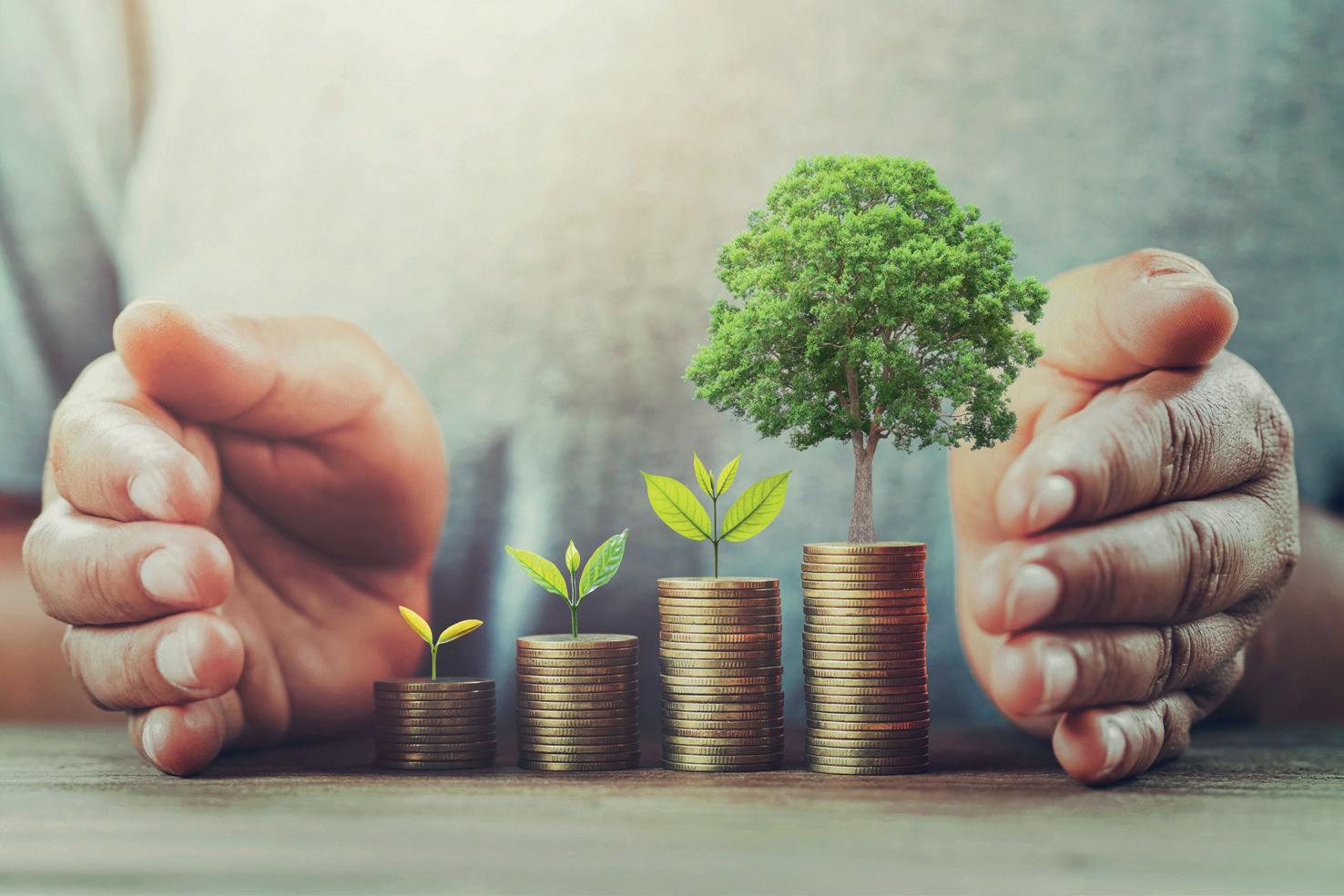
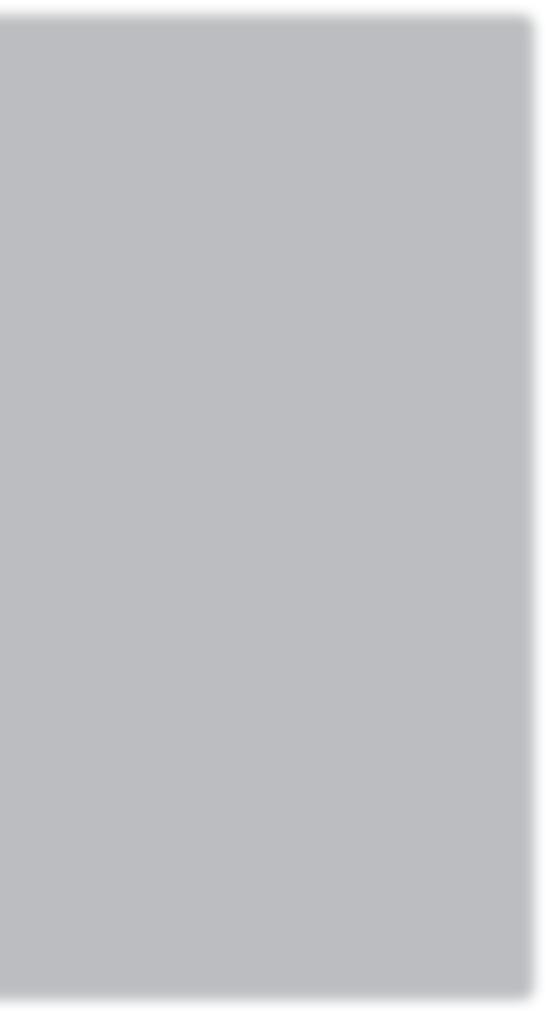
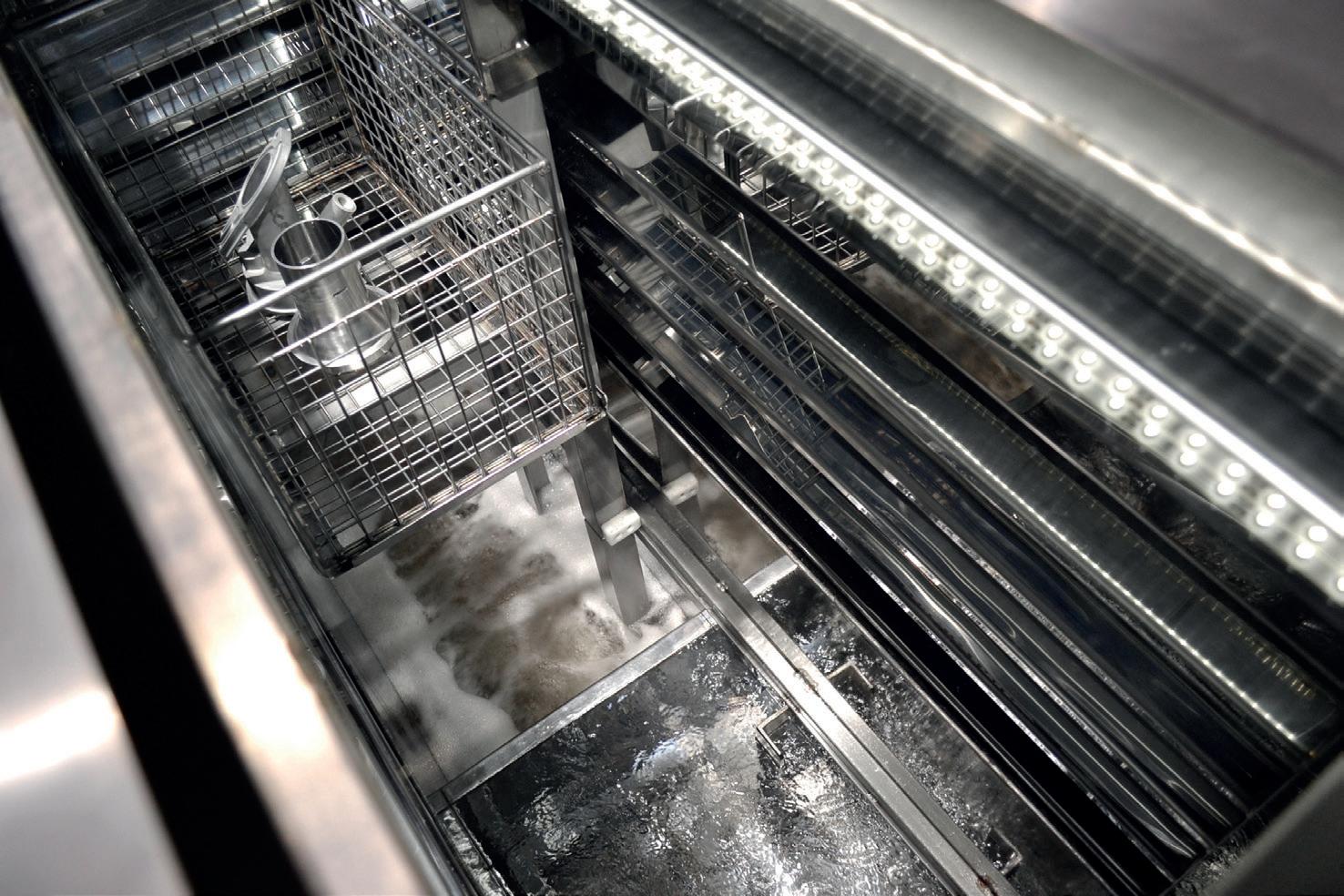
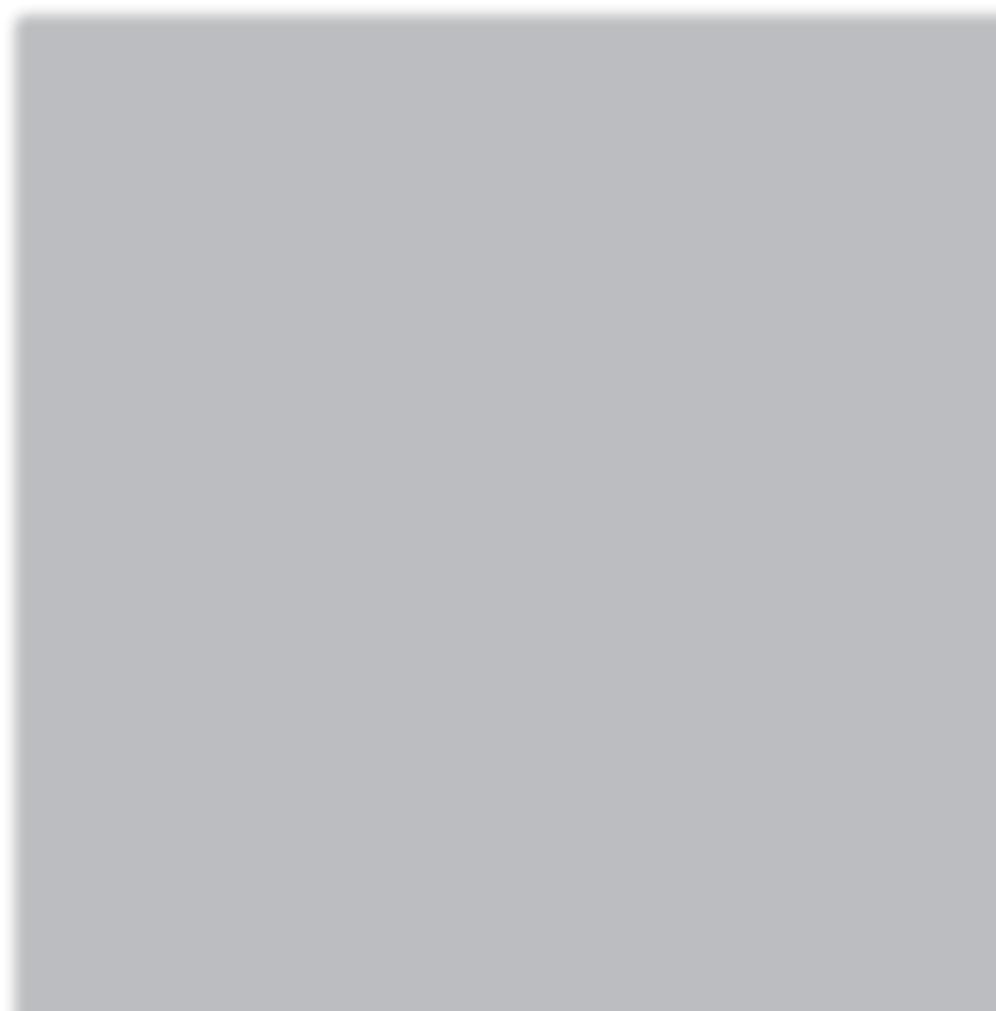
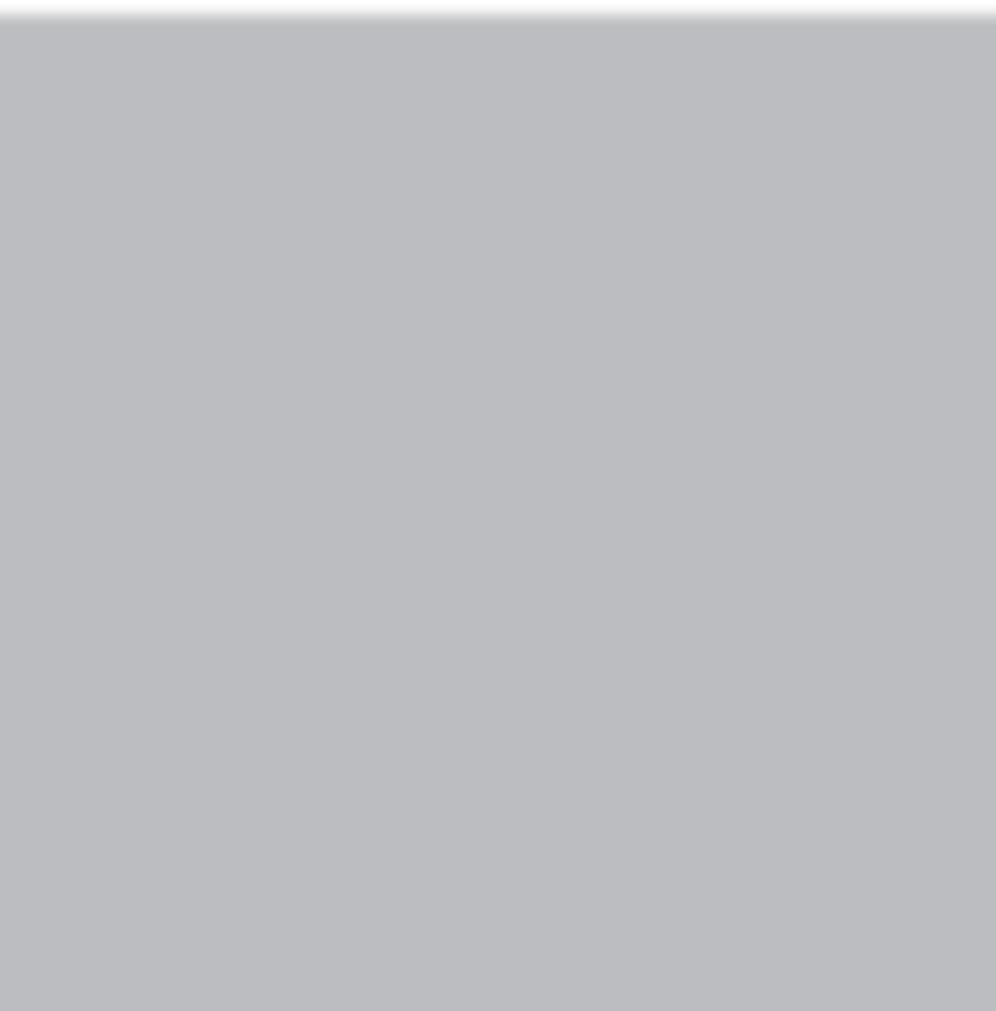
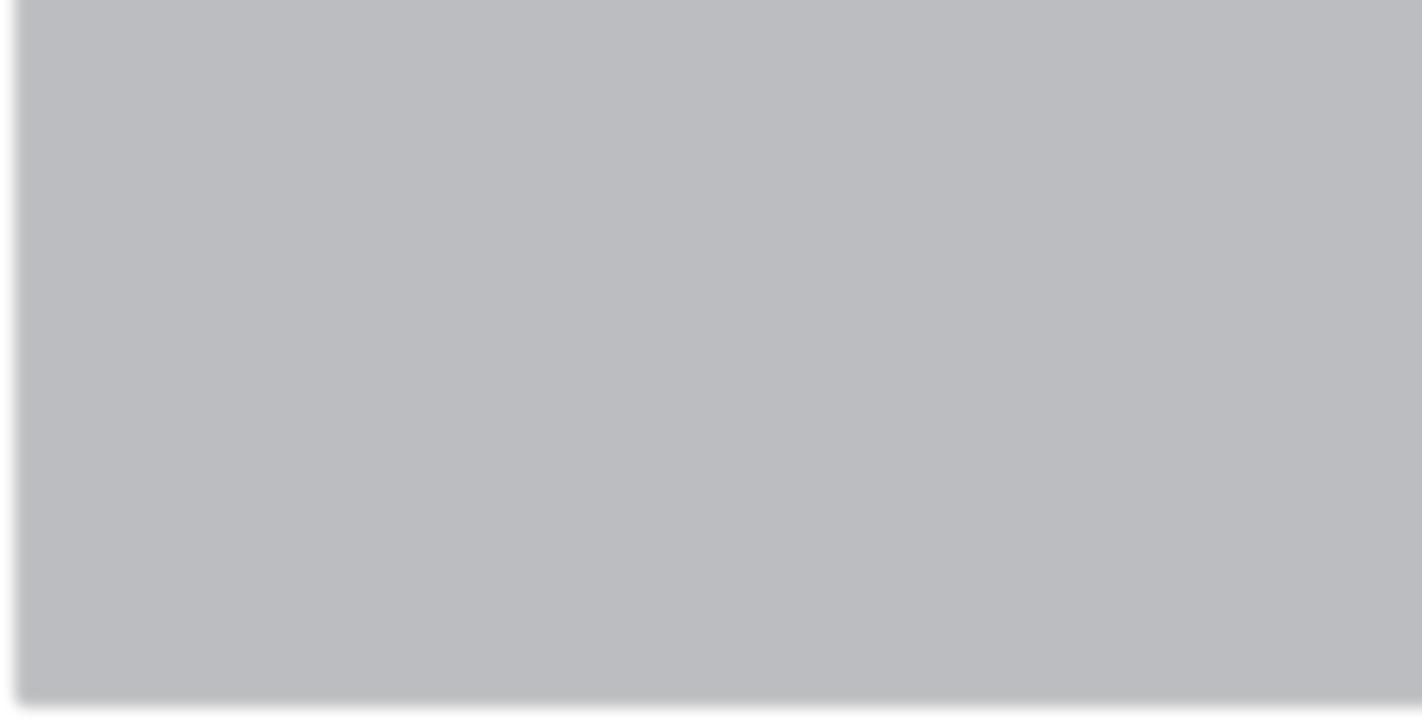

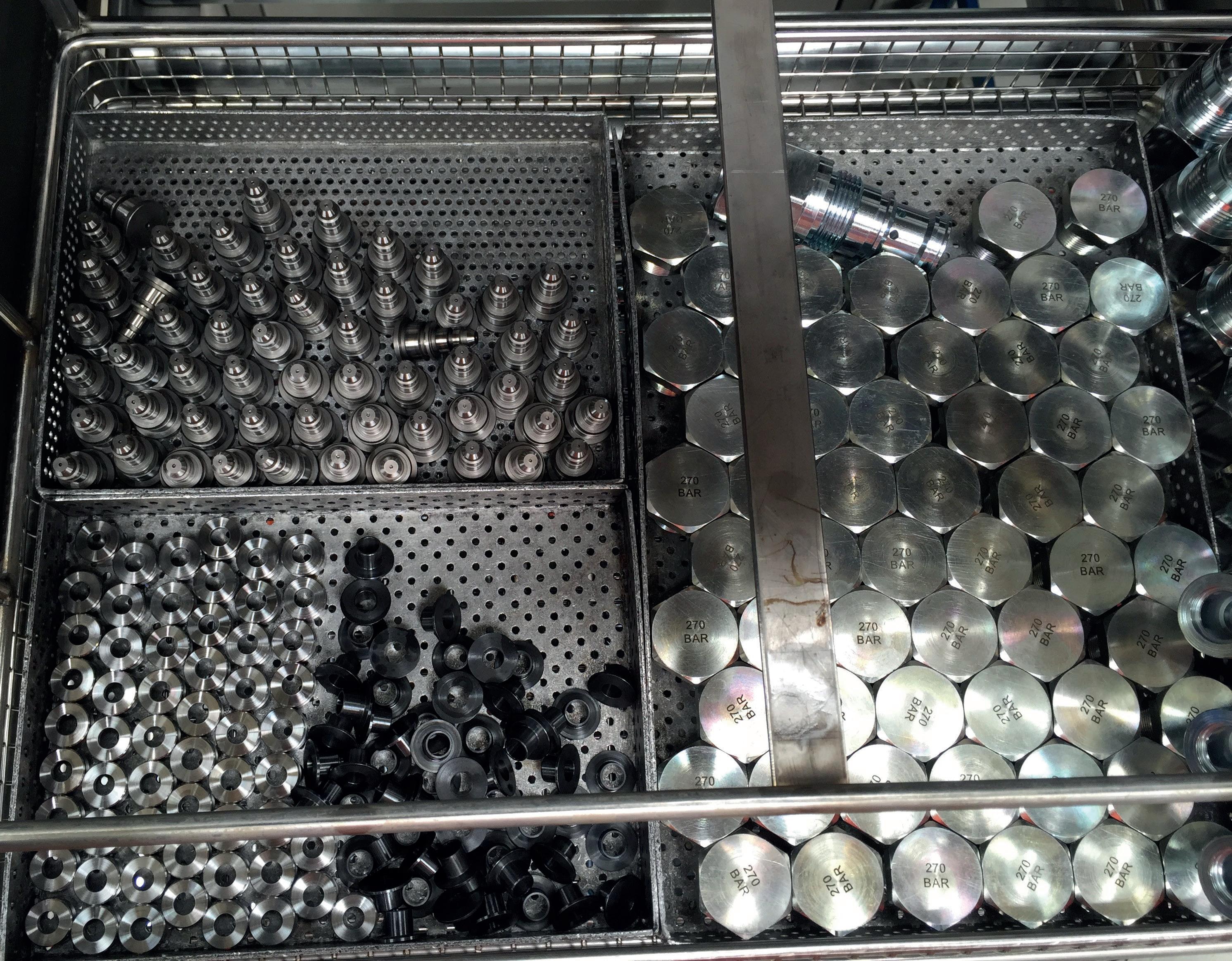
at alternative solutions. While this organisation had - quite rightly - moved away from old generation solvents, Fraser Tecnhologies was able to introduce them to the new generation of solvents that have been developed specifically with the environment in mind and are far less harmful than comparable solutions. One such product is Opteon™ SF80 from Chemours. SF80 has an ultralow global warming potential (GWP) of less than 2.5, unlike common F-gas solvents that can have a significantly higher GWP. SF80 is just as effective as these damaging competitor products – and in many cases can be even more efficient.
Installing one of our best-selling Solvent machines – which is compact, good value for money and extremely simple to use – along with SF80 has revolutionised their cleaning process. Not only are the parts now consistently spotlessly clean, they can clean more at a time and the process is complete in just minutes – with no need for rinsing or drying. They’ve found it to be less messy, more efficient, and it also has a positive impact on the team as it is silent and all enclosed, so a much safer and less distracting process. They’re so pleased with the results, they’ve started putting additional parts from other contracts and customers through the process, as it saves them time on the floor. What was initially a short term investment for a specific contract has turned into a new way of cleaning for the full team, and one that they’re keen to continue. As well as saving time and boosting cleanliness levels, by considering the system in place and making sure it’s properly set up – whether with a new machine or an upgrade - the amount of chemistry solution being used can be controlled to very low levels, which again saves money in the long term. In addition, most of the waste solvent can be recovered and recycled from the machine by the Fraser Technologies team. As a result of this, the energy consumption of the process is also reduced. Solvent cleaning uses one fifth of the energy required with an aqueous cleaner and is more controlled than manual washing. Not only is it five times more energy efficient, but it also has quicker cleaning cycles, leaves zero residue, and has three times better surface penetration. Using an Opteon™ specialty fluid such as SF80 reduces weekly CO2 usage by 75%, reduces weekly fluid consumption by 50%, and reduces the cost of average daily consumables by eliminating water treatment. In the current climate, all investments need to be able to demonstrate a return, but when it comes to cleaning, the return is literally clear to see. An efficient process saves time and money, while also ensuring quality – protecting the reputation of the business and keeping clients happy. When considering investing in cleaning – can any business afford not to?
For more information about the products off ered by Fraser Technologies, get in touch at sales@frasertech.co.uk, call 01506 443 058 or visit www.frasertech.co.uk.